滚动轴承常见的失效形式及原因分析
机械设计(9.4.1)--滚动轴承内部载荷分布及失效分析

二、失效形式
9-4 滚动轴承内部载荷分布及失效分析 一、载荷分布
1. 滚动轴承内部载荷分布
承受不偏心轴向载荷 A
承受径向载荷 R 或轴向 A 和径向 R 联 合载荷
各滚动体受力不等
一、载荷分布
9-4 滚动轴承内部载荷分布及失效分析 一、载荷分布
1. 滚动轴承内滚动轴承内部载荷分布及失效分析 一、载荷分布
1. 滚动轴承内部载荷分 布
固定套圈
一、载荷分布
9-4 滚动轴承内部载荷分布及失效分析 二、失效形式
1. 失效形式
① 疲劳点蚀
② 塑性变形
二、失效形式
9-4 滚动轴承内部载荷分布及失效分析 二、失效形式
1. 失效形式
③ 磨损
④ 套圈断裂
滚道 磨损
滚动轴承寿命校核
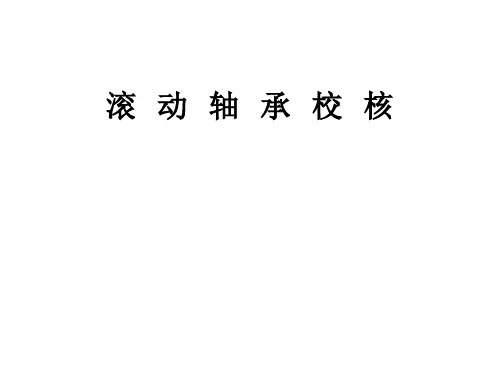
70000B(=40°) Fd=1.14Fr
2
Fa1 C0
1005.05 20000
0.0503
Fa 2 C0
605.05 20000
0.0303
由表2进行插值计算,得e1=0.422,e2=0.401。再计算
5、应用
例 设某支撑根据工作条件决定选用深沟球轴承。轴承径向载
荷Fr=5500N,轴向载荷Fa=2700N,轴承转速n=1250r/min,装轴
承处的轴颈直径可在50~60mm范围内选择,运转时有轻微冲击,
预期计算寿命Lh’=5000h。试选择其轴承型号。
解
1. 求比值
Fa Fr
2700 5500
产生派生轴向力的原因:承载区内每个滚动体的反力 都是沿滚动体与套圈接触点的法线方向传递的。
轴承安装不同时,产生的派生轴向力也不同。
工作情况2
派生力的方向总是由轴承宽度中点指向轴承载荷 中心。
S的方向:沿轴线由轴承外圈的宽边→窄边。
轴承所受总载荷的作用线与轴承轴心线的交点 , 即 为轴承载荷中心(支反力的作用点)。
4、滚动轴承寿命的计算公式
4.1 轴承的载荷-寿命曲线
如右图所示曲线是在
大量试验研究基础上得出
的代号为6208轴承的载荷寿命曲线。其它型号的轴
承也有与上述曲线的函数
规律完全一样的载荷-寿命
曲线。
该曲线公式表示为:
轴承的载荷-寿命曲线
L10
(C P
)(106 转)
式中,L10的单位为106r。 P为当量动载荷(N)。
角接触球轴承及圆锥滚子轴承的派生轴向力的大小取 决于该轴承所受的径向载荷和轴承结构,按下表计算。
§13-4 滚动轴承的寿命计算
第9章滚动轴承

第二节 常用滚动轴承类型、代号及选择
角接触球轴承
类型代号:70000C/AC/B
尺寸系列代号: 19、(1)0、(0)2、 (0)3、(0)4、
特点:可承受径向载荷 和单向轴向载荷。
第二节 常用滚动轴承类型、代号及选择 推力圆柱滚子轴承
类型代号:80000 尺寸系列代号: 11、12 特点:只能承受单向轴向 载荷。要求轴刚度大。
转化原则 寿命相同
计算寿命时条件不 同,不方便比较
第四节 滚动轴承寿命计算
当量动载荷 1.仅能承受径向载荷的轴承 圆柱滚子轴承(N0000型) 和滚针轴承(NA0000型) 2.仅能承受轴向载荷的推力轴承 推力球轴承(51000、52000型) 推力圆柱滚子轴承(80000型) 径向载荷
PR
轴向载荷
第二节 常用滚动轴承类型、代号及选择 双列深沟球轴承
类型代号:40000 尺寸系列代号: 2(2) (2)3 特点:可同时承受径向载 荷和双向轴向载荷,比 深沟球轴承承载能力大。
第二节 常用滚动轴承类型、代号及选择 推力球轴承
类型代号:50000 尺寸系列代号:11、12、 13、14 特点:只能承受单方向的 轴向载荷,极限转速较低。
(3)调心性能
轴承座孔不平行 调心轴承
非调心轴承
非调心轴承
轴承座孔不同轴 调心轴承 轴挠曲变形 非调心轴承 调心轴承
第二节 常用滚动轴承类型、代号及选择
(4)轴承的安装和拆卸 无内圈
第二节 常用滚动轴承类型、代号及选择
2. 尺寸选择
类型——类型代号,根据载荷的大小、性质选取
内径——内径代号,根据轴径选取
第九章 滚动轴承
第一节 概述 第二节 常用滚动轴承的类型、代号及选择 第三节 滚动轴承内部载荷分布及失效分析
滚动轴承的失效形式及预防措施

5 4一
石 油 与 化 工设 备 2 1 年第1 卷 00 3
滚 动轴承 的失效形式及预 防措 施
侯 国安 ห้องสมุดไป่ตู้崔 艳 宏
( 银川科技 职业学院, 宁夏 银川 7 01 5 5 0)
[ 摘 要]轴承 失效可分为止转失效和精度丧 失两种 。其损 伤机理 大致可分为:接 触疲劳失效、摩擦磨损失效、断裂失效 、 变形失效 、腐蚀 失效和 游隙变化失效等几种基本形 式。文章对预防轴承早期 失效 ,提 出了应采取 的措施 。
1 . 损 失效 2磨
指 表 面 之 间 的相 对 滑 动 摩 擦 导致 其 工 作 表 面 金 属 不 断磨 损 而 产 生 失效 。持 续 的 磨损 将 引 起轴 承 零件 逐 渐 损 坏 ,并 最终 导 致 轴 承 尺寸 精 度 丧 失 及 其 他 相关 问题 。磨 损会 影 响到 形 状变 化 ,配 合 间隙 增 大及 工 作 表 面 形貌 变 化 ,影 响 到润 滑 剂 或 使 其 污 染达 到 一定 程度 造 成 润 滑 功 能完 全 丧 失 , 最 终 使轴 承 丧 失 旋 转精 度 乃 至 不 能 正 常运 转 。磨 损 失效是各 类轴 承常 见 的失效形 式之一 。
在 外 力 和 环 境 温 度 作 用 下 , 轴 承 零 件 表 面 局 部 塑性 流 动 或 整 体变 形 ,导 致 整套 轴 承 不 能 正 常 工 作 而造 成 的失 效称 为变 形 失 效 。如 保 持 架 翘
作 者 简 介 :侯 国安 (9 5 ) ,男,宁夏中卫人 ,北 京化 工大 1 7一
滚 动 轴 承 是 机 械 转 动 和 传 递 运 动 的 重 要 零 件 ,通 常 由外 套 、 内套 、滚 动 体f 球 、滚 柱 、滚 钢 针) 保 持架 等 组成 。滚动 轴 承 的服 役特 点足 受力 和 集 中,高 载荷 ( 轴承 接触 应 力 可达4 0 MP ,滚 球 90 a 柱轴 承达2 4 MP ) 9 0 a,高速 度f 速度 因数 d 高达 1 值 . 5 0mm・ /mi) 交 变 应 力作 用 。主 要 失效 形 ×1 。 r n ̄ 式 是 疲 劳 、磨 损 。 以下 为滚 动 轴 承 失 效 的基 本 形 式和 常见 失效形 式 、对策及 预 防措施 。
铁路货车滚动轴承常见故障分析及外检判定方法的探讨
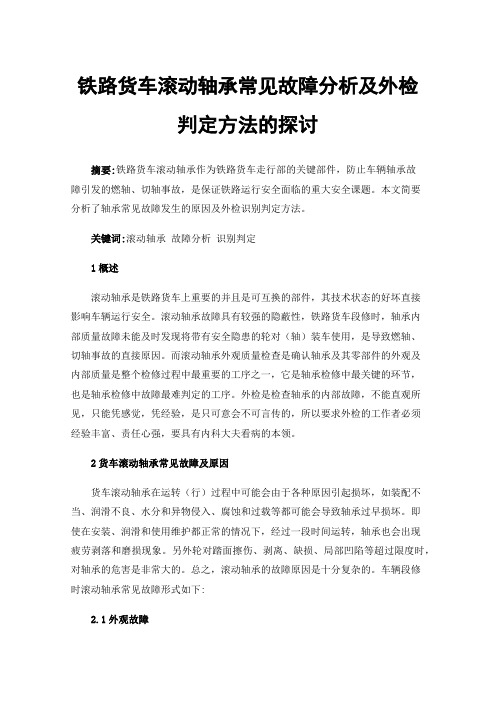
铁路货车滚动轴承常见故障分析及外检判定方法的探讨摘要:铁路货车滚动轴承作为铁路货车走行部的关键部件,防止车辆轴承故障引发的燃轴、切轴事故,是保证铁路运行安全面临的重大安全课题。
本文简要分析了轴承常见故障发生的原因及外检识别判定方法。
关键词:滚动轴承故障分析识别判定1概述滚动轴承是铁路货车上重要的并且是可互换的部件,其技术状态的好坏直接影响车辆运行安全。
滚动轴承故障具有较强的隐蔽性,铁路货车段修时,轴承内部质量故障未能及时发现将带有安全隐患的轮对(轴)装车使用,是导致燃轴、切轴事故的直接原因。
而滚动轴承外观质量检查是确认轴承及其零部件的外观及内部质量是整个检修过程中最重要的工序之一,它是轴承检修中最关键的环节,也是轴承检修中故障最难判定的工序。
外检是检查轴承的内部故障,不能直观所见,只能凭感觉,凭经验,是只可意会不可言传的,所以要求外检的工作者必须经验丰富、责任心强,要具有内科大夫看病的本领。
2货车滚动轴承常见故障及原因货车滚动轴承在运转(行)过程中可能会由于各种原因引起损坏,如装配不当、润滑不良、水分和异物侵入、腐蚀和过载等都可能会导致轴承过早损坏。
即使在安装、润滑和使用维护都正常的情况下,经过一段时间运转,轴承也会出现疲劳剥落和磨损现象。
另外轮对踏面擦伤、剥离、缺损、局部凹陷等超过限度时,对轴承的危害是非常大的。
总之,滚动轴承的故障原因是十分复杂的。
车辆段修时滚动轴承常见故障形式如下:2.1外观故障2.1.1前盖、后档(挡)、外圈有裂纹、碰伤、松动、变形或其他异状。
轴承在运用中受到非正常的外力作用造成的,如由于车辆脱线造成轴承外圈裂损、前盖、后档(挡)碰伤、车辆行走(走行)时带起的飞石或其它外力造成轴承外圈裂损。
另外轴承在检修过程中操作不当也会造成轴承故障缺陷,如磕碰伤、划伤、拉伤等。
2.1.2密封罩、密封组成裂纹、碰伤、松动、变形。
密封罩、密封组成裂纹、碰伤、变形主要是外力所致,而密封罩松动是密封装置最常见也是危害最大的,其主要原因是轴承一般检修或大修时,外圈牙口与密封罩配合过(过盈量)小,密封罩在车辆运行中受到离心力及转动力矩作用,导致密封罩中的密封圈与密封座摩擦加剧从而带动密封罩一起转动,使得密封罩松动脱出,过盈量过大在密封罩组装过程中容易破坏甚至切掉凸台,而且会使密封罩受力产生变形,在受到振动或冲击力时容易瞬间脱出。
航空发动机主轴轴承失效模式分析

航空发动机主轴轴承失效模式分析摘要:经济的发展推动了航空业的发展,但与此同时,我国航空发动机出现的故障中,轴承失效导致的事故在不断增加。
但当前对轴承失效的分析工作,常常以某一套飞行事故发动机轴承的失效研究为主,而因其他原因造成的航空发动机滚动轴承的早期失效模式,受条件制约,未进行系统分类和深一步的研究。
航空发动机主轴轴承的主要损伤模式为剥落、微粒损伤、压延印痕、夹杂物损伤、打滑蹭伤、磨损、接触腐蚀、断裂和变色。
这些失效模式分类对于滚动轴承的设计、制造工作具有一定的指导意义,但分类后的失效模式缺乏相关失效案例和实验数据,实际现场中此类失效模式可能不太适用,因此采用多种实验手段对轴承失效模式分析就显得极为重要。
关键词:航空发动机;主轴轴承;失效模式引言航空发动机主轴钢质轴承的主要失效模式包括疲劳失效,磨损失效,过热,塑性变形以及蹭伤等。
航空发动机圆柱滚子轴承常规失效模式主要为滚子轻载打滑及保持架断裂等。
而某航空发动机主轴圆柱滚子轴承出现有异于常规失效模式的滚子端面严重磨损的非典型失效模式。
目前对航空发动机主轴圆柱滚子轴承失效机理分析一般都采用定性分析,很少从轴承动力学特性进行失效机理定量分析。
1圆柱滚子轴承非典型失效表征圆柱滚子轴承非典型失效表征主要体现在以下方面:某航空发动机主轴圆柱滚子轴承使用过程中出现的失效模式表现为滚子的端面与工作表面严重磨损,内圈的挡边与滚道表面和保持架的兜孔横梁存在严重的磨损变色。
经初步分析,滚子倒角在磨削加工中产生的动不平衡量较大以及内圈挡边轴向游隙超差导致滚子歪斜过大是引起该轴承失效的主要原因。
本文从圆柱滚子轴承动力学特性理论方面加以研究此失效机理。
2航空发动机主轴轴承失效模式分析明确各种失效模式间的转变,首先就要确定各种失效模式各自的具体表现形式,失效机理及描述轴承运转状态的参数。
(1)疲劳失效。
表现形式及失效机理:疲劳失效主要分为次表面初始疲劳和表面疲劳。
疲劳失效常表现为滚动体或滚道接触表面上由最初的不规则的剥落坑逐渐延伸,直至发展为大片剥落。
发动机连杆滚针轴承失效分析及产品改进

THANKS
谢谢您的观看
工艺改进
总结词
优化轴承的加工和装配工艺
详细描述
改进轴承的加工工艺,提高加工精度和表面质量,降低表面粗糙度,从而减少摩擦和磨损。优化轴承 的装配工艺,确保轴承的预紧力和间隙调整达到最佳状态,提高轴承的工作稳定性和寿命。
设计改进
总结词
优化轴承的结构设计
VS
详细描述
根据实际工况和使用要求,对轴承的结构 进行优化设计。例如,改进轴承的滚针排 列方式、优化轴承的接触角和接触点等, 以提高轴承的承载能力和稳定性。同时, 考虑轴承的散热性能和润滑性能,以减少 热量积聚和摩擦磨损。
改进后的连杆滚针轴承可以提高发动机的性能和使用寿命,降低机械故障率, 提高生产效率和经济效益。同时,可以为相关行业提供技术支持和参考,推动 行业的技术进步和发展。
02
发动机连杆滚针轴承工作原理 及失效形式
发动机连杆滚针轴承工作原理
发动机连杆滚针轴承是一种滚动轴承 ,由内圈、外圈、滚针和保持架组成 。在工作时,滚针在内外圈之间滚动 ,传递扭矩和承受载荷。
发动机连杆滚针轴承失效分 析及产品改进
汇报人: 2023-12-27
目录
• 引言 • 发动机连杆滚针轴承工作原理
及失效形式 • 发动机连杆滚针轴承失效案例
分析 • 产品改进方案 • 改进后产品性能验证 • 结论与展望
01
引言
研究背景
发动机是机械设备中的重要组成部分,其性能直接影响机械 的整体性能。连杆滚针轴承是发动机中的关键部件,其失效 会导致发动机运转不平稳、振动和噪音等问题,严重影响发 动机的性能和使用寿命。
轴承产品缺陷分析报告

轴承产品缺陷分析报告滚动轴承和滑动轴承是应用在转动设备中应用最为广泛的机械零件,是轴及其它旋转构件的重要支承。
在日常的使用与维修中发现,轴承同时也是最容易产生故障的零件,对轴承零件的缺陷预测与分析具有很高的经济价值,所以轴承工作状态实时监控和诊断的研究受到广泛重视。
由于滚动轴承与滑动轴承在缺陷方面有许多共同点,缺陷分析方法可以通用,所以本文以讨论滚动轴承作为重点。
1.滚动轴承常见缺陷故障由于滚动轴承在实际生产中应用广泛,其产生的故障现象也多种多样,常见的有疲劳剥落、过量的永久变形和磨损。
1.疲劳剥落轴承在正常的条件下使用,内圈、外圈和滚动体上的接触应力是变化的,工作一段时间后,接触表面就可能发生疲劳点蚀,以致造成疲劳剥落。
所以疲劳剥落是轴承的正常失效形式,它决定了轴承的工作寿命。
2.过量的永久变形轴承在转速很低或者间歇往复摆动的工作状态时,在过大的静载荷或冲击载荷作用下,会使套圈滚道和滚动体接触处的局部应力超过材料的屈服强度,以致在表面发生过大的塑性变形,使轴承不能正常工作3.磨损在润滑不良和密封不严的情况下,轴承工作接触面容易发生磨损,转速越高,磨损越严重。
磨损会使轴承的游隙增加,振动和噪声增大,各项技术性能急剧下降,导致轴承失效。
此外,轴承还有胶合、烧伤、轴圈断裂、滚动体压碎、保持架磨损和断裂、锈蚀等失效形式。
在正常的使用条件下,这些失效是可以避免的,因此称为非正常失效。
2.轴承缺陷诊断方法轴承缺陷常用诊断分析方法可概括为以下几种:(1)检测润滑油温度、轴承温度及主油道润滑油压力波等物理参数(2)油样分析包括理化分析、污染度测试、发射光谱分析、红外线分析和铁谱分析(3)振动分析(4)声发射(AE)分析以上各种方法各有其特点,能够在一定程度上反应轴承缺陷。
第一种方法安装传感器简单、成本低但不实用,主要原因是测量温度有其滞后性,不能实时预测轴承缺陷。
油样分析只能测量油润滑轴承,但不能测量脂润滑轴承。
- 1、下载文档前请自行甄别文档内容的完整性,平台不提供额外的编辑、内容补充、找答案等附加服务。
- 2、"仅部分预览"的文档,不可在线预览部分如存在完整性等问题,可反馈申请退款(可完整预览的文档不适用该条件!)。
- 3、如文档侵犯您的权益,请联系客服反馈,我们会尽快为您处理(人工客服工作时间:9:00-18:30)。
滚动轴承常见的失效形式及原因分析+浪逐风尖 2008-11-05 10:55
滚动轴承在使用过程中,由于很多原因造成其性能指标达不到使用要求时就产生
了失效或损坏.常见的失效形式有疲劳剥落、磨损、塑性变形、腐蚀、烧伤、电腐蚀、保持架损坏等。
一,疲劳剥落 疲劳有许多类型,对于滚动轴承来说主要是指接触疲劳。滚动轴承套圈各滚动体表面在接触应力的反复作用下,其滚动表面金属从金属基体呈点状或片状剥落下来的现象称为疲劳剥落。点蚀也是由于材料疲劳引起一种疲劳现象,但形状尺寸很小,点蚀扩展后将形成疲劳剥落。
疲劳剥落的形态特征一般具有一定的深度和面积,使滚动表面呈凹凸不平的鳞状,有尖锐的沟角.通常呈显疲劳扩展特征的海滩装纹路.产生部位主要出现在套圈和滚动体的滚动表面.
轴承疲劳失效的机理很复杂,也出现了多种分析理论,如最大静态剪应力理论、最大动态剪应力理论、切向力理论、表面微小裂纹理论、油膜剥落理论、沟道表面弯曲理论、热应力理论等。这些理论中没有一个理论能够全面解释疲劳的各种现象,只能对其中的部分现象作出解释。目前对疲劳失效机理比较统一的观点有:
1、次表面起源型 次表面起源型认为轴承在滚动接触部位形成油膜的条件下运转时,滚动表面是以内部(次表面)为起源产生的疲劳剥落。 2、表面起源型 表面起源型认为轴承在滚动接触部位未形成油膜或在边界润滑状态下运转时,滚动表面是以表面为起源产生的疲劳剥落。
3、工程模型 工程模型认为在一般工作条件下,轴承的疲劳是次表面起源型和表面起源型共同作用的结果。
疲劳产生的原因错综复杂,影响因素也很多,有与轴承制造有关的因素,如产品设计、材料选用、制造工艺和制造质量等;也有与轴承使用有关的因素,如轴承选型、安装、配合、润滑、密封、维护等。具体因素如下:
A、制造因素 1、产品结构设计的影响 产品的结构设计是根据使用性能目标值来确定的,这些目标值如载荷容量、寿命、精度、可靠性、振动、磨损、摩擦力矩等。在设计时,由于各种原因,会造成产品设计与使用的不适用或脱节,甚至偏离了目标值,这种情况很容易造成产品的早期失效。
2、材料品质的影响 轴承工作时,零件滚动表面承受周期性交变载荷或冲击载荷。由于零件之间的接触面积很小,因此,会产生极高的接触应力。在接触应力反复作用下,零件工作表面将产生接触疲劳而导致金属剥落。
就材料本身的品质来讲,其表面缺陷有裂纹、表面夹渣、折叠、结疤、氧化皮和毛刺等,内部缺陷有严重偏析和疏松、显微孔隙、缩孔、气泡、白点、过烧等,这些缺陷都是造成轴承早期疲劳剥落的主要原因。
在材料品质中,另一个主要影响轴承疲劳性能的因素是材料的纯洁度,其具体表现为钢中含氧量的多少及夹杂物的数量多少、大小和分布上。
3、热处理质量的影响 轴承热处理包括正火、退火、渗碳、淬火、回火、附加回火等。其质量直接关系到后续的加工质量及产品的使用性能。
4、加工质量的影响 首先是钢材金属流线的影响。钢材在轧制或锻造过程中,其晶粒沿主变形方向被拉长,形成了所谓的钢材流线(纤维)组织。试验表明,该流线方向平行于套圈工作表面的与垂直的相比,其疲劳寿命可相差2。5倍。其次是磨削变质层。磨削变质层对轴承的疲劳寿命与磨损寿命有很大的影响。变质层的产生使材料表面层的组织结构和应力分布发生变化,导致表面层的硬度下降、烧伤,甚至微裂纹,从而对轴承疲劳寿命产生影响。
受冷热加工条件及质量控制的影响,产品在加工过程中会出现质量不稳定或加工误差,如热加工的材料淬、回火组织达不到工艺要求、硬度不均匀和降低,冷加工的几何精度超差、工作表面的烧伤、机械伤、锈蚀、清洁底低等,会造成轴承零件接触不良、应力集中或承载能力下降,从而对轴承疲劳寿命产生不同程度的影响。
B、使用因素 使用因素主要包括轴承选型、安装、配合、润滑、密封、维护等。 不正确的安装方法很容易造成成轴承损坏或零件局部受力产生应力集中,引起疲劳。过大的配合过盈量容易造成内圈滚道面张力增加及零件抗疲劳能力下降,甚至出现断裂。
润滑不良会引起不正常的摩擦磨损,并产生大量的热量,影响材料组织和润滑剂性能。如果润滑不当,即便选用再好的材料制造,加工精度再高,也起不到提高轴承寿命的效果。
密封不良容易使杂质进入轴承内部,既影响零件之间的正常接触形成疲劳源,又影响润滑或污染润滑剂。
根据疲劳产生的机理和主要影响因素,可以有针对性地提出预防措施。如对表面起源损伤引起的疲劳,可以通过对零件表面进行表面强化处理,对次表面起源型疲劳可以通过改善材料品质等措施。而提高零件加工质量尤其是零件表面质量、提高使用质量、控制杂质流入轴承内部、保证润滑质量等措施对预防和延缓疲劳都有十分重要的意义。 二、表面塑性变形 表面塑性变形主要是指零件表面由于压力作用形成的机械损伤。在接触表面上,当滑动速度比滚动速度小得多的时候会产生表面塑性变形。
表面塑性变形分为一般表面塑性变形和局部表面塑性变形两类。 A、一般表面塑性变形 是由于粗糙表面互相滚动和滑动,同时,使粗糙表面不断产生塑性碰撞所造成,其结果形成了冷轧表面,从外观上看,这种冷轧表面已被辗光,但是,如果辗光现象比较严重,在冷轧表面上容易形成大量浅裂纹,浅裂纹进一步发展可能(在粗糙表面区域区)导致显微剥落,但这种剥落很浅,只有几个微米,它能够覆盖很宽的接触表面.
根据弹性流体动压润滑理论,一般表面塑性变形产生的原因是由于两个粗糙表面直接接触,其间没有形成承载的弹性流体动压润滑膜.因此,当油膜润滑参数小于一定值时,将产生的一般表面塑性变形.一般油膜润滑参数值越小表面塑性变形越严重.
B、局部表面塑性变形 局部表面塑性变形是发生在摩擦表面的原有缺陷附近。最常见的原有缺陷,如压坑(痕)、磕碰伤、擦伤、划伤等。
1、压坑(痕) 压坑(痕)是由于在压力作用下硬质固体物侵入零件表面产生的凹坑(痕)现象。
压坑(痕)的形态特征是:形状和大小不一,有一定深度,压坑(痕)边缘有轻微凸起,边缘较光滑。
硬质固体特的来源是轴承零件在运转中产生的金属颗粒、密封不良造成轴承外部杂质侵入。
压坑(痕)产生的部位主要在零件的工作表面上。 预防压坑(痕)的措施主要有:提高零件的加工精度和轴承的清洁度、改善润滑、提高密封质量等。
2、磕碰伤 磕碰伤是由于两个硬质特体相互撞击形成的凹坑现象。 磕碰伤的形态特征视两物体形状和相互撞击力的不同其形状和大小不一,但有一定深度,在其边缘处常有突起。
磕碰伤主要是操作不当引起的。产生部位可以在零件的所有表面上。 预防磕碰伤的措施主要有:提高操作者的责任心、规范操作、改进产品容器的结构和增加零件的保护措施等。
3、擦伤 擦伤是两个相互接触的运动零件,在较大压力作用下因滑动摩擦产生的金属迁移现象。严重时可能伴随烧伤的出现。
擦伤的形状不确定,有一定长底和宽度,深度一般较浅,并沿滑动(或运动)方向由深而浅。
擦伤可以在产品制造过程中产生也可以在使用过程中产生。 轴承制造成过程中的擦伤预防措施与磕碰伤的预防措施相同。使用中的擦伤预防措施主要是从防止“打滑”方面考虑,改进产品内部结构、提高过盈配合量、调整游隙、改善润滑、保证良好接触状态等。
4、划(拉)伤 划(拉)伤是指硬质和尖锐物体在压力作用下侵入零件表面并产生相对移动后形成的痕迹。
划伤一般呈线型状,有一定深度,宽度比擦伤窄,划伤的伤痕方向是任意的,长度不定。产生部位主要在零件的工作表面和配合表面上。而拉伤只发生在轴承内径(过盈)配合面上,伤痕方向一般与轴线平行,有一定长度、宽度和深度,并成组出现。
划伤可以在轴承制造过程中产生也可在使用中产生。而拉伤只发生在轴承安装拆卸过程中。
预防轴承制造过程中的划伤与预防磕碰伤的措施相同。预防使用中划伤与预防压坑(痕)的措施基本相同。 预防拉伤的措施是严格安装拆卸规程、保证配合面的清洁、安装时在配合面上适当润滑等。
综上所述,预防表面塑性变形的措施是要正确选用轴承、增强材料的耐磨性,保证润滑的有效性、注意安装方法、提高轴承密封装置的密封性等。
三、磨损 在力的作用下,两个相互接触的金属表面相对运动产生摩擦,形成摩擦副。磨擦引起金属消耗或产生残余变形,使金属表面的形状、尺寸、组织或性能发生改变的现象称为磨损。
磨损过程包含有两物体的相互作用、黏着、擦伤、塑性变形、化学反应等几个阶段。其中物体相互作用的程度对磨损的产生和发展起着重要的作用。
磨损的基本形工有:疲劳磨损、黏着磨损、磨料(粒)磨损、微动磨损和腐蚀磨损等。
产生磨损的主要原因: A、异物通过了密封不良的装置(或密封圈)进入了轴承内部。 B、润滑不当。如润滑油中的杂质未过滤干净、润滑方式不良、润滑剂选用不当、润滑剂变质等。 C、零件接触面上的材料颗粒脱离, D、锈蚀。如,由于轴承使用温度变化产生的冷凝水、润滑剂中添加剂的腐蚀性特质等原因形成的锈蚀。
实际中多数磨损属于综合性磨损,预防对策应根据磨损的形式和机理分别采取措施。
对于微动磨损,可以采用小游隙或过盈配合来减少使用过程中的微动磨损;可在套圈与滚动体之间采用稀润滑剂润滑或分别包装来减少运输过程的微动磨损;另外,轴承应放在无振动环境下保管,或将轴承内外圈隔离存放可以防止保管过程中产生的微动磨损。
对于黏着磨损可以采取提高加工精度、增强润滑效果等措施来解决。 对于磨料(粒)磨损,可以采用表面强化处理、表面润滑处理(如渗硫、磷化、表面软金属膜涂层等)、改善轴承密封结构、提高零件加工精度、保证润滑油过滤质量、减少制造和使用过程中对表面的损伤等方法来解决。
对于腐蚀磨损,应减少轴承使用环境中腐蚀物质的侵入、对零件表面进行耐腐蚀处理或采用耐腐蚀材料制造产品等手段来解决。另外,还可以从产品结构设计和制造的角度进行改进,如提高零件的加工精度、减少磨削加工中产生的变质层、保证弹性流体动压润滑膜等实现预防磨损的目的。
四、腐蚀