酸化腐蚀;缓蚀剂能力;缓蚀率
缓蚀剂的缓蚀效率及其评价方法(最新版)

缓蚀剂的缓蚀效率及其评价方法(最新版)Safety management is an important part of production management. Safety and production are inthe implementation process( 安全管理 )单位:_________________________姓名:_________________________日期:_________________________精品文档 / Word文档 / 文字可改缓蚀剂的缓蚀效率及其评价方法(最新版)缓蚀剂的评价采用的是金属腐蚀速率的测试方法,即测定金属在添加一定缓蚀剂的腐蚀介质中的腐蚀速率,并与此金属在不加缓蚀剂的腐蚀介质中的腐蚀速率进行对比,从而确定缓蚀效率和最佳使用条件。
(1)缓蚀剂的缓蚀效率缓蚀效率是表征缓蚀剂性能的重要参数,定义为:式中v0——未加缓蚀剂时金属的腐蚀速率,单位为g/(m2·h)或mm/a等;v——加缓蚀剂后金属的腐蚀速率,单位为g/(m2·h)或mm/a等;η——缓蚀剂的缓蚀效率。
(2)缓蚀剂缓蚀效果的评价方法①实验室测试方法:a.失重法失重法是最常见的、最简单的测定缓蚀剂缓蚀效果的方法。
它通过实验室模拟腐蚀介质环境和现场试验来进行。
分别测取金属在未加缓蚀剂和加入缓蚀剂后的腐蚀介质中的腐蚀失重,从而确定其腐蚀速率,再比较缓蚀剂的缓蚀效果。
缓蚀剂配方的筛选、浓度、用量的选用、失效期的测定及复配物的选择也可采用失重法。
b.电化学法电化学方法采用电化学极化手段,利用电化学动力学理论和测试手段,通过对缓蚀剂加入前后在腐蚀介质中金属表面的极化特征的研究,以及利用T如l曲线外推法和极化电阻法对金属腐蚀速率的测定,来评价金属在缓蚀剂中缓蚀性能的优劣。
c.光谱法和表面谱法近年来,采用光谱法和表面谱法对添加缓蚀剂后金属表面膜结构的作用的研究,也已成为评价缓蚀剂的手段和技术。
硝酸对碳钢及不锈钢的腐蚀特性及缓蚀剂
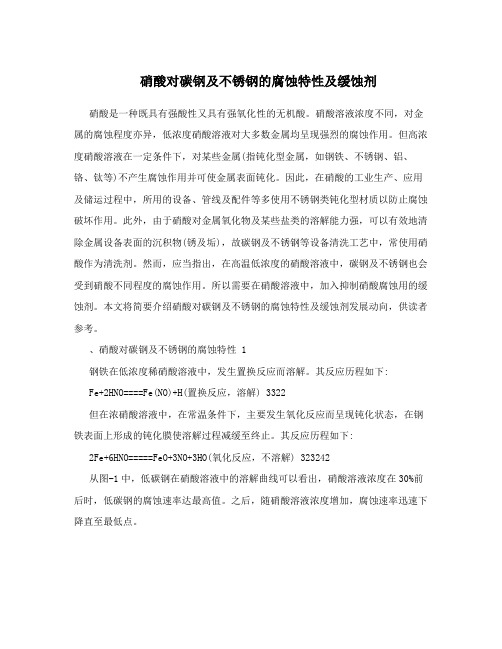
硝酸对碳钢及不锈钢的腐蚀特性及缓蚀剂硝酸是一种既具有强酸性又具有强氧化性的无机酸。
硝酸溶液浓度不同,对金属的腐蚀程度亦异,低浓度硝酸溶液对大多数金属均呈现强烈的腐蚀作用。
但高浓度硝酸溶液在一定条件下,对某些金属(指钝化型金属,如钢铁、不锈钢、铝、铬、钛等)不产生腐蚀作用并可使金属表面钝化。
因此,在硝酸的工业生产、应用及储运过程中,所用的设备、管线及配件等多使用不锈钢类钝化型材质以防止腐蚀破坏作用。
此外,由于硝酸对金属氧化物及某些盐类的溶解能力强,可以有效地清除金属设备表面的沉积物(锈及垢),故碳钢及不锈钢等设备清洗工艺中,常使用硝酸作为清洗剂。
然而,应当指出,在高温低浓度的硝酸溶液中,碳钢及不锈钢也会受到硝酸不同程度的腐蚀作用。
所以需要在硝酸溶液中,加入抑制硝酸腐蚀用的缓蚀剂。
本文将简要介绍硝酸对碳钢及不锈钢的腐蚀特性及缓蚀剂发展动向,供读者参考。
、硝酸对碳钢及不锈钢的腐蚀特性 1钢铁在低浓度稀硝酸溶液中,发生置换反应而溶解。
其反应历程如下:Fe+2HNO====Fe(NO)+H(置换反应,溶解) 3322但在浓硝酸溶液中,在常温条件下,主要发生氧化反应而呈现钝化状态,在钢铁表面上形成的钝化膜使溶解过程减缓至终止。
其反应历程如下: 2Fe+6HNO=====FeO+3NO+3HO(氧化反应,不溶解) 323242从图-1中,低碳钢在硝酸溶液中的溶解曲线可以看出,硝酸溶液浓度在30%前后时,低碳钢的腐蚀速率达最高值。
之后,随硝酸溶液浓度增加,腐蚀速率迅速下降直至最低点。
图-1 低碳钢(C 0.03%)的腐蚀速率与硝酸浓度的关系(常温)不锈钢及其它合金钢在硝酸溶液中,在一般条件下,具有较好的耐蚀性能。
然而,当系统温度升高时,则随硝酸溶液浓度增加,不锈钢亦会受到不同程度的腐蚀(参考图-2,表-1)。
图-2,硝酸中高级不锈钢的腐蚀速率(沸点)表-1,不锈钢在发烟硝酸中的腐蚀情况比较(71?)2 h) 腐蚀速度(g/m不锈钢白色发烟硝酸红色发烟硝酸 (AISI)304 3.368 4.964304L 4.255 -309 1.684 2.659310 1.773 3.811316,316L 4.432 -321 5.319 8.865347 5.141 4.432410 4.077 6.294430 2.925 3.81120Cr29Ni 0.975 -2、硝酸缓蚀剂硝酸缓蚀剂的开发研究工作始于二十世纪初,早期曾提出生物碱、硫醇、糖类等有机化合物。
醋酸的腐蚀特性及缓蚀剂
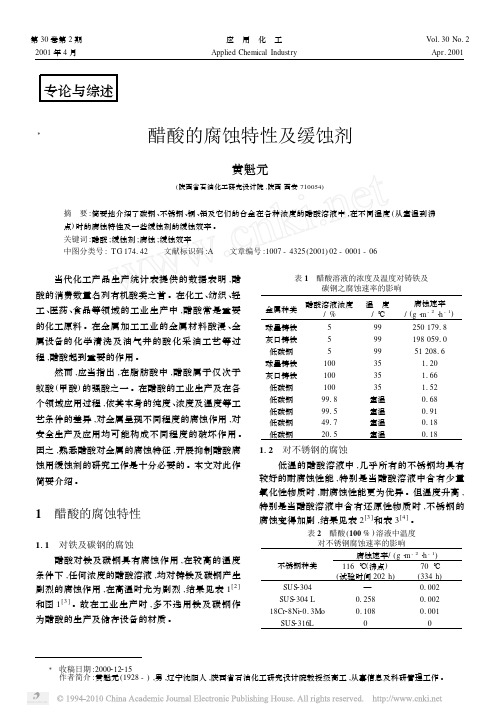
112 对不锈钢的腐蚀
低温的醋酸溶液中 ,几乎所有的不锈钢均具有
较好的耐腐蚀性能 ,特别是当醋酸溶液中含有少量
氧化性物质时 ,耐腐蚀性能更为优异 。但温度升高 ,
特别是当醋酸溶液中含有还原性物质时 ,不锈钢的
腐蚀变得加剧 ,结果见表 2[3 ]和表 3[4 ] 。
121940 1281609 231754 11347
1 526129 810147
01036 0185 01038 01038 1114 119
加入缓蚀剂后之腐蚀 速率/ (g·m - 2·h - 1)
11347 11018 01269 01269 11887 121692
醋酸在常温条件下 ,对纯铝基本上不腐蚀 ,随温 度升高腐蚀逐渐加剧 ,1 %的稀醋酸溶液在沸腾温度 时 ,对铝之腐蚀速率为常温时的百倍以上 ,结果见图 3[6 ] 。醋酸溶液浓度增加 ,一般其腐蚀速度趋向下 降 ,结果见表 5[6 ] 、表 6[1 ] 。此外 ,铝的纯度对腐蚀速 率也有一定影响 ,纯度高的铝 ,在表面上可形成致密 的保护膜 ,屏蔽腐蚀作用 。纯度低的铝 (含有铁 、硅 、 锰 、镁 、锌 、钼及铝之盐类等杂质) 在表面上 ,则形成 疏松的膜 ,屏蔽作用差 ,而腐蚀性能下降 。但纯铝的 强度低 ,为提高其强度 ,在保持足够的耐腐蚀性能的 前提下 ,常使用各种铝合金作为结构材质 (1100 , 3003 ,5052 ,5154 等铝合金) 。
(2)
31935
89 Cu22. 5 Fe24. 5 Al24 Mn 01068 01290 01892
316
冰醋酸 11813 (1)
(2)
01130
缓蚀剂的缓蚀效率测定原理

缓蚀剂的缓蚀效率测定原理
缓蚀剂的缓蚀效率测定原理是通过在实验条件下将缓蚀剂添加到腐蚀介质中,然后观察或测定相应的腐蚀指标来评价缓蚀效果。
常用的测定方法包括质量损失法、电化学法和电化学阻抗法等。
以下是其中一种常用的原理介绍:
质量损失法原理:
1. 实验前将待测金属样品的初始质量精确称重,并测定其表面积。
2. 将待测金属样品置于特定环境中(如腐蚀溶液),在一定时间内使其与腐蚀介质接触。
3. 完成一定时间后,将金属样品取出,洗净并通过干燥至恒定质量。
4. 重新称重金属样品并计算其质量损失,用于评估缓蚀效果。
缓蚀效率(%)=(1-质量损失/质量损失对照样品)×100%
质量损失法的原理是测量金属样品与腐蚀介质接触后经过一定时间的质量变化,通过比较不添加缓蚀剂的对照样品和添加缓蚀剂的样品的质量损失,来确定缓蚀效率。
质量损失越小,说明缓蚀效果越好。
需要注意的是,该原理存在一些局限,如实验条件对结果的影响较大,不同样品之间的比较相对准确性较差等。
因此,在具体应用时,结合其他测试方法,综合
评估缓蚀效率更为准确。
缓蚀剂性能的测试和评定

缓蚀剂性能的测试和评定概述缓蚀剂是一种用于防止金属被腐蚀的添加剂。
在金属加工、运输和存储过程中,金属会与各种物质接触,如水、盐、氧气等,容易受到腐蚀的影响。
缓蚀剂可以减少金属腐蚀的发生,并增加金属的使用寿命。
该文档旨在介绍缓蚀剂的性能测试和评定方法。
测试方法1. 电化学测试法电化学测试法是一种常用的缓蚀剂性能测试方法。
它通过测量金属在缓蚀剂存在下的电位变化,来评定不同缓蚀剂的腐蚀保护能力。
电化学测试法的实验步骤如下:1.准备测试样品。
将待测试的金属样品切成适当的大小,进行清洗和抛光的处理,使其表面光滑、无氧化层、无脏物。
2.选择合适的电化学测试仪器,将测试样品在一定的电解液中进行测试。
3.根据测试仪器的指引,将缓蚀剂加入电解液中,进行测试。
通过测量不同时间点下金属电位的变化,来评定不同缓蚀剂的腐蚀保护能力。
2. 盐水喷雾测试法盐水喷雾测试法主要用于评定金属在盐水环境下的缓蚀剂性能。
该测试法以人造海水为试验介质,在特定条件下进行喷雾测试,来评定缓蚀剂的腐蚀保护能力。
盐水喷雾测试法的实验步骤如下:1.准备测试样品。
将待测试的金属表面进行处理,使其光滑、无氧化物和脏物。
2.将样品放入盐水喷雾测试箱中(温度为35℃,湿度为95%),每小时将样品用盐水喷雾1.5小时,然后干燥1小时,实验持续时间根据具体情况而设。
3.对样品进行评估,评估标准包括样品表面的腐蚀情况、斑点数量和大小、发黑程度等指标。
评估结果可以通过外观观察、显微镜观察等方式进行判断。
3. 重量损失测试法重量损失测试法是一种简便的评定缓蚀剂性能的方法。
该测试法通过测量金属表面重量的变化,来评定不同缓蚀剂的抗腐蚀能力。
重量损失测试法的实验步骤如下:1.准备测试样品。
将待测试的金属样品处理成适当大小,清洗干净并使用酒精擦拭干净。
2.将样品固定在指定的容器中,加入测试液,并加入不同缓蚀剂溶液。
3.定期取出样品并干燥,重量损失量越少则缓蚀剂的抗腐蚀能力越强。
季铵盐咪唑啉缓蚀剂及其性能的研究
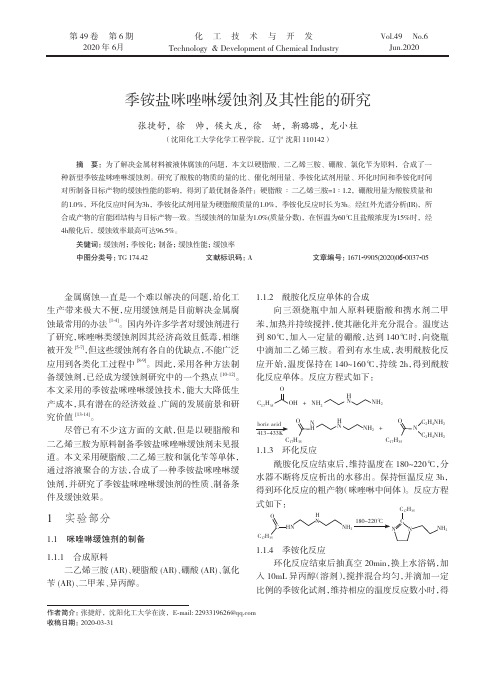
第 49 卷 第 6 期2020 年 6月Vol.49 No.6Jun.2020化工技术与开发Technology & Development of Chemical Industry季铵盐咪唑啉缓蚀剂及其性能的研究张捷舒,徐 帅,候大庆,徐 妍,靳璐璐,龙小柱(沈阳化工大学化学工程学院,辽宁 沈阳 110142)摘 要:为了解决金属材料被液体腐蚀的问题,本文以硬脂酸、二乙烯三胺、硼酸、氯化苄为原料,合成了一种新型季铵盐咪唑啉缓蚀剂。
研究了酸胺的物质的量的比、催化剂用量、季铵化试剂用量、环化时间和季铵化时间对所制备目标产物的缓蚀性能的影响,得到了最优制备条件:硬脂酸∶二乙烯三胺=1∶1.2,硼酸用量为酸胺质量和的1.0%,环化反应时间为3h,季铵化试剂用量为硬脂酸质量的1.0%,季铵化反应时长为3h。
经红外光谱分析(IR),所合成产物的官能团结构与目标产物一致。
当缓蚀剂的加量为1.0%(质量分数),在恒温为60℃且盐酸浓度为15%时,经4h酸化后,缓蚀效率最高可达96.5%。
关键词:缓蚀剂;季铵化;制备;缓蚀性能;缓蚀率中图分类号:TG 174.42 文献标识码:A 文章编号:1671-9905(2020)06-0037-05作者简介:张捷舒,沈阳化工大学在读,E -mail:*****************收稿日期:2020-03-31金属腐蚀一直是一个难以解决的问题,给化工生产带来极大不便,应用缓蚀剂是目前解决金属腐蚀最常用的办法[1-4]。
国内外许多学者对缓蚀剂进行了研究,咪唑啉类缓蚀剂因其经济高效且低毒,相继被开发[5-7],但这些缓蚀剂有各自的优缺点,不能广泛应用到各类化工过程中[8-9]。
因此,采用各种方法制备缓蚀剂,已经成为缓蚀剂研究中的一个热点[10-12]。
本文采用的季铵盐咪唑啉缓蚀技术,能大大降低生产成本,具有潜在的经济效益、广阔的发展前景和研究价值[13-14]。
材料腐蚀与防护
材料腐蚀与防护名词解释:1、高温氧化:金属与环境介质中的气相或凝聚想物质发生化学反应而遭到破坏的过程称高温氧化。
2、缓蚀率:缓蚀剂的缓蚀效率,即缓蚀剂降低的腐蚀速度与原腐蚀速度的比值。
3、PB比:氧化物与金属的体积差对氧化物的保护性的影响,即氧化生成的金属氧化膜的体积与生成这些氧化膜所消耗的金属的体积的比值叫PB比。
4、平衡电极电位:当金属电极上只有唯一一种电极反应,并且该反应处于动态平衡时,金属的溶解速度等于金属离子的沉积速度,则此时电极获得的不变的电位值,称为平衡电极电位。
5、去极化:凡是能消除或印制原电池阳极或阴极极化过程的均叫做去极化。
6、应力腐蚀:是指金属材料在特定腐蚀介质或拉应力共同作用下发生的脆性断裂。
7、自腐蚀电位:在一个电极表面同时进行两个不同的氧化还原过程,当平衡时仅仅是电荷平衡而无物质平衡的电极电位,即外电流为零时的电极电位,称作自腐蚀电位。
简答:1、高温氧化条件下,金属氧化膜具有保护作用的条件有哪些?(充分条件)必要条件:PBR值大于1充分条件:(1)膜要致密,连续无孔洞,晶体缺陷少。
(2)稳定性好,蒸气压低,熔点高。
(3)膜与基体的附着力强,不易脱落。
(4)生长内应力小。
(5)与金属基体具有相近的热膨胀系数。
(6)膜的自愈能力强。
2、简述提高合金抗氧化的可能途径有哪些?通常利用合金化来提高金属的抗氧化性。
方法有:(1)、减少基体氧化膜中晶格缺陷的浓度;(2)、生成具有保护性的稳定相;(3)、通过选择性氧化生成优异的保护膜。
3、流速对扩散控制下的腐蚀速度有什么影响?溶液流速增加使扩散层厚度减小,腐蚀速度增加。
对于活化体系,腐蚀速度随溶液流速增加而增加,但当流速增大到一定值后,由于氧供应充足,阴极由氧的扩散控制变成了活化控制,此时活化控制的腐蚀速度与介质的流速无关。
对于可钝化体系,在氧扩散控制的条件,体系未进入钝态前,腐蚀速度随流速增加而增加。
当速度达到或超过临界值时,即极限扩散电流密度已达到或超过临界钝化电流密度时,金属由活化态变为钝态,此时阳极的腐蚀由阳极扩散控制转变为阳极电阻极化控制,腐蚀速度为维钝电流密度,但当溶液流速继续增加时,腐蚀过程又转为氧扩散控制,腐蚀速度将迅速增加。
缓蚀剂性能评价方法探讨
缓蚀剂性能评价方法探讨摘要:文章详细介绍了缓蚀剂(anti-corrosive.corrosive inhibiter.)的评价方法及缓蚀剂的浓度对缓蚀率的影响。
适用于中性、酸性与气体介质中,常见的有在锅炉、冷却系统中用的加入水中的缓蚀剂,在电镀工业中,电镀前要用酸性溶液去掉电镀件表面的锈,但又要求酸性溶液对电镀件的腐蚀小时,就要在酸性溶剂中加入缓蚀剂,缓蚀剂一般用量不大,但效果显著,其效果用抑制效率(也叫缓蚀效率)I来表示,I=V0-VV×10%,其中V0为没加缓蚀剂时的金属受到腐蚀的速率,V为加入缓蚀剂时的金属受到腐蚀的速率,0≤I≤1,值越大,缓蚀效果越好。
关键词:缓蚀剂;评价方法;浓度;缓蚀率缓蚀剂是这样一类物质,只要在腐蚀环境中添加少量的此类物质,就可将金属材料受的腐蚀大大减少,缓蚀剂的这种减少腐蚀的性能称为缓蚀作用。
1缓蚀剂的评价方法缓蚀剂的测试评价主要在各种条件下,对金属在腐蚀介质中,有无缓蚀剂时的腐蚀速率,从而测定缓蚀效率、最佳添加量和最佳使用条件。
缓蚀剂的性能可以通过缓蚀率η表征。
缓蚀率越大,缓蚀性能越好。
η=×100%或η= ×100%式中,η为缓蚀率,%;Δm0为空白试验(无缓蚀剂)中试片的质量损失,g;Δm1为加药试验(有缓蚀剂)中试片的质量损失,g;ik、ik0为用电化学方法测定的有、无缓蚀剂条件下相应的腐蚀电流密度值。
评价缓蚀剂的缓蚀性能,还需检测其后效性能,即缓蚀剂浓度从其正常使用浓度显著降低后仍能保持其缓蚀作用的能力。
这表明缓蚀剂膜从形成到被破坏能维持的时间。
因此,对缓蚀剂除了要求其具有较高的缓蚀效率以减少缓蚀剂用量、减少加入次数和总用量外,还希望具有较好的后效性能。
为评价后效性能,需在较长的一段时间内进行试验。
水处理系统中通常使用腐蚀速率来评价缓蚀剂的优劣。
平均(均匀)腐蚀速率的计算公式如下:rcoor=式中,rcoor为平均(均匀)腐蚀速率,mm/a;m为试验前的试片质量,g;m1为试验后的试片质量,g;S1为试片的总面积,cm2;ρ为试片材料的密度,g/cm3;t为试验时间,h。
酸化介质中几种氨基酸的缓蚀性能及缓蚀机理
酸化介质中几种氨基酸的缓蚀性能及缓蚀机理陈武;郝敬丽;王大勇;梅平;赖璐【摘要】采用失重法、电化学方法研究了5种氨基酸在酸化介质中对A3钢片的缓蚀性能及缓蚀机理。
结果表明,在30℃时,五种氨基酸对A3钢的缓蚀效率均随盐酸浓度的增加而减小。
半胱氨酸对2%的盐酸中A3钢的缓蚀效率随温度的升高而增大,其余氨基酸的缓蚀效率均随温度的升高而下降;半胱氨酸对A3钢的缓蚀效率随加量的增加而下降,而其余四种氨基酸的缓蚀效率均随加量的增加而升高;在2%的盐酸中,氨基酸加量为200mg/L时,五种氨基酸对A3钢片的缓蚀效率依次为半胱氨酸〉酪氨酸〉组氨酸〉精氨酸〉亮氨酸;通过正交试验确定了半胱氨酸对A3钢在盐酸中的最佳缓蚀条件。
缓蚀机理探讨表明,五种氨基酸均为阴极抑制型缓蚀剂;亮氨酸和酪氨酸在A3钢片表面的吸附基本服从Frumkin等温线,而半胱氨酸、精氨酸和组氨酸的吸附不服从该等温线。
%The inhibition performance and mechanism of five amino acids as inhibitors for steel were studied in acidic media by weight loss method and electrochemical method.The results showed that the inhibition efficiency of these amino acids for A3 steel decreased with increasing the concentration of HCl at 30 ℃.The inhibition efficiency of cysteine for A3 steel in 2% HCl increased with the rise of the temperature while that of other amino acids decreased.To A3 steel,the inhibition efficiency of cysteine decreased with increasing the dosage of the amino acids while that of others increased.When the dosage of amino acids was 200 mg/L,the order of inhibition efficiency to A3 steel of these five kinds of amino acids was cysteine histidine tyrosine arginine leucine in 2% HCl.The optimal inhibiting condition of cysteine to A3 steel in HCl wasconfirmed through an orthogonal test.The results of the corrosion inhibition mechanism study show that all of these amino acids are cathodic inhibitors and the adsorption of leucine and histidine on A3 steel obeys the Frumkin equation while the adsorption of other amino acids do not obey it.【期刊名称】《腐蚀与防护》【年(卷),期】2012(033)005【总页数】5页(P390-393,399)【关键词】氨基酸;缓蚀效率;腐蚀机理;酸化介质【作者】陈武;郝敬丽;王大勇;梅平;赖璐【作者单位】长江大学化学与环境工程学院,荆州430023;长江大学化学与环境工程学院,荆州430023;长江大学化学与环境工程学院,荆州430023;长江大学化学与环境工程学院,荆州430023;长江大学化学与环境工程学院,荆州430023【正文语种】中文【中图分类】TG174.42氨基酸是分子中兼具有碱性氨基和酸性羧基的两性化合物,不但可以通过蛋白质水解制得,且在自然环境中能够全部分解成为缓蚀剂研究中受到关注的化合物[1,2]。
缓蚀剂
文章摘要:在酸洗过程中,去除水垢和锈垢的同时,H+离子会对金属基体产生腐蚀并出现氢脆现象。
实践证明,在酸洗剂中加入缓蚀剂可大大减弱金属基体的腐蚀。
因此缓蚀剂就是化学清洗中腐蚀的抑制剂。
而在清洗之后,加入钝化剂处理可使金属得到保护,因此钝化处理是防止金属表面再度锈蚀的必要措施。
一、缓蚀剂的作用缓蚀剂是减缓金属腐蚀的添加剂,是具有抑制金属生锈腐蚀的化学药品的总称。
一般要求在酸洗液中加入少量缓蚀剂即有强烈抑制金属......在酸洗过程中,去除水垢和锈垢的同时,H+离子会对金属基体产生腐蚀并出现氢脆现象。
实践证明,在酸洗剂中加入缓蚀剂可大大减弱金属基体的腐蚀。
因此缓蚀剂就是化学清洗中腐蚀的抑制剂。
而在清洗之后,加入钝化剂处理可使金属得到保护,因此钝化处理是防止金属表面再度锈蚀的必要措施。
一、缓蚀剂的作用缓蚀剂是减缓金属腐蚀的添加剂,是具有抑制金属生锈腐蚀的化学药品的总称。
一般要求在酸洗液中加入少量缓蚀剂即有强烈抑制金属在酸洗过程被腐蚀的效果。
金属腐蚀分化学腐蚀与电化学腐蚀。
金属与化学物质(酸)直接反应造成的腐蚀叫化学腐蚀,如Fe+2HCl==FeCl2+H2↑的化学反应。
金属与电解质溶液形成化学微电池,在电池阴极发生还原反应,阳极发生氧化反应叫做金属的电化学腐蚀。
电化学腐蚀速度要比化学腐蚀快得多而且危害也大得多:在酸液中金属发生的电化学腐蚀主要是析氢腐蚀,又称氢去极化腐蚀,具体表现为:阴极反应2H+2e——>H2阳极反应Fe-2e——>Fe2+而产生的H2如果扩散到金属内部会弓I起金属脆性增加,在有应力部位开裂或强度较低部位发生鼓疱,这种现象称为氢脆或氢鼓疱,会造成设备的突然破损,其危害比腐蚀更大。
加入酸洗缓蚀剂的作用就是减缓电化学腐蚀中某个电极反应的发生。
不同种类缓蚀剂的作用机理是大不相同的。
有的缓蚀剂可吸附在金属表面形成连续的薄膜阻隔清洗介质对金属的腐蚀;有的与金属作用形成保护层;有的缓蚀剂阻滞电化学腐蚀的阴、阳极反应,抑制金属溶解和析氢吸氢等。
- 1、下载文档前请自行甄别文档内容的完整性,平台不提供额外的编辑、内容补充、找答案等附加服务。
- 2、"仅部分预览"的文档,不可在线预览部分如存在完整性等问题,可反馈申请退款(可完整预览的文档不适用该条件!)。
- 3、如文档侵犯您的权益,请联系客服反馈,我们会尽快为您处理(人工客服工作时间:9:00-18:30)。
酸化腐蚀;缓蚀剂能力;缓蚀率第1章概述1.1酸化过程中缓蚀剂的作用油气井开采过程中,常常需要通过酸化提高采收率。
在压裂酸化中,盐酸或氢氟酸酸液不仅对地层有很强的溶蚀作用,而且对金属也都有很强的腐蚀作用。
酸处理时,由于酸直接与储罐、压裂设备、井下油管、套管接触,特别是在深井井底温度很高,所用的酸又比较浓时,这些金属设备往往会遭到严重的腐蚀。
如果不加有效的缓蚀剂,不但会使设备损坏,缩短使用寿命,甚至造成事故,而且因酸和钢铁的反应产物被挤入储层,会造成储层堵塞而降低酸处理效果[1]。
在酸化施工过程中,为防止酸液对油管和套管造成腐蚀,必须向酸液中加入缓蚀剂。
腐蚀是指金属材料或制件在周围环境介质作用下,逐渐产生的损坏或变质现象通常认为:金属在环境中,由于它们之间所产生的化学,电化学反应及物理溶解作用而引起损坏或变质。
或者说,金属腐蚀是金属在环境中,在金属表面或界面上进行的化学或电化学多相反应,结果使金属转入了氧化(离子)状态。
热力学研究揭示出绝大多数金属都具有与周围环境发生作用而转入氧化离子状态的倾向,即金属腐蚀是一种自发的趋势,不可避免[2]。
由于金属腐蚀给国民经济的发展带来的经济损失约占当年国民经济总值的1.5%~4.2%左右[3],金属腐蚀问题遍及国民经济的各个领域,从日常生活到工农业生产,从尖端科学技术到国防工业的发展,凡是使用金属材料的地方,都不同程度地存在地存在着腐蚀问题。
它给人们带来了巨大的经济损失,造成了灾难性的事故,耗竭了宝贵的能源与资源。
为将腐蚀造成的损失减低到最低限度,腐蚀研究者创造和发展了很多防腐蚀措施,而缓蚀剂应用则是其中应用较广,效果比较显著的手段之一。
目前在国内外油气田所使用的缓蚀剂主要是丙炔醇类、有机胺类、咪唑啉类、季铵盐等有机化合物[4,5],其中丙炔醇类和芳香胺类毒性较大,现场较多使用的油气田缓蚀剂主要是低毒、环保型的咪唑啉类缓蚀剂。
美国试验与材料协会(ASTM)将缓蚀剂定义为“以适当的浓度和形式存在于介质中时,可以防止或减缓材料腐蚀的化学物质或复合物”。
这一定义具有严格的科学性。
1860年英国公布的酸洗铁板用缓蚀剂这一世界上第一个缓蚀剂专利,从此,宣告了人们研究、应用缓蚀剂时代的开始。
此后的百多年间,缓蚀剂的研究一直相当活跃,成果卓著,每年都有大量的专利和产品问世,现在人们已从应用天然物质转向合成性能优越的化合物来适应不同层次、不同方面的需求,同时也将缓蚀剂从实际应用上升到理论研究高度,使缓蚀剂理论得到迅速发展和完善,反过来指导缓蚀剂的研制和应用[6]。
1.2 国内外缓蚀剂的发展与现状和发展方向1.2.1 国外缓蚀剂的发展与现状缓蚀剂分低温(<104℃)和高温(>104℃)两类。
低温缓蚀剂通常为有机物,包括含氯化合物、含硫化合物、炔醇化合物、醛类、酮类、醇类等亲油化合物和表面活性剂等。
高温缓蚀剂[7]在成分上类似低温缓蚀剂,只是加入了增强剂,增强剂有甲酸及其衍生物、酸溶性碘盐及酸溶性铜盐、锑盐、铋盐和汞盐。
20世纪90年代开发的缓蚀剂如下[8]:(1)苯乙烯-马来酸酐共聚物的多胺缩合物缓蚀剂[9]由苯乙烯-马来酸酐的共聚物[10]与多胺缩聚而成。
苯乙烯-马来酸酐可用松香、C23-24改性松香、C8-20脂肪酸、C9-22改性脂肪酸及其化合物代替,苯乙烯-马来酸酐的共聚物与多胺的比例为1∶1~2.5∶1,这两种组分在180℃~240℃缩合反应16~24小时可制得最终产品聚亚氨基胺。
该缓蚀剂可以较好抑制酸液对钢铁的腐蚀,25℃下l010中性钢在加有该缓蚀剂的15%酸液中浸泡37天后失重10%左右。
(2)苯乙烯-丙烯酸树脂的共聚物与多胺缩合物缓蚀剂α-甲基苯乙烯与丙烯酸(或甲基丙烯酸)比例为1∶99~99∶1,共聚物与多胺比例为2∶8~8∶2。
这两种组分在180℃~260℃下反应2~8小时,制得最终产品聚酰氨基胺。
该缓蚀剂经实验室和现场在酸液中试验表现出极好的金属保护性,1010中性钢浸泡在25℃下加有该缓蚀剂的15%酸液中,60天后失重7.5%~9.0%。
(3)胺衍生物缓蚀剂该剂最大优点是毒性低。
酸化压裂后含缓蚀剂的残酸排入海洋和淡水水域不会使水生物致死,并且缓蚀效果较好。
缓蚀剂由脂肪胺与不饱和羧酸反应,或脂肪酸与胺形成酰胺或咪唑啉,然后与不饱和羧酸反应制成。
用于制备缓蚀剂的脂肪胺可以是椰子油或妥尔油的烃基胺、二胺或三胺,最好是二胺或三胺,因为它们的毒性比单胺低。
(4)复合缓蚀剂1)由0.1%~1.5%表面活性剂、0.7%~0.8%锑化合物和0.4%~2%季铵类化合物组成的一种复合缓蚀剂。
其中表面活性剂可润湿金属表面,有利于锑化合物和季铵类化合物形成的络合物附着于金属表面以达到防腐的目的。
该缓蚀剂可用于任一浓度的各种酸。
2)氧乙基化的烷基酚和烷芳基磺酸盐的混合物。
两者比例为(1~5)∶(1~2),这种缓蚀剂在酸中对钢和水泥都具有较好的防腐作用。
3)由组分A和B组成的缓蚀剂。
A为不饱和醛、酮、醚或醇、芳香季铵化合物、季氮杂环化合物;B可以是钼酸及其盐、氧化钼、磷钼酸及其盐,可以是钼酸的铵盐或碱金属盐,还可加入有助于两种组分分散的表面活性剂。
4)木质素磺酸盐与浮选剂T-80或T-66或丙酮复配的缓蚀剂,用其配制的酸液适用于碳酸盐地层。
(5)增效缓蚀剂该缓蚀剂为复配型缓蚀剂,适用于各种浓度的油气井酸化工作液。
其组成如下:7.5%~35%缓蚀剂(如炔醇类、季铵化合物类、醛类、胺类等);1%~3%增效剂(即碘);10%~60%溶剂(如二甲基甲酰胺(DMF)、二甲基亚砜(DMSO)、二甲基乙酰胺(DMA)及它们与醇的混合物);10%~20%甲酸;10%~25%表面活性剂;1%~5%分散剂(如氨基苯酚、苯胺、氯苯氨、烷基吡啶等)。
该缓蚀剂在酸液中的浓度为0.1%~5%,在120℃下能形成有效隔膜,使酸不能接触金属表面,有效地抑制了酸的腐蚀。
(6)苯烯酮缓蚀剂该缓蚀剂由苯烯酮和N-取代喹啉组成,在酸中用量为0.1%~2%,适用于100℃~200℃高温下任何浓度的各种酸液。
(7)工业废物作缓蚀剂由炼油过程产生的副产品制备而成的缓蚀剂。
所用副产品为含C12-15脂肪胺的石蜡。
该缓蚀剂专用于处理盐酸工作液,除防腐蚀外还能降低酸液表面张力。
这些产品优点是价廉、易得,缓蚀效果好,在酸化施工中,用量为0.5%~1.5%。
1.2.2 国内缓蚀剂的发展与现状20世纪60年代至70年代,我国油气井较浅,一般在1000m~2000m之间,井下温度不高,油气井酸化缓蚀剂主要是前苏联使用的一些油气井酸化缓蚀剂如甲醛、乌洛托品、亚砷酸(砒霜)等化合物。
后来经过室内复配试验,将两种以上缓蚀剂复配如乌洛托品+碘化钾、乌洛托品+OP、丁炔二醇+碘化钾、丁炔二醇+OP、丁炔二醇+碘化钾+OP等,其适用的井下温度和盐酸浓度都不高。
70年代以后,我国石油工业迅速发展,一大批二、三千米甚至四、五千米深的生产井投产使用,高浓度盐酸和大酸量的油气井酸化能显著提高油气采收率,这对油气井酸化缓蚀剂的研究发展起着推动作用。
许多单位先后开展了油气井酸化缓蚀剂的研究工作,研究出以746l-102、7701、CT1-2、CT1-3、7801、7812、IMC为代表的酸化缓蚀剂;80年代中期至90年代初又研究出8601-G、8703-A、CT1-8、IMC80-5、SD1-3、CFR、XA-139等油井酸化缓蚀剂。
我国酸化缓蚀剂研究和应用虽然已取得了很大的成绩,但与国外相比仍有一定差距。
国外用于油气井酸化缓蚀剂的品种很多,且形成了系列化酸液配制规范并采用计算机管理。
我国酸化缓蚀剂大多在盐酸和土酸溶液中应用,在乳化液、泡沫酸、稠化(胶凝)酸、超(微)乳化酸、固体酸和有机酸方面应用的品种很少[10,11]。
缓蚀剂产品如下:(1)7701油气井酸化缓蚀剂7701是一种含有多种烷基吡啶和喹啉类的苄基季铵盐物质,在盐酸和土酸溶液中有很好分散性,对碳钢有很好的缓蚀作用,对三价铁离子有一定抑制腐蚀作用,抗H2S腐蚀性强,是耐180℃~200℃高温的浓盐酸酸化缓蚀剂,已在国内多个油田高温井酸化施工中广泛应用。
(2)7801高温浓盐酸缓蚀剂7801是以酮醛缩合物为主的多组分复合物。
适用于90℃~160℃高温深井20%~28%盐酸的酸化施工,已在国内一些油田现场中使用。
该剂具有良好的抗H2S 腐蚀性能,且与酸液中其他组分配伍性好,施工时可以根据井下情况调节其浓度,在28%盐酸120℃条件下使用浓度在2%以上。
(3)8401-3土酸酸化低点蚀缓蚀剂该缓蚀剂以吡啶季铵盐为主,多组分复合而成。
适用于120℃高温井的土酸压裂酸化,已在国内多个油田高温井中使用,使用结果表明可有效防止油井井下残酸腐蚀(点坑蚀)。
(4)8703-A高温土酸酸化低点蚀缓蚀剂8703-A主剂由喹啉、吡啶季铵盐与碘化钾及其它试剂复配而成,适用于150℃下土酸防腐,有较好的抑制土酸及其残液对油管的腐蚀和点蚀作用,已在国内多个油田高温井酸化施工中应用。
(5)CT1-2高温盐酸酸化缓蚀剂该缓蚀剂是以醛酮胺缩合物为主的多种有机组分复合而成,适用于120℃~200℃的高温油气井的盐酸酸化。
在180℃时能适用于15%~28%的盐酸,在180℃~190℃温度范围内,可适用于15%~20%的盐酸,在190℃~200℃能适用于15%的盐酸.在以上条件下腐蚀速率均可控制在100g/m2·h以下。
(6)CT1-3高浓度盐酸缓蚀剂这也是一种以醛酮铵缩合物为主的多组分复合有机缓蚀剂,适用于130℃以下15%~28%盐酸溶液的油气井压裂酸化,腐蚀速度可小于40g/m2·h,能直接在盐酸、土酸中使用,可与表面活性剂磺化醚、SD-1配伍,防H2S腐蚀性能较好,已在油田生产中使用。
(7)CT1-5高温酸化缓蚀增效剂这是为解决高温油气井酸化防腐问题而研制的与缓蚀剂配合的一类助剂,它可以增强抗高温防腐蚀能力。
该增效剂是由锑化合物制得,常与CT1-3复配,满足15%~20%的盐酸在60℃~200℃温度范围内油井酸化施工要求。
(8)CT1-8酸化缓蚀剂该缓蚀剂是有机胺缩合物,在90℃~160℃的15%~28%盐酸中N80油管钢腐蚀速度可小于40g/m2·h~50g/m2·h,缓蚀剂用量也较小。
(9)SH-2酸化缓蚀剂这种缓蚀剂主要由阳离子表面活性剂组成,可用于盐酸和土酸在油水井中的压裂酸化施工,可以较好抑制酸液对钢铁的腐蚀。
(10)SD1-3酸化缓蚀剂该缓蚀剂主要成分是醛酮胺缩合物和阳离子表面活性剂。
其适用于130℃以下15%~28%盐酸的油气井酸化。
该剂在水、酸中分散性好,与酸化液中其他的添加剂配伍性好,不发生乳化,并且使用浓度低,效果良好。