关于精馏塔设备的设计与节能探究
精馏过程的节能途径及新型的精馏技术
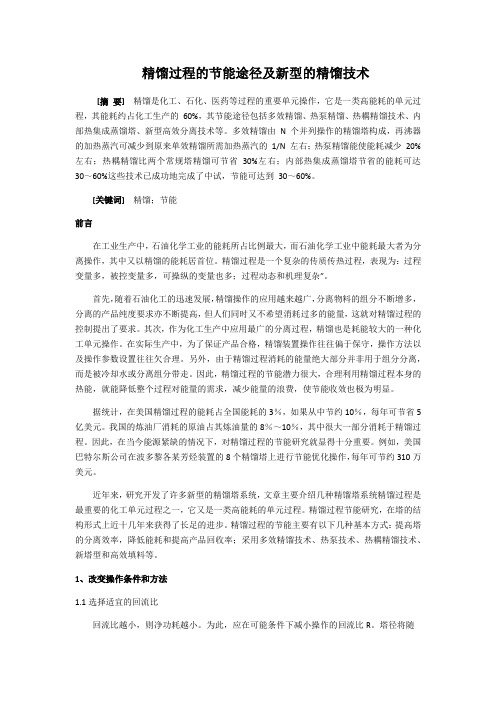
精馏过程的节能途径及新型的精馏技术[摘要]精馏是化工、石化、医药等过程的重要单元操作,它是一类高能耗的单元过程,其能耗约占化工生产的60%,其节能途径包括多效精馏、热泵精馏、热耦精馏技术、内部热集成蒸馏塔、新型高效分离技术等。
多效精馏由N 个并列操作的精馏塔构成,再沸器的加热蒸汽可减少到原来单效精馏所需加热蒸汽的1/N 左右;热泵精馏能使能耗减少20%左右;热耦精馏比两个常规塔精馏可节省30%左右;内部热集成蒸馏塔节省的能耗可达30~60%这些技术已成功地完成了中试,节能可达到30~60%。
[关键词]精馏;节能前言在工业生产中,石油化学工业的能耗所占比例最大,而石油化学工业中能耗最大者为分离操作,其中又以精馏的能耗居首位。
精馏过程是一个复杂的传质传热过程,表现为:过程变量多,被控变量多,可操纵的变量也多;过程动态和机理复杂”。
首先,随着石油化工的迅速发展,精馏操作的应用越来越广,分离物料的组分不断增多,分离的产品纯度要求亦不断提高,但人们同时又不希望消耗过多的能量,这就对精馏过程的控制提出了要求。
其次,作为化工生产中应用最广的分离过程,精馏也是耗能较大的一种化工单元操作。
在实际生产中,为了保证产品合格,精馏装置操作往往偏于保守,操作方法以及操作参数设置往往欠合理。
另外,由于精馏过程消耗的能量绝大部分并非用于组分分离,而是被冷却水或分离组分带走。
因此,精馏过程的节能潜力很大,合理利用精馏过程本身的热能,就能降低整个过程对能量的需求,减少能量的浪费,使节能收效也极为明显。
据统计,在美国精馏过程的能耗占全国能耗的3%,如果从中节约10%,每年可节省5亿美元。
我国的炼油厂消耗的原油占其炼油量的8%~10%,其中很大一部分消耗于精馏过程。
因此,在当今能源紧缺的情况下,对精馏过程的节能研究就显得十分重要。
例如,美国巴特尔斯公司在波多黎各某芳烃装置的8个精馏塔上进行节能优化操作,每年可节约310万美元。
近年来,研究开发了许多新型的精馏塔系统,文章主要介绍几种精馏塔系统精馏过程是最重要的化工单元过程之一,它又是一类高能耗的单元过程。
关于化工精馏节能的思考

科学技术关于化工精馏节能的思考163000 大庆职业学院(黑龙江大庆) 郭鑫【摘 要】现代化工进程对节能工作非常重视,国内外投入大量人力、物力进行节能技术的开发,节能新技术、新工艺、新措施、新方法不断问世。
本文就化工精馏节能进行初步探讨。
【关键词】化工;精馏;节能1、引言在化工生产过程中,分离是非常重要的一个过程单元,它直接决定了最终产品的质量和收率,工业生产中占据着主导地位的分离方法就是精馏,精馏是利用混合物中各组分挥发度的不同,利用能量交换和气液间传质进行分离的单元操作,具有独特的优势。
据估计,化工过程中40%-70%的能耗用于分离,而精馏能耗又占其中的95%。
同时,同时精馏在热力学上是低效的耗能过程,有极高的热力学不可逆性。
因此,在当今世界能源日益短缺的情况下,对精馏过程的节能研究就显得十分重要,它的每一个进展都会带来巨大的经济效益和社会效益。
现代化工进程对节能工作非常重视,国内外投入大量人力、物力进行节能技术的开发,节能新技术、新工艺、新措施、新方法不断问世。
本文就化工精馏节能进行初步探讨。
2、化工精馏节能的有效措施2.1优化操作条件该方法主要是利用模拟软件对精馏过程的操作条件进行研究,精馏塔的主要操作条件包括操作压力、操作温度、塔板压降,进料位置及温度、理论板数、回流比以及回流温度、塔顶塔底采出量、关键组分的清晰分割程度,塔顶塔底热负荷等等,除塔的操作压力一般是给定的(在设计双效流程除外),其它的都可以作为操作变量,通过灵敏度分析、设计规定或者优化技术来确定满足分离任务的最佳值,以获得最小的冷凝负荷和再沸器热负荷,从而使精馏塔能耗最少。
2.2使用中间换热装置对于塔顶塔底温差较大的精馏塔,可通过增设中间换热器的方式来节省或回收热(冷)量。
增设的中间换热器改变了操作线斜率,利用了低品位能源:若塔上部的温度分布存在显著变化时,可在精馏段的某塔板间处设置中间冷凝器,并用低品位冷剂作为冷源,节省主冷凝器高品位冷剂的用量,以减少能耗,但其上方塔板的分离能力有所下降;若塔下方的温度分布存在显著变化,可在提馏段的某塔板问处设置中间再沸器,减少主再沸器高品位热量消耗,由于塔的热能有效降级,使得热效率提高,达到最大的节能效果,但其下方塔板分离能力被削弱,如当乙烯精馏塔装置中间再沸器的热负荷约为提馏段总热负荷的30%时,所节约的能量相当于整塔能耗的17%左右。
精馏的节能技术

分抽提出去。
5.当组分α>2,可考虑简单蒸馏,不必用萃取精馏。
对普通精馏塔所组成的顺序用试探法寻优
一般原则: 1.如果各组分的相对挥发度的范围很宽,则按相对挥发度 递减的顺序逐个从塔顶分离出各组分。这是因为,①先分出α 大的,使后续塔的蒸汽量V下降,塔径减小,操作压力P下降 ,冷凝温度T上升。②产品逐个从塔顶出,塔顶蒸汽量小,冷 凝负荷小。 2.如果各组分在原料中的含量差别比较大,而相对挥发度
如图所示:
需要说明的是,在大 多数情况下,采用上述 的节能技术均会减少操 作费用,但可能增加设 备费用,而且操作会变 得更加复杂,要求有较 高的控制水平。因此需 工业分离问题常常涉及到将多组分混合物分 离成两个以上的产品。尽管一个用复杂方法设计 的分离器有可能得到所需要的多个产品,但广泛 采用的仍是一连串的简单分离器(即一股进料, 两个产品的分离器)。这样就引出了先分离哪个 组分,后分离哪个组分的问题,也就是分离顺序 的问题。一般来说,人们总要寻找最优的或费用 最低的顺序,同时兼顾其它因素,例如可操作性、 可靠性和安全性等问题。
多效精馏
多效精馏的基本方式如图:
采用两效或多效精馏是充分利用能级的一个方法。
不论采用哪种方式,其精馏操作所需的热量与单塔
精馏相比较,都可以减少30~40%。 塔压、液体及蒸汽流动组合方式的确定与分离物 系的相对挥发度、进料中低沸点组分和高沸点组分 的相对比例、进料热状态以及热源蒸汽压力和冷却 介质的温度等有关。
(3)用再沸器液体闪蒸的热泵
当塔底产品是一种好的制冷剂时,塔釜液通过膨胀阀 闪蒸到相应于馏出物饱和温度的压力。塔顶冷凝器又起再 沸器的双重作用。在冷凝器中生成的蒸汽在进塔前被再压 缩到塔底压力。下图为该热泵系统在丙烯-丙烷分离中的应 用。 将釜液闪蒸到496.4kPa,用它来除去冷凝器中所需的
精馏过程节能技术综述

精馏过程节能技术综述现代工业生产过程中,精馏过程是十分常见的一种操作,用于从混合物中分离出不同组分。
然而,传统的精馏过程存在能源浪费的问题,因为它需要大量的能源来进行加热和冷却。
因此,如何降低精馏过程的能源消耗成为了一个重要的研究方向。
在过去的几十年里,研究人员提出了多种节能技术,以下综述了一些常见的节能技术。
首先,改进传统精馏塔的设计是一种简单但有效的节能方法。
例如,使用多级精馏塔可以增加分馏塔的效率,减少需加热和冷却的动力。
此外,增加塔内的换热面积也可以改善能量利用率。
此外,通过使用先进的塔内填料和分布器,可以提高物质的传质效率,从而减少所需的塔高和物料回流比例。
其次,热力耦合是另一种常用的节能技术。
该技术通过将不同温度的流体进行热交换,来降低能源消耗。
例如,实施热力耦合可以将进出精馏塔的气体进行热交换,从而降低所需的加热和冷却负荷。
此外,热力耦合还可以用于塔内热交换,例如通过使用塔内回流来预热进入精馏塔的物料。
另外,采用较低的工艺温度和压力也可以有效地减少精馏过程的能耗。
降低工艺温度可以减少所需的加热负荷,而降低工艺压力可以减少所需的冷却负荷。
因此,在设计和操作精馏过程时,应考虑选取较低的工艺温度和压力,以降低能源消耗。
此外,使用较低的辅助能源,如太阳能、余热等,也是一种常用的节能技术。
太阳能可以用于提供所需的加热或冷却能量,从而降低对传统能源的依赖。
余热是指在其他工艺过程中产生的废热,在精馏过程中可以被回收利用,用于提供所需的加热或冷却能源,进一步减少能源消耗。
最后,引入新的分离技术也是提高精馏过程能耗效率的一种途径。
例如,膜分离技术被广泛应用于分离混合物中的气体或液体组分,并且其能耗通常较低。
相比传统的蒸馏过程,膜分离技术不需要额外的加热和冷却能源,因此能够有效地节约能源。
总的来说,精馏过程节能技术的研究和应用对能源的合理利用具有重要意义。
通过改进传统精馏塔的设计、热力耦合、降低工艺温度和压力、使用低辅助能源和引入新的分离技术等方法,可以有效地降低精馏过程的能耗。
精馏塔控制和节能优化研究综述

精馏塔控制和节能优化研究综述摘要:在工业生产流程内,精馏塔属于常用装置类型之一,其能够在制造环节中发挥关键作用,因此具有重要价值。
精馏处理属于复杂程度较高的反应过程,其内部控制变量丰富、可操作变量多样化,同时技术原理专业性强。
因此,精馏作为生产阶段应用最为频繁的基础过程,需要消耗大量人力资源进行管理,能耗级别也较为庞大。
为降低基础成本并提高生产效率,需要针对精馏塔进行改进,使其能够贴合实际需求,达到理想应用目标。
本文结合笔者化工原料精馏行业工作经验,对精馏塔控制与节能优化进行深入研究,以供参考。
关键词:精馏塔;控制节能;优化处理前言:为实现改进精馏塔控制、节能环节的最终目标,需要首先明确精馏操作基础原理,并从控制角度、节能角度进行针对性分析,明确优化措施,确保精馏塔应用能够达到最佳效果。
笔者在化工原料精馏、结晶分离提纯行业中具有丰富工作经验,长期从事塔装置、换热蒸发装置的设计工作,能够对精馏塔控制、节能进行改进分析,确保后续进一步应用能够达到理想效果。
1精馏原理介绍精馏操作属于化工生产行业中较为常见的处理流程之一,其需要将混合物体内部液体部分、气体部分进行接触操作,使相关物质在固定条件下进行反应。
常规状态中,物质会在逆向流动、全面接触前提下逐渐开始反应流程,使液相内部轻组分快速进入气相内部,气相完成重组分操作,最终进入液相内部。
精馏本质属于传质活动,会导致热量不断传导,最终达成反应目标。
在压力恒定环境下,独立组分液体沸腾会持续产生加热效果,但温度却始终维持原有状态。
多组分液体会同样会在沸腾阶段持续加热,但温度会发生对应变化。
恒定压力会使溶液气相平衡与组分存在产生相对联系,组分沸腾温度点越高、浓度级别越高、平衡状态所需温度级别也会越高[1]。
因此,相对于物质气液相平衡状态,溶液气液进入平衡具有独特表现,即气相、液相平衡浓度存在差异。
常规气相低沸腾点组分浓度高于液相组分浓度,与纯组分气态、液态平衡相对比,常规压力条件下平衡温度主要代指冷凝点、沸腾点。
精馏过程的节能降耗

精馏过程的节能降耗摘要:精馏过程的节能,对于减少能源消耗,降低生产成本和保护环境具有十份重要的意义。
在精馏过程中可以采用最适宜回流比操作和最佳进料状态,使用中间冷凝器和中间再沸器,多效精馏技术、热泵精馏技术。
合理安排多组分物料分离流程,提高过程的分离效率、提高物料回收率,进而降低能耗。
并介绍我国精馏过程的节能现状与趋势。
关键词:精馏过程;节能;回流比;降耗,0前言在化工生产过程中,分离是非常重要的一个过程单元,它直接决定了最终产品的质量和收率,工业生产中占据着主导地位的分离方法就是精馏。
精馏是利用混合物中各组分挥发度的不同利用能量进行分离的操作单元,具有独特的优势。
据估计,化工过程中40%~70%的能耗用于分离,而精馏能耗又占其中的95%。
因此随着世界能源的日益短缺,精馏过程一直是研究者节能挖潜的热点对象,它的每一个进展都会带来巨大的经济效益。
多年来,人们已采用了多种方法和手段对精馏过程进行节能降耗的研究,按照流程是否改变及是否利用过程技术可以将其分为三类:1)利用过程技术对精馏塔的操作条件进行优化,以减少精馏塔所消耗的能量,如以产品物流预热进料、增加塔板数、减小回流比、增设中间再沸器和中间冷凝器等;2)开发了许多高效节能的特殊精馏工艺流程,如热泵精馏、多效精馏等。
1.1最适宜回流比和最佳进料状态[1]回流比直接影响再沸器和冷凝器的热负荷,决定精馏分离的净功耗,因此大体上确定了操作费用,同时还与塔设备的投资密切相关。
在最小回流比Rmin附近,随R的增长,操作线与平衡线间的距离增大,达到规定分离要求所需的塔板数减少,使得设备费用下降。
如果进一步增加回流比,在塔板数减少的同时,塔中蒸汽流率和换热器热负荷的增大,造成塔径、再沸器和冷凝器传热面积增大,使设备费用增加。
因此,应当根据总费用最小原则来选取适宜回流比。
进料状态(用加料状态参数q表示)的不同,将造成塔中精馏段和提馏段气液相流率的变化,从而影响R,以及达到规定分离要求所需的理论板数和再沸器和冷凝器的热负荷。
精馏过程节能技术分析及应用

精馏过程节能技术分析及应用发表时间:2020-09-08T11:08:18.570Z 来源:《工程管理前沿》2020年4月第12期作者:周建华[导读] 当前社会对资源的需求量不断增加,且需求速度也日益增长摘要:当前社会对资源的需求量不断增加,且需求速度也日益增长,大量的矿产资源以极快的速度被消耗,能源危机已经成为我国面临的主要问题,为更好的优化能源利用,减缓能源消耗速度,促进我国的可持续发展,必须对工业技术进行优化,以此节约能源,所以为提升精馏过程的能源利用效率,降低精馏能源消耗,本文将从精馏过程节能技术展开分析,并对其应用展开研究。
关键词:精馏过程;节能技术;能源精馏过程属于一个传质传热的过程,其复杂程度较高,在精细化工领域及石油化工领域均被广泛应用,精馏过程属于当前化工生产过程中能源消耗的最主要环节,化工生产过程中变量因素较多,其机理复杂程度较高,精馏能耗在化工中所占能耗可高达95%以上。
所以为更好的节约能源,精馏过程中的节能问题就显得尤为重要,下面就精馏节能现状展开分析,并对精馏节能技术的开展与应用展开论述。
一、精馏节能现状当前,化工生产中所需分离的物料种类不断提升,产品的精度和纯度要求也日益增长,但是当前化工领域应用的精馏装置操作方式比较保守,操作规格不合理,操作方式困难。
在精馏过程中,需要将混合物料由中间位置放入塔内位置,在塔内,主要由填料或者塔板设计为主,以确保汽液能够紧密接触,在沸腾器中加热塔底液相后,于冷凝器中对蒸汽进行冷凝干预。
在开展该精馏过程干预时,能量均会被冷却水或者分离组分携带,而并不是应用于组分分类之中,所以具备更大的精馏潜力[1]。
当前,世界各地均提升了对精馏节能的重视程度,建立在节能基础上的应用和研究也不断发展进步,美国所采用的精馏塔,能量消耗程度可以高达120万桶石油,在全国能源消耗中所占比例为3%,若是提升精馏过程中的节能技术,每次节约能源消耗的10%,则可每年节约5亿迈远。
精馏过程节能技术综述
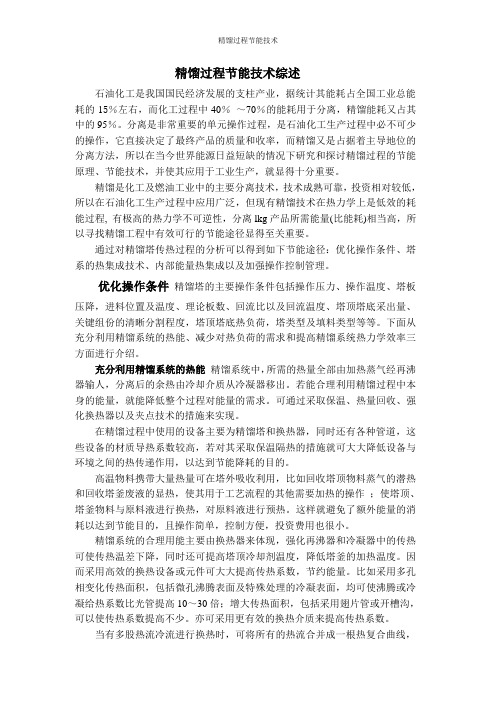
精馏过程节能技术综述石油化工是我国国民经济发展的支柱产业,据统计其能耗占全国工业总能耗的15%左右,而化工过程中40%~70%的能耗用于分离,精馏能耗又占其中的95%。
分离是非常重要的单元操作过程,是石油化工生产过程中必不可少的操作,它直接决定了最终产品的质量和收率,而精馏又是占据着主导地位的分离方法,所以在当今世界能源日益短缺的情况下研究和探讨精馏过程的节能原理、节能技术,并使其应用于工业生产,就显得十分重要。
精馏是化工及燃油工业中的主要分离技术,技术成熟可靠,投资相对较低,所以在石油化工生产过程中应用广泛,但现有精馏技术在热力学上是低效的耗能过程, 有极高的热力学不可逆性,分离lkg产品所需能量(比能耗)相当高,所以寻找精馏工程中有效可行的节能途径显得至关重要。
通过对精馏塔传热过程的分析可以得到如下节能途径:优化操作条件、塔系的热集成技术、内部能量热集成以及加强操作控制管理。
优化操作条件精馏塔的主要操作条件包括操作压力、操作温度、塔板压降,进料位置及温度、理论板数、回流比以及回流温度、塔顶塔底采出量、关键组份的清晰分割程度,塔顶塔底热负荷,塔类型及填料类型等等。
下面从充分利用精馏系统的热能、减少对热负荷的需求和提高精馏系统热力学效率三方面进行介绍。
充分利用精馏系统的热能精馏系统中,所需的热量全部由加热蒸气经再沸器输人,分离后的余热由冷却介质从冷凝器移出。
若能合理利用精馏过程中本身的能量,就能降低整个过程对能量的需求。
可通过采取保温、热量回收、强化换热器以及夹点技术的措施来实现。
在精馏过程中使用的设备主要为精馏塔和换热器,同时还有各种管道,这些设备的材质导热系数较高,若对其采取保温隔热的措施就可大大降低设备与环境之间的热传递作用,以达到节能降耗的目的。
高温物料携带大量热量可在塔外吸收利用,比如回收塔顶物料蒸气的潜热和回收塔釜废液的显热,使其用于工艺流程的其他需要加热的操作;使塔顶、塔釜物料与原料液进行换热,对原料液进行预热。
- 1、下载文档前请自行甄别文档内容的完整性,平台不提供额外的编辑、内容补充、找答案等附加服务。
- 2、"仅部分预览"的文档,不可在线预览部分如存在完整性等问题,可反馈申请退款(可完整预览的文档不适用该条件!)。
- 3、如文档侵犯您的权益,请联系客服反馈,我们会尽快为您处理(人工客服工作时间:9:00-18:30)。
关于精馏塔设备的设计与节能探究
发表时间:
2019-09-10T16:42:57.827Z 来源:《工程管理前沿》2019年第14期 作者: 王占伟
[导读] 作为化工行业中最耗能的工业,石油化工工业长期面临降能耗省能源的问题。
美克美欧化学品(新疆)有限责任公司
841000
摘要:作为化工行业中最耗能的工业,石油化工工业长期面临降能耗省能源的问题。而在石油化工行业,使用最普遍的分离单位是精
馏,介于精馏过程的能量消耗高,热力学效率低,因此,精馏塔的设备始终是化工节能设计的关键部分。
关键词:精馏塔;设备设计;节能
1
引言
由于能源的不断消耗,对具有较高能耗的精馏过程的研究始终具有广阔的发展前景。自21世纪初以来,科学水平的提升,精馏塔的计
算机辅助设计逐渐替换掉了人工计算和设计。精馏塔的研究热点也正在通过初步整改,从作为一个单元发展,到进行反应与精馏相耦合的
反应精馏,然后逐步向高能效、低投资的分隔壁精馏塔(
DWC)的研究。
2
精馏塔精馏技术原理
2.1
精馏工艺技术
混合物会在各种成分挥发时发生变化,精馏在这一原理下,通过气体,液体回流,从而将气体和液体之间实现逆向多解,使相对挥发
性成分强的从液相中逐渐向气体中流出,挥发相对弱的部分逆向进行移动以分离混合物,这是精馏过程。在精馏过程中,质与热是同步传
递的,原料进入精馏塔,则精馏段位于塔的上半区,反之如果没有进原料,提馏段位于下半部分。所谓的精馏技术,是指借助蒸馏设备中
的转移设施输送的适量浓度的液体,这部分溶液通过连续气化和冷凝,并在精馏塔顶部与底部共同得到产物的生产过程。在整个精馏塔精
馏过程中,必须同时操作其他技术设备。在石化行业,大多数精馏设备采用连续精馏运行方式。
2.2
连续精馏工艺技术的运行
原材料运输到进料口,接着将整个精馏塔分成精馏工艺段和萃取工艺段;因为每个组别具有不同的沸点,从而导致低沸点的气化升
腾,另一方面,高沸点组流下溶液并通过精馏塔内的蒸汽上升;蒸馏分离后,液体的下半部分被引出,部分液体被连续加热,然后返回精
馏塔;在冷凝器中部分干净地转化成液体,并通过回流泵送入回流罐。这部分蒸气的有些成为产品,有些作为回流液流回蒸馏塔。
2.3
关于精馏塔能源节约和优化
在当前的社会经济和科学背景下,精馏塔的节能降耗问题与科学和理论研究以及各个公司的实际研究难度相吻合。通过一系列科技人
员的付出和现实实践,取得了一定优化成果。要逐步改善再沸器和冷凝器的热交换效果;要修改精馏塔多塔精馏工艺,尽早将精多效馏技
术应用于精馏塔过程中;要开发高效的普通填料,更换板塔;要在精馏塔的节能控制部分中,如有需要,使用热交换泵技术。
3
精馏塔设备设计分析
3.1
关于塔板的设计
近年来,精馏塔的设计变得更加完善。大量试验结果表明,组合导向浮阀的效率明显高于传统塔板,对生产效率是极大提高。通过分
析塔板上区域的流动状态,发现塔板的导电液压效应,进一步提高了传质效率。
FGC-vT是用于精馏过程的相对较新的塔板,不仅提高了塔
的效率,而且提高了塔的灵活性,从而降低了能耗。
3.2
关于填料的设计
最初,精馏塔中的填料主要是竹片和石头。目前科学技术发展迅速,深化了精馏塔填料的研究,陶瓷拉西环成为蒸馏塔的新型填料。
由于压降小和流量大的优点,工业中填料塔的使用变得越来越广泛。在精馏塔的设计中,精馏塔的内部构件用网孔波纹填料,在同一过程
的基础上,不仅可以促进精流塔的负荷,而且可以实现高效节能的双赢局面。
3.3
其他方面的设计
在精馏塔的设计中,可以改变混合塔板的位置和进料位置。如若优化设计,则会设计多个进料口,以便某些材料可用于特定设计,根
据进给类型选择相应的进给连接。以这种方式,可以避免在精馏过程中组合物的波动,从而确保精馏的效果并增加产量。如果特定瘤区段
中存在大的负荷区域,则混合的塔板可被使用进行有效低耗蒸馏。
4
精馏塔的节能优化设计
4.1
分隔壁精馏塔设计
分隔壁精馏塔在精馏塔内设有垂直隔板,精馏塔分为四段,分别是上方共用精馏段、下方共用提馏段、隔板隔开的精馏供给段以及中
间侧线采出段。它对应于具有完整热电偶的特定类型的精馏塔,并且在热力学上等同于具有完整热电偶的精馏塔。由于其特殊结构,
DWC
塔拥有许多优势,而这并非一般侧线精馏塔所具备的。
对于分隔壁精馏塔的静态设计,研究了三种不同位置的分隔壁精馏塔的动态特性,与控制策略相比,结果表明DWCU在三种形式中表
现最差。在大多数情况下,
DWCL具有更好的动态性,但同时需要更多的耗能。与DWCL相比,DWCU在可控性能方面没有明显差异,但
经济效益具有明显优势。有研究者通过分析甲苯
--二甲苯--重苯系精馏分离粗苯精制,对传统的分离顺序和分隔塔技术进行了定量测试和比
较,发现传热和传质耦合的技术在能源效率方面提供了显着的特点。鉴于中国目前的能源状况和未来化工行业的发展趋势,大力发展和推
进相邻壁塔技术的进步具有至关重要的意义。
4.2
反应精馏与分隔壁精馏塔的耦合
反应精馏塔的结构具有特殊性,Muler等在2004年定义了反应精馏隔壁塔(RDWC)的概念。反应精馏和隔壁塔的优势在RDWC上得
到融合,通过减少工艺,降低能耗,减少投资和提高选择性,可作为化学工业的新研究热点。
IvoMueller等根据反应速率在反应精馏隔壁塔
中进行了模拟。由于反应体系的特点是转化率比较高、选择性较低,模拟的目的是将酯基相互转移到碳酸酯,模拟是理论上被证实的,采
用隔壁塔技术和反应系统可有效提高选择性和可分离性,减少操作单元数量,节省设备投资。此外,许多相关材料证实,分隔壁精馏塔的
新工艺科技可利用在现有的反应精馏工艺,从而节约能源和设备损耗。孙兰义等用
RDWC模拟了乙酸甲酯的合成,解释了回流比和气相分
配比对反应精馏隔壁塔性能的影响。与传统工艺相比,反应精馏隔壁塔可以节省再沸器消耗
11.9%的能量,可有效降低设备的损耗和运行
资本。齐彩霞通过模拟和控制分隔壁塔中碳酸二乙酯合成过程,对精馏隔壁塔流程和一般方法的有效对比,发现在反应精馏隔壁塔中合成
碳酸二乙酯的方法可以大大降低能耗,减少二氧化碳排放,提高系统的热力学效率,节省了可观的投资成本。简言之,在分隔壁蒸馏塔与
反应精馏技术相结合后,原反应精馏过程得以成功改造,对未来蒸馏塔节能研究具有良好的指导作用。
4.3
热集成工艺
热集成工艺具有相当大的应用优势,主要是通过塔顶部气相的潜热预热精馏材料的方法。该方法不需要在冷凝过程中添加制冷剂,材
料的预热降低了分离的难度,从而减少加热介质的量,并且与常规的变压精馏相比可以减少热集成精馏能耗的
35%至58%。在随后的运行
阶段,主要进行三种类型的精馏过程:正压,常压和负压。在具体过程中,使用压力处理,其具有比常规真空加热处理更显着的节能效
果。
5
结语
综上所述,随着计算机技术的进步,特别是集成控制系统水平的提升,在精馏塔的控制应用中计算机控制技术不断变革和进步。控制
器的成熟度越高,精馏技术越强,精馏技术越能创新,越能节约能源,提高盈利能力。在普通蒸馏塔的设计和研究过程中,重点放在各种
材料的开发上,从而加强化学工业的计算机辅助计算,加强学科之间的跨学科交叉。另外,在设计用于测定反应的精馏塔时,有必要不断
改进现有的设计方法以形成各种非理想系统。分隔壁精馏塔与反应精馏工艺相结合,对设备投资和运行成本节约具有明显意义,因此,势
必要大力加强反应蒸馏技术和分隔壁蒸馏塔技术的结合。
参考文献:
[1]
谢英芹,李玲.浅析精馏塔设计以及节能的研究[J].化工设计通讯,2017(11):149-150.
[2]
岳婷.精馏塔设备设计以及节能的研究情况[J].化工管理,2017(05):259.