锻造操作机的可视化刚体动力学仿真
机械系统的动力学建模与仿真分析

机械系统的动力学建模与仿真分析一、引言机械系统是由多个相互作用的部件组成的复杂系统,其动力学行为是研究的核心问题之一。
动力学建模与仿真分析可以帮助工程师深入理解机械系统的运动规律,预测系统的性能,并优化设计。
本文将介绍机械系统的动力学建模方法以及仿真分析技术。
二、动力学建模1. 基本原理机械系统的动力学建模是基于牛顿力学的基本原理进行的。
通过分析受力、受力矩以及质量、惯性等因素,可以建立机械系统的运动方程。
在建立方程时,需要考虑系统的自由度、刚体或者弹性体的运动特性以及约束条件等因素。
2. 运动学建模运动学建模是机械系统动力学建模的前提。
通过研究机械系统的几何结构和运动规律,可以得到系统的等效长度、转动角度等信息。
基于运动学建模,可以计算系统的速度、加速度以及运动的轨迹等。
3. 动力学建模动力学建模是机械系统分析的核心部分。
基于受力和受力矩的平衡条件,可以建立机械系统的运动方程。
通常采用牛顿第二定律和力矩平衡条件,可以得到刚体的平动和旋转方程。
对于复杂的非线性系统,也可以采用拉格朗日方程或者哈密顿原理进行建模。
三、仿真分析1. 数值解算方法为了求解机械系统的运动方程,需要采用适当的数值解算方法。
常见的方法包括欧拉法、龙格-库塔法、变步长积分法等。
这些方法可以将微分方程离散化,然后通过迭代计算求解系统的状态变量。
2. 动力学仿真动力学仿真是建立在动力学模型的基础上。
通过将模型转化成计算机程序,可以在计算机上模拟机械系统的运动行为。
通过仿真分析,可以研究系统的稳定性、动态响应以及力学性能等。
3. 优化设计动力学仿真还可以应用于优化设计。
通过改变系统参数、构型和控制策略等,可以研究不同设计方案的性能差异,并选择最佳方案。
通过仿真分析,可以避免实际试验的成本和时间消耗。
四、案例分析以汽车悬挂系统为例,进行动力学建模与仿真分析。
汽车悬挂系统是一个典型的机械系统,包含减震器、弹簧、悬挂臂等部件。
首先进行运动学建模,分析车轮的运动状态和轨迹。
机械系统动力学建模中的模型仿真方法研究

机械系统动力学建模中的模型仿真方法研究在现代机械工程领域,机械系统动力学建模与仿真成为了设计、分析和优化复杂机械系统的重要手段。
通过对机械系统的动力学行为进行准确建模和仿真,可以提前预测系统的性能,减少试验次数,缩短研发周期,降低成本,并提高产品的质量和可靠性。
机械系统动力学建模是对机械系统的运动和力的关系进行数学描述的过程。
这一过程需要考虑系统的结构、约束、驱动力、摩擦力等多种因素。
模型的准确性直接影响到仿真结果的可靠性,因此建模过程需要对机械系统的物理特性有深入的理解,并选择合适的数学模型和建模方法。
在机械系统动力学建模中,常见的模型类型包括刚体模型、柔体模型和多体系统模型。
刚体模型假设物体在运动过程中不发生变形,适用于对简单机械系统的初步分析。
柔体模型则考虑了物体的弹性变形,适用于对具有较大变形的部件进行分析。
多体系统模型将机械系统视为由多个相互连接的刚体或柔体组成,可以更全面地描述复杂机械系统的运动。
模型仿真方法是实现机械系统动力学分析的关键步骤。
有限元法是一种广泛应用的仿真方法,它将连续的物体离散化为有限个单元,通过求解单元节点的位移和应力来得到物体的整体响应。
有限元法在处理复杂的几何形状和边界条件时具有优势,但计算量较大,对于大规模的机械系统仿真可能需要较长的计算时间。
另一种常用的仿真方法是多体动力学仿真。
它基于拉格朗日方程或牛顿欧拉方程,通过建立系统的运动方程来求解系统的运动轨迹和受力情况。
多体动力学仿真能够有效地处理多自由度的机械系统,并且计算效率相对较高。
在进行机械系统动力学模型仿真时,首先需要确定模型的边界条件和初始条件。
边界条件包括约束、载荷和接触等,初始条件则包括物体的初始位置、速度和加速度等。
这些条件的准确设定对于仿真结果的准确性至关重要。
同时,模型的参数识别也是一个重要环节。
模型中的参数,如质量、转动惯量、刚度和阻尼等,需要通过实验测量或理论计算来确定。
参数的准确性直接影响到模型的精度和仿真结果的可靠性。
机械系统的动力学建模与仿真分析
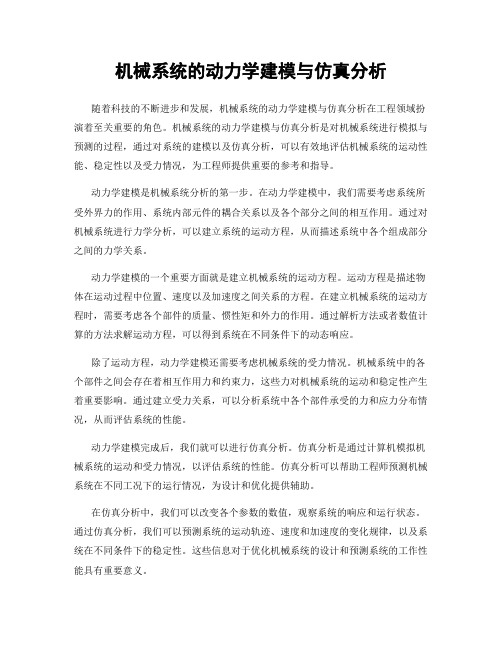
机械系统的动力学建模与仿真分析随着科技的不断进步和发展,机械系统的动力学建模与仿真分析在工程领域扮演着至关重要的角色。
机械系统的动力学建模与仿真分析是对机械系统进行模拟与预测的过程,通过对系统的建模以及仿真分析,可以有效地评估机械系统的运动性能、稳定性以及受力情况,为工程师提供重要的参考和指导。
动力学建模是机械系统分析的第一步。
在动力学建模中,我们需要考虑系统所受外界力的作用、系统内部元件的耦合关系以及各个部分之间的相互作用。
通过对机械系统进行力学分析,可以建立系统的运动方程,从而描述系统中各个组成部分之间的力学关系。
动力学建模的一个重要方面就是建立机械系统的运动方程。
运动方程是描述物体在运动过程中位置、速度以及加速度之间关系的方程。
在建立机械系统的运动方程时,需要考虑各个部件的质量、惯性矩和外力的作用。
通过解析方法或者数值计算的方法求解运动方程,可以得到系统在不同条件下的动态响应。
除了运动方程,动力学建模还需要考虑机械系统的受力情况。
机械系统中的各个部件之间会存在着相互作用力和约束力,这些力对机械系统的运动和稳定性产生着重要影响。
通过建立受力关系,可以分析系统中各个部件承受的力和应力分布情况,从而评估系统的性能。
动力学建模完成后,我们就可以进行仿真分析。
仿真分析是通过计算机模拟机械系统的运动和受力情况,以评估系统的性能。
仿真分析可以帮助工程师预测机械系统在不同工况下的运行情况,为设计和优化提供辅助。
在仿真分析中,我们可以改变各个参数的数值,观察系统的响应和运行状态。
通过仿真分析,我们可以预测系统的运动轨迹、速度和加速度的变化规律,以及系统在不同条件下的稳定性。
这些信息对于优化机械系统的设计和预测系统的工作性能具有重要意义。
虽然动力学建模与仿真分析在机械工程中具有重要的地位,但是这一过程并不是一蹴而就的。
动力学建模与仿真分析需要工程师具备扎实的理论基础和工程经验,同时还需要熟练掌握相应的计算软件和数值方法。
机械系统动力学建模与仿真

机械系统动力学建模与仿真机械工程是一门应用科学,涉及设计、制造、分析和维护各种机械设备和系统的原理与方法。
在机械工程领域中,机械系统动力学建模与仿真是一项重要的技术,它可以帮助工程师们更好地理解和预测机械系统的运行行为,从而提高设计和制造的效率。
机械系统动力学建模是将机械系统的结构和运动特性抽象为数学模型的过程。
在建模过程中,工程师需要考虑系统的物理特性、运动学关系、力学原理等因素,以及系统中各个组件之间的相互作用。
通过建立准确的数学模型,工程师可以深入研究系统的运动规律和响应特性,为系统设计和性能优化提供理论依据。
机械系统动力学仿真是基于建立的数学模型,利用计算机技术进行系统行为模拟和预测的过程。
仿真可以模拟系统在不同工况下的运动状态、力学响应和能量传递等行为,帮助工程师们更好地理解系统的性能和行为特点。
通过仿真,工程师可以进行多种设计方案的比较和优化,减少试错成本,提高工程效率。
机械系统动力学建模与仿真在许多领域都有广泛的应用。
例如,在汽车工程中,工程师可以建立车辆悬挂系统的动力学模型,并通过仿真分析不同路况下的车辆运动行为,以优化悬挂系统的设计。
在航空航天工程中,工程师可以建立飞行器的动力学模型,并通过仿真评估飞行器的稳定性和控制性能。
在机械制造领域,工程师可以建立机床的动力学模型,并通过仿真分析机床的运动特性,以提高加工精度和生产效率。
机械系统动力学建模与仿真的发展离不开计算机技术的支持。
随着计算机计算能力的不断提高和仿真软件的不断发展,工程师们可以更加方便地进行复杂系统的建模和仿真。
同时,计算机技术的发展也为机械系统动力学建模与仿真提供了更多的应用场景,例如虚拟现实技术的应用可以实现对机械系统的虚拟仿真,加快设计和验证的过程。
总之,机械系统动力学建模与仿真是机械工程领域中一项重要的技术。
通过建立准确的数学模型和进行系统行为的仿真分析,工程师们可以更好地理解和预测机械系统的运行行为,从而提高设计和制造的效率。
机械系统动力学模拟与仿真

机械系统动力学模拟与仿真在现代工程学中,机械系统动力学模拟与仿真是一个被广泛研究和应用的领域。
它可以帮助工程师和科学家更好地理解机械系统的运动特性,并通过模拟和仿真来优化设计和改进系统性能。
一、动力学模拟的基本概念动力学模拟是指通过数学建模和计算机仿真,研究机械系统在各种外部力和运动约束下的运动规律。
它需要考虑到系统的质量、惯性、摩擦、弹性等因素,并建立相应的数学模型来描述系统行为。
例如,在研究机械臂的运动时,我们可以将其抽象为刚性杆件的组合,并根据运动学关系、惯性和动力学定律来建立机械臂的数学模型。
通过数值计算和仿真,可以预测机械臂在给定外部力作用下的运动轨迹、速度和加速度等参数。
二、动力学模拟的应用领域动力学模拟在多个领域都有广泛应用。
其中,机械制造、航空航天和汽车工业是其中的主要应用领域之一。
在机械制造领域,动力学模拟可以用于评估机械系统的性能和稳定性。
例如,在机床设计中,通过模拟机床结构和切削过程,可以预测机床的振动和变形情况,以便减少切削误差并提高精度。
在航空航天领域,动力学模拟被广泛应用于飞行器设计和控制。
通过模拟飞行器的运动和空气动力学特性,可以优化飞行器的设计,提高其操纵性和稳定性。
在汽车工业中,动力学模拟可以用于研究汽车的悬挂系统、转向系统和刹车系统等。
通过模拟和仿真,可以提高汽车的操控性和安全性,并减少对试验样车的依赖。
三、动力学仿真软件的发展为了方便工程师和科学家进行动力学模拟和仿真,许多动力学仿真软件已经开发出来。
这些软件可以提供直观的用户界面和强大的计算功能,使用户能够快速建立模型、设置仿真参数并进行仿真计算。
例如,ADAMS(Automatic Dynamic Analysis of Mechanical Systems)是一种广泛使用的动力学仿真软件,它可以用于模拟机械系统的多体动力学行为。
通过ADAMS,用户可以轻松地建立机械系统模型,并通过各种分析和优化工具来改进系统的性能。
刚体动力学仿真在机器人设计中的应用

刚体动力学仿真在机器人设计中的应用随着科技的发展,机器人设计已经成为了当今最为热门的领域之一。
从工业机器人到医疗机器人,从适用于家庭的机器人到可用于军事行动的机器人,它们的用途越来越广泛。
然而,在机器人设计中,刚体动力学仿真已经成为一种不可或缺的工具。
本文将重点讨论刚体动力学仿真在机器人设计中的应用。
一、机器人设计中的刚体动力学仿真刚体动力学仿真是指以机械刚体为对象,利用物理学原理,通过计算机仿真技术对机械系统进行动力学分析的过程。
刚体动力学仿真在机器人设计过程中被广泛应用,因为它可以预测机器人在运动过程中的表现,避免因设计不足导致机器人性能不佳、稳定性差等问题。
刚体动力学模拟软件可用于仿真运动学和动力学特性,例如速度、加速度、力和扭矩等特性。
利用这些软件,机器人设计人员可以模拟机器人在执行任务时的行为,并验证机器人的设计性能,尤其是在复杂的任务中。
此外,刚体动力学仿真还可以帮助机器人设计人员识别机器人在模拟过程中可能出现的问题,并提供解决方案。
二、刚体动力学仿真在机器人设计中的具体应用1. 运动学刚体动力学仿真软件可以帮助机器人设计人员确定机器人的轨迹和姿态。
轨迹和姿态是机器人进行各种任务的基础,因此,明确这些参数非常重要。
机器人设计人员通常使用仿真软件来虚拟机器人的轨迹和姿态,并更改设计参数以优化机器人性能。
2. 动力学刚体动力学仿真软件可以模拟机器人在运动过程中的各种动态特性,例如重心位置、惯性矩、力和扭矩的分布等等。
这些参数可以帮助机器人设计人员更好地了解机器人的动态行为,从而优化机器人的设计。
3. 碰撞力学因为机器人在执行任务时可能会发生碰撞,因此在机器人设计和仿真阶段,需要考虑碰撞的影响。
刚体动力学仿真软件可用于模拟机器人的碰撞力学,并优化机器人的结构,以提高机器人的抗碰撞能力。
4. 控制算法机器人的智能控制算法对机器人的性能和稳定性至关重要。
机器人设计人员可以使用刚体动力学仿真软件,通过模拟各种场景和任务,优化机器人的控制算法,确保机器人在执行任务时表现良好。
机械系统动力学建模与仿真分析

机械系统动力学建模与仿真分析引言机械系统是现代工业中的重要组成部分,其动力学行为的建模和仿真分析对于系统设计、性能优化以及故障诊断起着关键作用。
本文将介绍机械系统动力学建模与仿真分析的基本概念和方法,并讨论其在实际工程中的应用。
一、机械系统的动力学建模机械系统的动力学建模是将复杂的物理过程抽象为数学模型的过程。
在建模过程中,我们需要考虑系统的结构、力学特性和工作条件等因素。
一般而言,机械系统的动力学建模可以分为两个层次:单体建模和系统建模。
1. 单体建模单体建模是将机械系统划分为若干个简化的单元,并对每个单元进行建模。
这些单元可以是机械元件(如齿轮、轴承)、机构(如齿轮传动、减速器)或者整个机器人等。
在建立单体模型时,我们需要考虑物体的质量、惯性、刚度和阻尼等因素,并利用牛顿运动定律和能量守恒原理进行建模。
2. 系统建模系统建模是将单体模型组合起来,构建整个机械系统的数学模型。
在系统建模中,我们需要考虑各个单体之间的相互作用,并确保整个系统的动力学特性的一致性。
此外,还需要考虑外部激励(如传感器反馈、控制器输入等)对系统的影响。
二、机械系统的动力学仿真机械系统的动力学仿真是在建立完整的数学模型之后,利用计算机软件对系统进行模拟的过程。
通过仿真分析,我们可以预测系统的运动轨迹、力学响应和能量传递等动力学行为。
常用的机械系统仿真方法包括基于方程求解的解析仿真和基于数值计算的数值仿真。
1. 解析仿真解析仿真是通过求解系统的动力学方程,得到系统在各个时刻的状态变量。
这种方法的优点是能够获得系统的精确解,但在复杂系统中,由于方程求解的复杂性,可能会出现求解困难的情况。
因此,解析仿真一般适用于简单的机械系统或者特定的研究问题。
2. 数值仿真数值仿真是通过将系统的动力学方程转化为差分或者微分方程的形式,并利用计算机进行数值求解。
这种方法的优点是能够处理复杂的非线性和时变系统,并能够模拟系统的长时间行为。
目前,常用的数值仿真软件有MATLAB/Simulink、ADAMS和ANSYS等。
机械系统的多体动力学分析与仿真
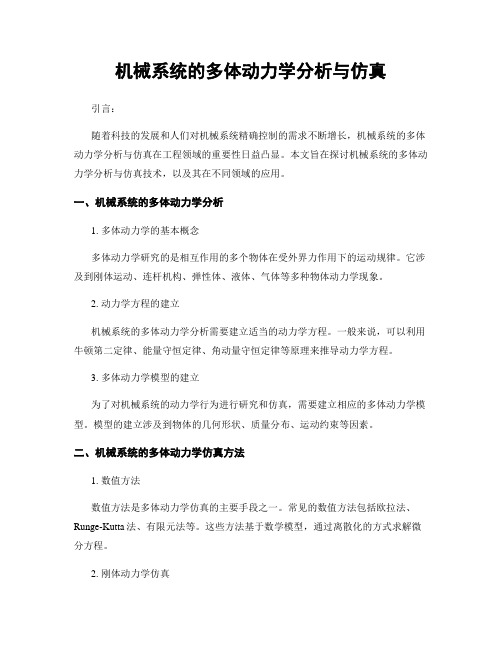
机械系统的多体动力学分析与仿真引言:随着科技的发展和人们对机械系统精确控制的需求不断增长,机械系统的多体动力学分析与仿真在工程领域的重要性日益凸显。
本文旨在探讨机械系统的多体动力学分析与仿真技术,以及其在不同领域的应用。
一、机械系统的多体动力学分析1. 多体动力学的基本概念多体动力学研究的是相互作用的多个物体在受外界力作用下的运动规律。
它涉及到刚体运动、连杆机构、弹性体、液体、气体等多种物体动力学现象。
2. 动力学方程的建立机械系统的多体动力学分析需要建立适当的动力学方程。
一般来说,可以利用牛顿第二定律、能量守恒定律、角动量守恒定律等原理来推导动力学方程。
3. 多体动力学模型的建立为了对机械系统的动力学行为进行研究和仿真,需要建立相应的多体动力学模型。
模型的建立涉及到物体的几何形状、质量分布、运动约束等因素。
二、机械系统的多体动力学仿真方法1. 数值方法数值方法是多体动力学仿真的主要手段之一。
常见的数值方法包括欧拉法、Runge-Kutta法、有限元法等。
这些方法基于数学模型,通过离散化的方式求解微分方程。
2. 刚体动力学仿真刚体动力学仿真是多体动力学仿真的重要方向之一。
它考虑了物体的质心运动、角速度和角加速度等因素,可以用于模拟机械系统中刚体的运动特性。
3. 柔性体动力学仿真柔性体动力学仿真是另一种常用的多体动力学仿真方法。
相比于刚体仿真,柔性体仿真考虑了物体的变形和挠曲等因素,更加逼真地模拟了机械系统的实际行为。
三、机械系统多体动力学分析与仿真的应用1. 机械设计与优化通过多体动力学分析与仿真,可以评估机械系统在不同工况下的稳定性、刚度和振动特性等,提供设计师有效的指导,优化机械系统的结构和参数。
2. 机器人动力学控制机器人是机械系统的重要应用领域之一。
多体动力学分析与仿真可以帮助研究人员分析和优化机器人的动力学性能,设计出更加灵活、高效的机器人控制算法。
3. 车辆动力学研究车辆动力学是研究车辆运动规律与性能的重要领域。
- 1、下载文档前请自行甄别文档内容的完整性,平台不提供额外的编辑、内容补充、找答案等附加服务。
- 2、"仅部分预览"的文档,不可在线预览部分如存在完整性等问题,可反馈申请退款(可完整预览的文档不适用该条件!)。
- 3、如文档侵犯您的权益,请联系客服反馈,我们会尽快为您处理(人工客服工作时间:9:00-18:30)。
基金项目国家自然科学基金资助项目()作者简介任云鹏(),男,高级工程师,博士生2y3@6锻造操作机的可视化刚体动力学仿真任云鹏1,2,张天侠1(1.东北大学机械工程与自动化学院,辽宁沈阳 110004;2.北方重工沈重集团有限责任公司研究院,辽宁沈阳 110025)摘要:在分析锻造操作机工作原理的基础上,采用ADAMS软件平台,建立锻造操作机的可视化三维数字化模型.考虑锻造操作机自重和外负载影响,对操作机各个部件施加相应的约束和载荷,然后进行多刚体系统的动力学三维可视化仿真,得到了典型工况运动过程中操作机受力的变化情况,并对极限载荷情况进行分析.仿真结果为锻造操作机的零部件合理设计提供了参考依据.关键词:锻造操作机;可视化方法;动力学仿真中图分类号:TP391.9;TB122 文献标识码:A 文章编号:1672-5581(2008)02-0127-06Rigid2dynamics2basedvisualizedsimulationonforgingmanipulatorsRENYun2peng1,2,ZHANGTian2xia1(1.SchoolofMechanicalEngineeringandAutomation,NortheasternUniversity,Shenyang,China;2.ResearchandDesignInstitute,NorthernHearyIndustriesShenyangHeavyMachineryGroupCo.Ltd,Shenyang,China)Abstract:Basedontheworkingprinciplesofforgingmanipulators,a3DvisualizeddigitalmodelisdevelopedusingMSC.ADAMSTMplatform.Pertainingtotheinherentgravityandimpactingloadofmanipulators,rele2vantconstraintsandloadsareappliedforcomponentsofforgingmanipulators.Afterwards,a3Dvisualizedsim2ulationisconducteduponamultiple2rigid2bodysystem.Then,themotionalforces,togetherwithboundaryloads,aredetectedandanalyzedintermsoftypicalconditions.Asaconsequence,thesimulationresultshaveprovidedcriticalspecificationsforembodimentdesignofforgingmanipulators.Keywords:forgingmanipulator;visualizedtechnique;dynamicssimulation 锻造操作机是万吨水压锻造机的主要配套设备,与加工设备协调作业,可以大大提高制造能力、制造精度、生产效率和材料利用率,并降低能耗.目前世界上著名的生产锻造操作机的公司主要有德国的SMS公司,DDS公司,捷克的ZDAS公司等[1].我国在大型锻造操作机装备方面相对薄弱,影响了大型复杂构件的制造能力.由于国内外市场的巨大需求,锻造操作机研究也不断发展,对掌握核心技术,提高特大型自由锻件的制造技术水平与制造能力起着关键性的作用[2].由于大型锻造操作机通常无法在物理样机的基础上进行实验并对其操作性能进行分析和验证,这就要求运用高效、高保真的可视化虚拟样机技术为锻压操作机的设计、性能评估与优化提供支持[3].机器设备具有良好的动力学特性是其可靠工作最有效的保证,动力学可视化就是用可视化的方法研究所设计的机械产品动态特性,使产品在未制造出前就能保证具有良好的性能和相应的工作寿命要求.建立可视化三维模型,在产品实际制造之前对产品的性能、行为、功能进行分析和评估,从而对设计方案进行检验与优化,达到产品制造的最优目标[4].目前国际上有一些较成熟的动力学仿真软件,如MSC.ADAMS软件,在第6卷第2期2008年6月中 国 工 程 机 械 学 报CHINESEJOURNALOFCONSTRUCTIONMACHINERYVol.6No.2 Jun.2008:10402008:1974-.Email:renunpeng91012.com机械系统动力学仿真分析方面得到广泛的应用[5].为保证锻造操作机安全可靠的工作,在设计的过程中必须考虑该操作机的动态性能.本文采用可视优化设计方法对锻造操作机动态性能进行了仿真分析,主要研究包括操作机整机系统动力学理论分析、操作机整机三维可视化模型的创建、刚体运动仿真以及仿真结果的分析与评价等.本文在确定锻造操作机的基本结构形式后[6],对机构方案进行详细的动态仿真和论证,计算不同工况时操作机机构在刚体运动过程中主要构件的受力状况,以此作为零部件结构强度设计的基础.
1 基于可视化方法的动力学分析的基本思想动力学可视化的研究目标就是通过仿真确定机械载荷分布情况、机械产品的主要动态特性及仿真在给定激励下的响应情况,从而可使产品在设计阶段就能保证拥有优异的结构性能.动力学可视化仿真重点研究以下3方面内容:
图1 动力学可视化仿真技术流程Fig.1 Visualizationdynamicssimulationtechnologyflow
(1)通过可视化仿真,确定载荷分布情况及进行强度验
证.在强度计算上,传统设计只考虑静态特性而忽略动态特性或乘以相应系数加以修正,这种设计方式导致设计出的产品结构可靠性不高.实际上,锻造操作机在工作中一直受到动载荷的作用,所以进行强度计算时必须考虑动态性能.动力学可视化是在充分考虑了各种动载荷而进行仿真研究的.进行动力学可视化仿真,要加入各种动态特性,通过仿真可非常直观地了解在工作过程或其他特殊情况下,载荷的分布情况,从而可确定结构的薄弱环节,进行强度校核.(2)通过动力学可视化仿真确定锻造操作机零部件的
固有动态特性.机械产品的固有频率及振型等特性对整个结构的动态特性有着显著的影响,因此获得所设计产品的固有动态特性对于优化产品的结构性能有着重要的意义.通过动力学可视化仿真可获得结构的各阶模态参数及振型图,尤其对于结构复杂的动力学系统,动力学可视化仿真与数值计算相比有着绝对的技术优势.(3)仿真确定在给定激励下的响应情况.在锻造操作机
未被制造出前,获知所设计的产品在给定激励下的响应情况也是非常有意义的.通过可视化仿真可在人为设定激励的形式、频率及幅度的情况下,检验响应是否在规定的范围内,或响应是否达到要求,这直接决定了机械产品的使用性能.动力学可视化仿真可按图1所示的流程进行.
2 锻造操作机的三维可视化模型建立锻造操作机的主要运动包括钳杆上下倾斜、上下平移、左右倾斜、左右平移,以及钳杆旋转、钳口开闭、大车行走等[7~9].这里以钳杆上下倾斜、上下平移2种运动工况为例进行说明,实现上下倾斜、上下平移运动的平行连杆式操作机机构简图如图2.如图2所示,构件①(即AB)为上升平移液压缸,当AB伸长时,能间接地推动钳杆⑧平稳上升;构件②(即BDG)为前推臂,其一外伸出端铰接在机架上;构件③(即DF)为吊杆,由部分组成,上吊杆悬挂在前推臂上,下吊杆用来悬吊钳杆;构件④(即M)为缓冲缸,当钳杆向上平移时,缓冲缸起缓冲作用,使钳口能竖直上升;构件⑤(即IN)为后推臂,其外部伸出端铰接在机架上;构件⑥(即G)为连杆,连821 中 国 工 程 机 械 学 报第6卷 CE2EHH接前推臂和后推臂;构件⑦(即NK)为上下摆动液压缸,能实现钳杆的上下摆动.由Solidworks建立的三维实体零部件模型,采用Parasolid标准文件,在ADAMS中导入整个样机装配体模型.模型导入ADAMS后,利用添加到地基形体的标记点,准确而快捷地建立活动框模型,形成虚拟样机的装配体模型,如图3所示.
图2 平行连杆式锻造操作机机构简图Fig.2 Parallel2linkmechanismofaforgingmanipulator图3 锻造操作机虚拟样机模型Fig.3 Virtualprototypemodelofaforgingmanipulator
根据基本工况添加运动约束如下:5个液压缸缸体和活塞之间添加5个移动副,其中2个液压缸与地之间添加2个转动副,前后推臂与地之间添加4个转动副,前后推臂与2个连杆之间添加4个转动副,前推臂与2个液压缸之间添加2个转动副,前推臂与地之间对中杆之间添加1个转动副,对中杆与吊杆之间添加2个转动副,吊杆与横向的2个液压缸的活塞之间添加2个转动副,吊杆与钳头之间添加2个转动副,钳头与上下摆动的液压缸的活塞之间添加1个转动副,上下摆动的液压缸的缸体与后推臂之间添加1个转动副,横向的2个液压缸的缸体和后支臂之间添加2个转动副,后支臂与地之间添加1个转动副,在上下摆动的液压缸和与地铰接的2个液压缸均添加驱动.共计24个转动副、5个移动副和3个驱动.根据锻造操作机工作载荷设计要求,负载是1600kN,位于距钳口正中心外延100mm处,方向竖直向下.机构运动的惯性力和重力由ADAMS/Solve求解器自动计算.
3 锻压操作机的刚体动态特性分析3.1 上下平移运动的动力学仿真锻造操作机的上下平移运动是通过双缸(图2中AB以及其对称的缸)驱动来实现的.其中缓冲缸和上下摆动液压缸无相对伸缩变化.仿真时间设为10s,钳口处受载为1600kN,仿真初始及结束状态如图4所示.
图4 上下平移运动仿真的初始和结束状态Fig.4 Preliminarystateandterminativestateofsimulationsofforging(22)921 第2期任云鹏,等:锻造操作机的可视化刚体动力学仿真 manipulatormoveupanddown