柴油非加氢脱氮技术研究进展o
柴油加氢改质装置节能降耗技术分析与对策

柴油加氢改质装置节能降耗技术分析与对策柴油加氢改质装置是一种用于提高柴油质量的技术装置。
通过加氢作用,可以将柴油中的硫、氮、氧等杂质降低,减少烯烃、芳香烃等不饱和化合物的含量,提高柴油的稳定性和抗氧化性能,从而降低排放物的含量,减少环境污染。
柴油加氢改质过程中也存在一些能量损耗的问题,为了提高柴油加氢装置的能源利用效率,降低能耗,可以采取以下技术对策:1. 提高催化剂活性:催化剂是柴油加氢过程中的关键组成部分,可以采用新型高活性催化剂,提高催化剂的活性,减少反应温度和压力,降低能耗。
2. 优化反应工艺条件:在柴油加氢过程中,可以通过优化反应温度、压力和进料速率等工艺条件,使得加氢反应更加充分,提高反应转化率,降低副反应和能耗。
3. 应用新型装置结构:传统的柴油加氢装置结构比较复杂,存在能量损耗的问题,可以采用新型装置结构,如流化床、旋转床等,提高柴油与催化剂之间的接触效果,降低能耗。
4. 应用热集成技术:热集成技术是一种将不同温度的流体进行热交换以实现能量回收的技术,可以应用于柴油加氢装置中,将高温废热回收利用,提高能源利用效率。
5. 应用催化剂再生技术:柴油加氢过程中,催化剂活性会逐渐下降,需要定期进行催化剂再生,传统的再生方法存在能量损耗的问题,可以采用新型催化剂再生技术,如超声波催化剂再生技术、微波催化剂再生技术等,降低能耗。
柴油加氢改质装置的节能降耗技术可以从提高催化剂活性、优化反应工艺条件、应用新型装置结构、应用热集成技术和应用催化剂再生技术等方面入手,以提高能源利用效率,降低能耗。
这些技术对策的应用将有助于推动柴油加氢改质装置技术的发展和应用,实现柴油质量的提升和环境污染的降低。
柴油加氢流程
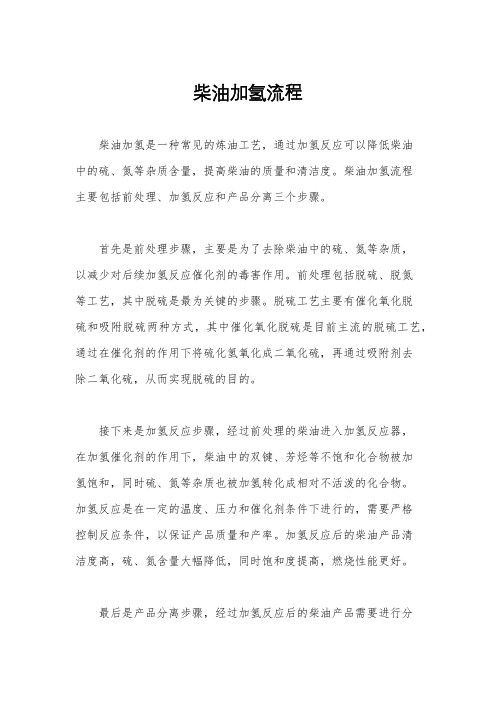
柴油加氢流程
柴油加氢是一种常见的炼油工艺,通过加氢反应可以降低柴油
中的硫、氮等杂质含量,提高柴油的质量和清洁度。
柴油加氢流程
主要包括前处理、加氢反应和产品分离三个步骤。
首先是前处理步骤,主要是为了去除柴油中的硫、氮等杂质,
以减少对后续加氢反应催化剂的毒害作用。
前处理包括脱硫、脱氮
等工艺,其中脱硫是最为关键的步骤。
脱硫工艺主要有催化氧化脱
硫和吸附脱硫两种方式,其中催化氧化脱硫是目前主流的脱硫工艺,通过在催化剂的作用下将硫化氢氧化成二氧化硫,再通过吸附剂去
除二氧化硫,从而实现脱硫的目的。
接下来是加氢反应步骤,经过前处理的柴油进入加氢反应器,
在加氢催化剂的作用下,柴油中的双键、芳烃等不饱和化合物被加
氢饱和,同时硫、氮等杂质也被加氢转化成相对不活泼的化合物。
加氢反应是在一定的温度、压力和催化剂条件下进行的,需要严格
控制反应条件,以保证产品质量和产率。
加氢反应后的柴油产品清
洁度高,硫、氮含量大幅降低,同时饱和度提高,燃烧性能更好。
最后是产品分离步骤,经过加氢反应后的柴油产品需要进行分
离和精制,以得到符合要求的成品柴油。
产品分离主要包括闪蒸、精馏、萃取等工艺,通过这些工艺可以分离出不同馏分的柴油,并对柴油进行精制,去除残留的杂质和重质组分,最终得到高品质的成品柴油。
总的来说,柴油加氢流程是一个复杂的工艺过程,需要多种工艺步骤的配合和严格的操作控制,才能实现对柴油的清洁化和提质改良。
随着环保要求的提高和市场对清洁能源的需求增加,柴油加氢技术将会得到更广泛的应用和发展,为炼油行业的可持续发展提供更多可能性。
几种催化柴油加氢改质技术
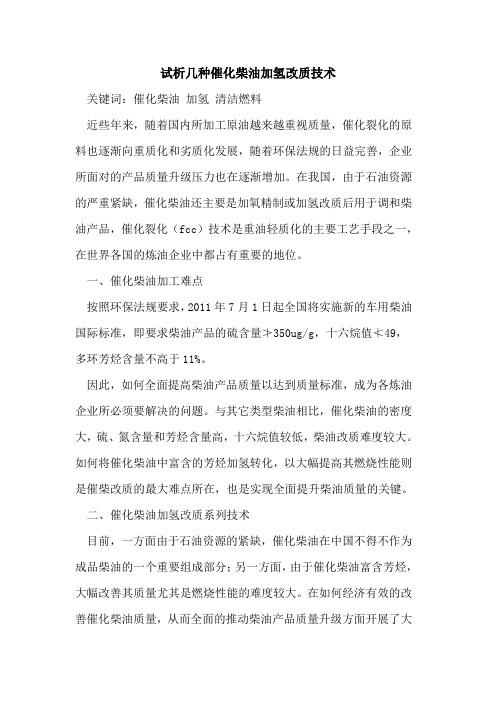
试析几种催化柴油加氢改质技术关键词:催化柴油加氢清洁燃料近些年来,随着国内所加工原油越来越重视质量,催化裂化的原料也逐渐向重质化和劣质化发展,随着环保法规的日益完善,企业所面对的产品质量升级压力也在逐渐增加。
在我国,由于石油资源的严重紧缺,催化柴油还主要是加氧精制或加氢改质后用于调和柴油产品,催化裂化(fcc)技术是重油轻质化的主要工艺手段之一,在世界各国的炼油企业中都占有重要的地位。
一、催化柴油加工难点按照环保法规要求,2011年7月1日起全国将实施新的车用柴油国际标准,即要求柴油产品的硫含量≯350ug/g,十六烷值≮49,多环芳烃含量不高于11%。
因此,如何全面提高柴油产品质量以达到质量标准,成为各炼油企业所必须要解决的问题。
与其它类型柴油相比,催化柴油的密度大,硫、氮含量和芳烃含量高,十六烷值较低,柴油改质难度较大。
如何将催化柴油中富含的芳烃加氢转化,以大幅提高其燃烧性能则是催柴改质的最大难点所在,也是实现全面提升柴油质量的关键。
二、催化柴油加氢改质系列技术目前,一方面由于石油资源的紧缺,催化柴油在中国不得不作为成品柴油的一个重要组成部分;另一方面,由于催化柴油富含芳烃,大幅改善其质量尤其是燃烧性能的难度较大。
在如何经济有效的改善催化柴油质量,从而全面的推动柴油产品质量升级方面开展了大量的研究工作。
开发了系列催化柴油加工技术,以适应用户的不同需求。
一下就介绍几种加氢技术的主要生产技术与特点。
1.加氢精制技术对于某些直馏柴油、焦化柴油在整体柴油中所占比例较大,而催化柴油占比例较小的企业来说,采用加氢精制方法加工混合柴油是一条全面提升柴油质量的最简单、可行的方法。
采用加氢精制技术加工催化柴油,生产符合环保法规清洁柴油的技术,适用于直馏柴油、焦化柴油所占比例大,催化柴油所占比例小,柴油十六烷值矛盾不突出的企业选用,其技术特点总结如下:1.1所开发的深度脱硫系列催化剂有较强的加氢脱硫性能,基本可以满足用户生产低硫清洁柴油的需求。
柴油加氢装置(汽柴油生产技术课件)
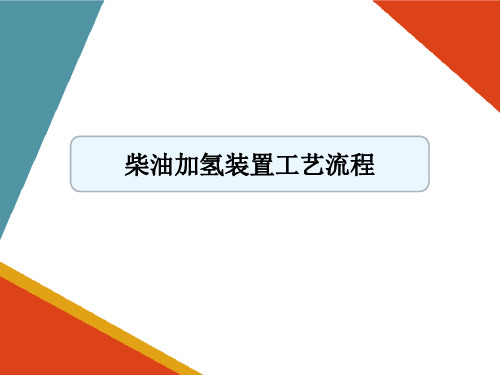
高分罐
LIC 排污
循环氢
LI 低分罐
图5—9 高分罐液位控制示意图
高分罐液位是油相液面高度。偏
高油相和气相分离效果将下降,偏低易形 成高压串低压导致分馏塔操作紊乱。
高分罐界位是水相与油相的界面
高度。偏高油带水,偏低水带油。
高分罐液位的影响因素:
1、高分罐与低分罐压差变化; 2、原料泵出口流量变化; 3、高分罐温度变化。
精制柴油十六烷值偏低,说明反应没有达到部分达到了第2步反应, 也即反应深度不够工艺要求。
1、反应温度偏低; 2、反应压力偏低;
3、催化剂活性偏低; 4、空速偏大。
1、塔顶压力偏 低; 2、塔顶温度偏 高;
精制油从低分罐来 原料泵
回流罐 粗汽油
分 馏 塔
粗汽油干点偏高?
柴油出装置
塔底的轻组分没有气化 上升到塔顶:
低分气
高
分
罐
低
分
分
馏
罐
塔
图5—10 低分罐压力控制示意图
低分罐的作用,一是分担些分馏塔
顶负荷,再是环节高压直接到低压而导致 分离塔的操作紊乱。
低分罐压力的影响因素:
1、高分罐压力变化; 2、分馏塔压力变化; 3、低分罐顶气体出口流量变化; 4、低分罐出口换热器的压降变化。
低分气
从高分罐来 低分罐
石脑油去催化重整装置
分
馏
塔
精制柴油溴价不合格的原
因?
柴油出装置
精制油从低分罐来 原料泵
回流罐
石脑油去催化重整装置
分馏Βιβλιοθήκη 塔精制柴油硫含量超标?
柴油出装置
循环氢压缩机
2、高分罐排污力度 不够工艺要求
新氢
柴油加氢改质装置节能降耗技术分析与对策

柴油加氢改质装置节能降耗技术分析与对策一、柴油加氢改质装置的技术原理柴油加氢改质装置,简称加氢装置,是通过在柴油发动机的进气道中加入氢气,利用氢气与柴油混合燃烧,从而提高燃烧效率,减少尾气排放,降低燃油消耗的一种技术手段。
其技术原理主要包括以下几个方面:1. 燃烧效率提高:通过向柴油中加入氢气,可以使得燃油在燃烧过程中更加充分,提高燃烧效率,从而减少燃油的消耗。
2. 尾气排放降低:氢气在燃烧过程中可以与氧气充分混合,从而减少燃烧产生的有害气体,降低尾气排放。
3. 发动机功率提升:利用氢气的高热值特性,可以提高柴油发动机的实际功率输出,实现动力提升的效果。
2. 排放水平降低:氢气的加入可以改善柴油发动机的燃烧过程,减少有害气体的排放,对环境保护具有显著效果。
在实际应用柴油加氢改质装置时,需要克服一些技术难题,从而实现更好的节能降耗效果。
以下是针对柴油加氢改质装置的技术对策:1. 加氢装置的稳定性:加氢装置在柴油发动机中的工作稳定性是关键,需要解决在车辆长时间运行或在极端环境下出现的稳定性问题。
2. 加氢装置的安全性:在加氢改质过程中,需要保证氢气供应系统的安全和稳定,避免出现安全隐患。
3. 加氢装置的成本控制:加氢装置需要在成本可控的基础上提供良好的节能降耗效果,因此需要在技术和成本的平衡上进行合理的控制。
4. 加氢装置与柴油发动机的匹配问题:加氢装置需要与柴油发动机良好的匹配,保证在不影响发动机正常工作的情况下提供更好的节能降耗效果。
四、结语柴油加氢改质装置的节能降耗技术具有很大的应用前景,需要不断进行技术创新和实践应用,从而为我国能源资源的可持续发展作出更大的贡献。
柴油加氢技术总结

柴油加氢技术总结2#柴油加氢装置开工总结宋火军1.开工前的准备1.1 学习装置理论知识生产低硫、低芳烃、低密度、高十六烷值得清洁柴油是今后世界范围内的柴油生产总趋势。
如何满足符合日趋苛刻的车用柴油标准,生产出符合环保要求的清洁柴油将成为炼油技术进步的一个重要课题。
柴油燃料质量升级的趋势与汽油类似,最主要的是对于硫含量的控制,同时对于柴油产品指标中的十六烷值、芳烃含量、冷流动性、密度等也提出了更为严格的要求。
二次加工的柴油含有相当多的硫、氮及烯烃类物质,油品质量差,安定性不好,储存过程容易变质,对直馏柴油而言,由于原油中硫含量升高,环保法规日趋严格,已经不能直接作为产品出厂,也需要经过加氢精制处理。
柴油加氢精制的生产原理就是在一定温度、压力、氢油比、空速条件下,借助加氢精制催化剂的作用,有效的使油品中的硫、氮、氧、非烃类化合物转化为响应的烃类和H2S、NH3和H2O。
另外,少量的重金属则截留在催化剂中,同时使烯烃和部分芳烃饱和,从而得到安定性、燃烧性、情节性都较好的优质柴油产品和粗汽油(裂解料)。
本装置中大量循环氢的存在能保证气相为连续相,液相为分散相,被气相打散的液相在固定床催化剂上从上至下以液滴的形态流过催化剂床层,从而发生一系列的加氢反应。
循环氢在其中的关键作用是:(1)维持反应所需的氢分压,用来维系气相中的氢气向油相溶解的推动力。
(2)控制催化剂床层的温升。
(3)稀释反应物流杂质的浓度,促进深度脱杂质的反应。
1.2 学习开工方案在开工前两个月,车间开始组织操作人员学习开工方案,让每个人对开工都心里有数,了解每一个步骤,提高了操作人员的操作水平,为这次成功的开工打下了基础。
1.3 联系调度,提供合格氮气,在系统催化剂干燥时能满足供应。
1.4 硫化剂与试车用直馏柴油准备充足。
2.催化剂干燥催化剂在包装、储运和装填中,都难免吸附一定水分,吸附水会降低催化剂的活性和强度。
因此催化剂要在预硫化前进行脱水。
柴油液相加氢过程中化学氢耗的研究
柴油液相加氢过程中化学氢耗的研究程杰;相春娥;刘宾;柴永明;赵秀文;王德会;刘晨光【摘要】在上流式固定床加氢中试实验装置上对柴油液相加氢过程中的化学氢耗进行研究,根据不同反应物的加氢反应方程推导出不同加氢反应的氢耗计算式,并建立了氢耗动力学模型.研究发现,在上流式柴油液相加氢过程中,前段催化剂床层的化学氢耗远远大于后段催化剂床层,70%的化学氢耗集中在前20%的催化剂床层上,从而导致后段床层H2浓度过低而影响加氢反应的进行;在进料量200 mL/h、氢/油质量比4.244×10-3、反应温度350℃和反应压力8 MPa条件下,化学氢耗计算值与实测值的平均相对误差为2.11%,表明推导的氢耗计算式准确、可靠;建立的氢耗动力学模型在预测化学氢耗时的相对误差小于2.0%,表明所建模型合理.%The chemical hydrogen consumption of diesel liquid-phase hydrogenation was studied in an up-flow fixed-bed hydrogenation pilot plant.The calculating equations of chemical hydrogen consumption were deduced based on various chemical reactions, and the kinetic model of hydrogen consumption was built.We reached the conclusion that chemical hydrogen consumption in the front catalyst bed is much higher than that in the back catalyst bed, because there is 70% of hydrogen consumption in the top 20% of catalyst bed, resulting in the bad reaction performance in the back catalyst bed due to the lack of sufficient hydrogen.Under the hydrogenation conditions of the feed rate of 200 mL/h, hydrogen to oil mass ratio of 4.244×10-3, reaction temperature of 350℃ and reaction pressure of 8 MPa, the average relative error of calculated chemical hydrogen consumption is 2.11%, as compared to actual value.Thecalculating equations we deduced were accurate and reliable.The relative error of chemical hydrogen consumption predicted by the hydrogen consumption kinetic model is less than 2.0%, indicating that the model established in this paper is reasonable.【期刊名称】《石油学报(石油加工)》【年(卷),期】2017(033)004【总页数】7页(P626-632)【关键词】柴油;液相加氢;化学氢耗【作者】程杰;相春娥;刘宾;柴永明;赵秀文;王德会;刘晨光【作者单位】中国石油大学重质油国家重点实验室, 山东青岛 266580;中国寰球工程有限公司北京分公司, 北京 100020;中国石油工程建设公司华东设计分公司, 山东青岛 266071;中国石油大学重质油国家重点实验室, 山东青岛 266580;中国石油大学重质油国家重点实验室, 山东青岛 266580;中国石油工程建设公司华东设计分公司, 山东青岛 266071;中国石油工程建设公司华东设计分公司, 山东青岛 266071;中国石油大学重质油国家重点实验室, 山东青岛 266580【正文语种】中文【中图分类】TE624柴油液相加氢是针对常规滴流床加氢存在的问题开发出的一种新型柴油加氢技术,该技术取消了循环氢系统,H2预先溶解在原料油中来满足加氢反应的需求,从而节省设备投资和降低装置运行能耗[1-3]。
基于柴油加氢脱芳烃的技术分析_马博
随着环保理念不断深化,可持续发展的概念在世界范围内逐渐普及,这就要求能源产业应当更加注重环保,消除各类油中的不环保物质。
对于柴油而言,其存在芳烃类物质,在使用过程中会产生不少污染物,需要对其中的芳烃进行脱出,优化柴油环保性能。
1 基本原理加氢反应在芳烃化合物中属于一个可逆反应,而可逆反应的基本性质就是存在化学平衡,不能实现完全反应。
要提高可逆反应的反应度,需要投入更多的温度、压力等,不符合经济发展基本要求。
相关研究表明,加氢反应可以划归一级不可逆化学反应。
利用13CNMR测定芳烃含量,可以得出一个基本的反应式:A+n/2H 2=AH,式中A代表了芳烃化合物、AH代表了加氢产物,该反应的平衡浓度可以表示为:,式中2H P 代表了氢分压,a K 表示平衡常数,和代表了对应物质的摩尔量。
基于这一基本原理,结合热力学和动力学相关知识,就可以对加氢最优条件进行设计,提升柴油脱芳烃的效用。
2 常用技术2.1 中压加氢改质中压加氢改质工艺是我国自主发明的一套柴油加氢脱芳烃工艺,由抚顺石化研究院和石油化工科学研究院联合研制的。
这种工艺技术主要是在中等压强条件下,通过精制和裂化两个阶段,实现脱硫和脱芳烃的作用。
在精制段,通过加氢可以实现深度脱硫以及饱和芳烃;在裂化段,可以实现芳烃裂化。
中压加氢改质的脱芳烃工艺简单、液收较高、操作灵活。
2.2 Syncat深度加氢脱芳烃Syncat深度加氢脱芳烃工艺是一种单段低压低空速的工艺,是美国标准公司所设计的四种脱芳烃方案之一,属于加氢裂化。
这种加氢脱芳烃工艺的压强较低,全程压强在4.8MPa到6.2MPa,能够将柴油中的硫含量降低至500ppm以下,使芳烃含量减少10%到90%。
由于这种工艺使用Syncat作为反应催化剂,氢耗在285左右,液体产率为107%。
如果改用其他催化剂,氢耗和液体产率会出现对应的变化。
2.3 托普索低压托普索低压工艺主要覆盖了单段、双段两部分。
在单段部分,应该确保柴油中的硫含量降至2ppm以下。
酸性离子液体脱除柴油中碱性氮化物
酸性离子液体脱除柴油中碱性氮化物李文深;牟浩文;刘洁【摘要】合成离子液体N-甲基吡咯烷酮磷酸二氢盐([Hnmp]H2 PO4),用吡啶红外探针法测定其酸性.采用500μg/g的喹啉模型油考察其对油品中碱性氮化物的脱除性能.结果表明,在剂油质量比1:7,反应温度为30℃,反应时间为30 min,静置时间120 min的条件下,模型油中碱性氮化物的脱除率可达到98.64%.在离子液体[Hnmp]H2PO4回收利用4次后,碱氮脱除率仍在96%以上.同时该离子液体也能有效脱除碱氮含量高达0.52%(质量分数)的抚顺页岩油柴油馏分中的氮化物,当剂油质量比为1:1时,柴油馏分的碱氮脱除率可达94.25%.%Acidic ionic liquid(IL) N-methyl pyrrolidone dihydrogen phosphate ([Hnmp]H2PO4) was synthesized and its acidity was determined by using pyridine as IR spectroscopic probes .The denitrogenation performance of the acidic ionic liquid was investigated by using the model oil containingquinoline .Results showed that the acidic ionic liquid exhibited good denitrogenation performance achieving 98.64%basic N-extraction efficiency under the operation conditions with temperature of30 ℃,1:7(w/w) IL:oil,reaction time of 30 min and settling time of 120 min.In addition,the basic N-removal efficiency can still reach 96%during four recycles of the ionic liquid .Furthermore ,the acidic ionic liquid also can effectively remove the basic nitrogen compounds from Fushun shale diesel fraction that included 0.52%basic nitrogen ,and basic N-extraction efficiency can reach 94.25%when mass ratio of IL to oil was 1:1.【期刊名称】《应用化工》【年(卷),期】2017(046)012【总页数】4页(P2358-2361)【关键词】[Hnmp]H2PO4离子液体;脱氮;喹啉;页岩油柴油;碱性氮化物【作者】李文深;牟浩文;刘洁【作者单位】辽宁石油化工大学化学化工与环境学部,辽宁抚顺 113001;辽宁石油化工大学化学化工与环境学部,辽宁抚顺 113001;辽宁石油化工大学化学化工与环境学部,辽宁抚顺 113001【正文语种】中文【中图分类】TQ021.4;TE622.1燃料油中的含氮化合物分为碱性氮化物和非碱性氮化物,主要以杂环芳香化合物的形式存在。
文献综述
加氢精制催化剂 学号:200809103126 姓名:蔡晗 班级B08091031 1、 课题分析:主要查络合铁法脱硫的应用及发展 2、 书库: 2.1、超星 检索词:加氢 精制 催化剂 检测不出 检索词:加氢 检索结果2条 2.2、方正 检索词:加氢 精制 检索结果266条 检索词:加氢 精制 催化剂 检索结果90条 3、 文献数据库 3.1、CNKI库 检索词:加氢 精制 催化剂 检索结果185条 【1】 作者:姜旭; 顾永和; 王魏民; 杨珊珊; 书名:柴油加氢精制催化剂研究进展 化学与粘合 2010 年03期 摘要:随着原油的劣质化和环保法规的日益严格,我国在清洁柴油生产方面面临着十分严峻的局面,所
以迫切需要研制具有高效加氢精制的催化剂来满足油品深度加氢处理的要求。多元复合氧化物具有比γ-Al2O3、TiO2和ZrO2更高的比表面积、更好的热稳定性和更强的表面酸碱性,作为催化剂载体已引起很大的研究兴趣并得到了重要的应用。介绍了载体、活性组分、助剂和制备方法(液相浸渍法、沉淀法和溶胶-凝胶法)等因素对催化剂活性的影响。研究得知,溶胶-凝胶法较其它方法有较优的一面。具体探讨了溶胶-凝胶法的制备条件对催化剂活性的影响,也为设计、开发高活性加氢精制催化剂积累了经验。 英文摘要:China is facing a very rigorous situation in the aspects of clean diesel production
because of the more strict environmental legislation and decline in quality of petroleum feedstocks.Therefore,it is very important to develop the novel catalysts for diesel hydrofining.The multiple oxide displays higher specific surface area,thermal stability and stronger surface acidity and alkalescence than γ-Al2O3,TiO2 and ZrO2 which has attracted researcher's attentions as catalyst carrier.In this paper,effects of factor... 【2】作者:张乐 书名:加氢精制催化剂制备方法的研究 石油化工科学研究院 硕士论文 摘要:由于世界原油重质化趋势日益明显,原油中的硫、氮、金属含量增加;而日益
- 1、下载文档前请自行甄别文档内容的完整性,平台不提供额外的编辑、内容补充、找答案等附加服务。
- 2、"仅部分预览"的文档,不可在线预览部分如存在完整性等问题,可反馈申请退款(可完整预览的文档不适用该条件!)。
- 3、如文档侵犯您的权益,请联系客服反馈,我们会尽快为您处理(人工客服工作时间:9:00-18:30)。
综述专论化工科技,2006,14(4):57~61
SCIENCE&TECHNOLOGYINCHEMICALINDUSTRY
收稿日期:2006202214
作者简介:纪绪强(1980-),男,山东章丘人,辽宁石油化工大学研究生,主要从事微波化学方面的研究与应用。33通讯联系人。
3基金项目:辽宁省科技厅资助项目(20041857)。
柴油非加氢脱氮技术研究进展3纪绪强,赵杉林33,郭文玲,张起凯,李 萍
(辽宁石油化工大学石油化工学院,辽宁抚顺113001)
摘 要:介绍了柴油非加氢脱氮技术的研究现状和发展前景,分析了酸精制、溶剂精制、配合法脱氮、吸附精制法、组合脱氮法、生物脱氮法和微波脱氮法等柴油脱氮技术的原理、优缺点。关键词:柴油;非加氢脱氮;技术;研究进展中图分类号:TE626.24 文献标识码:A 文章编号:100820511(2006)0420057205
柴油是我国目前消费量最大的发动机燃料之一,主要用于装有柴油发动机的农业机械、重型车辆、铁路机车、船舶、工程和矿山机械等[1]。但是,柴油中的氮化物在燃烧过程中可形成导致空气污染和酸雨的氮氧化合物,其中的碱性氮化物在柴油的催化加工过程中会使酸性催化剂的活性中心减少,造成催化剂中毒[2~5]。与此同时,碱性氮化物还会使柴油的氧化安定性变差,影响其储存和使用性能。为了适应新的环保法规的实施,改善柴油品质,必须尽可能的脱除其中的氮化物。我国原油氮质量分数一般为0.1%~0.5%,
普遍偏高[6],因此柴油脱氮在我国显得尤为重
要。柴油中的氮化物分为碱性氮化物和非碱性氮化物,前者包括苯胺、吡啶、喹啉及其衍生物,后者包括吡咯、吲哚及其衍生物。目前,国内外从石油及其产品中脱氮的方法分加氢精制和非加氢精制两种。其中加氢精制工艺已经较为成熟,精制的收率高,产品安定性好,但脱氮率较低,还需要充足的氢源,设备投资及操作费用高,在应用上受到很大的限制。因此,国内外很多研究者已经把目光转向设备投资少,操作费用又低的非加氢脱氮工艺。非加氢精制的主要方法有:酸精制、溶剂精制、配合法精制及组合法精制、生物脱氮和微波脱氮等。
1 主要脱氮工艺1.1 酸精制碱性氮化物是影响柴油品质的主要因素。酸精制的原理即根据酸碱中和理论将其脱除。很早以前人们就发现用蚁酸2水溶液脱除页岩油中的氮化物,可以降低炼厂氢耗,使处理后油品的含氮量满足下游加工的要求。酸精制脱氮常用的酸有浓硫酸、盐酸、磷酸等无机强酸。它们可以脱除柴油中的碱性氮化物以及硫醇类、硫酚类、硫醚、噻吩等各种非烃化合物,部分非碱性氮化物、烯烃类、芳烃类也可以被洗去。舒运贵等人[7]用磷酸和稀碱联合精制掺炼重油的催化裂化柴油,精制过程中,磷酸循环使用,磷酸渣经氨水中和后,分离出的氮化物作为燃料烧掉,而磷酸铵的化合物经热分解后得到的磷酸可以再循环使用。李季[8]用二氧化碳酸性水溶液作脱氮剂洗涤焦化柴油,使柴油中碱性氮化物溶于水而被分离出来,
碱性氮脱除率约为60%。该工艺简单,无污染,
可进一步回收利用碱性氮化物,且中试效果比小试好,但是脱氮率偏低。酸精制操作简单,但是选择性往往较低,一些不含氮的烃类化合物也可溶于酸相中,使精制后油的收率降低,另外,废渣的处理和设备腐蚀问题也限制其应用。1.2 溶剂精制溶剂精制工艺用于油品脱氮已经有几十年的历史,并且已成功开发了几种具有代表性的工艺过程。该工艺是根据相似相容原理,利用溶质在
© 1995-2006 Tsinghua Tongfang Optical Disc Co., Ltd. All rights reserved.两种互不相容的液体间分配性质的不同达到液体混合物分离、提纯的目的。溶剂精制一般采用的是极性溶剂,如甲醇、乙醇、酚类、丙酮、糠醛、二甲亚砜(DMSO)、N,N2二甲基甲酰胺(DMF)、N2甲基22吡咯烷酮(NMP)和有机酸类等。有些研究者以甲醇为溶剂对安定性差的柴油进行抽提,研究影响柴油安定性的因素及其影响程度[9,10],但单纯的甲醇与氮化物的作用力弱,萃取选择性低。吕志凤等人[11]发现用质量分数2%硫酸2甲醇溶剂精制重油催化裂化柴油,可脱除大部分氮化物和芳烃类化合物,可使柴油的安定性得到明显改善。如果重油催化裂化柴油经碱洗后再用此溶剂精制,精制后油的安定性比单独碱洗或用质量分数2%硫酸2甲醇精制的效果明显。王军民等人[12]用含硫极性溶剂和含氢键化合物组成的萃取剂,可根据催化柴油含氮量,采用2~4级逆流萃取工艺进行精制,精制柴油总氮脱除率90%左右,硫的脱除率为30%左右,起到了脱氮保硫的作用。因而大幅度地提高了催化裂化柴油的氧化安定性,油品收率不低于96%。张科良等[13]应用正交实验设计方法筛选出DMF2烃复合溶剂精制催化裂化柴油,总氮脱除率71.1%,柴油收率95%,溶剂可回收,残液可制成高附加值的精细化学品,无污染物排放。糠醛也有较好的选择性,可有效脱除油中的胶质、含氮化合物、含硫化合物,但其溶解能力低。杨丽娜等[14]以纯糠醛为溶剂脱除催化裂化柴油中的碱性氮化物,发现剂油比和抽提级数对脱氮效果影响显著,相同溶剂用量情况下,多级溶剂抽提较简单抽提的效果要好,碱氮脱除率可达到91.52%。此工艺大规模工业化生产效果也较好。南阳石蜡精细化工厂[15]8.0×104t/a柴油精制装置采用清华大学溶剂萃取脱氮精制催化柴油专利技术,精制后柴油的安定性和色度均可以达到新标准要求。加工成本远远低于加氢精制的费用,操作易于掌握,技术简便易行,具有很好的工业应用前景。中原石化总厂[16]对旧碱洗系统加以改造,建成投产了柴油非加氢精制装置,所用的稳定剂是石油大学(华东)的专利技术,利用萃取原理,将柴油中的杂质萃取出来。经过萃取分离,使柴油中的杂质组分大量减少,从而提高柴油的质量,而且剂油比范围较宽,可满足不同牌号柴油的精制要求。溶剂精制可以脱除氮化物、胶质、多环芳烃和含氧、含硫等极性化合物,但一般溶剂的选择性较差,在脱除上述化合物的同时,很多烃类也被脱除,并且随精制程度的提高,精制油收率明显降低,而氮化物含量趋于平衡。因此该方法适用于粗原料的精制,不适用于油品质量的进一步提高。1.3 配合法脱氮配合法脱氮工艺是基于Lewis酸碱理论。柴油中的含氮化合物中的氮原子具有孤对电子,是电子给予体,为Lewis碱,它能与质子或其它Lewis酸结合,形成配合物。此工艺就是利用了这一特点,达到使氮化物从柴油中脱除的目的。配合脱氮剂通常由配合剂、助溶剂、和稀释剂组成,配合剂具有相应的官能团,可与待分离的组分络合。研究人员常选用一些过渡金属化合物作为配合剂,利用金属原子核外电子发布的d轨道或s空轨道与含孤对电子的氮原子形成配合物。金属卤化物作为油品脱氮配合剂的研究很多,Ti、Cu、Zn、Fe、Pd、Sn、Hg等的卤化物均可用作脱氮的配合剂。助溶剂应选用配合剂的良好溶剂,在反应过程中,它可促进配合物的生成和相间转移。稀释剂用于调节脱氮剂的粘度、密度及界面张力等,使分离易于进行。配合精制工艺已经有几十年的历史。早在1972年,Bernheiner[17]就用含Cr2+、Zn2+、Fe3+或
Li+盐的丙酮、甲醇或乙醇溶液脱除石油馏分中
的氮化物,脱氮率高达99%。孙学文等人[18]研究了加入一种络合剂对催化柴油中碱氮含量的影响,发现:柴油中的碱氮含量随着络合剂加入量的增加而降低,当络合剂质量分数为0.25%~0.
5%时,柴油中的碱氮含量达到最低值。用此方法处理重催原料,可以有效脱除催化柴油中的碱性氮化物,同时可以降低柴油中的烯烃含量,从而改善催化柴油的氧化安定性,且络合剂不影响柴油的酸值。魏毅等人[19]自行研制了保硫脱氮剂,
该脱氮剂为含有过渡金属的酸性化合物。由于该化合物的过渡金属核外有空的d轨道且离子半径小,有利于与含有孤对电子的碱性氯化物形成配位化合物。利用生成物与试油的比重差使生成物富集,达到脱去碱性氯化物的目的。将该脱氮剂与质量分数20%的醋酸水溶液搭配,在剂油质量比1∶9的条件下处理柴油,鞍山直馏柴油碱性氮脱除率为84.9%、鞍山催化柴油碱性氮脱除率为
・85・
化 工 科 技第14卷
© 1995-2006 Tsinghua Tongfang Optical Disc Co., Ltd. All rights reserved.98.9%,取得了满意的效果。丛玉凤等人[20]采用自行研制的FS化学精制剂和FS0l络合捕集剂对两种焦化柴油进行精制。结果表明,在剂油质量比为1∶350时,焦化柴油色度降低,两种焦化柴油氧化安定性总不溶物从7.9和8.7mg/100mL降低到1.5和2.4mg/100mL,柴油收率在99.5%以上。精制后的焦化柴油,直馏柴油和催化裂化柴油按体积比1∶1∶1调和后,各项指标均达到-l0#轻柴油国家标准要求,且调和油的储存安定性较好。该方法精制工艺简单、投资少、成本低,是缓解目前无加氢能力的炼厂精制焦化柴油的良好途径。严家保等人[21]用自行开发的无机酸性配合脱氮剂精制催化裂化柴油,当剂油质量比为1∶200,反应时间为25min,反应温度20℃时,碱性氮化物的脱除率高达94.33%。配合精制工艺大都用高价金属离子与有机溶剂组成的复合溶剂为脱氮剂对油品进行精制,该工艺所得精制油的含氮量有所降低,但脱氮剂所含金属离子的盐使用起来不方便,并且有机溶剂对油品中烃类的溶解,降低了精制油的收率,这两个问题需要解决。1.4 吸附精制吸附精制一般用比表面积大的极性物质,利用吸附原理对油品进行精制,改善油品质量。常用的吸附剂如白土、分子筛、硅胶、氧化铝、硅藻土等。吸附精制工艺分混和接触工艺和渗滤吸附工艺两种。混和接触工艺是油品与粉状固体吸附剂(酸性白土、活性白土、漂白土、氧化铝等)先在一定温度下充分混合,然后剂油分离,以除去油中极性物质(包括含氮化合物)。它作为一种精制手段常与酸精制或溶剂精制工艺构成组合工艺,如酸2白土、溶剂2白土精制工艺。渗滤吸附工艺的吸附剂以固定床层形式装填,油品通过吸附剂床层进行脱氮。渗滤吸附工艺操作费用较混合接触工艺低,污染少,且脱氮能力强。白土精制是一种比较常用的方法,但白土脱氮能力较差,吸附量偏小,用量大于3%油品回收率就会降低。Robert[22]以催化裂化催化剂为吸附剂,对合成燃料脱氮,并把吸附工艺与催化裂化工艺联合起来,对吸附后的催化剂进行再生并循环使用,连续生产低氮产品。栾锡林等人[23]在实验室小型固定床装置上选用A、B、C三种吸附剂脱除焦化蜡油中的碱性氮化物,取得了良好的
效果。陈文艺等人[24]采用磷酸处理颗粒白土吸附剂,可使其吸附能力得到显著提高。FCC柴油经过吸附处理后,质量得到了明显的改善。吸附剂可在溶剂中再生。马骏等人[25]将吸附剂C经实验室处理后,将其转入微波反应釜中,接受微波辐射,得实验用吸附剂,用此吸附剂对油品的碱性氮化物脱除率在90%以上,吸附基本饱和的吸附剂置苯2乙醇溶液中解吸,再经补酸和微波等方法再生后,吸附剂吸附性能得到了较好的恢复,处理能力基本与新鲜吸附剂相当。王延飞等人[26]分别用有机粘土和无机粘土作吸附剂对催化裂化柴油进行吸附精制处理,考察它们的精制效果。发现有机粘土对柴油的精制效果比无机粘土好,有机粘土除了对柴油中的含氮化合物具有较高的选择性以外,对含硫化合物也具有一定的脱除能力。在加剂量为0.08g/mL,温度25℃,吸附时间20min的条件下,有机粘土可将催化裂化柴油中总氮含量由原来的0.1022%降至0.0232%;碱氮含量由原来的0.02218%降至0.00964%;硫含量由原来的0.0985%降至0.4297%。离子交换树脂是一种特殊的吸附剂。用它作吸附剂是20世纪50年代以来广泛使用的一种分离技术。它比一般吸附剂的吸附量大,可以有效地脱除油品中的含氮化合物。此方法分离氮化物的机理比较复杂,是多种因素共同作用的结果,其中最主要的分离因素是离子交换作用。它的关键是离子交换树脂的再生,常用强酸、强碱、过渡性离子和有机溶剂对失活的树脂进行再生。Masao[27]用大孔的H型磺酸阳离子交换树脂分