(完整版)磨削加工的特点是什么
各种磨削加工特点介绍
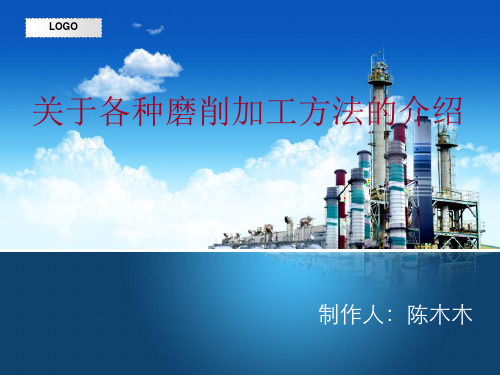
磨削方法:纵磨法和横磨法
纵磨法:加工精度高,Ra值较小,生产 率低,广泛用于各种类型的生 产中;
横磨法:加工精度低,Ra值较大,生产 率高,只适用于大批量生产中 磨削刚度较好、精度较低、长 度较短的轴类零件上的外圆表 面和成形面。
加工方法:周磨法、端磨法(磨平面)
①周磨法:加工精度高,表面粗糙度Ra值小, 但生产率较低,多用于单件小批生产中,大 批大量生产中亦可使用。 ②端磨法:生产率较高,但加工质量略差于周 磨法,多用于大批大量生产中磨削精度要求 不太高的平面。
恒力磨削
横磨法的特殊形式。磨削时,无 论外界因素如磨削余量、工件材料硬 度、砂轮钝化程度等如何变化,砂轮 始终以预定的压力压向工件,直到磨 削结束为止。
恒压力磨削加工质量稳定,生产 率高,避免砂轮超负荷工作,操作安 全。
宽砂轮与多砂轮磨削
宽砂轮磨削是用增大磨削宽度来提 高磨削效率的。 宽砂轮外圆磨削采用横磨法,主要 用于大批量生产中,如磨削花键轴、 电机轴等。尺寸公差等级可达IT6,Ra 值可达0.4 μ m。 多砂轮磨削是宽砂轮磨削的另一种 形式。主要用于大批量生产中外圆和 平面的磨削。
各种表面:内外圆表面、圆锥面、平面、齿面、螺旋面 各种材料:普通塑性材料、铸件等脆材、淬硬钢、硬质 合金、宝石等高硬度难切削材料。
(3)磨削速度高、耗能多,切削效率低,磨削温度 高,工件表面易产生烧伤、残余应力等缺陷。 (4)砂轮有一定的自锐性。
LOGO
多砂轮磨削
砂带磨削
定义:利用砂带,根据加工要求以相应 的接触方式对工件进行加工的方 法称为砂带磨削。是一种新型高 效工艺方法。 特点:效率高、磨削热少,散热条件好。 砂带磨削的工件,其表面变形强 化程度和残余应力均大大低于砂 轮磨削。
第五节 磨削的工艺特点及其应用

第五节磨削的工艺特点及其应用用砂轮或其他磨具加工工件,称为磨削。
本节主要讨论用砂轮在磨床上加工工件的特点及其应用,磨床的种类很多,较常见的有外圆磨床、内圆磨床和平面磨床等。
作为切削工具的砂轮,是由磨料加结合剂用烧结的方法而制成的多孔物体。
由于磨料、结合剂及制造工艺等的不同,砂轮特性可能差别很大,对磨削的加工质量、生产效率和经济性有着重要影响。
砂轮的特性包括磨料、粒度、硬度、结合剂、组织以及形状和尺寸等。
一.磨削过程磨削可以加工外圆面、内孔、平面、成形面、螺纹、齿轮等1.外圆磨削1、在外圆磨床上进行磨法:纵磨法横磨法综合磨深磨法2、无心外圆磨圆面必须连续,不能有较长键槽等孔的磨削2.平面磨削周磨质量较高,但较慢端磨较快,但质量不高特点:主运动是砂轮的旋转运动;磨削过程:实际上是磨粒对工件表面的切削、刻削和滑擦三种作用的综合效应;砂轮的“自锐性” :磨削中,磨粒本身也会由尖锐逐渐磨钝,使切削能力变差,切削力变大,当切削力超过粘结剂强度时,磨钝的磨粒会脱落,露出一层新的磨粒,这就是砂轮的“自锐性”。
磨削往往作为最终加工工序。
砂轮的修整由于砂轮的“自锐性”以及切屑和碎磨粒会阻塞砂轮,在磨削一定时间后,需用金刚石车刀等对砂轮进行修整。
二.磨削的工艺特点磨床的特点:a.使用磨料、磨具(如砂轮、砂带、油石、研磨料等)为工具,进行切削加工。
b.用来加工硬度较高的材料。
c.加工精度高、光洁度高。
d.一般加工余量较小。
工业发达国家,磨床比例高(约30%左右),磨床用于粗、精加工,发展了新型强力磨和高速磨。
三.磨削的应用和发展(一)外圆磨床磨床中所占比例较大的一种,包括万能外圆磨床、外圆磨床、无心外圆磨床。
1.万能外圆磨床万能性好,常用于加工以下几种典型表面。
<1>磨外圆加工所需的运动砂轮主运动 n工件的圆周进给运动 f1工件的纵向进给运动 f2砂轮的横向切入运动 c<2>磨长圆锥面外圆磨床工作台分两层,上工作台相对下工作台调整至一定的角度位置(不超过±7°)机床运动与(1)相同,但工件回转中心线与工作台纵向进给方向不平行,故磨削出来的是圆锥面。
磨削加工
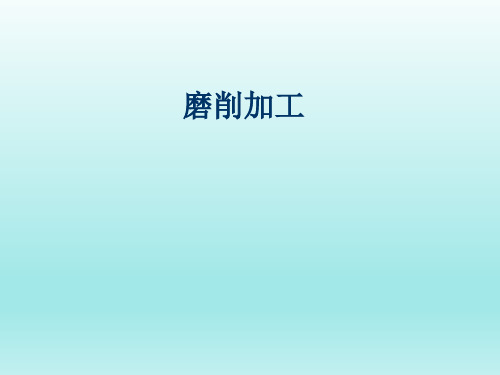
(1)体积小、重量轻,例如同功率液压马达的重量只有电动机的10%~20%。 (2)换向容易,在不改变电机旋转方向的情况下,可以较方便地实现工作机构
旋转和直线往复运动的转换;
(3)液压装置工作比较平稳,由于重量轻,惯性小,反应快 , 液压装置易于实现快速启动、制动和频繁的换向; (4)操纵控制方便,可实现大范围的无级调速(调速范围达 2000:1),它还可以在运行的过程中进行调速;
28
液压传动的工作介质
液压系统对工作介质的要求 液压工作介质一般称为液压油。液压介质的性能对液压 系统的工作状态有很大影响,对液压系统对工作介质的基本 要求如下: (l)有适当的粘度和良好的粘温特性。 粘度是选择工作介质的首要因素。液压油的粘性,对减 少间隙的泄漏、保证液压元件的密封性能都起着重要作用。 液压介质粘度用运动粘度 表示。在国际单位制中的 单 2 位是 m 2 / s ,而在实用上油的粘度用 m m / s (cSt,厘沲)表示。 粘度是液压油(液)划分牌号的依据。按国标GB/T314194所规定,液压油产品的牌号用粘度的等级表示,即用该液压 油在40℃时的运动粘度中心值表示。
硬度——结合剂黏结磨料颗粒的牢固程度,它 表示砂轮在外力(磨削抗力)作用下磨料颗粒从砂 轮表面脱落的难易程度 。
影响磨削的加工精度和生产率。
组织
组织——砂轮内部结构的疏密程度 。
根据磨粒在整个砂轮中所占体积的比例不同,砂轮 组织分成紧密、中等和疏松三大类共16级。
砂轮的选择
磨削硬材料时,应选择软的,粒度号大的砂轮; 磨削软材料时,应选择硬的,粒度号小的、组织号大的 砂轮; 粗磨时,应选择粒度号小,软的砂轮;提高生产率 精磨时,粒度号大,硬的砂轮;提高表面质量 …..
简述磨削加工的原理和主要特点-解释说明

简述磨削加工的原理和主要特点-概述说明以及解释1.引言1.1 概述磨削加工是一种常见的金属加工方法,通过磨盘或砂轮在工件表面旋转摩擦来去除材料,以达到对工件进行精密加工的目的。
磨削加工可以提高零件的精度和表面质量,广泛应用于机械制造、航空航天、汽车制造等领域。
本文将从磨削加工的原理和主要特点入手,探讨其在工业生产中的重要性和应用领域,旨在帮助读者更深入地了解磨削加工技术的本质和价值。
1.2 文章结构文章结构部分应该包括以下内容:文章结构部分主要介绍整篇文章的组织结构,包括各个部分的内容概述、关联性和逻辑性,以及各部分之间的内在联系和发展关系。
文章结构部分有助于读者更好地理解整篇文章的内容,把握文章的主题和要点,提高文章的阅读效果和理解深度。
1.3 目的磨削加工是一种重要的金属加工方法,在工业生产中有着广泛的应用。
本文的目的在于深入探讨磨削加工的原理和特点,帮助读者更加全面地了解这一加工方法。
通过对磨削加工的原理进行解析,可以帮助读者掌握其工作过程和机理,进而提高加工的精度和效率。
同时,介绍磨削加工的主要特点可以让读者了解其在加工过程中的优势和局限性,从而更好地选择适合的加工方法。
最后,通过分析磨削加工的应用领域,可以帮助读者在实际生产中更好地应用这一技术,提高工件的加工质量和产量。
综合来看,本文旨在为读者提供有关磨削加工的全面知识,以促进相关行业的发展和进步。
2.正文2.1 磨削加工的原理:磨削加工是通过磨料与工件之间的相对运动来去除工件表面切屑,达到加工和改善工件表面质量的目的。
其基本原理可以简单概括为磨料在较高的线速度下对工件表面进行切削。
磨削加工的原理主要包括以下几个方面:1. 磨削过程中,磨料的颗粒与工件表面接触,产生高温和高压力,使工件表面的金属发生塑性变形和切屑脱落。
2. 磨料颗粒的形状、尺寸、硬度等特性直接影响磨削效果和工件表面质量,不同的磨料可以应用于不同的工件材料和加工要求。
3. 磨料与工件之间的相对运动方式包括旋转磨削、平面磨削、外圆磨削等多种形式,根据具体的工件形状和加工要求选择合适的磨削方式。
车削,铣削,磨削,刨削,钻削的工艺特点

车削,铣削,磨削,刨削,钻削的工艺特点
车削的工艺特点:
1. 利用旋转刀具对工件进行切削加工,工件固定在回转工作台上。
2. 适用于加工轴类工件和旋转对称零件。
3. 刀具与工件之间有相对运动,可以实现高精度的切削加工。
4. 可以实现多种切削操作,如外圆车削、内圆车削、平面车削等。
铣削的工艺特点:
1. 利用旋转刀具在工件表面上进行直线或曲线方向的切削加工,工件固定在工作台上。
2. 适用于加工平面、曲面、齿轮等复杂形状的工件。
3. 切削速度较高,加工效率高。
4. 可以实现多种切削方式,如平面铣削、立铣、侧铣等。
磨削的工艺特点:
1. 利用磨料粒子对工件进行磨擦切削,工件固定在工作台上。
2. 适用于加工高硬度、高精度要求的工件,如模具、工具等。
3. 能够实现高精度的尺寸和形状加工。
4. 磨料粒子具有自锋性,切削力小,可加工硬度高的材料。
刨削的工艺特点:
1. 利用刨刀对工件进行切削加工,工件固定在工作台上。
2. 主要用于加工大型工件的面、平面和槽的加工。
3. 加工速度较低,但能够达到高表面精度和平面度。
4. 切削力大,适用于切削材料的加工。
钻削的工艺特点:
1. 利用旋转钻头对工件进行切削加工,工件固定在工作台上。
2. 主要用于加工孔类零件,可以实现精确的孔径和孔位。
3. 可以加工各种孔型,如圆孔、长孔、螺纹孔等。
4. 切削速度较慢,但能够达到较高精度和光洁度。
磨削加工

磨削加工一.磨削的起源、发展及磨削的特点:1.磨削加工是利用磨料去除材料的加工方法。
用磨料去除材料的加工是人类最早使用的生产技艺方法。
远在石器时代,以开始使用磨料研磨加工各种贝壳、石头、及兽骨等,用于生活和狩猎工具。
青铜器出现以后磨削加工技术得到了进一步的发展,用来制造兵器和及生产工具,用磨料研磨铜镜已达到镜面的要求。
铁器的出现,使磨料加工成为一种普遍的工艺技巧得到应用。
2.磨削加工的特点:(1)磨削速度高磨削时砂轮具有较高的线速度。
一般在35m/s左右,高速磨削线速度可达40m/s、最高可达50m/s以上。
阿享工科大学(Aachen),进行砂轮线速度500m/s为目标的超高速磨削实验,一般认为告诉磨削工艺不适于加工大平面或圆柱型表面的精加工,主要用于沟槽和缺口件的磨削及切入磨削。
(2)能达到较高的加工精度和很低的表面粗糙度例如:车床上能达到的精度等级为IT7~10级。
普通的磨削可达到IT5~7级、表面粗糙度可达到Ra0.2~0.8um。
镜面磨削Ra0.01um,工件表面光如镜面尺寸精度和形状精度可达1um以内,其误差相当于一个人头发丝粗细的1/70或更小。
(头发丝的直径一般在0.06mm左右)IT为国家精度等级标准,共分20级。
IT01级、IT0级、IT1级、IT2级……IT18级。
(3)可磨削高硬材料,又可以磨削软材料。
磨粒是一种高硬度的非金属晶体。
它不但可以磨削铜、铝等较软的材料,又可以磨削各种淬硬钢、高速钢刀具和硬质合金等及一些超硬材料。
(如氮化硅)例:可磨削车刀、铣刀。
一般认为当硬度超过HRC40以上,普通的车、铣就无法进行加工。
(4)磨削是一种少切屑的加工例:车床上初加工是的进给量可以是3~5mm,而磨床上一般为0.02mm。
高精度镜面磨削一般为0.02mm的1/4左右。
二.磨床产生、现状及发展趋势18世纪中期出现了第一台外圆磨床,有石英石、石榴石等天然磨料敲凿成磨具,进而用天然磨料和粘土烧结成砂轮,随后又研制成功平面磨床,应用磨削技术形成。
(完整版)磨削加工的特点是什么
磨削加工的特点是什么?
磨削是一种常用的半精加工和精加工方法,砂轮是磨削的切削工具,磨削是由砂轮表面大量随机分布的磨粒在工件表面进行滑擦、刻划和切削三种作用的综合结果。
磨削的基本特点如下:
1•磨削的切削速度高,导致磨削温度高。
普通外圆磨削时v=35m/s,高速磨削v> 50m/s。
磨
削产生的切削热80%〜90%传入工件(10%〜15%传入砂轮,1%〜10%由磨屑带走),加上砂轮的导热性很差,易造成工件表面烧伤和微裂纹。
因此,磨削时应采用大量的切削液以降低磨削温度。
2•能获得高的加工精度和小的表面粗糙度值加工精度可达IT6-IT4,表面粗糙度值可达
Ra0.8-0.02卩m。
磨削不但可以精加工,还可以粗磨、荒磨、重载荷磨削。
3•磨削的背向磨削力大因磨粒负前角很大,且切削刃钝圆半径rn较大,导致背向磨削力
大于切向磨削力,造成砂轮与工件的接触宽度较大。
会引起工件、夹具及机床产生弹性变形,影响加工精度。
因此,在加工刚性较差的工件时(如磨削细长轴),应采取相应的措施,防止因工件变形而影响加工精度。
4.砂轮有自锐作用出一层新的锋利磨粒,利于磨削加工。
在磨削过程中,磨粒有破碎产生较锋利的新棱角,及磨粒的脱落而露
能够部分地恢复砂轮的切削能力,这种现象叫做砂轮的自锐作用,有
5.能加工高硬度材料磨削除可以加工铸铁、碳钢、合金钢等一般结构材料外,还能加工
一般刀具难以切削的高硬度材料,如淬火钢、硬质合金、陶瓷和玻璃等。
但不宜精加工塑性较大的有色金属工件。
磨削有哪些原理特点
磨削加工都有哪些类型及原理特点《磨削加工》以制造工艺为主线,数据与方法相结合,汇集了我国多年来工艺工作的成就和经验,反映了国内外现代工艺水平及其发展方向。
工艺基础包括车削、镗削、铣削、锯削、钻削、扩削、铰削、拉削、刨削、插削、磨削加工,齿轮、蜗轮蜗杆、花键加工,螺纹加工,特种加工,精密加工和纳米加工,高速切削,难加工材料的切削加工,表面工程技术。
主要包括磨削原理、磨削液、磨床与磨床夹具、磨料磨具、磨削加工工艺等内容。
磨削加工磨削加工1、外圆磨削主要在外圆磨床上进行,用以磨削轴类工件的外圆柱、外圆锥和轴肩端面。
磨削时,工件低速旋转,如果工件同时作纵向往复移动并在纵向移动的每次单行程或双行程后砂轮相对工件作横向进给,称为纵向磨削法。
如果砂轮宽度大于被磨削表面的长度,则工件在磨削过程中不作纵向移动,而是砂轮相对工件连续进行横向进给,称为切入磨削法。
一般切入磨削法效率高于纵向磨削法。
如果将砂轮修整成成形面,切入磨削法可加工成形的外表面。
2、内圆磨削主要用于在内圆磨床、万能外圆磨床和坐标磨床上磨削工件的圆柱孔、圆锥孔和孔端面。
一般采用纵向磨削法。
磨削成形内表面时,可采用切入磨削法。
在坐标磨床上磨削内孔时,工件固定在工作台上,砂轮除作高速旋转外,还绕所磨孔的中心线作行星运动。
内圆磨削时,由于砂轮直径小,磨削速度常常低于30米/秒、耐磨性是普通砂轮的20-100倍,极大的减少了砂轮的修正及更换频率。
3、平面磨削主要用于在平面磨床上磨削平面、沟槽等。
平面磨削有两种:用砂轮外圆表面磨削的称为周边磨削,一般使用卧轴平面磨床,如用成形砂轮也可加工各种成形面;用砂轮端面磨削的称为端面磨削,一般使用立轴平面磨床。
4、无心磨削一般在无心磨床上进行,用以磨削工件外圆。
磨削时,工件不用顶尖定心和支承,而是放在砂轮与导轮之间,由其下方的托板支承,并由导轮带动旋转。
当导轮轴线与砂轮轴线调整成斜交1°~6°时,工件能边旋转边自动沿轴向作纵向进给运动,这称为贯穿磨削。
磨削的工艺特点及其应用
磨粒破碎或整块从砂轮表面脱 落,露出里面新的磨粒,继续 进行磨削
砂轮的这种自行推陈出新,保持“自身锋锐”的性能称为 砂轮的自锐性。
由于砂轮这种自锐性,一方面破碎磨粒会堵塞孔隙,另一 方面随机脱落的磨粒引起砂轮尺寸精度下降,所以,经一段磨 削的砂轮需要重新修整,以保证其加工精度。
三、磨削的加工工艺特点:
①外圆磨削 分为有心磨削和无心磨削 在普通外圆磨床和万能外圆磨床上进行的
外圆柱面的加工是有心磨削。根据磨削运动的 不同,有心磨削分为纵磨法、横磨法、综合磨 法和深磨法。
纵磨法 横磨法 综合磨法 深磨法
进给运动
工件旋转实现周向进给;工作台 往复直线运动实现纵向进给;工 件一次往复行程终了时,砂轮做 周期性的径向进给。
1. 砂轮的特性包括:
1)磨料 目前应用的主要是人造磨料,分为固结磨 具磨料(F系列,表3-1列出了常用磨料A、C、MBD、 CBN)和涂附磨具磨料(P系列)。
2)粒度 反映磨料颗粒大小的程度。粒度号用F+数 字 表示,数字越大颗粒越小。一般情况下,粗磨时选 用颗粒大的磨粒,精磨时选用颗粒较小的磨料。
结合剂:有陶瓷结合剂、树脂结合剂、橡胶结合 剂等。
陶瓷结合剂适用于外圆、内圆、平面和各种成形表 面磨削;树脂结合剂和橡胶结合剂适用于制成各种切 割用的薄片砂轮。
由于磨料、结合剂和制造工艺不同,砂轮性能差别 很大,对磨削效果、生产率和经济性有很大影响。
砂轮的特性是指磨料种类、粒度大小、硬度、结合 剂、结构组织、形状和砂轮尺寸等指标。
滑擦、 摩擦严重,切削热多。 ③砂轮本身传热性能很差,短时间内切削热传不出去 。
由于磨削过程切削温度很高。因此,磨削中应大 量采用切削液。切削液除冷却、润滑作用外,还可以 冲洗砂轮,保证磨削的正常运行,提高砂轮的耐用度 和工件的加工质量。
磨削加工培训资料
磨削加工培训资料一、磨削加工的特点1、磨具为多刃刀具:磨削加工时所用的的刀具是砂轮,它是由磨粒和结合剂粘接而成的多刃刀具。
在砂轮表面每平方厘米面积上约有60—1400颗磨粒。
磨粒的形体各异,呈不规则分布,每个磨粒相当于一个刀齿。
当砂轮高速旋转时,磨粒上的锋利微刃便切入工件,并去掉一部分金属,这就是磨粒的切削作用。
2、磨削时砂轮具有较高的圆周速度:一般在35m/s左右。
砂轮在磨削时除了对工件表面有切削作用外,还有强烈的挤压和磨擦抛光作用,在磨削区域瞬时温度高达成1000℃左右。
3、既可磨软材料又可磨硬材料:磨粒是一种高硬度的非金属晶体,它不但可以磨削铜、铝、铸铁等较软的材料,而且还可以磨削各种淬硬钢件,高速钢刀具和硬质合金等到硬材料以及一些超硬材料(如氮化硅)。
4、既可切除极薄表面又可有极高的切除率:砂轮工作面经修整后,磨粒尖部多呈-15°~60°的负前角,形成极微细的切削刃,可切除工件表面极薄的金属层。
因此,磨削一般用作精加工工序。
但是,磨削也可有极高的金属切除率,如通过强力磨削,一次可切除2~20mm金属。
5、可获得极高精度的精细表面:磨削加工能获得极高的加工精度和极低的表面粗糙度值。
磨削精度通常可以达到公差等级IT6~IT7,表面粗糙度可达Ra1.25~0.16um。
采用镜面磨削,工件的表面粗糙度可达Ra0.01um。
工件表面光滑如镜,尺寸精度和形状精度可达1um以内,其误差相当于一个人头发丝粗细的1/70或更小。
6、砂轮具有“自锐”作用:砂轮在磨削时,部分磨钝的磨粒在一定条件下能自动脱落或崩碎,露出新的锋利磨粒参加磨削加工,这一特性称为砂轮的“自锐”作用,能使砂轮保持良好的磨削性能。
二、磨削分类磨削分类的方法很多,通常按工具类型进行分类,可分为使用固定磨粒的和使用游离磨粒的两大类。
固定磨粒加工有砂轮磨削、五行磨、电解磨削等;游离磨粒加工则有研磨、抛光、滚磨、喷射加工、振动加工等。
- 1、下载文档前请自行甄别文档内容的完整性,平台不提供额外的编辑、内容补充、找答案等附加服务。
- 2、"仅部分预览"的文档,不可在线预览部分如存在完整性等问题,可反馈申请退款(可完整预览的文档不适用该条件!)。
- 3、如文档侵犯您的权益,请联系客服反馈,我们会尽快为您处理(人工客服工作时间:9:00-18:30)。
磨削加工的特点是什么?
磨削是一种常用的半精加工和精加工方法,砂轮是磨削的切削工具,磨削是由砂轮表面大量随机分布的磨粒在工件表面进行滑擦、刻划和切削三种作用的综合结果。
磨削的基本特点如下:
1.磨削的切削速度高,导致磨削温度高。
普通外圆磨削时v=35m/s,高速磨削v>50m/s。
磨削产生的切削热80%~90%传入工件(10%~15%传入砂轮,1%~10%由磨屑带走),加上砂轮的导热性很差,易造成工件表面烧伤和微裂纹。
因此,磨削时应采用大量的切削液以降低磨削温度。
2.能获得高的加工精度和小的表面粗糙度值加工精度可达IT6-IT4,表面粗糙度值可达Ra0.8-0.02μm。
磨削不但可以精加工,还可以粗磨、荒磨、重载荷磨削。
3.磨削的背向磨削力大因磨粒负前角很大,且切削刃钝圆半径rn较大,导致背向磨削力大于切向磨削力,造成砂轮与工件的接触宽度较大。
会引起工件、夹具及机床产生弹性变形,影响加工精度。
因此,在加工刚性较差的工件时(如磨削细长轴),应采取相应的措施,防止因工件变形而影响加工精度。
4.砂轮有自锐作用在磨削过程中,磨粒有破碎产生较锋利的新棱角,及磨粒的脱落而露出一层新的锋利磨粒,能够部分地恢复砂轮的切削能力,这种现象叫做砂轮的自锐作用,有利于磨削加工。
5.能加工高硬度材料磨削除可以加工铸铁、碳钢、合金钢等一般结构材料外,还能加工一般刀具难以切削的高硬度材料,如淬火钢、硬质合金、陶瓷和玻璃等。
但不宜精加工塑性较大的有色金属工件。