铝电解预焙阳极生块裂纹问题的探讨
电解铝预焙阳极炭块焙烧质量分析(5篇模版)

电解铝预焙阳极炭块焙烧质量分析(5篇模版)第一篇:电解铝预焙阳极炭块焙烧质量分析电解铝预焙阳极炭块焙烧质量分析一、前言我公司焙烧有54炉室和18炉室两个生产系统,焙烧炉是敞开式、w型环式炉,分别采用煤气和重油做燃料进行加热升温。
54室焙烧炉结构为8火道7料箱,料箱尺寸为:3440×730×4170mm,每炉平装生块84块,有三个火焰系统每个火焰系统为18个炉室。
18室焙烧炉结构为9火道8料箱,料箱尺寸为:5330×703×5240mm,每炉立装生块192块,一个火焰系统。
两系统年生产能力达到8万吨。
二、制定合理的升温曲线焙烧是炭素制品生产中的一个重要工序,生坯炭块的焙烧是生坯炭块在专门设计的加热炉内周围用填充料隔绝空气,按一定升温速度将生坯加热到1000℃---1050℃左右的生产工序。
在焙烧过程中生坯炭块主要是进行粘结剂的分解和聚合反应。
焙烧的升温速度、温度梯度及最高温度对阳极质量都有很大影响。
生坯炭块在焙烧过程中主要是粘结剂的焦化过程,即是沥青进行分解、环化、芳构化和缩聚等反应的综合过程。
具体生坯炭块在焙烧炉内焦化过程与温度加热变化如下表。
我公司根据生坯炭块在焙烧炉内焦化的过程及54室焙烧炉室、18室焙烧炉室的结构和煤气、重油的热值计算,分别对54室焙烧炉室和18室焙烧炉室采用了252小时和168小时的加热炭块升温曲线的生产过程。
移炉周期分别采用36小时和28小时。
低温预热阶段200℃左右制品粘结剂开始软化中温阶段200℃--300℃制品内吸附的水和化合水以及低分子烷烃被排出。
400℃以上变化最为突出500℃--650℃ 碳环聚合形成半焦高温烧结阶段700℃以上半焦结构分解,逐渐形成焦炭,构成乱层堆积结构基本单位的六角网状平面。
900℃以上这种二维排列的碳原子网格进一步脱氢和收缩,以后就变成了沥青焦。
燃料生产大规格炭块和炭块平装的生产要求,及用重油作为燃料生产大规格炭块和炭块立装的生产要求,该曲线容易操作又安全,尤其在排出挥发份阶段,排出的挥发份不但能充分燃烧,焦化反映比较彻底,而且对低温炉室起到一个很好的预热作用,使系热得到合理利用,烟气进入烟斗后温度平均为200 ℃,到净化系统温度在60℃--130℃,达到技术要求,有利于净化系统对烟气的净化与排放。
预焙阳极电解槽侧部碳块破损后的修复

铝 液 的水 平 电流 , 提 高 电流 效 率 , 有 效延 长 电解槽 生 会 与槽钢壳 直接接触 , 致使该 处的槽钢 壳经常发 红 , 稍 产寿命 。 疏 忽 就会 造成 钢壳熔 化 被击穿 , 发 生漏槽 事 故 。根 据 多年生产 实际经验 , 总结 出在 不停槽 的情 况下 , 使 用
2 0 1 4 正
新 疆 有 色 金 属
8 5
3 相 间短路 方 向电流保护 中 G J 的接线方式
9 0 o 接 线方 式 :
A相 G J :I j= , U x=U B c
附近 ) , 但对各种两相短路不存在死区( , 中包含非 故障相电压 , 其值较大 , 大于正常相电压 ) 。 ( 3 ) 若 已知 线路 阻抗 角 , 为 降低 死 区 , 应 尽量 使 一 一 ( 9 O 。 一 ) 。 ( 微 机保 护 一 般在 内部 固定 取 J 埘 = 一 3 0 。 或 取 = 一 4 5 。 ) 。 ( 4 ) 为 了消 除方 向元 件 的死 区 , 可采 用 记忆 作
温度较高 , 使电解槽不能形成好的侧部炉帮 , 引起的边 的接 触 。 部加工频繁和方法不当 , 会对侧部碳块造成机械破坏 ( 4 ) 用风镐将侧 部破 损处残 留的侧碳 和氧化铝料块 沿槽 钢 壳清理 刨 出 , 深度 到较硬 的底 部约 5 0 ~ 6 0 c m, 宽 而损 耗 。 ( 4 ) 砌筑 工艺及 材料 质量 。在 电解槽 大修 过程 中 , 度约 1 5 e m, 长 度视侧部 破损多 少而定 。 ( 下转 8 5 页)
2 0 1 4 钜
新 疆 有 色 金 属
8 3
预焙 阳极 电解槽侧 部碳块 破损后的修复
张保社
( 新疆有 色金属工业集 团稀有金属有限责任公 司 可可托海 8 3 6 3 0 0 )
谈预焙开槽阳极在电解槽使用中的问题

谈预焙开槽阳极在电解槽使用中的问题作者:李鸿斌程生兰来源:《中国科技博览》2013年第24期【摘要】:铝电解预焙阳极炭块是铝电解生产中的一种重要原材料,它在铝电解的生产中起着“心脏”的作用。
阳极炭块内在质量和各项技术参数的设计直接影响着电解生产工艺、经济指标以及生产成本。
本文通过对包铝在200KA预焙槽近几年的使用,探讨了使用过程中出现并注意解决的问题。
【关键词】:电解槽、电压、效应系数、开槽阳极、阳极开裂、阳极掉角。
中图分类号:TQ151.1+51、包铝是在2008年底至2009年初开始使用开槽阳极。
在200KA预焙槽上使用的,目前已使用了三年,目前使用的情况较好,200KA电解系列的生产工艺、经济指标见下表1.。
2、包铝使用的开槽方式为是在生阳极成型过程中成槽。
这种方式的主要优点是:(1)开槽无需额外设备。
(2)不象在机械加工时对生成的碳粉进行收集、运送和循环。
该方式的缺点是:(1)槽的方向受阳极块取出方向的控制。
(2)成槽后的生阳极在搬运过程中易受到损坏,增加了废品率。
这时棍道运输就不如积放式运输好。
(3)在焙烧过程中填充料常填满成型的槽并与表面粘连。
清理槽沟很麻烦,且需要专用的设备。
(4)将清理不彻底的阳极块用于电解生产中,则会增加碳尘量,从而增加了电解质电阻和降低电流效率。
3.1、要加大对开槽阳极的抽检频次及数量,对电解影响较大的抗压强度、真密度、CO2反应性等参数的监控。
包铝在使用使用开槽阳极后,将抽检的取样量由120吨取一个样本,增加到了取两个样本。
这样可以有针对进行使用炭块情况和参数的对比,做到对使用情况的有效监控。
3.2、要加强对开槽炭块的外观检查。
由于开槽阳极开槽方式决定,炭块的强度受到一定影响,再加上运输、吊装等因素造成阳极开裂、阳极掉角、开槽中夹杂的焙烧料较多,将检查不到位的阳极块用于电解生产中,则会增加碳渣量,从而增加了电解质电阻和降低电流效率。
3.2.1、阳极开裂、阳极掉角进入电解生产,则会使开槽阳极通过改善电解质的流动场,来改善电解槽的温度场。
阳极组装工序对预焙阳极质量影响及控制措施探讨
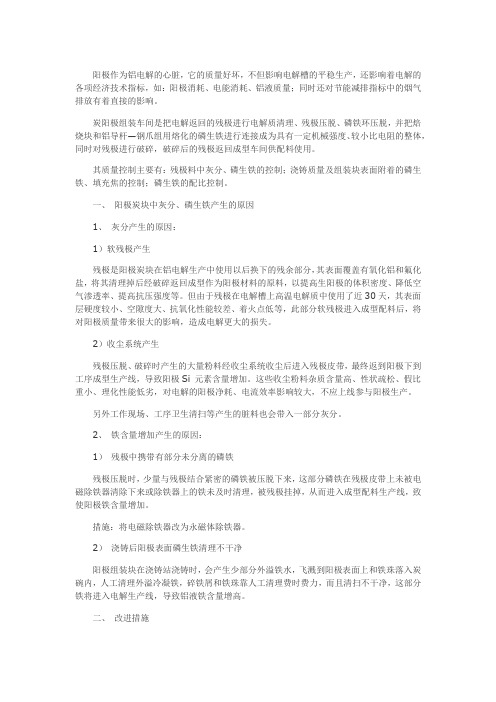
阳极作为铝电解的心脏,它的质量好坏,不但影响电解槽的平稳生产,还影响着电解的各项经济技术指标,如:阳极消耗、电能消耗、铝液质量;同时还对节能减排指标中的烟气排放有着直接的影响。
炭阳极组装车间是把电解返回的残极进行电解质清理、残极压脱、磷铁环压脱,并把焙烧块和铝导杆—钢爪组用熔化的磷生铁进行连接成为具有一定机械强度、较小比电阻的整体,同时对残极进行破碎,破碎后的残极返回成型车间供配料使用。
其质量控制主要有:残极料中灰分、磷生铁的控制;浇铸质量及组装块表面附着的磷生铁、填充焦的控制;磷生铁的配比控制。
一、阳极炭块中灰分、磷生铁产生的原因1、灰分产生的原因:1)软残极产生残极是阳极炭块在铝电解生产中使用以后换下的残余部分,其表面覆盖有氧化铝和氟化盐,将其清理掉后经破碎返回成型作为阳极材料的原料,以提高生阳极的体积密度、降低空气渗透率、提高抗压强度等。
但由于残极在电解槽上高温电解质中使用了近30天,其表面层硬度较小、空隙度大、抗氧化性能较差、着火点低等,此部分软残极进入成型配料后,将对阳极质量带来很大的影响,造成电解更大的损失。
2)收尘系统产生残极压脱、破碎时产生的大量粉料经收尘系统收尘后进入残极皮带,最终返到阳极下到工序成型生产线,导致阳极Si 元素含量增加。
这些收尘粉料杂质含量高、性状疏松、假比重小、理化性能低劣,对电解的阳极净耗、电流效率影响较大,不应上线参与阳极生产。
另外工作现场、工序卫生清扫等产生的脏料也会带入一部分灰分。
2、铁含量增加产生的原因:1)残极中携带有部分未分离的磷铁残极压脱时,少量与残极结合紧密的磷铁被压脱下来,这部分磷铁在残极皮带上未被电磁除铁器清除下来或除铁器上的铁未及时清理,被残极挂掉,从而进入成型配料生产线,致使阳极铁含量增加。
措施:将电磁除铁器改为永磁体除铁器。
2)浇铸后阳极表面磷生铁清理不干净阳极组装块在浇铸站浇铸时,会产生少部分外溢铁水,飞溅到阳极表面上和铁珠落入炭碗内,人工清理外溢冷凝铁,碎铁屑和铁珠靠人工清理费时费力,而且清扫不干净,这部分铁将进入电解生产线,导致铝液铁含量增高。
预焙阳极生坯质量控制探究
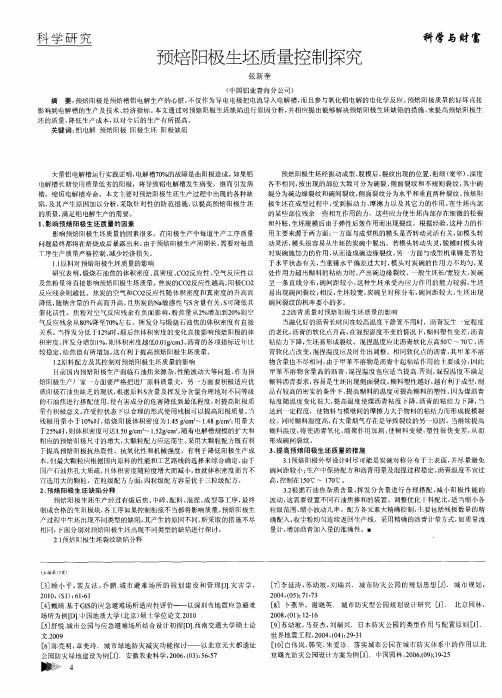
坯的质量 , 降低生产成本 , 以对今后的生产宵所提高。 关键 词: 铝电解 预焙 阳极 阳极生士 不 阳极缺陷
大 量 铝 电解 槽 运 行 实 践证 明 , 电解 槽 7 0 % 的故 障是 由阳 极 造 成 。 如 果 铝 电解槽长期使用质景低劣的阳极,将导致铝电解槽发生病变,继而引发病
Байду номын сангаас
甲苯不溶 物含量 高的沥青 , 混 捏温 度也应适 当提高 . 否则, 混捏温度 不满 足 糊 料沥青要求, 容易是生坯出现侧面裂纹 。 糊料塑性越好 , 越仃利于成型 , 制 品何较高的密实的条件 F, 提高糊料的温度可提 高糊料的塑性 。 冈为煤沥青 粘度随温度变化很大, 提高温度 使煤沥青粘度 卜 降, 沥青的粘结力 F 降, 当
的质 量 , 满 足 铝 电解 生 产 的 需要 。
裂分为碗边缘裂纹和碗 间裂纹, 侧 面裂纹分为水平和垂直两种裂纹。 于 ! ; ! 焙阳 极生坯在成型过程中, 受到振动力、 摩擦力以及其它 力的作 用, 在生坯内部
1 、 影响预焙阳极生坯质量的因素 影 响预焙阳极生坯质量的因素很多,在阳极生产 巾每道生产工序质量 『 u J 题最终部将在焙烧成后暴露 出来。 由于预焙阳极生产周期长 , 需要对每道 T序生产质节严格控制 , 减少经济损失。 1 1 原料 对 预 焙 阳极 生 坯 质量 的 影 响 研 究表 明, 煅烧 石油焦的体积密度、 真密度 、 C 02 反应性、 空气反应性 以 及 焦粉 最将 直 接 影 响预 焙 阳极 生 坯质 罩 。焦 炭 的C 02 反应性越高, 阳 极C 02 反应残余则越低。焦炭 的空气 ̄ l l C O2 反应性随体积密度和真密度的升高而 降低, 随钠含 量的升 高而升高, 目 焦炭 的N a 敏感性 与S 含量有关, s 可降低其 倦化活性 。焦粉对空气 反应残余有负面影响, 粉焦量从2 %增加到2 0 %则空 气 反应残余从8 0 %降 7 0 %左右 。挥发分与煅烧 石油焦 的体积密度有直接 关系。 j 挥 发分低 于l 2 %时, 煅后焦体积密度 的变化直接影响预焙阳极的体 积密度。 挥 发分增加1 %, 则体积密度越低O . O 1 c m3 。 沥青 的各项指标近年比 较稳定 , 结焦值仃所增加, 这仃利 于提 高预焙阳极生坯质晕。 1 . 2 原料配方及其控制对预焙阳极生坯质量的影 响 目前国内预焙阳极生产面I 临 石油焦来源杂 , 性能波动大等问题 。 作为预 焙『 j f _ I 极生产厂家 方面要严格把进厂原料质量关,另 一 方面要积极适戍优 质阳极石油焦缺乏的现状, 根据原料s 含量及挥 发分含量合理地对不同等级 的石油焦进行搭配使用 , 使冉害成分的危害 降低到最低程度 , 对提高阳极质 最仃积极意义。 受控状态 F 以合理 的形式使用饯极可以提高阳极质龟 。 当 残极用量小 于1 0 %I t , j , 焙烧 阳极 体积密 度为1 . 4 5 g / c m ~1 . 4 8 g / c m ; 用量大 于2 5 %时 , 则体积密度可达1 . 5 0g / c m 1 . 5 2 g / c m 。 随着 电解槽规模的扩大 1 相 的预焙 I j l j 极尺寸的增大 , 大颗粒配方应运而生 。 采用大颗粒配方既有利 丁提高项焙阳极抗热震性、抗氧化性和机械强度 ,有利于降低 阳极生产成 本。 仙最大颗 粒应根据国内原料的性能和工艺路线 的选择来综合确定。 由于 n { 产石油焦孔 大质疏, H . 体积密度随粒度增大而减小, 故就体秋密度而吉不 宜选 用 大 的颗 粒 。在 粒 级配 方 方面 : 四粒 级 配 方容 量 优 于三 粒 级 配 方 。
氧化掉渣裂纹掉块的危害和影响因素

在原料方面:) ( 石油焦的质量— 纯度, 1 结构, 孔度, 灰分, 杂质成分与含量等; ) ( 煤沥青质量— 2 苯不溶物, 哇淋不溶物, 析焦率, 灰分, 杂质成分与含
量等。
比表面积
0 1 一0. 2 0 1 一 0. 0 .3 8 .7 4
0. 1一 2. 0 4 9
2 阳极炭块氧化掉渣裂纹掉块的影响
因素
炭阳极在电解槽上承受电、 力、 热、 化学等作用 和物质流动运动冲击等多种因素的作用, 尤其与气 体接触、 反应和渗透是整体性的, 并非仅仅在阳极表 面。即炭阳极的上部, 下部, 内部和外部均受电、 热、 力、 化学作用及气体腐蚀, 所以炭阳极的氧化, 疏松 也是在阳极炭块的上部, 下部, 内部和侧部同时产 出。在阳极炭块使用后期, 阳极疏松, 钢爪容易脱钩
上[。 4 )
料活性的影响(。图9 5 ) 是石油焦质量对炭阳极 C 2 0
反应性的影响。 日 本直江津铝厂上世纪 7 年代末发生两次较 0 大的炭阳极在铝电解使用中大量氧化掉渣的事故, 经研究人员现场与实验室研究分析, 主要是原料中 微量元素, 氧化钠含量高引起。 美铝 D・ 贝欠茨库等人在实验室对 1 种石油焦 6 及其不同粒度分布的 12 5 种特性与炭阳极性能的影 响进行较为深入的研究。通过实验和计算确定不同 粒度分布, 不同焦子的振实体积密度、 真密度、 晶粒 度、 电阻率、 比表面积、 水银孔率、 金属杂质等对阳极 各特性的影响。表 2 D・ 为 贝尔茨库等人的部分试 验结果。从表 2 可以看出, 即便是同一种粒度范围, 不同的石油焦其特性范围有时差异一倍以上。尤其 是孔面积, 比表面积和电阻率。为了改善原料特性,
20 年我国铝产量20 00 8 多万 t 消耗碳阳极和阳 极糊 10 6 多万 t 10 , 2 多家铝厂和 10 在 0 多家铝用炭 素工厂中, 约有三分之一以上的工厂, 时常被阳极碳 块在铝电解槽使用中发生氧化掉渣和裂纹掉块所困 扰。一些阳极碳块常规指标很好, 但在铝电解槽上 应用, 氧化掉渣和裂纹掉块严重。表 1 是青海铝厂 和贵州铝厂 19 年 3 月阳极碳块的技术指标和 91 -6
电解铝用预焙阳极质量的提升策略研究

电解铝用预焙阳极质量的提升策略研究摘要:预焙阳极的质量直接影响电解铝的生产质量和效果,因此,一定要选择性能优质合格的预焙阳极,同时,在采购、生产、使用各个环节需要加强对阳极质量的实时监控,避免出现安全问题,阻碍电解铝的稳定、顺利生产。
本文通过对预焙阳极质量标准、质量检测进行分析,指出电解铝预焙阳极质量对电解铝生产的重要影响并分析应对措施。
关键词:预焙阳极;电解铝;生产;影响引言:预焙阳极个各项技术指标达标与否,关乎着电解铝是否能够高质量生产,由此可见,预焙阳极在电解槽中位置相当重要,直接影响电解铝生产环节是否能够顺利开展。
把控预备焙阳极质量需要贯穿整个电解铝阳极采购、生产及使用的各个环节,电解铝的预焙阳极质量检测工作也十分重要。
本文结合预焙阳极质量检测技术及方法分析电解铝预焙阳极质量对电解铝生产的影响及意义。
1.电解铝阳极质量检测技术现状在过去的很长一段时间,我国在电解铝阳极检测技术方面依然停留在模仿国外技术的阶段,随着科学技术的不断技术与发展,一些新型的阳极检测设备不断研发,但是仍然存在一些数据不能实时共享的问题,仅仅依靠人工采集;近几年,我国科研人员也在不断优化创新智能采集数据,但是依旧不具备智能化的控制水平,无法实时上传和共享阳极检测数据[1]。
二、电解铝预焙阳极质量对电解铝生产的重要性电解铝预焙阳极质量直接关乎着电解铝生产工作是否能够顺利正常运转,一旦预焙阳极质量出现问题,那么,在电解铝生产过程中就会出现掉渣、裂纹、氧化等问题,不利于电解铝的正常生产。
电解铝用预焙阳极质量的指标也是有一定标准的,分别有电阻率、耐压强度、灰分、热膨胀率等。
对于电解铝的电解槽而言,更加注重其导电效率及导热性能和抗氧化性,其中最明显的效果就是性能较好的阳极能够最大限度的承受电流密度,开展强化电流阳极生产,并且会降低阳极电压,很少出现炭渣及脱落裂纹等现象,增强其氧化性能、耐高温、低消耗;合格达标的阳极能够增强电解槽的稳定性能,提升电流效率,减少电能消耗,确保电解铝预焙阳极的高质量生产,所以,应该高度重视电解铝生产过程中阳极质量所造成的影响。
影响预焙阳极质量的因素分析

石油 焦是 众多 石油工 业副 产品之 一 。我国是 石油 消耗大
国 ,近 年来 国产石油和 进 口石油基本 各 占总 消耗量 的 5 0%左 右 。国产 石油 含硫 量较低 ,而 进 口石油硫 、钒等 含量 高 ,且
炭 耗 降 低 电 解 生产 成 本 , 也 可 以提 高 阳极 生 产厂 的 市场 竞 争 力 预 焙 阳极 生产 中的 各个 环 节 对 于提 高阳极 质 量均 有 重要 作 用, 本 文主要 从 影 响预 焙 阳极 质 量相 关 因素 对 质量 的 影 响逐 一进 行 分 析探 讨 。 关 键词 : 预 焙 阳极 ; 质量 ; 优化 ; 稳 定 中图 分 类号 : T Q1 2 7 . 1 1 文献 标识 码 : A 文章 编 号 : 1 1 — 5 0 0 4 ( 2 0 1 7) I 2 - ( J ( ) 5 9 — 5
中 国 金 属 通 报
影 响 预 焙 阳 极 质 量 的 因 素 分 析
孪宁 ,王素 生 ,黎文 湘 ,高 守 磊
( 索通 发 展股 份 有 限公 司,山东 临 邑 2 5 1 5 0 0)
摘
要 : 顸 焙 阳极被 称 为铝 电 解槽 的 “ 心脏 ” , 其质 量 和 工作 状 况 对铝 电解 生 产影 响 十分 巨大 。 提 高 阳极 质量 可 以减 少
( 2)同一生产厂家 的石油焦质量波 动也较大 ,如挥发分
波 动 7% ~ 1 7 %。
( 3)球状焦 ,高沥青焦时有出现。 ( 4)l mm 以下 细粉焦 比例不 断增 多 ,个别 含量 高的在
4 0 % 以上 …。 2 . 1 . 2 石 油 焦 对 预 焙 阳 极质 量 的 影 响
- 1、下载文档前请自行甄别文档内容的完整性,平台不提供额外的编辑、内容补充、找答案等附加服务。
- 2、"仅部分预览"的文档,不可在线预览部分如存在完整性等问题,可反馈申请退款(可完整预览的文档不适用该条件!)。
- 3、如文档侵犯您的权益,请联系客服反馈,我们会尽快为您处理(人工客服工作时间:9:00-18:30)。
. . 铝电解预焙阳极生块裂纹问题的探讨 丁邦平 摘 要:根据四川启明星铝业公司铝用阳极生产新线特点,对阳极生块生产中经常出现的几种裂纹以及阳极焙烧后较大的抗压强度进行了原因分析,并提出了一些具体措施,以期对生块生产有所指导。 关键词:预焙阳极、生块、裂纹 、抗压强度 1、前言 目前世界铝产量3500万吨,国内产量已达900万吨以上,产能已超过1000万吨。预焙阳极的需求将达 600万t。生块经焙烧而成预焙阳极,因而生块质量对预焙阳极的质量至关重要。就四川启明星铝业有限责任公司阳极生产而言,生块经常出现的质量缺陷主要缺损、掉棱、尺寸超标、裂纹、表面粗糙等,其中裂纹出现最多,也最难解决。本文就生块裂纹以及阳极焙烧后较大的抗压强度产生的原因进行探讨,并提出一些措施,供参考。 2、铝用阳极生产新线简介 2.1生产工艺流程新配置
中碎系统生产的四种不同粒级通过七台配料秤配料形成骨料,由集合螺旋、斗式提升机及过渡螺旋输送到四周预热螺旋加热到180—190℃,热骨料与180—190℃液体沥青连续进入到强力混捏机混捏4-5分钟,一般混捏温度在200—210℃,高温混捏后的糊料进入强力冷却机由喷入的冷却水均匀冷却到160—
液体沥青四轴预热螺旋180—190 ℃粗粒中粒粉子粉尘
抽真空高温振动成型160-170℃
强力冷却
❖阳极混捏成型新工艺配置强力混捏200-210 ℃全自动控制冷却水.
. 165℃,冷却后糊料通过振动给料机送到真空型成型机振动成型,成型制品由悬链带入冷却水池经过两小时左右水浴冷却,制品继续被悬链带入到输送辊道处,再由推进器推到辊道上输送到制品库。 2.2生产工艺新线特点 该新线特点较多,这里仅列出可能产生裂纹有关系的工艺新线特点: 选用EIRICH立式高速混捏机作为糊料混捏设备,替代传统的低速单轴或双轴卧式混捏机。 采用真空型振型机,振型温度可达160±5℃,高于非真空型温度混捏温度(145±5℃),高温振型要求高温混捏,因此混捏温度远高于非真空型混捏温度。 混捏机虽无加热装置,但因混捏机高速运行发热,由此带来混捏温度高于热骨料和沥青的混合温度。 强力冷却机不仅起到冷却作用,还对混捏后的糊料在冷却过程中再混捏。 真空成型机的真空度能达到730—745mmHg。 真空成型机的预压气囊可以在振动前充进3—5kg压力的压缩空气对糊料提前预压实。 3、问题的由来 启明星自2005年1月28日投产以来生产近两年半的时间,产量已达25万吨,期间除生产自用产品以外,还生产有不同规格的国内铝电解需求的产品以及国外俄罗斯铝电解需求的产品,各类产品都出现过不同类型的裂纹,以下列出不同阶段一些典型裂纹案例,包括焙烧后出现的可能是上工序引起的生块暗裂纹。 (1) 生产初期,成型后的生块经冷却水池冷却后出现较多的裂纹,并伴有爆裂声,一般出现在长侧面的垂直裂纹,严重时出现生块断裂。 (2) 2006年年初,焙烧制品出现大面积的裂纹,焙烧废品率超过30%,同时这批制品在组装过程中也产生裂纹,进入电解槽出现较多的阳极垂直断裂而化爪现象,导致电解槽生产不正常。 (3) 2007年年初,生产外销制品时,生块出冷却水池放置几天后出现数量较多的炭碗内部各向裂纹,并伴有爆裂声。 (4) 生产过程中有时发生长侧面横向裂纹,裂纹处非常光洁。 . . 4、预焙阳极生块裂纹种类 预焙阳极生块经振动成型、脱模后,裂纹出现的位置、粗细(宽 窄)、深度各不相同,按出现的部位大致可分为碗裂、侧面裂纹和不规则裂纹,其中碗裂又分为碗边缘裂纹、碗间裂纹和碗底部裂纹,侧面裂纹分为水平和垂直两种裂纹,见表 1。 表1 预焙阳极生块裂纹种类 序号 裂纹类型 定义 特征
1 炭碗裂纹 碗边缘裂纹 由炭碗指向斜面边坡的裂纹 长度不一,可有一条或数条裂纹
2 碗间裂纹 两个炭碗之间的裂纹 一般出现在生块上表面中部的两个炭碗,沿生块长度方向,贯穿于两个炭碗
3 碗底部裂纹 单个炭碗底部各方向裂纹 一块炭块至少出现一个有裂纹的炭碗,其长度不一,有贯穿性裂纹,可有一条或数条裂纹,
4 侧面裂纹 水平裂纹 出现在四个侧面的平行底平面裂纹 多为水平裂纹,沿生块长度方向,较细,长度从2—10cm不等,一般为连续裂纹
5 垂直裂纹 出现在四个侧面的垂直底平面裂纹 多为水平裂纹,沿生块长度方向,较细,长度从2—10cm不等,一般为连续裂纹
6 不规则裂纹 包括网裂和斜面与侧面交线处的裂纹 如蜘蛛网或放射线一样沿各方向;多发生在斜面与面积较小的侧面交界处
5、生块裂纹产生原因及采取的措施 不同类型的裂纹,其产生的原因不同,所采取的措施也不尽相同,下面分别探讨 。 5.1炭碗裂纹 5.1.1 碗边缘裂纹 预焙阳极生块在成型过程中,受到振动力、摩擦力以及其他力的作用,在生块内部的某些部位残余一些相互作用的力,这些应力使生块内部存在细微的松裂 和外胀,生块脱模后由于弹性后效作用而出现裂纹。根据经验,这种力的作用主要来源于两方面 : (1) 一方面与成型机的模头是否转动灵活有关,如模头转动灵活,模头很容易. . 从生块的炭碗中脱出;若模头转动失灵,脱模时模头将对炭碗施加力的作用,从而造成碗边缘裂纹; (2) 另一方面与成型机重锤是否处于水平状态有关,当重锤水平偏差过大时,模头对炭碗的作用力不均匀,某处作用力超出糊料的粘结力时,产生碗边缘裂纹。 针对这种裂纹,采取的措施:成型工在生块成型前必须认真检查每个模头,保证模头转动灵活;经常检查并调整成型机的重锤,使之处于水平状态 。 5.1.2碗间裂纹及碗底部裂纹 形成碗间裂纹和碗底部裂纹的因素基本相同,可以归到一起来讨论。 (1) 与生块外形尺寸和炭碗分布有关 碗间裂纹根据制品形状不同和碳碗排布方式不同,其造成废品量明显有差异。一般来讲:炭阳极窄而长;碳碗(棒孔)呈一条直线分布,有较多的碗间裂纹,相对较宽类型的炭阳极;碳碗呈对称分布,碳碗间距较大,则极少有碗间裂纹出现。碳碗间距小,强度低,在弹性后效作用下易形成中间开裂。 (2) 台阶高度 炭阳极外型因为要减少电解残极量和工艺上考虑,一般将其外型上部设计为斜面。如图1所示。
图 1 因此在振动成型过程中,将改变力的分布状态,因物料为塑性材料,外力将均匀分布向下传递,这样在斜面上产生了反支力,使力在水平方向有分力作用。 设:外作用力分布密度为:f 则水平分力分布密度:f平=aftgθ/b=f 而水平分力:F=bf . . 由上分析说明: 当有斜面时,水平方向分布密度与垂直方向分布密度相等,与斜面斜角大小无关,斜面高度越大,水平方向力越大,撤去外力后,被改变位置的颗粒力图恢复原位,形成的弹性后效越大,尤其是糊料塑性较差时,弹性后效力体现更为显著。当弹性后效力超过颗粒之间粘结力时,出现中间裂纹。另外,物料总是沿垂直于力的方向分层,使物料之间的粘结力变小,是产生裂纹的另一原因。由此可见:炭阳极生坯台阶越高,糊料塑性差,糊料粘结力小则易出现碗间和碗底部裂纹。 (3) 与糊料特性有关 胶料论指出:将焦碳颗粒粘结在一起的不是沥青,而是胶料,胶料在制品中是连续相,是制品的基质,焦碳颗粒分散在胶料中,胶料的性质由胶胞决定,小颗粒之间的粘结力大于颗粒之间的粘结力。在生产中若配方中粉子纯度低,碳粉颗粒直径大,则形成的胶料粘结力小:-0.075mm含量小,则混捏时产生的胶料少,糊料塑性差、颗粒之间的粘结力小,振动成型时易形成碳碗间的贯通性大裂纹。反之,形成的胶料粘结力强,但细粉形成的弹性后效力增大,碳碗间形成细小裂纹。另外,当融化好的沥青长时间在较高温度下静置不用时,沥青发生一定程度的老化(氧化),沥青的软化点升高,在混捏温度不变的情况下,糊料塑性变差,沥青粘结力下降,生块易形成裂纹;混捏过程若沥青量小形成的糊料塑料差,同样也形成碗间或碗底部裂纹。 (4) 振动台的频率影响 目前启明星使用的振动成型机是真空型预压式,结构主要是振动台、带真空罩和预压气囊的重锤、底部装有密封的模具等部分组成。其中振动台是双轴振动台,由激振器、减震气囊和固定夹具等部件组成,激振器一组两个偏心块与另一组两个偏心块旋转方向相反,但保持同样的旋转速度,两组偏心块的质量相同,它们在水平方向产生的惯性离心力分力在任何角度下都是大小相同,方向相反,因而互相抵消为零,而垂直方向的分力则叠加作用在振动台上。因此偏心轴振动台只具有垂直方向的定向振动。工作时的定向振动引起振动台连同上面的物料颗粒是沿一直线往复运动,所经过的路程是从一个边缘位置到另一个边缘位置(可称为幅度),其振幅是幅度的二分之一。 由于振动台不同组成部件的影响,如: . . 八个减震气囊减震性能的不同 四组固定夹具固定压力不平衡 模具、真空罩密封破坏而局部失出弹性 模具内糊料不均匀分布引起重锤的倾斜 等等因素都会导致振动台不同部位所受的激振力不一样,振动频率不同步,甚至是相反,使振动台的某些部位形成振幅极小,甚至是零振幅,某些部位振幅大,整体表现上下为非直线运动,而是一种椭圆或圆形运动,致使糊料没有被均匀振实而产生碗间或碗底部裂纹裂纹。 碗间和碗底部裂纹应采取的措施 : (1) 预焙阳极外型设计时尽可能使炭碗对称分布于上表面,并尽量避免碗间距较小。避免台阶高度过高。 (2) 生产中保持配方和沥青用量及混捏过程稳定。 (3) 沥青温度不宜过高,控制在180—185℃。 (4) 振动成型时合理布料,糊料堆积与生块外型相吻合,以减少糊料迁移量,减少中间部位内应力。 (5) 经常检查振动台各部位,使振动台处于良好的运行状态。 5.3 侧面裂纹 侧面裂纹是指发生在炭阳极四周侧面的裂纹,其基本上为水平方向和纵向裂纹。振动成型生产炭阳极,炭阳极四周总是与模具间有力的作用,在提模过程中产生摩擦力,当摩擦力大于物料间的粘结力时,即发生侧面裂纹。此外,物料沿垂直于激振力方向分层是产生侧面裂纹的另一因素。产生裂纹具体原因如下: 5.3.1 糊料温度的影响 一般来讲,糊料塑性越好,越有利于成型,制品有较高的密实度。在干料组成和沥青量一定的条件下,提高糊料的温度可提高糊料塑性,因为煤沥青粘度随温度变化很大,提高温度使煤沥青粘度下降,沥青的粘结力下降具体讲是胶料粘结力下降,当达到一定程度,使物料与模壁间的摩擦力大于物料的粘结力而形成提模裂纹。同时糊料温度高,有大量烟气存在是导致裂纹的另一原因。当继续提高糊料温度,将使沥青氧化、缩聚作用加剧,使糊料变硬,塑性很快变差,从而形成碗间裂纹,同时制品密度降低,增加振动时间会引起内部粒子结构破坏形成