第三代催化裂化干气制乙苯技术的应用
国内干气法乙苯脱氢制苯乙烯单位产品能耗分析及建议

国内干气法乙苯脱氢制苯乙烯单位产品能耗分析及建议杜建文【摘要】根据国内苯乙烯行业能耗计算标准长期不统一的现状,结合新发布的《苯乙烯单位产品能源消耗限额标准》(GB32053--2015),对国内部分干气法乙苯脱氢制苯乙烯工艺相关装置的设计和实际运行能耗进行了对比,并对苯乙烯单位产品能耗进行了较为系统的分析和研究,结果表明:相关装置能耗均符合苯乙烯单位产品能源消耗限额要求。
针对目前能耗计算标准不统一的现状,提出了计算苯乙烯单位产品能耗的方法,列出了能耗计算的范围和范例。
另外,还针对不同苯乙烯生产装置能耗水平和存在差异化的主要原因进行了阐述,建议在GB32053--2015基础上进一步完善能耗计算指标和方法,如对电能的能耗换算系数进行统一,增加各装置间能耗数值的可比性。
【期刊名称】《石油石化绿色低碳》【年(卷),期】2018(003)001【总页数】6页(P62-67)【关键词】干气法乙苯脱氢;苯乙烯;能耗;分析;建议【作者】杜建文【作者单位】中国石化巴陵石化分公司,湖南岳阳414014;【正文语种】中文【中图分类】TQ241.21苯乙烯是重要的基本有机化工原料,广泛用于生产聚苯乙烯树脂、苯乙烯—丙烯腈共聚物、不饱和聚酯、丁苯橡胶、丁苯胶乳以及苯乙烯系热塑性弹性体等塑料、树脂和合成橡胶产品,其中聚苯乙烯是苯乙烯最重要的应用领域。
此外,苯乙烯还可用于制药、染料、农药及选矿等行业[1]。
目前,工业化苯乙烯生产方法主要有乙苯脱氢法、苯乙烯—环氧丙烷联产法、选择氧化脱氢法、裂解汽油抽提法等,新开发的CO2氧化脱氢制苯乙烯、乙醇直接烃化制苯乙烯等新技术工业应用较少[2]。
其中,乙苯脱氢法产量约占全球总产量的90%,其他技术所产苯乙烯数量约占10%。
催化脱氢法苯乙烯生产工艺主要以国外的Lummus/UOP工艺、Fina/Badger工艺和国内近年来中国石化开发的ST 技术为主;乙苯共氧化法(PO/SM)由Halcon公司开发。
干气制乙苯工艺参数分析
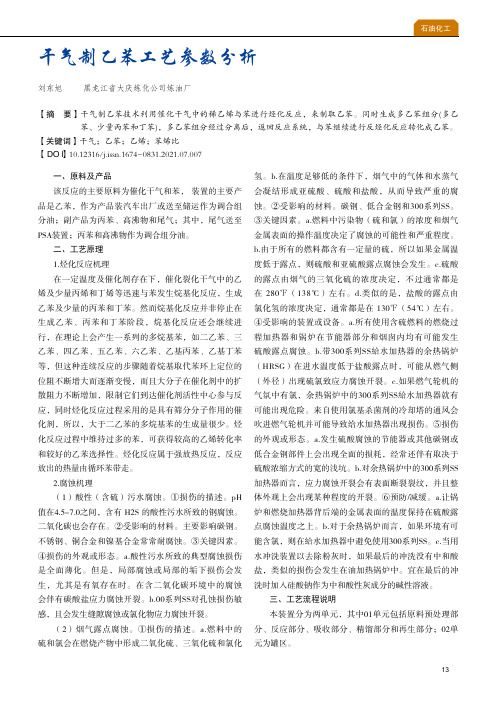
13一、原料及产品该反应的主要原料为催化干气和苯, 装置的主要产品是乙苯,作为产品装汽车出厂或送至储运作为调合组分油;副产品为丙苯、高沸物和尾气;其中,尾气送至PSA装置;丙苯和高沸物作为调合组分油。
二、工艺原理1.烃化反应机理在一定温度及催化剂存在下,催化裂化干气中的乙烯及少量丙烯和丁烯等迅速与苯发生烷基化反应,生成乙苯及少量的丙苯和丁苯。
然而烷基化反应并非停止在生成乙苯、丙苯和丁苯阶段,烷基化反应还会继续进行,在理论上会产生一系列的多烷基苯,如二乙苯、三乙苯、四乙苯、五乙苯、六乙苯、乙基丙苯、乙基丁苯等,但这种连续反应的步骤随着烷基取代苯环上定位的位阻不断增大而逐渐变慢,而且大分子在催化剂中的扩散阻力不断增加,限制它们到达催化剂活性中心参与反应,同时烃化反应过程采用的是具有筛分分子作用的催化剂,所以,大于二乙苯的多烷基苯的生成量很少。
烃化反应过程中维持过多的苯,可获得较高的乙烯转化率和较好的乙苯选择性。
烃化反应属于强放热反应,反应放出的热量由循环苯带走。
2.腐蚀机理(1)酸性(含硫)污水腐蚀。
①损伤的描述。
pH 值在4.5-7.0之间,含有 H2S 的酸性污水所致的钢腐蚀。
二氧化碳也会存在。
②受影响的材料。
主要影响碳钢。
不锈钢、铜合金和镍基合金常常耐腐蚀。
③关键因素。
④损伤的外观或形态。
a.酸性污水所致的典型腐蚀损伤是全面薄化。
但是,局部腐蚀或局部的垢下损伤会发生,尤其是有氧存在时。
在含二氧化碳环境中的腐蚀会伴有碳酸盐应力腐蚀开裂。
b.00系列SS对孔蚀损伤敏感,且会发生缝隙腐蚀或氯化物应力腐蚀开裂。
(2)烟气露点腐蚀。
①损伤的描述。
a.燃料中的硫和氯会在燃烧产物中形成二氧化硫、三氧化硫和氯化氢。
b.在温度足够低的条件下,烟气中的气体和水蒸气会凝结形成亚硫酸、硫酸和盐酸,从而导致严重的腐蚀。
②受影响的材料。
碳钢、低合金钢和300系列SS。
③关键因素。
a.燃料中污染物(硫和氯)的浓度和烟气金属表面的操作温度决定了腐蚀的可能性和严重程度。
炼厂干气利用的现状
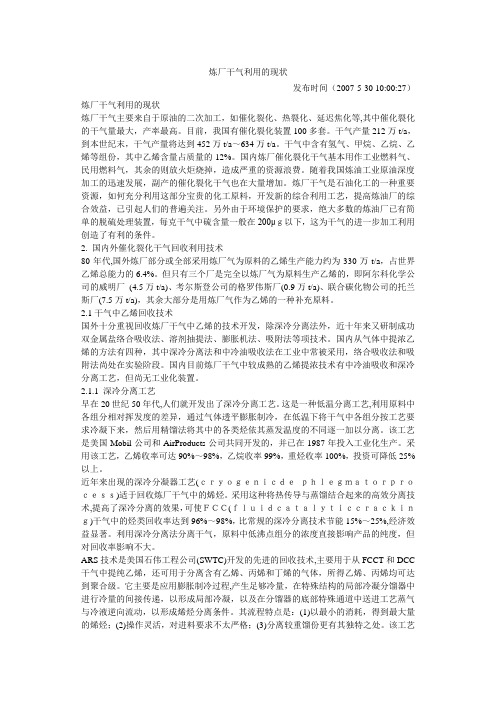
炼厂干气利用的现状发布时间(2007-5-30 10:00:27)炼厂干气利用的现状炼厂干气主要来自于原油的二次加工,如催化裂化、热裂化、延迟焦化等,其中催化裂化的干气量最大,产率最高。
目前,我国有催化裂化装置100多套。
干气产量212万t/a,到本世纪末,干气产量将达到452万t/a~634万t/a。
干气中含有氢气、甲烷、乙烷、乙烯等组份,其中乙烯含量占质量的12%。
国内炼厂催化裂化干气基本用作工业燃料气、民用燃料气,其余的则放火炬烧掉,造成严重的资源浪费。
随着我国炼油工业原油深度加工的迅速发展,副产的催化裂化干气也在大量增加。
炼厂干气是石油化工的一种重要资源,如何充分利用这部分宝贵的化工原料,开发新的综合利用工艺,提高炼油厂的综合效益,已引起人们的普遍关注。
另外由于环境保护的要求,绝大多数的炼油厂已有简单的脱硫处理装置,每克干气中硫含量一般在200μg以下,这为干气的进一步加工利用创造了有利的条件。
2. 国内外催化裂化干气回收利用技术80年代,国外炼厂部分或全部采用炼厂气为原料的乙烯生产能力约为330万t/a,占世界乙烯总能力的6.4%。
但只有三个厂是完全以炼厂气为原料生产乙烯的,即阿尔科化学公司的威明厂(4.5万t/a)、考尔斯登公司的格罗伟斯厂(0.9万t/a)、联合碳化物公司的托兰斯厂(7.5万t/a),其余大部分是用炼厂气作为乙烯的一种补充原料。
2.1干气中乙烯回收技术国外十分重视回收炼厂干气中乙烯的技术开发,除深冷分离法外,近十年来又研制成功双金属盐络合吸收法、溶剂抽提法、膨胀机法、吸附法等项技术。
国内从气体中提浓乙烯的方法有四种,其中深冷分离法和中冷油吸收法在工业中常被采用,络合吸收法和吸附法尚处在实验阶段。
国内目前炼厂干气中较成熟的乙烯提浓技术有中冷油吸收和深冷分离工艺,但尚无工业化装置。
2.1.1 深冷分离工艺早在20世纪50年代,人们就开发出了深冷分离工艺。
这是一种低温分离工艺,利用原料中各组分相对挥发度的差异,通过气体透平膨胀制冷,在低温下将干气中各组分按工艺要求冷凝下来,然后用精馏法将其中的各类烃依其蒸发温度的不同逐一加以分离。
催化裂化(LTAG+MIP)技术工业应用

催化裂化( LTAG+MIP)技术工业应用摘要:某炼化企业新建催化裂化装置,采用LTAG工艺技术,配置有催化柴油加氢改质装置,双反应器共用再生器,主反应器进料为加氢蜡油与低硫渣油混合进料,副反应器进料为加氢后催化柴油。
主反应器采用MIP技术,提升管分第一、第二反应区。
LTAG+MIP技术的应用,多生产高辛烷值汽油组分及化工原料,提高轻油收率,全厂柴汽比降至1以下。
关键词:催化裂化双器柴汽比轻油收率化工原料目前,汽油需求增长缓慢,柴油需求有下降趋势,航空煤油需求保持相对稳定增长,化工原料需求增长迅速,炼油产能过剩,为可持续发展,提高经济效益,需要炼化企业提高轻油收率,减少柴油生产,多生产化工原料。
向“油产化、油转化、油转特”方向发展。
根据公司自身状况,合理利用原有装置流程,选用(LTAG+MIP)技术催化裂化装置,灵活调整产品结构,以适应市场需求。
1装置概况及技术特点某炼化公司新建120×104t/a催化裂化装置,同时配置65×104t/a催化柴油加氢改质装置。
采用中国石化股份有限公司石油化工科学研究院的MIP技术和LTAG技术,以生产高辛烷值低烯烃的汽油、富含丙烯的液化气为主,催化剂为CGP专用催化剂。
再生部分采用单段逆流高效再生技术。
重油沉降器、柴油沉降器、再生器并列式三器布置。
重油提升管加工加氢蜡油与低硫渣油,加工规模80×104t/a。
柴油提升管加工加氢后催化柴油,加工规模40×104t/a。
主副反应器顶反应油气管线合并后进入分馏塔。
主要产出物料有干气、液化气、稳定汽油、柴油、油浆。
简要流程见图1。
图1 反应再生系统简图2原料性质装置3股原料,其中柴油及蜡油2股原料经过加氢处理,渣油原料采用低硫渣油,原料性质提高,大幅降低原料硫含量、多环芳烃、残碳、金属含量等指标,在催化剂及高温条件下尽量向预想方向进行反应,既可达到理想收率,又能提高产品性质。
低硫原料也降低催化装置烟气脱硫设施负担。
211018596_乙苯装置地下污油罐D607_改造及抽出泵P603_负压吸水罐外形设计

或
h2=m(d/D)2×L+(M-1)h1。
(5)
将式(4)、式(5)代入式(1)得:
V=m(Vg+V1)+V3。
(6)
或 ℎ=m[( / ) × + ℎ ] + ℎ 。 (7)
式中:pa —本地大气压,kPa; p1 —水泵正常运行时罐内空气的绝对压强,kPa; pk —水泵正常运行时罐内真空度,kPa; Vg—负压罐吸水管容积,m3; H—水池最低设计水位与吸水管出口间标高差,m; h—负压罐总高度,m; h1、h2、h3—分别与 V1、V2、V3 对应部分的高度,m; L—负压罐吸水管总长度,m; D—负压罐直径,m; d —吸水管管径,m; hω—吸水管总水头损失,kPa; v —吸水管流速,m·s-1; —水的容重,9.8 kN·m-1; g—重力加速度,9.8 m·s-2。
[4] 孙振飞.干气制乙苯装置腐蚀分析与预防[J].中国化工贸易,2021(19): 137-138.
[5] 吴振青.干气制乙苯装置危险性分析和安全设计[J].当代化工研究, 2017(4):105-106.
[6] 姜文源.气压给水技术[M].北京:中国建筑工业出版,1993. [7] 苗田林,王屹,刘家平.负压罐引水装置设计要点[J].工业用水与废水,
ℎ=m[( / ) × + ℎ ] + ℎ =0.82 m;
h/D=1.26。
符合外观要求,且小于泵的允许吸上真空度, 离心泵 P603 可以连续使用,以此为依据进行负压 罐得设计制造即可满足要求。
外形设计结论:负压引水罐的外形为圆柱筒形 结构,对称布置 DN80 进水排水管口各 1 个,高度 0.82 m,直径 0.65 m,底部出口管中心线到罐底高 度 0.15 m,上部入口管中心线至罐顶 0.15 m,罐体 壁厚 6 mm。当然,现场实际并未为依据此数据进行 设计制造,而是购买了机泵厂家的合格产品且为压 力容器,笔者是对其进行核算验证,目前已经将此 设备投入运行,运行良好。
现代催化干气制乙苯技术工艺进展

现代催化干气制乙苯技术工艺进展摘要乙苯作为重要的化工原料之一,主要用途是生产苯乙烯。
全球绝大部分乙苯都是用苯和乙烯通过烃化反应而得,且几乎都是采用纯乙烯作为原料,进而导致了乙烯成本过高。
伴随我国原油消费量逐年增加,年产含有大量乙烯的催化干气却主要作为燃料使用,不仅造成了资源浪费,也对环境造成破坏。
因此,利用催化干气作为原料,使其中的乙烯与苯反应制成乙苯的生产工艺成为迫切需要。
关键词催化干气;稀乙烯;技术工艺;发展前景引言第三代催化干气制乙苯是我国具有自主知识产权的新型工艺,已得到广泛运用。
它是以催化干气中的稀乙烯作为原料,采用气相烷基化和液相烷基转移反应,实现了催化干气中稀乙烯的最大化利用,同时還配套生产国内紧缺的用于合成聚苯乙烯、丁苯橡胶等的苯乙烯产品。
不仅开拓了催化干气利用的新路子,还大大增加了公司的效益,提升公司竞争力[1]。
1 催化干气制乙苯技术工艺过程及发展分析1.1 烃化和反烃化反应原理(1)生成乙苯:C2H4+C6H6=C6H5C2H5在沸石催化剂上存在Lewis酸中心,吸附干气中乙烯分子,再与苯反应生成乙苯。
(2)生成多乙苯:如:C6H5C2H5+ C2H4=C6H4(C2H5)2乙苯进一步烷基化生成二乙苯、三乙苯等。
(3)多乙苯反烃化:C6H4(C2H5)2+ C6H6=2 C6H5C2H5反烃化反应器中,沸石催化剂上存在Lewis酸中心,吸附多乙苯分子,与苯发生烷基转移反应生成乙苯。
(4)生成丙苯和丁苯:C2H6+ C6H6= C6H5C3H7 C4H8+ C6H6=C6H5C4H9干气中含有少量的丙烯和丁烯,在烃化催化剂上与苯发生烷基化反应,生成丙苯和丁苯。
(5)生成甲苯、二甲苯:非芳烃、乙苯和二甲苯生成甲苯;在Lewis酸中心作用下,乙苯能够异构化生成二甲苯。
1.2 工艺发展分析(1)传统A1C13液相法A1C13液相法将A1C13催化剂与苯均成液相反应状态,在反应器中进行烷基化反应,同时二乙苯与苯发生烷基转移反应。
国内干气制乙苯技术研发进展
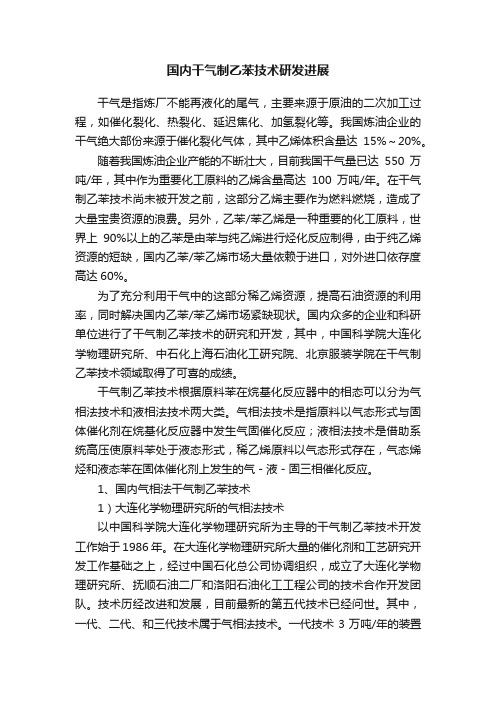
国内干气制乙苯技术研发进展干气是指炼厂不能再液化的尾气,主要来源于原油的二次加工过程,如催化裂化、热裂化、延迟焦化、加氢裂化等。
我国炼油企业的干气绝大部份来源于催化裂化气体,其中乙烯体积含量达15%~20%。
随着我国炼油企业产能的不断壮大,目前我国干气量已达550万吨/年,其中作为重要化工原料的乙烯含量高达100万吨/年。
在干气制乙苯技术尚未被开发之前,这部分乙烯主要作为燃料燃烧,造成了大量宝贵资源的浪费。
另外,乙苯/苯乙烯是一种重要的化工原料,世界上90%以上的乙苯是由苯与纯乙烯进行烃化反应制得,由于纯乙烯资源的短缺,国内乙苯/苯乙烯市场大量依赖于进口,对外进口依存度高达60%。
为了充分利用干气中的这部分稀乙烯资源,提高石油资源的利用率,同时解决国内乙苯/苯乙烯市场紧缺现状。
国内众多的企业和科研单位进行了干气制乙苯技术的研究和开发,其中,中国科学院大连化学物理研究所、中石化上海石油化工研究院、北京服装学院在干气制乙苯技术领域取得了可喜的成绩。
干气制乙苯技术根据原料苯在烷基化反应器中的相态可以分为气相法技术和液相法技术两大类。
气相法技术是指原料以气态形式与固体催化剂在烷基化反应器中发生气固催化反应;液相法技术是借助系统高压使原料苯处于液态形式,稀乙烯原料以气态形式存在,气态烯烃和液态苯在固体催化剂上发生的气-液-固三相催化反应。
1、国内气相法干气制乙苯技术1)大连化学物理研究所的气相法技术以中国科学院大连化学物理研究所为主导的干气制乙苯技术开发工作始于1986年。
在大连化学物理研究所大量的催化剂和工艺研究开发工作基础之上,经过中国石化总公司协调组织,成立了大连化学物理研究所、抚顺石油二厂和洛阳石油化工工程公司的技术合作开发团队。
技术历经改进和发展,目前最新的第五代技术已经问世。
其中,一代、二代、和三代技术属于气相法技术。
一代技术3万吨/年的装置由洛阳石油化工工程公司完成设计,于1993年7月在抚顺石油二厂一次投料开车成功。
炼厂干气中乙烯回收和利用技术进展

炼厂干气中乙烯回收和利用技术进展炼厂干气主要来自原油的二次加工,如催化裂化,热裂化,延迟焦化等,其中催化裂化的干气量最大,产率也最高[1,2]。
干气中含有氢气、氮气、甲烷、乙烯、乙烷等,其中催化裂化干气中乙烯的含量约占15%[3]。
过去因为没有合适的分离回收和综合利用技术,大多数干气当作为燃料气使用或放火炬烧掉,造成了极大的资源浪费和环境污染[4]。
据统计,随着炼油企业的发展,国内催化裂化装置能力已经达到93Mt/a,每年生产的干气产量约为4.14Mt,其中含有乙烯730Kt左右[5]。
若炼厂干气回收轻烃技术能全面推广,每年可以节约用于生产乙烯的轻质油4.15Mt,创造效益上百亿元[6]。
因此,回收利用炼厂干气已经成为炼油企业降低乙烯生产成本和实现资源有效利用的重要手段。
目前,炼厂干气中乙烯回收利用技术分为两大类:一是通过对干气的精制,然后对干气中的乙烯进行浓缩,最后通过分离回收得到聚合级的乙烯;二是用干气作为原料,利用其中的稀乙烯,直接生产乙苯、环氧乙烷、丙醛等。
本文重点对国内外回收利用干气技术进行了综述。
1 炼厂干气中乙烯分离回收技术从炼厂干气中提取乙烯的技术主要有深冷分离法、吸收分离法、水合物分离法、吸附分离法和膜分离法等。
其中水合物分离法是新出现的分离方法,膜分离法正处于实验室阶段或工业试验阶段,而深冷分离法,吸收分离法和吸附分离法已经成熟并实现工业化[7]。
下面分别做以介绍。
1.1深冷分离法深冷分离法是一种已经相当成熟的技术。
早在20世纪50年代,人们就开发了常规深冷分离技术[8,9,10]。
该方法是一种低温的分离工艺,利用原料中各个组分的相对挥发度的不同,通过气体透平膨胀制冷,在低温下将干气中各个组分按工艺要求冷凝下来,然后利用精馏法将其中的各类烃按照蒸发温度的不同逐一进行分离。
但由于常规深冷分离工艺能耗大,人们不断对其进行改进,最突出的是利用分凝分馏器进行分离。
分凝分馏器是美国空气产品公司的设计专利;九十年代初,美国Stone&Webster 公司将其应用于烃气分离工艺中,形成了以分凝分馏器为核心的第一代ARS (Advanced Recovery System)技术[11]。
- 1、下载文档前请自行甄别文档内容的完整性,平台不提供额外的编辑、内容补充、找答案等附加服务。
- 2、"仅部分预览"的文档,不可在线预览部分如存在完整性等问题,可反馈申请退款(可完整预览的文档不适用该条件!)。
- 3、如文档侵犯您的权益,请联系客服反馈,我们会尽快为您处理(人工客服工作时间:9:00-18:30)。
矿产资源开发利用方案编写内容要求及审查大纲
矿产资源开发利用方案编写内容要求及《矿产资源开发利用方案》审查大纲一、概述
㈠矿区位置、隶属关系和企业性质。
如为改扩建矿山, 应说明矿山现状、
特点及存在的主要问题。
㈡编制依据
(1简述项目前期工作进展情况及与有关方面对项目的意向性协议情况。
(2 列出开发利用方案编制所依据的主要基础性资料的名称。
如经储量管理部门认定的矿区地质勘探报告、选矿试验报告、加工利用试验报告、工程地质初评资料、矿区水文资料和供水资料等。
对改、扩建矿山应有生产实际资料, 如矿山总平面现状图、矿床开拓系统图、采场现状图和主要采选设备清单等。
二、矿产品需求现状和预测
㈠该矿产在国内需求情况和市场供应情况
1、矿产品现状及加工利用趋向。
2、国内近、远期的需求量及主要销向预测。
㈡产品价格分析
1、国内矿产品价格现状。
2、矿产品价格稳定性及变化趋势。
三、矿产资源概况
㈠矿区总体概况
1、矿区总体规划情况。
2、矿区矿产资源概况。
3、该设计与矿区总体开发的关系。
㈡该设计项目的资源概况
1、矿床地质及构造特征。
2、矿床开采技术条件及水文地质条件。