挤压模具设计
铝型材挤压模具设计课件

铝型材挤压模具设计课件一、铝型材挤压工艺概述二、铝型材挤压模具结构三、铝型材挤压模具设计原则1.尺寸精度:铝型材挤压模具设计时要保证挤压后的铝型材尺寸精度。
模具的内芯设计需考虑材料的收缩率和强度,确保挤压后的铝型材尺寸准确。
2.结构合理:铝型材挤压模具设计时应尽量减小模具的重量和尺寸,提高模具的使用寿命。
同时,要增加模具的刚度和强度,确保在挤压过程中不会变形或断裂。
3.表面质量:铝型材挤压模具的表面光洁度直接影响到挤压后的铝型材表面质量。
因此,在设计模具壳和模具翼时应注意表面的光洁度,减少表面缺陷。
4.降低生产成本:铝型材挤压模具的设计应考虑降低生产成本。
例如,可以采用可更换模具芯片的设计来替换整个模具,从而降低维修和更换模具的成本。
四、铝型材挤压模具制造工艺1.材料选择:铝型材挤压模具一般选用高硬度、高强度的工具钢,如优质合金工具钢或高速工具钢等。
2.预先加工:将选定的工具钢进行粗加工,包括锻造、切割、拉伸等工艺,将模具的初始形状制作出来。
3.精密加工:通过数控加工等精密加工技术,对模具进行精细加工,包括车削、铣削、镗削、磨削等工艺,保证模具的尺寸精度和表面质量。
4.表面处理:对模具进行表面处理,如热处理、氮化等工艺,提高模具的硬度和耐磨性。
5.装配调试:将各个组成部分进行装配,并进行调试,保证模具的合理性和可靠性。
五、铝型材挤压模具的维护与保养1.清洁:定期对铝型材挤压模具进行清洁,除去铝屑和污垢,保持模具的清洁度。
2.润滑:对铝型材挤压模具的摩擦部位进行润滑,减少磨损和摩擦力,并延长模具的使用寿命。
3.定期检查:定期对铝型材挤压模具进行检查,发现问题及时修理,确保模具的正常使用。
4.储存:将不使用的铝型材挤压模具储存到干燥、防尘的环境中,避免受潮和污染。
六、铝型材挤压模具的发展趋势1.高精度:随着制造业对产品精度要求的提高,铝型材挤压模具的精度也将不断提高。
2.高效率:铝型材挤压模具的开发将更加注重提高生产效率和降低能耗。
挤压成型模具设计手册

挤压成型模具设计手册一、模具设计基础模具设计是挤压成型工艺中的重要环节,它涉及到产品的形状、尺寸、精度和生产效率等方面。
在进行模具设计时,需要充分了解产品的用途和性能要求,同时考虑到生产条件和制造成本等因素。
二、材料选择与处理模具材料的选择和处理对于模具的寿命和性能至关重要。
常用的模具材料包括钢材、硬质合金、陶瓷等,具体选择应根据产品的要求和生产条件来确定。
材料处理包括热处理、表面处理等,可以提高材料的硬度、耐磨性和耐腐蚀性等性能。
三、模具结构设计模具结构设计是模具设计的核心,它决定了模具的功能和生产能力。
结构设计应充分考虑产品的形状、尺寸、精度和生产效率等因素,同时考虑到材料的流动和排溢等条件。
此外,结构设计还应考虑到维修和保养的方便性。
四、成型工艺优化挤压成型工艺是模具设计的重要环节之一,它涉及到材料的流动、温度和压力的控制等方面。
工艺优化可以提高生产效率、降低能耗和提高产品质量。
在进行工艺优化时,需要考虑多种因素,包括材料的性能、模具的结构和尺寸等。
五、温度控制系统温度是影响挤压成型工艺的重要因素之一,因此温度控制系统的设计也是模具设计的重要环节之一。
温度控制系统应能够精确控制模具的温度,并保持温度的稳定。
此外,温度控制系统的设计还应考虑到加热和冷却的速度和时间等因素。
六、模具强度与刚性模具的强度和刚性是影响模具寿命和产品质量的重要因素。
在进行模具设计时,应充分考虑模具的强度和刚性要求,并采取相应的措施来提高模具的强度和刚性。
例如,可以采用加强筋、增加厚度等方法来提高模具的强度和刚性。
七、润滑与保养润滑和保养是保持模具性能和延长模具寿命的重要措施。
在进行模具设计时,应充分考虑润滑和保养的要求,并采取相应的措施来实现润滑和保养的目的。
例如,可以采用润滑剂、密封圈等来润滑和保养模具。
挤压设计与模具课程设计

挤压设计与模具课程设计一、课程目标知识目标:1. 让学生掌握挤压设计的基本原理,理解模具在挤压过程中的作用;2. 使学生了解不同类型的挤压模具及其特点,并能结合实际需求选择合适的模具;3. 引导学生掌握挤压工艺参数对产品质量的影响,能够优化挤压工艺。
技能目标:1. 培养学生运用CAD软件进行挤压模具设计的能力,提高设计效率;2. 培养学生运用CAE软件对挤压过程进行模拟分析,优化模具结构;3. 提高学生实际操作能力,能够参与简单的挤压模具组装和调试。
情感态度价值观目标:1. 培养学生对挤压设计与模具制造的热爱,激发学生探究新技术的兴趣;2. 培养学生严谨的工作态度,提高团队合作意识,增强解决实际问题的自信心;3. 引导学生关注我国挤压模具产业的发展,树立为国家和企业贡献力量的责任意识。
课程性质:本课程为专业实践课,旨在提高学生对挤压设计与模具制造的理论知识和实践技能。
学生特点:学生具备一定的机械基础知识和动手能力,对新技术充满好奇。
教学要求:结合理论知识与实践操作,注重培养学生的实际应用能力和创新精神。
通过课程学习,使学生能够达到以上设定的知识、技能和情感态度价值观目标,为后续专业课程学习和未来职业发展打下坚实基础。
二、教学内容1. 挤压设计基本原理:包括金属塑性变形理论、挤压成形方法分类、挤压工艺参数对产品质量的影响等;教材章节:第1章 挤压成形原理2. 挤压模具结构与设计:介绍不同类型挤压模具的结构特点、设计方法和注意事项;教材章节:第2章 挤压模具设计3. 挤压模具材料及热处理:分析挤压模具材料的选用原则、热处理工艺及其对模具性能的影响;教材章节:第3章 挤压模具材料及热处理4. 挤压模具CAD/CAE技术:讲解CAD软件在挤压模具设计中的应用,以及CAE软件对挤压过程进行模拟分析的方法;教材章节:第4章 挤压模具CAD/CAE技术5. 挤压模具制造与装配:介绍挤压模具的加工工艺、装配方法及调试技巧;教材章节:第5章 挤压模具制造与装配6. 挤压模具应用实例:分析典型挤压模具在实际生产中的应用案例,提高学生的实际操作能力;教材章节:第6章 挤压模具应用实例教学内容安排与进度:第1-2周:挤压设计基本原理及挤压成形方法;第3-4周:挤压模具结构与设计;第5-6周:挤压模具材料及热处理;第7-8周:挤压模具CAD/CAE技术;第9-10周:挤压模具制造与装配;第11-12周:挤压模具应用实例分析及实践操作。
挤压模具设计书说明书

挤压模具设计书说明书1. 引言本说明书旨在提供挤压模具设计的详细指导。
挤压模具是在挤压工艺中使用的一种关键工具,它对产品的质量和生产效率具有重要影响。
本说明书将涵盖挤压模具设计的基本概念、设计要点和步骤等内容,旨在帮助设计人员更好地理解和应用挤压模具设计相关知识。
2. 挤压模具设计概述挤压是一种通过挤压机将熔融的原料挤出成型的工艺。
挤压模具是挤压过程中起到塑料流动、形成和冷却等作用的工具。
挤压模具设计需要考虑多个因素,如材料选择、模具结构、模具加工工艺等。
3. 挤压模具设计步骤3.1. 产品分析在进行挤压模具设计之前,首先需要对待生产产品进行详细分析。
这包括产品的材料、形状、尺寸、表面要求等方面的分析。
通过产品分析,可以为模具设计提供基本的设计要求和指导。
3.2. 模具结构设计模具结构设计是挤压模具设计的核心部分。
在模具结构设计过程中,需要考虑到产品的形状和尺寸要求,确定模具的结构形式、模腔布置、模具开合方式等。
合理的模具结构设计能够有效提高产品的一致性和精度。
3.3. 材料选择挤压模具的材料选择对于模具寿命和产品质量具有重要影响。
常见的挤压模具材料包括合金钢、硬质合金等。
在选择材料时,需要综合考虑材料的硬度、强度、热导率等因素。
3.4. 模具加工工艺模具加工工艺是指模具从原料到成品的全过程。
挤压模具加工工艺包括切割、车削、铣削、磨削等。
在进行模具加工时,需要根据模具的具体要求选择合适的加工工艺,保证模具的加工精度和质量。
4. 挤压模具设计要点4.1. 模具结构要点•模具结构应满足产品的外观要求,确保产品的形状和尺寸精度。
•模具结构应具备良好的冷却系统,以提高模具的散热效果,避免产品变形和模具损坏。
•模具结构应具备合理的模腔设计,以确保塑料流动的均匀性和稳定性。
4.2. 模具材料要点•模具材料应具有高硬度和耐磨性,以提高模具的使用寿命。
•模具材料应具有良好的热导率,以实现有效的模具冷却效果。
4.3. 模具加工工艺要点•模具加工工艺应具有高加工精度和稳定性,以确保模具的质量和精度。
冷挤压模具设计
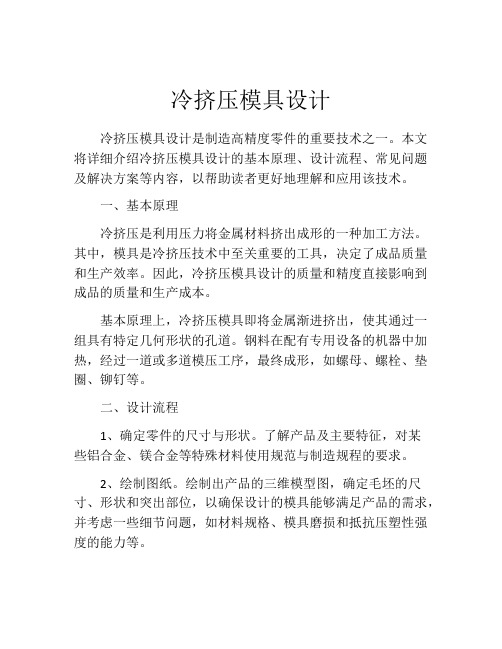
冷挤压模具设计冷挤压模具设计是制造高精度零件的重要技术之一。
本文将详细介绍冷挤压模具设计的基本原理、设计流程、常见问题及解决方案等内容,以帮助读者更好地理解和应用该技术。
一、基本原理冷挤压是利用压力将金属材料挤出成形的一种加工方法。
其中,模具是冷挤压技术中至关重要的工具,决定了成品质量和生产效率。
因此,冷挤压模具设计的质量和精度直接影响到成品的质量和生产成本。
基本原理上,冷挤压模具即将金属渐进挤出,使其通过一组具有特定几何形状的孔道。
钢料在配有专用设备的机器中加热,经过一道或多道模压工序,最终成形,如螺母、螺栓、垫圈、铆钉等。
二、设计流程1、确定零件的尺寸与形状。
了解产品及主要特征,对某些铝合金、镁合金等特殊材料使用规范与制造规程的要求。
2、绘制图纸。
绘制出产品的三维模型图,确定毛坯的尺寸、形状和突出部位,以确保设计的模具能够满足产品的需求,并考虑一些细节问题,如材料规格、模具磨损和抵抗压塑性强度的能力等。
3、确定模具类型。
根据产品的尺寸、形状和工艺要求,确定冷挤压模具的类型。
常用的冷挤压模具包括拉伸模、挤压模、钝化模、套筒模等。
4、设计模具的结构。
设计模具的结构时,需要考虑到模具主体的结构、腔体形状、孔形结构等几个方面,还需要根据压力、预压、挤出量等要素,确定可承受的载荷。
同时,还需要考虑一些实际运用中需要注意的问题,例如设定模具配合公差、调整模具的开合间隙、设定模具的定位和定向等。
5、制作模具样品。
样品制作过程中,需要考虑到模具结构的合理性,以及各种元素的配合度。
制作完成后,需要进行模具的调试、试胶、实验成型等环节,进行逐渐的调整和完善。
三、常见问题及解决方案1、模具寿命不够长。
在设计时应考虑模具的材质和硬度,通过表面热处理、高频淬火、氮化等方式进行强化处理,以延长模具的使用寿命。
2、模具容易出现磨损或变形。
在制作过程中,要合理设定模具的使用寿命,并且需要根据产品的多重要素,优化模具的设计结构,来提高其使用的稳定性。
挤压模具设计.doc
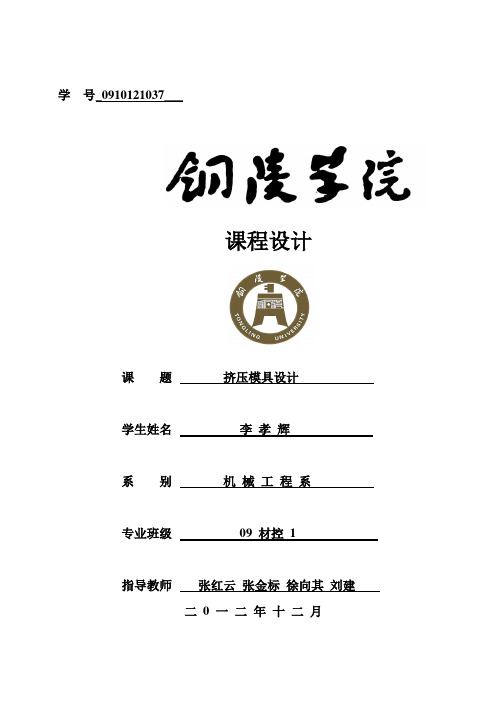
学号_0910121037___课程设计课题挤压模具设计学生姓名李孝辉系别机械工程系专业班级09 材控1指导教师张红云张金标徐向其刘建二0 一二年十二月课程设计任务书机械工程系09材控(1,2)班指导教师:张红云,张金标,徐向其,刘建。
设计课题:挤压模具设计一、设计条件:在19.6MN挤压机的Φ200mm挤压筒上生产出下列条件的合格型材,设计出相应的型材模具。
1.单模孔模具生产如下图型材。
(1,2,3组同学设计)2.双模孔生产ф12mm的圆棒材。
(4,5,6组同学设计)3.三模孔生产ф8mm的圆棒线材。
(7,8,9组同学设计)4.四模孔生产ф6mm的圆棒线材。
(10,11,12组同学设计)二、设计内容:1.模孔布置。
2.设计工作带长度。
3.型材模孔尺寸设计。
4.模子强度校核。
5.画出模具图。
三、设计时间:2012年12月10日至12月14日四、设计地点:实验楼C楼501,502五、分组情况:目录第一章概述 (1)第二章模孔布置 (2)2.1 挤压比的计算 (2)2.2 模孔的布置 (2)2.3模孔尺寸的计算 (3)第三章工作带长度的确定 (5)第四章模具尺寸的确定 (6)4.1模具材质的选取 (6)4.2模具外形尺寸设计 (6)第五章模具的强度校核 (8)第六章设计的模具示意图 (10)设计总结与体会 (12)参考文献 (13)第一章概述模具是金属压力加工的基础,模具的设计与制造技术是金属压力加工的核心,而模具的质量和使用寿命是决定金属压力加工过程是否经济可行的关键。
模具技术特别是设计制造精密,复杂,大型,寿命长的模具是衡量一个国家工业水平的重要标志之一,因此有“模具是工业之母”之说。
本次设计主要是在给定挤压筒和挤压机的条件下,设计挤压出直径为12mm的圆棒材所用的双模孔模具。
在此次设计中,本组以黄铜为例,对模孔的布置,工作带长度,模孔的尺寸以及模具外形尺寸的进行确定的设计,并对模子的强度进行校核以及绘制各种模具图;此次的课程设计是对我们所学的专业知识进行的一个总结,对我们以后的学习和工作具有一定的指导意义,同时通过对模具的设计还可以让我们进一步了解挤压模具的工艺过程,通过查阅更多的资料,能够开阔我们的视野和见识,提高我们将理论运用于实践的能力。
铝型材挤压模具设计中的关键点和问题

铝型材挤压模具设计中的关键点和问题一、材料选择:在铝型材挤压模具设计中,材料的选择十分重要。
模具的材料应具有良好的硬度、强度和耐磨性。
常见的模具材料有H13、3Cr2W8V、4Cr5MoSiV1等。
根据使用要求和成本控制,选择合适的材料。
二、模腔设计:模腔的设计是铝型材挤压模具设计的核心。
模腔的几何形状和尺寸应符合产品的要求,并能保证产品的几何精度。
在设计模腔时,应考虑材料的流动性、收缩率、气泡和焊接等问题,以确保铝型材的挤压过程顺利进行。
三、内冷却设计:内冷却设计是提高模具使用寿命和产品质量的重要手段。
通过合理布置冷却水管道,能够在挤压过程中及时冷却模具,降低模具的工作温度,减少模具磨损和热载荷,延长模具寿命。
四、橡胶垫设计:橡胶垫在铝型材挤压过程中起到密封和保护模具的作用。
橡胶垫的设计应考虑到材料的选择、厚度、硬度和形状等因素,以确保橡胶垫能够准确地封闭模腔,并能够承受高压和高温的挤压过程。
五、冷却系统设计:冷却系统的设计直接影响到挤压速度和产品质量。
合理的冷却系统能够快速冷却挤压铝型材,降低铝材的热度和产生的内应力,提高铝材的强度和硬度。
冷却系统的设计应综合考虑冷却水的流量、速度、温度和位置等因素。
六、毛刺控制:毛刺是铝型材挤压过程中常见的缺陷之一、在模具设计中,应考虑到挤压过程中金属的流动和退火等因素,采取合适的措施来控制毛刺的产生。
例如,合理设计模腔的边缘形状,使用抛光或涂覆耐磨材料等。
七、凸模设计:凸模的设计直接影响到铝型材的外形和尺寸精度。
凸模的形状、尺寸和相对位置应合理设置,以确保铝材的挤压过程顺利进行,并且保证产品的几何精度和表面质量。
八、磨损和冲击问题:由于挤压过程中金属的高速流动和冷却周期的反复,模具表面很容易受到磨损和冲击。
因此,在模具设计过程中应考虑到材料的硬度、涂层和冲击吸收等因素,以延长模具的使用寿命和提高产品质量。
九、模具拆卸与维护:在设计模具时,应考虑到模具的维护和拆卸。
挤压模具制作与设计实验报告

挤压模具制作与设计实验报告实验目的本实验旨在探究挤压模具的制作与设计,并通过实际操作来了解挤压模具的使用方法和注意事项。
实验设备与材料- 挤压机- 铝合金材料- 挤压模具- 计算机辅助设计软件实验步骤步骤一:挤压模具设计1. 根据需要制作的铝合金产品的形状和尺寸,在计算机辅助设计软件上进行三维模型设计。
2. 根据设计好的三维模型,进行模具设计。
考虑到材料的流动性和受力情况,设计合理的模具结构和出模方式。
步骤二:挤压模具制作1. 准备所需的模具材料,一般使用高强度、高硬度的合金材料。
2. 根据设计好的模具结构制作模具的零件。
可以使用数控机床进行加工,确保模具精度和质量。
3. 将加工好的模具零件进行组装,并进行必要的热处理和表面处理,提高模具的使用寿命和质量。
步骤三:挤压模具调试1. 将制作好的挤压模具安装到挤压机上。
2. 启动挤压机,并根据所制作的铝合金产品的要求,调整挤压机的参数,如温度、压力等。
3. 进行模具试压,检查铝合金产品的质量和尺寸是否符合要求。
4. 根据试压结果,调整模具的结构和参数,直至满足产品要求为止。
实验结果与分析经过实验,成功制作了一套挤压模具,并使用挤压机进行了模具试压。
铝合金产品的质量和尺寸达到了设计要求,说明挤压模具的制作与设计是成功的。
通过实验过程中的观察和分析,我们可以得出以下结论:1. 挤压模具的设计要考虑材料流动性和受力情况,以保证产品质量。
2. 挤压模具的制作需要使用高强度、高硬度的合金材料,并进行必要的热处理和表面处理。
3. 挤压模具的调试是一个迭代的过程,需要根据试压结果不断调整模具的结构和参数,直至满足产品要求。
4. 计算机辅助设计软件在挤压模具设计中起到了重要的作用,能够提高设计的精度和效率。
实验总结挤压模具的制作与设计是一项复杂的工艺,需要对材料和工艺有深入的理解和掌握。
本次实验通过实际操作,使我们更加熟悉了挤压模具的制作过程和设计原理。
通过本次实验,我们深刻认识到挤压模具在工业生产中的重要性,它在航空航天、汽车制造、建筑等领域都有广泛的应用。
- 1、下载文档前请自行甄别文档内容的完整性,平台不提供额外的编辑、内容补充、找答案等附加服务。
- 2、"仅部分预览"的文档,不可在线预览部分如存在完整性等问题,可反馈申请退款(可完整预览的文档不适用该条件!)。
- 3、如文档侵犯您的权益,请联系客服反馈,我们会尽快为您处理(人工客服工作时间:9:00-18:30)。
矿产资源开发利用方案编写内容要求及审查大纲
矿产资源开发利用方案编写内容要求及《矿产资源开发利用方案》审查大纲一、概述
㈠矿区位置、隶属关系和企业性质。
如为改扩建矿山, 应说明矿山现状、
特点及存在的主要问题。
㈡编制依据
(1简述项目前期工作进展情况及与有关方面对项目的意向性协议情况。
(2 列出开发利用方案编制所依据的主要基础性资料的名称。
如经储量管理部门认定的矿区地质勘探报告、选矿试验报告、加工利用试验报告、工程地质初评资料、矿区水文资料和供水资料等。
对改、扩建矿山应有生产实际资料, 如矿山总平面现状图、矿床开拓系统图、采场现状图和主要采选设备清单等。
二、矿产品需求现状和预测
㈠该矿产在国内需求情况和市场供应情况
1、矿产品现状及加工利用趋向。
2、国内近、远期的需求量及主要销向预测。
㈡产品价格分析
1、国内矿产品价格现状。
2、矿产品价格稳定性及变化趋势。
三、矿产资源概况
㈠矿区总体概况
1、矿区总体规划情况。
2、矿区矿产资源概况。
3、该设计与矿区总体开发的关系。
㈡该设计项目的资源概况
1、矿床地质及构造特征。
2、矿床开采技术条件及水文地质条件。