氯氧镁水泥研究
耐水高强硫氧镁质胶凝材料的研制

Ab s t r a c t : T h e ma g n e s i u m o x y s u l f a t e c e me n t w a s p r e p a r a t e d b y u s i n g Mg S O4 i n s t e a d o f Mg Cl 2 . T h e n e w c e me n t i t i o u s ma t e r i ls a wa s r e s e a r c h e d a n d I t s s t r e n g t h a n d wa t e r r e s i s t a n c e w e e r b e t t e r t h a n ma g n e s i u m o x y c h l o id r e c e me n t , nd a d i s c u s s e d t h e p e f r o r ma nc e o f
四川建 筑科 学研究
21 4
S i c h u a n B u i l d i n g S c i e n c e
第3 9卷 第 3期 2 0 制
刘 涛 , 郑 亚林 , 杜 沛 , 林 海燕。 , 韩 敏 , 王玉江
,
( 1 . H e n a n P r o v i n c i a l A c a d e m y o f B u i l d i n g R e s e a r c h C o . ,L t d . , Z h e n g z h o u 4 5 0 0 5 3 , C h i n a ; 2 . Z h e n g z h o u C i t y E n g i n e e r i n g Q u a l i y t S u p e r v i s i o n S t a t i o n , Z h e n g z h o u 4 5 0 0 5 3 , C h i n a ; 3 . D e p a r t me n t o f Ma t e r i l a S c i e n c e a n d E n in g e e r i n g , L u o y a n g I n s i t t u t e o f T e c h n o l o g y , L u o y a n g 4 7 1 0 2 3 , C h i n a )
氯氧镁制品以摩尔比计算配比方法
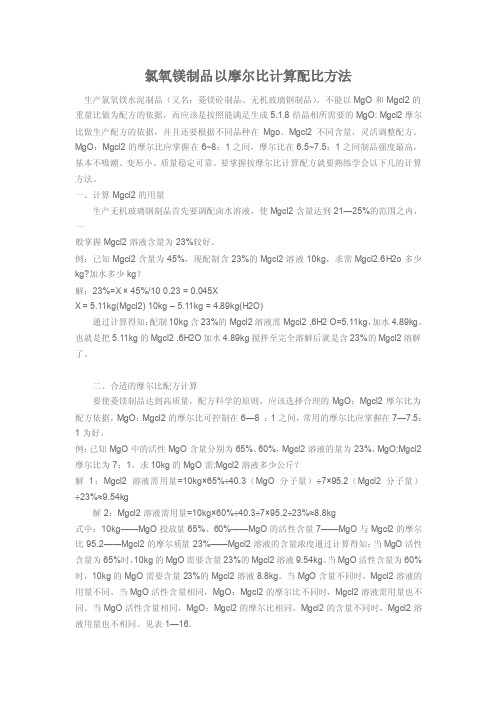
氯氧镁制品以摩尔比计算配比方法生产氯氧镁水泥制品(又名:菱镁砼制品、无机玻璃钢制品),不能以MgO和Mgcl2的重量比做为配方的依据,而应该是按照能满足生成5.1.8结晶相所需要的MgO: Mgcl2摩尔比做生产配方的依据,并且还要根据不同品种在Mgo、Mgcl2不同含量,灵活调整配方。
MgO:Mgcl2的摩尔比应掌握在6~8:1之间,摩尔比在6.5~7.5:1之间制品强度最高,基本不吸潮、变形小、质量稳定可靠。
要掌握按摩尔比计算配方就要熟练学会以下几的计算方法。
一、计算Mgcl2的用量生产无机玻璃钢制品首先要调配卤水溶液,使Mgcl2含量达到21—25%的范围之内,一般掌握Mgcl2溶液含量为23%较好。
例:已知Mgcl2含量为45%,现配制含23%的Mgcl2溶液10kg,求需Mgcl2.6H2o多少kg?加水多少kg?解:23%=X × 45%/10 0.23 = 0.045XX = 5.11kg(Mgcl2) 10kg – 5.11kg = 4.89kg(H2O)通过计算得知:配制10kg含23%的Mgcl2溶液需Mgcl2 .6H2 O=5.11kg,加水4.89kg。
也就是把5.11kg的Mgcl2 .6H2O加水4.89kg搅拌至完全溶解后就是含23%的Mgcl2溶解了。
二、合适的摩尔比配方计算要使菱镁制品达到高质量,配方科学的原则,应该选择合理的MgO:Mgcl2摩尔比为配方依据,MgO:Mgcl2的摩尔比可控制在6—8 :1之间,常用的摩尔比应掌握在7—7.5:1为好。
例:已知MgO中的活性MgO含量分别为65%、60%,Mgcl2溶液的量为23%,MgO:Mgcl2摩尔比为7:1,求10kg的MgO需:Mgcl2溶液多少公斤?解1:Mgcl2溶液需用量=10kg×65%÷40.3(MgO分子量)÷7×95.2(Mgcl2分子量)÷23%≈9.54kg解2:Mgcl2溶液需用量=10kg×60%÷40.3÷7×95.2÷23%≈8.8kg式中:10kg——MgO投放量65%、60%——MgO的活性含量7——MgO与Mgcl2的摩尔比95.2——Mgcl2的摩尔质量23%——Mgcl2溶液的含量浓度通过计算得知:当MgO活性含量为65%时,10kg的MgO需要含量23%的Mgcl2溶液9.54kg。
菱镁水泥砖瓦的反卤和褪色
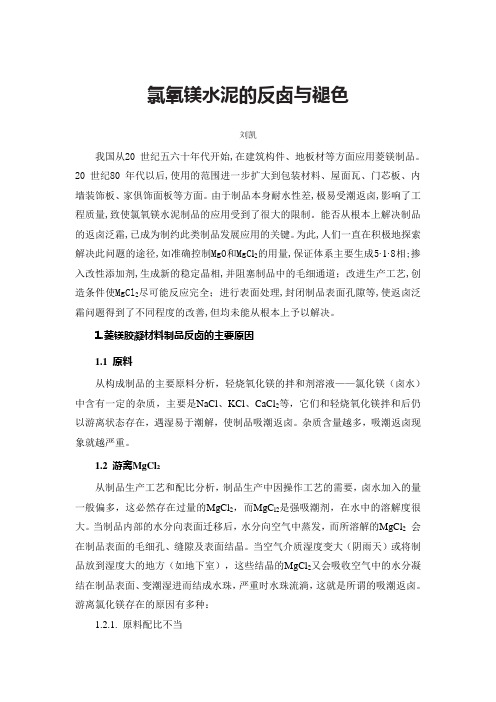
氯氧镁水泥的反卤与褪色刘凯我国从20 世纪五六十年代开始,在建筑构件、地板材等方面应用菱镁制品。
20 世纪80 年代以后,使用的范围进一步扩大到包装材料、屋面瓦、门芯板、内墙装饰板、家俱饰面板等方面。
由于制品本身耐水性差,极易受潮返卤,影响了工程质量,致使氯氧镁水泥制品的应用受到了很大的限制。
能否从根本上解决制品的返卤泛霜,已成为制约此类制品发展应用的关键。
为此,人们一直在积极地探索解决此问题的途径,如准确控制MgO和MgC l2的用量,保证体系主要生成5·1·8相;掺入改性添加剂,生成新的稳定晶相,并阻塞制品中的毛细通道;改进生产工艺,创造条件使MgCl2尽可能反应完全;进行表面处理,封闭制品表面孔隙等,使返卤泛霜问题得到了不同程度的改善,但均未能从根本上予以解决。
1.菱镁胶凝材料制品反卤的主要原因1.1原料从构成制品的主要原料分析,轻烧氧化镁的拌和剂溶液——氯化镁(卤水)中含有一定的杂质,主要是NaCl、KCl、CaCl2等,它们和轻烧氧化镁拌和后仍以游离状态存在,遇湿易于潮解,使制品吸潮返卤。
杂质含量越多,吸潮返卤现象就越严重。
1.2游离MgCl2从制品生产工艺和配比分析,制品生产中因操作工艺的需要,卤水加入的量一般偏多,这必然存在过量的MgCl2,而MgC l2是强吸潮剂,在水中的溶解度很大。
当制品内部的水分向表面迁移后,水分向空气中蒸发,而所溶解的MgCl2会在制品表面的毛细孔、缝隙及表面结晶。
当空气介质湿度变大(阴雨天)或将制品放到湿度大的地方(如地下室),这些结晶的MgCl2又会吸收空气中的水分凝结在制品表面、变潮湿进而结成水珠,严重时水珠流淌,这就是所谓的吸潮返卤。
游离氯化镁存在的原因有多种:1.2.1. 原料配比不当大量文献指出,原料配比应保证制品中生成结构稳定的5相,即MgO/MgCl2的摩尔比应为5以上,以避免MgCl2过剩。
研究表明,氯氧镁水泥的水化是多样的、复杂的,甚至存在着未知相。
氧化镁与氯化镁
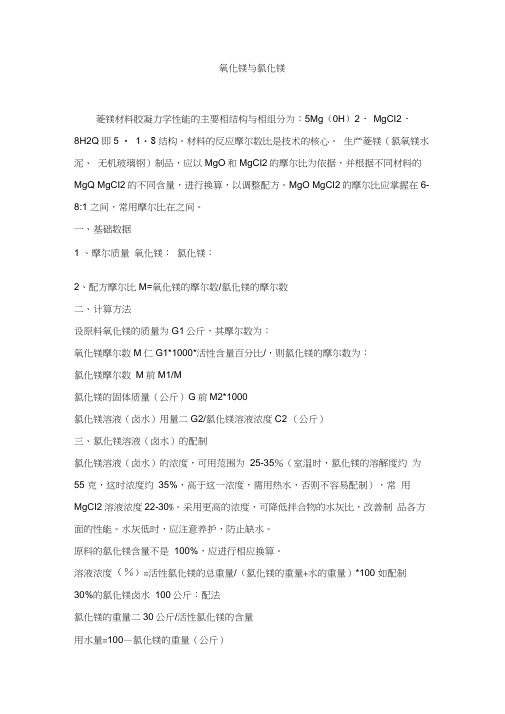
氧化镁与氯化镁菱镁材料胶凝力学性能的主要相结构与相组分为:5Mg(0H)2・ MgCI2・8H2Q 即5 • 1・8结构。
材料的反应摩尔数比是技术的核心。
生产菱镁(氯氧镁水泥、无机玻璃钢)制品,应以MgO和MgCI2的摩尔比为依据,并根据不同材料的MgQ MgCI2的不同含量,进行换算,以调整配方。
MgO MgCI2的摩尔比应掌握在6-8:1 之间,常用摩尔比在之间。
一、基础数据1 、摩尔质量氧化镁:氯化镁:2、配方摩尔比M=氧化镁的摩尔数/氯化镁的摩尔数二、计算方法设原料氧化镁的质量为G1公斤,其摩尔数为:氧化镁摩尔数M仁G1*1000*活性含量百分比/,则氯化镁的摩尔数为:氯化镁摩尔数M前M1/M氯化镁的固体质量(公斤)G前M2*1000氯化镁溶液(卤水)用量二G2/氯化镁溶液浓度C2 (公斤)三、氯化镁溶液(卤水)的配制氯化镁溶液(卤水)的浓度,可用范围为25-35%(室温时,氯化镁的溶解度约为55 克,这时浓度约35%,高于这一浓度,需用热水,否则不容易配制),常用MgCI2溶液浓度22-30%。
采用更高的浓度,可降低拌合物的水灰比,改善制品各方面的性能。
水灰低时,应注意养护,防止缺水。
原料的氯化镁含量不是100%,应进行相应换算。
溶液浓度(%)=活性氯化镁的总重量/(氯化镁的重量+水的重量)*100 如配制30%的氯化镁卤水100公斤:配法氯化镁的重量二30公斤/活性氯化镁的含量用水量=100—氯化镁的重量(公斤)四、填充料菱镁制品在生产中加入填充料,填充料可降低生产成本,并改变制品的性能。
用量可按实际生产要求添加。
填充料包括:锯屑、稻壳、农作物秸杆;各种石粉、珍珠岩、粉煤灰等。
但不应加入含钙的填料。
五、计算示例设氧化镁的活性含量为65%,氯化镁溶液浓度为30%,氧化镁与氯化镁的摩尔比为7 ,则10 公斤原料氧化镁应配氯化镁溶液的量为[(10*1000*65% 盖发脆爆裂,后果不堪设想。
氯氧镁凝胶/聚丙烯酸酯复合材料弯曲性能的研究

这是 以氯氧 镁凝 胶/ 丙 烯 酸酯 为 共 混 基体 ,以砂 聚
料 为增强 填料 的复 合材料 。 将六 水氯 化 镁用 水 溶 解 ,配 制 成 氯化 镁 溶 液 ; 根 据实 验设 计 的 目的 ,按 配 方 加 入 一 定 量 的 氧化 镁 、聚 丙烯 酸 酯 乳 液 、水 和 砂料 ,充 分 搅 拌 几 分 钟 。然后 ,将 物料倒 人模 具 中 ,静 置数 小时 ,待试 样 基本 干透之后 开模 。试 样置 于空气 中养护一 段 时 间 ,即可 用 于测试 力学性 能 。本工作 以氯氧镁 凝胶 / 增强 复合材 料 ( CC m ois 砂 MO o pse,简 称 MO t C复 合 材料 )做 为 空 白对 照 试 样 。 这是 以氯 氧 镁凝 胶
材料 与 聚丙 烯 酸 酯 ( 称 P R) 这 种 有 机 高分 子 简 A 聚合物进 行共 混 复 合 ,可 以形 成 一 种 新颖 的无
} 收 稿 日期 :20 0 0 0 6— l一 8
基 金 项 目 :国 家 自然科 学 基 金 资 助 项 目 (0 7 00 ;中 山大 学 理 科 科 研 资 助 项 目 ( 1 0 8— 10 4 ; 中 山 大 学 50 33 ) 0 — 5 7 19 ) “ 新 化 学 实 验研 究基 金 ” 资助 项 目 创
理 、色调 、质感 的制品,同时 ,具有较好的抗弯曲 性 能 ,可 以代替 石料 。 因而 ,在 环境艺 术装饰 中具
有很 好 的发 展前 景 ¨ …。 然而 ,通 常的氯 氧镁水 泥经 常会 出现 “ 出汗 ”
本工作的主要研究对象是氯氧镁凝胶/ 聚丙烯 酸酯复 合 材 料 ( C P R C mpse,简 称 氯 氧 MO / A o ois t
镁水泥基复合保温材料的研究

镁水泥基复合保温材料的研究
姜洪义;黄芳;张延林
【期刊名称】《广东建材》
【年(卷),期】2001(000)007
【摘要】本文对利用具有高强快凝和防火性能好的氯氧镁水泥作为基材,引入镁粉发泡剂和有机聚氨酯发泡剂制作复合保温材料进行了实验研究,实验表明在复合材料中氯氧镁水泥和聚氨酯泡沫体的性能都得到了改善和提高,镁水泥基复合保温材料可以作为新一代轻质保温墙体材料.
【总页数】2页(P10-11)
【作者】姜洪义;黄芳;张延林
【作者单位】武汉理工大学材料学院,530070;武汉理工大学材料学院,530070;武汉理工大学材料学院,530070
【正文语种】中文
【相关文献】
1.水泥基复合发泡轻质保温材料的试验研究 [J], 姜葱葱;李国忠;张水
2.水泥基复合保温材料的防水性能研究 [J], 李静;李国忠
3.聚合物改性水泥基复合保温材料的制备与性能研究 [J], 李小龙;李国忠
4.EPS颗粒对超轻水泥基复合保温材料性能的影响 [J], 吴子豪;王武祥;刘广东;王爱军;张磊蕾;杨俊
5.硅灰对超轻水泥基复合保温材料性能的影响 [J], 吴子豪;王武祥;刘晓通;王爱军;张磊蕾;杨俊
因版权原因,仅展示原文概要,查看原文内容请购买。
镁水泥

• 3、提高氧化镁搅拌和反应过程中的水灰比,增加 制品的密实性和防水率,能克制氯氧鎂水泥中搅拌 过程中氯化镁分子超标的特性,使氯氧鎂水泥反应 过程中温度均衡及反应的更加充分.如各类高效减 水剂、表面活性乳化剂、扩散剂等。 • 四、科学和动态的组成配比,从成份组成而言, 轻烧镁MgO和氯化镁的克分子用量组成至少是5: 1。以上仅是化学平衡角度而言,实际物理化学反 应不可能完全进行,还应具体制成不同MgO/ MgCI2的摩尔比的胶凝硬化体,分别测试不同龄 期的强度及耐水性能,确定最佳组份的物理力学 性能,可以肯定的是组成的MgO/ MgCI2的摩尔 比用量大于5的基本原则。
• 7、可低温成型,四季皆可生产 镁水泥由于 有良好的抗低温下可照常生产,一般不受 影响,这有利于延长生产期。 • 8、制品工艺简单,易于生产 镁水泥由于凝 固快,对生产条件要求不严格,一般条件 就能从事其制品加工,很多产品均不需要 大型设备,手工半手工可从事生产,所以 镁水泥制品很容易马上生产,门槛较低。 • 9、制品生产成本低、利润高 镁水泥由于强 度极高,可掺用大量废弃物,就使它的材 料用量减少,总成本降低,生产成本低于 普通硅酸盐水泥。
(8)抗盐卤腐蚀 镁水泥由于是用盐卤作调和剂的 (大多为氯化镁),也就是说它本身就是有盐卤 成分,所以它就不怕盐卤腐蚀,而且遇盐卤还会 增加强度。这就使它可以克服普通水泥及混凝土 制品的不足,用于高盐卤地区。 • (9)空气稳定性和耐侯性 由于镁水泥是气硬性 的,在终凝后只有在空气中才能继续凝结硬化, 这就使它具有良好的空气稳定性,空气越干燥, 它就越稳定。 • 试验表明,镁水泥制品在干燥空气中,其抗压和 抗折度均随龄期而增长,直至两年龄期还在增长, 十分稳定。也证明了,镁水泥在干燥空气中的强 度是持续增长的。
水泥中氧化镁的作用

水泥中氧化镁的作用水泥是一种常用的建筑材料,它在建筑工程中起到了至关重要的作用。
其中,氧化镁是水泥中的一种重要成分,它在水泥中起到了多种作用。
本文将从多个角度来探讨水泥中氧化镁的作用。
氧化镁在水泥中起到了增强水泥强度的作用。
水泥中的氧化镁能够与水中的氢氧根离子反应生成氢氧化镁,而氢氧化镁具有较高的碱性。
这种碱性能够与水泥中的硅酸盐反应生成硅酸镁凝胶,从而增强了水泥的强度。
此外,氧化镁还能够与水泥中的铝酸盐反应生成铝酸镁凝胶,进一步提高水泥的强度和硬度。
氧化镁在水泥中还起到了调节水泥硬化速度的作用。
水泥中的氧化镁可以调节水泥的反应速率,使水泥在硬化过程中适度延缓反应速度,从而使水泥能够具有较长的操作时间。
这对于施工人员来说非常重要,因为他们需要有足够的时间来完成各种工作。
氧化镁还能够改善水泥的耐久性。
水泥中的氧化镁能够与水泥中的氢氧根离子反应生成氢氧化镁,而氢氧化镁能够与水泥中的氯离子反应生成氯化镁。
这种氯化镁具有一定的防腐蚀性能,能够防止水泥受到外界环境的侵蚀,延长水泥的使用寿命。
氧化镁还能够改善水泥的抗裂性能。
水泥中的氧化镁能够与水泥中的硅酸盐反应生成硅酸镁凝胶,这种凝胶具有较高的粘结强度和韧性,能够有效地抵抗外界的拉伸力和剪切力,提高水泥的抗裂性能。
氧化镁还能够提高水泥的耐高温性能。
水泥中的氧化镁能够与水泥中的硅酸盐反应生成硅酸镁凝胶,这种凝胶具有较高的熔点和耐高温性能。
在高温环境下,水泥中的氧化镁能够保持其结构的稳定性,不会发生熔化和变形,从而保证了水泥在高温环境下的使用性能。
水泥中的氧化镁具有增强水泥强度、调节水泥硬化速度、改善水泥耐久性、提高水泥抗裂性能和提高水泥耐高温性能等多种作用。
这些作用使得水泥能够在建筑工程中发挥出更好的性能,保证了建筑物的安全和耐久性。
因此,水泥中的氧化镁是不可或缺的重要成分之一。
- 1、下载文档前请自行甄别文档内容的完整性,平台不提供额外的编辑、内容补充、找答案等附加服务。
- 2、"仅部分预览"的文档,不可在线预览部分如存在完整性等问题,可反馈申请退款(可完整预览的文档不适用该条件!)。
- 3、如文档侵犯您的权益,请联系客服反馈,我们会尽快为您处理(人工客服工作时间:9:00-18:30)。
氯氧镁水泥新课题(转摘)字体大小:大| 中| 小2008-06-24 12:59 - 阅读:39 - 评论:0我国以氯氧镁为基料生产的制品有:防火装饰板、通风管道、硅镁加气混凝土、轻质隔墙板、仿琉璃波形瓦、无木包装箱和门窗框、道路铺地砖、发泡屋面保温隔热板、建筑装饰线条和梁柱、建筑装饰墙裙和天花板以及美工艺术品和活动房等,而且出现了为数不少的并具有相当规模和机械化生产的企业取得了卓有成效的业绩。
以氧化镁胶凝体和氯化镁为的水化反应不可能完全是适人皆知的,而且配比中MgO/MgCI2克分子比大于5的理论也是肯定的,因此制作加入相应的改性剂必要的,主要作用是改善制品内载功能,主要表现为提高制品的离水渗透性能,减少变形和反卤。
作为改性剂应具备二个条件:一是能使具有负作用的成份形成难溶于水且有力学性能的化学元组成物,作为工业副产物中的硅灰,高炉矿渣、粉煤灰、沸腾炉渣、烧结磷矿渣等它们都是经过高温煅烧的烧结料,本身就具有胶凝性能形成有力学性能的结构物。
采用工业废渣不但能消除工业污染,而且有大幅度降低制品的生产成本,是一举两得的好事。
二是自身具有硬胶凝性且不阻碍氯氧镁的水化反应,能粘附在氯氧结晶相的表面提高抗水侵能力,或者自身具有抗水功能堵塞毛细通道,改善抗水性能的同时提高氯氧镁制品的抗冲击性能和防变形性能。
三、提高氧化镁搅拌和反应过程中的水灰比,增加制品的密实性和防水率,能克制氯氧鎂水泥中搅拌过程中氯化镁分子超标的特性,使氯氧鎂水泥反应过程中温度均衡及反应的更加充分.如各类高效减水剂、表面活性乳化剂、扩散剂等。
值得生产者应注意的是:所加入的外加剂不一定有良好的功能和作用,其实所有的改性助剂都是能制标而不能制本,切不可画蛇添足,以免适得其反。
选择合格稳定的原材料要制作好的氯氧镁制品,必须采用合格稳定的原材料是应注意的环节。
作为主要原料轻烧氧化镁的要求,在GB9854—88标准中有明确的规定,应结合氯氧镁制品在建筑中的应用来选用。
A、氧化镁含量在80~85%为宜,大于85%以上轻烧粉一般是做耐火材料的原料价格也较高。
(有的生产者往往注重价格越低越好,常常采用立窑烧成的含有较多煤粉的菱苦土做原料,这就无法做好高质量的氯氧镁制品,有的原料供应者受到经济效益的驱动,往往在轻烧粉中掺石粉,)如果是这样生产者就必须对轻烧氧化镁原料进行氧化镁含量,活性氧化镁含量,游离子氧化钙含量、细度、烧失量等进行监控测定。
活性氧化钙的含量应小于2%,活性氧化镁含量应在65%±2。
烧失量7-11%。
B、氯化镁应严格控制含量,选用正规的生产厂,含在45-46%(MgCI2)应用中不能低于这个标准。
一些土制小窑生产的切不能选用。
C、细度要求一般应为150-200目。
因为细度大,比表面积相应大,增加了反应的接触面,相应表现出较好的力学性能和化学性能。
实践证明,在同等条件下,200目的制品强度比150目的制品要高出10%~15%。
D、玻璃纤维布应采用中碱玻璃纤维布,不应采用高碱玻璃纤维布。
玻璃纤维布的强度视制品的用途,可分别采用4×4、6×6、8×8、10×10等,玻璃纤维布的正确使用对提高制品的强度和约束变形是十分重要的,切不可轻视。
四、合理工艺有利于制品质量工艺制度要重视两个问题:一是搅拌,二是养护制度。
A、混凝搅拌:氧化镁,MgCI2水溶液,改性助剂及填充料只有混合均匀才能使MgO与MgCI2界面充分结合,改性助剂与填充料空隙内,拌料均匀性与搅拌速度和时间有关,搅拌速度应控制在39-49转为宜,搅拌机在搅拌工艺上应避免涡流现象和死角,应在造型构造上能使混合性能达到充分碰撞、冲击、翻涌,磨擦达到混合均匀的目的。
特别强调氧化镁,MgCI2水溶液混凝搅拌外,其它外加剂应单独搅拌后与其混合。
实践证明分立搅拌能使制品强度提高10%左右,不会出现局部泛霜、返卤现象。
B、正确的养护制度:由于氯氧镁制品的水化硬化过程是一显著的放热过程,而业放热十分急剧,曾测得放热温度最高可达140ºC,如果不控制升温速度就会使制品内部结构破坏,表现为制品酥松脆化。
养护过程中内部升温不能超过55ºC,否则就应采取降温措施。
一般成型温度应控制在10ºC以上,低于此温度应采用保温措施,在室温下约需14-16小时可脱模,脱模后制品应进行保温保湿养护,可将制品叠码在一起并时行覆盖。
利用自身的水化热和排湿增生养护3-5天,7天后可达到预定强度的70%~80%,应重视脱模的保温保湿养护,因为制品脱模后的水化硬化反应并未停止,过早的将制品置于空间养护或干燥处理,会造成水分逸出,使反应不完全,也会出现返卤、泛霜及翘曲变形现象。
五、氯氧镁制品的变形、反卤氯氧镁制品变形表现的形式有收缩变形;厚度与密度偏差及结构不对称所造成的翘曲变形,变形影响建筑功能和使用效果。
造成变形的主要原因有:A、过多过大的用水量,在实际生产中,操作者为了操作的方便对混合物加入了过量的水(氯化镁溶液),或片面的通过多加入填充物降低生产成本,又企图通过加大用水量加大混合料的流动度达到可操作性。
这样做会造成水分过多使氯氧镁料浆碱度过度降低,加速了水镁石Mg(OH)2的形成,抑制了固相列生成,导致不能获得应有的力学性能和化学稳定性,水镁石不是形成稳定性能的胶凝相,渗析在制品表面上形成白色Mg(OH)2盐析物,同时由于活性氧化镁部分为水所水化,也会形成“返卤”现象。
另一方面,多余的水要排出去。
如果这种排湿不均速不一致,其收缩也不一致,收缩应力会造成制品的变形性,特别是幅面大而且厚度薄的制品表现较为突出。
正确的用水量为0.43-0.48。
强调一点如果用MgCI2+ Mg SO4 混和溶液的话MgCI2浓度应控制在14.5-18.5度,MgSO4的浓度应控制在12-12.5度,MgCI2 +MgSO4溶液浓度为26.5-30.5度。
显而易见用混和溶液相对降低了MgCI2的使用量又不影响氯氧镁水泥结晶固相的生成。
同时起到控制反卤的作用。
B、我认为生成相应为5.1.6或5.1.5相,克分比应控制在5(MgH2O)/ MgCI2+MgSO4=1:0.89,具体的做法应尽可能的控制MgCI2+MgSO4溶液投放比例,以混合溶液即MgCI2+Mg SO4加无水石膏进行无机改性。
如用无水石膏进行无机改性的话无水石膏凝固点应在5-10分钟。
制品即有氯氧镁水泥的气硬性又有石膏制品的干燥性两者兼有。
经实验证明效果良好,在相对潮湿度90-95%的条件下没有出现反卤和变形现象。
应强调的是生产企业应设置干燥设备,干燥窑内温度应控制在50-60℃。
使制品的含水率在出厂前控制在8%~10%,避免制品在使用过程中因排湿的不一致所造成的反卤和变形。
我认为用水化法处理去控制反卤是不理智的,其实经过水化处理的制品还是会反卤的(看相对环境湿度),氯氧镁制品材料本身耐水性差,经过水化后加快了氯氧镁制品的老化,使其氯氧镁制品使用时限变短。
C、制品的厚度、密度公差大和结构不对称所造成的变形。
这种现象多发生在厚度公差超过板材厚度的10%,板材的容重公差超过6%,这将造成板材的内应力偏差大而造成变形。
另一方面是增强的玻璃纤维或网格布分布不均匀,在制品中的分布位置不对称也会造成结构应力引起变形。
此外,还应注意作为填充的料比重应尽可能和轻烧氧化镁粉相一致,避免填料的比重不同,造成在成型过程中产生容重差异大,板材内部的收缩膨胀不一致,产生结构应力引起翘曲变形。
在使用过程中当外界湿度和温度发生变化时,板材因容重的差异大,收缩与膨胀也不一致从而造成变形。
因此克服厚度公差、容重公差和注重结构的对称性是也防止变形的关键举措。
总之,制作与生产优质、稳定的氯氧镁制品是一个多因素的系统工程,它涉及到合格稳定的原材料、严格科学的配比和动态的调整、有效的改性剂、合理的技术工艺与养护制度等等,决不能用粗放简单的生产与应用。
只有这样才是氯氧镁制品的本质。
氯氧镁水泥理论配料公式氯氧镁水泥是一种气硬性双组份胶凝材料,双组份(轻烧氧化镁和卤水)间的配料没有理论计算依据。
一般是根据实际生产经验或按理论上形成518相所需的各组成材料的克分子比来计算。
本文从氯氧镁水泥水化反应出发,推导出理论配比公式,供生产配料时参考。
一、公式推导氯氧镁水泥是由MgO-MgCl2-H2O组成的三元体系。
下面的讨论假设组成三元体系的MgO、MgCl2和H2O刚好能充分反应完全而没有任何一者多余,反应过程中也没有水份得失,且反应终了产物只有Mg(OH)2和518相。
设MgO-MgCl2-H2O体系中MgCl2溶液量为G、浓度为C(重量百分浓度),则其中MgCl2量为CG,H2O量为(1-C)G,并设体系中的水有x份用于生成Mg(OH)2,(1-x)份用于生成518相。
则有:MgO + H2O →Mg(OH)240.3 (1-C)Gx 18生成氢氧化镁反应所需的MgO量=40.3(1-C)Gx÷18 ①5MgO + MgCl2+ 13H2O → 5Mg(OH)2·MgCl2·8H2O5×40.3 95.2 13×18CG (1-C)G(1-x)生成518相所需的MgO量=5×40.3CG÷95.2 ②且有:CG÷95.2=(1-C)G(1-x)÷(13×18) ③该体系反应所需的总MgO量=①+②④根据式③可求出x,代入式④并整理即得:总MgO量=(2.24-5.62C)G 或MgO量/G=2.24-5.62C ⑤假设轻烧氧化镁中能参与水化反应的活性MgO含量(有效MgO含量)为a,则⑤式可改写为:轻烧氧化镁/卤水=(2.24-5.62C)/a ⑥上式即为MgO、MgCl2和H2O三者之间完全反应时的配比公式。
根据式⑥,只要确定卤水浓度,便可方便地求出轻烧氧化镁和卤水间的比例。
二、讨论由式⑥可见:1.轻烧氧化镁中的活性MgO含量(有效MgO含量)a越低,轻烧氧化镁需用量越大。
轻烧氧化镁的质量要求及活性MgO含量的测试方法参见标准WB/T1019-2002。
从活性MgO含量的测试方法可知,检测结果反映的是在一定条件下能参与水化反应的MgO 含量,而非MgO活性(据此,称之为有效MgO含量似更合理)。
组成氯氧镁水泥的各原材料中以轻烧氧化镁的质量对其性能影响最大。
轻烧氧化镁的质量指标中最重要的是MgO的活性及其分布:MgO活性的高低不仅影响氯氧镁水泥的水化反应速度(制品凝结硬化的快慢),还影响其水化反应产物的组成和结构(进而影响制品的性能)。
有关MgO活性及其对制品性能的影响,有待进一步深入研究。
2.卤水浓度越高,组成氯氧镁水泥体系所需的氧化镁量越少;卤水浓度越低,所需的氧化镁量越多。