轮对轴承跑合试验台技术部分
BTS200轴承寿命预测性试验台技术参数
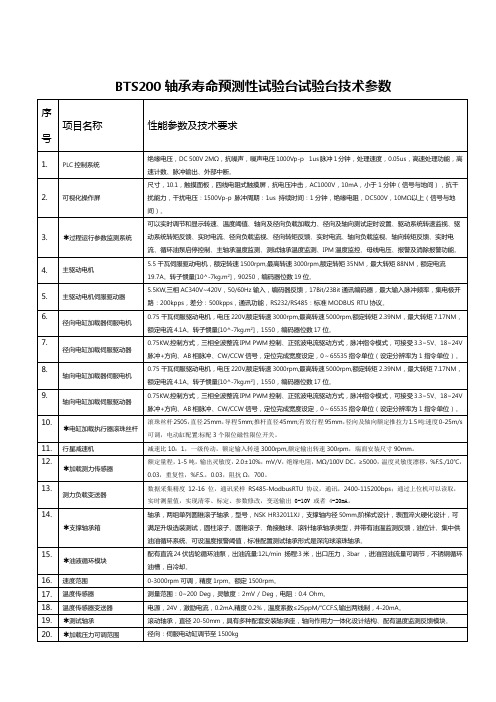
✱电缸加载执行器滚珠丝杆
滚珠丝杆2505,直径25mm,导程5mm;推杆直径45mm;有效行程95mm,径向及轴向额定推拉力1.5吨:速度0-25m/s可调,电动缸配置:标配3个限位磁性限位开关。
11.
行星减速机
减速比10:1,一级传动,额定输入转速3000rpm,额定输出转速300rpm,端面安装尺寸90mm。
6.
径向电缸加载伺服驱动器
1个
0.75KW,控制方式,三相全波整流IPM PWM控制
7.
轴向电缸加载器伺服电机
1个
0.75千瓦伺服驱动电机,电压220V,额定转速3000rpm,最高转速5000rpm。
8.
轴向电缸加载伺服驱动器
1个
0.75KW,控制方式,三相全波整流IPM PWM控制
9.
电缸加载执行器滚珠丝杆
6.
径向电缸加载器伺服电机
0.75千瓦伺服驱动电机,电压220V,额定转速3000rpm,最高转速5000rpm,额定转矩2.39NM,最大转矩7.17NM,额定电流4.1A。转子惯量[10^-7kg.m2],1550,编码器位数17位。
7.
径向电缸加载伺服驱动器
0.75KW,控制方式,三相全波整流IPM PWM控制、正弦波电流驱动方式,脉冲指令模式,可接受3.3~5V、18~24V脉冲+方向、AB相脉冲、CW/CCW信号,定位完成宽度设定,0~65535指令单位(设定分辨率为1指令单位)。
4.
主驱动电机
5.5千瓦伺服驱动电机,额定转速1500rpm,最高转速3000rpm,额定转矩35NM,最大转矩88NM,额定电流19.7A。转子惯量[10^-7kg.m2],90250,编码器位数19位。
巴西1A线轮对跑合试验台的设计计算与结构分析
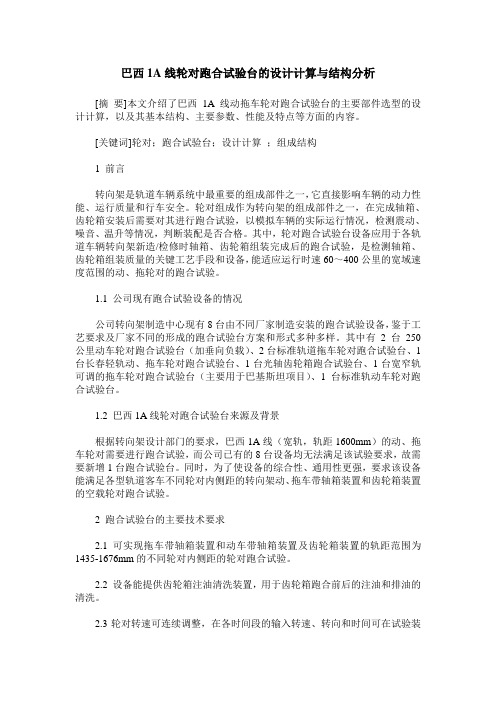
巴西1A线轮对跑合试验台的设计计算与结构分析[摘要]本文介绍了巴西1A线动拖车轮对跑合试验台的主要部件选型的设计计算,以及其基本结构、主要参数、性能及特点等方面的内容。
[关键词]轮对;跑合试验台;设计计算;组成结构1 前言转向架是轨道车辆系统中最重要的组成部件之一,它直接影响车辆的动力性能、运行质量和行车安全。
轮对组成作为转向架的组成部件之一,在完成轴箱、齿轮箱安装后需要对其进行跑合试验,以模拟车辆的实际运行情况,检测震动、噪音、温升等情况,判断装配是否合格。
其中,轮对跑合试验台设备应用于各轨道车辆转向架新造/检修时轴箱、齿轮箱组装完成后的跑合试验,是检测轴箱、齿轮箱组装质量的关键工艺手段和设备,能适应运行时速60~400公里的宽域速度范围的动、拖轮对的跑合试验。
1.1 公司现有跑合试验设备的情况公司转向架制造中心现有8台由不同厂家制造安装的跑合试验设备,鉴于工艺要求及厂家不同的形成的跑合试验台方案和形式多种多样。
其中有2台250公里动车轮对跑合试验台(加垂向负载)、2台标准轨道拖车轮对跑合试验台、1台长春轻轨动、拖车轮对跑合试验台、1台光轴齿轮箱跑合试验台、1台宽窄轨可调的拖车轮对跑合试验台(主要用于巴基斯坦项目)、1台标准轨动车轮对跑合试验台。
1.2 巴西1A线轮对跑合试验台来源及背景根据转向架设计部门的要求,巴西1A线(宽轨,轨距1600mm)的动、拖车轮对需要进行跑合试验,而公司已有的8台设备均无法满足该试验要求,故需要新增1台跑合试验台。
同时,为了使设备的综合性、通用性更强,要求该设备能满足各型轨道客车不同轮对内侧距的转向架动、拖车带轴箱装置和齿轮箱装置的空载轮对跑合试验。
2 跑合试验台的主要技术要求2.1可实现拖车带轴箱装置和动车带轴箱装置及齿轮箱装置的轨距范围为1435-1676mm的不同轮对内侧距的轮对跑合试验。
2.2 设备能提供齿轮箱注油清洗装置,用于齿轮箱跑合前后的注油和排油的清洗。
轮对电机跑合试验台操作使用说明书
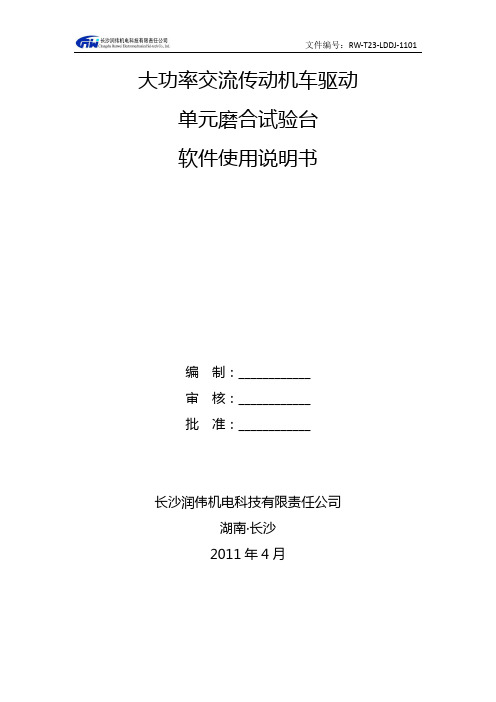
文件编号:RW-T23-LDDJ-1101大功率交流传动机车驱动单元磨合试验台软件使用说明书编制:____________审核:____________批准:____________长沙润伟机电科技有限责任公司湖南·长沙2011年4月[为保证安全使用]使用前请详细阅读本说明书,遵守注意事项,正确使用。
有关注意事项记载的说明警告用语警告用语的含义危险·如果不遵守,则有可能导致死亡或身受重伤的危险。
注意·如果不遵守则有可能受到中度或轻度伤害的注意事项。
·如果不遵守则有可能会使试验无法正常进行,或导致机器故障。
对产品的注意事项危险安装试验对象品时请注意安全。
以免碰伤人等。
注意试验结束取下轮对时必须确认速度已经停止,以免碰伤身体。
注意连接轮对时、请确认接口是否正常连接。
如果没被正常连接或固定,可能会在试验过程中,出现设备和人员的伤害事故。
注意本说明书没有记载的项目、请不要擅自修改设备的设定。
否则将导致正常的试验、操作将无法进行。
注意断开电源之前,应先关闭计算机,不然会破坏计算机里面存储的数据和资料,不能进行自动试验。
危险触摸配线及柜内电气部件时要确认电源开关在OFF状态。
可能会由此导致触电。
其他的注意事项注意试验设备为精密仪器,粗暴使用会造成设备故障,请充分注意。
注意清扫时请不要用水浇撒。
是造成电气机器故障的原因。
注意不要擅自修改移动本软件,不要擅自重装系统,导致数据丢失,后果自负。
计算机上不可擅自安装与本试验无关的应用软件,否则可能导致系统文件损坏,无法进行自动试验。
注意试验结束后,必须确认轮对已经停止磨合,才能去拆除电缆。
注意试验过程中请不要动面板上和电源柜上的相关按钮开关,否则影响试验。
注意必须先通过电源柜上的按钮选择自动试验(手动/自动)才能开始自动试验。
注意试验过程中出现异常情况,可以急停按钮停止试验,通过面板上的电源分按钮,切断试验台电源。
注意平时请不要随便乱动电源柜上的按钮和开关。
轮对跑合试验台温度检测系统硬件设计

10
鞍山师范学院学报
第 20卷
RS485二线制输出接口,具有+15kV的 ESD保护功能;(4)允许通过电流≤5mA. PT100温度传感器测量温度范围广,具有体积小、抗干扰能力强、精度高的特点.且 PT100温度传感
器价格低廉,操作简单,适合采用. 2.2.2 放大器的选择 本次设计中,使用了 A/D转换器,A/D转换器允许电压范围是 0~5V,因为 PT100温度传感器允许通过的电流有限制,PT100温度传感器两端电压变化很小,不易被 A/D转换器 识别,需要设计一个放大电路,将电压放大合适的倍数.运算放大器选择 AD620.AD620具有高精度(最 大非线性度 40ppm)、低失调电压(最大 50μV)和低失调漂移(最大 0.6μV/°C)特性,是电子秤和传感 器接口等精密数据采集系统的理想之选.它还具有低噪声、低输入偏置电流和低功耗特性. 2.2.3 A/D转换器的选择 PT100温度传感器输出量是模拟量,但显示器只能显示数字量,因此需 要将 PT100输出的模拟量转换成数字量.只有这样 PT100温度传感器测出的温度才能正常在显示器上 显示.
JournalofAnshanNormalUniversity
鞍山师范学院学报
201808,20(4):9-12
轮对跑合试验台温度检测系统硬件设计
邓玉萍1,孔祥瑞2
(1.鞍山师范学院 物理科学与技术学院,辽宁 鞍山 114007;2.燕山大学 电气工程学院,河北 秦皇岛 066004)
轮对跑合试验台是模拟轮对实际运转情况的专用试验台,能够对装车前的机车、轻轨、地铁轮对进 行跑合,即在不同转速和不同旋转方向时,通过检测牵引传动齿轮箱的温度变化以及齿轮箱油温的变化 来分析判断齿轮箱各部件的适配状态和性能.从而防止因轴承生产及组装质量问题而引发的轮对运行 早期的热轴、燃轴事故,进一步完善了对轴承生产及组装质量的检测,对于城轨车辆的安全运行有着重 要的意义[1].
轮对轴承跑合试验台技术部分

1技术条件1.1 适用范围主要适用于主要应用于轨道车辆转向架制造、检修时轮对轴承组装完成后的轮对轴承跑合试验,是检查轮对轴承组装质量的主要工艺手段和设备。
本试验台为具有轮对轴承正反转跑合、轮对轴承温升监控等功能的综合试验台。
1.2 适用环境环境温度:-20℃~+55℃海拔高度:≤2000m相对湿度:≤80%使用电源:AC380V±10%,50Hz1.3 设备的基本要求1.3.1 设备的总体要求1.3.1.1 该设备可应用于轮对滚动轴承跑合作业。
1.3.1.2 该设备为离线停留式1.3.1.3 该设备关键部件材质均采用国内外业界著名厂商生产的合格产品,性能指标都达到或者超过相关标准的要求。
1.3.1.4 该设备具备的功能:●能对轮对轴承进行跑合试验。
●可输入轮对轴号。
●有软起动、变速、制动功能。
●摩擦压力、制动力可调。
●跑合作业时间可调。
●每端两点远红外测温。
●超温报警。
●转速可测。
●计算机显示屏显示检测数据并存储,可随时输出。
●能自动判别跑合是否合格。
●基础数据长期存储和恢复功能。
●遇见紧急情况时设备具有急停功能。
1.3.1.5 该设备是完整的、全新的,并且具有合理的结构、高的稳定性、可靠性和耐久性,具有足够的刚度和强度,程序简单易懂,操作、维修方便。
1.3.1.6 该设备设有安全保护联锁装置和短路、断路及漏电保护装置,停电或意外停机时的保护装置。
具有完善、可靠的联锁、安全保护和故障报警等功能。
1.3.1.7 该设备的零部件选用优质材料制造,所选用的机械、液压、电气元器件和控制系统是先进的、优质的、可靠的系列产品。
1.3.1.8 提供该设备必要的易耗品和备件,所需数量应满足两年的正常使用。
1.3.2 选用材料的技术要求该设备及工装的零部件所用材料的牌号符合图纸所规定的牌号,符合GB1591-88、GB699-88、GB700-88之规定,进厂原材料有质量合格证件,属国家大型钢铁企业的产品。
交直流轮对电机跑合试验台控制系统设计

交直流轮对电机跑合试验台控制系统设计张春红【摘要】轮对电机组装完成之后,为了检查齿轮箱、电机轴承、轮对轴承等是否符合安装要求,需要对轮对进行跑合试验.从数据采集、交直流传动和智能测控这三个方面进行跑合试验台控制系统的设计.数据采集系统设计采用传感器采集电机跑合过程中的振动、温度、转速等信号.交直流传动设计是为了满足交直流机车电机传动的需求.智能测控设计采用工控机作为控制终端,用MCGS组态软件和485通讯实现试验过程数据自动采集等功能.该试验装置具备手动和自动两种功能,具有自动化程度高、控制精度高等优点.【期刊名称】《电气传动自动化》【年(卷),期】2014(036)002【总页数】4页(P30-33)【关键词】跑合;数据采集;交直流传动;MCGS【作者】张春红【作者单位】江苏联合职业技术学院常州铁道分院,江苏常州213011【正文语种】中文【中图分类】TM8351 概述轮对是车辆行走的重要部件。
轮对电机总成作为机车转向架上最重要的组成部分,由车轴、轮对、牵引电机、齿轮箱、轴承等组成。
其性能直接决定了机车以及机车后方运行列车的安全。
在转向架总组装之前要对机车轮对电机总成进行跑合试验,跑合试验有以下功能:①轴箱匀脂;②齿轮箱齿轮磨合;③测试牵引电机轴承温升值、振动值;④测试轮对轴承温升值、振动值;⑤测试齿轮箱温升值、振动值;⑥测试轮对实时转速;通过以上参数的采集测量,判断机车轮对内部齿轮以及轴承的安装是否正常,是否符合安装要求。
2 系统总体设计思路试验台设计考虑到效率问题,将台位设计为三工位,可以进行单轴试验,也可同时三轴试验。
系统框图如图1所示。
三相交流电源经变频器和直流驱动器后,输出的电压驱动轮对电机旋转。
轮对跑合过程中,采用工控机作为输入、输出控制和数据处理的核心单元。
工控机采集的输入信号有转速信号(每轴1路))、振动信号((每轴6路))、温度信号(每轴6路)。
同时工控机输出模拟量调节信号,控制电机自动调速功能。
MS-KLM02轮对磨合试验台技术方案Z

KLM02轮对磨合试验台技术方案一、简介MS-KLM02轮对磨合试验台(以下简称试验台)是我公司专为铁路客车轮对检测而设计开发的试验设备。
试验台模拟轮对实际运转情况,能够对装车前的轮对进行磨合,检查轴承的生产和组装质量,对铁道车辆安全有着重要意义。
试验台采用先进的PLC技术、变频器技术和工控机技术,从而极大地提高了控制精度和工作稳定性,简化了操作程序,并可实现监控测量参数,是一种高性价比的轮对检测设备,可广泛应用于车辆段和机车车辆工厂。
二、安全注意事项试验台只可在规定的范围内使用。
请注意在试验时还要超出所有的额定值和标称值。
配电柜内有危险电压,非专业人员不要在通电状态下打开配电柜的后门和侧门,否则会导致电击或保护失效。
操作人员和维修人员应在确认系统无输出断电的情况下才能更换和连接线路。
未经培训的人员禁止操作试验台。
保持试验场地干净整洁。
系统接地(零)。
三、工作环境和使用条件海拔不超过1500米。
相对湿度在于20℃时不超过90%,在40℃时不超过80%。
试验台应远离电磁干扰,避免腐蚀性气体侵蚀。
试验温度在通常情况0-80℃。
电压波动不大于10%。
供电频率在某种程度上50±1Hz范围内。
四、工作原理和用途试验台模拟列车的实际运行工况,轮对在不同转速和压力下进行磨合,使润滑脂涂布均匀。
检测轴承温升以检验轴承的生产和组装质量,从而防止因轴承生产和组装质量问题引发轮对早期的热轴、燃轴事故,进一步完善轴承生产及组装质量的检测,以确保铁道车辆安全。
试验台可用于Φ840-Φ930的轮对检查试验。
五、主要特点采用PLC技术,控制精确,工作可靠、维修方便。
采用变频器技术,调速范围广,可正反转。
采用工控机可实时显示测试参数,轴承运转温升的变化,并可保存历史数据、打印测试报告。
液压加载,加载力大小可以单独调节。
采用高精度红外线传感器,测量误差小:转速、压力误差小于±0.5%,温度误差小于±0.5℃。
铁路工程车轮对跑合试验台设计

摘 要:针对目前铁路工程车轮对跑合试验台安装测试困难,部分转速达不到工艺测试要求,需要人 工进行数据采集等多方面问题,提出一种铁路工程车轮对跑合试验台新设计方案。详细论述轮对跑合试验 台的设计要求、机械系统及支撑方式、电气系统等。新设计的轮对跑合试验台能够满足当前宝鸡中车时代 工程机械有限公司所有铁路工程车轮对跑合试验,测试轮对在不同转速时产生的噪音,记录轴箱及齿轮箱 表面温度,实现数据自动采集。
efficiency. Keywords:Rail Construction & Maintenance Vehicle;Wheelset Running-in Test Bench;Design Scheme
0 引言
为了检验组装完成后的工程车轮对轴承、齿轮 箱的噪音和温升,在高速运转时,是否满足设计和 工艺要求,设计工程车轮对自动跑合试验台 (以 下简称“ 试验台 ”)。要求试验台能够自动测量并记 录轮对在不同运行速度条件下的噪音、温升、异响 等,并自动判断轮对中的运行部件 (如轴承) 是否 存在异常、齿轮啮合间隙是否到位以及轴封是否安装 到位等。生产车间能根据试验台的测试结果及时处 理,避免不合格轮对流入总装车间,甚至最终用户。
要求。 (4) 具有自动识别数据是否合格功能。 (5) 过载保护快速切断功能。
1.2 结构要求 (1) 试验台有良好的稳定性,以 0~160 km/h
的速度运转时能够保持轮对及工装平稳。 (2) 动力轴与光轴的轴端支撑方式应通用,
动力轴车轴齿轮箱由工装固定在平台上,要求稳定可 靠,拆卸方便,同种轮对更换拆卸时间小于 30 min。
软件评定原则应符合 ISO 9001:2015 《质量 管理体系 要求》。 1.5 参数
1 试验台设计要求
- 1、下载文档前请自行甄别文档内容的完整性,平台不提供额外的编辑、内容补充、找答案等附加服务。
- 2、"仅部分预览"的文档,不可在线预览部分如存在完整性等问题,可反馈申请退款(可完整预览的文档不适用该条件!)。
- 3、如文档侵犯您的权益,请联系客服反馈,我们会尽快为您处理(人工客服工作时间:9:00-18:30)。
1 技术条件1.1 适用范围主要适用于主要应用于轨道车辆转向架制造、检修时轮对轴承组装完成后的轮对轴承跑合试验,是检查轮对轴承组装质量的主要工艺手段和设备。
本试验台为具有轮对轴承正反转跑合、轮对轴承温升监控等功能的综合试验台。
1.2 适用环境环境温度:-20℃~+55℃海拔高度:≤2000m相对湿度:≤80%使用电源:AC380V±10%,50Hz1.3 设备的基本要求1.3.1 设备的总体要求1.3.1.1 该设备可应用于轮对滚动轴承跑合作业。
1.3.1.2 该设备为离线停留式1.3.1.3 该设备关键部件材质均采用国内外业界著名厂商生产的合格产品,性能指标都达到或者超过相关标准的要求。
1.3.1.4 该设备具备的功能:●能对轮对轴承进行跑合试验。
●可输入轮对轴号。
●有软起动、变速、制动功能。
●摩擦压力、制动力可调。
●跑合作业时间可调。
●每端两点远红外测温。
●超温报警。
●转速可测。
●计算机显示屏显示检测数据并存储,可随时输出。
●能自动判别跑合是否合格。
●基础数据长期存储和恢复功能。
●遇见紧急情况时设备具有急停功能。
1.3.1.5 该设备是完整的、全新的,并且具有合理的结构、高的稳定性、可靠性和耐久性,具有足够的刚度和强度,程序简单易懂,操作、维修方便。
1.3.1.6 该设备设有安全保护联锁装置和短路、断路及漏电保护装置,停电或意外停机时的保护装置。
具有完善、可靠的联锁、安全保护和故障报警等功能。
1.3.1.7 该设备的零部件选用优质材料制造,所选用的机械、液压、电气元器件和控制系统是先进的、优质的、可靠的系列产品。
1.3.1.8 提供该设备必要的易耗品和备件,所需数量应满足两年的正常使用。
1.3.2 选用材料的技术要求该设备及工装的零部件所用材料的牌号符合图纸所规定的牌号,符合GB1591-88、GB699-88、GB700-88之规定,进厂原材料有质量合格证件,属国家大型钢铁企业的产品。
1.3.3 结构件工艺要求1.3.3.1 焊接工艺机架焊接编制相应焊接工艺,选择先进合理的焊接方法、焊接材料及焊接工艺参数,确定焊接坡口等。
1.3.3.2 焊缝质量设备及工装上的焊缝质量按GB/T12469-90规定的第II级执行,所有焊缝均进行无损探1.3.4 零件的防腐要求1.3.4.1 涂装前进行抛丸除锈表面处理为了提高设备油漆质量,钢结构件在涂装前均抛丸除锈表面处理,达到Sa2.5级标准。
1.3.4.2 所有电气元件选用适合湿热、盐雾环境的产品。
1.3.4.3 设备及工装的金属构件除装配表面和电镀表面外,都进行除锈处理和油漆。
对于封闭结构的部件内部,在组装封闭前完成除锈处理和油漆。
1.3.5 设备的电气保护和安全保护1.3.5.1 设备的电气保护等级为IP54。
1.3.5.2 设备的主要安全防护措施该设备配备相应的机械、液压、电气等保护措施,严格执行GB/T15706《机械安全基本概念与设计通则》、GB16754《机械安全急停设计原则》、GB16855.1《机械安全控制系统有关安全部件》、GB/T4064-1983《电器设备安全设计导则》等国家有关安全设计的标准。
1.3.6 电气系统技术要求1.3.6.1 设备的电气系统的设计和制造要把安全运行放在重要的位置上,要有必要的防护措施,防止发生意外的触电事故和碰撞事故。
1.3.6.2 采用的电气元件和部件要充分保证系统的可靠性、稳定性、耐用性。
1.3.6.3 保证采用的电气元件和部件等产品的连续性,能长期保证备件的供应,并可在当地方便的购买。
1.3.6.4 设备的控制柜和元器件都要保留足够的检测和维修空间,并且可方便的搬运和安装,要方便维修、更换和拆卸部件。
1.3.6.5 电控箱防护等级不低于IP55,所有接线采用航空接插式简易连接,易于安装1.3.6.6 具备常规电气保护:过流、过压、欠压、短路、过热、接地、漏电等。
1.3.6.7 控制系统采用成熟品牌产品,实现对设备完整控制操作。
设置人机操作界面,操作者可按程序提示自动完成检测作业。
同时,应具有人控手动操作功能。
1.3.6.8 软件组成应具有设备故障自诊断、设备参数设置、数据管理、设备校准标定检测等基本功能。
1.3.7 表面油漆1.3.7.1 设备及工装表面要求采用高质量防锈漆,油漆寿命不小10年。
1.3.7.2 涂料供商要选用国内外知名品牌产品,涂层总厚度不小于80um。
1.3.7.3 设备所有的钢结构、机械设备及零部件都作防腐处理。
制造钢结构的板材和型材均经过抛丸予处理,管材除镀锌外,均经过化学方法或机械手工除锈。
1.3.7.4 钢结构经抛丸除锈处理表面达到GB8923-88或相应标准(SIS)的Sa2.5级。
1.3.7.5 涂料的类型与颜色:封闭金属结构件的内部涂环氧树脂底漆。
金属结构件外表面要涂底漆、中间漆和面漆,面漆及标记满足《运装管验2008(324号)》规定。
1.3.7.6 外购的机电设备的颜色与周围环境相协调,提交时不会有任何损坏。
1.3.7.7 所有金属结构和机械设备表面的涂装用高压无气喷气机喷涂。
每度漆喷涂前,实施预涂装。
金属结构涂装时,机械设备给予遮蔽保护;机械设备涂装时,金属结构应遮蔽保护。
1.3.7.8 涂装按涂料厂产品说明书要求进行,并按本技术书要求进行涂装检查,涂装前工况、涂装后质量、每道工序是由中标方检验并经招标方认可,方进行下道工序。
1.3.7.9 漆膜的外观检查为湿膜不得缩边、缩水、起泡、发白、失光,涂料流挂。
干膜不得有细微龟裂、剥膜等现象。
面漆应均匀,平整、色泽一致,不得有漏漆、流漆、开裂、针孔、脱层等缺陷。
1.3.7.10 漆膜性能检验,漆膜的干透性、粘附力参照GB9286-88规定的一级质量要求进行。
漆膜的厚度检验,每10m2不少于3处,厚度误差20%,中标方应向招标方提供涂装记录与涂装质量检验报告,经招标方审查认定合格后,确认涂装工作结束。
1.3.7.11 发运途中,所有金属表面都有防湿防潮保护。
1.3.8 信息系统1.3.8.1 具有和“轮对管理信息系统”进行数据联网交换的接口。
1.3.8.2 能提供与动车组信息管理系统的接口,通信协议,信息内容及格式符合铁道部《铁路动车段(所)信息系统设计规范》和《动车组管理信息系统自动化设备接口规范》有关规定。
1.4 设备的技术要求1.4.1 设备的组成该设备位于轮轴组装流水线的跑合工位。
设备主要由主机、气控部分.电控柜三大部分构成。
1.4.1.1 主机装有轮对升降装置,驱动装置,检测系统,制动装置。
驱动装置驱动车轮旋转;检测系统测轴承转速与温度,制动装置减少空转时间。
1.4.1.2 气源为气缸动作提供动力。
1.4.1.3 电控柜装有工业计算机控制机器运转并采集检测数据,记录、判别结果,输出结果。
1.4.2 主要技术参数电源: AC380V±10%,50Hz工作环境温度: -20~+55℃工作湿度: 80%RH以下磨合轮对转速:≥500转/分钟转/分。
适应轮径范围: 790—920mm,动车轮对轨距为: 1435mm—1676mm。
测温范围: -10—+100℃。
测温精度:±1.℃。
分辨率: 0.1℃整机总功率: 18KW.风源: 0.5~0.8MPa摩擦轮贴合压力:≤1Mpa噪音不高于85dB(A)主机尺寸:3000*2000*1300mm控制柜尺寸:1800*800*600mm设备外形(长x宽x高):3000 x2000x1300mm设备重量4.8t1.4.3 作业过程简述1.4.3.1 将轮对吊送至跑合工位。
1.4.3.2 升降机构托起轴承将轮对升至工作位。
1.4.3.3 驱动机构旋转带动轮对转动。
1.4.3.4 跑合过程中测温、测速,记入计算机。
1.4.3.5 跑合结束轮对复位,轮对吊送至指定工位。
1.5 投标书提供详细的设备整体方案设计和检修工艺文件,说明各设备的构成及功能,所列设备的性能、技术参数、数量作为最终设备验交的依据。
2 验收和交付使用2.1设备出厂前,应在供货商处进行预验收。
预验收时,中标方应提前书面通知招标方,招标方根据确认的标书中的标准到生产厂进行试验。
2.2在预验收通过之后, 中标方应该提供试验记录和试验结果供招标方确认,得到招标方签字确认后,设备才能发往用户安装地。
2.3中标方提供设备安装计划、方案和设备基础条件图,并负责设备安装(安装单位须具备相应设备安装资质)和系统测试工作。
在设备安装和系统测试期间, 招标方、设计、监理、施工单位派员全程参与。
2.4在设备安装调试结束前一周,中标方提出设备的最后验收测试申请,招标方组织专家和设计、监理、施工单位人员组成测试组对设备进行最后验收测试,最后的验收测试项目及方案由中标方根据行业标准提出,测试组审定,试验通过后参加单位在最后的验收证书上签认。
2.5设备的安装调试由中标方负责,设备运到招标方安装现场后,中标方根据招标方的通知,及时派专业人员到现场进行安装、调试。
2.6中标方设备安装调试、售后服务人员必须严格遵守国家有关安全生产的法律法规和《铁路工程施工安全技术规程》(TB10401.1-2003)等有关安全生产的规定。
中标方工作期间应穿戴防护用品并遵守招标方施工现场管理规定。
2.7中标方应对设备安装调试(含售后服务)人员办理人身伤害保险,进入工作现场前,需提交招标方相关证明文件。
2.8中标方设备安装调试人员须具备该设备相关工种相应从业资质。
3 技术支持3.1 本项目人员组成表:3.2 售后服务3.2.1 中标方自设备安装验收正式交接后至质量保证期结束,应无偿为招标方提供售后服务。
在设备寿命期内,中标方应提供技术支持、维修支持和以优惠价格提供备件。
3.2.2 中标方应挑选身体健康、技术熟练和能胜任工作的人员,成立售后服务小组,在收到设备发生故障信息的24小时内到达设备使用现场,快速解决设备出现的任何问题,最大限度地保证设备的正常使用。
3.2.3 中标方应配备足够数量的售后服务人员和准备充足的备品备件,以保证售后服务的质量。
3.2.4 售后服务人员在售后服务期间应对招标方技术、管理、操作人员详细讲解技术资料、进行必要的示范操作,并随时解答招标方人员提出的技术问题。
3.3 人员培训3.3.1 在设备出厂之前,中标方对用户进行培训,中标方应提供用于培训的详细资料。
a.培训地点:设备制造工厂b.培训人数: 4人/台c.培训时间: 7天(56小时)3.3.2 在设备安装后,中标方需要就设备的操作和维护对用户进行现场培训,中标方应提供用于培训的详细资料。
a.培训地点: 招标方的设备安装地点b.培训人数: 4人/台c.培训时间: 2天(16小时)3.4 技术资料3.4.1 技术联络中标方在方案图纸设计完后,招标方和设计院对图纸进行审查,方案通过后,方可进行施工设计。