铝型材挤压模具设计实践
扁方管挤压铝型材模具设计方法
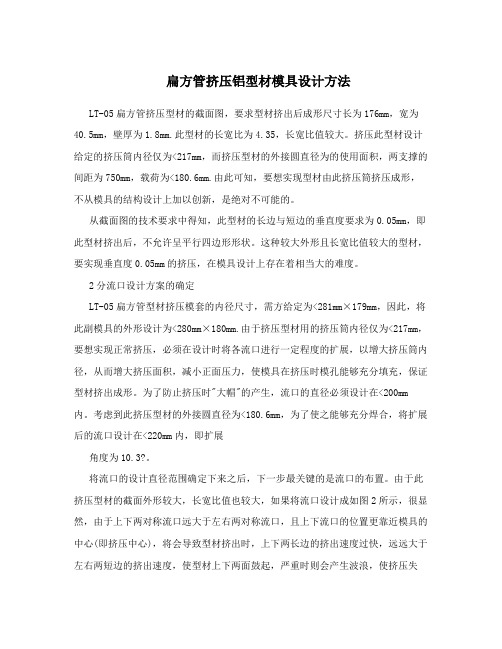
扁方管挤压铝型材模具设计方法LT-05扁方管挤压型材的截面图,要求型材挤出后成形尺寸长为176mm,宽为40.5mm,壁厚为1.8mm.此型材的长宽比为4.35,长宽比值较大。
挤压此型材设计给定的挤压筒内径仅为<217mm,而挤压型材的外接圆直径为的使用面积,两支撑的间距为750mm,载荷为<180.6mm.由此可知,要想实现型材由此挤压筒挤压成形,不从模具的结构设计上加以创新,是绝对不可能的。
从截面图的技术要求中得知,此型材的长边与短边的垂直度要求为0.05mm,即此型材挤出后,不允许呈平行四边形形状。
这种较大外形且长宽比值较大的型材,要实现垂直度0.05mm的挤压,在模具设计上存在着相当大的难度。
2分流口设计方案的确定LT-05扁方管型材挤压模套的内径尺寸,需方给定为<281mm×179mm,因此,将此副模具的外形设计为<280mm×180mm.由于挤压型材用的挤压筒内径仅为<217mm,要想实现正常挤压,必须在设计时将各流口进行一定程度的扩展,以增大挤压筒内径,从而增大挤压面积,减小正面压力,使模具在挤压时模孔能够充分填充,保证型材挤出成形。
为了防止挤压时"大帽"的产生,流口的直径必须设计在<200mm 内。
考虑到此挤压型材的外接圆直径为<180.6mm,为了使之能够充分焊合,将扩展后的流口设计在<220mm内,即扩展角度为10.3?。
将流口的设计直径范围确定下来之后,下一步最关键的是流口的布置。
由于此挤压型材的截面外形较大,长宽比值也较大,如果将流口设计成如图2所示,很显然,由于上下两对称流口远大于左右两对称流口,且上下流口的位置更靠近模具的中心(即挤压中心),将会导致型材挤出时,上下两长边的挤出速度过快,远远大于左右两短边的挤出速度,使型材上下两面鼓起,严重时则会产生波浪,使挤压失败。
如果将左右流口相应扩大,上下流口相应减小,虽然能使流速得到一定的改善,但由于上模型芯在左右两侧探出流口的部分较大,直接受到正面挤压力的作用。
几种铝型材挤压模具的优化设计

轻
合
金
加
工
技
术
/’
几种铝型材挤压模具的优化设计
!"#$%$&$’( )*+$(’ ,- .*/*012 )$*+ -,0 34#056$’( 725%$’$5% 722,8
于 立 敏
23 45&657
(北京铝材厂, 北京 !%!!*()
摘要: 铝型材的挤压缺陷很大一部分与挤压模的设计和结构有关。 简要介绍了部分大断面空心型材、 双模孔易偏壁空心 型材、 小开口悬臂面积大的平面型材、 壁薄而长宽比大的平面型材等挤压模的优化设计。 关键词: 铝型材; 挤压模; 设计; 矮墙式阻流带; 尺寸余量; 悬臂桥; 桥式供料板 中图分类号: 89%/)’.*! 文献标识码: : 文章编号: ("%%" ) !%%)&)"/’ %’&%%/’&%/
参 考 文 献2
3"4 3$4
王孝培 . 冲压设计资料 3#4. 北京 2 机械工业出版社, "(’&. 罗曼诺夫斯基(苏) . 冷压手册 3#4. 北京 2中国工业出版社, "(’*.
)
结束语
实践证明,以上几种铝型材挤压模具设计的优化
图# 带桥式供料板的长断面型材模
在实际生产中都是行之有效的。挤出的铝合金型材与 过去 的 相 比 , 成形好、 尺寸精度易保证、 表面质量也得 到了良好的改善。从而大大提高了挤压型材的生产效 率, 降低了生产成本。 随着各行业的经济发展,对铝型材断面形状的要
求也逐渐复杂化, 多样化, 按常规形式设计, 存在许多 不足。因此, 要生产出各种优质型材, 就要在生产、 工作 中不断地学习、 积累经验, 不断地改革和创新。
壁厚悬殊铝型材挤压模具的一般设计方法
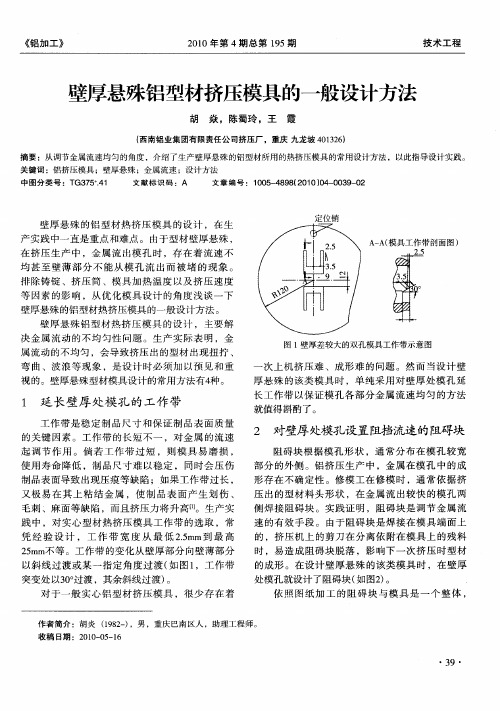
长 工作 带 以保 证 模 孔 各 部 分金 属 流速 均 匀 的方 法
就值 得斟酌 了。
2 对壁厚 处模孔设置 阻挡流速的 阻碍块
阻 碍块 根 据 模 孔 形 状 ,通 常分 布在 模 孔 较 宽 部 分 的外 侧 。铝 挤 压 生 产 中 ,金 属 在模 孔 中 的成
起 调 节 作 用 。 倘 若 工 作 带 过 短 ,则 模 具 易 磨 损 , 使 用 寿命 降低 ,制 品尺 寸 难 以稳 定 ,同 时会 压 伤 制 品表 面 导致 出现 压 痕等 缺 陷 ;如果 工 作 带过 长 , 又 极 易 在 其 上 粘 结 金 属 ,使 制 品 表 面 产 生 划 伤 、
的成 形 。在 设 计 壁 厚 悬殊 的该 类 模 具 时 ,在 壁 厚 处模孔 就设计 了阻碍块 ( 图2 。 如 )
2mm不等 。工作 带 的变化 从 壁 厚部 分 向壁 薄部 分 5
以斜 线 过 渡 或 某 一指 定 角 度 过 渡 ( 图 1 如 ,工 作 带
突变处 以3 。 渡 ,其余 斜线过 渡 ) 0过 。
对 于 一 般 实 心 铝 型 材 挤 压 模 具 ,很 少 存 在 着
依 照 图纸 加 工 的 阻碍 块 与 模 具 是 一 个 整 体 ,
作 者 简 介 :胡 炎 (9 2 ) 18 一 ,男 ,重 庆 巴南 区人 ,助 理 工 程 师 。
收 稿 日期 :2 1— 5 1 00 0 — 6
流 模 腔 ,实 现 初 次分 配 ,然后 迅 速 到达 前 置 室 焊
3 对壁薄处模孔设 置前置室焊合腔
根 据 型材 名 义 尺 寸 ,设 计 热 挤 压模 具 时 ,对
宽 窄不 同的模 孔设 置深 浅 不 一 的焊合 腔 。焊 合 腔
薄壁铝型材挤压模具设计和维护

1挤压模具介绍挤压模具结构设计和制造环节较多,包括选材、设计、制造、修模等环节,其成本占到型材挤压生产成本的35%左右。
在型材加工生产中,一般有两种主要挤压方法:分流组合模挤压法和穿孔针挤压法。
前者加工起来简单且成本较低,后者成本高且应用范围较小,在实际型材加工生产中,分流组合模应用更为广泛。
1.1挤压模具的工作条件。
对于大截面复杂型材的挤压成形,挤压难度比较大,对挤压模具的结构与形状要求也很高,特别是对于这种断面形状较复杂,壁厚相差悬殊,断面面积及外接圆大,多腔空心等型材,挤压模具的工作条件变得更加恶劣。
因此,对挤压模具要求较高,主要有如下几个方面:一是高温高压条件下工作;二是要具有较好的抗磨损能力;三是具有很高的强度和韧性,避免在工作中出现应力集中而使模具破坏。
1.2挤压模具的分类。
挤压模具种类很多,根据不同的分类条件可以进行归类。
分类的主要依据有模具结构和模孔压缩区断面外形。
分流组合模在目前是应用最为广泛的一种模具形式,平面分流组合模的组成结构主要包括上模、下模、定位销和联结螺钉四个部分,其工作原理是在一定的挤压力作用下,锅淀通过分流孔被分流成金属流,流经焊合室进行汇集和傅合,最终由模芯和模孔流出,形成具有所要求几何形状的型材产品。
1.3模具的设计步骤。
实际生产中,产品类型、工艺方法、设备和模具结构都是影响模具设计过程的重要因素。
但是在设计过程中,挤压模具模腔的设计一般按照以下步骤进行:1.3.1模腔参数确定和模孔布置。
模腔参数的确定主要根据挤压机、工艺规程和现场工具设备来确定。
模孔布置合理与否直接影响着模具强度,同时影响金属流动的均匀性。
一般在设计过程中,即使非对称的型材也要尽量保证模孔的对称性,同时使其尽量接近中心紧凑一些。
通常情况下,模孔多设置在同心圆上(模孔之间的间距大于30-50mm,模孔距离模具边缘大于25-50mm,模孔与挤压筒边缘的距离大于20-40mm)。
1.3.2设计模孔尺寸。
铝合金边封型材挤压模具设计

目录摘要 (3)ABSTRACT (4)1、绪论 (6)1.1、引言 (6)1.2、挤压模具在铝型材挤压生产中的重要性 (6)1.3、铝型材挤压模具技术发展概况 (9)1.4、论文的主要研究内容 (11)2、型材挤压模具设计技术 (11)2.1、型材模具的设计原则及步骤: (11)2.1.1、挤压模具设计时应考虑的因素: (11)2.1.2、模具设计的原则与步骤: (12)2.1.3、模具设计的技术条件及基本要求: (15)2.2、挤压模典型结构要素的设计: (16)2.2.1、模角: (16)2.2.2、定径带长度和直径: (17)2.2.3、出口直径或出口喇叭锥: (17)2.2.4、入口圆角: (18)2.3、确定采用平面和分流模的原则: (18)2.4、平面分流组合模的特点与结构: (19)2.4.1、工作原理与特点: (19)2.4.2、分流组合模的结构: (21)2.5、模具外形尺寸的确定原则: (22)3、铝合金边封型材挤压模具设计技术 (23)3.1、封边铝型材的模具设计: (24)3.1.1、封边铝型材产品结构分析: (24)3.1.2、铝合金封边型材挤压模具整体结构设计方案: (24)3.1.3、铝合金封边型材模具结构设计: (25)3.1.4、铝合金封边型材模具结构设计详图: (35)4、模具的选材与热处理及维护与保养 (37)4.1、模具材料的选择: (37)4.1.1、模具材料的使用条件: (37)4.1.2、模具材料的性能要求: (38)4.1.3、挤压工模具选材的特点: (39)4.1.4、模具材料的选择: (41)摘要铝合金因质轻、美观、良好的导热性和易加工成复杂的形状,而被广泛地用于工业生产的各种环节,尤其是散热,装饰门窗等方面。
铝合金型材涉及多种样式,多种功能。
与其他铝型材比,铝合金封边型材有其自身的特点:卡位之间距离长,深宽比很大,中间部分为保证材料壁厚的均匀通常挖空处理,截面拐点多,且多呈直角分布并有受力需求。
第八讲_空心铝型材挤压模具优化设计_2_赵云路 (2)

第八讲 空心铝型材挤压模具优化设计(2)沈阳新光模具制造公司 赵云路西南铝加工厂 刘静安 在不带穿孔装置的普通型、棒挤压机上生产空心型材,必须采用一种特殊结构的模子—分流组合模。
实心锭在挤压筒中,通过挤压机作用在挤压轴上的力使锭从模孔中挤出之前先分成几股,随后再在模孔前汇合,形成围绕模芯的环形整体而被挤出模孔,形成闭合的空心型材。
分流组合模的特点是必须有一个或几个形成内腔的芯子,芯子设计在桥上,桥把金属辟开成几股而流向模孔。
由于模桥设计的不同,分流组合模可分为平面分流模(分流模)、舌型模(桥式模)和叉架模等。
1 平面分流组合模的特点平面分流组合模一般用来生产空心和悬臂较大的半空心型材。
在建筑型材中,大多数都是外形较大,壁较薄,断面形状复杂,沟槽和丝孔较多的空心和半空心型材。
在空心型材中又出现单腔、双腔和多腔。
即使在有穿孔系统的挤压机上也很难实现挤压生产。
在生产半空心型材或断面壁厚相差悬殊的型材时,如果采用平模,无论怎样调整工作带和设计促流角或阻碍角,都很难把流速调整均匀。
若采用分流组合模,用分流孔和桥芯来调整流速,就很少出现波浪、扭拧和弯曲。
能够很顺利地生产出合格产品。
平面分流模较舌型模易加工,在挤压生产时操作简单,分离残料较舌型模易加工,生产效率高,残料较舌型模短,产品的成品率也高。
对于形状复杂的半空心型材,分流模结构可减小悬臂上的承压力,保证模具强度。
用分流模可实现多根铸锭的连续挤压,按需要的制品长度截取。
还可实现在小挤压机上挤出外形较大规格的产品,并且可以达到所给定的变形量。
用分流组合模,可采用实心铸锭在型、棒挤压机上一次生产单根和多根管材,制品内外表面好,尺寸精确。
但分流组合模和平模相比,用它生产的型材存在焊缝。
如果模具上涂油或铸锭表面不干净,制品焊缝中会存在夹渣。
若挤压温度过低或模具设计不合理,都会影响焊合质量。
另外,分流模的变形阻力较平模大,目前只限于生产一些纯铝、铝-锰和铝-镁-硅合金。
挤压铝型材模具课程设计

挤压铝型材模具课程设计一、课程目标知识目标:1. 学生能够掌握铝型材挤压模具的基本结构及其工作原理;2. 学生能够理解并描述挤压过程中金属流动特性及对模具设计的影响;3. 学生能够了解并运用模具设计的相关技术参数和标准。
技能目标:1. 学生能够运用CAD软件进行铝型材模具的基本设计;2. 学生能够分析实际工程问题,提出合理的模具设计方案;3. 学生能够通过实验和模拟,对模具设计进行优化和改进。
情感态度价值观目标:1. 学生能够培养对模具设计及制造工作的兴趣,增强工程意识;2. 学生能够认识到模具设计在制造业中的重要性,树立质量意识;3. 学生能够通过团队协作,培养沟通、交流和解决问题的能力。
本课程针对高中年级学生,结合学科知识深度,注重理论联系实际,培养学生实际操作能力。
课程性质为实践性较强的设计课程,要求学生在掌握基础知识的基础上,运用所学技能解决实际问题。
通过本课程的学习,使学生能够达到以上所述的具体学习成果,为后续相关专业课程的学习打下坚实基础。
二、教学内容1. 铝型材挤压模具基础知识- 模具的分类、结构及其工作原理;- 铝型材挤压工艺流程及其对模具的影响;- 模具设计的相关技术参数和标准。
2. 铝型材模具设计方法- CAD软件在模具设计中的应用;- 模具设计的基本原则和步骤;- 模具设计中金属流动分析及优化。
3. 模具设计实例分析- 分析实际工程中的铝型材模具设计案例;- 针对不同类型的铝型材,讨论模具设计的要点和注意事项;- 通过实例,引导学生运用所学知识解决实际问题。
4. 模具设计的实验与模拟- 实验室进行铝型材挤压实验,观察金属流动现象;- 利用模拟软件进行模具设计验证,优化设计方案;- 分析实验与模拟结果,提出改进措施。
教学内容依据课程目标,结合教材相关章节进行组织。
教学进度安排如下:第1周:铝型材挤压模具基础知识学习;第2周:铝型材模具设计方法及CAD软件应用;第3周:模具设计实例分析;第4周:模具设计的实验与模拟。
推拉窗铝合金型材热挤压模设计设计word版
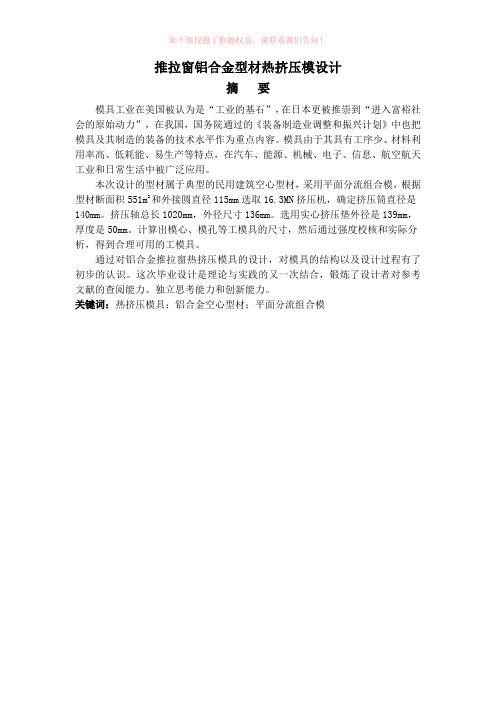
推拉窗铝合金型材热挤压模设计摘要模具工业在美国被认为是“工业的基石”,在日本更被推崇到“进入富裕社会的原始动力”,在我国,国务院通过的《装备制造业调整和振兴计划》中也把模具及其制造的装备的技术水平作为重点内容。
模具由于其具有工序少、材料利用率高、低耗能、易生产等特点,在汽车、能源、机械、电子、信息、航空航天工业和日常生活中被广泛应用。
本次设计的型材属于典型的民用建筑空心型材,采用平面分流组合模,根据型材断面积551m2和外接圆直径115mm选取16.3MN挤压机,确定挤压筒直径是140mm。
挤压轴总长1020mm,外径尺寸136mm。
选用实心挤压垫外径是139mm,厚度是50mm。
计算出模心、模孔等工模具的尺寸,然后通过强度校核和实际分析,得到合理可用的工模具。
通过对铝合金推拉窗热挤压模具的设计,对模具的结构以及设计过程有了初步的认识。
这次毕业设计是理论与实践的又一次结合,锻炼了设计者对参考文献的查阅能力、独立思考能力和创新能力。
关键词:热挤压模具;铝合金空心型材;平面分流组合模Sliding 88822 aluminum alloy hot extrusion die designAbstractMold industry in the United States is considered to be "the cornerstone of industry", in Japan even been respected to the "raw power into the affluent society", in China, the State Council passed the "equipment manufacturing restructuring and revitalization plan," also the mold and manufacturing the technical level of equipment as the main focus. Because of its small mold processes, material utilization, low energy consumption, easy to produce, etc., in the automotive, energy, machinery, electronics, information, aerospace industry and are widely used in daily life.The design of the profile is typical of civil hollow profiles, using the plane porthole die, according to the profiles basal area 551m2 and circumcircle diameter 115mm Select 16.3MN extruder, extrusion cylinder diameter is determined 140mm. Extrusion axis length 1020mm, diameter size 136mm. Extruded solid selection pad diameter is 139mm, thickness 50mm. Calculate the mold core, mold tooling holes and other dimensions, and then through the strength check and the actual analysis, reasonably available tooling.By hot extrusion aluminum sliding mold design, mold structure and the design process have a preliminary understanding. The graduation project is yet another combination of theory and practice, exercise designers references inspection, independent thinking and innovative ability.Keywords:hot extrusion dies; aluminum hollow profiles; plane Porthole Die目录摘要Abstract第一章概述 (1)1.1铝合金挤压技术的概况及发展趋势 (1)1.1.1铝合金挤压技术的概况 (1)1.1.2铝挤压技术的发展趋势 (1)1.2铝合金门窗的特点和发展趋势 (1)1.2.1铝合金门窗的特点 (1)1.2.2铝合金门窗的发展趋势 (2)1.3挤压模具种类和特点 (2)1.4 研究的目的和意义 (3)第二章挤压产品的工艺分析 (4)2.1产品代号及设计要求 (4)2.2产品形状及结构分析 (4)2.2.1形状和尺寸分析 (4)2.2.2 尺寸偏差的选择 (5)2.2.3产品材料分析 (7)2.3成形工艺分析与选择 (7)2.3.1挤压方法的确定 (7)2.3.2挤压工艺制度的确定 (8)2.4 模具总体结构分析 (9)第三章工艺计算 (11)3.1坯料尺寸的计算 (11)3.1.1 坯料直径的计算 (11)3.1.2坯料长度的计算 (12)3.2挤压力的计算 (12)3.3挤压机的选择 (15)3.4压力中心的计算 (16)第四章挤压工模具结构设计 (17)4.1模具结构设计 (17)4.1.1分流孔的设计 (17)4.1.2分流桥的选择 (19)4.1.3模芯的设计 (19)4.1.4 焊合室的选择 (20)4.1.5模孔尺寸的确定 (20)4.1.6 模孔工作带长度的确定 (21)4.1.7 模孔空刀结构设计 (22)4.18 模具外径及厚度的确定 (22)4.2模具的强度校核 (23)4.2.1 抗弯强度校核 (23)4.2.2 抗剪强度校核 (23)4.3挤压筒的设计 (24)4.3.1挤压筒的结构形式 (24)4.3.2挤压筒的加热方式 (24)4.3.3 挤压筒工作内套的结构 (24)4.3.4 挤压筒与模具的配合方式 (24)4.3.5 挤压筒结构尺寸的设计与强度校核 (25)4.4挤压轴的设计 (27)4.4.1挤压轴的结构形式 (27)4.4.2挤压轴的尺寸确定 (27)4.4.3挤压轴的强度校核 (28)4.5挤压垫的结构设计 (29)4.5.1 挤压垫片尺寸的确定 (29)4.5.2 挤压垫的强度校核 (29)4.6模具实体图 (30)总结 (32)参考文献 (33)致谢 (34)第一章概述1.1铝合金挤压技术的概况及发展趋势1.1.1铝合金挤压技术的概况随着科技和国民经济的不断发展,铝合金型材挤压所使用的工模具产业技术有了非常的进步过程。