粉末的制备-液相沉淀法详解
纳米材料的制备方法(液相法)
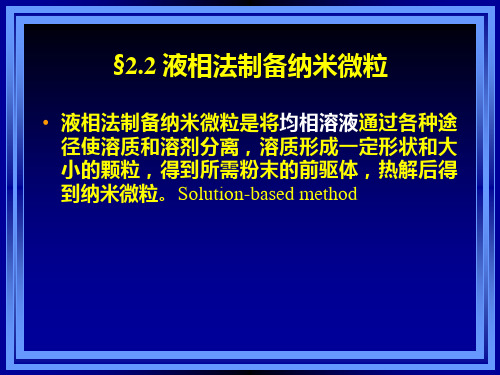
(2)雾化水解法
将一种盐的超微粒子,由惰性气体载入含有金属 醇盐的蒸气室,金属醇盐蒸气附着在超微粒的 表面,与水蒸气反应分解后形成氢氧化物微粒, 经焙烧后获得氧化物的超细微粒。
这种方法获得的微粒纯度高,分布窄,尺寸可控。 具体尺寸大小主要取决于盐的微粒大小。
例如高纯Al2O3微粒可采用此法制备: 具体过程是将载有氯化银超微粒(868一923K)的 氦气通过铝丁醇盐的蒸气,氦气流速为500— 2000 cm3/min,铝丁醇盐蒸气室的温度为395— 428K,醇盐蒸气压<=1133Pa。在蒸气室形成 以铝丁醇盐、氯化银和氦气组成饱和的混合气 体。经冷凝器冷却后获得了气态溶胶,在水分 解器中与水反应分解成勃母石或水铝石(亚微 米级的微粒)。经热处理可获得从Al2O3的超细 微粒。
• 金刚石粉末的合成
5ml CCl4 和过量的20g金属钠被放到50ml的高压釜中,质量比为Ni:Mn:Co = 70:25:5的Ni-Co合金作为催化剂。在700oC下反应48小时,然后的釜中冷却。 在还原反应开始时,高压釜中存在着高压,随着CCl4被Na还原,压强减少。 制得灰黑色粉末。
(A)TEM image (scale bar, 1 mm) (B) electron diffraction pattern (C) SEM image (scale bar, 60 mm)
§2.2 .1 沉淀法 precipitation method
沉淀法是指包含一种或多种离子的可溶性盐溶液, 当加入沉淀剂(如OH--,CO32-等)后,或在一定 温度下使溶液发生水解,形成不溶性的氢氧化 物、水合氧化物或盐类从溶液中析出,并将溶 剂和溶液中原有的阴离子除去,经热分解或脱 水即得到所需的化合物粉料。
ZrOCl2 2NH 4OH H 2O Zr(OH ) 4 2NH 4Cl
粉末的制备液相沉淀法详解

随着还原反应的进行,金属离子浓度降低,同时,金属 电位下降,而氢离子浓度则增高,氢电位升高。当达到 平衡时
=
25 °C及pH2=1atm条件下氢还原金属的可能程度
Me n+=10-2 时的平衡pH值
增加氨浓度有两个相反的效应,一方面由于中和了 析出的酸而有利于沉淀;另一方面由于形成络合物, 降低了浓度又会使还原过程减慢。
25 oC时在水中的标准电极电位
电极电位与溶液中离子浓度之间的关系式可表示为
E=
+ RT lnc nF
25 oC时的电极电位,用
R =8.316 V·C/K·mol, F=96500 Cε
ε=
+ 0.0591 lgc n
Zn + Cu 2+= Cu + Zn 2+
Δε= εCu 2+/ Cu +(- εZn 2+/ Zn)
课外自己学习!
镍催化剂量对镍沉淀速度的影响
(6)添加剂的影响 向溶液中添加某种物质将大大影响沉出金属粉末的物理 性能,常用的添加剂有聚丙烯酸铵、胶(树胶和动物 胶)、脂肪酸(如甘油三油脂酸)、葡萄糖等。 添加剂有两个作用: a.可防止结团,调整粉末的粒度;b.使沉淀均匀
蒽醌对镍沉淀 速度的影响
3. 溶液氢还原法生产铜、镍、钴粉工艺
1. 溶液氢还原的基本原理
Men+
+
1 2
nH2 =
Me + nH+
(1) (2)
εMe n+/ Me与Me n+浓度的关系和εH+/ H2与pH的关系
显然,只有当金属线高于氢线时,还原过程在热力学上 才是可能的。 增大溶液氢还原总反应的还原程度有两个途径:
高纯氧化铝粉末主制备方法有哪些?
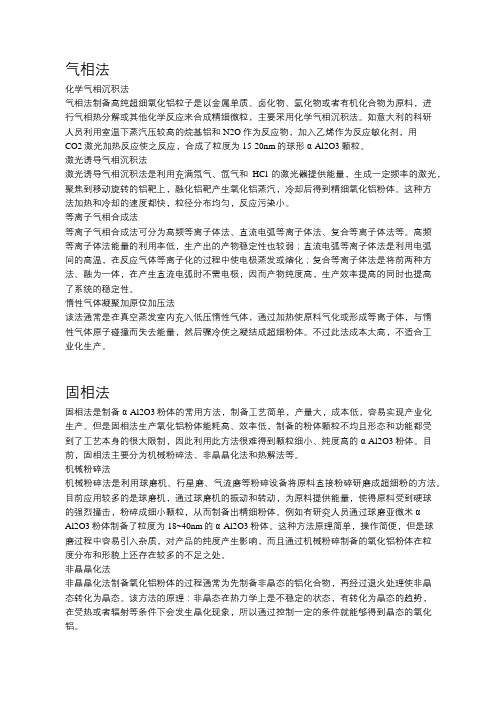
气相法化学气相沉积法气相法制备高纯超细氧化铝粒子是以金属单质、卤化物、氢化物或者有机化合物为原料,进行气相热分解或其他化学反应来合成精细微粒,主要采用化学气相沉积法。
如意大利的科研人员利用室温下蒸汽压较高的烷基铝和N2O作为反应物,加入乙烯作为反应敏化剂,用CO2激光加热反应使之反应,合成了粒度为15-20nm的球形α-Al2O3颗粒。
激光诱导气相沉积法激光诱导气相沉积法是利用充满氖气、氙气和HCl的激光器提供能量,生成一定频率的激光,聚焦到移动旋转的铝靶上,融化铝靶产生氧化铝蒸汽,冷却后得到精细氧化铝粉体。
这种方法加热和冷却的速度都快,粒径分布均匀,反应污染小。
等离子气相合成法等离子气相合成法可分为高频等离子体法、直流电弧等离子体法、复合等离子体法等。
高频等离子体法能量的利用率低,生产出的产物稳定性也较弱;直流电弧等离子体法是利用电弧间的高温,在反应气体等离子化的过程中使电极蒸发或熔化;复合等离子体法是将前两种方法、融为一体,在产生直流电弧时不需电极,因而产物纯度高,生产效率提高的同时也提高了系统的稳定性。
惰性气体凝聚加原位加压法该法通常是在真空蒸发室内充入低压惰性气体,通过加热使原料气化或形成等离子体,与惰性气体原子碰撞而失去能量,然后骤冷使之凝结成超细粉体。
不过此法成本太高,不适合工业化生产。
固相法固相法是制备α-Al2O3粉体的常用方法,制备工艺简单,产量大,成本低,容易实现产业化生产。
但是固相法生产氧化铝粉体能耗高、效率低,制备的粉体颗粒不均且形态和功能都受到了工艺本身的很大限制,因此利用此方法很难得到颗粒细小、纯度高的α-Al2O3粉体。
目前,固相法主要分为机械粉碎法、非晶晶化法和热解法等。
机械粉碎法机械粉碎法是利用球磨机、行星磨、气流磨等粉碎设备将原料直接粉碎研磨成超细粉的方法。
目前应用较多的是球磨机,通过球磨机的振动和转动,为原料提供能量,使得原料受到硬球的强烈撞击,粉碎成细小颗粒,从而制备出精细粉体。
氧化铝的制备

10
4、反应物浓度的影响
LOGO
❖ 当反应物浓度小于某一值时,瞬间产生晶核,由 于处在稀溶液中,晶核不易长大,故所得氧化铝
粉末粒径较小。当反应物浓度大于某一值时,超
细氧化铝颗粒粒径随反应物浓度增加有明显的长
大趋势。这是由于反应物浓度越大,溶液的过饱
和度越大,而颗粒的生长速率随溶液中结晶物质
过饱和度增大而加快,反应物浓度的增大一方面
12
LOGO
4
二、液相沉淀法
LOGO
❖我们通过调配沉淀剂的种类以及加入方式、 反应物的浓度、反应体系的pH、反应时间、 反应温度、表面活性剂的添加量等条件, 控制氧化铝前驱体晶粒的生长,控制粒子 的团聚,通过考察氧化铝粉体的粒度、收 率、松装密度等性质,来确定最佳的优化 方案,最后通过对钠的控制,制备出产率 高,纯度高,疏松性好,粒径小且分布均 匀的超细氧化铝粉末。
9Hale Waihona Puke 3、反应温度的影响LOGO
❖ 氧化铝的粒径随温度的升高而明显地增大,这是 由于反应温度不仅影响沉淀生成速度,而且对己 形成的晶粒的增长速度也有很大的影响。随反应 温度的升高,氧化铝晶粒的生成和增长速度都会 增大,且温度越高,晶体颗粒之间的碰撞也越频 繁,故晶体之间的团聚作用也越明显。而且温度 太高会加速NaAl(OH)4的水解,不利于反应的进 行。但温度过低,反应速率会减慢,也会影响晶 粒的成长。总而言之,温度过低或者过高所得粉 末粒径都比较大,故选择其反应温度范围为: 25-45℃。
LOGO
LOGO
一、超细氧化铝 二、液相沉淀法 三、沉淀剂的选择 四、各因素对氧化铝影响 五、结语
2
一、超细氧化铝
LOGO
❖超细氧化铝是具有高熔点、高硬度、良好 的耐腐蚀、耐热及绝缘等良好性能的特种 功能材料。
液相沉淀法制备Al2O3-SiO2-CaF2系玻璃粉体的晶化特性

粉体的颗粒尺寸. 采用 Y4 - Q全 自 动型 x射线衍射仪对初始粉体及热处理后的粉体分别进行 X D R
相沉淀法制备的超细粉体 , 谱线 B为某牙科材料 厂采用传统 方法制备 的微 细粉体. 然, 显 两者 的 谱线非常近似 , 均为非晶物质所特有 的馒头型谱 线, 可证明两者均 为非晶态粉体 ; 虽然通过这种
衍射谱不能确定各 自 粉体 的相组成 , 由于两者 但 的馒头 主峰位 置一致 , 其余 峰线也 能很 好吻 且
A , i a 1 一 O 一 F 系生物玻璃粉体具有 良好的生物相容性 , O S C 既可以高温烧结成硬组织替代材
料, 又可以室温固结成玻璃离子水门汀( l s oo e C m n, Ga nm r e et简称 GC 型粘结材料 , sI I) 还可释放
F , 一 因而在牙科 、 骨科领域具有 良好的应用前景. 然而, 在临床应用上, 人们发现, 由于生物玻璃 材料的易脆性和固结收缩性常导致其过早地破碎和脱落 , 因此 , 改善该材料的结构和物理力学 性能 , 具有十分重要的意义¨ 文献 [ ] 出, 引. 7指 细化玻璃粉体是改善 固结组织与牙齿粘结状态
2 1 原始粉体的特性 . 图 1 a 、b 为液相沉淀法制备 A2 i: a ()( ) 1 - O - F 系玻璃粉体的 T M形貌 , 中, a 放 OS C E 其 图( )
大倍数为 7万倍 , b 为 35 图( ) . 万倍. 可见 , 粉体粒子呈近球形形状 ; 粒子尺寸约在 3 7 0 ̄ 0 m范 n
纳米粉末的制备方法
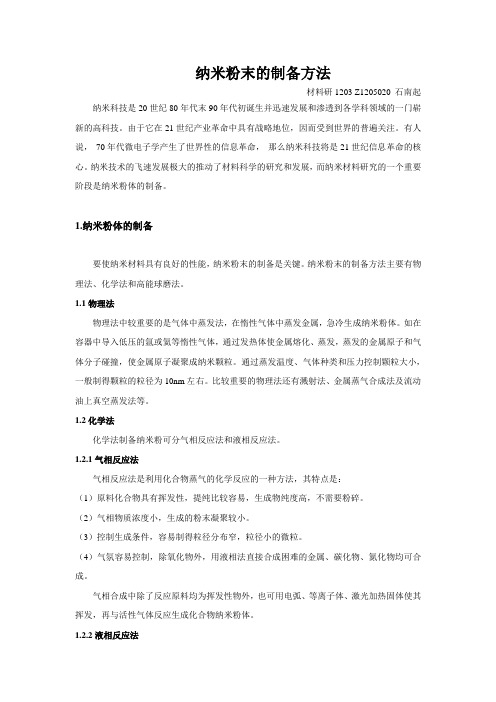
纳米粉末的制备方法材料研1203 Z1205020 石南起纳米科技是20世纪80年代末90年代初诞生并迅速发展和渗透到各学科领域的一门崭新的高科技。
由于它在21世纪产业革命中具有战略地位,因而受到世界的普遍关注。
有人说,70年代微电子学产生了世界性的信息革命,那么纳米科技将是21世纪信息革命的核心。
纳米技术的飞速发展极大的推动了材料科学的研究和发展,而纳米材料研究的一个重要阶段是纳米粉体的制备。
1.纳米粉体的制备要使纳米材料具有良好的性能,纳米粉末的制备是关键。
纳米粉末的制备方法主要有物理法、化学法和高能球磨法。
1.1物理法物理法中较重要的是气体中蒸发法,在惰性气体中蒸发金属,急冷生成纳米粉体。
如在容器中导入低压的氩或氦等惰性气体,通过发热体使金属熔化、蒸发,蒸发的金属原子和气体分子碰撞,使金属原子凝聚成纳米颗粒。
通过蒸发温度、气体种类和压力控制颗粒大小,一般制得颗粒的粒径为10nm左右。
比较重要的物理法还有溅射法、金属蒸气合成法及流动油上真空蒸发法等。
1.2化学法化学法制备纳米粉可分气相反应法和液相反应法。
1.2.1气相反应法气相反应法是利用化合物蒸气的化学反应的一种方法,其特点是:(1)原料化合物具有挥发性,提纯比较容易,生成物纯度高,不需要粉碎。
(2)气相物质浓度小,生成的粉末凝聚较小。
(3)控制生成条件,容易制得粒径分布窄,粒径小的微粒。
(4)气氛容易控制,除氧化物外,用液相法直接合成困难的金属、碳化物、氮化物均可合成。
气相合成中除了反应原料均为挥发性物外,也可用电弧、等离子体、激光加热固体使其挥发,再与活性气体反应生成化合物纳米粉体。
1.2.2液相反应法液相反应法作为一种制备超细粉体的方法成为各国材料科学家研究的热点,它具有无需高真空等苛刻物理条件、易放大的特点,并且得到的粉体性能比较优越。
常用的液相反应法有共沉淀法、水解法、溶胶凝胶法、微乳液反应法等。
共沉淀法是利用各种在水中溶解的物质,经反应成不溶解的氢氧化物、碳酸盐、硫酸盐、醋酸盐等,再经加热分解生成高纯度的超微粉料。
化学法制备粉体材料及表征-深圳大学材料教学试验中心
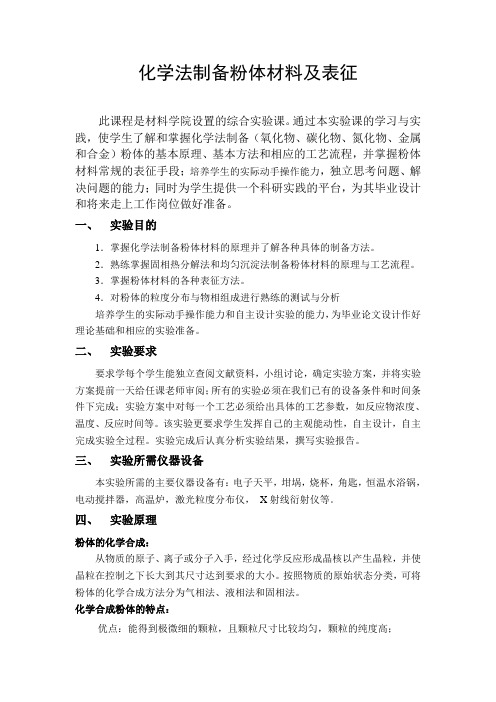
化学法制备粉体材料及表征此课程是材料学院设置的综合实验课。
通过本实验课的学习与实践,使学生了解和掌握化学法制备(氧化物、碳化物、氮化物、金属和合金)粉体的基本原理、基本方法和相应的工艺流程,并掌握粉体材料常规的表征手段;培养学生的实际动手操作能力,独立思考问题、解决问题的能力;同时为学生提供一个科研实践的平台,为其毕业设计和将来走上工作岗位做好准备。
一、实验目的1.掌握化学法制备粉体材料的原理并了解各种具体的制备方法。
2.熟练掌握固相热分解法和均匀沉淀法制备粉体材料的原理与工艺流程。
3.掌握粉体材料的各种表征方法。
4.对粉体的粒度分布与物相组成进行熟练的测试与分析培养学生的实际动手操作能力和自主设计实验的能力,为毕业论文设计作好理论基础和相应的实验准备。
二、实验要求要求学每个学生能独立查阅文献资料,小组讨论,确定实验方案,并将实验方案提前一天给任课老师审阅;所有的实验必须在我们已有的设备条件和时间条件下完成;实验方案中对每一个工艺必须给出具体的工艺参数,如反应物浓度、温度、反应时间等。
该实验更要求学生发挥自己的主观能动性,自主设计,自主完成实验全过程。
实验完成后认真分析实验结果,撰写实验报告。
三、实验所需仪器设备本实验所需的主要仪器设备有:电子天平,坩埚,烧杯,角匙,恒温水浴锅,电动搅拌器,高温炉,激光粒度分布仪,X射线衍射仪等。
四、实验原理粉体的化学合成:从物质的原子、离子或分子入手,经过化学反应形成晶核以产生晶粒,并使晶粒在控制之下长大到其尺寸达到要求的大小。
按照物质的原始状态分类,可将粉体的化学合成方法分为气相法、液相法和固相法。
化学合成粉体的特点:优点:能得到极微细的颗粒,且颗粒尺寸比较均匀,颗粒的纯度高;缺点:制备过程比较复杂,成本较高。
1.固相反应法:1)化合或还原化合法直接化合的反应通式可写为:Me +X =MeXMe 、X 分别代表金属和非金属元素。
用这一方法还可以生产多种碳化物、硅化物、氮化物粉体。
液相共沉淀法制备四氧化三铁纳米粉(2)
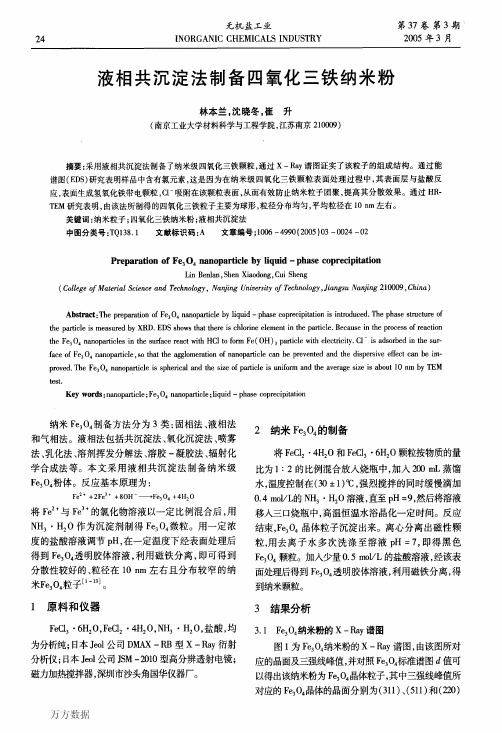
参考文献:
[1]孟哲.磁性纳米级Fe3 04的氧气诱导、空气氧化液相合成与表征
[J].光谱实验室,21303(7):489—491 [2]刘蕾.液相法制备纳米Fe3 04的研究进展[J].应用化工,2003(10):
6—10
[3]宋宝珍,甘耀昆超微Fe3 04胶体粒子的制备[J].化工冶金,1995 (5):165—169
[4]刘湘涟,何火生.Fe,04纳米级超微粉末的制备试验[J].湖南冶 金,1996(4):6—9
[5]程海斌,刘桂珍,李立春.纳米Fe,04的亭电位合分散稳定陛[J].武 汉理工大学学报,21x)3(5):4—7
[6]Shen Rongsen.Parameters concerning the preparation and performance of a magnetic microparticle antibody[J].Journal of Radioanalytical and Nuclear Chemistry,1997,128(1):131—133
关键词:纳米粒子;四氧化三铁纳米粉;液相共沉淀法
中图分类号:TQl38.1
文献标识码:A
文章编号;1006—4990(2005)03—0024—02
Preparation of Fe3 04 nanoparticle by liquid—phase coprecipitation Lin Benlan,Shen Xiaodong,Cui Sheng
[10]Yu h1.Mayers and younan xia modifying the surface properties of su- perparamagnetic iron oxide nanoparticles through a sol—gel approach
- 1、下载文档前请自行甄别文档内容的完整性,平台不提供额外的编辑、内容补充、找答案等附加服务。
- 2、"仅部分预览"的文档,不可在线预览部分如存在完整性等问题,可反馈申请退款(可完整预览的文档不适用该条件!)。
- 3、如文档侵犯您的权益,请联系客服反馈,我们会尽快为您处理(人工客服工作时间:9:00-18:30)。
= Cu 2+/ Cu -
Zn 2+/ Zn
+ 0.0591
n
a lg
Cu 2+
a Zn 2+
正电位较大的金属离子浓度的变化速度取决于下列方程式
速度常数
金属与溶液的接触面;
-
dc dt
=k
A V
c
正电性金属离子浓度
反应溶液的体积
k=
-
V1 A ·t
ln c2 c1
c1 正电性金属反应之前的浓度; c2 正电性金属经反应 t时间后的浓度
课外自己学习!
镍催化剂量对镍沉淀速度的影响
(6)添加剂的影响 向溶液中添加某种物质将大大影响沉出金属粉末的物理 性能,常用的添加剂有聚丙烯酸铵、胶(树胶和动物 胶)、脂肪酸(如甘油三油脂酸)、葡萄糖等。 添加剂有两个作用: a.可防止结团,调整粉末的粒度;b.使沉淀均匀
蒽醌对镍沉淀 速度的影响
3. 溶液氢还原法生产铜、镍、钴粉工艺
Me1 2+ + Me2 = Me1 应速度=k ·A ·[Me1 2+]i
当反应状态稳定时,扩散速度等于分界面上的 化学反应速度,那末,可得
D δ
A{[Me1 2+] -[Me1 2+]i} = k ·A ·[Me1 2+]i
D [Me1 2+] δ
[Me1 2+]i
= [Me1 2+]i(k+ D )
2.5 液相沉淀法
液相沉淀法在粉末冶金中的应用有以下四种: 1. 金属置换法
2. 溶液气体还原法:主要是溶液氢 还原法
3. 从熔盐中沉淀法
从熔盐中沉淀即是从熔盐中的金属热还原。
Mg ZrCl4+KCl 750 oC
H2O Zr+Mg(少量) HCl
4.辅助金属浴法 可以制取优质的难熔化合物。
用作熔体金属的有Fe、 Cu 、 Ag 、 Co 、Ni 、 Al 、 Pb 、 Sn等 1. 从辅助金属浴中可析出碳化物、硼化物、硅化 物、氮化物和碳氮化物。
2.增加溶液中金属离子浓度来提高金属电位
随着还原反应的进行,金属离子浓度降低,同时,金属 电位下降,而氢离子浓度则增高,氢电位升高。当达到 平衡时
=
25 °C及pH2=1atm条件下氢还原金属的可能程度
Me n+=10-2 时的平衡pH值
增加氨浓度有两个相反的效应,一方面由于中和了 析出的酸而有利于沉淀;另一方面由于形成络合物, 降低了浓度又会使还原过程减慢。
恰当的[NH3]:[Me 2+]的体积比为2.0~2.5。
从动力学因素考虑,溶液氢还原涉及到析出金属 的新相生成问题。高压氢从溶液中还原金属有两个 途径进行:
1. 均相沉淀,即不存在固体表面。 均相沉淀时,沉淀速度取决于开始的金属离子浓度
2.多相沉淀,即在固体表面上沉淀, 这种固体表面起催化剂作用以诱导还原反应开始。
2. 难熔化合物的固溶体,如TiC-WC固溶体等。
1. 金属置换法
金属置换法可用来制取铜粉、铅粉、锡粉、 银粉和金粉等。 用一种金属从水溶液中取代出另一种金属的过 程叫做置换。从热力学上讲,只能用负电位较 大的金属去置换溶液中正电位较大的金属。
反应的通式为 Me1 2+ + Me2 = Me1 + Me2 2+
2. 影响还原过程和粉末性能的因素 (1) 氨浓度的影响 氨不仅是为了调整溶液的pH值,也影响沉淀度。
[NH3]:[Co 2+]的体积摩尔比对钴沉淀速度的影响
[NH3]:[Co 2+]的体积摩尔比对钴沉淀速度的影响
(2)硫酸铵的影响 添加硫酸铵对不同溶液有不同的效果。
(NH4)2SO4:NiSO4
(NH4)2SO4对镍沉淀速度的影响
(3)氢气压力的影响 从动力学因素考虑,增加氢气压力,沉淀速度是增加的。
在不同氢气压 力下从NiSO4溶 液中沉淀镍的 速度
(4) 温度的影响 随着温度升高,沉淀速度也是增大的。
在不同温度下从NiSO4溶液中沉淀镍的速度
(5)催化剂的影响 多相沉淀的速度取决于固体催化剂表面的大小。
2. 置换出金属粉末,特别是以实验规模可制取多种粉 末。
2. 溶液氢还原法
溶液氢还原法制取两类粉末: (1)铜粉、镍粉、钴粉等 (2)合金粉(如镍 钴合金粉)和各种包覆粉
溶液氢还原法制取粉末的用途
高温涂层:镍包铝、镍包氧化铝 硬质合金刀具表面:钴包碳化钨、镍包金刚石 硬质合金:钴包碳化钨 弥散强化材料:镍包氧化铝、镍包氧化钍
1. 溶液氢还原的基本原理
Men+
+
1 2
nH2 =
Me + nH+
(1) (2)
εMe n+/ Me与Me n+浓度的关系和εH+/ H2与pH的关系
显然,只有当金属线高于氢线时,还原过程在热力学上 才是可能的。 增大溶液氢还原总反应的还原程度有两个途径:
1.增加氢的分压和提高溶液的pH值来降低氢电位
25 oC时在水中的标准电极电位
电极电位与溶液中离子浓度之间的关系式可表示为
E=
+ RT lnc nF
25 oC时的电极电位,用
R =8.316 V·C/K·mol, F=96500 Cε
ε=
+ 0.0591 lgc n
Zn + Cu 2+= Cu + Zn 2+
Δε= εCu 2+/ Cu +(- εZn 2+/ Zn)
影响置换过程和粉末质量的因素有: 1. 金属沉淀剂的影响
从氯化铅溶液中用铁或锌置换铅
2. 被沉淀金属的影响 (1)被沉淀金属的性质是控制置换动力学的重要因素。 (2)被沉淀金属离子浓度影响粉末的粒度
3. 置换时溶液酸度要控制适当
金属置换法可应用于: 1. 从溶液中净化杂质或分离两种可溶性的金属。
δ
=
D/δ k+ D/δ
[Me1
2+]
置换过程示意图
置换反应速度= k
·A
·
D/δ k+D/δ
[Me1 2+]
=
k ·D/δ k+ D/δ
A·
[Me1 2+]
当k« D/δ时
速度= k ·A ·[Me1 2+] 即过程为化学反应所控制
当k» D/δ时 速度= D/δ ·A [Me1 2+] 即过程为扩散所控制