3《辊底式热处理炉过程控制系统及应用》
PLC在热处理电阻炉温度控制系统设计中的应用

新疆工业高等专科职业技术学院毕业设计〔论文〕2012 级机电一体化专业题目:PLC在热处理电阻炉温度控制系统中的应用毕业时间:二〇一四年六月学生:李婕指导教师:何涛班级: 12机电一体化2013年 12月20日PLC在热处理电阻炉温度控制系统设计中的应用摘要:热处理电阻炉的温度控制系统对零件的热处理质量有着重要影响。
本文主要讨论了以可编程控制器(PLC)为核心的箱式热处理炉温度控制系统的设计。
在提出炉温控制方案的基础上,对炉温控制系统进行了硬件设计和温度控制程序的设计。
本文以45钢零件进行等温球化退炽热处理工艺为例,介绍炉温控制系统的具体应用。
关键词:热处理;电阻炉;温度控制;可编程控制器(PLC).一、关键技术与解决方案箱式热处理电阻炉是金属热处理中应用最为广泛的一种周期式作业炉,其测温控温系统对于保证工件的热处理质量具有重要作用。
传统箱式热处理电炉存在主要问题之一是炉温均匀度差,控温精度低,从而造成产品质量问题。
控温方式采用位式调节的箱式热处理炉,在教学实验、科学研究和零件热处理中有着广泛的应用,但由于其控温系统相对落后,常常导致温度控制不准确而造成实验数据的不准确或产品缺陷。
因此,针对位式调节的箱式热处理炉的温度控制系统进行改造设计,对于提高温控精度、保证产品质量具有十分重要的意义。
〔一〕、温度传感器的选取目前市场上温度传感器较多,主要有以下几种方案:方案一:选用铂电阻温度传感器。
此类温度传感器线性度、稳定性等方面性能都很好,但其成本较高。
方案二:采用热敏电阻。
选用此类元器件有价格廉价的优点,但由于热敏电阻的非线性特性会影响系统的精度。
方案三:采用K型〔镍铬-镍硅〕热电偶。
其可测量1312℃以内的温度,其线性度较好,而且价格廉价。
1 温度检测电路比较以上三种方案,方案三具有明显的优点,因此选用方案三。
〔二〕、控制电路部分图3 炉温控制系统工作流程1.选择K型热电偶,其测量温度范围为-200~+1200℃,在工业上应用最多,适应氧化性气氛,线性度好,可以充分保证测量精度。
辊底式热处理炉节能技术进展
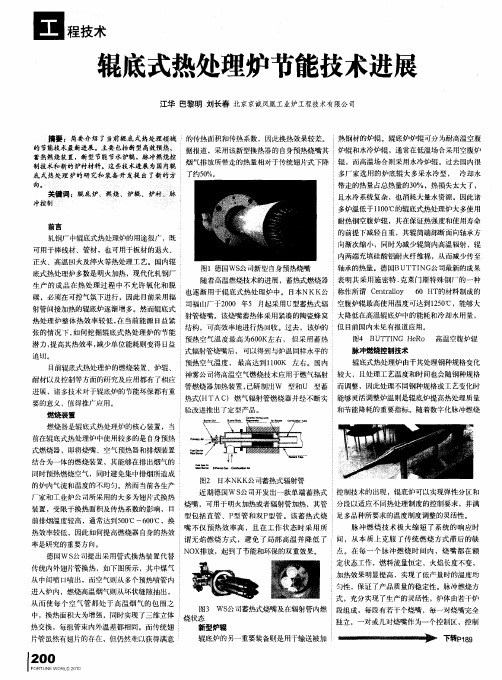
嘴 不仅 预热 效率 高 ,且在 工作 状态 时采 用所 热效率较低 ,因此如何提高燃烧 器 自身的热效
脉 冲燃 烧技 术极 大缩 短 了系 统的 响应时
率是研 究的重要方 向。
德 国W S公司提 出采用管式 换热装置代替
传统 内外翅片管换热 ,如下 图所示 ,其 中煤 气
从 中问喷 口喷 出,而空气则从多个预热喷管 内
蓄热 燃烧 装 置 ,新 型 节能 节水 炉辊 ,脉 冲燃 烧 控 制技术和新 的炉衬材料 这 些技术进展为国内辊
烟气排放所带走 的热 量相 对于传统翅片式下降
辊 ,而 高温场 合则采用水冷炉辊 。过去 国内很
底 式热处理 炉的研 究和装备开 发提 出 了新 的方 了约 50%。
多厂 家选用的炉底辊 大多采水冷 型 , 冷却水
司福 山厂于2000 年5 月起采用u型蓄热式辐 空 腹炉辊 最高使用温度可达 ̄1 ]1250 ̄C,能够大 射管间接加热的辊底炉逐渐增 多。然而 辊底式
射管烧嘴 。该 烧嘴蓄热体采用紧凑的陶瓷蜂 窝 大 降低在高温辊底炉 中的能耗和冷却水 用量 , 热处理炉 整体热效率 较低 ,在 当前能 源 日益 紧
轴承的热量。德国BUTTING公司最新的成果
随 着高温燃烧技 术的进 展,蓄热式燃 烧器 表 明其 采用施密 特 .克 莱门斯特殊 钢厂的 一种 生产 的成 品在 热处 理过 程 中不允 许氧 化和 脱
也 逐渐用于 辊底式热处 理炉 中。 日本NKK公 称作所谓 Centratloy 60 HT的材料制成的 碳 ,必须在可控气氛下进行 ,因此 目前采用辐
图2 日本NKK公司蓄热式辐射管 近期德 国w S公司开发 出一款 单端蓄热式 控 制技术的出现 ,辊底炉可以 实现弹性 分区和
中厚板无氧化低温辊底式热处理炉的脉冲控制策略

图 3 脉冲周期可调时序图
图 2 烧 嘴前阀门配置图
2 脉 冲控 制原 理
挺
一
一
一
一
脉冲 燃烧控 制是%一 种一 间断%燃 烧一 的方% 式 ,使用脉宽调
使无氧化 热处理 炉在 低温下获得 了很好 的温度均匀性 ,扩大了该热处理炉产品种类范 围,取得很好的效果 。
关键词 :辊底 炉; 中厚板;脉冲控制;温度均 匀性
中 图分类号 :TF341;TG156.1
文献标 志码 :A
文章 编号 :1002-1639(2011)03·0027—03
The Pulse Control Strategies of non-oxidation Low Tem perature Roller H earth H eat Treatment Furnace for Treat ing M edium and Heavy Plate DENG Yong—bin, FENG Yong·sheng
参考文献: 【1】闫晓燕,卫英 慧,胡 兰青 ,等.纳米 ZnO粉体的 制备及其 表
征 【J】.太原科 技大学学 报,2005,26 (3):224—227. 【2】钟香崇 ,贾 晓林 ,叶方保.矾土基莫来石纳米 粉体的制备方
法 :中国,CNl62395O [P].2005·06—08. [3】李玉生,郭贵宝,李 元,等.熔融法氧化钇纳米粉体的制备
图 4 脉 冲 周 期 固定 时 J芋图
优 点:按脉冲周 期定期进行 热负荷更新 ,经调 试可 找到最佳周期 时间,确保温度控 制有最佳 的动态性 能和 稳态偏差 ;燃烧 时间可设为较小值 ,小流量可控性好 。
LOI辊底式加热炉在济钢中厚板厂的应用
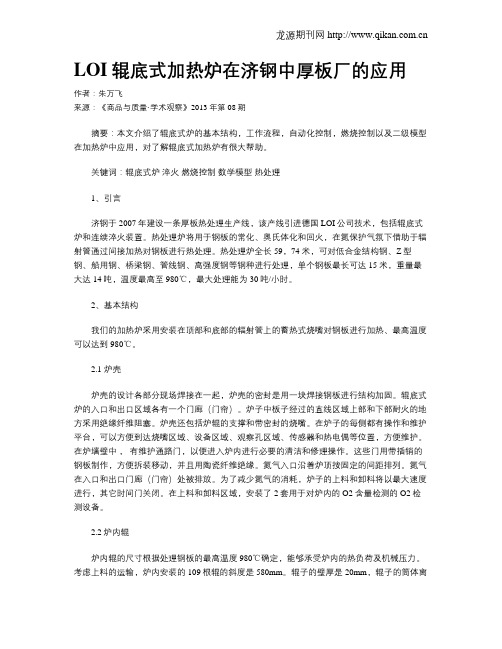
LOI辊底式加热炉在济钢中厚板厂的应用作者:朱万飞来源:《商品与质量·学术观察》2013年第08期摘要:本文介绍了辊底式炉的基本结构,工作流程,自动化控制,燃烧控制以及二级模型在加热炉中应用,对了解辊底式加热炉有很大帮助。
关键词:辊底式炉淬火燃烧控制数学模型热处理1、引言济钢于2007年建设一条厚板热处理生产线,该产线引进德国LOI公司技术,包括辊底式炉和连续淬火装置。
热处理炉将用于钢板的常化、奥氏体化和回火,在氮保护气氛下借助于辐射管通过间接加热对钢板进行热处理。
热处理炉全长59,74米,可对低合金结构钢、Z型钢、船用钢、桥梁钢、管线钢、高强度钢等钢种进行处理,单个钢板最长可达15米,重量最大达14吨,温度最高至980℃,最大处理能为30吨/小时。
2、基本结构我们的加热炉采用安装在顶部和底部的辐射管上的蓄热式烧嘴对钢板进行加热、最高温度可以达到980℃。
2.1 炉壳炉壳的设计各部分现场焊接在一起,炉壳的密封是用一块焊接钢板进行结构加固。
辊底式炉的入口和出口区域各有一个门廊(门帘)。
炉子中板子经过的直线区域上部和下部耐火的地方采用绝缘纤维阻塞。
炉壳还包括炉辊的支撑和带密封的烧嘴。
在炉子的每侧都有操作和维护平台,可以方便到达烧嘴区域、设备区域、观察孔区域、传感器和热电偶等位置,方便维护。
在炉墙壁中,有维护通路门,以便进入炉内进行必要的清洁和修理操作。
这些门用带插销的钢板制作,方便拆装移动,并且用陶瓷纤维绝缘。
氮气入口沿着炉顶按固定的间距排列。
氮气在入口和出口门廊(门帘)处被排放。
为了减少氮气的消耗,炉子的上料和卸料将以最大速度进行,其它时间门关闭。
在上料和卸料区域,安装了2套用于对炉内的O2 含量检测的O2检测设备。
2.2炉内辊炉内辊的尺寸根据处理钢板的最高温度980℃确定,能够承受炉内的热负荷及机械压力。
考虑上料的运输,炉内安装的109根辊的斜度是580mm。
辊子的壁厚是20mm,辊子的筒体离心浇注。
30CrMnSiA钢调质热处理炉温智能控制系统
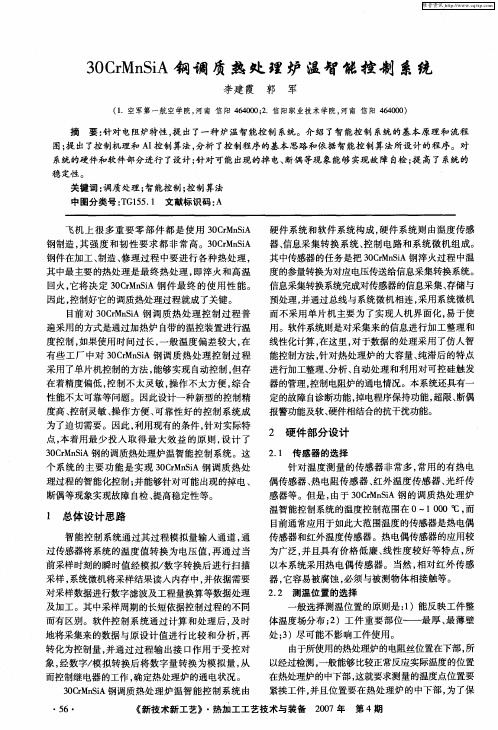
图; 出了 提 控制机理和 A 控制算法 , I 分析 了控制程序的基本 思路 和依据智能控制算法所设计的程序。对 系统的硬件和软件部分进行 了设计 ; 针对可能 出现的掉 电、 断偶等现 象能够实现故障 自 ; 高了系统的 检 提
稳定性 。
关键 词 : 质 处理 ; 能控 制 ; 制 算法 调 智 控 中图分 类号 :G 5 . 文献标 识 码 : T 15 1 A
20 0 7年 第 4期
地将采集来 的数据与原设计值进行 比较 和分析 , 再 转化为控制量 , 并通过过程输 出接 口作用于受控对 象, 经数字/ 模拟转换后将数字量转换为模拟量 , 从
而控制继电器 的工作 , 确定热处理炉的通电状况 。 3CM S 0 r ni A钢调质热处理炉温智能控制系统由
1 总体 设计思路
智能控制系统通过其过程模拟量输入通道 , 通
过传感器将系统的温度值转换为 电压值 , 再通过当
前采样时刻的瞬时值经模拟/ 数字转换后进行扫描
采样 , 系统微机将采样结果读入内存 中, 并依据需要 对采样数据进行数字滤波及工程量换算等数据处理
及加工。其中采样周期的长短依据控制过程的不同 而有区别。软件控制系统通过计算 和处理后 , 及时
回火 , 它将决定 3 CM S 0 r ni A钢件最终 的使用 性能。 因此 , 控制好 它 的调质 热处 理过 程就成 了关 键 。
目前 对 3 CMni 钢 调 质 热 处 理 控 制 过 程 普 0 r SA
遍采用 的方式是通过加热炉 自 带的温控装置进行温 度控制 , 如果使用时 间过长 , 一般温度偏差较大 , 在 有些工厂 中对 3 CM S 0 r ni A钢调 质热处 理控制过程
辊底式热处理炉数学模型
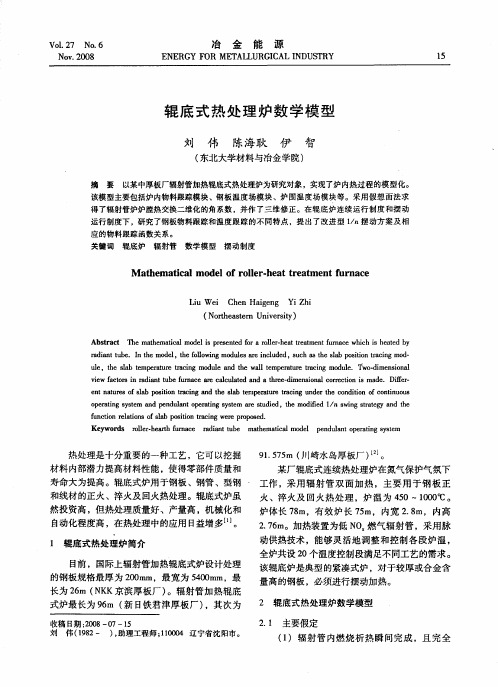
关键词
辊底 炉
辐射管
数学模型
摆动制度
M a he tc lm o e f r le . e tt e t n u na e t ma ia d lo ol r h a r a me tf r c
L u W e Ch n Hag n YiZh i i e ie g i
V0. 7 No 6 12 . No . 0 8 v2 0
冶
金
能
源
1 5
E RG R ME A L GI AL I NE Y F0 T L UR C NDUs R T Y
辊 底 式 热 处 理 炉 数 学 模 型
刘 伟 陈 海耿 伊 智
( 东北 大学材料 与冶金学 院)
摘 要 以某 中厚板厂辐射管加热辊底式热处理炉为研究对象 ,实现了炉内热过 程的模 型化。
该模型主要包括炉 内物料跟踪模块 、钢板 温度场模块 、炉围温度场模块等 。采用假 想面法求 得 了辐射管炉炉膛热交换二维化的角系数 ,并作 了三维修正。在辊底炉连续运行 制度和摆动 运行制度下 ,研究 了钢板物料跟踪和温度 跟踪的不 同特点 ,提 出了改进 型 1n摆 动方案及相 /
f n t n r lt n fs o i o a i gwee p o o e . u ci e a o o l p s in t c n r rp s d o is b a t r Ke wo d mi rh a t u n c rd a t u e mah maia d e p n u a t p r t g s e y rs l —e r fra e a i b e h n t t e t lmo l e d ln e ai  ̄tm c o n
热处理加热炉电气控制系统

课程设计说明书(2011 /2012 学年第 2 学期)课程名称:《可编程序控制器》课程设计题目:热处理加热炉电气控制系统设计专业班级:学生姓名:学号:指导教师:设计周数:二周设计成绩:2012年6月21日目录一、课程设计目的 (3)二、课程设计正文 (3)2.1设计原理 (3)2.2设计内容 (3)2.2.1 加热炉原理 (3)2.2.2 PID控制 (4)2.3设计要求 (4)2.4 I/O地址分配 (5)2.5程序流程图 (6)2.6 PLC主程序 (7)2.7 PLC源程序 (12)三、课程设计总结 (14)四、参考文献 (15)五、附表 (16)1、课程设计目的(1)了解掌握PLC控制系统的常用编程思路、程序功能。
(2)了解热处理加热炉的结构和工作过程。
(3)掌握PLC控制程序对热处理加热炉电气的控制。
2、课程设计正文2.1 设计原理通过PLC控制电机M1和电机M2,实现对物品加热进出炉,炉门开关的要求,对加热保温阶段采用PID控制2.2 设计内容2.2.1 加热炉原理加热炉具有热量传递过程。
热量通过金属管壁传给工艺介质,因此它们同样符合导热与对流传热的基本规律。
但加热炉属于火力加热设备,首先由燃料的燃烧产生炽热的火焰和高温的气流,主要通过辐射传热将热量传给管壁,然后由管壁传给工艺介质,工艺介质在辐射室获得的热量约占总热负荷的70%~80%,而在对流段获得的热量约占热负荷的20%~30%。
因此加热炉的传热过程比较复杂,想从理论上获取对象特性是很困难的。
加热炉的对象特征一般基于定性分析和实验测试获得。
从定性角度出发,可以看出其传热过程为:炉膛炽热火焰辐射给炉管,经热传导、对流传热给工艺介质。
所以与一般传热对象一样,具有较大的时间常数和纯滞后时间。
特别是炉膛,它具有较大的热容量,故滞后更为显著,因此加热炉属于一种多容量的被控对象。
根据若干实验测试,并做了一些简化,可以用一介环节加纯滞后来近似,其时间常熟和纯滞后时间与炉膛容量大小及工艺介质停留时间有关。
新型淬火线工艺及功能分析

一
四、淬火系统
淬火机框 架分成 上下两 部分 。底部框 架 是 固定 的, 上 部框架 由导辊 限制, 并 且可 以通 过 螺旋 升降机构进 行调节 钢 板实 际厚度通 过 炉内尾部光栅监 测 ,当淬火机上框 架调整 到与实际钢板厚度后 ,钢板 出炉进入淬火机 。 连 续淬火机可均 匀淬火 ,它不压紧 ,以免 留 下划 痕或者损坏钢 板表面 。在钢板 的宽度方 向上, 高压段 分为 三部分 , 每 部分单 独供 水和 调整水量 。为避免瓢 曲,需调节高压 端各部 分水流量来使 钢板顶部和 底部具有相 同冷却 速度。 高压水幕 在淬火机入 口处 ,分别位于钢 板上部和下部 ,喷 口间隙,喷射角度 是可调 节的 。上下部 喷嘴及连 接切断 阀的供水管 由 不锈钢制 造。水幕 头后面 是 “ 喷射箱 ” ,上部 和下部各有 3排喷嘴由不锈钢 制造,水幕从 同一个 高压 泵 中提供 。这些喷嘴 相对运行 线 以一定 的角度 安装 。上部与 阀相 连的供水 管 由不锈钢 制造,高压段还包 括 2 组喷 管,每 个提供 6排 HP喷嘴 。 低压段有 1 2组阀,每组提供 3到 4排喷 管 ,这 些带钻孔 的喷管相对钢 板运输 以不同 角度 安装。这些 阀和供水 管由不锈钢 制造。 切 断阀和流量 调节阀是液 压控 制 的蝶 阀,流 量控制 阀 由电机控 制。淬火机 上部和下 部流 量控 制阀和切 断阀各 自独立 。最后一 段高压 部分 在宽度上 是一个整体 ,但 其上部 和下部
- 1、下载文档前请自行甄别文档内容的完整性,平台不提供额外的编辑、内容补充、找答案等附加服务。
- 2、"仅部分预览"的文档,不可在线预览部分如存在完整性等问题,可反馈申请退款(可完整预览的文档不适用该条件!)。
- 3、如文档侵犯您的权益,请联系客服反馈,我们会尽快为您处理(人工客服工作时间:9:00-18:30)。
收稿日期:2011-03-16作者简介:唐郑磊(1985-),男,助理工程师,双学位,主要从事宽厚板方面的技术工作。
Process Controlling System and Its Application for Roller Hearth Heat -treating FurnaceTANG Zheng -lei ,ZHANG Hong -wei ,YANG Dong ,ZHU Cheng -jie(Nanyang Hanye Special Steel Co.,Ltd.,Nanyang474500,China )ABSTRACT :The article analyzes comprehensively the process controlling distinguishing features of roller hearth heat -treating furnace of Nangang.Moreover on the basis of mathematical model of roller hearth furnace ,achieves computer optimal controlling of roller hearth heat -treating furnace.The online optimal controlling of roller hearth heat -treating furnace can achieve real-time tracking of plate position inner furnace ,dynamic calculation of the temperature ,the best temperature optimization and online feedback correction ,plate loading and unloading online correction and other functions ,finally realizes the computer controlling system network in the whole line.KEY WORDS :roller hearth heat-treating furnace ;process controlling ;mathematical model ;optimal controlling摘要:以南钢辊底式热处理炉为研究对象,全面分析了其过程控制特点。
并以辊底式热处理炉数学模型为基础,实现了辊底式热处理炉的计算机优化控制。
该辊底式热处理在线优化控制可实现炉内钢板位置的实时跟踪、温度的动态计算、最佳炉温优化及在线反馈修正、钢板装出炉在线修正等功能,最终实现了全线计算机控制系统网络。
关键词:辊底式热处理炉;过程控制;数学模型;优化控制中图分类号:TF 806.4文献标识码:A文章编号:1005-6084(2011)03-0019-05唐郑磊,张红伟,杨东,朱承杰(南阳汉冶特钢有限公司,河南南阳474500)2011年6月Jun 2011METAL MATERIALS AND METALLURGY ENGINEERING辊底式热处理炉过程控制系统及应用热处理工艺是中厚板生产的最后处理工序,热处理在这个过程中扮演着极其重要的角色,钢板的加热质量将直接影响产品的质量。
辊底式热处理炉由于其处理的钢材质量好,产量高,易于实现机械化、自动化操作而被广泛应用于冶金及机械行业生产中[1]。
辐射管加热辊底式热处理炉由于充入氮气做保护气,炉内保持无氧化气氛,使钢板不会被氧化,大大提高了钢板的加热质量[2]。
本文针对南阳汉冶特钢有限公司已建成的采用辐射管加热的辊底式热处理炉进行研究,全面分析了其过程控制特点,并以辊底式热处理炉数学模型为基础,实现了辊底式热处理炉的计算机优化控制。
1南阳汉冶特钢有限公司辊底式热处理炉南阳汉冶特钢有限公司的辊底式热处理炉用于钢板的淬火、正火(常化)、回火,正火﹢回火,退火等。
辊底式热处理炉炉子有效炉长为85800mm,炉膛内宽4100mm。
在炉子有效加热长度上分12个炉节,每个炉节分上、下温度控制段,全长有24个温度控制段(上12个,下12个)。
共有340个辐射管烧嘴。
采用脉冲燃烧控制自身预热式烧嘴进行炉温自动控制,根据设定的炉温,对燃气及空气量自动进行增减,以适应不同热处理制度的控制要求,满足不同品种所要求的工艺制度。
炉子装有143根炉辊,采用单独传动,交流变频调速。
炉辊传动分为三个速度区域:入炉区、中间区和出炉区(见图1)。
根据加热钢板的厚度可任意调整炉辊速度。
图1炉辊传动示意辊底炉过程控制计算机系统的主要任务是按生产工艺要求,对辊底炉内的钢板进行合理的加热,准确控制钢板的出炉温度和均匀度,降低钢板的氧化烧损,在提高加热质量及产量的前提下节省能源,并对辊底炉区内的钢板进行跟踪和控制。
辊底炉过程控制计算机主要完成如下功能:钢板核对、钢板跟踪、实际数据处理、燃烧模型、炉温设定计算、操作和显示画面等。
2.1钢板核对用辊底式热处理炉操作室HMI上显示的热处理计划数据和钢板PDI数据,与辊底式热处理炉区入口辊道上实测的钢板宽度和钢板长度等数据进行核对,判断钢板是否正确。
2.2钢板跟踪对热处理炉区的钢板运行状况进行跟踪和控制。
它根据L1级计算机系统传来或操作员输入的钢板数据,结合热处理炉机械设备的动作情况,跟踪钢板在热处理炉区的位置并保留当前炉区所有钢板的分布图。
炉区物料跟踪是根据钢板在辊道上移动时冷热金属检测器、编码器产生的信号,或其他可用信号,及时正确地反映钢板的实际位置。
炉区的物料跟踪包括热处理炉的入口跟踪、炉内跟踪、出口跟踪。
2.2.1辊底炉入口侧钢板位置跟踪从钢板被吊到对中辊道开始到钢板至钢板入炉结束,包括钢板的测宽测长。
当钢板进入热处理炉炉区时,系统根据上一级计算机传来的数据同实际检测的数据进行钢板数据的检验,同时对入炉钢板数据建立数据跟踪记录。
钢板通过装料炉门的冷热金属检测器时,由电气PLC 传来的检测器的接通(或断开)信号和运送钢板的辊道的旋转方向信号是钢板位置跟踪的依据,它允许正向和反向跟踪。
当钢板定位完毕,本入口跟踪记录完成。
2.2.2辊底炉内跟踪炉内每一块钢板都有一个跟踪记录。
检测信号来自辊道编码器。
这些记录在计算机内以钢板的入炉顺序依次排列,中间不留空白,并随着钢板的向前移动而移动、随着相应钢板的入炉而出现,且随着相应钢板的出炉而删除。
2过程控制系统的特点及研究21 2011年第3期唐郑磊等:辊底式热处理炉过程控制系统及应用钢板每前进一个料位或后退一个料位,炉内跟踪将自动正向和反向跟踪。
在炉内长度方向上设若干HMD,对以上跟踪坯料进行修正。
2.2.3辊底式热处理炉出口侧钢板位置跟踪从钢板出钢开始至钢板离开炉内辊道结束。
当钢板输送到炉内出料辊道上,热金属检测器接通(或断开)信号以及辊道的旋转方向是跟踪的依据,它允许正向和反向跟踪。
每次出炉热金属检测器接通,就进行炉内跟踪到出口跟踪的转换,由炉内跟踪记录编辑出口跟踪记录。
2.2.4跟踪修正为了保持跟踪的正常,在某些情况下使用一些自动或手动的修正方法,包括钢板核对异常时的钢板吊销。
当钢板在辊道上进行钢板核对时,如果钢板实测长度与计算机中钢板长度之差超过允许范围值,或者钢板上的实际钢板号与计算机中的钢板号不一致时,由操作人员判断此钢板是否允许继续装入辊底式热处理炉。
如果不能装入辊底式热处理炉,进行“钢板吊销”操作。
2.2.5数据强制装入当钢板已经被装入到辊底式热处理炉里,而数据还停留在炉前辊道时,需要进行“数据强制装入”操作。
2.2.6炉内位置的修正在炉内长度方向上设若干HMD,利用炉内HMD接通,自动对炉内钢板的位置进行修正。
当误差大于设定值时,可以认为不是误差的累积,而是跟踪有误,因此不进行误差修正,而进行报警输出。
2.2.7数据强制抽出当钢板已经从辊底式热处理炉到出炉辊道上,而数据还停留在辊底式热处理炉内时,需要进行“数据强制抽出”操作。
2.2.8跟踪位置修正为使炉区钢板的实际位置与L2识别的位置相一致,操作人员人工修正L2识别的位置。
2.3实际数据处理实际值数据来源于辊底式热处理炉入口辊道始至出炉之间的装置或仪表,具体包括:辊底式热处理炉装入钢板的长度测量值,辊底式热处理炉入炉钢板温度值,炉内实际值,实际的钢板宽度,休炉实绩。
2.4钢板温度计算的热工模型热处理炉热工数学模型用于周期性地(如每分钟一次)计算炉内每一块钢板的温度分布,温度变化和特殊热焓。
钢板温度计算是通过一个二元有限差分模型进行在线计算的。
通过炉内热元件的热辐射、炉膛尺寸、炉内气氛、炉墙导热系数等基本参数,建立起本热交换模型。
根据系统中存储钢板的尺寸、材质、规格、钢板在炉内的位置,钢板的运行速度,同时考虑辊道的影响,对每一代表钢板沿长度方向上的纵向剖面进行网格结点的温度计算。
不同钢种的热工物理特性被作为温度功能,存储在系统内的钢种数据表中。
对于每一结点,在线模型都运用所要求的热物理特性的合适的插入值作为当前结点温度的计算。
根据热处理炉的设计,该模型根据当前钢板在炉内的位置动态地改变不同的观察因子。
重要的一点要注意系统内所有的热交换计算都使用同上所述的热工模块,包括设定值计算,热处理炉生产率计算和离线模拟应用。
2.4.1炉温设定值的计算炉温设定值计算软件周期性地(如每一分钟)计算以确定热处理炉每个燃烧控制段的合适的温度设定值。
炉温设定值计算的目的是决定燃烧控制段的温度设定值,使控制段的每一块钢板到达其控制段末端时能被加热到理想的温度分布。
计算过程如下:(1)获取热处理炉内工件当前的温度:当前的热工条件和由热工模型计算得到的钢板温度分布。
(2)预测热处理炉出钢节奏:这个功能是在完成一次出钢动作时开始执行,它根据前热处理炉实际出钢节奏来预测以后的热处理炉出钢节奏。
(3)预测钢板的在炉时间。
(4)预测钢板的出钢温度:采用钢板温度计算同样的热工模型进行预测计算。
(5)确定各燃烧控制段的炉温设定值:一个燃烧控制段的温度设定值要综合考虑这个段的炉温能影响到的所有钢板,要使这些钢板出炉时都能尽量达到理想的加热状况。
因此,根据燃烧控制段温度对每一块钢板影响力的不同,对这些计算出来的炉温设定值进行加权计算,得出累计均方差最小的最佳温度设定值。
由于该设定温度是计算机根据实际的钢板精密计算而得出的,所以其较传统的人工根据经验设定温度要精确和合理得多。
(6)确定各燃烧控制段对每一块钢板加热最佳的炉温设定值:计算机里保存有每一种钢板在热处理炉内的最佳热处理曲线,把预测的钢板出钢时的加热状况与最佳升温曲线所要求的情况相比较,从而确定钢板能达到理想加热状况的炉温设定值。