(完整版)自动导引小车(AGV)系统的设计
agv设计方案
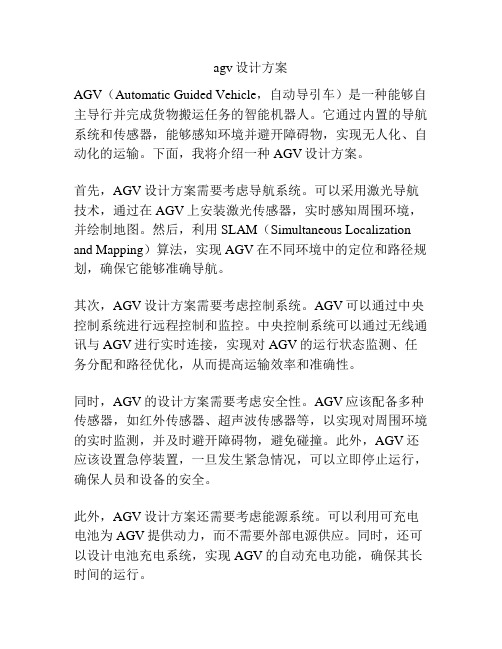
agv设计方案AGV(Automatic Guided Vehicle,自动导引车)是一种能够自主导行并完成货物搬运任务的智能机器人。
它通过内置的导航系统和传感器,能够感知环境并避开障碍物,实现无人化、自动化的运输。
下面,我将介绍一种AGV设计方案。
首先,AGV设计方案需要考虑导航系统。
可以采用激光导航技术,通过在AGV上安装激光传感器,实时感知周围环境,并绘制地图。
然后,利用SLAM(Simultaneous Localization and Mapping)算法,实现AGV在不同环境中的定位和路径规划,确保它能够准确导航。
其次,AGV设计方案需要考虑控制系统。
AGV可以通过中央控制系统进行远程控制和监控。
中央控制系统可以通过无线通讯与AGV进行实时连接,实现对AGV的运行状态监测、任务分配和路径优化,从而提高运输效率和准确性。
同时,AGV的设计方案需要考虑安全性。
AGV应该配备多种传感器,如红外传感器、超声波传感器等,以实现对周围环境的实时监测,并及时避开障碍物,避免碰撞。
此外,AGV还应该设置急停装置,一旦发生紧急情况,可以立即停止运行,确保人员和设备的安全。
此外,AGV设计方案还需要考虑能源系统。
可以利用可充电电池为AGV提供动力,而不需要外部电源供应。
同时,还可以设计电池充电系统,实现AGV的自动充电功能,确保其长时间的运行。
最后,AGV设计方案还需要考虑扩展性。
AGV应该具备可扩展性,可以根据需求扩充数量,并能够与其他智能设备进行联动,实现更高效的物流和生产管理。
总之,这种AGV设计方案通过激光导航技术、中央控制系统、多传感器安全保障、可充电电池能源系统以及可扩展性的考虑,实现了AGV的自主导行和货物搬运功能。
它在工业生产、仓储物流等领域具有广阔的应用前景。
固定路径自动引导车(AGV)的控制系统设计

固定路径自动引导车(AGV)的控制系统设计摘要随着工厂自动化、计算机集成制造系统技术的逐步发展以及柔性制造系统、自动化立体仓库的广泛应用,AGVA(utomatieGuidedVehiele)即自动导引车作为联系和调节离散型物流系统以使其作业连续化的必要的自动化搬运装卸手段,其应用范围和技术水平得到了迅猛的发展。
AGV是以微控制器为控制核心、蓄电池为动力、装有非接触导引装置的无人驾驶自动导引运载车,其自动作业的基本功能是导向行驶、认址停准和移交载荷。
作为当代物流处理自动化的有效手段和柔性制造系统的关键设备,AGV已经得到了越来越广泛的应用,对AGV的研究也具有十分重要的理论意义和现实意义。
发展现状作出综述,系统地分析了自动导引车的特点、类型和技术组成,并对关键技术加以进一步的说明.本课题设计了一辆自动导引车,进行了系统总体设计,利用反射式光电红外收发管作为AGV(Automated Guided Vehicle)寻航检测装置,蓄电池和直流马达作为驱动装置,舵机作为方向控制装置,用单片机作为控制器来控制各个模块协同工作,以实现自动导引车自动导航。
关键词:单片机,AGV,红外传感器,PIDA fixed path Automatic Guided Vehicle (AGV) control systemdesignAbstractAs the factory automation, computer integrated manufacturing systems technology, as well as the progressive development of flexible manufacturing systems, automated warehouse extensive use, AGVA (utomatieGuidedVehiele) is automatically guided vehicle as an associate and regulation of discrete logistics system to make it necessary for continuous operation automated transport loading and unloading means, its scope of application and level of technology has seen rapid development.AGV is a micro-controller to control the core, battery-powered, equipped with a non-contact guiding devices, unmanned automatic guided transport vehicles, its automatic operation’s basic function is to guide traffic and identifying potential sites and the transfer of load to stop。
AGV小车的设计

AGV小车的设计一、AGV小车的发展从1953年第一辆AGV诞生至今AGV已经过了长达60年的革命使。
第一辆AGV它是由一辆简易的AGC产品牵引式拖拉机改造而成的,带有车兜,在一间杂货仓库中沿着布置在空中的导线运输货物。
在这60年中由于科技不断的发展,AGV无论是从外形还是性能方面都得到了质的飞跃。
可无论怎么更新换代,也改变不了AGV原有的本质。
-------AGV的引导装置,即便是怎样高科技的引导方式,但它必须拥有,不然AGV就无法行走。
从而,在这里也就解释了什么是AGV?-------AGV简单来讲它就是有自动引导装置,能够自动行走的运输小车。
二、AGV的设计理念AGV是针对自动化生产制造系统和自动化仓储物流系统的实际应用而开发设计的系列产品;其控制系统采用最先进的AGV运动控制模式;该产品采用磁引导的导航方式;具备磁地标或RFID地标识别模组,实现站点识别控制;I-SO AGV操控界面采用触控面板,界面设计人性化,简洁易用;车体可配备升降动力滚筒装置或牵引装置,与自动流水线对接。
AGV可用于电子行业的物料或成品搬运,并可广泛应用于柔性制造系统和自动化仓储系统。
三、AGV的特点●自动化程度高——由计算机,电控设备,磁气感应SENSOR,激光反射板等控制。
当车间某一环节需要辅料时,由工作人员向计算机终端输入相关信息,计算机终端再将信息发送到中央控制室,由专业的技术人员向计算机发出指令,在电控设备的合作下,这一指令最终被AGV接受并执行——将辅料送至相应地点。
●充电自动化——当AGV小车的电量即将耗尽时,它会向系统发出请求指令,请求充电(一般技术人员会事先设置好一个值),在系统允许后自动到充电的地方“排队”充电。
另外,AGV小车的电池寿命很长(2年以上),并且每充电15分钟可工作4h左右。
●美观——提高观赏度,从而提高企业的形象。
●安全性——人为驾驶的车辆,其行驶路径无法确知。
而AGV 的导引路径却是非常明确的,因此大大提高了安全性;●成本控制——I-SOAGV 系统的资金投入是短期的,而员工的工资是长期的,还会随着通货膨胀而不断增加;●易维护——红外传感器和机械防撞可确保AGV免遭碰撞,降低故障率;●可预测性——I-SOAGV 在行驶路径上遇到障碍物会自动停车,而人为驾驶的车辆因人的思想因素可能会判断有偏差;●降低产品损伤——可减少由于人工的不规范操作而造成的货物损坏;●改善物流管理——由于I-SOAGV 系统内在的智能控制,能够让货物摆放更加有序,车间更加整洁;●较小的场地要求—I-SO AGV 比传统的叉车需要的巷道宽度窄得多。
AGV自动导航车控制系统的设计与改进

AGV自动导航车控制系统的设计与改进AGV(Automatic Guided Vehicle)自动导航车是一种能够在工业环境中自动导航、运载物料的无人驾驶车辆。
AGV自动导航车控制系统的设计与改进,是为了提高生产效率,减少人工操作,实现自动化和智能化生产。
首先,AGV自动导航车的控制系统需要设计一个可靠的定位系统,以确定车辆的准确位置。
传统的定位方法包括激光导航、磁导航和视觉导航等,但这些方法都存在一定的局限性。
为了解决这个问题,可以采用多传感器融合的方法,结合使用激光、磁导航和视觉等多个传感器,提高定位的准确性和可靠性。
其次,AGV自动导航车的控制系统需要设计一个路径规划算法,以确定车辆的最佳路径。
传统的路径规划算法包括A*算法和Dijkstra算法等,但这些算法的计算复杂度较高,无法满足实时性的要求。
为了解决这个问题,可以采用快速路径规划算法,如D*算法和RRT算法等,减少路径规划的计算时间。
此外,AGV自动导航车的控制系统还需要设计一个动态避障算法,以确保车辆能够避免障碍物。
传统的避障算法包括静态避障算法和动态避障算法,但这些算法在遇到复杂环境时无法处理。
为了解决这个问题,可以采用深度学习算法,如卷积神经网络(CNN)和循环神经网络(RNN)等,实现车辆的智能避障。
此外,AGV自动导航车的控制系统还可以设计一个自适应控制算法,以应对不同工作场景下的变化。
自适应控制算法可以根据工作场景的变化,调整车辆的速度、加速度和转向角度等,使车辆能够更好地适应工作场景的变化,提高车辆的运行效果。
最后,AGV自动导航车的控制系统还需要设计一个远程监控和调度系统。
远程监控和调度系统可以实时监控车辆的运行状态和位置,并对车辆进行操作和调度,提高车辆的运行效率和生产效率。
总之,AGV自动导航车控制系统的设计与改进是一个综合性的工程,需要考虑定位、路径规划、避障、自适应控制和远程监控等多个方面,以实现自动化和智能化生产。
AGV小车设计资料
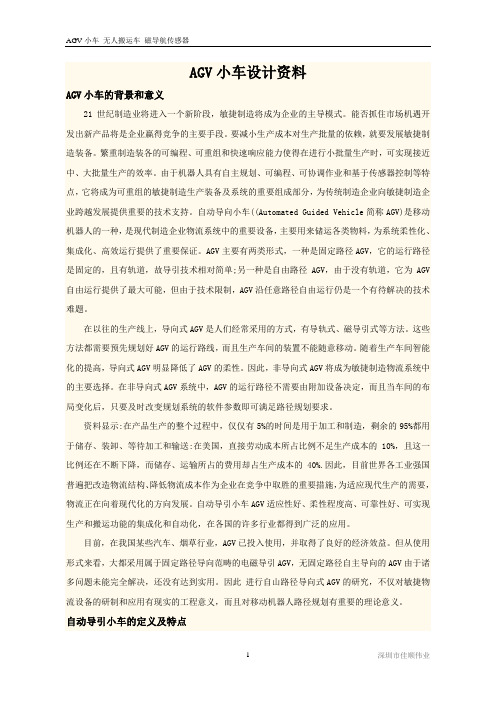
AGV小车设计资料AGV小车的背景和意义21世纪制造业将进入一个新阶段,敏捷制造将成为企业的主导模式。
能否抓住市场机遇开发出新产品将是企业赢得竞争的主要手段。
要减小生产成本对生产批量的依赖,就要发展敏捷制造装备。
繁重制造装各的可编程、可重组和快速响应能力使得在进行小批量生产时,可实现接近中、大批量生产的效率。
由于机器人具有自主规划、可编程、可协调作业和基于传感器控制等特点,它将成为可重组的敏捷制造生产装备及系统的重要组成部分,为传统制造企业向敏捷制造企业跨越发展提供重要的技术支持。
自动导向小车((Automated Guided Vehicle简称AGV)是移动机器人的一种,是现代制造企业物流系统中的重要设备,主要用来储运各类物料,为系统柔性化、集成化、高效运行提供了重要保证。
AGV主要有两类形式,一种是固定路径AGV,它的运行路径是固定的,且有轨道,故导引技术相对简单;另一种是自由路径AGV,由于没有轨道,它为AGV 自由运行提供了最大可能,但由于技术限制,AGV沿任意路径自由运行仍是一个有待解决的技术难题。
在以往的生产线上,导向式AGV是人们经常采用的方式,有导轨式、磁导引式等方法。
这些方法都需要预先规划好AGV的运行路线,而且生产车间的装置不能随意移动。
随着生产车间智能化的提高,导向式AGV明显降低了AGV的柔性。
因此,非导向式AGV将成为敏捷制造物流系统中的主要选择。
在非导向式AGV系统中,AGV的运行路径不需要由附加设备决定,而且当车间的布局变化后,只要及时改变规划系统的软件参数即可满足路径规划要求。
资料显示:在产品生产的整个过程中,仅仅有5%的时间是用于加工和制造,剩余的95%都用于储存、装卸、等待加工和输送:在美国,直接劳动成本所占比例不足生产成本的10%,且这一比例还在不断下降,而储存、运输所占的费用却占生产成本的40%.因此,目前世界各工业强国普遍把改造物流结构、降低物流成本作为企业在竞争中取胜的重要措施,为适应现代生产的需要,物流正在向着现代化的方向发展。
计算机控制自动导向小车(AGV)的设计与实现

计算机控制自动导向小车(AGV)的设计与实现计算机控制自动导向小车(AGV)的设计与实现一、引言近年来,随着工业自动化程度的提高,自动导向小车(Automated Guided Vehicle,简称AGV)在物流和生产线等领域得到了广泛应用。
AGV通过计算机控制实现智能导航和自动定位,具有工作效率高、成本低、灵活性好等优点,成为现代制造业中不可或缺的重要工具。
二、AGV系统架构1. 机械硬件:小车平台、驱动系统、传感器等组成物理框架。
2. 电气控制:电机驱动、位置测量、通信等关键电气元件。
3. 软件系统:控制算法、路径规划、决策逻辑等软件部分。
三、AGV导航技术1. 路标导航:在地面铺设路标或磁条,小车通过感应器读取路标信息实现位置定位和导航。
2. 惯性导航:利用加速度计、陀螺仪等惯性传感器感知小车的位姿变化,计算位姿信息并实现导航。
3. 视觉导航:利用摄像头采集环境图像,通过图像处理和识别算法实现导航和避障。
4. 激光导航:借助激光雷达感知环境,通过测量距离和位置实现导航。
四、AGV控制系统设计1. 功能设计:根据实际需求和使用场景确定小车的功能,如载货、拆卸、挤压等。
2. 系统模块设计:将功能分解为多个模块,如导航模块、路径规划模块、障碍物避免模块等。
3. 控制算法设计:根据不同导航技术选择相应的算法,如PID控制、遗传算法等。
4. 通信模块设计:实现小车与上位机、其他设备的通信,通过发送和接收指令实现控制。
五、实验与结果分析在实验中,我们设计了一个基于激光导航技术的AGV系统。
首先进行硬件组装,包括激光雷达的安装、电机驱动系统的安装等。
然后进行软件程序编写,包括传感器数据的读取、导航算法的实现等。
最后进行实验测试,通过设定目标点和路径规划,验证系统对于导航和避障的性能。
实验结果表明,我们设计的AGV系统能够准确地实现导航和避障功能。
激光雷达能够精确感知环境,路径规划算法能够高效地确定最佳路径,并通过电机驱动系统控制小车进行移动。
AGV自动导航车控制系统的设计与改进

AGV自动导航车控制系统的设计与改进AGV(Automated Guided Vehicle)自动导航车是一种用于物料运输和自动化生产的设备,其控制系统设计和改进对于提高AGV的性能和效率至关重要。
下面将介绍AGV控制系统的设计和改进,并提出一些关键的考虑因素和建议。
首先,AGV控制系统的设计应考虑以下几个关键因素:1.导航技术:AGV的导航技术可以使用多种方法,如激光导航、视觉导航、磁导航等。
根据实际需求和环境条件选择最适合的导航技术。
同时,控制系统应提供可靠的定位和导航算法,以实现精准的路径规划和导航功能。
2.避障系统:AGV在工作过程中需要避免碰撞障碍物,因此控制系统应配备可靠的避障算法和传感器。
例如,可以使用红外线、超声波或激光传感器来检测环境中的障碍物,并通过控制系统中的避障算法实时调整AGV的路径。
3.通信系统:AGV与其他设备和系统之间需要进行数据交互和通信,因此控制系统应具备稳定的通信功能。
可以使用无线网络或有线网络实现与其他设备的连接,同时控制系统应提供可靠的数据传输和通信协议,以保证数据的实时性和准确性。
其次,对于AGV控制系统的改进,可以考虑以下几个方面:1.系统集成:AGV控制系统一般包括导航、避障、通信、路径规划等功能,可以将这些功能进行系统集成,以减少系统的复杂性和提高系统的性能。
例如,可以使用嵌入式系统来实现多个功能的集成,以提高系统的灵活性和效率。
2.自动调整和路径优化:AGV在工作过程中可能会出现路径偏差或时间延迟等问题,可以通过控制系统进行自动调整和路径优化,以提高AGV的导航精度和运行效率。
例如,可以根据实际情况对路径进行动态调整和优化,以避免不必要的行驶距离和时间浪费。
3.传感器和算法的改进:控制系统的性能和效率很大程度上取决于传感器和算法的质量和可靠性。
因此,可以对传感器进行升级或改进,以提高对环境的感知能力;同时,可以对算法进行改进和优化,以提高AGV的导航和避障能力。
AGV小车设计方案改

机电一体化课程设计自动导引小车(AGV)设计方案小组成员:褚亚鹏柯健镪孙登强指导老师:***2014.6.19目录一、绪论 ............................................................................................. - 4 -1.1 AGV概述 ................................................................................. - 4 -1.2 AGV国内外研究现状.............................................................. - 6 -1.3 AGV的应用范围: ................................................................. - 9 -1.4 AGV的发展趋势分析:........................................................ - 11 -1.5 AGV的市场前景分析:........................................................ - 12 -二、总体方案设计 ........................................................................... - 14 -2.1 设计方案概述: ..................................................................... - 14 -2.2 传感器部分初步设计:.......................................................... - 14 -2.3 机械结构及驱动部分初步设计: .......................................... - 14 -2.4 控制部分初步设计:.............................................................. - 14 -三、传感器部分设计........................................................................ - 18 -四、机械结构及驱动部分设计 ........................................................ - 20 -4.1车体的设计: .......................................................................... - 20 -4.2车轮及转向装置选择:........................................................... - 20 -4.3电机的选择: .......................................................................... - 20 -4.4驱动部分校核计算:............................................................... - 24 -4.5蓄电池的选择: ...................................................................... - 25 -4.6总体机械结构设计及建模: ...................................................... - 27 -五、控制部分设计 ........................................................................... - 30 -5.1电源模块: .............................................................................. - 30 -5.2驱动模块 .................................................................................. - 30 -5.3循迹模块 .................................................................................. - 32 -5.4避障模块 .................................................................................. - 33 -5.5主控制模块 .............................................................................. - 34 -六、项目总结与感悟........................................................................ - 37 -七、参考文献 ................................................................................... - 39 -八、附录 ........................................................................................... - 40 -8.1 车体结构ANSYS仿真报告: .................................................... - 40 -Project ............................................................................................... - 40 -Contents ......................................................................................... - 41 -Units ............................................................................................... - 41 -Model (C4) ...................................................................................... - 41 -Geometry..................................................................................... - 41 -Coordinate Systems ..................................................................... - 53 -Connections ................................................................................. - 53 -Mesh ............................................................................................ - 67 -Static Structural (C5) ....................................................................... - 68 -Solution (C6) ................................................................................ - 71 -Material Data .................................................................................. - 73 -Structural Steel ............................................................................ - 73 -8.2 单片机控制程序: .................................................................... - 75 -一、绪论1.1 AGV概述(1)AGV的简介:根据美国物流协会定义,AGV(Automated Guided Vehicle)是指装备有电磁或光学导引装置,能够按照规定的导引路线行驶,具有小车运行和停车装置、安全保护装置以及具有各种移载功能的运输小车。
- 1、下载文档前请自行甄别文档内容的完整性,平台不提供额外的编辑、内容补充、找答案等附加服务。
- 2、"仅部分预览"的文档,不可在线预览部分如存在完整性等问题,可反馈申请退款(可完整预览的文档不适用该条件!)。
- 3、如文档侵犯您的权益,请联系客服反馈,我们会尽快为您处理(人工客服工作时间:9:00-18:30)。
目 录 摘 要……………………………………………………………………………… ABSTRACT………………………………………………………………………… 目 录……………………………………………………………………………… 第1章 绪论……………………………………………………………………… 第2章 AGV的总体设计…………………………………………………………… 第3章 AGV机械结构和驱动转向系统的设计…………………………………… 第4章控制系统与行走策略………………………………………………… 摘要:随着工厂自动化、计算机集成制造系统技术的逐步发展以及柔性制造系统、自动化立体仓库的广泛应用,AGV(Automatic Guided Vehicle)即自动导引车作为联系和调节离散型物流系统以使其作业连续化的必要的自动化搬运装卸手段,其应用范围和技术水平得到了迅猛的发展。 AGV是以微控制器为控制核心、蓄电池为动力、装有非接触导引装置的无人驾驶自动导引运载车,其自动作业的基本功能是导向行驶、认址停准和移交载荷。作为当代物流处理自动化的有效手段和柔性制造系统的关键设备,AGV已经得到了越来越广泛的应用,对AGV的研究也具有十分重要的理论意义和现实意义。 本文介绍了AGV在国内外的发展现状和应用情况,在此基础上,结合毕业设计的课题要求,设计了红外导引AGV小车。其研究内容主要包括以下几个方面: 1.论述了AGV系统的组成、路径导引方式及原理,结合课题要求,选择“红外导引”作为该系统的导引方式。 2.介绍了AGV车体机械结构的设计,并根据小车的驱动方式和工作要求,对底盘、电机、蓄电池等进行了设计和选型。 3.根据AGV系统的控制和工艺要求,确定了控制系统的总体框架结构。硬件方面,选择合适的传感器、单片机以及电机驱动器,对传感检测电路和 关键词:红外导引;AGV;单片机;驱动控制电路;行走策略;控制策略。
THE DESIGN OG AGV SYSTEM ABSTRACT With the growing of Factory Automation, Computer Integrated Manufacture System and extensive application of Flexible Manufacture System、Automatic Warehouse, the application field and technical level of AGV which contact and adjust the discrete logistics system, make the mission continuous, has greatly enlarged and improved. AGV is the unmanned driver automatic guided vehicle which has its untouched guided equipment, its control center is the microcontroller and storage battery is driving power, its basic function of automatic action is guided driving, recognizing the address to stop precisely and remove the load. As the valid measure of contemporary logistics processing automation and the key equipment of flexible manufacture system, the AGV has already got more and more extensive application, so that the research on AGV has very important theory meaning and realistic meaning. The dissertation introduced the applications and developments of AGV at home and abroad. Combining with the request of this graduation project topic, we designed a whole infrared rays guided vehicle. The main work in this dissertation was arranged as follows: 1. The constitution of AGV system, the path guided means and their principles were discussed. According to the requests of the topic, infrared rays guided method was used in the AGV system. 2. The design of AGV mechanical structure was introduced, in terms of driving manner and working requests, the type of the chassis, electrical motor and storage battery etc. was chosen and designed. 3. According to the control and the craftwork requests of the AGVS, the total frame structure of control system was designed. About hardware, the right sensor, MCU and motor controller had been chosen, the sensing circuits and MCU controlling hard circuits was designed, about software, to achieve many system functions, and to realize serial communication between the MCU and motor controller, blocking programming method was employed. Kywordse: Infrared rays guided; AGV; MCU; Drive and control circuit; Running strategy; Control strategy;Serial communication.
1. 绪 论 1.1 概述 AGV(Automatic Guided Vehicle)——自动导引车是上世纪50年代发展起来的智能搬运型机器人。AGV是现代工业自动化物流系统中的关键设备之一,它是以电池为动力,装备有电磁或光学等自动导航装置,能够独立自动寻址,并通过计算机系统控制,完成无人驾驶及作业的设备。自从1913年美国福特汽车公司使用有轨底盘装配车,1954年英国采用地下埋线电磁感应导向车以来,到九十年代全世界拥有AGV(Automated Guided Vehicles)10万台以上。近年来,自动化技术呈现加速发展的趋势,国内自动化立体仓库和自动化柔性装配线进入发展与普及阶段。其中,在自动仓库与生产车间之间,各工位之间,各段输送线之间,AGV起了无可替代的重要作用,与传统的传送辊道或传送带相比,AGV输送路线具有施工简单、路径灵活,不占用空间、较好的移动性、柔性等优点。 1.1.1国外研究状况 世界上第一台AGV是美国Basrrett电子公司于20世纪50年代开发成功的,它是一种牵引式小车系统。小车中有一个真空管组成的控制器,小车跟随一条钢丝索导引的路径行驶。 60年代和70年代初,除Basrrett公司以外,Webb和Clark公司在AGV市场中也占有相当的份额。在这个时期,欧洲的AGV技术发展较快,这是由于欧洲公司已经对托盘的尺寸与结构进行了标准化,统一尺寸的托盆促进了AGV的发展。欧洲的主要制造厂家有Schindler-Digitron, Wogner HJC, ACS, BT. CFC, FATA, Saxby, Denford和Blecbert等‘21。70年代中,欧洲约装备了520个AGV系统,共有4800台小车,1985年发展到一万台左右,为美、欧、日之首。在机械制造行业的应用为:汽车工业(57%),柔性制造系统FMS(8%)和柔性装配系统FAS(4%)。 欧洲的AGV技术于80年代初,通过在美国的欧洲公司以许可证与合资经营的方式转移到美国。芝加哥的Keebler分发中心从欧洲引进直接由计算机控制的AGV} 1981年John公司将AGV连接到AS/RS,以提供在制造过程中物料自动输送和跟踪。1984年,通用汽车公司便成为AGV的最大用户,1986年已达1407台(包括牵引式小车、叉式小车和单元装载小车),1987年又新增加1662台。美国各公司在欧洲技术的基础上将AGV发展到更为先进的水平。他们采用更先进的计算机控制系统(可联网于FMS或CIMS),运输量更大,移载时问更短,具有在线充电功能,以便24小时运行,小车和控制器可靠性更高‘31。此时美国的AGV生产厂商从23家(1983年)骤增至74家(1985年)。日本的第一家AGV工厂于1966年由一家运输设备供应厂与美国的Webb公司合资开设。到1988年,日本AGV制造厂已达20多家,如大福、Fanuc公司、Murata(村田)公司等。到1986年,日本己累计安装了2312个AGV系统,拥有5032台AGV。 1.1.2国内发展情况 六十年代开始研究; Š 七十年代北京起重运输机械研究所研制的ZDB-1型自动搬运车是最早的实用 型AGV; Š 八十年代邮电部设计研究院等单位先后开始对AGV进行研究与实践; Š 九十年代沈阳自动化所为沈阳金杯汽车公司总装线上设计的九台AGV自动装 配系统,是国内较先进的实用型AGV;