QC培训及考核标准
品质、qc重点岗位培训内容
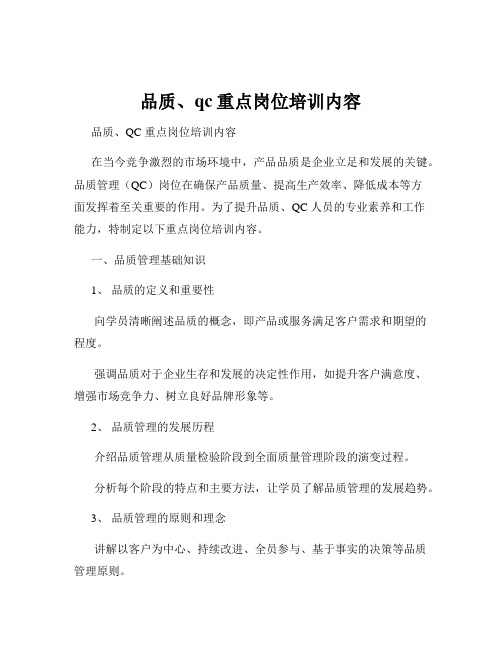
品质、qc重点岗位培训内容品质、QC 重点岗位培训内容在当今竞争激烈的市场环境中,产品品质是企业立足和发展的关键。
品质管理(QC)岗位在确保产品质量、提高生产效率、降低成本等方面发挥着至关重要的作用。
为了提升品质、QC 人员的专业素养和工作能力,特制定以下重点岗位培训内容。
一、品质管理基础知识1、品质的定义和重要性向学员清晰阐述品质的概念,即产品或服务满足客户需求和期望的程度。
强调品质对于企业生存和发展的决定性作用,如提升客户满意度、增强市场竞争力、树立良好品牌形象等。
2、品质管理的发展历程介绍品质管理从质量检验阶段到全面质量管理阶段的演变过程。
分析每个阶段的特点和主要方法,让学员了解品质管理的发展趋势。
3、品质管理的原则和理念讲解以客户为中心、持续改进、全员参与、基于事实的决策等品质管理原则。
培养学员树立正确的品质管理理念,将品质意识融入日常工作中。
二、品质管理工具与方法1、常用统计工具详细介绍直方图、柏拉图、鱼骨图、控制图等统计工具的原理和应用。
通过实际案例,让学员掌握如何运用这些工具进行数据分析和问题诊断。
2、抽样检验方法讲解抽样检验的基本概念和原理,如随机抽样、分层抽样、系统抽样等。
介绍抽样方案的制定和评估方法,以及如何根据不同情况选择合适的抽样方法。
3、六西格玛管理介绍六西格玛管理的概念、方法和实施步骤。
通过案例分析,让学员了解六西格玛在提高品质、降低成本方面的显著效果。
三、品质标准与检验流程1、品质标准的制定与解读讲解品质标准的制定依据和原则,如客户需求、法律法规、行业标准等。
培养学员准确解读品质标准的能力,确保在检验过程中能够严格按照标准执行。
2、进料检验介绍进料检验的流程和方法,包括检验项目、抽样数量、检验标准等。
强调进料检验对于保证原材料质量的重要性,以及如何处理不合格原材料。
3、过程检验讲解过程检验的要点和方法,如首件检验、巡检、末件检验等。
分析过程检验在及时发现和解决生产过程中的质量问题方面的作用。
qc小组培训学时要求

qc小组培训学时要求QC小组培训学时要求为了提升QC小组成员的专业能力和团队合作能力,培训是必不可少的环节。
本文将介绍QC小组培训的学时要求,以确保培训效果的达成。
一、培训内容QC小组培训的内容包括但不限于以下几个方面:1. 质量控制基础知识:包括质量管理体系、质量控制方法、质量工具和技术等方面的基础知识;2. 质量控制实践案例分析:通过分析真实的案例,了解质量控制在实际工作中的应用;3. 团队合作与沟通技巧:培养团队成员之间的合作意识和沟通能力,提高团队的整体效能;4. 问题解决与决策能力:通过培养问题解决和决策能力,提高QC 小组成员在面对困难和挑战时的应变能力;5. 数据分析与统计方法:了解常用的数据分析和统计方法,提高QC小组成员对数据的理解和利用能力。
二、学时要求为了保证培训的全面性和深入性,QC小组的学时要求如下:1. 每位成员需参加至少40小时的培训课程;2. 培训课程可分为多个阶段,每个阶段的学时要求不低于8小时;3. 培训课程可以通过线下面授或线上网络学习的形式进行,但线下面授课程的学时要求不得低于总学时的50%;4. 培训课程应根据成员的实际情况和能力需求进行个性化设置,确保培训的针对性和实用性;5. 培训课程应由专业的培训师或相关领域的专家进行授课,确保培训内容的准确性和权威性。
三、培训考核为了评估成员的学习效果和培训成果,培训考核是必要的环节。
培训考核的方式可以根据实际情况选择,包括但不限于以下几种形式:1. 考试:通过笔试或在线考试的方式,测试成员对培训内容的掌握情况;2. 项目实践:要求成员在实际工作中应用培训所学知识和技能,完成相关项目任务;3. 小组讨论:组织小组成员进行讨论,分享培训心得和经验,加深对培训内容的理解;4. 个人报告:要求成员撰写培训心得或总结报告,以展示对培训内容的理解和应用。
四、培训计划为了保证培训的有序进行和高效完成,制定培训计划是必不可少的。
印刷厂qc培训计划

印刷厂qc培训计划一、培训目的印刷厂QC培训计划的目的是为了提升员工的品质检验能力,使其能够熟练掌握印刷品质检验的各个环节和技能,提高印刷品的质量,满足客户的需求,使印刷品更加精美和完美。
二、培训对象本培训计划主要对象为印刷厂的QC人员,也包括其他有意向从事印刷品质检验工作的人员。
三、培训内容1. 印刷品质量标准- 了解印刷品质量标准的相关知识和标准要求- 熟悉ISO9001质量管理体系- 掌握颜色、印刷、印刷纸、装订等相关知识2. 印刷品质量检验技术- 掌握印刷品质量检验的各项技术方法,如视觉检验、触摸检验等- 学习使用各种检验设备,如色差仪、平衡仪、电子千点仪等- 熟悉印刷品的常见质量问题及解决方法3. 印刷品质量检验实践- 在实际的印刷品质量检验过程中,进行实际操作,熟悉和掌握检验技术- 学习如何建立质量文件和记录4. 印刷品质量改进- 学习印刷品质量改进的方法和技巧- 了解如何分析质量问题的根本原因,并提出改进措施5. 印刷品质量管理- 学习建立完善的质量管理体系- 掌握客户满意度调查和质量标准评估的方法6. 安全培训- 学习印刷生产中的安全管理知识- 掌握印刷设备的安全操作规程四、培训方式本培训计划采用理论与实践相结合的方式进行,包括课堂教学、现场实习、模拟操作等多种形式。
1. 课堂教学- 通过专业讲师进行课堂教学,传授相关的理论知识和技术方法2. 现场实习- 在印刷厂的实际生产环境中进行实习,学习和实践印刷品质检验技术3. 模拟操作- 采用模拟操作方式,让学员在真实环境下进行练习和操作五、培训考核为了确保培训效果,我们将采用多种形式进行培训考核,包括理论考核、实际操作考核和综合能力考核等。
1. 理论考核- 经过一段时间的学习后,进行相关理论知识的考核2. 实际操作考核- 经过实践操作后,进行实际操作的考核,测试学员的实际操作能力3. 综合能力考核- 在培训结束后进行综合能力考核,对学员的整体能力进行考核评价六、培训时间本培训计划将采用分阶段、分模块的方式进行,每个阶段的培训时间为一个月,总共为三个阶段,加上考核的时间,总时长为四个月。
QC检验能力考核管理规范

QC检验能力考核管理规范一、背景介绍为了确保产品质量和生产流程的稳定性,对于质量控制部门的QC检验人员的能力进行考核是必要的。
本文旨在制定一套QC检验能力考核管理规范,以确保检验人员的能力达到要求,提高产品质量和生产效率。
二、考核目的1. 确保QC检验人员具备必要的技能和知识,能够准确、可靠地进行产品质量检验。
2. 评估QC检验人员的工作表现,发现问题并及时进行改进。
3. 为QC检验人员提供个人成长和发展的机会。
三、考核内容1. 理论知识考核:对QC检验人员的理论知识进行考核,包括产品规格、检验标准、检验方法等。
考核方式:书面考试或在线考试。
考核内容:根据产品特点和行业标准制定的考题,包括选择题、判断题、简答题等。
2. 技能操作考核:对QC检验人员的实际操作能力进行考核,包括使用检验设备、操作检验仪器、判断产品合格与否等。
考核方式:实际操作考核。
考核内容:根据产品特点和检验要求,设置一系列的检验项目,要求考核人员独立完成。
3. 问题解决能力考核:对QC检验人员的问题解决能力进行考核,包括发现问题、分析问题原因、提出解决方案等。
考核方式:个人面试或小组讨论。
考核内容:根据实际工作情况,设置一系列的问题场景,要求考核人员进行思考和回答。
四、考核流程1. 考核计划制定:质量控制部门根据实际情况制定年度考核计划,明确考核的时间、内容和参与人员。
2. 考核准备工作:质量控制部门组织相关培训,确保考核人员具备必要的知识和技能。
3. 考核实施:按照考核计划进行考核,分别进行理论知识考核、技能操作考核和问题解决能力考核。
4. 考核结果评估:质量控制部门根据考核结果进行评估,确定考核人员的能力水平。
5. 反馈和改进:质量控制部门将考核结果反馈给考核人员,并提出改进意见和建议。
6. 能力提升计划:根据考核结果,制定个人能力提升计划,为考核人员提供个人成长和发展的机会。
五、考核记录和管理1. 考核记录:质量控制部门对每次考核进行记录,包括考核时间、内容、参与人员和考核结果等。
qc检验新人培训计划

qc检验新人培训计划一、培训目标1. 了解公司的质量方针和QC检验的重要性。
2. 掌握QC检验的基本理论知识和技能。
3. 熟悉QC检验设备的操作和维护。
4. 具备独立进行QC检验的能力。
二、培训内容1. 公司介绍和质量方针- 公司的发展历程和业务范围;- 公司的质量方针和质量目标;- QC检验对公司质量管理的重要性。
2. QC检验基本理论知识- QC检验的基本概念和内涵;- QC检验的原则和方法;- QC检验的注意事项和常见问题。
3. QC检验技能培训- 样品的接收和处理;- 实验室常用设备的操作方法;- QC检验的具体操作步骤;- QC检验结果的处理和分析。
4. 实践操作训练- 新员工在导师的指导下,进行实际样品的QC检验操作;- 熟练掌握操作方法和技巧;- 学习如何准确记录和汇报检验结果。
5. 设备操作和维护- 了解实验室常用设备的结构和原理;- 学习设备的正确使用和维护方法;- 掌握设备故障的排除和维修技能。
6. 质量管理知识- 了解质量管理体系和标准;- 学习如何根据质量管理要求进行QC检验;- 熟悉不合格品处理流程和方法。
7. 知识检测和总结- 对新员工进行知识巩固测试;- 对培训内容进行总结和复习;- 鼓励新员工提出问题和建议,促进互动和交流。
三、培训方式1. 理论与实践相结合:采用理论讲解、实验操作、案例分析等方式,深入浅出地传授知识和技能,让新员工学以致用。
2. 一对一指导:每位新员工都有一位经验丰富的导师进行一对一指导,及时纠正错误,提高培训效果。
3. 集中培训和分散培训相结合:既进行集中的培训课程,又让新员工在实验室中进行反复实践,形成肌肉记忆。
四、培训保障1. 提供必要的教材和资料,让新员工可以随时翻阅和学习。
2. 提供优质的培训设施和设备,确保培训质量和效果。
3. 严格按照培训计划进行培训,不得擅自改变或减少培训内容和时间。
五、培训考核1. 培训结束后,进行理论知识和实操技能的考核,合格方可上岗工作。
QC检验能力考核管理规范

QC检验能力考核管理规范引言概述:QC(Quality Control)检验能力考核管理规范是指对企业质量控制部门进行检验能力的评估和管理的一套规范。
通过对检验能力的准确评估和有效管理,可以提高产品质量,降低不合格品率,提升企业竞争力。
本文将从四个方面介绍QC检验能力考核管理规范。
一、考核标准的制定1.1 确定考核指标:根据企业的产品特点和质量要求,制定适合的考核指标,如检验项目的准确性、可靠性、稳定性等。
1.2 设定考核等级:根据考核指标的重要性和难易程度,将考核等级划分为不同层次,以便对不同水平的检验员进行评估和管理。
1.3 确定考核周期:根据企业的生产周期和产品特点,确定适宜的考核周期,保证考核的及时性和有效性。
二、考核方法的选择2.1 实地考核:通过对检验员的实际操作进行观察和记录,评估其检验能力的准确性和熟练程度。
2.2 文化考核:通过书面考试或者在线测试等方式,对检验员的理论知识进行考核,评估其对相关标准和规范的掌握程度。
2.3 绩效考核:通过对检验员的工作成果进行评估,如检验报告的准确性和及时性等,评估其工作效率和质量。
三、考核结果的分析与反馈3.1 考核结果的统计分析:对考核结果进行统计和分析,了解不同等级检验员的分布情况,发现问题和不足。
3.2 考核结果的反馈:将考核结果及时反馈给检验员本人,指出其优点和不足,并提出改进意见和建议。
3.3 考核结果的应用:根据考核结果,对不同等级的检验员进行分类管理,提供相应的培训和发展机会,促进其能力的提升和成长。
四、考核管理的持续改进4.1 定期评估和修订:定期对QC检验能力考核管理规范进行评估和修订,根据实际情况进行相应的调整和改进。
4.2 培训和提升计划:根据考核结果和企业的需求,制定相应的培训和提升计划,提高检验员的技能水平和专业素质。
4.3 经验分享和交流:建立检验员之间的经验分享和交流机制,促进彼此之间的学习和进步,提升整个团队的检验能力。
药厂qc检验培训计划
药厂qc检验培训计划一、培训目标1. 帮助员工了解质量控制检验的重要性,强化他们的质量意识和责任感;2. 帮助员工掌握相关检验方法和技能,提高他们的工作质量和效率;3. 帮助员工加强团队合作意识,提升整体质量管理水平。
二、培训对象本培训计划主要面向药厂QC部门的检验人员及相关质量管理人员。
三、培训内容1. 质量控制基础知识- 质量控制的概念和重要性- 质量控制的基本原则- 质量控制的流程和方法2. 检验方法和技能- 原材料的抽样和检验- 半成品和成品的检验方法- 化学、生物学和物理学检验方法- 仪器设备的使用和维护3. 质量控制的管理- 质量记录和文档管理- 质量异常处理和改进措施- 质量问题的追踪和整改4. 团队合作和沟通- 团队合作意识和精神- 良好的沟通与协调能力- 紧急事件处理和危机管理1. 理论讲授:通过课堂教学,员工学习质量控制的基本知识和相关检验方法;2. 实际操作:员工在实际生产环境中进行模拟操作,学习实际的检验技能;3. 现场考察:前往其他药厂或质量管理优秀企业进行现场考察,学习其先进的质量管理经验;4. 案例分析:通过真实案例分析,帮助员工理解和解决质量控制中的问题;5. 交流互动:组织员工进行小组讨论、研讨会和角色扮演等形式,促进员工之间的交流和学习。
五、培训流程1. 培训前准备- 确定培训内容和形式- 确定培训时间和地点- 确保培训设备和材料准备充分2. 培训实施- 理论讲授和实际操作- 现场考察和案例分析- 交流互动和小组讨论3. 培训总结- 总结培训效果和反馈意见- 梳理培训内容和记录资料- 制定培训总结报告和未来改进计划六、培训考核1. 考核方式:采用测试题、实际操作和案例分析等多种方式进行考核;2. 考核内容:考核员工的理论知识掌握情况、实际操作能力和解决问题的能力;3. 考核标准:根据培训内容和目标制定考核标准,确保员工的学习成果。
1. 培训效果评估:通过员工的考核成绩、实际操作表现和反馈意见等多方面评估培训效果;2. 培训改进计划:根据评估结果,制定未来的培训改进计划,不断提升培训质量和水平。
qc基础知识培训计划
qc基础知识培训计划一、背景介绍质量控制(Quality Control,简称QC)是一种生产活动中对产品质量进行检验、控制和管理的实际活动。
通过QC的实施,可以提升产品质量,降低成本,提高客户满意度,最终实现企业的长期发展和竞争力。
因此,加强对QC的培训和知识普及,对于企业的发展至关重要。
二、培训目标1.了解QC的基本概念和原理2.掌握QC的实施方法和工具3.了解QC在企业生产中的作用和重要性4.能够运用所学知识进行实际工作三、培训内容1. QC基础概念- 什么是质量控制- QC的起源和发展- QC的作用和意义2. QC的基本原理- PDCA循环- 6σ管理- TQM理论3. QC的实施方法- 抽样检验方法- 测量精度和稳定性- 测量系统分析4. QC的工具与技术- 控制图- 标准化工具- 因果分析法5. QC在企业中的应用- QC在生产流程中的应用- QC在产品质量管理中的应用- QC在服务质量管理中的应用6. 案例分析和讨论- 讲解一些企业实际案例,以深入理解QC的应用和实施过程- 开展讨论,共同探讨如何在实际工作中应用所学知识7. 讲师带领学员进行实际操作- 实验设备的使用- 数据采集方法- 数据分析和处理8. 结业考核四、培训方法1. 组织专家授课由相关领域的专家进行讲解,以系统的理论知识为主,对QC的概念和原理进行详细讲解。
2. 现场操作演练引入实际的操作案例,让学员亲自动手进行实验,体会QC的应用方法和技巧。
3. 案例分析讨论分析真实案例,让学员通过讨论的方式加深对QC的理解和应用。
4. 结业考核通过考核学员对QC基础知识和实际操作的掌握情况,以检验培训效果。
五、培训时间和地点时间:预计为期一周(具体时间可根据实际情况而定)地点:企业内部会议室或培训机构六、培训对象和要求培训对象:企业内部相关部门员工要求:具有一定的专业知识基础和实际工作经验,能够积极参与培训活动并将所学知识运用到实际工作中。
qc质量管理培训内容
qc质量管理培训内容
质量控制(QC)是一种关键的管理过程,旨在确保产品或服务的一致性和质量。
为了保证高质量的产品和服务交付,组织需要进行质量管理培训,以提高员工在质量控制方面的技能和知识。
以下是一些常见的质量管理培训内容:
1.质量概述:培训应该以讲解质量管理的基本概念和原则为开始。
这将使员工
了解质量的重要性和如何对其进行管理。
2.质量体系标准:培训应该介绍与质量相关的国际标准,如ISO 9001。
员工应
该了解标准的要求以及如何应用它们于实际情景中。
3.过程管理:培训应该强调过程管理在质量控制中的重要性。
员工应该学习如
何设计和改进流程,以确保产品和服务的一致性。
4.数据分析方法:培训应该包括各种数据分析方法,如趋势分析、根本原因分
析和统计过程控制。
这些工具将帮助员工识别质量问题的根本原因,并采取适当的纠正措施。
5.质量工具和技术:培训应该介绍各种质量工具和技术,如质量检查表、直方
图和散点图。
这些工具可以帮助员工识别和解决质量问题。
6.团队合作和沟通:质量管理需要团队的合作和有效的沟通。
培训应该强调团
队合作和沟通技巧的重要性,以确保良好的质量管理实践。
7.持续改进:培训应该鼓励员工积极参与质量管理的持续改进活动。
员工应该
学习如何识别改进机会,并使用适当的工具和方法进行改进。
质量管理培训的目标是使员工具备识别和解决质量问题的能力,并致力于持续
改进。
通过提供高质量的培训,组织可以提高产品和服务的质量,增强客户满意度,并增强竞争力。
qc能力培训计划
qc能力培训计划一、培训内容1. QC知识培训:介绍QC的基本概念、原则和方法论,包括六西格玛、质量管理工具等内容。
2. 产品知识培训:对产品的特性、工艺流程、质量标准等进行详细介绍,使员工对产品有深入的了解。
3. 质量管理工具培训:介绍各种质量管理工具的使用方法,包括流程图、因果图、帕累托图、控制图等。
4. 质量审核培训:对质量审核的方法和流程进行详细介绍,包括内审、外审等内容。
5. 解决问题的方法培训:介绍如何对质量问题进行分析、定位和解决的方法和工具。
二、培训目标1. 提升员工的QC知识水平,使其具备一定的质量管理理论基础。
2. 增强员工对产品的理解和把控能力,提高对产品质量的重视程度。
3. 掌握一定的质量管理工具和方法,能够灵活运用于实际工作中。
4. 培养员工的质量意识和问题解决能力,使其能够快速、准确地应对质量问题。
三、培训方式1. 理论学习:通过课堂教学、培训讲座等形式,向员工介绍QC知识和方法。
2. 实践操作:通过实际操作、案例分析等方式,模拟员工在实际工作中遇到的质量问题,进行解决。
3. 讨论交流:组织员工进行讨论、经验交流,分享质量管理的实际应用经验。
4. 考核评估:通过考试、实际操作等方式对员工进行能力评估,检验培训效果。
四、培训计划1. 培训时间:预计培训周期为3个月,每周进行2次培训,每次培训2小时。
2. 培训内容:第1-4周:QC知识培训,包括质量管理原则、QC工具、质量审核等内容。
第5-8周:产品知识培训,包括产品特性、工艺流程、质量标准等内容。
第9-12周:质量管理工具培训,包括流程图、因果图、帕累托图、控制图等内容。
3. 培训方式:第1-4周:理论学习+实践操作,强调对QC知识的学习和运用。
第5-8周:实践操作+讨论交流,重点放在产品的实际情况分析和解决。
第9-12周:理论学习+考核评估,对员工进行能力评估和培训总结。
五、培训材料1. 教材:为员工准备相关的教材和参考书籍,供其在课后复习和深入学习。
- 1、下载文档前请自行甄别文档内容的完整性,平台不提供额外的编辑、内容补充、找答案等附加服务。
- 2、"仅部分预览"的文档,不可在线预览部分如存在完整性等问题,可反馈申请退款(可完整预览的文档不适用该条件!)。
- 3、如文档侵犯您的权益,请联系客服反馈,我们会尽快为您处理(人工客服工作时间:9:00-18:30)。
QC岗位培训教材及考核标准目录简介一.标准产品检验流程。
QC需要熟悉的公司检验操作流程。
二.重点客户与重点产品全程跟踪检验细则。
QC需要熟悉全程跟踪的每一步骤。
三.成品验货标准步骤。
QC需要熟练掌握操作步骤和检验方法。
四.半成品及材料检验步骤。
QC要熟练掌握操作步骤。
五.业务部门与品保部门在发生质量问题时的分工与合作。
QC遇到问题时与业务部门的责权分工。
六.QC考核。
QC考核内容/方式及考核表单。
2一标准产品检验流程1.业务部门将客户认可的确认样品及相关的资料转交给品保部门业务部门需交付给品保部门的资料包括:订单验货联随附检查清单(参见附件《订单检查表》)/ 确认样品/ 检验测试标准/ 包装盒实物或彩稿或详细说明。
若有修改需及时通知品保部门。
若是重点产品或重点客户特殊要求均必须书面通知品保部门。
2.品保部门对收到的样品及相关的资料进行核对,对有疑问的地方向业务部门反馈品保经理收到资料后依《订单检查表》审核资料是否完整,并将资料交付给依照《QC职责分配表》挑选出的具体负责QC。
QC应仔细核对确认样品与验货资料是否相符,验货资料是否完整,测试标准是否详尽可行。
若有缺失或疑问应书面向业务部门反馈。
在资料未补充完整的前提下QC不能安排终期验货。
3.品保部门与工厂联系确认验货时间品保部门在收到订单验货联后按照交货时间提前两周(少于两周则为当日)与工厂相关人员联系,确认终期验货时间。
发现有推迟交货的可能或情况必须马上书面通知业务部门,并说明工厂给出的理由。
经与业务部门合作再次确认交货时间后,保持与工厂的联系直到按时终期验货。
4.QC到厂验货QC出发前,需检查清楚是否所有必须品都已经齐备,包括文件,检验工具等(参见附件《订单检查清单》)。
QC到达工厂后对产品数量、质量检验完成后出据验货报告,当日或次日晨将有工厂品保人员签名的报告回传到公司品保部门。
按照业务部门的要求带回出货样。
若验货结果判为拒收,还需要及时向业务部门汇报。
若工厂同意返工必须同时汇报给业务部门确定的再次验货时间。
按照业务部门或品保经理的要求拍照或带回不良品样品。
若工厂拒绝返工则QC必须在验货报告上注明“工厂拒绝返工”及“是否提供不良品样品”。
按照业务部门或品保经理的要求拍照或带回不良品样品。
5.拒收需重验QC对于因质量问题或其他需重新验货的工厂必须提高重视,除重点检查问题是否解决外,对产品其他的检验必须按照验货标准步骤执行检验测试标准。
3二重点客户与重点产品全程跟踪检验细则对于重点客户与重点产品,业务部门从开始就要与品保部门密切合作,安排全程跟踪检验确保保质保量如期完成。
实施细则如下:重点客户定义:新合作的客户;长期大量订单合作客户;重要活动不允许延期的订单客户;其他经业务主管签核的客户。
重点产品定义:新开发的产品;重要活动不允许延期的产品;生产工序繁多易延期或返工的产品;生产厂家产能可能不足的产品;其他经品保经理签核的产品。
1.业务部门对重点产品或重点客户特殊要求均必须在业务主管签署后书面通知品保部门;2.确认样品及相关资料由业务部门召集品保部门共同研究,消除隐患;3.业务部门与相关工厂协调安排产前材料检验、生产计划执行、产中流程检验、生产样品核对、成品终期质量检验的日期;4.品保部门安排资深QC进行产前材料检验、生产计划执行、产中流程检验、生产样品核对、成品终期质量检验。
对于发现的问题及时通知业务部门并在业务部门协助下与生产厂商沟通解决。
5.品保部门在安排验货人员时除挑选资深QC外,还应安排助手并使其熟悉掌握产品知识。
消除人为失误的几率。
6.物流部门对货物的运输实时掌握直到安全进入客户仓库。
发现问题在解决的同时及时反馈给业务部门。
其他流程同“标准产品检验流程”4三半成品及材料检验步骤QC到厂由相关人员带领到达货物堆放地点开始检验工作。
1.按照零件表清点数量;2.按照抽样标准(MIL-STD-105E,General LevelⅡ,CR 0/MA 2.5/MI 4.0除非另有通知)抽出规定数量的样品;3.依照相应产品类别检验标准对所有抽样产品进行外观检查,功能测试依相应产品类别检验标准规定的数量和方法测试;需要组装的部件一定要组装。
4.验货结束,清点不良品数量并分类,与工厂相关人员一同核对,填写检验报告由工厂品保人员加签后传真回公司。
5.了解生产产品实际需要的时间,判断有无可能逾期并向业务部门汇报。
参考资料:检验知识讲义:《常规检验程序培训》,《抽检培训》,《体积重量手感测试》。
5四成品验货标准步骤QC到厂由相关人员带领到达货物堆放地点开始检验工作。
1.清点数量;2.核对箱唛;3.按照抽样标准(MIL-STD-105E,General LevelⅡ,CR 0/MA 2.5/MI 4.0除非另有通知)抽出规定数量的样品;a)抽样数量:按MIL-STD-105E,General LevelⅡ,CR 0/MA 2.5/MI 4.0的要求(除非另有通知),具体请见附件。
b)样本数量:要验货结果准确反映实际情况,抽查的样本必须随机。
准则如下:i.抽查的箱数为总箱数的平方根加1例:如总箱数为81,要抽查的箱数为√81+1=10即随机抽出10箱。
ii.从随机抽出的箱,平均抽出要抽查的样本数量。
例如随机抽出10箱而要抽查的样本数量为300。
每箱抽出的样本数量为30。
iii.在每箱抽出样本数量时亦要随机。
4.记录外箱尺寸,并与订单验货联进行核实;5.依要求做摔箱测试;摔箱数量:2箱;摔高:76厘米,箱重≤9公斤;61厘米,9公斤<箱重≤18公斤;45厘米,18公斤<箱重≤27公斤。
摔法:每箱依一角三边六面顺序从规定高度自由落地。
判别:产品或产品包装{彩盒/PVC盒或其他}有一只破损即为不合格。
6.检查外箱有无污损,检查内包装有无污损;7.依照相应产品类别检验标准对所有抽样产品进行外观检查,功能测试依相应产品类别检验标准规定的数量和方法测试;注意:不良品一定要贴箭头标,单独摆放在面前,以防协助验货的工人错拿或调换。
所有测试设备都要检测确保功能良好。
8.验货结束,清点不良品数量并分类,与工厂相关人员一同核对,用钢笔/签字笔/圆珠笔填写检验报告由工厂品保人员加签后传真回公司。
参考资料:检验知识讲义:《常规检验程序培训》,《抽检培训》,《体积重量手感测试》。
6五业务部门与品保部门在发生质量问题时的分工与合作发现质量问题后,品保部门的职责分工是及时反馈、了解原因、与厂方探讨解决方案、监督质量改进方案的落实。
是业务部门了解工厂实际情况的最有效途径,也是协助业务部门判断质量问题的关键来源。
对质量问题有决定权。
品保部的职责是:1)对产品的放行与否有决定权;2)如果产品不能放行,必须先下令停止生产,并将问题产品隔离;3)发问题报告书;4)了解原因、与厂方探讨解决方案;5)监督现场的返工;6)返工后的产品检验;7)如果合格,则放行产品;8)监督改进方案的落实,并确保在问题真正被彻底解决后,才允许生产的重新开始。
发现质量问题后,业务部门的职责分工是判断问题的严重程度是否导致客户损失、决定是否需要向客户通报、与工厂和品保部门沟通确定解决方案。
是品保部门在工厂工作时的指示来源,也是解决问题的信息枢纽。
对非质量问题有决定权。
7六QC考核新QC培训分为基础知识培训和技能培训。
基础知识培训由讲师参照讲义《常规检验程序培训》,《抽检培训》,《体积重量手感测试》讲解,当堂由讲师现场出题目考核,95分以上为合格可进入技能培训。
95分以下需要补训,需补训的人员在一周后再次安排考核。
两次补考均未通过将由品保部上报管理部不与其签约。
技能培训由资深QC带领新QC到厂现场实际操作/指导完成。
具体安排是:一. 新QC完全在旧QC的带领下工作,此时,新QC只在旁边学习,不能放行产品。
两周后即安排首次考核并填写《QC考核记录单》。
需补训的人员在一周后再次安排考核。
两次补考均未通过将由品保部上报管理部不与其签约。
通过考核的新QC在资深QC监督下进行两周的实习,新QC有权放行产品,但旧QC对最终的结果负有责任。
并需通过最终考核方可以独立上岗。
在职QC年度安排考核并填写《QC考核记录单》;凡需补训的人员在一周后再次安排考核。
两次补考均未通过将由品保部上报管理部作辞退处理。
考核记录单存档成绩将列为QC绩效考核的重要参数。
考官由稽核课随机抽调人员担任,但考核考官不得再次担任同一QC的补考考官。
8新员工考核记录单姓名:所在部门:QC 加入时间:评分标准:每一项熟练完成得满分,发现预设问题依熟练程度可得一半至满分,未发现问题不得分。
每次考核获得满分90%(含)为合格。
序号培训内容实际培训日期被培训者签名培训者签名分数比例实际成绩是否通过考核备注1 资料检查102 与业务沟通103 与工厂联系验货时间104 清点货物105 核对外箱106 抽样207 量外箱尺寸108 包装检查109 产品检查9.1 外观检查9.2 功能检查9.3 技术测试20 20 2010 不良品判别/分类2011 验货报告2012 出货样品处理10结论。