0Cr18Ni9换热器应力腐蚀开裂失效分析
换热器板片腐蚀穿孔原因分析及解决方案

换热器不锈钢板片腐蚀穿孔
原因分析及解决方案
板式换热器泄露穿孔问题可能原因分析
1、换热器板片材料选用的是奥式体类不锈钢,比如304或321
型材质.这种不锈钢材质对氯离子特别敏感,抗点蚀性能比较差。
2、由于循环冷却水补充水中氯离子含量很高(超过180mg/l),
造成通过浓缩后的循环水中氯离子含量超过国家国标不锈钢换热设备对水中氯离子含量300mg/l的标准,引起换热器板片点蚀。
3、人字形波纹波纹板片是经冲压成型的,在冲压成型过程中,因
为形变产生的内应力,使板片加大了应力腐蚀的倾向。
解决方案
1、更换已经穿孔的板片,在可能的情况下采用钛板等类似抗
腐蚀能力较强的板片。
2、严格控制循环水中氯离子的含量,每日有专人化验,通过
排污的方式,把循环水中的氯离子含量控制在300mg/l以
内。
换热器管座角焊缝裂纹原因分析及防范措施

换热器管座角焊缝裂纹原因分析及防范措施摘要:本文在换热器实际使用环境的基础上,简要阐述了换热器管座的常见缺陷,之后对主要缺陷,即换热器管座角焊缝疲劳裂纹从分类与分布上进行了详细分析,最后,提出了一些检测疲劳裂纹的方法以及检修换热器管座角焊缝疲劳裂纹的措施,提供相关单位进行参考。
关键词:换热器;管座角焊缝;疲劳裂纹;维护技术前言:换热器是将热流体的部分热量传递给冷流体的设备,又称热交换器。
换热器是化工、石油、动力、食品及其它许多工业部门的通用设备,在生产中占有重要地位。
在化工生产中换热器可作为加热器、冷却器、冷凝器、蒸发器和再沸器等,在化工企业内得到了广泛应用。
然而,在复杂的生产工况条件以及换热器管座自身的结构型式、受力特点和材料特性,以及制造成型工艺的影响下,换热器管座会在容器内压、重力载荷(包括设备自重、介质、附属设备、管道等)、连接管道等部件的作用力、温度梯度引起的作用力、压力激烈波动引起的冲击载荷[1]的作用下,产生一系列的缺陷,最为典型的就是疲劳损伤。
疲劳断裂是一种主要的金属结构失效形式,在循环载荷的强烈影响下,钢结构会因腐蚀、应力集中等状况出现裂纹,归根结底,这种裂纹是由于疲劳强度引起的,而扩展的裂纹将会引发结构的失效。
目前,换热器管座疲劳开裂以及成为了设计维护关键问题。
一、换热器管座的常见病害(一)涂装劣化换热器通常都是直接接触到大气、周边空气的,而这种长期暴露会对换热器产生一定的侵蚀,对换热器管座安全造成不良影响。
为保护换热器管座的完整性,通常会对结构表面进行一定的维护,而其中最具有效力及最为经济型的就是涂装。
但是观察长期服役的换热器管座表面涂层可以发现,其仍出现大量生锈、脱落、裂纹、起泡、粉化问题,涂层的劣化将导致进一步的腐蚀。
(二)腐蚀不同生产装置所面临的环境有所区别,但工业废气中含有的大量盐粒子、水分、氮化物及硫化物会对换热器管座角焊缝产生一定的腐蚀作用,而所处位置周边空气通常会存在大量工业废气。
应力腐蚀断裂

应力腐蚀断裂一.概述应力腐蚀是材料、机械零件或构件在静应力(主要是拉应力)和腐蚀的共同作用下产生的失效现象。
它常出现于锅炉用钢、黄铜、高强度铝合金和不锈钢中,凝汽器管、矿山用钢索、飞机紧急刹车用高压气瓶内壁等所产生的应力腐蚀也很显著。
常见应力腐蚀的机理是:零件或构件在应力和腐蚀介质作用下,表面的氧化膜被腐蚀而受到破坏,破坏的表面和未破坏的表面分别形成阳极和阴极,阳极处的金属成为离子而被溶解,产生电流流向阴极。
由于阳极面积比阴极的小得多,阳极的电流密度很大,进一步腐蚀已破坏的表面。
加上拉应力的作用,破坏处逐渐形成裂纹,裂纹随时间逐渐扩展直到断裂。
这种裂纹不仅可以沿着金属晶粒边界发展,而且还能穿过晶粒发展。
应力腐蚀过程试验研究表明:当金属加上阳极电流时可以加剧应力腐蚀,而加上阴极电流时则能停止应力腐蚀。
一般认为压应力对应力腐蚀的影响不大。
应力腐蚀的机理仍处于进一步研究中。
为防止零件的应力腐蚀,首先应合理选材,避免使用对应力腐蚀敏感的材料,可以采用抗应力腐蚀开裂的不锈钢系列,如高镍奥氏体钢、高纯奥氏体钢、超纯高铬铁素体钢等.其次应合理设计零件和构件,减少应力集中。
改善腐蚀环境,如在腐蚀介质中添加缓蚀剂,也是防止应力腐蚀的措施.采用金属或非金属保护层,可以隔绝腐蚀介质的作用。
此外,采用阴极保护法见电化学保护也可减小或停止应力腐蚀。
本篇文章将重点介绍应力腐蚀断裂失效机理与案例研究,并分析比较应力腐蚀断裂其他环境作用条件下发生失效的特征。
,由于应力腐蚀的测试方法与本文中重点分析之处结合联系不大,故不再本文中加以介绍.二.应力腐蚀开裂特征(1)引起应力腐蚀开裂的往往是拉应力。
这种拉应力的来源可以是:1.工作状态下构件所承受的外加载荷形成的抗应力。
2.加工,制造,热处理引起的内应力.3.装配,安装形成的内应力。
4.温差引起的热应力。
5.裂纹内因腐蚀产物的体积效应造成的楔入作用也能产生裂纹扩展所需要的应力。
(2)每种合金的应力腐蚀开裂只对某些特殊介质敏感.一般认为纯金属不易发生应力腐蚀开裂,合金比纯金属更易发生应力腐蚀开裂。
应力腐蚀开裂

分类
1、点腐蚀
是一种导致腐蚀的局部腐蚀形式。
2、晶间腐蚀
晶粒间界是结晶学取向不同的晶粒间紊乱错合的界城,因而,它们是钢中各种溶质元素偏析或金属化合物 (如碳化物和δ相)沉淀析出的有利区城。因此,在某些腐蚀介质中,晶粒间界可能先行被腐蚀乃是不足为奇的。 这种类型的腐蚀被称为晶间腐蚀,大多数的金属和合金在特定的腐蚀介质中都可能呈现晶间腐蚀。
2、减少或消除零件中的残余拉应力
残余拉应力是产生应力腐蚀的重要条件。为此,设计上应尽量减小零件上的应力集中。从工艺上说,加热和 冷却要均匀,必要时采用退火工艺以消除内应力。或者采用喷丸或表面热处理,使零件表层产生一定的残余压应 力对防止应力腐蚀也是有效的。
3、改善介质条件
这可从两个方面考虑:一方面设法减少或消除促进应力腐蚀开裂的有害化学离子,如通过水净化处理,降低 冷却水与蒸汽中的氯离子含量对预防奥氏体不锈钢的氯脆十分有效;另一方面,也可以在腐蚀介质中添加缓蚀剂, 如在高温水中加入300×10-6mol/L的磷酸盐,可使铬镍奥氏体不锈钢抗应力腐蚀性能大大提高。
2、不能得出裂纹扩展速率的变化规律
因为这种传统的方法是以名义应力作为裂纹扩展驱动力的,它不能反映裂纹顶端的应力状态。只有把断裂力 学引入应力腐蚀的研究以后,这一问题才得到解决。
3、费时,且不能用于工程设计
现在对应力腐蚀的研究,都是采用预制裂纹的试样。
防止的措施
1、合理选择材料
针对零件所受的应力和使用条件选用耐应力腐蚀的材料,这是一个基本原则。如铜对氨的应力腐蚀敏感性很 高,因此,接触氨的零件应避免使用铜合金;又如在高浓度氯化物介质中,一般可选用不含镍、铜或仅含微量镍、 铜的低碳高铬铁素体不锈钢,或含硅较高的铬镍不锈钢,也可选用镍基和铁一镍基耐蚀合金。
板式换热器不锈钢板片腐蚀失效原因分析
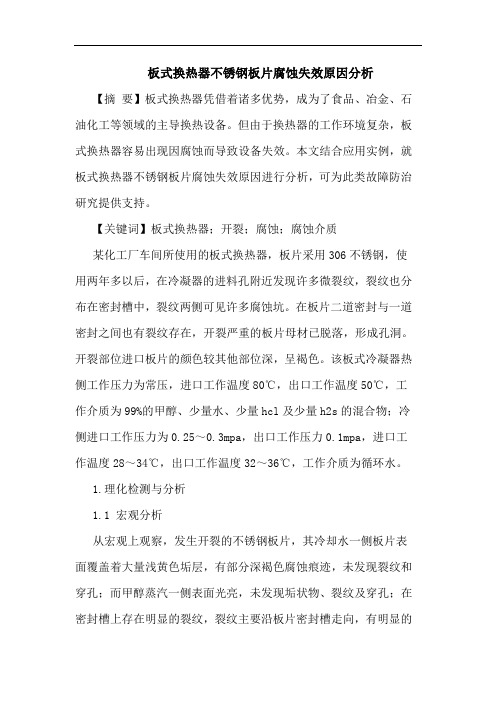
板式换热器不锈钢板片腐蚀失效原因分析【摘要】板式换热器凭借着诸多优势,成为了食品、冶金、石油化工等领域的主导换热设备。
但由于换热器的工作环境复杂,板式换热器容易出现因腐蚀而导致设备失效。
本文结合应用实例,就板式换热器不锈钢板片腐蚀失效原因进行分析,可为此类故障防治研究提供支持。
【关键词】板式换热器;开裂;腐蚀;腐蚀介质某化工厂车间所使用的板式换热器,板片采用306不锈钢,使用两年多以后,在冷凝器的进料孔附近发现许多微裂纹,裂纹也分布在密封槽中,裂纹两侧可见许多腐蚀坑。
在板片二道密封与一道密封之间也有裂纹存在,开裂严重的板片母材已脱落,形成孔洞。
开裂部位进口板片的颜色较其他部位深,呈褐色。
该板式冷凝器热侧工作压力为常压,进口工作温度80℃,出口工作温度50℃,工作介质为99%的甲醇、少量水、少量hcl及少量h2s的混合物;冷侧进口工作压力为0.25~0.3mpa,出口工作压力0.1mpa,进口工作温度28~34℃,出口工作温度32~36℃,工作介质为循环水。
1.理化检测与分析1.1 宏观分析从宏观上观察,发生开裂的不锈钢板片,其冷却水一侧板片表面覆盖着大量浅黄色垢层,有部分深褐色腐蚀痕迹,未发现裂纹和穿孔;而甲醇蒸汽一侧表面光亮,未发现垢状物、裂纹及穿孔;在密封槽上存在明显的裂纹,裂纹主要沿板片密封槽走向,有明显的分叉现象,局部有二次裂纹,裂纹附近没有明显的塑性变形;对裂纹部分取样打磨后发现有点腐蚀存在,腐蚀坑由冷却水侧向甲醇蒸汽侧延伸。
宏观观察表明,换热板片冷却水侧发生点腐蚀,腐蚀源于水侧;板片裂纹具有应力腐蚀的基本特征,这可能与板片密封部位冷冲压成型具有较高的残余应力、冷却水的化学成分、垫片和板片的相互作用等因素有关,需进一步检验。
1.2 微观分析在板片断面用线切割切取试样,用扫描式电子显微镜进行断口微观形貌观察。
发现断口表面覆盖大量的腐蚀产物;断口表面存在泥状花样微观形貌;断口表面呈现出不同位向的晶粒多面体外形的冰糖块状花样,晶粒明显,且观察到沿晶二次裂纹和穿晶二次裂纹;断口表面具有准解理花样,稍有撕裂岭。
应力腐蚀失效及防护措施
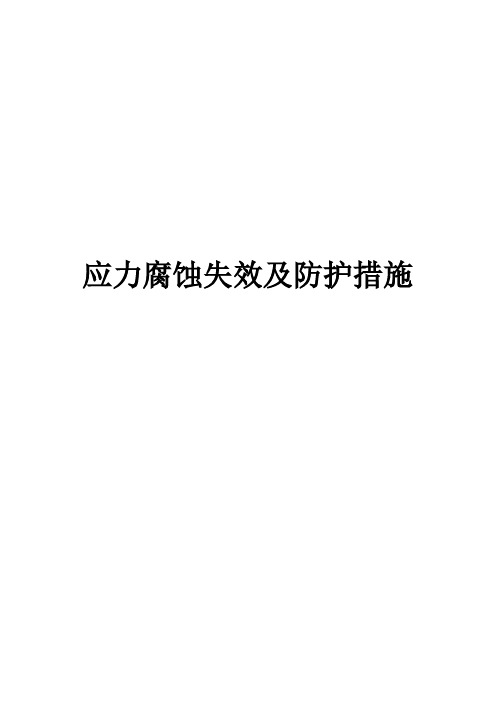
应力腐蚀失效及防护措施1.应力腐蚀失效机理在压力容器的腐蚀失效中,应力腐蚀失效所占的比例高达45 %左右。
因此,研究不锈钢制压力容器的应力腐蚀失效显得尤为重要。
所谓应力腐蚀,就是在拉伸应力和腐蚀介质的联合作用下而引起的低应力脆性断裂。
应力腐蚀一般都是在特定条件下产生:①只有在拉应力的作用下。
②产生应力腐蚀的环境总存在特定的腐蚀介质,不锈钢在含有氧的氯离子的腐蚀介质及H2SO4 、H2S 溶液中才容易发生应力腐蚀。
③一般在合金、碳钢中易发生应力腐蚀。
研究表明,应力腐蚀裂纹的产生主要与氯离子的浓度和温度有关。
压力容器的应力来源:①外载荷引起的容器外表面的拉应力。
②压力容器在制造过程中产生的各种残余应力,如装配过程中产生的装配残余应力,制造过程中产生的焊接残余应力。
在化工生产中,压力容器所接触的介质是多种多样的,很多介质中含有氯离子,在这些条件下,压力容器就发生应力腐蚀失效。
铬镍不锈钢在含有氧的氯离子的水溶液中,首先在金属表面形成了一层氧化膜,它阻止了腐蚀的进行,使不锈钢钝化。
由于压力容器本身的拉应力和保护膜增厚带来的附加应力,使局部地区的保护膜破裂,破裂处的基体金属直接暴露在腐蚀介质中,该处的电极电位比保护膜完整的部分低,形成了微电池的阳极,产生阳极溶解。
因为阳极小、阴极大,所以阳极溶解速度很大,腐蚀到一定程度后,又形成新的保护膜,但在拉应力的作用下又可重新破坏,发生新的阳极溶解。
在这种保护膜反复形成和反复破裂过程中,就会使某些局部地区的腐蚀加深,最后形成孔洞,而孔洞的存在又造成应力集中,更加速了孔洞表面的塑性变形和保护膜的破裂。
这种拉应力与腐蚀介质的共同作用便形成了应力腐蚀裂纹。
2.应力腐蚀失效的防护措施控制应力腐蚀失效的方法,从内因入手,合理选材,从外因入手,控制应力、控制介质或控制电位等。
实际情况千变万化,可按实际情况具体使用。
(1)选用耐应力腐蚀材料近年来发展了多种耐应力腐蚀的不锈钢,主要有高纯奥氏体铬镍钢,高硅奥氏体铬镍钢,高铬铁素体钢和铁素体—奥氏体双相钢。
金属焊接中的应力腐蚀开裂分析与预防
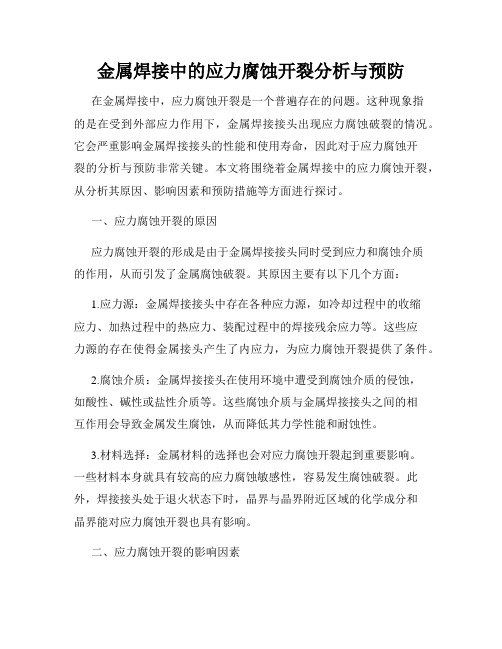
金属焊接中的应力腐蚀开裂分析与预防在金属焊接中,应力腐蚀开裂是一个普遍存在的问题。
这种现象指的是在受到外部应力作用下,金属焊接接头出现应力腐蚀破裂的情况。
它会严重影响金属焊接接头的性能和使用寿命,因此对于应力腐蚀开裂的分析与预防非常关键。
本文将围绕着金属焊接中的应力腐蚀开裂,从分析其原因、影响因素和预防措施等方面进行探讨。
一、应力腐蚀开裂的原因应力腐蚀开裂的形成是由于金属焊接接头同时受到应力和腐蚀介质的作用,从而引发了金属腐蚀破裂。
其原因主要有以下几个方面:1.应力源:金属焊接接头中存在各种应力源,如冷却过程中的收缩应力、加热过程中的热应力、装配过程中的焊接残余应力等。
这些应力源的存在使得金属接头产生了内应力,为应力腐蚀开裂提供了条件。
2.腐蚀介质:金属焊接接头在使用环境中遭受到腐蚀介质的侵蚀,如酸性、碱性或盐性介质等。
这些腐蚀介质与金属焊接接头之间的相互作用会导致金属发生腐蚀,从而降低其力学性能和耐蚀性。
3.材料选择:金属材料的选择也会对应力腐蚀开裂起到重要影响。
一些材料本身就具有较高的应力腐蚀敏感性,容易发生腐蚀破裂。
此外,焊接接头处于退火状态下时,晶界与晶界附近区域的化学成分和晶界能对应力腐蚀开裂也具有影响。
二、应力腐蚀开裂的影响因素除了上述原因外,还有一些其他因素会进一步影响应力腐蚀开裂的产生与发展。
这些因素包括:1.温度:温度是影响应力腐蚀开裂的重要因素之一。
在一定温度范围内,金属的活化能和扩散速率会显著增加,从而加剧金属的腐蚀破裂。
2.应力:外部应力对金属焊接接头的应力腐蚀开裂有着直接影响。
当外部应力超过金属材料的抗应力裂纹扩展能力时,应力腐蚀开裂就会产生。
3.介质浓度:腐蚀介质的浓度对应力腐蚀开裂的发生和发展也起到重要作用。
高浓度的腐蚀介质会加速腐蚀破裂的速度。
三、应力腐蚀开裂的预防措施为了有效预防金属焊接中的应力腐蚀开裂,我们可以采用以下方法:1.材料选择:选择抗应力腐蚀开裂性能良好的金属材料,如高强度合金钢、不锈钢等。
应力腐蚀开裂分析
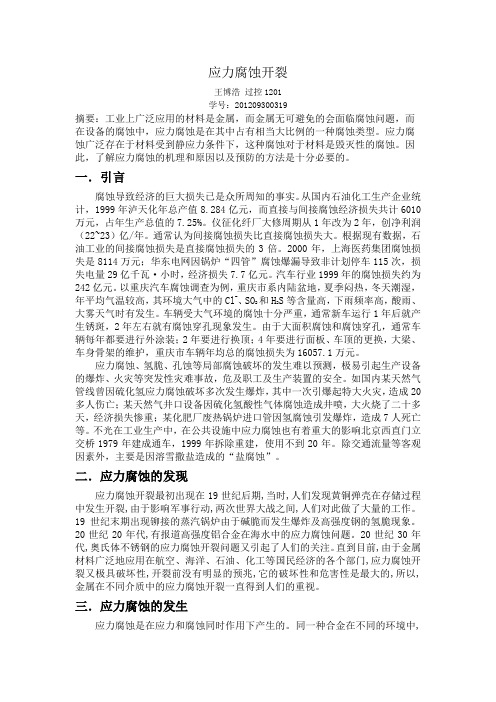
应力腐蚀开裂王博浩过控1201学号:201209300319摘要:工业上广泛应用的材料是金属,而金属无可避免的会面临腐蚀问题,而在设备的腐蚀中,应力腐蚀是在其中占有相当大比例的一种腐蚀类型。
应力腐蚀广泛存在于材料受到静应力条件下,这种腐蚀对于材料是毁灭性的腐蚀。
因此,了解应力腐蚀的机理和原因以及预防的方法是十分必要的。
一.引言腐蚀导致经济的巨大损失已是众所周知的事实。
从国内石油化工生产企业统计,1999年泸天化年总产值8.284亿元,而直接与间接腐蚀经济损失共计6010万元,占年生产总值的7.25%。
仪征化纤厂大修周期从1年改为2年,创净利润(22~23)亿/年。
通常认为间接腐蚀损失比直接腐蚀损失大。
根据现有数据,石油工业的间接腐蚀损失是直接腐蚀损失的3倍。
2000年,上海医药集团腐蚀损失是8114万元;华东电网因锅炉“四管”腐蚀爆漏导致非计划停车115次,损失电量29亿千瓦·小时,经济损失7.7亿元。
汽车行业1999年的腐蚀损失约为242亿元。
以重庆汽车腐蚀调查为例,重庆市系内陆盆地,夏季闷热,冬天潮湿,年平均气温较高,其环境大气中的Cl-、SO2和H2S等含量高,下雨频率高,酸雨、大雾天气时有发生。
车辆受大气环境的腐蚀十分严重,通常新车运行1年后就产生锈斑,2年左右就有腐蚀穿孔现象发生。
由于大面积腐蚀和腐蚀穿孔,通常车辆每年都要进行外涂装;2年要进行换顶;4年要进行面板、车顶的更换,大梁、车身骨架的维护,重庆市车辆年均总的腐蚀损失为16057.1万元。
应力腐蚀、氢脆、孔蚀等局部腐蚀破坏的发生难以预测,极易引起生产设备的爆炸、火灾等突发性灾难事故,危及职工及生产装置的安全。
如国内某天然气管线曾因硫化氢应力腐蚀破坏多次发生爆炸,其中一次引爆起特大火灾,造成20多人伤亡;某天然气井口设备因硫化氢酸性气体腐蚀造成井喷,大火烧了二十多天,经济损失惨重;某化肥厂废热锅炉进口管因氢腐蚀引发爆炸,造成7人死亡等。
- 1、下载文档前请自行甄别文档内容的完整性,平台不提供额外的编辑、内容补充、找答案等附加服务。
- 2、"仅部分预览"的文档,不可在线预览部分如存在完整性等问题,可反馈申请退款(可完整预览的文档不适用该条件!)。
- 3、如文档侵犯您的权益,请联系客服反馈,我们会尽快为您处理(人工客服工作时间:9:00-18:30)。
46 化工装备技术 第32卷第6期2011年12月
0Cr1 8Ni9换热器应力腐蚀开裂失效分析
上官丰收 牛建文 刘强 陈兵
(1.中国石油管工程技术研究院2.中国石油长庆油田)
摘 要某厂锅炉给水预热器在投入使用3.5年后,管箱外壁近横焊缝处发现裂纹。该换热
器设计材质为0Crl8Ni9,截取含有裂纹的试样,进行化学成分分析、金相分析、硬度检测、
拉伸强度测试、裂纹分析和扫描电子显微镜分析。材质Cr元素含量17.75%,硬度306
HV10,这两项检测结果不符合GB/T 4237--2007《不锈钢热轧钢板和钢带》要求;裂纹表
面发现s元素。应力腐蚀是此次失效的主要原因。
关键词换热器0CrlSNi9化学成分硬度应力腐蚀
中图分类号TQ 051.5
Failure Analysis on Stress Corrosion Cracking of
0Crl8Ni9 Heat——exchanger
Shangguan Fengshou Niu Jianwen Liu Qiang Cheng Bing
Abstract:After 3.5 years service,cracks were found on horizontal weld of shell wall of a boiler feed water
preheater.The heat-exchanger was made of 0Crl 8Ni9.Samples containing cracks were cut for chemical composition
analysis,metallographie analysis,hardness testing,tensile testing,cracks analysis and scanning electron microscopy
analysis.Two results didn’t meet the requirement of GB/T 4237—2007——stainless steel hot—rolled steel sheet
and strip,that’S the content of Cr(17.75%)and the hardness 306 HV10;and S element was f0und on the crack
surface.Stress corrosion was the main reason for the failure.
Key words:Heat—exchanger;0Crl SNi9;Chemical composition;Hardness;Stress corrosion
0前言
某厂锅炉给水预热器在投入使用3.5年后,管
箱外壁近横焊缝处发生泄漏,经检测管箱内表面发
现近30条裂纹,设计材质0CrlSNi9。为避免类似
事故发生,对该换热器进行了失效分析。
1 工况
锅炉给水预热器的结构及其裂纹见图1、图2、
图3.设计材质为0Crl8Ni9奥氏体不锈钢。管程
流体B出口 流体A出口
5
1一管板2一壳体3一管束4一法兰5一管箱
图1锅炉预热器结构
¥上官丰收,男,1975年12月生,博士,高级工程师。西安市,710065。
2011年12月 上官丰收等:0Crl8Ni9换热器应力腐蚀开裂失效分析 47
图2管箱内表面近焊缝处裂纹
图3焊缝周围的小裂纹
介质见表1,壳程的介质为锅炉水。管程,进口
280℃,出口176℃,工作压力2.9 MPa;壳程,
进15 102℃,出口190℃,工作压力4.3 MPa。
表1管程介质
2锅炉给水预热器开裂分析
从锅炉给水预热器上截取含有裂纹的试样.进
行化学成分分析、金相分析、硬度检测、拉伸强度 试验、裂纹分析和扫描电子显微镜分析。 2.1化学成分分析 依据标准ASTM A751,采用Baird Spectrovac 2000直读光谱仪和LECO CS一444红外碳硫分析仪 对试样进行化学成分分析,结果见表2。Cr元素含 量仅17.75%,没有达到GB/T 4237--2007《不锈钢 热轧钢板和钢带》要求的18%~20%,化学成分不 合格。 2.2金相组织分析 依据GB/T 13298、GB/T 10561--2005和GB/T 6394--2002.使用MEF3A金相显微镜和MEF4M 金相显微镜对试样进行金相观察分析,见图4和 表3。试样组织为奥氏体,见图4(a),晶粒度 表2化学成分(%) 分析结果 0.059 8.14≤0.001 O.05≤o.001 O.30 G 孑37/8~10.5/ / / / 一 (a)组织 (b)管箱内表面裂纹 (c)微裂纹沿品和穿晶混合形貌 图4金相分析 表3夹杂物分析结果 为6.5。夹杂物分析结果见表3。 2.3硬度测试 依据标准GB/T 4340.1—1999,在HSV一20型
维氏硬度计上沿壁厚方向测量材料硬度。结果依次
显示:297 HV10、307 HV10、305 HV10、290
HVIO 301 HV10 303 HVIO 319 HV10、314
HVIO、318 HV10,平均硬度306HVlO。硬度不符
合标准GB/T 4237--2007的要求≤210 HV。
2.4拉伸强度测试
沿管壁纵向切取标距06.25 ram ̄25 mm的圆
棒拉伸试样,依据标准GB/T 228--2002,室温下
在CMT5105拉伸试验机上进行试验,结果见表4。
拉伸试验结果符合GB厂r 4237--2007。
2.5裂纹分析
对试样进行裂纹分析。腐蚀是非均匀腐蚀,内
表面存在多处裂纹,见图4(b),垂直于表面并呈
化工装备技术 第32卷第6期
表4纵向拉伸试验结果
树枝状分叉。裂纹形貌呈沿晶和穿晶混合特征。见 图4(c),裂纹周围组织无显著区别,仍为奥氏体 组织。 2.6电子显微镜及能谱分析 将含裂纹试样打开,使用TESCAN—VEGA 11型 扫描电子显微镜和OXFORD—INCA350型能谱仪对 裂纹形貌进行分析,结果见图5和表5。断口形貌 显示断面上晶粒轮廓清晰。晶界面较为光滑.呈现 (a)裂纹表面形貌 (b)裂纹断口扩展区形貌 图5电镜分析 表5裂纹上能谱分析结果 典型的“冰糖状”。且裂纹表面有S元素存在。 3分析及讨论 材质组织为奥氏体,正常;硬度较高,超过标 准规定要求。由于锅炉给水预热器工作载荷加上残 余应力的作用,同时材料硬度较大,因此材料的应 力腐蚀敏感性较高。材料未发生均匀腐蚀;裂纹表 面存在S元素,S元素是工作介质带来的。S 一是引
起奥氏体不锈钢应力腐蚀开裂的较敏感介质离子.
介质中如含有微量的S2。.随着使用时间的延长。
S}在一些边角部位会不断积聚变多。最终导致材料
应力腐蚀开裂。
4结论
(1)材质Cr元素含量和硬度不符合GB/T 4237
—
2007《不锈钢热轧钢板和钢带》要求;
(2)裂纹表面发现S元素;
(3)应力腐蚀是此次失效的主要原因。
参考文献
【1】 GB/T 4237—2007.不锈钢热轧钢板和钢带[S】.
『2】 GBfr 13298—1991.金属显微组织检验方法【S】.
『3] GB/T 10561—2005.钢中非金属夹杂物含量的测定[S】.
『4】 GB/T 6394—2002.金属平均晶粒度测定方法[S】.
f5] GB/T 4340.1—1999.金属维氏硬度试验[S】.
f6] GB/T 228—2002.金属材料室温拉伸试验方法【S].
[7】 吴剑.不锈钢的腐蚀破坏与防蚀技术——(四)应力腐
蚀破裂[J1.腐蚀与防护,1997,18(4):38--42.
(收稿日期:2011-07—11)
阿特
阿特拉斯・科普柯在华开建压缩机新工厂 妻萎釜
国无锡正式开工建设其新工厂 以满足中国及其他
亚洲市场对空气压缩机不断增长的需求。阿特拉斯・
科普柯此次投资约1.5亿瑞典克朗(约合1.5亿元人
民币),用于建设包括一家新的压缩机装配工厂、一
间测试实验室和一个研发中心。新工厂和升级后的 现有无锡工厂将大幅提高阿特拉斯在移动压缩机、 工业压缩机、无油压缩机以及压缩机部件上的产能。 “通过此次投资,我们将有能力更好地满足本地 客户的需求,支持整个集团在亚洲地区的业务增 长。”阿特拉斯・科普柯压缩机技术业务领域总裁 Stephan Kuhn表示.“同时,我们将继续提高创新能 中国对压缩机效能日益严格的要求。” 新工厂坐落于无锡新区。距阿特拉斯・科普柯在 无锡现有的工厂约10km.占地面积约45 000 m2。预 计新工厂将于2012年7月投入使用,更好地为建筑 技术和压缩机技术业务领域服务。
阿特拉斯・科普柯是一家在压缩机、膨胀机与空
气处理系统、建筑与采矿设备、动力工具与装配系统
领域占据全球领先地位的工业集团。该集团创立于
1873年,总部位于瑞典的斯德哥尔摩。目前,阿特拉
斯・科普柯在中国拥有超过5 000名员工,分布于国
内13个制造工厂和100多个办事处。 (晓敏)