正丁烷法顺酐溶剂吸收与水吸收比较2015
溶剂吸收法顺酐装置工艺介绍

溶剂吸收法顺酐装置工艺介绍
田赟
【期刊名称】《甘肃科技》
【年(卷),期】2010(026)019
【摘要】介绍了丁烷氧化溶剂吸收法顺酐装置的生产工艺,重点介绍了溶剂吸收过程当中的工艺关键环节.包括溶剂损失的控制,溶剂的再生处理.
【总页数】2页(P33-34)
【作者】田赟
【作者单位】兰州石化公司,甘肃,兰州,730060
【正文语种】中文
【中图分类】TQ216
【相关文献】
1.顺酐溶剂吸收装置的关键控制工艺分析 [J], 罗志海
2.丁烷法顺酐装置溶剂吸收工艺开车过程中的主要控制因素 [J], 姚忠宝
3.顺酐装置溶剂系统故障分析及改造建议 [J], 田赟;董海军
4.顺酐溶剂吸收法装置中影响溶剂洗涤效果的因素分析 [J], 杨立光
5.顺酐生产溶剂回收装置技术综述 [J], 余婷
因版权原因,仅展示原文概要,查看原文内容请购买。
瑞华化工正丁烷氧化制顺酐工艺要点20150130
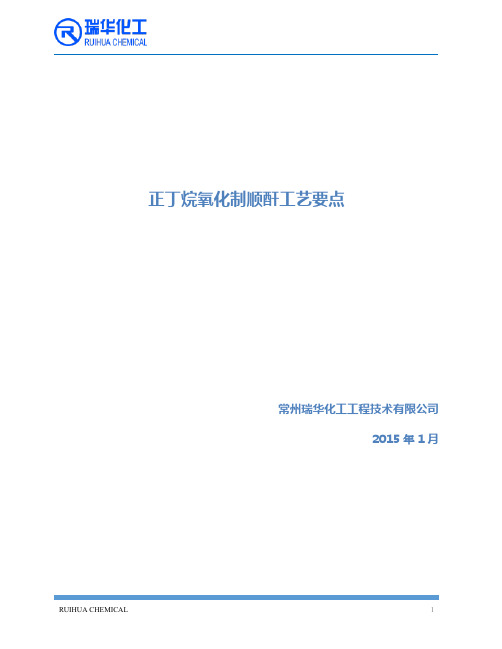
正丁烷氧化制顺酐工艺要点常州瑞华化工工程技术有限公司2015年1月1.概述常州瑞华化工目前设计并转让的单套5万吨顺酐装置,采用的是正丁烷氧化法生产工艺,后续处理采用溶剂吸收法。
全球范围内,因技术成熟性、环保要求及原料来源的问题,超过80%的顺酐产能都来源于正丁烷氧化生产工艺。
而中国有较为丰富的苯资源(石油苯,加氢苯),顺酐行业初期的生产工艺都为苯氧化法。
截止目前,苯法顺酐产能已经超过100万吨/年。
而从2008年开始,正丁烷氧化制顺酐工艺逐渐被行业接受并快速发展。
近几年新建顺酐项目多为正丁烷氧化法。
目前,包括在建项目,正丁烷法顺酐产能已经接近每年100万吨。
较为廉价的原料及突出的环保性,是其相对于苯氧化法工艺具有的优势。
瑞华化工于2011年起接受顺酐项目设计邀请,吸收了国外先进的顺酐工艺技术精华,开发并完成了具有自主知识产权的先进顺酐反应及吸收工艺。
于2014年完成单套5万吨/年正丁烷氧化制顺酐工艺的商业技术转让,目前项目进展顺利。
根据深入的市场调研及今后的行业发展方向,瑞华化工选择了正丁烷氧化法制顺酐工艺进行开发投入。
而对于难度较大的吸收工艺,则采用了使用DBP做为溶剂的溶剂吸收工艺。
溶剂吸收工艺相比于水吸收工艺,有着顺酐收率高、装置能耗低的优点。
传统的溶剂吸收工艺在装置运行时往往存在系统堵塞、溶剂消耗量大、废水处理困难等问题。
为此,瑞华化工针对这些问题进行了深入的研究并开发出先进的设计,给出最优化的解决方案,最大限度地发挥溶剂吸收工艺的优势。
2.工艺简述以正丁烷为原料生产顺酐为部分氧化反应。
空气与正丁烷按照一定比例进入反应器,在VPO催化剂的存在下,反应生成顺酐及部分CO,CO2,H2O。
副产物为乙酸、丙烯酸等。
反应为强放热反应,采用列管式反应器,以熔盐做为换热介质将反应热移出,并控制反应温度。
使用脱盐水换热回收熔盐热量,副产高压蒸汽。
反应产物利用溶剂(DBP)将顺酐吸收后,进一步解吸精制,得到产品顺酐。
溶剂吸收法顺酐装置工艺介绍
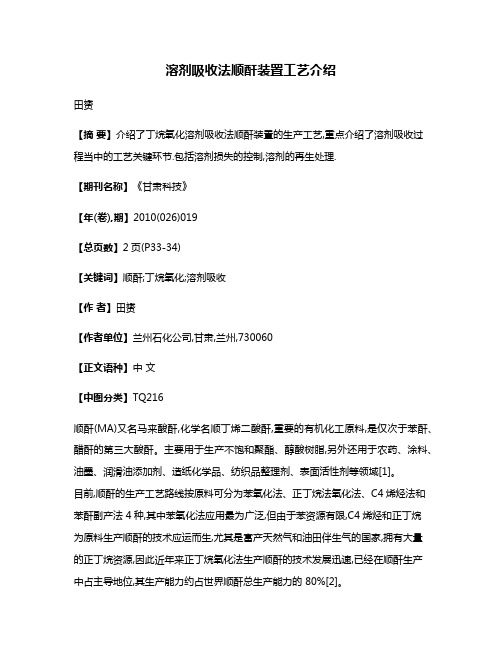
溶剂吸收法顺酐装置工艺介绍田赟【摘要】介绍了丁烷氧化溶剂吸收法顺酐装置的生产工艺,重点介绍了溶剂吸收过程当中的工艺关键环节.包括溶剂损失的控制,溶剂的再生处理.【期刊名称】《甘肃科技》【年(卷),期】2010(026)019【总页数】2页(P33-34)【关键词】顺酐;丁烷氧化;溶剂吸收【作者】田赟【作者单位】兰州石化公司,甘肃,兰州,730060【正文语种】中文【中图分类】TQ216顺酐(MA)又名马来酸酐,化学名顺丁烯二酸酐,重要的有机化工原料,是仅次于苯酐、醋酐的第三大酸酐。
主要用于生产不饱和聚酯、醇酸树脂,另外还用于农药、涂料、油墨、润滑油添加剂、造纸化学品、纺织品整理剂、表面活性剂等领域[1]。
目前,顺酐的生产工艺路线按原料可分为苯氧化法、正丁烷法氧化法、C4烯烃法和苯酐副产法 4种,其中苯氧化法应用最为广泛,但由于苯资源有限,C4烯烃和正丁烷为原料生产顺酐的技术应运而生,尤其是富产天然气和油田伴生气的国家,拥有大量的正丁烷资源,因此近年来正丁烷氧化法生产顺酐的技术发展迅速,已经在顺酐生产中占主导地位,其生产能力约占世界顺酐总生产能力的 80%[2]。
我国的顺酐生产工艺,长期以来基本以苯氧化、水吸收的生产工艺为主。
近年以来,国内陆续开始引进丁烷氧化、溶剂吸收法的顺酐生产工艺。
主要针对该工艺进行简单的介绍,以便于国内同行了解溶剂吸收法顺酐生产工艺状况。
传统的水吸收工艺中,采用脱盐水对顺酐进行吸收,该过程为化学过程,生成物为顺丁烯二酸。
与传统的水吸收工艺进行对比,溶剂吸收主要采用有机溶剂作为吸收剂,该过程是物理吸收过程。
兰州石化公司引进工艺当中采用邻苯二甲酸二丁酯(DBP)作为吸收溶剂。
该工艺的主要设备是两个部分,及吸收部分及解吸部分。
该工艺的主要优点是吸收过程中不产生顺酸,勿需脱水,减轻了设备腐蚀;同时,减少了顺酸的异构化,提高了收率。
但缺点是投资回收周期长,溶剂净化难度大,溶剂循环过程中的损失量不易控制[3]。
正丁烷氧化做顺酐工艺介绍

正丁烷氧化做顺酐工艺介绍正丁烷氧化工艺是以正丁烷为原料,在V2O5-P2O5系催化剂作用下发生气相氧化反应生成顺酐。
该工艺自1974年由美国孟山都等公司实现工业化以来,由于原料价廉、对环境污染小以及欧美等国家正丁烷资源丰富等原因而得到迅速的发展,代表了顺酐生产工艺的发展趋势。
在固定床工艺中,由于正丁烷氧化选择性和反应速率均比苯法低,正丁烷-空气混合物中正丁烷浓度可高达1.6%-1.8%(摩尔分数),顺酐收率按正丁烷计约为50%,故对于同样规模的生产装置需求较大的反应器和压缩机;采用流化床反应器可使正丁烷在空气中的浓度提高到3%-4%(摩尔分数)。
流化床反应器传热效果好,且投资较少,但流化床用的催化剂磨损较多,对大型顺酐生产装置(20kt/a以上),如能获得价廉且供应有保障的正丁烷原料,宜选用流化床反应器。
与传统苯法相比,正丁烷氧化法具有原料价廉、污染小等优点。
正丁烷法每吨顺酐产品消耗1.l-1.2吨正丁烷,而苯法每吨顺酐产品消耗1.1-1.3吨苯。
而且正丁烷法生产顺酐理论产量为1:1.69,苯法为1:1.256,因此正丁烷的顺酐理论产量比苯法高许多。
随着技术的不断发展,正丁烷作原料其单耗将比苯法低得多,正丁烷不仅消耗少,而且与苯法相比,其毒性也小,同时正丁烷法生产顺酐对环境污染小,随着全球环保压力越来越大,正丁烷法在满足环保要求以及发展前景方面比苯法更具有生命力。
正因为如此,目前全球顺酐生产能力约80%采用正丁烷路线,而且还有不断增加的趋势。
目前,国外顺酐生产技术由以苯法为主向正丁烷氧化法为主转变,没有其他新的生产路线出现,技术进展主要体现在现有装置的工艺改进和提高催化剂性能两个方面。
顺酐产品成本50%左右是原料费用,已工业化的顺酐生产技术都是以控制最大收率来确定工艺条件。
目前,三菱化学/英国BOC公司、SISAS/Conser公司等分别开发了回收尾气中未反应的正丁烷,将其重新送回反应器中参与反应,以减少正丁烷消耗量的催化剂和生产工艺。
正丁烷氧化法制顺酐

实验名称:正丁烷氧化制顺丁烯二酸酐二、实验原理1、苯氧化法:通常采用V-P-Ti-O催化剂,在固定床或流化床反应器于380~450℃下反应。
该方法工艺路线成熟,原料易得,是国内应用比较普遍的方法,但是由于在苯的六个碳中有两个变成CO2,对原料浪费较大,在国际上开始被正丁烷氧化代替。
C6H6 + 4.5O2→C4H2O3 +CO2 +H2O2、碳四馏分氧化法CH3-CH2-CH2-CH3 +2O2→C4H2O3 +H2O丁烷是碳四馏分中最廉价又容易获得的原料,它与空气混合氧化生产成本较低,采用V -O-P催化剂,由于能充分利用原料,且原料的重量收率较高,近年来该法发展迅速,工业上已有替代苯氧化法的趋势,本实验采用此方法。
但是,由于近年国际市场石油价格变动较大,丁烷气的价格也变化较大,使该工艺在原料材料价格上不占优势。
同时,由于丁烷气在空气中的爆炸极限只有1.8%,在用固定床进行生产时,反应放热剧烈,反应器体积和操作空速要求较高,生产的工艺要求和技术比苯直接氧化法高,现在国际上使用流化床反应器,可以使原料气浓度在丁烷的爆炸上限范围,即40%以上,但该反应器对催化剂强度和活性要求较高,在我国尚未投入生产。
三、实验流程及仪器设备本实验由原料气配气系统,反应器控温系统,催化反应器,产物吸收及气相色谱分析系统组成。
具体介绍如下:1、原料气配气系统由液化丁烷气罐、空气压缩机、空气储罐、丁烷气体及空气质量流量计、原料气混合罐组成。
空气首先由压缩机压缩到空气储气罐里,然后经过减压阀到空气流量计,流量计的读数由显示仪控制,一般为1000ml/min左右,注意流量计的读数是指气体在标准状态下的体积,不是实际测定状态下的体积或质量流量,流量计的读数和气体温度、压力没有太大关系。
可以换算摩尔或质量。
丁烷经过减压阀也到质量流量计,并根据实验的条件,一般控制和空气的体积比为1.6%以下,以免发生爆炸危险。
丁烷气体质量流量计的读数需乘以0.29,才是丁烷的标准体积。
14丁二醇合成技术方案原料消耗比较
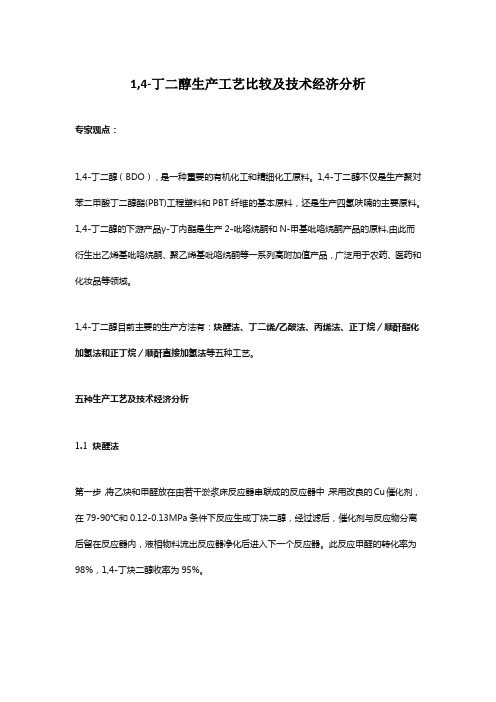
1,4-丁二醇生产工艺比较及技术经济分析专家观点:1,4-丁二醇(BDO),是一种重要的有机化工和精细化工原料。
1,4-丁二醇不仅是生产聚对苯二甲酸丁二醇酯(PBT)工程塑料和PBT纤维的基本原料,还是生产四氢呋喃的主要原料。
1,4-丁二醇的下游产品γ-丁内酯是生产2-吡咯烷酮和N-甲基吡咯烷酮产品的原料,由此而衍生出乙烯基吡咯烷酮、聚乙烯基吡咯烷酮等一系列高附加值产品,广泛用于农药、医药和化妆品等领域。
1,4-丁二醇目前主要的生产方法有:炔醛法、丁二烯/乙酸法、丙烯法、正丁烷/顺酐酯化加氢法和正丁烷/顺酐直接加氢法等五种工艺。
五种生产工艺及技术经济分析1.1 炔醛法第一步,将乙炔和甲醛放在由若干淤浆床反应器串联成的反应器中,采用改良的Cu催化剂,在79-90℃和0.12-0.13MPa条件下反应生成丁炔二醇,经过滤后,催化剂与反应物分离后留在反应器内,液相物料流出反应器净化后进入下一个反应器。
此反应甲醛的转化率为98%,1,4-丁炔二醇收率为95%。
第二步,在淤浆床内采用改良的催化剂,丁炔二醇在120-150℃条件下加氢生成BDO,最后通过蒸馏和薄膜蒸发提纯BDO,BDO纯度≥99%。
改良法的技术特点是:a.采用改良的Cu催化剂,低压操作,乙炔自身的分解压力不超过0.14MPa,简化了外加安全设施,省去了高压容器和压缩机;b.反应器配有专门的过滤系统,便于催化剂和反应物在反应器内分离;c.进料组成较灵活,甲醛水溶液中甲醛含量可为2%-10%,乙炔进料时不需惰性气体稀释。
据测算,操作费用和投资比经典法减少10%-20%。
1.2 丁二烯法日本三菱化成开发的以丁二烯为原料制备BDO的方法,分为三步:(1)丁二烯、醋酸和空气在催化剂条件下制得1,4-二乙酰氧基-2-丁烯;(2)加氢制得1,4-二乙酰氧基丁烷;(3)水解得到1,4-丁二醇。
典型的收率以丁二烯计,为80%-85%。
该工艺所用原料资源丰富,无安全隐患,中间产物和产品收率较高,但工艺流程复杂,投资高、催化剂昂贵、蒸汽耗量大,只有在一定规模及丁二烯价格较低的情况下才具有竞争力。
正丁烷法顺酐生产工艺现状

正丁烷法顺酐生产工艺现状摘要:顺酐是世界上仅次于苯酐的第二大酸酐原料,其下游产品有着广泛的开发和应用前景。
本文综述了正丁烷法顺酐的生产工艺现状,从不同工艺技术路线介绍了正丁烷法顺酐工艺流程,以及正丁烷法顺酐生产工艺的优势。
关键词:正丁烷法顺酐氧化反应器一、顺酐生产工艺概况顺酐生产工艺按原料路线可分为苯氧化法、正丁烷氧化法两种主要生产方法。
按生产工艺技术氧化反应部分分为固定床与流化床,后处理回收部分分为水吸收与溶剂吸收。
1.原料路线顺酐生产原料路线可分为苯氧化法、正丁烷氧化法。
国外目前占主导地位的是以正丁烷为原料的生产路线,国内生产装置以苯法为主。
由于我国资源的特殊性,煤资源较丰富,焦炭产量大,煤化工的下游产品焦化苯供应充足,使苯法生产顺酐具有资源优势。
正丁烷法制顺酐工艺资源利用方面比苯法合理,环境污染程度比苯法轻。
随着我国石化行业快速发展和炼油能力提高,C4资源逐步得到综合利用,正丁烷法顺酐装置近几年发展较快。
2.氧化工艺2.1正丁烷法流化床正丁烷进料浓度通常为 4.0 mol~4.3 mol%,流化床反应器上部设有催化剂分离装置,外部设有催化剂过滤装置。
反应器操作温度为400~430 ℃,热量通过反应器内安装的蒸汽盘管产生蒸汽供装置使用。
反应生成气体冷却后进入回收工序。
2.2正丁烷法固定床原料正丁烷与空气按一定比例充分混合后进入反应器,在装填了一定数量催化剂的列管内发生反应,正丁烷与空气的混合比例通常为 1.6 mol~2.0 mol%。
反应器热点温度通常在440~470 ℃。
反应热由熔盐冷却器和气体冷却器移出,产生蒸汽供装置使用。
反应生成气体冷却后进入回收工序。
二、正丁烷法顺酐生产工艺现状正丁烷法与苯法在工艺流程上近似,区别最大的就是氧化反应催化剂不同,丁烷法氧化反应器反应管比苯法长一些,最长达到 6 500 mm,后处理既可以采用水吸收也可以采用溶剂吸收。
1.氧化反应部分(固定床反应器)国内运行的正丁烷法顺酐装置全部为国产化技术固定床工艺。
正丁烷溶剂吸收工艺顺酐装置主要物料消耗分析与控制

正丁烷溶剂吸收工艺顺酐装置主要物料消耗分析与控制摘要:丁烷法溶剂吸收顺酐生产工艺是国外较普遍采用的方法,而在国内正丁烷法溶剂吸收顺酐生产工艺正处于发展阶段,成熟运行的仅吐哈油田公司石化厂一家。
但随着顺酐技术的发展和苯价格的上升,国内丁烷法溶剂吸收工艺顺酐生产技术将成为主趋势。
该工艺是以正丁烷为原料,通过氧化反应生成顺酐,再以邻苯二甲酸二丁酯作为溶剂吸收顺酐,在解析塔内将顺酐在真空状态下解析出来。
解析后的溶剂经过进一步真空闪蒸以降低顺酐含量,最后送至离心分离、气提干燥形成品质较高的新鲜溶剂实现循环利用。
但在实际生产中,其生产控制方法往往影响原料及各种辅助材料的消耗,尤其是正丁烷和溶剂消耗的控制直接影响着企业的效益和发展。
关键词:顺酐,物料消耗,因素,影响,分析,控制前言正丁烷法溶剂吸收顺酐装置,其工艺过程可分为气分、反应、吸收、解吸、洗涤、精制、造粒包装、司炉等8各工段,对于设有余热发电装置,要同时考虑发电和司炉负荷的合理调整和蒸汽平衡的优化。
主要生产流程是在催化剂的作用下氧化反应生产顺酐,再经过冷却和使用邻苯二甲酸二丁酯作为吸收剂将顺酐气体充分吸收,然后在解吸工段负压条件下进行顺酐和溶剂的物理分离,分离出的顺酐送往精制工段精制后进行造粒包装为成品出厂销售,溶剂返回吸收工段循环利用,约15%的溶剂送往洗涤工段进行洗涤除去有机酸和焦油等杂质。
司炉工段主要提供开工所需蒸汽和补充生产所需蒸汽,同时焚烧反应吸收的尾气及装置产生的部分废液,达到清洁生产的目的。
生产过程中原料正丁烷、溶剂及水电气消耗的控制是决定生产成本的直接因素,本文着重分析主要物料中原料、溶剂消耗的影响因素及控制。
1正丁烷消耗分析及控制1. 主要因素分析1.1 气体分离控制不好,正丁烷纯度低,导致反应副产物增加,目的产品减少,收率下降。
1.2 反应状态控制不佳,收率低,同时由于副产物的影响,容易导致系统堵塞或导致离心机无法有效分离,进一步造成消耗上升。
- 1、下载文档前请自行甄别文档内容的完整性,平台不提供额外的编辑、内容补充、找答案等附加服务。
- 2、"仅部分预览"的文档,不可在线预览部分如存在完整性等问题,可反馈申请退款(可完整预览的文档不适用该条件!)。
- 3、如文档侵犯您的权益,请联系客服反馈,我们会尽快为您处理(人工客服工作时间:9:00-18:30)。
1.概要
常州瑞华化工目前设计并转让的单套5万吨正丁烷法顺酐采用了溶剂吸收法。
溶剂吸收工艺相比于水吸收工艺,有着顺酐收率高、装置能耗低的优点。
传统的溶剂吸收工艺在装置运行时往往存在系统堵塞、溶剂消耗量大、废水处理困难等问题。
为此,瑞华化工针对这些问题进行了深入的研究并设计出更新的技术:开发出最优化的解决方案,最大限度地发挥溶剂吸收工艺的优势。
2.装置经济性
正丁烷法顺酐的后处理,有水吸收和溶剂吸收两种工艺。
水吸收法具有流程短、设备投资省、工艺成熟等优点。
但不足之处在于吸收及脱水操作时,温度控制不当易生成富马酸杂质。
富马酸的大量生成除了影响装置的顺酐收率外,更严重的危害在于,富马酸易和丙烯酸聚合成胶状物,堵塞塔盘,严重时甚至会造成塔盘脱落。
该聚合胶状物的存在严重影响了塔效率,造成了脱水操作的能耗增加;又由于该胶装物无法用水洗除去,必须用碱液蒸煮,这不仅增加了废水量及废水处理难度,同时也造成脱水工序无法连续进行。
间歇操作时装置蒸汽不易平衡,另外操作工人的工作强度也随之增加。
溶剂吸收工艺的吸收过程没有顺酐水合成顺酸的过程。
尽管由于反应系统中带水仍会有少量顺酸生成,进而异构成富马酸,但生成量比水吸收工艺少得多,装置堵塞的可能性同时降低了许多。
这不仅使顺酐后处理工艺的回收率比水吸收法高(约3~5%),也提高了装置的操作稳定性,增加了生产时间,提高了经济效益。
此外,由于没有顺酐水合成顺酸的过程,也就无需相应的脱水过程,顺酐后处理操作消耗的蒸汽量减少,节约了能耗。
以5万吨/年正丁烷氧化法顺酐规模计算,水吸收与溶剂吸收的经济性比较如下表:(价格以2014年各项价格粗略估算。
其中未包括计算人工、维修、仓储、运输、财务成本等费用)
表1 水吸收与溶剂吸收的经济性比较
估算值。
由表1可见,溶剂吸收法的处理成本比普通水吸收法每吨低近900元,这是较为可观的数据。
除去正常运转中的操作成本比较,常州瑞华化工的溶剂吸收工艺,充分配置了装置堵塞的解决方案。
能使装置连续稳定运行,周期可达6~12个月。
这大大降低了停车清洗的频次,增加装置的稳定生产时间,提高装置产能。
在顺酐市场好的情况下,能创造更多的效益;停车频次降低,也能降低因停车清洗造成的物耗及能耗,从而提高装置的整体经济效益。
3.运行稳定性
正丁烷法顺酐的水吸收工艺的原理是将反应尾气中的顺酐用水吸收,而顺酐遇水生成顺酸,再将顺酸水溶剂脱水得到顺酐。
首先,由于顺酸脱水时,在高温条件下易异构成富马酸,富马酸又会与丙烯酸聚合成高沸点的物质,这使得脱水塔极易堵塞;其次,由于正丁烷法顺酐在反应过程中加入了蒸气,使得产物中的顺酸相比于苯法工艺要高得多,顺酸的熔点比顺酐高得多,为134 ℃,在水吸收工艺的部冷器及溶剂吸收工艺的二冷器中非常容易在管道中凝固堵塞;另外,由于正丁烷法顺酐工艺在反应时会生成少量丙烯酸,而
丙烯酸本身极易聚合,这也使得精制塔顶冷凝器极易堵塞。
由于以上三点,水吸收法装置的稳定性很差,几乎半个月就会发生装置堵塞问题,需要停车清洗,这不仅需要花费人力物力,也使得装置开工率不足,整体影响了装置效益。
因而,许多工厂开始采用溶剂吸收法来生产顺酐,尽管传统的溶剂吸收法能降低装置堵塞清洗的频次,但由上述系统堵塞的原因可知,溶剂吸收法并不能避免装置堵塞的可能。
为了更好的解决装置堵塞问题,瑞华化工的顺酐溶剂吸收工艺中运用了大量防堵专利技术,这些技术已在国内数十套苯乙烯装置中成功应用,能够保证顺酐溶剂吸收装置能长期稳定运行,最长不停车操作时间有望达一年。
这些技术总结为以下几个方面:
1.采用非水溶剂吸收工艺
采用溶剂吸收的好处是,顺酐不必水合生成顺酸,这减少了顺酸异构成富马酸,从而减少富马酸和丙烯酸聚合生成聚合物的可能,这不仅提高了顺酐收率,也减小了装置堵塞的可能。
2.先进的二冷系统
在以往的顺酐装置中,二冷器是堵塞的重灾区,因而瑞华化工采用了以下技术来保证二冷器的正常生产:
①采用更高的二冷出口温度,减少顺酸、富马酸结晶的可能;
②采用在二冷器进口加溶剂的方案,将结晶出的顺酸、富马酸等高凝固点物质溶解
带出;
③采用一开一备的工艺设计,能够确保装置不停车,保障装置连续生产。
3.设置顺酸脱水塔
吸收塔底的富溶剂在进入解吸塔之前先经过顺酸脱水塔脱水,以减少富溶剂中的顺酸含量,这不仅能得到更多的顺酐产品,也能减少顺酸在解吸塔内的含量,从而减少富马酸含量,减少了解吸塔的堵塞可能。
4.解吸塔再沸器采用一开一备
解吸塔再沸器操作温度高,在生产过程中,溶剂中会富集苯酐、富马酸、重质物等,这些高凝固点的物质容易造成解吸塔再沸器系统的堵塞,因而采用一开一备的形式能保证装置堵塞时不停车连续生产。
5.精制塔采用间歇操作
精制塔在操作时,顺酐中的丙烯酸易在塔顶聚合,进而堵塞精制塔顶冷凝器,因而采用间歇操作,批次生产,不仅能有效控制每批顺酐产品的质量,还能在发生堵塞时及时清理,保证前系统正常连续操作。
4.废水,废气包括固废的处理
尽管溶剂吸收相较于水吸收工艺来说有诸多优点,但溶剂吸收也存在溶剂的损耗、降解、溶剂回收工艺较复杂等问题,另外,目前溶剂吸收工艺最大的难点是溶剂再生时产生的大量废水的处理,这限制了溶剂吸收工艺的推广。
在常州瑞华化工工程技术有限公司的溶剂吸收工艺中,对废水、废气及固废处理均有周到的考虑。
目前的溶剂再生工艺多为水洗、离心、脱水三步法,在水洗过程中会产生大量废水,由于废水中主要含有反应生成的乙酸、丙烯酸、顺酸、富马酸等有机酸,还含有一些溶剂水解的产物。
为了处理这些酸性废水,瑞华化工的工艺先采用三效蒸发装置将废水进行浓缩,被蒸出来的水则送入液环式真空泵做密封液后,再送入溶剂水洗罐水洗溶剂,如此循环利用,大大降低了装置产生的废水量;而浓缩后的酸水则送入尾气饱和塔,被尾气带入焚烧炉进行焚烧,生成CO2和H2O,实现了废水的零排放。
目前,瑞华化工拥有成熟的三效蒸发废水处理的成套技术,能够提供完整的撬装设备,模块化的理念方便与现有装置或新建装置进行无缝对接,减少多前期的设备投资,并能有效保证设备的稳定运行。
当然,对于现有三效蒸发装置,我们也能提供专业的技术服务。
顺酸装置的尾气,瑞华化工的处理方法是,将尾气进行充分的回收处理,回收其中的顺酐后,余下的废气送入焚烧炉,烧掉废气中的有机物,同时副产蒸汽以回收热量。
废水与废水的处理采用同一个焚烧炉,这样既减少了投资,也能实现废水与废气焚烧时的热量互补,利于节能。
顺酸装置的固体废物,主要是来自精制塔釜及离心机的焦油。
焦油主要由各种聚合物组成,形态为胶状物。
瑞华化工的处理方法是,先将各设备的焦油全部收集起来,然后用固废焚烧炉进行焚烧处理。
至此,顺酐装置产生的三废已完全妥善处理,在瑞华化工的溶剂吸收工艺中,仅用焚烧炉便能将顺酐装置产生的三废全部处理。
由于这些三废均来自于生产装置,焚烧炉内仅加入燃料气,并没有外加其它化学品进行处理,因而这些三废在焚烧处理过程中,仅生成CO2和H2O,能满足废气排放要求。
5.初步预算(设计/设备/工程)
对于我们在5万吨/年顺酐项目上,溶剂吸收单元的设备统计及设备价格及工程投资及费用总和估算约为5千万元。
6.改造周期
初步估计,溶剂吸收工艺建设的整个周期约为6~9个月。
1)工艺包设计 1个月
2)工程设计制造 4~6个月3)安装调试 1~2个月。