汽车轮毂冲击的与实验分析
轮毂的轮毂中心盖的测试

轮毂的轮毂中心盖的测试轮毂的轮毂中心盖是一部车辆最重要的组成部分之一,可以有效地保护轮毂,并增加整车的美观性和品味。
因此,对于车辆制造商而言,轮毂中心盖的质量和性能测试非常重要,这有助于确保车辆的安全性和可靠性。
在本文中,我们将探讨轮毂中心盖的测试,包括其作用、测试方法和测试结果的分析。
1. 轮毂中心盖的作用轮毂中心盖最基本的作用是保护轮毂免受损坏和污损。
由于轮毂处于车轮部件的最外侧,因此它们直接受到路面,尘土,石子等因素的影响。
轮毂中心盖可以有效地保护轮毂和轮毂螺栓,防止这些零件受到损坏,使汽车车轮正常运转并确保驾驶者和乘客的安全。
除了保护轮毂的作用之外,轮毂中心盖还可以为车辆增加美观度。
轮毂中心盖通常被设计为具有车辆标志、品牌或型号的标志,以引起人们对车辆的关注和兴趣。
因此,车辆制造商通常将轮毂中心盖视为一种宣传工具,从而提高消费者对其品牌和产品的认知度和接受度。
2. 轮毂中心盖的测试方法为确保轮毂中心盖的性能和质量,车辆制造商通常会进行各种测试和评估。
以下是轮毂中心盖的三种最常用的测试方法:2.1 冲击测试在车辆在行驶中或从路面上碰到障碍物时,轮毂中心盖会受到物理撞击。
因此,在制造轮毂中心盖时,必须评估其抗冲击性,以确保其耐用性和可靠性。
冲击测试通常会通过使用特殊的测试设备模拟车辆行驶过程中的撞击,从而评估轮毂中心盖的抗冲击性,确定其是否符合安全标准。
2.2 耐用性测试耐用性测试是指在模拟车辆实际使用场景时,对轮毂中心盖做全面的测试。
此类测试评估轮毂中心盖是否耐用且可靠,是否能够承受车辆在特定工况下的负荷和压力。
这种测试通常需要应用特定的机器设备进行模拟,以确保轮毂中心盖在具有挑战性的条件下的性能表现。
2.3 光泽度和防滑性测试在轮毂中心盖的设计中,如何保持其光泽和增加防滑性是两个关键因素。
因此,进行光泽度测试和防滑性测试非常必要。
光泽度测试涉及轮毂中心盖表面的反射水平,以及其表面处理技术的效果。
轮毂单元泥浆盐水冲击试验规范

Q/WQZ166-2000 轮毂单元泥浆/盐水冲击试验规范1.0 范围本标准适用于轿车和轻型卡车前、后轮毂轴承单元内、外密封圈的密封性试验,用来评价轮毂单元密封系统的密封性能。
2.0 引用标准STI—07J 德尔福轮毂轴承泥浆/盐水冲击测试3.0 试验规范3.1 记录形式所有的试验数据都要记录在STI—07J《德尔福轮毂轴承泥浆/盐水冲击测试》试验记录单上。
3.2 设备要求试验设备应满足各试验参数的要求,且符合试验方法的要求。
3.2.1保持输入负荷不超过5%。
3.2.2保证载荷循环时间不超过3%。
3.2.3保证试验转速误差不超过2%。
3.2.4测量和记录轴承单元在轮毂外径表面的温度。
3.2.5控制试验轴承单元试验时的振动值。
3.2.6保证泥浆/盐水的喷溅循环按规定要求执行。
3.2.7保证载荷、电流、试验温度、振动值超标时能自动停机。
3.2.8保证水泵的流量及压缩空气的压力。
3.2.9保证泥浆/盐水的配制比例。
3.2.10 有能保证混合液循环的水箱和管路。
3.2.11 所有的控制元件应校准,且在规定的到期时间内。
Q/WQZ166-20003.3 试验轴承样品3.3.1试验轴承样品应是经检测符合图纸要求的合格品,每一批次随机抽样八套,其中六套作为试验样品,另两套备用。
3.3.2在样品的非基准面上逐套编号,批与批,套与套不得重号或缺号,每种轴承编号的位置应一致。
3.4试验方法3.4.1 定义3.4.1.1 径向负荷是一垂直于轴承旋转轴线且作用于车轮中心线的一恒力。
3.4.1.2 轴向负荷是一平行于试验轴承旋转轴线的一周期性循环力。
它与旋转轴线的距离等于车轮旋转半径。
3.4.1.3气管为1/4″×0.03″的软铜管。
3.4.1.4水管直径为3/8″。
3.4.1.5如果试验轴承出现任何包括面积为0.01平方英寸(6.452平方毫米)或更大的剥落,则应视为失效。
(失效是通过声音及振动来确定的)3.4.2安装3.4.2.1试验轴承必须履行下列检查:a、记录轴承的重量,精确到十分之一克。
《2024年铝合金轮毂的力学性能及有限元分析》范文

《铝合金轮毂的力学性能及有限元分析》篇一一、引言随着汽车工业的快速发展,铝合金轮毂因其轻量化、高强度、耐腐蚀等优点,逐渐成为现代汽车的重要部件。
了解铝合金轮毂的力学性能及进行有限元分析,对于提高其设计水平、优化结构、增强安全性能具有重要意义。
本文将重点探讨铝合金轮毂的力学性能及有限元分析方法。
二、铝合金轮毂的力学性能1. 强度与刚度铝合金轮毂的强度和刚度是评价其力学性能的重要指标。
铝合金材料具有较高的屈服强度和抗拉强度,使得轮毂在承受载荷时能够保持较好的稳定性。
此外,铝合金轮毂的刚度也较高,能够有效地抵抗弯曲和扭曲变形。
2. 耐疲劳性能铝合金轮毂在使用过程中需要承受周期性载荷,因此其耐疲劳性能尤为重要。
铝合金材料具有良好的耐疲劳性能,能够在长期使用过程中保持较好的机械性能。
此外,通过合理的结构设计,可以进一步提高铝合金轮毂的耐疲劳性能。
3. 抗冲击性能铝合金轮毂在行驶过程中可能会受到意外冲击,因此其抗冲击性能也是评价其力学性能的重要指标。
铝合金材料具有较好的吸能和缓冲性能,能够在受到冲击时吸收部分能量,减少对轮毂本身的损伤。
三、铝合金轮毂的有限元分析有限元分析是一种有效的工程分析方法,可以用于研究铝合金轮毂的力学性能。
通过建立轮毂的三维模型,并利用有限元软件进行网格划分、材料属性赋值、边界条件设定等操作,可以实现对轮毂的力学性能进行仿真分析。
1. 网格划分与材料属性赋值在有限元分析中,首先需要对轮毂进行网格划分,将轮毂离散化为有限个单元。
然后,为每个单元赋予铝合金材料的属性,如弹性模量、密度、泊松比等。
这些属性将直接影响有限元分析的结果。
2. 边界条件设定与加载在有限元分析中,需要设定轮毂的边界条件,如约束轮毂的旋转自由度等。
然后,在轮毂上施加载荷,如径向力、侧向力等。
这些载荷将用于模拟轮毂在实际使用过程中的受力情况。
3. 仿真结果分析与优化设计通过有限元分析软件进行计算,可以得到轮毂在各种工况下的应力、应变、位移等结果。
车轮过凹坑冲击力计算

车轮过凹坑冲击力计算全文共四篇示例,供读者参考第一篇示例:车轮通过凹坑时会受到冲击力的影响,这个冲击力不仅会对车轮本身产生影响,还会对整个车辆的运行稳定性产生影响。
对车轮过凹坑冲击力的计算显得尤为重要。
在车辆行驶时,车轮通过凹坑时会面临一个瞬时的冲击力。
这个冲击力的大小取决于凹坑的深度、长度以及车辆速度等因素。
而具体如何计算这个冲击力呢?下面我们将来介绍一种常用的方法。
我们需要了解一下车轮通过凹坑时的动力学原理。
当车轮通过凹坑时,车轮会受到一个向上的冲击力,这个冲击力的大小可以用冲量来表示。
冲量是冲击力随时间的积分,可以用下面的公式来表示:\[J = \int F(t)dt\]\(J\)是冲量,\(F(t)\)是冲击力随时间的变化函数。
通过计算冲量,我们可以得到车轮通过凹坑时的冲击力大小。
接下来,我们需要考虑到凹坑的形状对冲击力的影响。
一般来说,凹坑的深度和长度越大,车轮受到的冲击力也会越大。
车辆的速度对冲击力也会有影响,速度越快,车轮受到的冲击力也会越大。
综合考虑以上因素,我们可以得到一个关于车轮通过凹坑时冲击力大小的计算公式。
具体计算过程比较复杂,需要考虑到车轮的弹性变形、凹坑的形状等因素,一般需要通过数值模拟方法来进行计算。
除了计算车轮通过凹坑时的冲击力大小,我们还需要考虑到减少冲击力的方法。
一种常见的方法就是通过调节悬挂系统来减少冲击力。
悬挂系统可以起到缓冲作用,减少车轮受到的冲击力,提高车辆的行驶稳定性。
选择合适的轮胎也可以减少车轮受到的冲击力。
一般来说,高弹性的轮胎可以起到一定的缓冲作用,减少车轮受到的冲击力。
对车轮通过凹坑时冲击力的计算是一个复杂的问题,需要考虑到多种因素。
通过合理的计算和控制,可以减少车轮受到的冲击力,提高车辆的运行稳定性。
希望以上内容可以对大家有所帮助。
第二篇示例:车轮过凹坑是指车辆在行驶过程中,轮胎与路面遇到凹坑或凸起时所产生的冲击力。
这种冲击力会对车辆的悬挂系统、车轮及车身结构造成影响,甚至会影响乘坐者的舒适感和安全性。
乘用车车轮台车冲击试验方法

乘用车车轮台车冲击试验方法1范围本文件规定了一种实验室试验方法,用于评价乘用车车轮在路试或服役过程中通过路面障碍物时的抗冲击性能。
本文件适用于GB/T 3730.1中规定的乘用车所使用的车轮。
转向节、控制臂、副车架等底盘结构件也可参照使用。
2规范性引用文件下列文件中的内容通过文中的规范性引用而构成本文件必不可少的条款。
其中,注日期的引用文件,仅该日期对应的版本适用于本文件;不注日期的引用文件,其最新版本(包括所有的修改单)适用于本文件。
GB/T 29332004,IDT 充气轮胎用车轮和轮辋的术语、规格代号和标志(GB/T 2933-2009,ISO 3911:)GB/T 3730.13汽车和挂车类型的术语和定义(GB/T 3730.1-2001,ISO 3833:1999,MOD )术语和定义GB/T 2933界定的以及下列术语和定义适用于本文件。
试验台车Test Sled 一台用于模拟真实车辆车架结构的台车。
其底盘为原车底盘或与原车等效的底盘,底盘安装参数与原车一致,底盘动力学性能与原车一致。
试验台车可以适配不同的底盘,在车身上可以按照原车质量分布进行配重,如图1。
台车冲击试验Impact Test by Sled 一种将原车或与原车等效的底盘安装到试验台车上,在实验室内由牵引系统将试验台车加速到目标速度后,单侧车轮通过安装在地面的障碍物,对车轮进行冲击,以评定其抗冲击性能的试验方法。
车轮轮胎总成Wheel-tire Assembly由车轮、轮胎和气门嘴组装成的组合件。
障碍物Obstacle 障碍物是指具有可模拟试车场或用户工况中路面冲击物形貌,且有足够刚性的钢制凸起物,如图2。
裂纹Crack 试验过程中出现的材料分离,扩大至3mm 及以上的情形。
4试验设备牵引系统牵引系统是牵引试验台车的动力系统,最大牵引质量应大于试验台车总质量。
试验过程中,牵引系统牵引试验台车达到目标速度,牵引速度误差精度±1km/h 。
GBT15704一1995轿车车轮冲击试验方法

GBT15704一1995轿车车轮冲击试验方法轿车车轮冲击试验方法Passenger cars一Wheels一Impact test procedure本标准等效采纳国际标准ISO 7141:1981(E)《道路车辆—车轮—冲击试验规程》。
1 主题内容与适用范畴本标准关于轿车内使用的车轮,规定了评判轴向(横向)路边石冲击的最低性能要求及台架试验方法。
本标准适用于由全部或部分轻合金制造的车轮。
钢制车轮也可参照使用。
2 引用标准GB/T 2933充气轮胎用车轮和轮辋术语、规格代号和标志3 定义见GB/T 2933。
4 试验样品试验用的车轮应是未经试验或使用的新成品车轮。
5 试验条件在车轮上施加冲击力的位置,除本标准7.5规定的径向位置外,在车轮周向应是最容易发生破裂、变形、空气泄漏等故障的部位。
试验环境温度为10~38℃。
6 试验设备试验设备是一个能够将冲击载荷施加到装有轮胎的车轮的轮辋轮缘上的装置。
为了使垂直下落的冲头能与轮辋的最高点接触,按车轮轴线与冲头垂直下落方向成13°士1°角的方式安装车轮。
冲头的冲击面长不小于375mm,宽不小于125mm。
为适应各种规格和形状的车轮做冲击试验,整个车轮支架的位置应能够调剂(见图1)。
试验设备应作如下校正:把校正装置放在如图2所示的车轮底座上,其1 000 kg的重量作用于车轮安装中心,测量钢板梁中心处在垂直方向的弯曲变形量,应为7.5mm土10%。
7 试验方法7.1 试验用轮胎试验用的轮胎应选用在车辆或车轮制造厂与该车轮相匹配的,最小公称断面宽度的无内胎轮胎。
轮胎的充气压力必须按车辆制造厂的规定,如无此规定, 可按200kPa充气。
7.2 冲头质量的确定7.3 车轮安装把试验车轮轮胎总成安装在与车辆轮毂一致的连接盘上。
车轮安装时,要按车辆或车轮制造厂举荐的方法或用手工拧紧至规定值。
7.4 调整冲头下落高度冲头的下落高度应在轮辋轮缘的最高点上方230±2mm。
侧向冲击对轮毂轴承性能影响的试验研究

5 379
5 920
6 157
6 378
速度载荷以上ꎬ滚道接触应力已超过 4 200 MPaꎬ达到
加ꎬ在相同侧向载荷条件下ꎬ轴承外侧滚道的应力比内
侧滚道应力更高ꎮ
3. 2 压痕深度分析
笔者对完成压痕试验后的样品进行拆解、清洗ꎬ
5 458
然后利用圆度仪对各个拆解零件的滚道进行逐行扫
6 007
处位置的压 痕 数 据ꎬ第 一 处 是 滚 道 最 大 压 痕 深 度 同
试验规范 [9ꎬ10] ꎬ笔者以 2 kN / s 的加载速率在车轮半径
处加载ꎬ然后在 1 s 内释放全部载荷ꎮ
试验原理图如图 3 所示ꎮ
图 1 驱动轮轮毂轴承安装状态
车轮在路面行驶时ꎬ冲击模式表现为两种:侧向冲
击和正向冲击ꎮ 其中ꎬ侧向冲击载荷的力臂为车轮半
径ꎬ而正向冲击载荷的力臂为车轮偏距ꎬ因车轮半径远
way contact stress and indentation depth. Finallyꎬ the vibration noiseꎬ moment rigidity and endurance life test of the bearing with indentation
defect were carried outꎬ and the test results were extracted and analyzed to characterize the influence of the indentation defect of the raceway
1 冲击路况对轮毂轴承特性的影响
样品ꎬ在数据处理时ꎬ取平均值进行分析ꎮ
笔者以轴承单元为研究对象ꎬ其轴承结构及与周
边转向节、驱动轴、刹车盘、轮辋、轮胎匹配关系ꎬ如图
铝合金车轮的有限元强度分析及试验验证
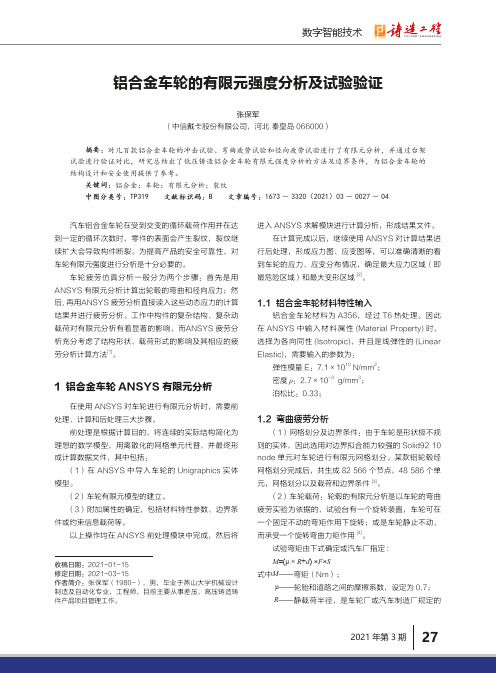
铝合金车轮的有限元强度分析及试验验证汽车铝合金车轮在受到交变的循环载荷作用并在达到一定的循环次数时,零件的表面会产生裂纹,裂纹继续扩大会导致构件断裂。
为提高产品的安全可靠性,对车轮有限元强度进行分析是十分必要的。
车轮疲劳仿真分析一般分为两个步骤:首先是用ANSYS有限元分析计算出轮毂的弯曲和径向应力;然后,再用ANSYS疲劳分析直接读入这些动态应力的计算结果并进行疲劳分析。
工作中构件的复杂结构、复杂动载荷对有限元分析有着显著的影响,而ANSYS疲劳分析充分考虑了结构形状、载荷形式的影响及其相应的疲劳分析计算方法[1]。
1 铝合金车轮ANSYS有限元分析在使用ANSYS对车轮进行有限元分析时,需要前处理、计算和后处理三大步骤。
前处理是根据计算目的,将连续的实际结构简化为理想的数学模型,用离散化的网格单元代替,并最终形成计算数据文件,其中包括:(1)在ANSYS中导入车轮的Unigraphics实体模型。
(2)车轮有限元模型的建立。
(3)附加属性的确定,包括材料特性参数、边界条件或约束信息载荷等。
以上操作均在ANSYS前处理模块中完成,然后将进入ANSYS求解模块进行计算分析,形成结果文件。
在计算完成以后,继续使用ANSYS对计算结果进行后处理,形成应力图、应变图等,可以准确清晰的看到车轮的应力、应变分布情况,确定最大应力区域(即最危险区域)和最大变形区域[2]。
1.1 铝合金车轮材料特性输入铝合金车轮材料为A356,经过T6热处理。
因此在ANSYS中输入材料属性(Material Property)时,选择为各向同性(Isotropic),并且是线弹性的(Linear Elastic),需要输入的参数为:弹性模量E:7.1×1010 N/mm2;密度ρ:2.7×10-3 g/mm3;泊松比:0.33;1.2 弯曲疲劳分析(1)网格划分及边界条件:由于车轮是形状极不规则的实体,因此选用对边界拟合能力较强的Solid92 10 node单元对车轮进行有限元网格划分。
- 1、下载文档前请自行甄别文档内容的完整性,平台不提供额外的编辑、内容补充、找答案等附加服务。
- 2、"仅部分预览"的文档,不可在线预览部分如存在完整性等问题,可反馈申请退款(可完整预览的文档不适用该条件!)。
- 3、如文档侵犯您的权益,请联系客服反馈,我们会尽快为您处理(人工客服工作时间:9:00-18:30)。
倡2013年11月
第19卷第4期安庆师范学院学报(自然科学版)
JournalofAnqingTeachersCollege(NaturalScienceEdition)Nov.2013
Vol.19No.4
网络出版时间:2013-12-1920:16 网络出版地址:http://www.cnki.net/kcms/detail/34.1150.N.20131219.2016.021.html汽车轮毂冲击的CAE与实验分析
闫胜昝1,童水光2,朱训明3(1.安庆师范学院计算机与信息学院,安徽安庆246133;2.浙江大学工业技术研究院,浙江杭州310027;3.万丰奥特集团,浙江新昌312500)
摘 要:针对汽车车轮冲击试验,通过动态响应有限元分析,确定车轮结构中的最大应力及危险位置,并通过实验应力分析,利用动态电阻应变仪等,测定并计算车轮结构中关键点的应力响应,利用MATLAB计算并绘制VonMises应力响应曲线。通过对比有限元分析与实测结果,提出修正系数,对有限元分析模型进行修正,该结果可用于企业的车轮设计,提高产品结构设计的一次合格率。关键词:冲击试验;CAE分析;动态响应;实验应力分析;动态电阻应变仪中图分类号:U463.34,O313,O348文献标识码:A文章编号:1007-4260(2013)04-0076-03
汽车车轮作为关键的汽车零部件之一,直接影响汽车的安全性,而安全性也是汽车设计的第一要求。汽车行驶中车轮高速转动,介于地面和汽车所有其他部件之间,承载着汽车、乘客等重力载荷,还有可能承受由于加速、减速和转弯等带来的附加载荷,车轮结构设计不仅要考虑美观,而且还要考虑可铸性,最重要的是要能够承受其应承受的载荷,才具使用性和安全性。因此,在车轮结构设计中,首先要使其满足强度要求,一般在车轮批量生产之前,必须通过冲击试验、径向滚动疲劳试验和弯曲疲劳试验。即便是在批量生产之前进行试验可避免大批量的报废,要得到试验用车轮仍需付出高昂代价,从车轮设计、模具设计、模具开制、上模具、小批生产、下模具,无论是时间还是成本,都是一个不小的支出。而小批量生产的车轮又不能保证必然通过试验,就有可能会造成更大的时间和成本的浪费。随着FEA技术的不断成熟和广泛应用,借助CAE在车轮的设计之初,对其进行针对三个性能试验的分析计算,将有助于缩短新产品开发周期、降低新产品开发成本。因此,利用CAE对车轮结构进行强度分析、寿命预测,从而优化设计就成为新产品开发的必要条件[1]。对车轮结构性能试验有限元分析方法的
研究成为热点之一。在受力模型较简单的疲劳试
验中,在掌握材料的N-S曲线后,疲劳寿命的预测是可行的[2,3]。而在冲击试验中存在复杂的冲
撞问题,结构模型还包含轮胎,是复杂的非线性问题,小西晴之等人在车轮的冲击强度上做过部分研究[4]。本文主要通过对车轮冲击试验的有限
元分析,利用动态响应的分析方法,分析车轮结构中的危险位置及最大应力等情况,并用实验应力分析方法对车轮冲击试验中的应力进行测量,再通过实验结果与分析结果的比较,提出对有限元分析模型的修正系数,从而可用车轮冲击试验有限元分析指导新产品设计,缩短其开发周期。
1 有限元分析模型1.1冲击试验根据GB/T15704-1995标准,将装有轮胎的车轮固定在试验装置上,施加一个冲击力,冲击后检查,轮辐无目测可见的穿透裂纹,轮辐不能从轮辋上分离,轮胎气压不会在60s内漏尽,才表明车轮通过冲击试验。摩托车车轮主要需进行90°冲击试验,而汽车车轮主要是进行13°冲击试验,将车轮安装在一个与水平地面成13°角的安装盘上,重锤质量根据车轮最大静载荷的0.6倍加180kg计算得到,下落高度固定为(230±2)mm,
倡收稿日期:2013-07-03作者简介:闫胜昝,女,河北辛集人,博士,安庆师范学院计算机与信息学院讲师,主要专业方向为机械CAD/CAE、模拟仿真、计算机技术应用。冲击后无肉眼可见的裂纹即为合格。 1.2 分析模型采用I-DEAS有限元分析软件,对在冲击载荷作用下车轮结构内的应力、应变、变形等进行分析。铝合金材料的弹性模量为6.9×104MPa,泊松比0.33,密度2.69×103kg/m3。对车轮结构实体模型,采用四面体和节点体单元进行网格单元划分,网格划分越细密分析结果越精确,但计算时间越长,而网格划分太粗大分析结果精度又不够,但计算时间会较短,因此,需综合考虑,此处根据车轮结构的尺寸,取单元大小为8mm。将车轮结构旋转到与水平方向成13°夹角,在车轮安装盘面及几个PCD孔进行全约束。首先进行动态响应分析,然后在响应分析模块进行强迫运动分析,指定冲击接触点及竖直冲击方向,设置重锤位置在与轮辋重叠(25±1)mm(与试验相同)的地方,指定根据标准计算得到的重锤质量为555kg,下落高度230mm,设定冲击过程在0.5s内完成,假设冲击过程中载荷F(t)的分布服从半正弦函数分布(力从零到峰值再到零[6]),并设定衰减系数
4%(轮胎的吸能作用[7])。 1.3 分析结果由以上分析得到车轮结构内的应力分布情况如图1所示,t=0.25s时为F(t)取最大值的时刻,由图1可看出该车轮结构中应力分布比较均匀,最大应力位于施加冲击载荷位置正对的辐条上,最大Mises应力120MPa,远远低于材料的抗拉强度极限240MPa(对该车轮进行实际取样,测量机械性能得出的结果)。因此,单从冲击试验有限元分析结果来看,该车轮结构还有进一步优化的潜力,但是有限元分析的算法本身导致其结果必然存在一定误差,分析结果的分布趋势虽是完全可靠的,却不能保证有限元分析结果的数值与实际的应力值完全一致,这也正是要进行实验应力测量的原因。
图1 车轮结构的应力分布(t=0.25s)
2 实验应力分析冲击过程完成于一瞬间,详细观察这些现象必须依赖于实验。本文采用技术成熟、操作简单、成本低廉的电阻应变计法进行车轮冲击动态响应实验应力分析,所使用的仪器设备和分析软件如表1所示,试验装置及测点如图2所示。按试验要求安装测试用轮胎,并充气达到试验要求2×105Pa,然后在车轮上粘贴45°应变花,
连接导线,如图2所示。调整冲锤重量及下落高度后,预热动态电阻应变仪,清零、标定、设定采集文件,由于冲击时间很短,为了避免漏掉数据,先点击开始测量,再开始对车轮的冲击试验。冲击位置与有限元分析中加载位置相同,对贴有应变片的辐条正对的轮辋进行冲击(冲击范围按试验标准要求,在重锤与轮辋重叠(25±1)mm的范围内)。
・77・第4期 闫胜昝,童水光,等:汽车轮毂冲击的CAE与实验分析表1 车轮冲击动响应实验仪器设备与分析软件名 称型 号13°车轮冲击试验机IMT-V1,VIAC-152-②电阻应变计BX120-3CA(XX)动态电阻应变仪CS-1A数据采集仪CDSP分析软件Vib’SYS图2 试验装置
对采集到的数据,利用MATLAB进行处理,得到并绘制vonMises应力响应曲线,如图3所示。由图示结果可以看出,在同一根辐条上如图2所示两点测得的应力,由于车轮结构的对称性,其变化趋势及数值均十分接近。由于先点击开始测量,后进行冲击,开始一段时间的应力为零。另外,从vonMises应力的结果可以看出,这两点在整个冲击试验过程中应力出现连续的几个峰值,且逐渐变弱。这一测量结果与实际完全一致,冲击中冲锤首先接触轮胎,轮胎作为高弹性元件,引起冲锤的弹跳,并且在轮胎的吸能作用下,逐渐静止下来。A,B两点测量得到的最大Mises应力分别为201.8MPa和208.4MPa,与有限元分析结果比较偏大,误差在41.5%左右。这些误差主要来自于模型的简化以及载荷谱的假设,因此对于车轮冲击试验的有限元分析,模型的建立还需完善,载荷谱最好能实测得到。目前,在没有建立更合理的有限元分析模型之前,通过大量实验与分析结果的比较,可采用修正系数1.7~2.0来弥补,即采用本文建立的分析模型,施加的载荷应乘以该修正系数,相当于动载系数,计算得到的应力峰值才与实测值更接近。
图3 A,B两点vonMises应力响应测量结果(下转第120页)
・87・安庆师范学院学报(自然科学版) 2013年ImplementationofDelayFunctionofMicrocontrollerUnitbyUsingCLoopStatementsXULei,SUNChang-zhi(Departmentofchemicalandphysical,BozhouTeachersCollege,Bozhou,Anhui236800China)
Abstract:Delayisoneofthemostcommonlyusedconceptsinmicrocontrollerteaching,anddelayfunctionisanimportantfunctioninthecontrollingprogramsofmicrocontrollerunit.TakeflashingLEDlampsataconstantfrequencylightedbytmsdelay
function,whichrealizedusingwhile,do-while,for,andcombinationofwhileandforloopstatements,asanexample,thedelayfunctionsofmicrocontrollerCloopstatementsaresummarizedtohelpstudentsenhanceunderstandingthedelayconceptsofmicro-controllerunitbasedontheCknowledge.Theresultsshowtheteachingmethodsareverygood.Keywords:microcontrollerunit,Clanguage,delayfunction,loopstatements
(上接第78页)3 结束语CAE分析可弥补由于试验条件限制而不能测量一些数据缺陷,可大大减少试验经费、缩短试验周期,降低新产品的研发成本,缩短研发周期,提高车轮产品结构设计的一次合格率。同时实验分析也表明,利用有限元方法来研究车轮结构的动力学问题是可行的,通过CAE建立公司内部的强度评价标准,提高试验合格率,具有十分重要的应用价值。对于涉及轮胎大变形、轮胎与车轮接触问题以及材料断裂问题的车轮冲击试验,有限元分析结果与实验结果还有一定差距,有限元分析模型相对简单,如能把高弹性的轮胎引入车轮结构的分析模型,利用逆推法或实验测得冲击试验载荷谱作为动响应分析的输入,将能使分析结果更接近于实际,从而取消修正系数,还有待于借鉴更新的CAE技术做进一步研究。