对动态优化设计的认识及其应用
优化设计概述

z第1章
内容
优化设计概述 优化方法的数学基础 一维搜索方法 无约束优化方法 约束优化方法 多目标优化 机械设计优化实例 MATLAB基础 MATLAB优化计算
2
第1篇 优化设计方法 Optimization
z第2章 z第3章 z第4章 z第5章 z第6章 z第7章 z第8章 z第9章
12
x2 ≥ 0 x3 ≥ 0 x1 x2 x3 = 100
11
数学模型
设计参数: 设计目标: 约束条件:
例3:直齿圆柱齿轮副的优化设计
x A , xB
max P = PA xA + PB xB
已知:传动比i, 转速n, 传动功率P,大小齿轮的材料,设 计该齿轮副,使其重量最轻。 分析: (1)圆柱齿轮的体积(v)与重量(w)的表达; (2)设计参数确定:模数m,齿宽b,齿数z1; (3)设计约束条件: (a)大齿轮满足弯曲强度要求; (b)小齿轮满足弯曲强度要求; (c)齿轮副满足接触疲劳强度要求; (d) 齿宽系数要求; (e) 最小齿数要求。 14
h( x ) = 0
(2)不等式约束
g ( x) ≤ 0
可行域 :凡满足所有约束 条件的设计点,它在设计 空间中的活动范围 . 约束函数有的可以表示成显式形式,即反映设 计变量之间明显的函数关系,有的只能表示成隐 式形式 ,如例中的复杂结构的性能约束函数(变 形、应力、频率等) 复杂结构的性能约束函数(变形、应力、固有 22 频率等)需要通过有限元等方法计算求得
图1-1 设计变量所组成的设计空间 (a)二维设计问题 (b)三维设计问题
目前已能解决200个设计变量的大型最优化设计问题。
19
20
2、约束条件
挖掘机动臂动态应力测试及优化设计

泛 应用 ,有 限元分析 、计 算 机 辅助 设 计 等现代 设 计 方
把 接 线架 及 应变 片按 图示 粘贴 到测试 点位 置 。贴
法 在 工程 机械 设 计领 域 得 到广泛 应用 。我公司挖 掘 机 片完成 以后对各贴片位 置进行 测量 并记录 。 动 臂综 合 使用 三维 建 模 、有 限元 分析 等先 进软 件设 计 1 . 焊接 接线 并测试 线路 .3 2 出来的。 但在 有 限元分 析三维 建模 时,一些模 型特 征 将 应变 片 和测试 线接 线 端分 别在 接 线架 上 焊 接 固 进 行 了简化 和处 理 ,况且 挖 掘 机 工作状 况 恶劣 ,在 挖 定 , 固定以后分别测量 应变 片两接 线焊接 点电阻值和测 掘过程 中承受很 大的交变 复合外力,极易受 到复杂 的瞬 试线测量仪接 口端两侧 电阻值 。 态冲 击 载荷 ,设 计 的产 品并不能够 完全 满足市场要 求。 因此 , 我们采用测量挖掘 机动臂工作状况下的动态应 力, 把 实 测数 据 与有 限元 分析 得 出的数 据 进行 比较 ,并 以 此 为基 础对 有 限元分 析 的模 型 参数 设 置进 行 修正,达 到有 限元 分析 和 实 际实验 结 果 相 符 合 的 目的,从 而提 供 更有 效的数 据对挖 掘机动臂进 行优化设计。
挖 掘 机 动 臂 动 态 应 力 测 试 及 优 化 设 计
Dyna i r s s nd O ptm i i e i n o m c St e sTe ta i z ng D s g n
t o ft c va o he Bo m o he Ex a t r
l 动臂的动态应 力测试
1 测 试 设备 . 1
将 结 构件 的微 观变 形 量转 化 为 电量 信号 ,同时将 电量 接 收和识别 的数字信 号进行 运算 和处理 。
工程优化设计的一般步骤

工程优化设计的一般步骤1.问题定义:确定优化设计的目标和限制条件。
在这一阶段,需要明确问题的目标,例如最小化成本、最大化利润、最大化产量等。
同时,还需确定优化设计的约束条件,例如资源限制、时间限制等。
通过明确问题目标和约束条件,可以为后续的优化设计提供有效的指导。
2.数据收集和验证:收集与问题相关的数据,并进行验证,确保数据的准确性和可靠性。
在这一阶段,需要确定所需的数据类型和数量,并通过可靠的方法进行数据采集。
同时,还需对数据进行验证和预处理,以排除错误和异常值的影响。
3.模型建立:根据问题定义和收集到的数据,建立适当的数学模型。
模型可以是线性或非线性的,可以是确定性或随机的。
根据实际情况和需求,选择适当的模型类型,并进行参数估计和模型验证。
4.参数优化:确定模型中的参数,并通过优化算法对参数进行估计。
常用的优化算法包括遗传算法、模拟退火算法、粒子群算法等。
通过调整模型的参数,可以使模型与实际情况更好地吻合,提高优化设计的准确性和可靠性。
5.约束条件优化:针对约束条件进行优化,以找到满足所有约束条件的最优解决方案。
常用的约束条件优化方法包括线性规划、非线性规划、整数规划等。
通过优化约束条件,可以使优化设计更符合实际需求,有效避免资源浪费和效果不佳的情况。
6.验证和分析:对优化设计的结果进行验证和分析。
通过与实际情况进行比较,评估优化设计的效果和可行性。
同时,还可以对优化设计的敏感性和稳定性进行分析,以了解其在不同条件下的性能表现。
7.结果展示和报告:将优化设计的结果以图表、报告等形式展示,并向相关人员和利益相关方进行沟通和汇报。
在报告中,应当明确说明优化设计的目标、方法和结果,以及可能存在的局限性和建议改进的方向。
8.反馈和改进:根据优化设计的结果和反馈意见,进行必要的改进和调整。
优化设计是一个动态的过程,需要不断地进行反馈和改进,以逐步提高优化效果。
总之,工程优化设计具有明确的步骤和方法,通过系统分析和模型建立,可以找到最优解决方案,提高工程项目的效率和经济性。
动态煤层气开采过程数值模拟与优化设计
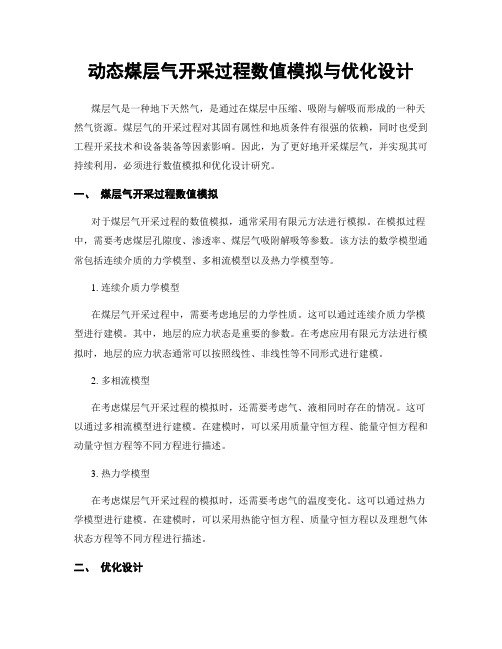
动态煤层气开采过程数值模拟与优化设计煤层气是一种地下天然气,是通过在煤层中压缩、吸附与解吸而形成的一种天然气资源。
煤层气的开采过程对其固有属性和地质条件有很强的依赖,同时也受到工程开采技术和设备装备等因素影响。
因此,为了更好地开采煤层气,并实现其可持续利用,必须进行数值模拟和优化设计研究。
一、煤层气开采过程数值模拟对于煤层气开采过程的数值模拟,通常采用有限元方法进行模拟。
在模拟过程中,需要考虑煤层孔隙度、渗透率、煤层气吸附解吸等参数。
该方法的数学模型通常包括连续介质的力学模型、多相流模型以及热力学模型等。
1. 连续介质力学模型在煤层气开采过程中,需要考虑地层的力学性质。
这可以通过连续介质力学模型进行建模。
其中,地层的应力状态是重要的参数。
在考虑应用有限元方法进行模拟时,地层的应力状态通常可以按照线性、非线性等不同形式进行建模。
2. 多相流模型在考虑煤层气开采过程的模拟时,还需要考虑气、液相同时存在的情况。
这可以通过多相流模型进行建模。
在建模时,可以采用质量守恒方程、能量守恒方程和动量守恒方程等不同方程进行描述。
3. 热力学模型在考虑煤层气开采过程的模拟时,还需要考虑气的温度变化。
这可以通过热力学模型进行建模。
在建模时,可以采用热能守恒方程、质量守恒方程以及理想气体状态方程等不同方程进行描述。
二、优化设计对于煤层气开采过程的优化设计,主要包括井网结构设计、注采方案设计和生产运营方案设计等。
1. 井网结构设计井网结构是指煤层气开采时地下各个井之间的联系结构。
井网结构设计的主要目的是最大化地提高煤层气开采效率,并减少煤层气开采过程的成本。
在进行井网结构设计时,需要考虑煤层气在地下的分布状况、开采技术和设备装备等因素。
2. 注采方案设计注采方案指开采过程中液态水和气体之间的注入和回收。
注采方案设计的主要目的是使液态水和气体之间达到最佳配比,以达到最高的采收率。
在进行注采方案设计时,需要考虑地层的物理性质、煤层气的产量和采收率等因素。
基于模态分析的结构优化设计

基于模态分析的结构优化设计一、引言结构优化设计是工程领域中的一项重要任务,其目的是通过提高结构的性能和效率,使之更加符合设计要求。
传统的结构优化设计往往是基于某个特定负载情况下的最小重量或最大刚度为目标,但实际工程中结构的工作条件和需求多样化,仅考虑单一因素往往不能得到最佳设计。
因此,基于模态分析的结构优化设计成为了一种有效的方法。
二、模态分析的基本原理模态分析是一种通过计算结构的固有频率和固有振型来研究结构动力学性能的方法。
在模态分析中,结构可以看作是由多个模态共同组成的,每个模态都具有自己的振动频率和振型形态。
通过模态分析,我们可以了解到结构的动态响应特性,如固有频率、振动模态和结构的动力特性等。
三、模态分析在结构优化设计中的应用1. 确定结构的固有频率:通过模态分析可以获得结构的固有频率,进而了解结构的振动特性。
在结构优化设计中,我们可以通过调整结构的几何形态或材料的性质来改变结构的固有频率,以满足工程要求。
2. 优化结构的振动模态:在模态分析中,我们可以观察和分析各个模态的振动模态,了解结构的不同部分的振动情况。
通过优化设计,可以调整结构的刚度和几何形态,使得结构的振动模态分布合理,减小结构的振动幅值和振动频率。
3. 提高结构的动态稳定性:模态分析还可以帮助我们评估结构的动态稳定性。
通过分析结构的振动模态,可以判断结构的临界振型和临界振频,为预防结构的失稳提供依据。
在优化设计中,可以通过增加结构的刚度或改变结构的几何形态,提高结构的动态稳定性。
四、应用实例以桥梁结构为例,结构的动力性能对于桥梁的安全性和使用寿命具有重要影响。
在结构优化设计中,可以利用模态分析方法对桥梁结构进行优化。
首先,通过模态分析确定桥梁的固有频率。
根据桥梁的设计要求和预期使用情况,可以确定合理的固有频率范围。
如果桥梁的固有频率偏低,可能会导致结构的动态响应大,增加了结构的疲劳破坏的风险;如果固有频率过高,可能会造成结构的共振问题,降低结构的稳定性。
《冲击载荷下结构拓扑优化设计与动态响应分析》

《冲击载荷下结构拓扑优化设计与动态响应分析》篇一一、引言随着现代工程技术的快速发展,结构拓扑优化设计在冲击载荷下的应用日益受到关注。
结构在承受冲击载荷时,其拓扑优化设计对于提高结构的稳定性和耐久性具有重要意义。
本文旨在探讨冲击载荷下结构拓扑优化设计的方法,并对其动态响应进行分析,以期为相关领域的研究和应用提供参考。
二、结构拓扑优化设计1. 优化目标与约束在冲击载荷下,结构拓扑优化设计的目标是在满足一定的约束条件下,使结构在承受冲击时的性能达到最优。
约束条件包括结构的质量、材料、尺寸等。
优化目标则主要包括结构的动态响应、稳定性、耐久性等。
2. 优化方法针对冲击载荷下的结构拓扑优化设计,常用的方法包括基于均匀化方法的拓扑优化、基于水平集方法的拓扑优化等。
这些方法可以通过数学规划、有限元分析等手段,对结构进行优化设计。
3. 实例分析以某桥梁结构为例,采用拓扑优化方法对其在冲击载荷下的结构进行优化设计。
通过有限元分析,确定结构的应力分布、位移等动态响应参数,进而对结构进行优化设计。
优化后的结构在承受冲击时,其动态响应性能得到显著提高。
三、动态响应分析1. 分析方法动态响应分析主要采用有限元分析方法。
通过建立结构的有限元模型,对结构在冲击载荷下的应力、位移、振动等动态响应进行计算和分析。
2. 分析步骤动态响应分析的步骤包括建立有限元模型、施加冲击载荷、求解动态响应等。
在建立有限元模型时,需要考虑结构的几何尺寸、材料属性、连接方式等因素。
在施加冲击载荷时,需要确定载荷的大小、方向、作用位置等。
通过求解动态响应,可以得到结构的应力分布、位移等参数。
3. 分析结果以某汽车碰撞事故为例,通过动态响应分析,可以得出结构在碰撞过程中的应力分布、位移等参数。
这些参数对于评估结构的稳定性和耐久性具有重要意义。
同时,通过对不同结构方案的动态响应进行比较,可以为结构的优化设计提供参考。
四、结论与展望本文针对冲击载荷下结构拓扑优化设计与动态响应分析进行了探讨。
凸轮优化设计解析

一.配气凸轮优化设计1.1配气凸轮结构形式及特点配气凸轮是决定配气机构工作性能的关键零件,如何设计和加工出具有合理型线的凸轮轴是整个配气系统设计中最为重要的问题。
对内燃机气门通过能力的要求,实际上就是对由凸轮外形所决定的气门升程规律的要求,气门开启迅速就能增大时面值,但这将导致气门机构运动件的加速度和惯性负荷增大,冲击、振动加剧、机构动力特性变差。
因此,对气门通过能力的要求与机构动力特性的要求间存在一定矛盾,应该观察所设计发动机的特点,如发动机工作转速、性能要求、配气机构刚度大小等,主要在凸轮外形设计中兼顾解决发动机配气凸轮外形的设计也就是对凸轮从动件运动规律的设计。
从动件升程规律的微小差异会引起加速度规律的很大变动,在确定从动件运动规律时,加速度运动规律最为重要,通常用其基本工作段运动规律来命名,一般有下面几种:1.1.1等加速凸轮等加速凸轮的特点是其加速度分布采取分段为常数的形式,其中又可分为两类,一类可称为“正负零型”,指其相应的挺柱加速度曲线为正一负一零:另一类可称“正零负型”,指其加速度曲线为正一零一负。
当不考虑配气机构的弹性变形时,对最大正负加速度值做一定限制且在最大升程、初速度相同的各种凸轮中,这种型式的凸轮所能达到的时面值最大。
等加速型凸轮常常适用于平稳性易保证,而充气性能较差的中低速柴油机中。
但就实际情况而言,配气机构并非完全刚性,等加速凸轮加速度曲线的间断性必然会影响机构工作平稳性,在高速内燃机中一般不采用等加速型凸轮[9]1.1.2组合多项式型组合多项式型凸轮的基本段为一分段函数,它由几个不同的表达式拼接而成。
通过调整各段所占角度及函数方程,获得不同斜率的加速度曲线。
组合多项式型凸轮时面值大,而且能够方便地控制加速度变化率及确保正、负加速段间的圆滑过渡,可以较好地协调发动机充气性能及配气机构工作平稳性的要求⑺。
由于凸轮从动件运动规律由若干函数组成,在各段间联结点处不易保证升程规律三阶以上导数的连续性,可能会影响配气机构工作的平稳性,组合多项式型凸轮主要应用在要求气门时面值大和较好动力性能的情形。
优化设计方法ppt
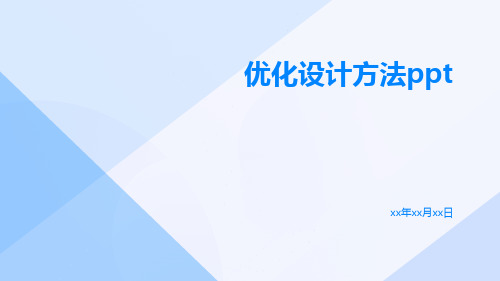
其他优化方法
粒子群优化算法
粒子群优化算法是一种基于群体智能的优化算法,通过模拟 鸟群、鱼群等自然现象的群体行为来寻找最优解。
人工神经网络
人工神经网络是一种模拟人脑神经元网络结构的计算模型, 通过训练来逼近某个映射函数或分类器。
03
优化设计的实际应用
建筑设计的优化
总结词
提高功能性、美观性和经济性
优化设计方法ppt
xx年xx月xx日
目录
• 引言 • 优化设计的基本方法 • 优化设计的实际应用 • 优化设计的新发展 • 优化设计的实践技巧
01
引言
什么是优化设计
优化设计是一种通过合理选择和调整设计方案参数,在给定 的一组约束条件下,使设计性能指标达到最优化的方法。
优化设计旨在找到一个或多个最优解,使设计在满足各种约 束条件的同时,最大化或最小化某一特定的设计性能指标。
迭代次数设置
合理设置迭代次数,避免 因迭代次数过多或过少导 致收敛效果不佳。
收敛条件设置
合理设置收敛条件,以便 在满足条件时实现算法收 敛。
初始化参数设置
合理设置初始化参数,避 免算法过早收敛或无法收 敛。
如何避免优化过程中的局部最优解
随机初始化
通过随机初始化参数,避 免算法在初始阶段就陷入 局部最优解。
适应性。
自适应选择
自适应选择是根据问题的特征和 性质,自适应地选择不同的算法 或策略,以获得更好的性能和适 应性。
自适应学习
自适应学习是通过学习历史经验和 数据,自适应地调整算法参数和策 略,以适应不同的情况和问题,提 高算法的效率和精度。
05
优化设计的实践技巧
如何选择合适的优化方法
根据问题特性选择
- 1、下载文档前请自行甄别文档内容的完整性,平台不提供额外的编辑、内容补充、找答案等附加服务。
- 2、"仅部分预览"的文档,不可在线预览部分如存在完整性等问题,可反馈申请退款(可完整预览的文档不适用该条件!)。
- 3、如文档侵犯您的权益,请联系客服反馈,我们会尽快为您处理(人工客服工作时间:9:00-18:30)。
对动态优化设计的认识及其应用 对动态优化设计的认识及其应用
摘要:在学习了动态优化设计理论后,查阅了相关资料,了解了动态优化设计
理论在机械工程中的应用。本文以前人的几个比较有代表性研究成果来说明动态优化设计在机械工程中的应用。
关键字:动态优化设计,摆动活齿传动机构,振动筛,高速凸轮机构 1.引言 现代机械动态优化设计是在产品的研究和开发过程中,对机械产品的运动学和动力学及与此相关的动态可靠性、安全性、疲劳强度和工作寿命等问题,进行分析和计算,以保证所研究和开发的设备具有优良的结构性能及其他相关性能。动态优化设计是产品设计的核心内容,它既有广度和深度,而且也有相当大的难度[1]。 随着科学技术的迅速发展,机械动态设计的内容,其广度与深度及所研究的对象正在发生深刻的变化。总体上可以分为以下三个发展方向:1)就研究的广度而言,研究内容已由狭义的向广义的方向发展,由此,机械动态设计按其涵盖的内容的广度可分为一下两类:狭义动态设计和广义动态设计。狭义的机械动态设计是以机器中的结构型零部件为研究对象,以线性动力有限元为手段,采用理论研究和模型试验相结合的方法,找出产品初步设计中的缺陷和问题,进而对零部件或结构进行动力修改,避免结构在工作发生共振和出现不稳定振动。广义的动态设计包括机器工作工程中发生的运动学、动力学等与动态特性有关的所有设计内容;2)由传统的动态优化设计向深层次的动态优化设计发展。传统的动态优化设计法是以提高产品结构性能为主要目标、以线性动力学理论为基础的动态优化设计法。具体地说,它的主要目的是使机器获得优良的结构性能,其中包括产品的系统可靠性、人机安全性、工作耐久性、结构紧凑性、造型艺术性、无环境污染性和设计经济性,以及其他的性关性能,如功效实用性、运行稳定性、操作宜人性、维修方便性等。深层次的动态优化设计与传统 的动态优化设计的区别是它以非线性动力学理论为基础,即:以非线性动力学理论为基础的动态设计和已非线性可靠性理论为基础的机器及其零部件可靠性设计;3)从一般机械的动态设计扩展到包括振动机械在内的动态设计[1]。 由于机械结构形式及功能的区别,机械动态设计的内容会有所不同。机械动态设计的一般过程为[2]: 1) 根据设计或实物进行动力学建模; 2) 按照所建立的动力学模型计算系统的动态特性并对初步设计进行审核。机械系统的动态特性通常指该机械系统的固有频率、固有振型及其在激振力作用下的响应; 3) 实物或模型试验与实验建模; 4) 根据初步计算结果和实验数据,对机械结构进行动力修改。 机械结构动态设计的关键技术有:结构结合部参数的辨识;系统中阻尼矩阵的确定;模型的修正方法;以设计变量直接作为优化变量,实现结构动力学的求解方法;寻求更快速、更准确的结构动态特性重分析模型与方法[3]。 本文以前人的几个比较有代表性的研究成果:摆动活齿传动机构[4]、振动筛 [5]、高速凸轮机构 [6]为例说明动态优化设计理论在工程实际中的应用。
2. 基于振动理论的摆动活齿传动机构动态优化设计 摆动活齿传动是一种新型活齿少齿差行星传动,具有传动比范围广、传动效率高、承载能力强和结构紧凑等优点。近几年,随着科学技术的进步和发展,高速重载和新型机械传动机构的应用越来越广,人们对机械传动的动态性能要求也越来越高,特别是对机械振动和噪声的控制要求更为突出。
2.1 摆动活齿传动的结构及传动原理 图la为摆动活齿传动机构的结构简图,偏心激波器1、活齿2、活齿架3、销轴4、中心轮5,其中活齿架3与输出轴固联,活齿2与激波器1和中心轮5分别形成啮合副,活齿架3与活齿2通过销轴4以转动副连接。机构的结构参数和传动原理如图1b所示,其中a为激波器偏心距,b为激波器与活齿的半径之和,c为活齿偏心距,d为活齿架上铰链分布圆半径,ABOO1为摆动活齿传动机构的等效机构—— 曲柄摇杆机构。 偏心激波器1(输入轴)以1等速转动,推动活齿2运动,在固定中心轮5齿廓约束下,通过销轴4反推活齿架3(输出轴)以3转动,从而实现摆动活齿传动输入轴和输出轴的速度变换。
(a) (b) 图1 摆动活齿传动机构的结构和等效机构图
2.2 摆动活齿传动扭转振动模型
图2 摆动活齿传动扭转振动模型 根据摆动活齿传动的动力学特点,应用等效集中参数的建模方法,建立了摆动活齿传动系统的扭转振动模型,如图2所示。其中1J为激波器的转动惯量,
2J为活齿架的转动惯量,iJ2为第i个活齿的转动惯量(i=1,2,3,…,n;n为
活齿数一半),ik1和ic1分别表示激波器与第i个活齿的啮合刚度和阻尼,ik5和ic5
分别表示中心轮与第i个活齿的啮合刚度和阻尼,ik4和ic4 分别表示销轴与第i 个活齿的啮合刚度和阻尼,1T和4T分别为输入转矩和输出转矩。 考虑到活齿的时变啮合刚度和啮合阻尼,建立传动机构的多自由度、变系数、非线性二阶动力学微分方程,其矩阵形式表示为:
)(...tFKCJ (1)
式中:,,...—分别为扭转振动角加速度、角速度和角位移列向量; J—转动惯量矩阵; C—扭转振动阻尼矩阵; K—扭转振动刚度矩阵; F(t)—系统外载荷列向量。
2.3 摆动活齿传动机构动态优化设计建模 建立的振动方程为二阶非线性振动微分方程,应用Runge—Kutta数值方法求出一个振动周期内的振动角位移、角速度.和角加速度..的离散值,利用Matlab软件进行动态优化设计,求解摆动活齿传动机构系统的动态响应。 以摆动活齿传动一个运动周期内的活齿振动角加速度的均方根值最小为目标函数f( X),即:
NXfNii/)(1.. (2)
式中:N— 一个啮合周期内的等分点数; ..i— 活齿任意时刻的角加速度。
根据图1b所示,影响机构动力学性能的独立参数有o,b,c,d和活齿半径zr,因此优化设计变量为: zTrdcbaxxxxxX,,,,,,,,54321 (3)
曲柄存在条件的约束为:
bcdadbcadcbadacaba,,,,
(4)
运动干涉约束: 02/02/2111zzrbddarddba
(5)
式中:1d—活齿柱销直径; 1—构件间的运动间隙; 2—构件间的运动间隙。 连续传动约束 02z (6)
式中: z— 活齿数 活齿偏心距约束:
zrdc2/1 (7) 相邻活齿销间距约束: 02sin22drcz (8)
强度约束:
01.32701.32721maxzLza
T
rLzaTz (9)
式中:T— 输入力矩; L— 活齿工作长度; 1— 活齿与激波器啮合副的许用应力;
maxz—z活齿与中心轮作用力系数的最大值;
2
— 活齿中心轮啮合副的许用接触应
力。 设计变量上下界约束: unnLnxxx (n=1,…,5) (10)
式中:unLnxx,— 各设计变量上下界 3. 基于动态优化设计方法振动筛设计 为了分析该系统的动态特性,振动筛简化成如图3所示具有3个自由度系统模型。机体(包括偏心块)的质量和绕质心的转动惯量分别为m和J,基于拉格朗日方程法求解该系统的振动运动微分方程,其具体形式为:
QKXXCXM... (11)
式中:M,C,K,Q— 分别为质量矩阵,阻尼矩阵,刚度矩阵,干扰力矩阵
图3 振动筛系统模型 因为筛体的具体结构比较复杂,所以在动力学分析的数值计算中,直接求质量阵M和刚度阵K就显得比较困难。这里借助于软件Pro/E和AutoCAD求解,得到质量矩阵M和刚度矩阵K。 基于振动筛的动态特性理论和利用Matlab软件编程进行数值求解。根据以上计算结果,求得系统的固有频率及振型向量和系统的响应。 经计算,得出该振动系统的响应(幅值单位为m)
)sin(53374628204001.000243215081004.009463417535004.0tyxX (12) 24
激振力修正前的系统 x、y方向的响应曲线如图4所示。 图4 激振力修正前的系统响应曲线 1.激振力修正前的系统x方向的响应曲线 2.激振力修正前的系统y方向的响应曲线 很显然,筛体的振幅并没有达到5.5 mm要求,这说明系统的激振力偏大。为此需要对激振力进行修正,设修正参数为n,通过数值计算程序试验,可以得出当n=0.901 441 569 374 04时,筛体的振幅m3'105.5与筛体的要求振幅m3105.5正好相等,说明此时刚好达到要求。修正后的激振力
kNnFFn608.67', kNFn75为厂方提供的一套激振器力数值。从计算结果来看,激振器需要进行改动,以使筛体达到要求的振幅。 激振力修正后,系统x、y方向的响应(幅值单位为m)
)sin(45092902085001.061073977678003.069835413088004.0tyxX (13) 激振力修正后的系统 x、y方向的响应曲线如图5
图4 激振力修正后的系统响应曲线