电镀金刚石工具镀层脱落原因的分析
电镀过程中镀层不良的描述、原因及对策

电镀过程中镀层不良的描述、原因及对策1、针孔。
针孔是由于镀件外表吸附着氢气,迟迟不开释。
使镀液无法亲润镀件外表,然后无法电析镀层。
跟着析氢点周围区域镀层厚度的添加,析氢点就构成了一个针孔。
特点是一个发亮的圆孔,有时还有一个向上的小尾巴"。
当镀液中短少湿润剂并且电流密度偏高时,容易构成针孔。
2、麻点。
麻点是由于受镀外表不洁净,有固体物质吸附,或许镀液中固体物质悬浮着,当在电场效果下到达工件外表后,吸附其上,而影响了电析,把这些固体物质嵌入在电镀层中,构成一个个小凸点(麻点)。
特点是上凸,没有发亮现象,没有固定形状。
总归是工件脏、镀液脏而构成。
3、气流条纹。
气流条纹是由于添加剂过量或阴极电流密度过高或络合剂过高而降低了阴极电流效率然后析氢量大。
假如当时镀液流动缓慢,阴极移动缓慢,氢气贴着工件外表上升的进程中影响了电析结晶的摆放,构成自下而上一条条气流条纹。
4、掩镀(露底)。
掩镀是由于是工件外表管脚部位的软性溢料没有除掉,无法在此处进行电析堆积镀层。
电镀后可见基材,故称露底(由于软溢料是半通明的或通明的树脂成份)。
5、镀层脆性。
在SMD电镀后切筋成形后,可见在管脚弯处有开裂现象。
当镍层与基体之间开裂,判定是镍层脆性。
当锡层与镍层之间开裂,判定是锡层脆性。
构成脆性的原因八成是添加剂,光亮剂过量,或许是镀液中无机、有机杂质太多构成。
6、气袋。
气袋的构成是由于工件的形状和积气条件而构成。
氢气积在"袋中"无法排到镀液液面。
氢气的存在阻挠了电析镀层。
使堆集氢气的部位无镀层。
在电镀时,只需留意工件的钩挂方向能够防止气袋现象。
如图示工件电镀时,当垂直于镀槽底钩挂时,不发生气袋。
当平行于槽底钩挂时,易发生气袋。
7、塑封黑体中心开"锡花”。
在黑体上有锡镀层,这是由于电子管在焊线时,金丝的向上抛物形太高,塑封时金丝显露在黑体外表,锡就镀在金丝上,像开了一朵花。
不是镀液问题。
8、"爬锡"。
电镀脱皮改善方案

电镀脱皮改善方案
电镀脱皮是常见的电镀缺陷,会造成脱皮的因素很多,抛光、前处理、活化、电解、镀液成分、杂质、导电性、操作等有任何一项未做好均有可能造成电镀脱皮;一些脱皮现象在镀后检验时不会发生,但放置一段时间后会产生剥落,如已出货就会造成客户投诉。
一直未能得到有效改善,造成客户很不满意。
采取有效措施降低、消除电镀脱皮、提高良品率刻不容缓。
一、产生脱皮的原因分析及措施
镀层与基体或镀层间结合力不好是造成脱皮的根本原因。
1、锌合金底材与镀层间脱皮
2、镀层间脱皮
3、返修品脱皮
二、品质控制
1、加强抛光后的进料、移转检验,抽样水平从原来的AQL2.5提
高到AQL1.0,如有水纹、砂孔等素材问题或镀铜返抛氧化露底
的批号分开电镀,镀后全部做烘烤测试;
2、每班电镀前技术部、生产单位做好溶液更换、槽液测试分析及
加药,并按要求填写记录表单;
3、品保做好首检、巡检、末检、专检等检验工作,除做好原检验
测试项目外,增加磨刷结合力测试;返修品、异常批隔离、标
识;
4、技术部做好原物料检验,资材、车间做好先进先出及批次管理;
三、设备、仪器、工艺管理改进
1、添加剂加药过量是造成电镀脱皮的重要因素之一,因此控制添
加剂加药量对于改善电镀脱皮十分重要。
建议购买安培小时计
或自动加药机,严格按工艺要求加入添加剂。
2、目前最重要的是要做好工艺管理工作,消除操作异常因素。
电镀失败分析报告
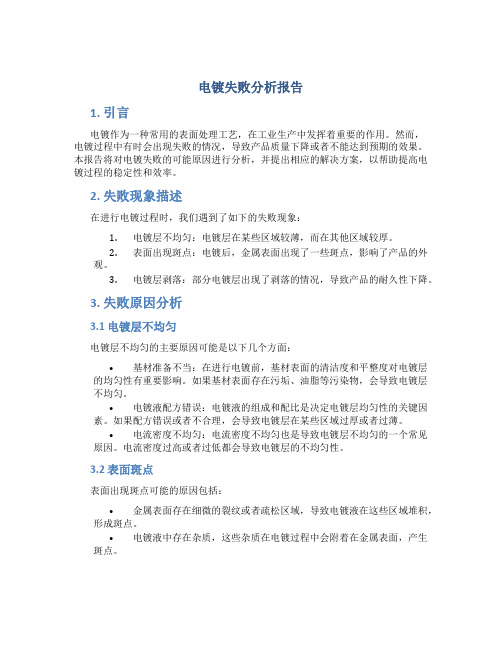
电镀失败分析报告1. 引言电镀作为一种常用的表面处理工艺,在工业生产中发挥着重要的作用。
然而,电镀过程中有时会出现失败的情况,导致产品质量下降或者不能达到预期的效果。
本报告将对电镀失败的可能原因进行分析,并提出相应的解决方案,以帮助提高电镀过程的稳定性和效率。
2. 失败现象描述在进行电镀过程时,我们遇到了如下的失败现象:1.电镀层不均匀:电镀层在某些区域较薄,而在其他区域较厚。
2.表面出现斑点:电镀后,金属表面出现了一些斑点,影响了产品的外观。
3.电镀层剥落:部分电镀层出现了剥落的情况,导致产品的耐久性下降。
3. 失败原因分析3.1 电镀层不均匀电镀层不均匀的主要原因可能是以下几个方面:•基材准备不当:在进行电镀前,基材表面的清洁度和平整度对电镀层的均匀性有重要影响。
如果基材表面存在污垢、油脂等污染物,会导致电镀层不均匀。
•电镀液配方错误:电镀液的组成和配比是决定电镀层均匀性的关键因素。
如果配方错误或者不合理,会导致电镀层在某些区域过厚或者过薄。
•电流密度不均匀:电流密度不均匀也是导致电镀层不均匀的一个常见原因。
电流密度过高或者过低都会导致电镀层的不均匀性。
3.2 表面斑点表面出现斑点可能的原因包括:•金属表面存在细微的裂纹或者疏松区域,导致电镀液在这些区域堆积,形成斑点。
•电镀液中存在杂质,这些杂质在电镀过程中会附着在金属表面,产生斑点。
3.3 电镀层剥落电镀层剥落主要有以下原因:•基材与电镀层之间的粘接力不足,可能是由于基材表面没有经过适当的预处理,或者电镀液的组分错误导致的。
•电镀过程中温度不稳定或者电镀时间过短,未能使电镀层与基材充分结合。
4. 解决方案4.1 电镀层不均匀为了解决电镀层不均匀的问题,可以采取以下措施:•对基材进行充分的预处理,确保基材表面的清洁度和平整度。
可以采用机械抛光、酸洗等方法。
•定期检查电镀液的配方和配比,确保其符合要求。
•调整电流密度,在电镀过程中保持均匀的电流密度分布。
电镀不良原因分析及对策
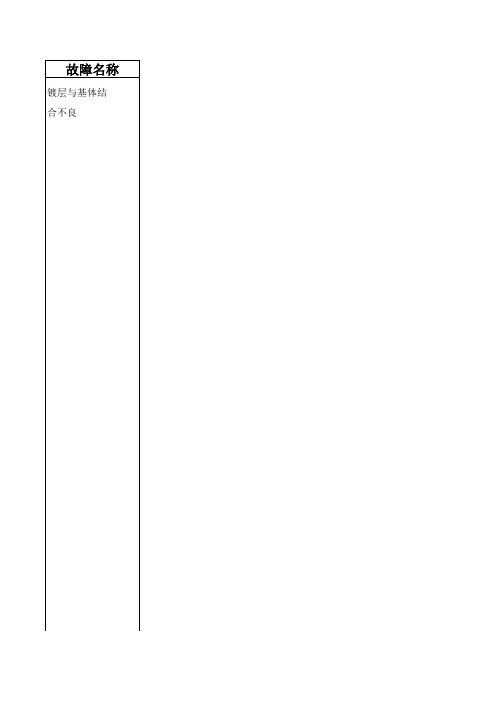
故障名称
镀层与基体结 合不良
镀层表面起泡 脱皮
由于制品成型条件对镀层结合力影响的因素相当复杂,处理较为困难,尚 无良好的针对性措施。但产生这类故障时,应从成型条件着手排除,通过改善 成型条件,使制品表面不产生白粉和裂纹。 制品的电镀一般采用多层电镀。镀件起泡脱皮,说明镀层与基体结合不牢, 或镀层之间结合不良。具体表现在5个方面: (1)金属镀层间分离。其成因及对策为: a、化学镀层钝化。应改善化学镀后的活化条件,减少传递时间,采用较厚 的化学镀层,病迅速覆盖一层光亮酸性铜或立即闪镀镍。 b、镀铜层钝化。应改进铜层酸洗条件和清除镀件表面油污。 c、镀镍层钝化。应在镀镍前进行活化处理。 (2)镀层与制品基体起泡分离。其成因与对策为: a、制品的基体材料不适合电镀。应更换原料品种,使用电镀级原料。 b、制品的成型条件控制不当。应适当调整制品的成型温度和浇口结构。 c、粗化不良。应适当调整粗化液组分、粗化温度和粗化时间。从经验上看, 制品经粗化厚的正常情况,应是表面既失去光泽,又无毛糙的感觉;制品经过 化许学镀后的正常情况,应是镀层呈暗光。 d、制品电镀层的组合设计不当。由于塑料的热膨胀率比金属镀层大得多,如 果表面为硬质镀层,当周转介质温度发生变化时就会引起镀层与基体起泡分离。 在设计镀层时,一般底层应为塑性镀层,且镀铜层应厚一些,占整个镀层的2/3, 而镀亮镍和铬时则应薄一些。 (3)电镀的电流密度太大或镀层内应力太大,导致镀层起泡。应适当降低电流 密度,调整电镀液的配比和电镀工艺条件。 (4)镀层表面产生线条或点状的鼓泡。其产生原因不在于镀层与基体结合不良 或金属化处理不当,而在于制品成型时,原料干燥不良,水份含量太高。对此, 应在制品成型时,对原料进行充分干燥,使水分含量达到成型时的要求。 (5)制品表面镀铬存放后层面起泡。其产生原因和处理方法如下: a、制品的前处理没有达到工艺要求。如粗化时间太断或太长,敏化和活化不 当等。对此,应检验粗化液的成分含量并进行调整,严格按照工艺要求控制粗 化时间和溶液温度。敏化和活化也应按工艺要求进行,特别是制品表面除油要 彻底。 b、电镀工艺条件控制不当。如光亮镍的镀层厚度大大超过了铜层的厚度,且 镀镍工艺条件又控制不当,造成镀镍层内应力过大。对此,应调整电镀工艺条 件,合理设计镀层厚度。 c、镀件存放不当。应注意镀件存放条件,存放环境温差不能太大。 当表面积较大的制品在镀酸性亮铜时,夹具周围接触的化学铜层活镍层溶 解,就会产生局部露塑。制品在电镀铜、镍或铬时,都是在化学镀铜或镍的基 础上进行的,因化学镀铜或镀镍层相当薄,厚度一般只有0.3~0.5μm,在酸性 溶液中,当挂具的接触导线太细或弹性不足时,出现露塑,接触点处的电阻较 大,会使触点周围流入的电流过小,引起学镀铜或镀镍层很快被溶解,出现露 塑,不过,电流过大也会产生接触点露塑。对此,一是将挂夹具导线改粗,一 般为金属电镀的一倍,一增加接触面积;二是先小后大的作业电流,逐渐升至 工艺要求;三是确保化学沉积金属层的厚度不得低于0.4μm,且化学镀铜后存 放时间不宜太长。 麻点是指电镀河腐蚀过程中镀层表面形成的小坑或小孔。在3~5倍放大镜下 可观察到许多微小的凹坑,但手摸时无粗糙感。这种故障产类方法时,支撑点尽可能安放在孔内侧的 根部。
现代电镀网:装饰铬镀铬层脱落的原因分析

现代电镀网:装饰铬镀铬层脱落的原因分析
1、底层镍钝化
2、镀铬过程中断电
原因分析:在镀铬过程中断电或导电不良,出现电流中断,易使工件的镍镀层在镀铬液中钝化,出现铬层发花现象
处理方法:
a.断电后,取出工件,用酸活化后重新电镀;
b.清理导电触点,擦洗阳极,保证导电良好
3、阴极电流密度过大
处理方法:
a.准确测量受镀工件面积,合理设定电流值,并严格控制镀液温度至标准值;
b.必要时采取阴极保护措施
4、镀镍层表面受到污物污染
原因分析:镍层抛光后再镀镍或退铬后的工件直接镀铬,若铬层退除不净,活化不良或经抛光的工件受到抛光膏的污染,在入镀铬槽前清洗不彻底保证镍层表面洁净和活化状态的话,出现镀铬层脱落
处理方法:加强镀铬前的前处理,保证工件洁净和镍层充分活化
5、镀铬层的硬度过大
处理方法:合理设定工艺参数和选择硬度稍低的镀铬工艺。
镀层脱落问题

镀层脱落问题实验室制取样品,待镀件为2.5cm*2cm面积铜片,镀层在取出,淋洗,用电吹风吹干的时候,出现了镀层爆裂脱落的问题,不知道怎么解决?这是镀层的结合力不佳的表现,问题是前处理活化不到位所造成的除油后:硫酸活化30秒+水洗+引镀60秒(直流电3v,20秒或镀锌件引镀)另外注意:1、基体是何材料。
什么铜,不同的铜要不同处理。
2、你的镀液是什么镀液?高磷应是没有问题的,压应力大。
如是中低磷则要注意。
你的镀液是自配还是商品镀液。
如是自己配则要有去应力药剂。
商品镀液则没有问题的(为了镀液稳定性还是采用商品镀液好再说自配的价格也相差无几3。
倒角抛光4、弱碱除油5、10--15%硫酸去锈活化6、温度和镀速在相应的范围内。
以上情况要做好否则结合力不好和镀层应力太大。
铜上化学镀就是没有问题的。
玻璃镀铜的有关资料玻璃上化学镀镍的主要难点在于前处理,一般前处理采用的方法为:刻蚀、敏化、活化、化学镀铜。
刻蚀工艺:氢氟酸200g/L、硝酸600g/L;敏化活化可用胶体钯工艺或使用银浆法工艺玻璃上镀铜,还要求镀锯齿状即在玻璃上铜分布不规则,我想用胶带把不需要镀的地方粘住,粗化不影响吗?胶带应使用耐酸碱耐高温胶带,完全可以达到目的。
我的联络方法:常州市旭光电镀化学品有限公司。
耐酸碱耐高温胶带那里有买的80元/圈联系电话:请教您几个问题:1.在实际生产中,只以酒石酸钠作络和剂,且R=3,PH=9,镀液是否稳定;如果不稳定,一般能保持多长时间;原理上不稳定时发生歧化反应,析出的是氧化亚铜,氧化亚铜应该是砖红色,可我在实际操作中析出物却为红褐色,好似纯铜的颜色,请问是铜吗?是什么原因造成的呢;实际生产和实验室的实验有太大的区别吗?2.在反应过程中,歧化反应有什么比较好的方法能控制呢?铜液的浓度、R值对歧化反应有影响吗?3.胶布贴上后立即撕去(敏化前),残余的胶对镀铜会有影响吗?4.如果玻璃活化后不清洗立即浸入铜液,钯核或锡离子有可能进入镀液,引起铜液的不稳定吗?5.锡液(敏化液)可以重复使用吗?它的稳定性怎样才能维护呢?玻璃敏化活化的不均匀有什么比较好的解决方法呢?电磁搅拌器搅拌会不会使离子移动过快从而导致不能附着在玻璃上?6.玻璃镀铜达到某一厚度时,会自然脱落,造成这一现象的原因有可能是什么呢?化學鍍之不解針孔問題您好:請問 1. 过期之化学镀液会不会造成针孔的产生??? 2. 未退磁之不锈钢做化学镀会不会产生针孔??? 3. 镍冲击(硬镀镍)的氯化镍和盐酸的比例为何??? 电流最好为?A/Dm2..4. 镀前使用盐酸活化14.1"大的不锈钢基板浓度及时间最好为何???盐酸浓度如何量测??? 5. 镀150UM厚之镍磷合金, 为何有很多针孔产生, 如何改善之???化学镀镍溶液一般不存在保质期问题,所以不存在过期问题,但是化学镀液的使用寿命有一定的期限,根据不同的配方,其使用寿命一般为6-10个周期或者是可以连续沉积40-60克镍磷镀层,镀液就要报废,在镀液已接近报废或已经报废的镀液中做出的化学镀镍层容易产生针孔。
电镀锡层脱落原因
电镀锡层脱落原因嘿,你知道电镀锡层脱落这事儿有多让人头疼吗?就像你满心期待地穿上一件新衣服,结果没一会儿扣子全掉了,那叫一个糟心。
我就碰到过这么一回,那可真是让我对电镀锡层脱落的原因有了深刻的“感悟”。
那是在我们厂子里,有一批镀锡的小零件。
这些小零件看着不起眼,可在整个产品里那也是起着关键作用的。
一开始呢,这些零件的电镀锡层看着可漂亮了,银光闪闪的,就像给零件穿上了一层闪亮的铠甲。
我当时就好奇,这电镀锡层是怎么弄上去的呢?后来一打听,原来就是通过电镀的方法,让锡离子在零件表面还原成锡原子,一层一层地堆积起来,就形成了这个锡层。
这就好比我们盖房子,一块砖一块砖地往上垒,最后就成了一堵结实的墙。
可是好景不长啊,没过多久,就发现这些零件上的锡层开始脱落了。
这可把大家急坏了,就像家里的屋顶开始掉瓦片,那还得了。
我就仔细去观察这些脱落的情况。
我发现有的地方是一大块一大块地掉,就像墙皮脱落一样,一块一块的,看着特别明显。
还有些地方呢,是像粉末一样一点点地掉,就好像是那墙上的灰,轻轻一抹就掉下来了。
那这到底是为啥呢?我就开始找原因。
首先我想到的是镀前处理的问题。
你想啊,这就好比我们盖房子之前得把地基打好一样。
如果零件表面没清理干净,有油污啊、锈迹啊之类的东西,那锡层能粘得牢吗?就像我们在脏桌子上贴贴纸,肯定贴不牢啊。
我们厂子里当时就有个情况,有一批零件在镀锡之前,清洗的工人可能没太注意,有几个零件上还残留着一些油渍。
那这些零件镀上锡层之后,就很容易脱落了。
然后呢,我又觉得电镀液可能也有问题。
电镀液就像是给锡离子提供的“交通工具”,把它们送到零件表面去。
要是这个电镀液的成分不对,比如说锡离子的浓度不合适,就像公交车没按时间表发车,该来的锡离子没来够,那镀出来的锡层肯定薄厚不均。
薄的地方就像纸糊的一样,稍微有点风吹草动就破了,也就是脱落了。
我记得当时我们为了节省成本,换了一种比较便宜的电镀液,结果就出问题了。
这就好比我们买东西,图便宜买了个质量不好的,最后吃亏的还是自己。
镀金手指金剥离原因分析(修改版)
TO : CC :一、背景镀金手指线搬迁至东城后于3月30日开始正式试板生产,第一个试板型号为仿照D1*******制作的金手指板,生产时按照0.8μm 金厚来制作,共4P 。
试板3M 胶带测试、孔隙率测试都OK 。
相关参数及结果见表1。
表1:开线试板参数记录表2:开线试板测试结果8.651生产至4月5日开始,工序反馈厚金板多出现剥离,同时伴有金面氧化。
至4月10日以后,所有厚金型号均出现金镍剥离。
且孔隙率结果也不OK 。
图1:4/5-4/10问题板图片从问题板来看,剥离板呈如下特点:①、均为厚金板(金厚≥0.76μm )剥离,两面都有剥离; ②、为金镍剥离,且剥离位置镍面光亮,无异常;③、部分型号3M 胶带测试剥离,部分不剥离,但所有剥离板孔隙率测试结果均NG 。
二、过程排查2.1所有生产板测试结果排查对3月30日开始镀金手指线所有生产的型号按照加烘后孔隙率的方法进行排查,结果确认4月6日开始所有的型号已经出现异常,至4月10日之后100%异常。
G F异常排查测试结果.xl sx2.2 异常原因排查2.2.1孔隙率测试过程排查孔隙率的作用主要是通过硝酸腐蚀的方法,来监控金面晶格的致密性。
当金面晶格疏松时,硝酸蒸汽会沿着金面空洞进入镍面,进而产生腐蚀,表观上为金面有被腐蚀的小黑点,严重的整个金面被剥离,裸露镍面。
实际操作方法是:取一40mm×40mm 左右的样片,使用异丙醇超声波清洗,风机吹干,放入剩有500ml 浓硝酸的干燥皿中,时间1H 。
在实际跟进孔隙率测试过程中,偶会发现硝酸蒸汽中有大量的黄色盐雾产生,而正常硝酸应为无色透明。
因此对孔隙率测试方法进行确认。
2.2.1.1 异丙醇对硝酸蒸汽测试结果影响表3:异丙醇对硝酸根测试结果影响4月21日新开硝酸缸4月22日 8:304月22日 10:00从结果来看,异丙醇与硝酸会发生反应产生大量黄色气体。
但需要进一步确认此黄色气体是否会对测试结果产生影响。
电镀件常见不良原因分析
电镀件常见不良原因分析电镀件是一种常见的表面处理方式,用于保护和美化金属制品。
然而,在电镀过程中,常会出现不良现象,例如涂层不均匀、气泡、黑点、膜裂纹等问题。
这些问题的产生往往是由于一系列原因导致的。
下面,就电镀件常见不良原因进行分析。
1.基材准备不当电镀前的基材处理非常重要,如果没有正确准备基材,会直接影响到电镀效果。
常见的基材准备不当原因有:-表面清洁不彻底:基材表面可能存在油污、灰尘等杂质,如果未经彻底清洁,这些杂质会影响镀层的附着力和均匀性。
-钝化处理不当:钝化处理可以增强镀层与基材之间的结合力,但处理时间、温度、浓度等参数不正确,会导致镀层不牢固。
2.电解液质量不合格电解液是电镀过程中的核心部分,如果电解液质量不合格,会直接影响到电镀效果。
常见的电解液质量问题有:-含杂质过多:电镀液中可能存在各种杂质,如金属离子、有机物等,它们会影响到电镀膜的致密性和均匀性。
-配方参数不正确:电解液的配方包括各种成分的浓度和比例,如果配方参数不正确,会导致镀层的颜色、硬度等性能不达标。
3.电镀工艺控制不当电镀工艺过程中的各个环节都需要精确控制,否则会产生不良现象。
常见的电镀工艺控制不当原因有:-电流密度不均匀:电镀过程中,电流密度分布不均匀会导致镀层厚度不均匀,甚至出现孔洞等问题。
-温度控制不准确:电镀过程中的温度控制对于镀层的质量和均匀性非常重要,如果温度控制不准确,会影响到电解液的反应速率和镀层的结构。
4.设备维护不当电镀设备的维护工作也是保证电镀质量的关键。
常见的设备维护不当原因有:-阴极和阳极污染:设备内部的阴极和阳极可能会受到电解液的腐蚀,长期使用后会产生污染物,需要定期清洗和更换。
-设备参数不稳定:设备的电流、温度、电压等参数需保持稳定,如果设备参数不稳定,会导致镀层质量下降。
综上所述,电镀件常见的不良现象往往由基材准备不当、电解液质量不合格、电镀工艺控制不当和设备维护不当等原因导致。
为确保电镀质量,操作人员应遵循正确的工艺流程,提高工作细致性和耐心性,严格控制每个环节的参数和条件,以及定期维护设备,确保设备的正常运行。
镀Ti金刚石工具磨粒破坏形态分析
大块破碎
工具寿命低
盎刚石强度低 。 投放澈度低
脱落
工 具寿命低. 蕺宰低 结台荆爵金f石 力低 . 把持 I
工具性能与磨削面上 金刚石 的状态关系 : 有如下
模式
响规律 如 下 :
国 家八 五科技 攻关项 目(5—79—0 —2/5 8 1 5 60 )
工具寿命长, 效率高——磨削面上金刚石主要是 完好和微破碎状态 工具寿命长, 效率低一 磨削面上金刚石主要是 磨钝状态 工具寿命低 , 效率高——磨削面上金剐石主要是 大块 破 碎 工具寿命低。 效率低——磨削面上金刚石主要是 脱落 , 大块破碎 真空微 蒸发 镀覆 技 术 工 业 化 应 用 以 来 , 在 国 内 已 近 百家金 刚石 工具 厂 应用 , 其生 产 的 镀 钛 金 刚 石适 用 于各类金属烧结结合剂金剐石工具 , 像各类金刚石切
T et - ̄rt s ray eue rm 5 % t aot 0 . 4l r i Ⅱ h , o aoiget d cdf 5 o bu 1%  ̄fe ms - . a i lr o i j
‘ c t r ohicesd. ̄ ti r e eto’ ei n  ̄cec u eb t nrae 1 a ml st lsl t ad e in y a n mv h o f i me
— —
几种钝化模式 ; 1完好一磨钝 ( ) 金刚石强度高, 投放浓度高 ) 2 完好一大块破碎( ) 金刚石强度低 . 投放浓度低 ) 3 完好一脱落( ) 结合剂把持力低) 几种低寿命模式 : 1 ) 完好一大块破碎( 金刚石强度低 , 投放浓度低) 2完好一脱落 ( ) 结合剂把持力低 ) 影响五种状态 的比例数的因素见表 l 。 衰l工 ‘ 面 盒 石 壮 豆影 园 | 工作 上 尉 的 奄 响 蠢
- 1、下载文档前请自行甄别文档内容的完整性,平台不提供额外的编辑、内容补充、找答案等附加服务。
- 2、"仅部分预览"的文档,不可在线预览部分如存在完整性等问题,可反馈申请退款(可完整预览的文档不适用该条件!)。
- 3、如文档侵犯您的权益,请联系客服反馈,我们会尽快为您处理(人工客服工作时间:9:00-18:30)。
矿产资源开发利用方案编写内容要求及审查大纲
矿产资源开发利用方案编写内容要求及《矿产资源开发利用方案》审查大纲一、概述
㈠矿区位置、隶属关系和企业性质。
如为改扩建矿山, 应说明矿山现状、
特点及存在的主要问题。
㈡编制依据
(1简述项目前期工作进展情况及与有关方面对项目的意向性协议情况。
(2 列出开发利用方案编制所依据的主要基础性资料的名称。
如经储量管理部门认定的矿区地质勘探报告、选矿试验报告、加工利用试验报告、工程地质初评资料、矿区水文资料和供水资料等。
对改、扩建矿山应有生产实际资料, 如矿山总平面现状图、矿床开拓系统图、采场现状图和主要采选设备清单等。
二、矿产品需求现状和预测
㈠该矿产在国内需求情况和市场供应情况
1、矿产品现状及加工利用趋向。
2、国内近、远期的需求量及主要销向预测。
㈡产品价格分析
1、国内矿产品价格现状。
2、矿产品价格稳定性及变化趋势。
三、矿产资源概况
㈠矿区总体概况
1、矿区总体规划情况。
2、矿区矿产资源概况。
3、该设计与矿区总体开发的关系。
㈡该设计项目的资源概况
1、矿床地质及构造特征。
2、矿床开采技术条件及水文地质条件。