文献阅读报告
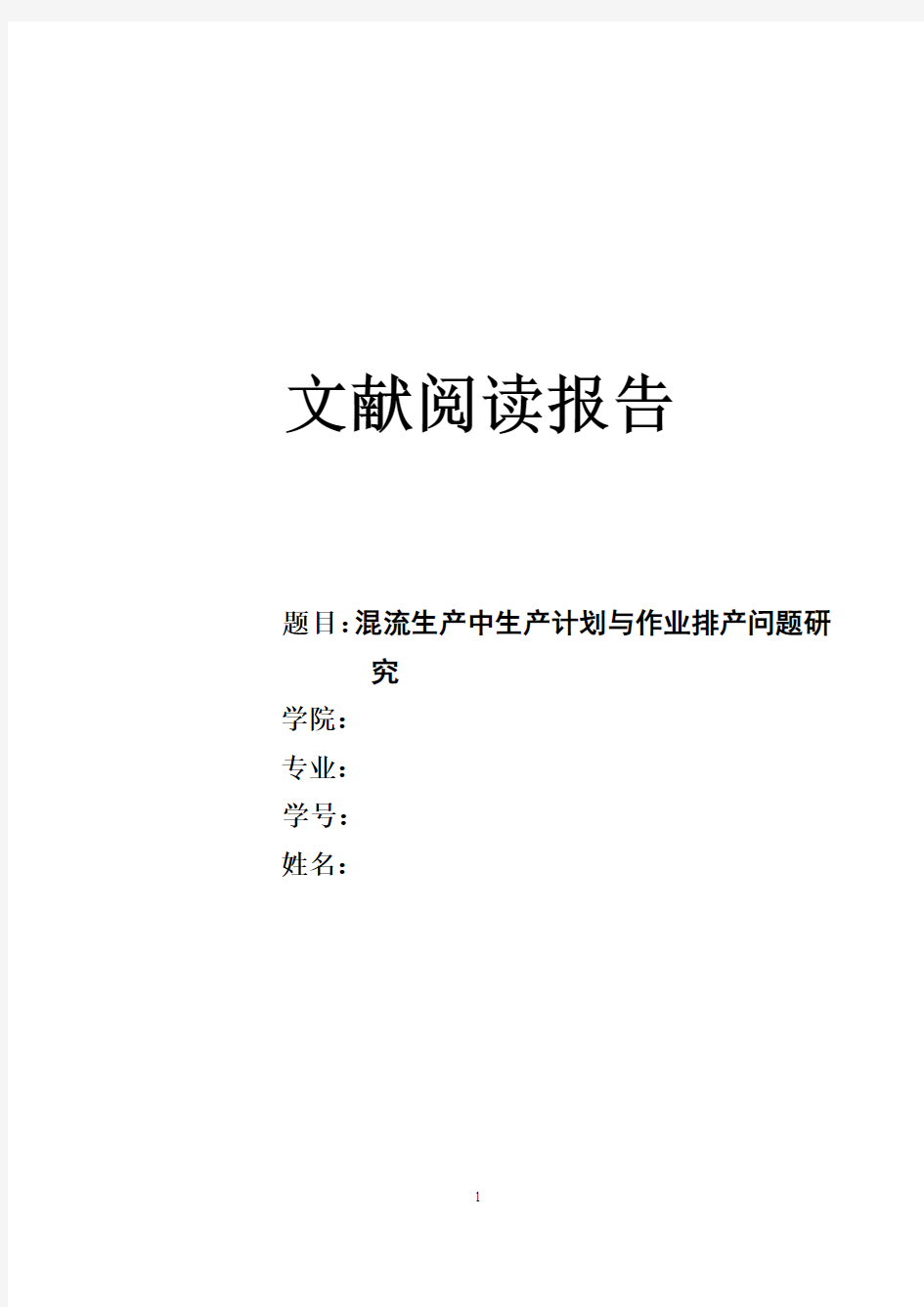
- 1、下载文档前请自行甄别文档内容的完整性,平台不提供额外的编辑、内容补充、找答案等附加服务。
- 2、"仅部分预览"的文档,不可在线预览部分如存在完整性等问题,可反馈申请退款(可完整预览的文档不适用该条件!)。
- 3、如文档侵犯您的权益,请联系客服反馈,我们会尽快为您处理(人工客服工作时间:9:00-18:30)。
文献阅读报告
题目:混流生产中生产计划与作业排产问题研究
学院:
专业:
学号:
姓名:
摘要
随着社会化生产的进一步细化和市场竞争的日益加剧,制造企业面临着前所未有的挑战。用户已不满足与从市场上买到标准化生产的产品,他们希望得到按照自己要求定制的产品或服务。这些变化导致产品生产方式革命性的变化。传统的“一对多”的生产方式,即企业开发出一种产品,然后组织规模化大批量生产,用一种标准产品满足不同消费者的需求,己不再能使企业继续获得效益。为了适应市场需求的多样化、动态化,现代企业的制造模式已开始转向基于订单的混流生产模式,即在基本上不改变现有生产手段、生产条件和生产能力的条件下,通过改变生产组织的方法,在一条流水线上进行多品种搭配,有序地生产多种产品,最大程度地满足客户需求。
关键词
混流生产生产计划作业排产
引言
在制定生产计划方面,车间必须综合考虑生产能力、客户需求、制造资源状况等因素,结合企业当前的生产负荷,制订出可行而且在一定程度上较优的生产计划。在混流生产模式下,由于不同品种产品的生产工序和作业时间各不相同,因此生产计划必须考虑流水线上产品的投放顺序。合理的投放顺序可以实现混流生产线的有节奏、按比例连续生产,使得品种、产量、工时、设备负荷等达到全面均衡。
在对生产计划的控制方面,由于生产计划时无法预期所有的意外状况,使得预先制定的计划排序常常难以得到严格执行。在这种情况下,必须及时调整生产过程,从而达到生产计划与生产过程的协调一致。为了实现这个目标,需要获取实时的生产状态信息,使得从计划、排产到执行调度、从物料配送到看板预警等形成多个可控的闭环。在混流生产模式下,物料管理及生产负荷的控制方面相对于单一产品的生产线更为复杂。因此,在混流生产模式下的生产计划与作业排产问题对一个制造企业来说就显得尤为重要了。
正文内容
1.研究方法
虽然ERP系统包含很多模块,但归根结底应该以MRPⅡ为核心,并以此编制生产计划。MRPⅡ的基本思想是:基于企业经营目标制定生产计划,围绕物料转化组织制造资源,实现按需按时地进行生产。MRPⅡ的逻辑流程图如图2所示。MRPⅡ可分为生产计划与控制、物流管理,财务管理三大子系统。生产计划与控制子系统按照预测的销售前景,并考虑销售订单的实际情况来编制生产大纲;再按主生产计划,编制物料需求计划,据此采购原材料和零件,并安排生产,使在制品数量、原材料数量及成品数量控制在最优水平上。此外,根据物料需求计划的结果来核算能力,调整主生产计划,尽量维持生产平衡。生产线的信息反馈也与财务系统、物流管理系统集成。物流管理系统向供销部门和库房管理部门提供日常业务处理功能,并自动将信息转达到财务部门和其他有关部门。财务管理系统除对各往来帐目和日常发生的货币支付帐目进行处理外,还向管理人员提供目前库存资金占用情况和企业运营情况。图中,右侧是计划与控制流程,包括决策层、计划层和执行控制层;中间是企业基础数据,这些数据的集成,把企业各个部门的业务沟通起来;左侧是企业的财务系统;联线表明信息的流向及相互之间的集成关系。MRPⅡ的计划层次体现了由宏观到微观、由战略到战术、由粗到细的深化过程,属于典型的递阶式计划模式。
但随着制造模式的变迁,以及客户对产品个性、质量等要求的不断变化,MRPⅡ在计划
原理、生产提前期、无限能力计划等方面的缺陷便表现出来。
(1)“提前期”和“批量”是制造麻烦的罪魁祸首。
在大量生产条件下,非流水线生产的产品转移是成批进行的,或整批一起转、或按容器分批转,物料的流动就出现了停滞现象——转出时的等待成批和转入时的等待加工。实际上,等待将分工的熟练工人那里争取到的高效率全部抹杀掉。著名的“加工时间大约仅仅是整个(周期)提前期的5%”的制造业顽疾,和加工前、后的等待,都被固化在ERP软件里。每一个提前期背后还都有一个批量的约束。批量变化了,提前期就不对了,不小心MRP还会出现下序开工早于上序完工的荒唐事。
(2)“一个产品一个BOM”易造成数据灾难。
MRPⅡ的基石BOM,其原理是对每一个确定的产品建立一个顶级的产品BOM,再根据产品内的零部件关系进行拆分,运行MRP。在基于订单的混线生产模式下,MRPⅡ为每一种产品确定一个产品BOM,有多少种产品就有多少种产品BOM。这样势必使MRPⅡ受到“一种产品一个BOM”的羁绊,带来一场数据灾难。
(3)采用无限能力计划,不考虑可行性。
MRPⅡ从诞生之初,就没有考虑能力问题。正如MRP创始人之一Joseph Orlicky所认为
的那样“MRP是与能力无关的系统,它的功能仅仅是确定为实现主生产计划需要什么物料、需要多少和什么时间需要”。MRP在作计划时,假设工厂能力是无限的,忽视了计划的可行性问题。多年来,理论界对MRP的这个缺陷进行了许多技巧性的改进。划,不考虑可行性。
2 问题描述
混流条件下基于MRPⅡ与TOC的生产计划与控制研究,不仅涉及到MRPⅡ与TOC等生产管理方式的研究,还涉及到以MRP II为基础,同时结合TOC思想的计划与控制系统框架的提出,以及详细的车间作业排产计划的编制方法的研究,问题涉及范围广、综合性强,复杂度高。目前国内理论界对这方面的研究还很少,需要进行长期的投入才会有所收获。
3 国内外研究现状
(1)国内研究现状
熊锐等建立了一种车间集成生产计划与调度模型,同时考虑了工序加工的先后顺序约束和作业在机床上的加工能力约束,并采用拉氏松弛法对其进行求解,但求解松弛调度子问题算法的计算复杂性较大,难以解决规模较大的问题。严洪森,张晓东等针对汽车制造企业生产计划与调度问题,做了较多的工作。他针对一类Job-shop车间的生产计划和调度的集成优化问题,提出一种非线性混合整数规划模型,该模型利用调度约束来细化生产计划,以保证得到可行的调度解;并采用由启发式规则和遗传算法构成的混合遗传算法进行求解,并在汽车装配车间生产计划与调度的同时优化方面,首先将汽车装配线简化为一个Flowshop问题,并建立其混合整数规划模型,以求得使各装配工位的准备成本和空闲时间尽可能少,并尽可能满足产品需求的粗生产计划,然后在粗生产计划的基础上考虑装配线的细节;用Tabu搜索法与快速调度仿真相结合的二种不同方法,使生产计划与调度同时得到优化;并给出了实际算例结果,然后对汽车制造企业的冲压、焊接和涂装二个成串联多级车间的生产计划与调度集成优化进行了研究,建立了其模型,并提出了批量动态分割合并的方法,构成一基十遗传进化的启发式算法来求解(2)国外研究现状
1998年Layden,J。发表论文提出一种基于有限生产能力的前向排产思想,但他并没有给出具体的排产模型。2001年S。Crawford建立一种混合整数规划(MIP --Mixed Integer Programming)模型用于解决资源分配和多阶段生产计划和排产方案。但并没有考虑到生产工序的优先关系。2003年Y ANRADEE设计一种优先权网络用来代表工序间的先后关系,通过启发式算法产生近似最优解的排产方案,并引进了关键路径的概念,但可惜的是,排产算法在很大程度上都是基于无限生产能力的。2004 Lambrecht 提出一种基于无限生产能力下的MRP,该方案假设生产间各个子工序的操作顺序是固定不变的,这就很难处理动态订单生产问题。2005年Moon,Kim和Gen共同提出一种动态的生产排产模型(DAPS),可以动态处理可变订单的问题。但遗憾的是,传统的MPS是基于生产的无限能力、生产时间固定不变和生产供需固定不变的前提下的,这就会产生许多问题,比如变动瓶颈等,而且,无法保证实现主生产计划的详细生产排产计划的可行性。当详细生产排产计划变得不可行的时候,需要对主生产计划做大幅度的调整。延长了产品交货时间。因此,详细生产排程应该基于企业的实际生产能力,并且尽可能做到均衡生产,这样编制出来的生产排产计划才更具有可操作性。