铝型材挤压模具
铝型材挤压模具设计课件

铝型材挤压模具设计课件一、铝型材挤压工艺概述二、铝型材挤压模具结构三、铝型材挤压模具设计原则1.尺寸精度:铝型材挤压模具设计时要保证挤压后的铝型材尺寸精度。
模具的内芯设计需考虑材料的收缩率和强度,确保挤压后的铝型材尺寸准确。
2.结构合理:铝型材挤压模具设计时应尽量减小模具的重量和尺寸,提高模具的使用寿命。
同时,要增加模具的刚度和强度,确保在挤压过程中不会变形或断裂。
3.表面质量:铝型材挤压模具的表面光洁度直接影响到挤压后的铝型材表面质量。
因此,在设计模具壳和模具翼时应注意表面的光洁度,减少表面缺陷。
4.降低生产成本:铝型材挤压模具的设计应考虑降低生产成本。
例如,可以采用可更换模具芯片的设计来替换整个模具,从而降低维修和更换模具的成本。
四、铝型材挤压模具制造工艺1.材料选择:铝型材挤压模具一般选用高硬度、高强度的工具钢,如优质合金工具钢或高速工具钢等。
2.预先加工:将选定的工具钢进行粗加工,包括锻造、切割、拉伸等工艺,将模具的初始形状制作出来。
3.精密加工:通过数控加工等精密加工技术,对模具进行精细加工,包括车削、铣削、镗削、磨削等工艺,保证模具的尺寸精度和表面质量。
4.表面处理:对模具进行表面处理,如热处理、氮化等工艺,提高模具的硬度和耐磨性。
5.装配调试:将各个组成部分进行装配,并进行调试,保证模具的合理性和可靠性。
五、铝型材挤压模具的维护与保养1.清洁:定期对铝型材挤压模具进行清洁,除去铝屑和污垢,保持模具的清洁度。
2.润滑:对铝型材挤压模具的摩擦部位进行润滑,减少磨损和摩擦力,并延长模具的使用寿命。
3.定期检查:定期对铝型材挤压模具进行检查,发现问题及时修理,确保模具的正常使用。
4.储存:将不使用的铝型材挤压模具储存到干燥、防尘的环境中,避免受潮和污染。
六、铝型材挤压模具的发展趋势1.高精度:随着制造业对产品精度要求的提高,铝型材挤压模具的精度也将不断提高。
2.高效率:铝型材挤压模具的开发将更加注重提高生产效率和降低能耗。
铝型材模具挤压成型所出现的问题

铝型材模具挤压成型问题分析1. 引言铝型材模具挤压成型是一种常用的铝型材加工方法,通过将铝料加热至柔软状态,然后通过挤压机将其挤压至模具中,形成所需的截面形状。
然而,在实际生产中,铝型材模具挤压成型过程中常常会出现一些问题,如尺寸偏差、表面缺陷等。
本文将对这些问题进行详细分析,并提出相应的解决方案。
2. 尺寸偏差问题尺寸偏差是指铝型材在挤压成型过程中与设计要求相比存在一定的误差。
尺寸偏差问题可能由以下几个方面引起:2.1 材料性质不同批次的铝料性质可能存在一定的差异,如硬度、弹性模量等。
这些差异会直接影响到铝料在挤压过程中的变形行为,从而导致尺寸偏差。
解决方案: - 选择稳定性能好的铝料供应商,并与其建立长期合作关系。
- 在生产前对每批铝料进行严格的质量检测,确保其性质符合要求。
2.2 模具设计模具的几何形状和尺寸对最终产品的尺寸精度有着直接影响。
如果模具设计不合理,如孔型尺寸过大或过小、边缘过于锐利等,都会导致挤压成型后的铝型材出现尺寸偏差。
解决方案: - 优化模具设计,确保孔型尺寸和边缘处理符合要求。
- 使用先进的CAD/CAM技术对模具进行设计和制造,提高制造精度。
2.3 挤压工艺参数挤压工艺参数是控制挤压成型过程中铝料变形行为的重要因素。
如果工艺参数设置不当,如挤压速度过快、温度控制不准确等,都会导致铝型材出现尺寸偏差。
解决方案: - 对挤压工艺进行充分的试验和优化,找到最佳的工艺参数组合。
- 加强对挤压机设备和温度控制系统的维护和管理,确保其正常运行。
3. 表面缺陷问题表面缺陷是指铝型材在挤压成型过程中表面出现的瑕疵,如气泡、划痕、凹陷等。
表面缺陷问题可能由以下几个方面引起:3.1 模具磨损模具在长期使用过程中会出现磨损,特别是挤压孔型部分。
模具磨损会导致挤压成型时铝料与模具壁之间的间隙不均匀,从而引起表面缺陷。
解决方案: - 定期对模具进行检修和维护,及时更换磨损严重的模具部件。
铝型材挤压模具知识

《铝型材挤压模具知识》铝型材挤压模具知识所谓挤压,就是对放在容器(挤压筒)中的锭坯一端加以压力,使之通过模孔成型的一种压力加工方法。
1.1.1 沿型材长度方向断面不变的实心型材挤压按金属制品相对于挤压杆运动方向可分为:1)金属正向流动的挤压2)金属反向流动的挤压通过挤压筒传递压力通过坯料传递压力同上图,运动构件不同3)正向和反向的联合挤压挤压筒、坯料、模具都参与先后运动形成挤压1.1.2 空心型材挤压可分为:1)固定针挤压2)随动针挤压无缝管材正向热挤压(a)固定针挤压;(b)随动针挤压1-挤压杆;2-挤压垫;3-挤压筒;4-挤压模;5-锭坯;6-挤压制品;7-挤压针3)焊合挤压焊合管材、空心型材正向热挤压1-挤压杆;2-挤压垫;3-挤压筒;4-上模;5-下模;6-锭坯;7-挤压制品1.1.3 阶段变断面实心型材的挤压用三个可拆卸模挤压阶段变断面型材的示意图a-挤压基本型材部分;b-挤压过渡区;c-挤压大头部分优点:1)具有比轧制更为强烈的三向压应力状态图,金属可以发挥其最大的塑性。
因此可以加工用轧制或锻造加工有困难甚至无法加工的金属材料。
也可以用挤压法先对锭坯进行开坯。
2)还可以生产断面极其复杂的,以及变断面的管材和型材。
3)具有极大的灵活性。
在同一台设备上能够生产出很多的产品品种和规格。
只需要更换相应的模具就可。
4)产品尺寸精确,表面质量高。
缺点:1)金属的固定废料损失较大,要留压余和有挤压缩尾。
2)加工速度低。
挤压法非常适合于生产品种、规格和批数繁多的有色金属管、棒、型材,以及线坯等。
在生产断面复杂或壁薄的管材和型材,直径与壁厚之比趋近于2 的超厚壁管材,以及脆性的有色金属和钢铁材料方面,挤压法是唯一可行的压力加工方法。
发展概况:目前的型材品种已经达到50000 多种,其中包括各种具有复杂外形的型材、逐渐变断面型材和阶段变断面型材、大型整体带筋壁板及异形空心型材。
挤压型材的最大宽度可达2500 mm,最大断面积可达1500 平方厘米,最大长度可达25~30 m,最重可达2 t左右。
薄壁铝型材挤压模具设计和维护

1挤压模具介绍挤压模具结构设计和制造环节较多,包括选材、设计、制造、修模等环节,其成本占到型材挤压生产成本的35%左右。
在型材加工生产中,一般有两种主要挤压方法:分流组合模挤压法和穿孔针挤压法。
前者加工起来简单且成本较低,后者成本高且应用范围较小,在实际型材加工生产中,分流组合模应用更为广泛。
1.1挤压模具的工作条件。
对于大截面复杂型材的挤压成形,挤压难度比较大,对挤压模具的结构与形状要求也很高,特别是对于这种断面形状较复杂,壁厚相差悬殊,断面面积及外接圆大,多腔空心等型材,挤压模具的工作条件变得更加恶劣。
因此,对挤压模具要求较高,主要有如下几个方面:一是高温高压条件下工作;二是要具有较好的抗磨损能力;三是具有很高的强度和韧性,避免在工作中出现应力集中而使模具破坏。
1.2挤压模具的分类。
挤压模具种类很多,根据不同的分类条件可以进行归类。
分类的主要依据有模具结构和模孔压缩区断面外形。
分流组合模在目前是应用最为广泛的一种模具形式,平面分流组合模的组成结构主要包括上模、下模、定位销和联结螺钉四个部分,其工作原理是在一定的挤压力作用下,锅淀通过分流孔被分流成金属流,流经焊合室进行汇集和傅合,最终由模芯和模孔流出,形成具有所要求几何形状的型材产品。
1.3模具的设计步骤。
实际生产中,产品类型、工艺方法、设备和模具结构都是影响模具设计过程的重要因素。
但是在设计过程中,挤压模具模腔的设计一般按照以下步骤进行:1.3.1模腔参数确定和模孔布置。
模腔参数的确定主要根据挤压机、工艺规程和现场工具设备来确定。
模孔布置合理与否直接影响着模具强度,同时影响金属流动的均匀性。
一般在设计过程中,即使非对称的型材也要尽量保证模孔的对称性,同时使其尽量接近中心紧凑一些。
通常情况下,模孔多设置在同心圆上(模孔之间的间距大于30-50mm,模孔距离模具边缘大于25-50mm,模孔与挤压筒边缘的距离大于20-40mm)。
1.3.2设计模孔尺寸。
铝型材挤压模具工作带加工方法
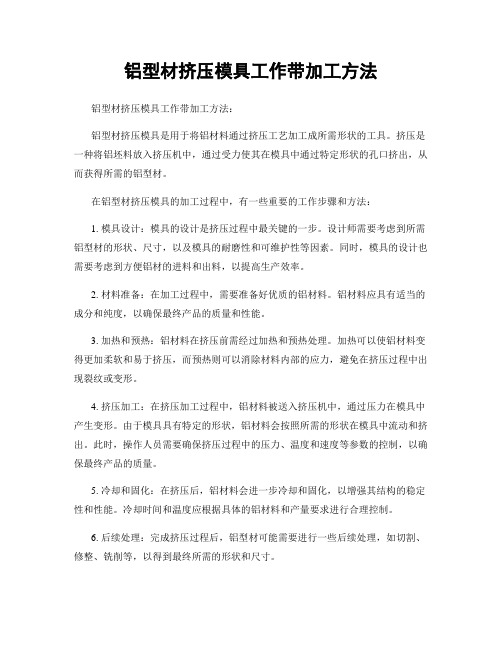
铝型材挤压模具工作带加工方法铝型材挤压模具工作带加工方法:铝型材挤压模具是用于将铝材料通过挤压工艺加工成所需形状的工具。
挤压是一种将铝坯料放入挤压机中,通过受力使其在模具中通过特定形状的孔口挤出,从而获得所需的铝型材。
在铝型材挤压模具的加工过程中,有一些重要的工作步骤和方法:1. 模具设计:模具的设计是挤压过程中最关键的一步。
设计师需要考虑到所需铝型材的形状、尺寸,以及模具的耐磨性和可维护性等因素。
同时,模具的设计也需要考虑到方便铝材的进料和出料,以提高生产效率。
2. 材料准备:在加工过程中,需要准备好优质的铝材料。
铝材料应具有适当的成分和纯度,以确保最终产品的质量和性能。
3. 加热和预热:铝材料在挤压前需经过加热和预热处理。
加热可以使铝材料变得更加柔软和易于挤压,而预热则可以消除材料内部的应力,避免在挤压过程中出现裂纹或变形。
4. 挤压加工:在挤压加工过程中,铝材料被送入挤压机中,通过压力在模具中产生变形。
由于模具具有特定的形状,铝材料会按照所需的形状在模具中流动和挤出。
此时,操作人员需要确保挤压过程中的压力、温度和速度等参数的控制,以确保最终产品的质量。
5. 冷却和固化:在挤压后,铝材料会进一步冷却和固化,以增强其结构的稳定性和性能。
冷却时间和温度应根据具体的铝材料和产量要求进行合理控制。
6. 后续处理:完成挤压过程后,铝型材可能需要进行一些后续处理,如切割、修整、铣削等,以得到最终所需的形状和尺寸。
总结而言,铝型材挤压模具工作带加工方法包括模具设计、材料准备、加热和预热、挤压加工、冷却和固化以及后续处理等环节。
掌握这些关键步骤和方法,可以确保铝型材挤压加工的效率和质量。
铝合金挤压模具标准

铝合金挤压模具标准铝合金挤压模具是用于铝合金挤压成型的重要工具,其质量和精度直接影响着挤压铝型材的质量和生产效率。
为了保证铝合金挤压模具的质量和性能,制定了一系列的标准,以规范和指导铝合金挤压模具的设计、制造和使用。
本文将介绍铝合金挤压模具的相关标准内容,帮助读者更好地了解和应用这些标准。
首先,铝合金挤压模具的标准主要包括以下几个方面,设计标准、材料标准、加工精度标准、使用和维护标准等。
设计标准是指铝合金挤压模具在设计过程中应符合的要求,包括模具结构设计、尺寸设计、表面处理等方面的规定。
材料标准是指铝合金挤压模具所选用的材料应符合的要求,包括材料的化学成分、力学性能、热处理工艺等方面的规定。
加工精度标准是指铝合金挤压模具在加工过程中应达到的精度要求,包括模具加工工艺、加工精度、表面质量等方面的规定。
使用和维护标准是指铝合金挤压模具在使用和维护过程中应遵守的规定,包括模具的安装、调试、使用、保养、维修等方面的规定。
其次,铝合金挤压模具的标准制定是为了保证模具的质量和性能稳定,提高铝型材的生产效率和产品质量。
通过遵循标准规定,可以有效地规范和指导铝合金挤压模具的设计、制造和使用,确保模具的质量和性能符合要求。
同时,标准的制定还可以促进模具制造技术的进步,推动铝合金挤压工艺的发展,提高铝型材的生产水平和市场竞争力。
最后,铝合金挤压模具的标准是行业标准和国家标准的重要组成部分,对于铝型材生产企业和模具制造企业来说具有重要的指导意义和规范作用。
因此,铝合金挤压模具的标准应得到充分重视和广泛应用,以确保铝型材生产的质量和效益。
同时,还需要不断完善和更新标准内容,以适应铝型材生产技术的发展和市场需求的变化。
综上所述,铝合金挤压模具标准是铝型材生产中不可或缺的重要内容,对于提高铝型材的质量和生产效率具有重要意义。
通过遵循标准规定,可以规范和指导铝合金挤压模具的设计、制造和使用,促进铝型材生产技术的进步和发展。
因此,铝合金挤压模具的标准应得到充分重视和广泛应用,以推动铝型材产业的健康发展和持续增长。
铝型材挤压模具的三种失效形式
铝型材挤压模具的三种失效形式1 失效形式铝挤压模的失效形式,生产中会因模具的冲击破裂、塑性变形、粘附及过早的磨损和热裂、细颈或拉断、压弯等现象出现早期失效,也会由于技术问题、氮化问题等造成模具损坏,同时还会因模具问题而造成压堵、间隙、扩、并口等故障,但挤压模的失效主要表现为磨损、开裂、变形三种正常失效方式。
(1)磨损失效,铝型材在挤压过程中是通过没有润滑加工的高温高压下的挤压材料碰上模具型腔的开口部分,一面与定径带平面直接接触,一面滑动,从而产生很大的摩擦力,使型腔表面和定径带表面受到磨损而失效。
同时模具在摩擦过程中,模具工作表面上粘附了一些坯料金属使得模具的几何形状发生变化而不能使用,也视为磨损失效,其表现形式为刃口钝化、棱角变圆、平面下陷、表面沟痕、剥落、粘模等。
磨损失效的根本原因是摩擦。
模具磨损的具体形式与摩擦过程的速度等诸多因素有关,如模具材料和被加工坯料的化学成分及机械性能、模具和坯料的表面粗糙度等以及挤压过程中的压力、温度、速度等有关系。
铝挤压模具的磨损主要是热磨损,热磨损是摩擦时,金属表面因温度升高而软化和模具型腔表面发生互相咬合所造成的,模具型腔表面高温软化后,其耐磨性降低。
热磨损过程十分复杂,显然温度是影响热磨损的主要因素,温度愈高,热磨损愈严重。
(2)开裂失效,在实际生产中裂纹分布在模具的某些部位,它经过一定的服役期,萌生细小的裂纹,并逐渐向纵深扩展,裂纹扩展到一定尺寸后,将严重削弱模具的承载能力而引起断裂,或在原热处理和加工制造模具时已经产生微裂纹,使模具在服役中容易扩展从而发生早期裂纹。
失效原因在设计方面主要是模具强度设计及过渡处圆角半径的选择;制造方面主要是材质的预检和加工时表面粗糙度及加损伤方面的注意,以及热处理和表面处理质量的影响。
在使用中主要注意模具预热、挤压比及锭坯温度的掌握以及挤压速度和金属变形流动的控制。
(3)变形失效,变形失效就是模具在使用中出现悬臂偏心、下陷,分流模上模在使用中出现的舌头偏心及下模出现的型腔塌陷、型孔胀大、棱角倒塌等失效形式,主要原因有材料强度不高;或模具材料虽选择正确,但热处理工艺不正确,未充分发挥模具钢的强韧性;或分流模设计不当,使流速不均,造成对舌头的侧向力不均而产生偏心;还有就是分流模虽设计正确,但加工制造水平不高,使进入各分流孔的流速不均,造成侧向力不同而导致偏心。
铝合金型材挤压模具及挤压生产流程详解
铝合金型材挤压模具及挤压生产流程详解铝合金型材挤压模具是一种用于加工铝合金型材的工具。
铝合金型材挤压生产流程如下:1. 材料准备:首先需要准备好适用于挤压的铝合金材料。
通常情况下,采用的是具有良好延展性和可塑性的铝合金材料。
2. 模具设计:根据产品的形状和尺寸要求,设计合适的挤压模具。
模具的设计需要考虑产品的形状、尺寸、角度和曲率等因素。
3. 模具制造:根据设计好的模具图纸,制造出挤压模具。
通常情况下,模具由高强度的工具钢制成,以确保其耐磨性和寿命。
4. 模具安装:将制造好的挤压模具安装在挤压机上。
挤压机是用于将铝合金材料加热并迫使其通过模具的设备。
5. 加热材料:将铝合金材料加热至所需的挤压温度。
挤压温度可以根据铝合金的特性和产品的要求进行调整。
6. 挤压加工:将加热好的铝合金材料送入挤压机中,通过压力迫使其通过模具。
在挤压过程中,铝合金材料会受到模具的限制,被迫形成与模具相同的形状。
7. 冷却处理:经过挤压后,铝合金型材会以较高的温度存在。
为了增加其强度和硬度,需要对其进行冷却处理。
冷却处理可以通过水冷或空气冷却进行。
8. 切割和加工:经过冷却处理后的铝合金型材需要进行切割和加工。
通常会使用锯床或切割机对其进行切割,并使用机械加工设备对其进行进一步的加工和修整。
9. 表面处理:为了提高铝合金型材的耐腐蚀性和表面光洁度,通常会对其进行表面处理,如阳极氧化、粉末涂装等。
10. 检验和包装:最后,对挤压生产出来的铝合金型材进行检验,确保其质量符合要求。
合格的铝合金型材会进行包装和标识,待发货或存储。
以上是铝合金型材挤压模具及挤压生产流程的详细解释。
铝型材挤压模具设计中的关键点和问题
铝型材挤压模具设计中的关键点和问题一、材料选择:在铝型材挤压模具设计中,材料的选择十分重要。
模具的材料应具有良好的硬度、强度和耐磨性。
常见的模具材料有H13、3Cr2W8V、4Cr5MoSiV1等。
根据使用要求和成本控制,选择合适的材料。
二、模腔设计:模腔的设计是铝型材挤压模具设计的核心。
模腔的几何形状和尺寸应符合产品的要求,并能保证产品的几何精度。
在设计模腔时,应考虑材料的流动性、收缩率、气泡和焊接等问题,以确保铝型材的挤压过程顺利进行。
三、内冷却设计:内冷却设计是提高模具使用寿命和产品质量的重要手段。
通过合理布置冷却水管道,能够在挤压过程中及时冷却模具,降低模具的工作温度,减少模具磨损和热载荷,延长模具寿命。
四、橡胶垫设计:橡胶垫在铝型材挤压过程中起到密封和保护模具的作用。
橡胶垫的设计应考虑到材料的选择、厚度、硬度和形状等因素,以确保橡胶垫能够准确地封闭模腔,并能够承受高压和高温的挤压过程。
五、冷却系统设计:冷却系统的设计直接影响到挤压速度和产品质量。
合理的冷却系统能够快速冷却挤压铝型材,降低铝材的热度和产生的内应力,提高铝材的强度和硬度。
冷却系统的设计应综合考虑冷却水的流量、速度、温度和位置等因素。
六、毛刺控制:毛刺是铝型材挤压过程中常见的缺陷之一、在模具设计中,应考虑到挤压过程中金属的流动和退火等因素,采取合适的措施来控制毛刺的产生。
例如,合理设计模腔的边缘形状,使用抛光或涂覆耐磨材料等。
七、凸模设计:凸模的设计直接影响到铝型材的外形和尺寸精度。
凸模的形状、尺寸和相对位置应合理设置,以确保铝材的挤压过程顺利进行,并且保证产品的几何精度和表面质量。
八、磨损和冲击问题:由于挤压过程中金属的高速流动和冷却周期的反复,模具表面很容易受到磨损和冲击。
因此,在模具设计过程中应考虑到材料的硬度、涂层和冲击吸收等因素,以延长模具的使用寿命和提高产品质量。
九、模具拆卸与维护:在设计模具时,应考虑到模具的维护和拆卸。
铝型材挤压工艺及模具设计
铝型材挤压工艺及模具设计1. 挤压工艺铝型材挤压是一种利用压力对铝型材进行塑性变形的加工工艺。
其基本工艺是:铝棒坯料通过加热软化后,被压入模头,通过模头出口挤出成需要的截面形状。
铝型材挤压工艺的优点包括:高成形精度、高表面质量、操作简便,高生产效率等等。
2. 模具设计铝型材挤压的模具主要包括模头、辅助金属件、固定板、滑动板、胚料夹持装置等组成。
其中,模头是铝型材挤出的关键装置,包括卡箍板、模板、模板底部垫片、模座、模膜等部分。
模头的最重要的特点是不同形状的铝型材需要不同形状的模头;其次需要各个部位的设计匹配度高,精度要求高。
滑动板和固定板是模具的基础结构,他们需要耐压、耐磨,同时需要精度高、边缘无毛刺。
辅助金属件在滑动板、固定板及模头之间起到了加强固定的作用,除此之外还需要具有良好的导向功能。
2.2. 理论参数的确定合理的选择合适的挤压荷载能够很好的保证挤压过程中的质量,同时也能够最大限度的提高生产效率。
因此,在模具设计阶段,应尽可能的确定相应的理论参数。
此外,应还需根据压力、速度、保压时间等因素来确定合适的机器配置,以及最优的辅助系统。
为了达到最优的效果,这些参数需要经过实验验证。
2.3. 模具材料的选择对于铝型材挤压模具来说,常见的材料包括H13钢、特种合金钢、定向硅钢、硬质合金等材料。
如:H13钢:具有高的耐磨性、硬度和强度,适用于铝型材的大批量生产。
特种合金钢:高抗氧化性、高强度、高磨损性,这些特性使其适用于生产高性能和高质量的铝型材。
硬质合金:它具有高硬度和强度、高耐磨性和高耐蚀性,是生产大规模、高复杂度的模具的首选。
2.4. 设计注意事项在模具设计过程中还需要注意以下问题:1)要防止铝材在挤压过程中发生撕裂断裂,因此要注意模具底部的角度把控2)要避免孔洞过大过小,且要容易拆卸,之所以拆卸是为了清洁铝型材上残余物。
3)在设计过程中,要考虑铝型材的变形,保证材料截面和尺寸的均匀性。
4)在滑动板部位,还需要考虑降低铝型材与模具接触时所产生的不良效果,例如顶出口和顶料等问题。
- 1、下载文档前请自行甄别文档内容的完整性,平台不提供额外的编辑、内容补充、找答案等附加服务。
- 2、"仅部分预览"的文档,不可在线预览部分如存在完整性等问题,可反馈申请退款(可完整预览的文档不适用该条件!)。
- 3、如文档侵犯您的权益,请联系客服反馈,我们会尽快为您处理(人工客服工作时间:9:00-18:30)。
定颈带长度对模具以及制品的影响:
过短,尺寸不稳定,降低使用寿命 过长,增大摩擦力,制品表面出现划伤、毛刺、麻面、
搓衣板型波浪等缺陷
定颈带长度的确定原则:
根据压力机的结构(立式或卧式)、被挤压金属材料、 产品的形状和尺寸等因素来确定。
(3)出口直径d出或出口喇叭锥
出口直径对模具以及制品的影响:
过小,易划伤制品表面,甚至会引起堵模 过大,引起定颈带过早地变形、压塌,明显地降低模具的使用寿命。
• 按合金成分
铝合金成型工艺
➢铸锭制备 ➢挤压成型 ➢热处理 挤压模具技术的发展概况
2.挤压模具结构要素
定义:
挤压模的一般外形结构和断面形 状。
(1)模角
定义: 模子轴线与其工作端面所构成的夹角
模角α的特点及作用
a)平模的模角α等于90°——较大的死区,阻止铸锭表面的 杂质、缺陷、氧化皮等流到制品的表面;某些易在死区产 生裂纹与断裂的金属与合金,表面分层、起皮和小裂纹 a)平模挤压消耗挤压力大,模具易变形,甚至压塌 b)锥形模,减小挤压力 c)条件 d)摩擦力
5、保证足够的模具强度
一般平面模 舌型模和平面分流
六、模具设计的技术条件及基本要求
➢有适中而均匀的硬度 ➢有足够高的制造精度 ➢有足够低的表面粗糙度 ➢有良好的对中性、平行度、直线度和垂直度 ➢模具无内部缺陷 ➢不得出现棱角
七、铝型材挤压模具的种类及组装形式
1、挤压工具分类
a)大型基本挤压工具 b)模具 c)辅助工具
八、设计实例
设计方案
尺寸 热处理 精度
制造工艺流程
✓车加工 ✓铣加工
原因: 上模形状复杂
✓电火花加工
注意: 选取石墨电极时, 不能有疏松和夹杂 等缺陷
✓线切割加工
热处理 模具试制应注意的问题
热处理完后要进行精加工 两端面合模后贴合无缝 精配合型孔壁厚达到图纸要求
(2)定颈带长度h定和直径d定
定义:
又称工作带,是模子中垂直模子工作端面并用以保证挤压 制品的形状、尺寸和表面质量的区段。
设计d定的基本原则:
在保证挤压制品在冷却状态 下不超出图纸规定的制品公差的 条件下,尽量延长模具寿命。
影响制品尺寸的因素:
温度 模具材料 被挤压金属材料 制品形状和尺寸 拉伸矫直量 模具变化情况
铝型材挤压模具
内容
• 产品简介 • 铝合金成型工艺 • 铝型材挤压模具结构 • 模具设计应考虑的因素 • 模具设计原则与步骤 • 技术条件及基本要求 • 模具种类及组装形式 • 设计实例
一、产品简介
1.定义
铝型材,就是铝棒通过热熔、挤压, 从而得到不同截面形状的铝材料
2.分类 • 按用途
①建筑铝型材 ②散热器铝型材 ③一般工业铝型材 ④轨道车辆结构铝合金型材 ⑤装裱铝型材
2、挤压模具分类及特点
模孔压缩区断面形状 被挤压的产品品种 模孔数目 挤压方法和工艺特点 模具结构 模具外形结构
几种常见的特殊结构模具:
桥式模 平面组合模 多孔空心壁板模 前室模 宽展模
保护模 变断面型材模 水冷模 其他结构的模具
3、挤压模具的组装方式
➢带倒椎体的模支承 ➢带正椎体的模支承
2、模孔在模子平面上合理布置
将单个或多个模孔合理地分布在模子平面上,使之 在保证模子强度的前提下获得最佳金属流动均匀性。
①单孔的棒材、管材和对称良好的型材模 ②各部分壁厚相差悬殊和对称性很差的产品 ③多空模的布置主要考虑模孔数目、模子强度,
制品表面的质量、金属流动的均匀性等问题
3、模孔尺寸的合理计算
在设计前,拟定合理的工艺流程和选择最佳的工艺 参数,综合分析影响模具效果的各种因素,是合理 设计挤压模具的必要和充分条件。
五、模具设计的原则与步骤
确定设计模腔参数 模孔在模子平面上合理布置 模孔尺寸的合理计算 合理调整金属的流动速度 保证足够的模具强度
1、确定设计模腔参数
a)设计正确的挤压型材图 b)拟定合理的挤压工艺 c)选择适当的挤压筒尺寸 d)挤压系数和挤压力 e)确定模孔数
设计原则:
(4)入口圆角
定义: 模子工作端面与定颈带形成的端面角。
作用: 选取原则:
(5)其他结构要素
3、模具的外形尺寸及其标准化
(1)外形结构
(2)外形尺寸的确定原则
外形尺寸定义: 原则:
模子的外圆直径D模
挤压机的结构形式和能力
厚度H模
挤压筒的直径
外形锥角
型材在模子工作平面上的分布位置
模孔外接圆的直径
①被挤压合金的化学成分 ②产品的形状 ③公称尺寸及允许公差 ④挤压温度及在此温度下模具材料与被挤压合金的热膨胀系数 ⑤产品断面上的几何形状的特点及其在挤压和拉伸矫正时的变化 ⑥挤压力的大小 ⑦模具的弹性变形情况
A=A。+M+[Ky+Kp+Kr]A。
4、合理调整金属的流动速度
①每一个质点应以相通的速度流出模孔 ②尽量采用多孔对称排列 ③中心很远的部分可采用促流角,或采用导料锥来加速金属的流动 ④阻碍角 ⑤工艺平衡孔,工艺余量,或者采用前室模、导流模
型材断面是否有影响模具 整套工具强度的因素
公式确定模具外圆直径:
①当挤压筒直径小于200mm时,D模>0.6D。 为了简化起见,可以直接取D模=(0.8~1)D筒。 ②模具的厚度H模应尽量薄,规格应尽量小, 以便于管理和使用。
(3)模具外形尺寸标准化和系列化
四、挤压模具设计应考虑的因素
➢模子设计者确定的要素 ➢模子制造者确定的因素 ➢挤压生产者确定的因素