铜管钎焊热裂纹形成的原因与分析_田泽生
几种焊缝热影响区裂纹的成因及对策研究
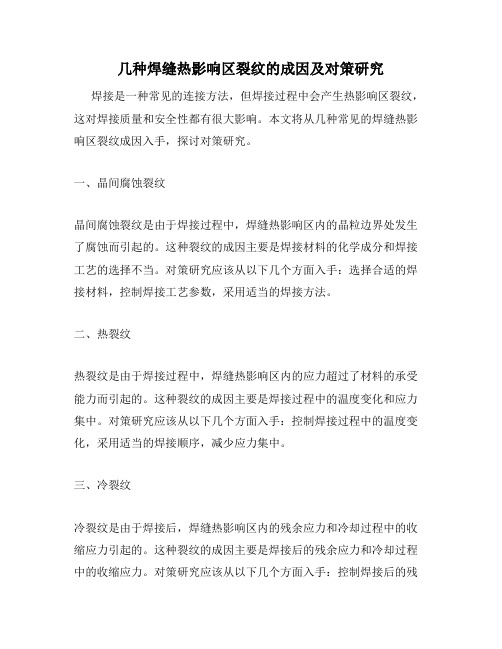
几种焊缝热影响区裂纹的成因及对策研究焊接是一种常见的连接方法,但焊接过程中会产生热影响区裂纹,这对焊接质量和安全性都有很大影响。
本文将从几种常见的焊缝热影响区裂纹成因入手,探讨对策研究。
一、晶间腐蚀裂纹
晶间腐蚀裂纹是由于焊接过程中,焊缝热影响区内的晶粒边界处发生了腐蚀而引起的。
这种裂纹的成因主要是焊接材料的化学成分和焊接工艺的选择不当。
对策研究应该从以下几个方面入手:选择合适的焊接材料,控制焊接工艺参数,采用适当的焊接方法。
二、热裂纹
热裂纹是由于焊接过程中,焊缝热影响区内的应力超过了材料的承受能力而引起的。
这种裂纹的成因主要是焊接过程中的温度变化和应力集中。
对策研究应该从以下几个方面入手:控制焊接过程中的温度变化,采用适当的焊接顺序,减少应力集中。
三、冷裂纹
冷裂纹是由于焊接后,焊缝热影响区内的残余应力和冷却过程中的收缩应力引起的。
这种裂纹的成因主要是焊接后的残余应力和冷却过程中的收缩应力。
对策研究应该从以下几个方面入手:控制焊接后的残
余应力,采用适当的焊接顺序,控制冷却速度。
综上所述,焊缝热影响区裂纹的成因主要有晶间腐蚀裂纹、热裂纹和
冷裂纹。
对策研究应该从选择合适的焊接材料、控制焊接工艺参数、
采用适当的焊接方法、控制焊接后的残余应力、采用适当的焊接顺序、控制冷却速度等方面入手。
只有这样,才能有效地预防焊缝热影响区
裂纹的产生,提高焊接质量和安全性。
铜电阻焊焊缝裂纹
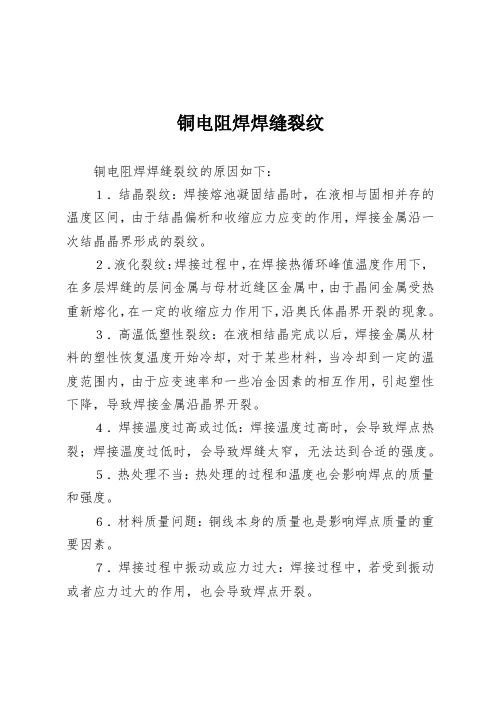
铜电阻焊焊缝裂纹
铜电阻焊焊缝裂纹的原因如下:
1.结晶裂纹:焊接熔池凝固结晶时,在液相与固相并存的温度区间,由于结晶偏析和收缩应力应变的作用,焊接金属沿一次结晶晶界形成的裂纹。
2.液化裂纹:焊接过程中,在焊接热循环峰值温度作用下,在多层焊缝的层间金属与母材近缝区金属中,由于晶间金属受热重新熔化,在一定的收缩应力作用下,沿奥氏体晶界开裂的现象。
3.高温低塑性裂纹:在液相结晶完成以后,焊接金属从材料的塑性恢复温度开始冷却,对于某些材料,当冷却到一定的温度范围内,由于应变速率和一些冶金因素的相互作用,引起塑性下降,导致焊接金属沿晶界开裂。
4.焊接温度过高或过低:焊接温度过高时,会导致焊点热裂;焊接温度过低时,会导致焊缝太窄,无法达到合适的强度。
5.热处理不当:热处理的过程和温度也会影响焊点的质量和强度。
6.材料质量问题:铜线本身的质量也是影响焊点质量的重要因素。
7.焊接过程中振动或应力过大:焊接过程中,若受到振动或者应力过大的作用,也会导致焊点开裂。
焊接横向裂纹产生的原因及控制

焊接横向裂纹产生的原因及控制焊接横向裂纹产生原因主要有以下几个方面:1、应力作用。
即钢管成型后的残余应力和焊接应力。
2、焊接工艺不合理。
如焊缝成形系数过小、预热温度不够或未进行焊前预热、焊接线能量过大、焊接后热处理不当、保温时间太短等。
3、由于氢的存在。
如焊剂烘干不够,预热温度不充分或未进行焊前预热、以及多层焊的层间温度不够。
4、冶金因素。
焊接过程中有低熔点杂质进入,如铜及铜合金。
铜的来源主要有焊丝表面所镀的用于防止焊丝锈蚀的铜,或者导电嘴、铜合金导电杆内壁被磨损产生的铜。
这些铜屑从导电嘴内孔进入焊剂,在焊接过程中接触焊接熔池导致横向裂纹。
控制措施:1、焊管成型。
为了合理控制残余应力,不仅需要采用针对性的设备和工艺,还需要在钢管成型前进行必要的成型工艺评定,对成型的设备、材料、产品的规格、预弯的程度、成型的速度、成型的压力、参数等进行试验和评定,合格后方进行焊管成型。
2、焊前预热。
要根据具体的材质、具体的工作环境确定预热及层间温度。
3、焊接工艺。
1)埋弧焊时,为了减少焊接热输入,不建议采用多丝焊,建议尽量采用单丝多道焊,焊道平行排列,且每条焊道的宽度控制在15min以内;层间温度控制在110-250℃。
2)严格控制焊道宽度焊道越宽,产生横裂的可能性越大。
焊接时,要尽量地采用窄焊道,多分道,减少焊道宽度,减少热输入。
4、焊接材料1)焊丝。
选择低强度的焊丝,这样可以适当降低焊缝的碳当量,提高焊缝的塑性,有助于减少焊接裂纹的产生。
同时注意使用不镀铜的焊丝,防止铜或铜合金进入焊缝熔池。
另外需要注意防潮和防生锈。
2)焊剂。
焊剂在使用前必须按照焊剂厂家推荐的烘干工艺烘干,烘干后在烘箱内进行保温,不可烘干后就倒出来,防止受潮。
及时对使用中的焊剂进行磁选,磁选后放进保温桶中储存,防止在空气中受潮。
及时更换焊剂,防止流落到焊剂内的铜及铜合金交换污染。
3)焊后保温、缓冷。
春秋两季,焊接好后可以在室温下直接暴露在空气中缓冷。
焊接接头再热裂纹产生原因、措施及方法

焊接接头再热裂纹产生原因、措施及方法再热裂纹的形成主要是由于焊接接头中的低合金高强钢材料中含有较多碳化物形成元素(如Cr、Mo、V),并且这些元素能够产生沉淀碳化物,从而导致焊后消除应力热处理过程中产生再热裂纹。
这种裂纹的形成机理在于晶内强度很大而晶界强度较弱,在应力松弛时的形变集中加在了晶界上,一旦晶界应变超出了晶界的强度极限,就会导致沿晶界开裂产生裂纹。
再热裂纹的预防措施为了预防再热裂纹的产生,需要采取以下措施:1.选择合适的焊接工艺和焊接材料,以减少裂纹的产生。
2.控制焊接接头的热输入和焊接过程中的温度,以减少应力的产生。
3.进行适当的后热处理,以减少残余应力和提高焊接接头的强度。
4.在焊接前进行材料的预热,以减少焊接接头中的应力和裂纹的产生。
再热裂纹的检验方法为了检验焊接接头中是否存在再热裂纹,可以采用以下方法:1.利用显微镜观察焊接接头的金相组织和裂纹情况。
2.采用磁粉探伤或超声波检测等无损检测方法,以检测焊接接头中是否存在裂纹。
3.进行拉伸试验和冲击试验,以检验焊接接头的强度和韧性是否符合要求。
总之,再热裂纹的产生是低合金高强钢焊接性要解决的主要问题之一,为了预防和检验再热裂纹的产生,需要采取相应的措施和方法。
微观检验是管道和部件质量检验的重要环节,包括浸蚀前和浸蚀后的检验。
浸前主要检查试样是否存在裂纹、非金属夹杂物和制样过程中的缺陷;浸蚀后主要检验试样的显微组织。
观察时,应先用显微镜的低倍率观察组织全貌,需要观察细微组织时再选用适宜的高倍率。
管道和部件的微观检验主要包括以下几个方面:a、鉴别材料中非金属夹杂物和显微裂纹的类型,观察其形态和分布,测量其数量和大小;b、鉴别被检件显微组织的组成,各种组织的形貌、分布和数量。
对晶粒度、带状组织、非金属夹杂物、XXX组织、球化组织、脱碳层等作出评定;c、鉴别组织特征,判定热处理工艺状态,必要时为重新制定热处理工艺提供依据;d、鉴别以上缺陷与所检裂纹之间的关联。
焊接裂纹产生原因及防治措施

以下为焊接裂纹产生原因及防治措施,一起来看看吧。
1、焊接裂纹的现象在焊缝或近缝区,由于焊接的影响,材料的原子结合遭到破坏,形成新的界面而产生的缝隙称为焊接裂缝,它具有缺口尖锐和长宽比大的特征。
按产生时的温度和时间的不同,裂纹可分为:热裂纹、冷裂纹、应力腐蚀裂纹和层状撕裂。
在焊接生产中,裂纹产生的部位有很多。
有的裂纹出现在焊缝表面,肉眼就能观察到;有的隐藏在焊缝内部,通过探伤检查才能发现;有的产生在焊缝上;有的则产生在热影响区内。
值得注意的是,裂纹有时在焊接过程中产生,有时在焊件焊后放置或运行一段时间之后才出现,后一种称为延迟裂纹,这种裂纹的危害性更为严重。
2、焊接裂纹的危害焊接裂缝是一种危害大的缺陷,除了降低焊接接头的承载能力,还因裂缝末端的尖锐缺口将引起严重的应力集中,促使裂缝扩展,最终会导致焊接结构的破坏,使产品报废,甚至会引起严重的事故。
通常,在焊接接头中,裂缝是一种不允许存在的缺陷。
一旦发现即应彻底清除,进行返修焊接。
3、焊接裂纹的产生原因及防治措施由于不同裂缝的产生原因和形成机理不同,下面就热裂缝、冷裂缝和再热裂缝三类分别予以讨论。
3.1、热裂纹热裂缝一般是指高温下(从凝固温度范围附近至铁碳平衡图上的A3线以上温度)所产生的裂纹,又称高温裂缝或结晶裂缝。
热裂缝通常在焊缝内产生,有时也可能出现在热影响区。
原因:由于焊接熔池在结晶过程中存在着偏析现象,低熔点共晶和杂质在结晶过程中以液态间层存在形成偏析,凝固以后强度也较低,当焊接应力足够大时,就会将液态间层或刚凝固不久的固态金属拉开形成裂缝。
此外,如果母材的晶界上也存在有低熔点共晶和杂质,则在加热温度超过其熔点的热影响区,这些低熔点化合物将熔化而形成液态间层,当焊接拉应力足够大时,也会被拉开而形成热影响区液化裂缝。
总之,热裂缝的产生是冶金因素和力学因素综合作用的结果。
防治措施:防止产生热裂缝的措施,可以从冶金因素和力学因素两个方面入手。
控制母材及焊材有害元素、杂质含量限制母材及焊接材料(包括焊条、焊丝、焊剂和保护气体)中易偏析元素及有害杂质的含量。
焊接裂纹的分析与处理

焊接裂纹的分析与处理焊接裂纹是焊接过程中常见的缺陷之一,它会降低焊接接头的强度和韧性,影响焊接工件的使用性能。
因此,对于焊接裂纹的分析和处理具有重要意义。
本文将从焊接裂纹的成因、检测方法、分析原因以及处理方法等方面进行综合讨论。
首先,焊接裂纹的成因可以归纳为以下几个方面:1.焊接材料的选择不当:焊接底材和填料材料的化学成分或力学性能不匹配,导致焊接接头受到内应力的影响而产生裂纹。
2.焊接过程中的温度变化:焊接过程中,由于热影响区的温度变化不均匀,会产生焊接接头内部的残余应力,从而造成裂纹。
3.焊接过程中的应力集中:焊接过程中,焊接接头处于高应力状态,如角焊接、搭接焊接等,容易造成应力集中,进而引发裂纹。
4.焊接过程中的焊接变形:焊接过程中,由于热变形和收缩的不均匀性,焊接接头可能会受到大的应力而产生裂纹。
其次,对焊接裂纹的检测方法有以下几种:1.可视检测法:用肉眼观察焊接接头表面是否有裂纹存在。
这种方法简单直观,但只能检测到较大的裂纹。
2.超声波检测法:通过超声波探测仪将超声波传递到焊接接头内部,根据超声波的传播和反射来判断是否存在裂纹。
这种方法可以检测到较小的裂纹,并且可以定量评估裂纹的大小和位置。
3.X射线检测法:通过X射线透射和X射线照相来检测焊接接头内部的裂纹。
这种方法可以检测到较小的裂纹,并且可以清晰地显示裂纹的形状和位置。
4.磁粉检测法:在焊接接头表面涂覆磁粉,通过观察磁粉的分布情况来判断是否存在裂纹。
这种方法适用于表面裂纹的检测。
然后,对焊接裂纹的分析原因可以采取以下步骤:1.裂纹形态分析:观察裂纹的形态,包括长度、宽度、走向等,可以初步判断裂纹的类型和可能的成因。
2.组织分析:通过金相显微镜观察焊接接头的组织结构,判断是否存在组织非均匀性或显微缺陷等。
3.应力分析:通过有限元分析或应力测试仪器测量焊接接头的应力分布,查找可能存在的应力集中区域。
4.化学成分分析:通过光谱分析或化学分析方法来检测焊接材料中的化学成分是否合格。
焊缝裂纹产生的原因

焊缝裂纹产生的原因
应力、拘束力、刚性、化学成分、焊缝预留的间隙、电流、焊道、母材清洁度等。
这些因素都可能是造成焊缝开裂。
虽然焊缝开裂原因很多,但在不同场合是多种因素造成,也有两种或三种因素造成的。
但不管几个因素,其中必有一个主要因素。
也有各种条件都没有什么影响,只受一个因素造成焊缝开裂。
因此出现焊缝开裂必须首先正确地分析出开裂的主要因素和次要因素,根据造成开裂的主要、次要因素采取相应措施进行解决。
焊接过程形成的焊缝是焊条和母材两者经过电流高温熔化后形成焊缝,是焊条和母材由固体变成液体,高温液体是热胀,冷却变成固体是收缩。
由于热胀冷缩,自然使焊接结构产生应力。
有些焊接结构本身就存有拘束力和刚性。
焊接过程是由固体变成液体,也就是由固态转变成液态(通常说铁水),再由液态变成固态,也就形成焊缝。
液态转变成固态(也就是铁水转变成晶粒)。
铁水变成晶粒的过程就是结晶过程。
母材温度低的位置先开始结晶,逐渐向焊缝中间位置伸展,焊缝中间最后结晶。
由于热胀冷缩的作用,焊接结构受应力或拘束力或刚性的影响,使母材晶粒连接不到一起,轻者在焊缝中间出现小裂纹,重者在焊缝中间出现明显的裂缝。
即使母材和电焊条的化学成分都好,受焊接结构的拘束力、刚性和焊接过程产生的应力影响,也会出现裂纹或裂缝。
如果母材和电焊条的化学成分不好(碳、硫、磷等偏高);或是焊缝预留间隙太大,母材在焊缝边缘杂质过多,或电流过大,并且焊接速度过快、过慢、焊道过宽等因素会使焊缝开裂情况更要加重。
焊接裂纹原因
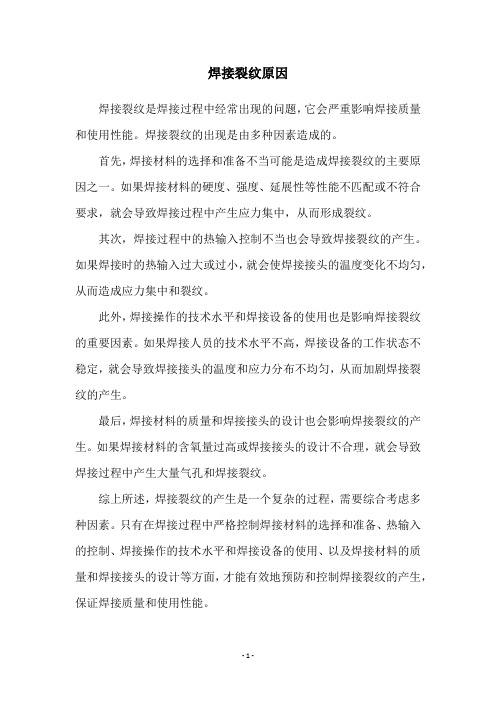
焊接裂纹原因
焊接裂纹是焊接过程中经常出现的问题,它会严重影响焊接质量和使用性能。
焊接裂纹的出现是由多种因素造成的。
首先,焊接材料的选择和准备不当可能是造成焊接裂纹的主要原因之一。
如果焊接材料的硬度、强度、延展性等性能不匹配或不符合要求,就会导致焊接过程中产生应力集中,从而形成裂纹。
其次,焊接过程中的热输入控制不当也会导致焊接裂纹的产生。
如果焊接时的热输入过大或过小,就会使焊接接头的温度变化不均匀,从而造成应力集中和裂纹。
此外,焊接操作的技术水平和焊接设备的使用也是影响焊接裂纹的重要因素。
如果焊接人员的技术水平不高,焊接设备的工作状态不稳定,就会导致焊接接头的温度和应力分布不均匀,从而加剧焊接裂纹的产生。
最后,焊接材料的质量和焊接接头的设计也会影响焊接裂纹的产生。
如果焊接材料的含氧量过高或焊接接头的设计不合理,就会导致焊接过程中产生大量气孔和焊接裂纹。
综上所述,焊接裂纹的产生是一个复杂的过程,需要综合考虑多种因素。
只有在焊接过程中严格控制焊接材料的选择和准备、热输入的控制、焊接操作的技术水平和焊接设备的使用、以及焊接材料的质量和焊接接头的设计等方面,才能有效地预防和控制焊接裂纹的产生,保证焊接质量和使用性能。
- 1 -。
- 1、下载文档前请自行甄别文档内容的完整性,平台不提供额外的编辑、内容补充、找答案等附加服务。
- 2、"仅部分预览"的文档,不可在线预览部分如存在完整性等问题,可反馈申请退款(可完整预览的文档不适用该条件!)。
- 3、如文档侵犯您的权益,请联系客服反馈,我们会尽快为您处理(人工客服工作时间:9:00-18:30)。
铜管钎焊热裂纹形成的原因与分析
田泽生
(北京万众空调制冷设备公司)
摘 要 本文阐述了铜管钎焊裂纹形成的常见原因及其金相组织状态。
关键词 铜管 钎焊 热裂纹
THECAUSE&ANALYSISABOUTTHECOPPER
TUBECRAZEDURINGWELDING
TIANZeSheng
(BeijingMTDConditioning&RefrigerationEquipmentCorp.)
ABSTRACT Thisarticleelaboratesthereasonaboutcoppertubecrazeduringweldingandthe
stateofmetalliccrystal
KEYWORDS Copper-tubeWeldingCraze
空调制冷业中大量铜质管材用于制造换热器
和输液管路。铜管之间的连接以及铜管与其它器件的连接,普遍采用火焰硬钎焊工艺。钎焊后有时会产生裂纹,造成在密封试验时泄漏。分析裂纹形成的原因主要有以下两个方面。1 操作不当造成钎焊温度过高钎焊是利用火焰加热母材和钎料使之达到钎料的熔化温度,熔化的钎料润湿在母材的表面并填充在结合间隙中。常用的钎料如黄铜、磷铜、银铜焊丝等其熔点均在700℃以上。钎焊时对母材加热应根据其形状、大小、异质材料的导热、散热性能照片1 80×以及选用的钎料种类等因素来掌握加热时间。如果加热温度过高,一种情况是使材料内部组织晶粒
过分长大,此时由于晶界在高温下强度降低甚至发
生流变,导致晶间裂纹形成(照片1)。另一种可能
是高温使母材局部熔化并重新结晶,此时会在熔化
区产生气孔(照片2),也使钎焊密封不良。
照片2 100×
2 铜管存在自身缺陷
有两种情况值得特别重视,一是铜管在生产加
工过程中造成损伤,个别部位存在微小裂纹或深入
管壁内部的缺陷(照片3、4)。恰将此处置于钎焊区,
第2卷 第2期
2002年4月
制冷与空调 REFRIGERATIONANDAIR-CONDITIONING
Vol.2,No.2
April2002
照片3管壁纵剖 30×照片4管壁纵剖 80×钎焊加热时随晶粒长大微裂纹或缺陷也随之扩大,以至穿透管壁,这种巧合虽然少见,但确有发生的实例。其二是铜管材料中某些微量元素含量较高导致钎焊裂纹发生。笔者曾遇到过一例T2铜管因含氧量高而造成的钎焊严重开裂。工艺操作正常,但钎焊后铜管出现明显的宏观裂纹,更严重的在焊接处自行断落。经取样作金相分析,发现热影响区晶界扩宽(照片5),进而作含氧量测定发现氧含量比正常值高数倍。氧在铜中呈氧化亚铜存在于晶界处,在焊接高温时与丙烷中氢发生反应生成水蒸汽,从组织内部将铜管胀裂。现在用二号磷脱氧铜制造的铜管广泛用于制冷设备,由于磷的脱氧作用使铜中氧的含量大大降低,从而避免了上述问题的发生。铜中除氧外还含有一些其它杂质元素。其含量超出正常值也是有害的,如铋、铅、硫在铜中生成低熔点化合物,大部聚集在晶界处,使铜的耐高温性能降低以至在正常的钎焊温度中仍有产生裂纹的危险。裂纹一旦产生,由于裂纹尖端的应力照片5 100×
效应会使裂纹随时间延续发生失稳扩展,是一种更
为严重的隐患。这种裂纹不仅发生在钎焊处温度
最高的地方,在钎焊热影响区内均可发生。金相分
析可发现裂纹周围的晶粒并不十分粗大(照片6、
7),足以说明绝非钎焊温度过高所致,这是此类裂
照片6 100×
照片7 100×
(下转第25页)
·72·
制 冷 与 空 调 第2卷
(1)选择更适合于描述湍浮力射流的数学模型,以便更好地处理浮力对冷风幕流动的影响。(2)分析相对湿度对陈列柜冷风幕负荷和柜内空气流动及换热的影响。(3)在货物堆放形式和堆放高度不同的条件
下,分析它们对陈列柜柜内空气流动及换热的影
响。
参考文献
1 GautherinW.,SrourS.,Influencedesconditionsclimatiquessurlefonstionnementdesequipements.19thInternational
Congressofrefrigeration,1995,2.705~712.
2 AnemaP.J.,Thechilledcabinetessentialinthefoodchains.19thInternationalConressofrefrigeration,1995,2.666~669.
3 AxellM.,FanhlenP.O.,Evaliationofcommercialrefrigeratedcabinet.19thInternationalConressofrefrigeration,1995,2.
673~680.
4 BilliaroF.,GautherinW.,Equipementenmeublesdeventeetconsommmationenergetique,19thInternationalConressofre-
frigeration,1995,2.689~695.
5 胡卫东,王启杰,罗来勤.轴对称卷吸紊流流动进口区的实验研究.西安交通大学学报,1989(23)6:43~48.
6 BELauder.OntheCalculationofGravitationalFieldontheTurbulentTransportofHeatandMomentum.JournalofFluid
Mechanics.1975,Volume67,Part3:569~581.
7 JirkaGH.TurbulentBuoyantJetsinShallowFluidLayers.InRodiW.TurbulentBuoyantJetsandPlumes.U.K.Perga-
monPress:69~120.
8 WesozowskiA,DworskiF.NewDevelopmentsintheDesignofOpenFrozenCabinetsforDisplayingFrozenfood.Progressin
RefrigerationScienceandTechnology.1975,Volume4:269~276.
9 牛璐琳.敞开式低温陈列柜冷风幕的流动及换热的研究.硕士学位论文.西安:西安交通大学,1996.
10 PapanicolaouE,JaluriaY.ComputationofTurbulentFlowInMixedConvectionInACavitywithALocalizedHeadSource.
JournalofHeatTransfer,1995,Volume17:649~658.
11 MurakamiS,KatoS,NakagawaH.NumericalPreDictionofHorizontalNonisothermal3-DJetInRoomBasedonThe
k—εModel.ASHRAETrans,1993,Volume99(1):38~48.
12 StriblingD,SavvasA,TassouDM.ATwo-dimensionalCFDModelofARefRigeratedDisplayCase.ASHRAETrans,
1997,Volume104(1):88~94.
13 刘冬毓.陈列柜空气流动与换热的研究.硕士学位论文.西安:西安交通大学,1997.
14 0ortVH,VanGerwenRJM.AirFlowOptimizationInRefrigeratedCabinetsIn:GrassoKAB.19thInternationalCongress
ofRefrigeration,1995,ProceedingsVolune2:446~451.
15 BaleoJN,GuyonnaudL,SolliecC.NumericalSimulationofAirFlowDistributionInARefRigeratedDisplayCaseAirCur-
tain.19thInternationalCongressofRefrigeration,1995,ProceedingsVolume2:681~688.
(上接第72页)
纹的一个重要特征。在没有条件作金相分析的情况下,可用放大镜作仔细的宏观检查,根据同批材料在钎焊区都有可能产生裂纹的特点,便可作出裂纹性质的判断。铜中杂质过量造成的钎焊热裂纹危害极大,应给以足够的重视。在确定属于此种原因后,同批铜管不应再用于有钎焊工艺的生产中。
对有钎焊裂纹的器件进行更换铜管的返修,无法返
修的果断地做报废处理。同时将发生质量问题的
有关信息反馈给铜管生产厂,通过交流、协商达成
双方满意的解决办法。
·25·
第2期 晏 刚等:敞开式陈列柜冷风幕的研究状况