磨削加工的特点简易版
2精密磨削加工

精密磨削机理
②磨粒的等高性
微刃是由砂轮的精 细修整形成的,分布在 砂轮表层的同一深度上 的微刃数量多,等高性 好(即细而多的切削刃具 有平坦的表面) 。 由于加工表面的残 留高度极小,因而形成 了小的表面粗糙度值。
磨粒的等高性
1 粘结剂 2 磨料 3 砂轮表面
精密磨削机理
③微刃的滑擦、挤压、抛光作用
多用球磨机,而涂敷多用类似印刷机的涂敷机,可获得质量
良好的砂带。
静电植砂法:利用静电作用将砂粒吸附在已涂胶的基底上。
能使砂粒尖端朝上,因此切削性能强,等高性好、加工质量好。
2. 2
精密磨削加工机理
精密磨削是指加工精度为l--0.1μm、表面粗糙度值R a 达到0.2--0.025μm的磨削加工方法,又称低粗糙值磨削。 它是用微小的多刃刀具削除细微切屑的一种加工方法。一般 是通过氧化铝和碳化硅砂轮来实现的。 一般用于机床主轴、轴承、液压滑阀、滚动导轨、量规 等的精密加工。
补充概念
粒度指磨料颗料的大小。粒度分磨粒与微粉两组。磨粒用 筛选法分类,它的粒度号以筛网上一英寸长度内的孔眼数来表 示。例如 60#粒度的的磨粒,说明能通过每英寸长有 60 个孔 眼的筛网,而不能通过每英寸 70 个孔眼的筛网。 微粉用显微测量法分类,它的粒度号以磨料的实际尺寸来 表示( W )。如W20表示微粉的实际尺寸为20μm。 粒度号 适用范围 粗磨、荒磨、切断钢 坯、打磨毛刺 粗磨、半精磨、精磨 粒度号 适用范围 精磨、超精磨、螺纹 磨、珩磨 精磨、精细磨、超精 磨、镜面磨
涂覆磨具
涂覆磨具是将磨料用粘结 剂均匀的涂覆在纸、布或其它 复合材料基底上的磨具,又称 为涂敷磨具。 常用的涂敷磨具是有砂纸、 砂带、砂布、砂盘和砂布套等。
内圆磨砂轮磨削加工特点分析及修整方法

内圆磨砂轮磨削加工特点分析及修整方法一、砂轮的磨削和磨损过程砂轮在使用过程中常常会出现磨损,影响磨削加工效果。
砂轮磨损一般分为磨耗磨损、破碎磨损和堵塞粘附。
针对砂轮的磨削和磨损过程,下文做了详细的分析。
1.磨削的过程磨粒形状和大小都是不规则的,在砂轮工作表面上是随机分布的。
磨粒的前刀面为空间曲面且形状不规则,磨粒的切削刃有几-几十个微米的圆角,经过修正磨粒上会出现微刃。
2.砂轮磨损过程分为三个阶段:第一阶段磨损主要是磨粒的破碎;第二阶段磨损主要是磨耗磨损;第三阶段磨损主要是结合剂破碎;砂轮磨损的具体表现形式也不尽相同。
磨削塑性材料时,形成带状切屑;磨削脆性材料时,形成挤裂切屑;在磨削过程中产生的高温作用下,切屑熔化可成为球状或灰烬形态二、CBN砂轮内圆磨砂轮的磨削误差分析及修整内圆磨削时,工件径向进给,砂轮轴向往复运动。
内圆磨削前的表面形状误差会复映到磨削后的工件表面上。
砂轮的磨损过程控制不理想、工艺系统刚性差,加工磨削参数大等因素都可能使磨削产生误差。
1. 砂轮直径小,为了保证磨削质量和效率,砂轮必须有足够的磨削线速度,这容易引起工艺系统的震动,另外砂轮直径小单位磨削量就大,砂轮易变钝,需要经常修整。
2. 砂轮轴为细长,刚度低,磨削中弹性变形量大,容易形成锥孔,导致磨削时间较长,磨削加工效率低。
3. 磨削接触面积大,砂轮内圆磨削接触弧长比外圆长,接触面积比外圆要大得多,所以产生的磨削热也多,切削液又不容易达到磨削区,所以工件的散热排屑条件都比较差。
修整砂轮的作用通常内圆磨削中在完成一个或几个工作循环后需要修整一次砂轮。
1.修整砂轮的形状,使之保持一定的直线度及圆度;2.去除砂轮钝化变质层,使砂轮保持锋利;3.改善砂轮表面平整度,细化砂轮表面锯齿形螺距。
解决内圆磨削砂轮磨削误差的方法可以分为两大方向。
砂轮修整是常用的方法之一,修整时砂轮退出内孔并在修整器位置往复运动一次,在砂轮表面去除一层磨料,把砂轮工作表面修整成所要求的型廓和锐度。
双端面磨床的磨削一般作为相加工工序其特点

双端面磨床的磨削一般作为相加工工序其特点
磨削就是在双端面磨床上用砂轮作为切削工具,对工件表面进行切削加工的一种方法。
磨削加工是机械零件精密加工的主要方法之一。
双端面磨床磨削用的砂轮是由许多细小而又坚硬的磨粒用耐高温的结合剂黏结而成的。
将砂轮表面放大,可以看到砂轮表面上杂乱无章地布满很多尖锐的多角形砂粒,这种砂粒叫做磨粒。
砂轮面每一个锋利的小磨粒,都具有很高的硬度和耐热性,相当于铣刀的一个刀齿,在砂轮高速旋转下,切入工件表面。
因此,磨削加工的实质就是一种多刀多刃的超高速铣削加工过程。
双端面磨床的磨削一般作为相加工工序,与车削、铣削、刨削相比较有如下特点。
(1)双端面磨床的磨削属于精加工,能获得较高的尺寸精度和较低的表面粗糙度。
磨削加的尺寸精度一般能达到IT6一IT5,表面粗糙度Ra值一般为o.8~0.2μm,低粗极度的镜面磨削可使只。
值小于0.01μm。
(2)由于砂轮磨粒硬度极高,磨削不仅可以加工碳钢、铸铁、未淬火钢、铜、铝等一般的金属材料,还可以加工淬火钢、各种切削刀具及硬质合金等硬度很高的材料。
这些材料用金属刀具很难加工,有的甚至根本不能加工。
这是磨削加工的一个显著特点。
(3)磨削时,切削深度较小,在一次行程中所能切除的金属层较薄。
粗磨时,t
=0.01~0.03mm;精磨时t=0.005~0.015mm。
(4)砂轮的工作速度高,可达到35m/s。
《磨削加工》课件

磨削加工的原理
总结词
磨削加工通过磨料和磨具的高速 旋转或往复运动,利用摩擦和切 削作用去除工件材料。
详细描述
在磨削加工过程中,磨料和磨具 的高速旋转或往复运动产生摩擦 和切削作用,将工件表面材料去 除,从而实现工件的加工。
磨削加工的应用领域
总结词
磨削加工广泛应用于机械制造、航空航天、汽车、能源等领域。
方法具有加工效率高、加工质量好的优点,是现代机械加工领域的重要技术之一。
03
磨削加工的主要技术参数
磨削速度
总结词
磨削速度是砂轮线速度,它直接影响磨削效率和磨削质量。
详细描述
磨削速度越高,单位时间内参与磨削的磨粒数越多,磨削效 率越高。但过高的磨削速度会导致工件表面温度升高,产生 烧伤和裂纹。因此,需要根据工件材料和砂轮特性选择合适 的磨削速度。
高效深切磨削
总结词
一种快速去除材料的磨削加工方法
详细描述
高效深切磨削是一种追求高效率的磨削方法,通过加大切深和切宽来快速去除材料。这种方法适用于 大型零件的粗加工和半精加工,具有加工效率高、加工成本低的优势。
超硬材料磨削
总结词
使用超硬材料作为磨料的磨削加工方法
详细描述
超硬材料磨削是指使用超硬材料(如碳化硅、金刚石等)作为磨料进行磨削加工的方法 。由于超硬材料的硬度极高,因此可以实现对硬质合金、陶瓷等高硬度材料的加工。该
磨削深度
总结词
磨削深度是砂轮表面与工件表面的距离 ,它决定了磨削层的厚度。
VS
详细描述
磨削深度对磨削效率和表面粗糙度有较大 影响。增加磨削深度可以提高磨削效率, 但过大的磨削深度会导致工件表面粗糙度 增加。因此,需要根据工件材料、砂轮特 性以及表面质量要求来选择合适的磨削深 度。
磨削加工

下一页 返回
2)砂轮磨料具有很高的硬度和耐热性,因此,能够磨削一些硬度 很高的金属和非金属材料,如淬火钢、硬质合金、陶瓷材料等。 这些材料用一般的车、铣等很难加工。但由于磨屑易堵塞砂轮表 面的孔隙,所以不宜磨削软质材料,如纯铜、纯铝等。 3)磨削速度大,磨削时磨削区温度可高达800~1000℃左右,这 容易引起零件的变形和组织的变化。所以在磨削过程中,需进行 充分的冷却,以降低磨削温度。 4) 砂轮在磨削时具有“自锐作用”。在磨削力的作用下会部分磨
筒形砂轮
杯形砂轮
碗形砂轮
蝶形砂轮
一、磨料
锋利的形状、高硬度和热硬性、适当的坚韧性
1、刚玉系(主要成份Al2O3)
① 棕刚玉(A):硬度低,韧性较好,廉价。磨碳素钢、合金钢、可锻铸铁 ② 白刚玉(WA):硬度高,韧性差,磨粒锋利,价格高。磨淬火钢、高速钢、 高碳钢
2、碳化物系(主要成份碳化硅、碳化硼)
动画3 纵磨法
2)横磨法
◆机床运动:工件不作纵向往复运动, 而是砂轮作慢速的横向进给。 ◆ 特点:砂轮宽度上的全部磨粒都参 加了磨削,生产率高;工件无纵向移 动,砂轮的外形直接影响了工件的精 度;磨削力大、磨削温度高,工件易 发生变形和烧伤,加工的精度和表面 质量比纵磨法要差。
◆用途:适用于加工批量大、刚度好
高速深切快 进给磨削
为防止深切缓进给磨削易产生烧伤,在磨削用量上尽量 避免高温区,可在加大切深与提高砂轮速度的同时,提高 工件进给速度,以提高材料切除率。
砂带磨削
根据工件型面,应用砂带形成贴合接触,进行加工的新型 高效磨削工艺;能加工各种复杂曲面,有较好的跑合和抛 光作用;效率达到铣削的10倍,普通砂轮磨削的5倍;产生 磨削热少,磨削条件稳定,设备简单;Ra值为0.8~0.2μm。
内圆磨削的工艺特点

内圆磨削的工艺特点
内圆磨削是一种用于加工内圆表面的金属切削工艺。
其工艺特点如下:
1. 高精度:内圆磨削能够实现高精度加工,可达到在微米甚至亚微米级别的精度要求。
2. 高表面质量:内圆磨削能够获得较高的表面质量,能够达到光洁度和平滑度要求,降低零件的摩擦和磨损。
3. 完整性好:内圆磨削能够保持零件的几何形状、尺寸和位置精度,具有较好的工件几何稳定性和一致性。
4. 适用范围广:内圆磨削适用于各种硬度和材料的内圆表面加工,包括金属、陶瓷、塑料等。
5. 加工效率高:内圆磨削具有高切削速度、大吃刃量和高金属切削率的特点,加工效率高,能够快速完成加工任务。
6. 适应性强:内圆磨削工艺适应性强,可以适应不同形状、尺寸和复杂度的内圆表面加工要求。
7. 自动化程度高:内圆磨削可以通过自动化设备进行操作,提高生产效率和减少人力成本。
总之,内圆磨削具有高精度、高表面质量、完整性好、适用范围广、加工效率高、适应性强和自动化程度高等工艺特点。
圆周磨削和端面磨削的特点

圆周磨削和端面磨削的特点
圆周磨削和端面磨削是两种常见的磨削方法,它们各有特点:
圆周磨削:
1. 圆周磨削是将工件放置在磨削轮的圆周上进行磨削,磨削轮通过旋转将磨削力传递给工件表面。
2. 圆周磨削适用于对工件外表面进行磨削,如圆柱体、圆锥体等形状的磨削。
3. 圆周磨削可以实现高精度的磨削,能够获得较好的表面质量。
4. 圆周磨削可以高效地去除工件表面的材料,提高工件的尺寸精度和几何形状。
端面磨削:
1. 端面磨削是将工件放置在磨削轮的端面上进行磨削,磨削轮通过旋转将磨削力传递给工件端面。
2. 端面磨削适用于对工件的端面进行磨削,如平面、圆形端面等形状的磨削。
3. 端面磨削可以实现高精度的磨削,能够获得较好的端面平整度和垂直度。
4. 端面磨削可以对工件的端面进行修整和加工,提高工件的尺寸精度和几何形状。
总的来说,圆周磨削适用于对工件外表面进行磨削,而端面磨削适用于对工件的端面进行磨削。
它们都可以实现高精度的磨削,并能够提高工件的尺寸精度和几何形状。
磨削加工的特点实用版
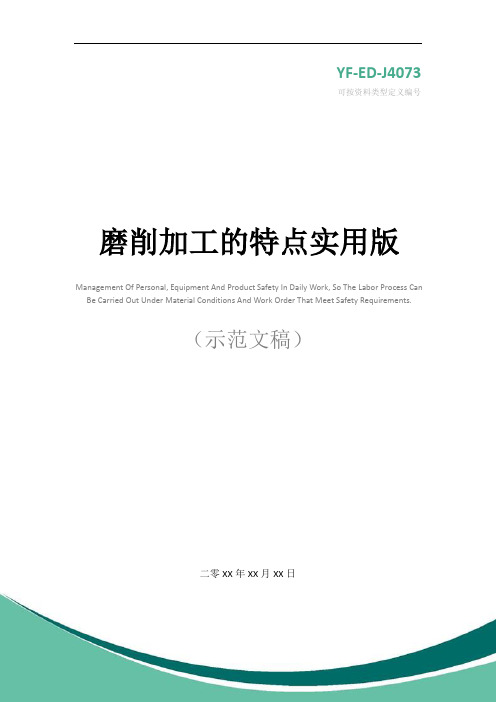
YF-ED-J4073可按资料类型定义编号磨削加工的特点实用版Management Of Personal, Equipment And Product Safety In Daily Work, So The Labor Process Can Be Carried Out Under Material Conditions And Work Order That Meet Safety Requirements.(示范文稿)二零XX年XX月XX日磨削加工的特点实用版提示:该安全管理文档适合使用于日常工作中人身安全、设备和产品安全,以及交通运输安全等方面的管理,使劳动过程在符合安全要求的物质条件和工作秩序下进行,防止伤亡事故、设备事故及各种灾害的发生。
下载后可以对文件进行定制修改,请根据实际需要调整使用。
磨削加工是借助磨具的切削作用,除去工作表面的多余层,使工件表面质量达到预定要求的加工方法。
进行磨削加工的机床称为磨床。
磨削加工应用范围很广,通常作为零件(特别是淬硬零件)精加工工序,可以获得很高的加工精度和表面质量,可以用于粗加工、切割加工等。
从安全角度来看,磨削加工有以下特点:1、磨具的运转速度高。
普通磨削可达30-50m/s,高速磨削可达45-60m/s甚至更高,其速度还有日益提高的趋势。
2、磨具的非均质结构。
磨具是由磨料,结合剂和气孔三要素组成的复合结构,其结构强度大大低于由单一均匀才智组成的一半金属切削刀具。
3、磨削的高热现象。
磨具的高速运动、磨削加工的多刃性和微量切削,都会产生大量的磨削热,不仅可能烧伤工件表面,而且高温时磨具本身发生物理、化学变化、产生热反应力、降低磨具的强度。
4、磨具的自砺现象。
在磨削力度作用下,磨钝的磨粒自身脆裂或脱落的现象,称为磨具的自砺性。
磨削过程中的磨具自砺作用以及修正磨具的作业,都会产生大量磨削粉尘。
- 1、下载文档前请自行甄别文档内容的完整性,平台不提供额外的编辑、内容补充、找答案等附加服务。
- 2、"仅部分预览"的文档,不可在线预览部分如存在完整性等问题,可反馈申请退款(可完整预览的文档不适用该条件!)。
- 3、如文档侵犯您的权益,请联系客服反馈,我们会尽快为您处理(人工客服工作时间:9:00-18:30)。
In Order To Simplify The Management Process And Improve The Management Efficiency, It Is
Necessary To Make Effective Use Of Production Resources And Carry Out Production Activities.
编 订:XXXXXXXX
20XX年XX月XX日
磨削加工的特点简易版
专业生产运营 / Sample Professional Contract 编号:EW/OF-VN629
第 2 页 / 共 3 页
磨削加工的特点简易版
温馨提示:本安全管理文件应用在平时合理组织的生产过程中,有效利用生产资源,经济合理
地进行生产活动,以达到实现简化管理过程,提高管理效率,实现预期的生产目标。文档下载
完成后可以直接编辑,请根据自己的需求进行套用。
磨削加工是借助磨具的切削作用,除去工
作表面的多余层,使工件表面质量达到预定要
求的加工方法。进行磨削加工的机床称为磨
床。磨削加工应用范围很广,通常作为零件
(特别是淬硬零件)精加工工序,可以获得很
高的加工精度和表面质量,可以用于粗加工、
切割加工等。
从安全角度来看,磨削加工有以下特点:
1、磨具的运转速度高。普通磨削可达30-
50m
/s,高速磨削可达45-60m
/s甚至更高,其速度还有日益提高的趋
专业生产运营 / Sample Professional Contract 编号:EW/OF-VN629
第 3 页 / 共 3 页
势。
2、磨具的非均质结构。磨具是由磨料,结
合剂和气孔三要素组成的复合结构,其结构强
度大大低于由单一均匀才智组成的一半金属切
削刀具。
3、磨削的高热现象。磨具的高速运动、磨
削加工的多刃性和微量切削,都会产生大量的
磨削热,不仅可能烧伤工件表面,而且高温时
磨具本身发生物理、化学变化、产生热反应
力、降低磨具的强度。
4、磨具的自砺现象。在磨削力度作用下,
磨钝的磨粒自身脆裂或脱落的现象,称为磨具
的自砺性。磨削过程中的磨具自砺作用以及修
正磨具的作业,都会产生大量磨削粉尘。
该位置可填写公司名或者个人品牌名
Company name or personal brand name can be filled in this position