模内铆接在级进模上的应用
飞机装配中先进手持铆接工具应用实践

飞机装配中先进手持铆接工具应用实践摘要:随着科技的不断发展,飞机制造业正在经历着前所未有的变革。
作为飞机制造过程中至关重要的一环,飞机装配的效率和精度对于飞机的性能和安全性具有直接的影响。
近年来,手持铆接工具在飞机装配中得到了广泛应用,大大提高了飞机装配的效率和灵活性。
本文将详细介绍先进手持铆接工具在飞机装配中的应用和实践,以期为相关领域的技术发展提供一些有益的参考。
关键词:飞机装配;手持铆接工具;应用手持铆接工具是飞机装配过程中常用的装配工具,通过铆接后铆接孔之间的连接强度,将被连接件可靠地连接在一起,从而使其成为一个整体,实现飞机结构的一体化装配。
由于铆接过程中铆接质量是影响装配质量的重要因素之一,因此如何提高铆接质量是每一个航空制造企业面临的一个难题。
本文主要介绍了在飞机制造过程中手持铆接工具的应用,以及在应用过程中如何保证铆接质量和精度,为手持铆接工具在飞机装配中的应用提供参考。
1.手持铆接工具的基本原理及组成手持铆接工具由气动系统、连接系统、传动系统、铆接操作装置和控制系统组成。
气动系统由气动马达、气体过滤装置和控制开关组成;连接系统由螺纹连接件和辅助铆接工具组成;传动系统由电机、减速器和制动器组成;铆接操作装置由操作手柄、铆枪、铆钉夹紧装置及辅助工具组成;控制系统由电气控制柜和人机界面组成。
气动原理图中,气动马达的旋转运动与铆钉枪的往复运动相结合,完成铆钉枪在钉杆上的移动。
当铆钉枪移动到所需位置时,气控马达向铆钉枪输出反向的拉力,使铆钉枪沿轴线方向移动,从而完成一个铆接操作。
在这个过程中,铆钉枪在钉杆上的移动通过对控制开关的操作来实现。
手持铆接工具的主要作用是在铆接过程中利用工具将被连接件可靠地连接在一起,以提高产品连接强度。
由于手持铆接工具具有使用方便、操作简单、工作可靠等优点,因此被广泛应用于飞机装配中。
手持铆接工具在实际使用过程中受到多方面因素的影响,如手持铆接工具的使用寿命、铆接质量等。
铆钉和焊接的应用及技术发展趋势
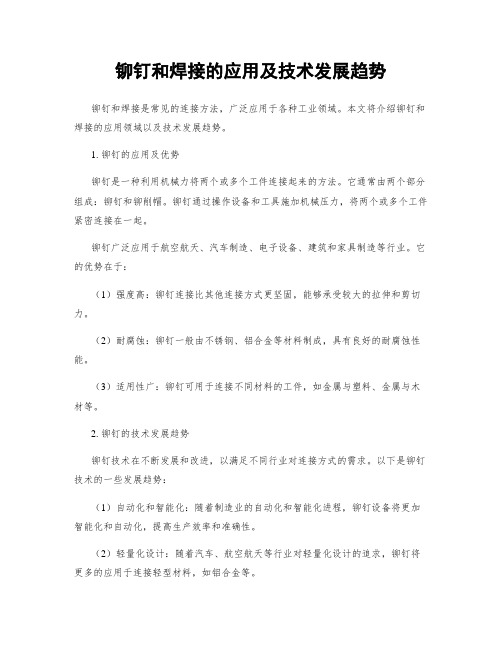
铆钉和焊接的应用及技术发展趋势铆钉和焊接是常见的连接方法,广泛应用于各种工业领域。
本文将介绍铆钉和焊接的应用领域以及技术发展趋势。
1. 铆钉的应用及优势铆钉是一种利用机械力将两个或多个工件连接起来的方法。
它通常由两个部分组成:铆钉和铆削帽。
铆钉通过操作设备和工具施加机械压力,将两个或多个工件紧密连接在一起。
铆钉广泛应用于航空航天、汽车制造、电子设备、建筑和家具制造等行业。
它的优势在于:(1)强度高:铆钉连接比其他连接方式更坚固,能够承受较大的拉伸和剪切力。
(2)耐腐蚀:铆钉一般由不锈钢、铝合金等材料制成,具有良好的耐腐蚀性能。
(3)适用性广:铆钉可用于连接不同材料的工件,如金属与塑料、金属与木材等。
2. 铆钉的技术发展趋势铆钉技术在不断发展和改进,以满足不同行业对连接方式的需求。
以下是铆钉技术的一些发展趋势:(1)自动化和智能化:随着制造业的自动化和智能化进程,铆钉设备将更加智能化和自动化,提高生产效率和准确性。
(2)轻量化设计:随着汽车、航空航天等行业对轻量化设计的追求,铆钉将更多的应用于连接轻型材料,如铝合金等。
(3)多材料连接:随着技术的发展,将会有更多的铆钉技术用于不同材料之间的连接,如金属与复合材料的连接。
(4)无损检测技术:随着对产品质量要求的提升,无损检测技术将更多应用于铆钉连接的质量控制,以保证连接的可靠性。
3. 焊接的应用及优势焊接是将两个或多个工件通过加热或压力相互熔合在一起的方法。
它是一种常用的连接技术,广泛应用于制造业的各个领域。
焊接的应用范围包括:(1)船舶和海洋工程:焊接在造船和海洋工程中起着至关重要的作用,在船舶的建造和维护过程中广泛应用。
(2)汽车制造业:焊接是汽车制造过程中最重要的连接方法之一,在车身结构和零部件的制造中广泛使用。
(3)建筑和桥梁工程:焊接在建筑和桥梁工程中用于连接不同材料的构件,提高结构的抗震和承载能力。
焊接的优势在于:(1)连接强度高:焊接产生的连接点强度高于其他连接方式,能够承受较大的力。
多工位级进模的使用条件与合理应用

多工位级进模的使用条件与合理应用使用多工位级进模的条件有以下几点:1.任务之间的独立性:多工位级进模适用于任务之间相互独立的情况。
如果任务之间需要共享数据或相互依赖,则需要考虑使用其他并发模型。
2.高度并行的任务:多工位级进模适用于可以被切分成小任务并且可以同时进行的任务。
如果任务之间存在较多的串行操作或阻塞操作,则并行性的效果不明显,可能不适合使用多工位级进模。
3.可扩展性:多工位级进模适用于可以动态添加工作线程的任务。
如果任务的数量是固定的,或者不会发生频繁的变动,则没有必要使用多工位级进模。
合理应用多工位级进模可以带来以下几个优点:1.提高程序的执行效率:通过同时执行多个任务,可以充分利用计算机的多个处理单元,提高任务的并行程度,从而加快任务的执行速度。
2.提高系统的响应能力:使用多工位级进模可以将耗时的任务分配给后台线程进行处理,从而减小主线程的负担,提高系统的响应能力。
例如在图形界面程序中,可以将一些耗时的操作(如文件读写、网络通信等)放到后台线程中执行,避免主线程的阻塞。
3.提高系统的可靠性:使用多工位级进模可以将任务分配给多个线程来处理,当其中一个线程出现错误或异常时,不会影响到其他线程的执行。
这样可以提高系统的容错性和稳定性。
4.提高系统的可扩展性:多工位级进模允许动态添加和删除工作线程,可以根据任务的数量和负载情况动态调整线程的数量,从而提高系统的可扩展性。
1.并行计算:对于大规模的计算任务,可以将任务分成多个小任务,分配给不同的工作线程来同时执行,从而加快计算速度。
例如在科学计算、数据分析等领域中,可以使用多工位级进模来提高计算效率。
2.图片/视频处理:对于图像或视频处理任务,可以将耗时的操作(如图像滤波、视频编码等)放到后台线程中执行,以提高用户界面的响应速度。
同时,可以利用多工位级进模来实现多个图像/视频的并行处理,加快处理速度。
3.并发网络通信:在网络通信中,可以使用多工位级进模来处理大量的并发连接。
铆工技术的优势和应用领域分析

铆工技术的优势和应用领域分析铆工技术是一种常见的连接技术,广泛应用于航空、汽车、船舶、机械制造等领域。
它通过将两个或多个金属件通过铆钉连接起来,形成坚固的结构。
相比于焊接和螺栓连接等传统方法,铆工技术具有许多独特的优势,使其在各个领域得到广泛应用。
首先,铆工技术的优势之一是连接强度高。
铆钉连接形成的连接点坚固可靠,能够承受较大的拉伸和剪切力。
这对于需要承受大荷载的结构非常重要,比如飞机机身、汽车底盘等。
铆工连接还能够有效分散应力,提高结构的整体强度,增加其抗震性能。
其次,铆工技术的另一个优势是连接方式多样。
铆工技术可以根据不同的需求选择不同的连接方式,如实心铆接、空心铆接、半空心铆接等。
这些不同的连接方式适用于不同的材料和结构,提供了更多的选择空间。
此外,铆工技术还可以连接不同材料的金属件,如铝合金与钢材的连接,扩大了其应用范围。
另外,铆工技术的第三个优势是施工便捷。
相比于焊接,铆工不需要大量的设备和复杂的操作,施工过程相对简单。
铆接过程中不产生高温和明火,避免了火灾和爆炸的风险。
此外,铆工技术对工件的表面处理要求较低,不需要进行除锈和涂装等繁琐的工序,节省了时间和成本。
铆工技术的应用领域非常广泛。
首先,在航空航天领域,铆工技术是连接飞机机身、发动机、翼面等部件的主要方法。
由于铆工连接具有轻量化、高强度和抗疲劳等特点,能够满足航空器对结构强度和安全性的要求。
其次,在汽车制造领域,铆工技术被广泛应用于汽车底盘、车身和车门等部件的连接。
铆工连接能够提高汽车的整体刚性和抗冲击性能,增加车身的稳定性和安全性。
同时,铆工连接还能够减轻汽车的自重,提高燃油经济性。
此外,铆工技术还在船舶制造、机械制造、电子设备制造等领域得到广泛应用。
在船舶制造中,铆工连接用于连接船体结构、船板和甲板等部件。
在机械制造中,铆工连接用于连接机械设备的零部件,如轴承座、齿轮和连杆等。
在电子设备制造中,铆工连接用于连接电子设备的外壳和散热片等部件。
连接支架自动攻丝多工位级进模设计

连接支架是某等离子 电视 的固定支架之一 , 材料 位上 。
A— A
\
/ 厂
/
l ,
I
小
/ j l— 寸 l 。 。 l f
/
。
-
={ = ==
—
—
—
—
—
ห้องสมุดไป่ตู้
J
件经过铆接模铆合在一起 )所需模具及设备较多 , , 机
床利用率低 , 而且成本较高 , 并且零件的铆接部分在 流水线上安装时容易脱落 、 松动造成质量不稳定 。经
中图分 类 号 :G 8 . T 3 52 文 献标 识 码 : B 文章 编 号 :S 0 0 — 0 C 2 1— 7 0 7 1
De i n o u t- o ii n Pr g e sv e sg fM li P st o r s i e Di o
f rt eJ i t u p r tmae a pn o h on p o t S Au o td T p ig
Ke r sjitu p r s m ig e h ooy l o t ei ; ut p s i rge s e i ywo d :o p ot t pn c n lg;a u s n m l - oio porsi e ns ; a t y d g i tn vd
1 零 件分 析
【 b tatI i pprtesu tr o e on spot uo ae p igi eporsie A s c】nt s ae,h t c e fh itu pratm tdt pn t rges r h r u t j a nh v
dei it d cdtru hatc n l ia a a s ftejit u p r p r a di d s n dte i s nr u e o g h oo cl n l i o o p ot at n ei e h o h e g ys h ns s g
多工位级进模的装配工艺及装配要点

第一章多工位级进模的装配工艺及装配要点(总10页)--本页仅作为文档封面,使用时请直接删除即可----内页可以根据需求调整合适字体及大小--教学项目四多工位级进模的装配、调试1.项目目标提高多工位级进模的装配和调试综合能力。
2.项目内容能进行多工位级进模的装配能熟练操作冲压设备能进行多工位级进模的调试工作3.项目要求能识读多工位级进模的装配图及相关工艺文件,能制订多工位级进模的装配工艺,并能按装配工艺进行正确装配作业能熟练操作冲压设备,正确安装模具,并调整冲压行程能进行多工位级进模的调试,并能分析常见质量问题第一章多工位级进模的装配工艺及装配要点第一节多工位级进模具结构要点一、级进模具有以下优点1)级进模是多工序冲模,在一副模具内,可以包括冲裁、弯曲、成形和拉深等多种多道工序,具有比复合模更高的劳动生产率,也能生产相当复杂的冲压件;2)级进模操作安全,因为人手不必进入危险区域;3)级进模设计时,工序可以分散。
不必集中在一个工位,不存在复合模中的“最小壁厚”问题。
因而模具强度相对较高,寿命较长。
4)级进模易于自动化,即容易实现自动送料,自动出件,自动叠片;5)级进模可以采用高速压力机生产,因为工件和废料可以直接往下漏;6)使用级进模可以减少压力机,减少半成品的运输。
车间面积和仓库面积可大大减小。
级进模的缺点是结构复杂,制造精度高,周期长,成本高。
因为级进模是将工件的内、外形逐次冲出的,每次冲压都有定位误差,较难稳定保持工件内、外形相对位置的一次性。
但精度高的零件,并非全部轮廓的所有内、外形相对位置要求都高,可以在冲内形的同一工位上,把相对位置要求高的这部分轮廓同时冲出,从而保证零件的精度要求。
二、冲压工序顺序安排的原则1)对于纯冲裁级进模,原则上先冲孔,随后再冲切外形余料,最后再从条料上冲下完整的工件。
应保持条料载体的足够强度,能在冲压时准确无误送进。
2)对于冲裁弯曲级进模,应先冲切掉孔和弯曲部分的外形余料,再进行弯曲,最后再冲靠近弯边的孔和侧面有孔位精度要求的侧壁孔。
折弯模具设计

折弯模具设计中国模具行业要进一步进展多功能复合模具, 一套多功能模具除了冲压成型零件外, 还担负叠压、攻丝、铆接与锁紧等组装任务。
据兰格钢铁10月18日报道, 中国模具行业将向大型、精密、复杂、高效、长寿命与多功能方向进展。
电子、汽车、电机、电器、仪器、仪表、家电、通讯与军工等产品中, 60%至80%的零部件, 都要依靠模具成型。
用模具成型的制件所表现出来的高精度、高复杂性、高一致性、高生产率与低消耗, 是其他加工制造方法所无法比拟。
模具在很大程度上决定着产品的质量、效益与开发能力。
专家认为, 中国模具行业日趋大型化, 而且精度将越来越高。
10年前, 精密模具的精度通常为5μm, 现在已达2至3μm。
不久, 1μm精度的模具将上市。
随着零件微型化及精度要求的提高, 有些模具的加工精度公差就要求在1μm下列, 这就要求进展超精加工。
中国模具行业要进一步进展多功能复合模具, 一套多功能模具除了冲压成型零件外, 还担负叠压、攻丝、铆接与锁紧等组装任务。
通过这种多功能的模具生产出来的不再是成批零件, 而是成批的组件, 如触头与支座的组件、各类微小电机、电器及仪表的铁芯组件等。
多色与多材质塑料成形模具也将有较快进展。
这种模具缩短了产品的生产周期, 今后在不一致领域将得到进展与应用。
随着热流道技术的日渐推广应用, 热流道模具在塑料模具中的比重将逐步提高。
使用热流道技术的模具可提高制件的生产率与质量, 并能大幅度节约制件的原材料, 这项技术的应用在国外进展很快, 已十分普遍。
国内热流道模具也已经生产, 有些企业已达30%左右, 但总的来看, 比例太低, 亟待进展。
随着塑料成型工艺的不断改进与进展, 气辅模具及习惯高压注射成型工艺的模具将随之进展。
模具标准件的应用将日渐广泛, 模具标准化及模具标准件的应用能极大地影响模具制造周期。
使用模具标准件不但能缩短模具制造周期, 而且能提高模具质量与降低模具制造成本。
同时, 快速经济模具的前景十分广阔。
多工位级进铸造模在汽车内板冲压件上的研究与应用论文

多工位级进铸造模在汽车内板冲压件上的研究与应用论文多工位级进铸造模在汽车内板冲压件上的研究与应用论文多工位级进模又称连续模,其模腔中具有两个或两个以上的工位,且这些工位都在一条直线上,在压力机一次行程中,可完成冲裁﹑弯曲﹑拉深﹑成形等多个工序。
具有效率高,生产成本低的特点。
在国内,多工位级进模一般在家电钢板模领域使用比较普遍,但在汽车领域,特别是铸造模领域应用还较少。
本文以某汽车门槛加强板为实例,将左右件合模并用级进模生产,从工序排布到模具设计、调试及实现给予简析,供有关人员参考。
一、产品工艺分析产品材质为 B 2 5 0 P 1 ,厚 1 . 4 m m ,零件尺寸为320mm×137mm×92mm,零件形面与孔均不左右对称(见图1)。
该件如用单冲工艺,工艺路线为OP10落料→冲孔→OP20成形→OP30翻边→OP40冲孔侧冲孔,共需开发7套模具。
因单冲生产效率低,不满足产能要求,经评议后采用左右件合模的多工位级进模生产,因模具尺寸较大,模具类型选用铸造模。
二、料带图设计在多工位级进模中,每冲压一次条料就由送料机向前送一个步距,以到达不同工位,每个工位的工作内容都不相同,在完成所有工序前,工序件与料带不分开。
料带图设计就是确定每个工位的加工内容。
料带图设计是多工位级进模设计的关键,也是模具结构设计的依据,料带图一经确定,也就确定了模具的工位数、步距及产品的材料利用率。
在设计料带图时,需注意如下事项:①压力机中心与模具中心需基本一致,保证受力平衡,如无法保证一致,偏心不得超过100mm,可适当设置空工位,以备后期产品设计变化或避让干涉及保证受力平衡。
②为使料带定位可靠,一般可在第一工位冲压一些工艺孔作为后工位定位孔,孔离形面较近时,可先冲小孔定位,后面冲到需要尺寸的大孔,或先成形后冲孔。
③废料及成品件应能顺畅排落,送料需要顺畅。
④既有成形又有弯曲的工件,先成形后弯曲,以免因材料流动影响已定形形面。
- 1、下载文档前请自行甄别文档内容的完整性,平台不提供额外的编辑、内容补充、找答案等附加服务。
- 2、"仅部分预览"的文档,不可在线预览部分如存在完整性等问题,可反馈申请退款(可完整预览的文档不适用该条件!)。
- 3、如文档侵犯您的权益,请联系客服反馈,我们会尽快为您处理(人工客服工作时间:9:00-18:30)。
20
5模具工业62002.No.10总260
模内铆接在级进模上的应用
马浩军,赵喜广,赵震,阮雪榆
(上海交通大学,上海200030)
摘要:为提高冲压生产效率,可将在冲压模具外的二次加工工序引入到模具中。现以电机托架组件模设
计为例,介绍了模内铆接技术在级进模上的应用。
关键词:级进模;铆接;排样
中图分类号:TG385.2文献标识码:B文章编号:1001-2168(2002)10-0020-03
TheApplicationoftheInsideRivetJointtoProgressiveDies
MAHao-jun,ZHAOXi-guang,ZHAOZhen,RUANXue-yu
(ShanghaiCommunicationUniversity,Shanghai200030,China)
Abstract:Inordertoimprovethestampingproductionefficiency,asecondprocessingprocedure
outofthestampingdiecouldbeputintotheprogressivedie.Withthedesignofthedieforthe
motorbracketpartsasanexample,theapplicationofthetechnologyofrivetjointinginsidethe
progressivediewasintroduced.
Keywords:progressivedie;rivetjoint;layout
))))))))))))))))))))))
作者简介:马浩军(1970-),男,工程师,硕士,在读博士研究生,
主要研究方向:模具CAD/CAM/CAE,地址:上海交通大学模具
CAD国家工程研究中心。电话:(021)32260288-8008
收稿日期:2002-03-27
1引言随着冲压件批量的增大,对模具冲压生产效率的要求越来越高。随着模具和冲压技术的不断发展,多工位级进模的应用越来越广泛,同时模具的集成度也越来越高,许多原来在冲压模具外进行的二次加工工序也逐渐引入到模具中,如模内攻螺纹、模内铆接等。本文结合生产实例,对多工位级进模模内铆接技术的应用作一介绍。2模内铆接的可行性分析图1为某打印机上走纸电机的托架,该组件由托架母体和转轴两部分组成,母体材料为1.2mm镀锌钢板,转轴尺寸见图2。因该零件生产批量较大,主要考虑了两种工艺方案:(1)采用级进模冲压托架母体,转轴在冲压模具外的夹具上进行铆接。(2)将铆接工序加在模具上,直接将组件冲压而成。基于对组件成本和生产效率的比较,倾向于选择方案2。对于方案2,级进冲压没有大的问题,主要矛盾是冲压过程中转轴的送进和与冲床行程的同步。通过对一些自动装配机和自动攻丝机的研究,
认为采用振动盘来进行排序和送进,再配合以模具
内的滑块送进机构可以很好地解决以上矛盾,因而
认为模内铆接是可行的。
图1电机托架组件
1.托架母体2.转轴
图2转轴尺寸图
3排样设计
通过对零件冲压工艺性分析,设计了如图3所
21
5模具工业62002.No.10总260
图3模具结构简图
1.振动盘2.振动托板3.转轴滑道4.振动器5.光电传感器6.滑块及压铆机构
图2排样图
示排样图。排样图中工位1~9主要是完成冲孔、导正和坯料轮廓冲裁;工位10~13主要完成成形、弯曲、边倒角、校平面度等;工位14冲孔;工位15倒角;工位16、17是预留的模内攻螺纹工位;工位18将转轴送进并将尾部胀开,使其能留在零件上随着条料向前送进;工位19为空位;工位20将转轴铆紧在托架母体上,并将零件切落。4模具结构电机托架组件级进模结构简图见图3,该模具采用4组滚动导向的主导柱,因模具尺寸较大,在模具长度方向上将模板分为4组,每组模板之间的相对位置靠模座上的定位销来保证,每组模板的内
部都有4个滑动导柱。模内铆接的工作部分主要由
振动托板2、振动盘1、转轴滑道3、振动器4、光电传
感器5、滑块机构及压铆机构6等组成,模具上还有
其他一些防误送及碰撞等安全装置。光电传感器主
要用来检测转轴漏铆而造成大批废品。
模具工作时,转轴通过振动盘振动排序后进入
滑道,在滑道上靠振动器的振动向前送进。模具铆
接机构如图4所示,随着上模的下行,首先压动斜楔
7,斜楔7推动滑块6前行,滑块6推动转轴8进入
转轴举升块2;随着上模的进一步下行,斜楔9推动
滑块1前行,推动举升块上行,将转轴举升到工作部
位;上模继续下行,铆接凸模将转轴尾部胀开,使其
22
5模具工业62002.No.10总260
图4模内铆接机构示意图
1、6.滑块2.举升块3.复位螺塞4.防退杆5.滑道7、9.斜楔8.转轴
留在托架母体上,随着载体前行至一定工位,靠凸模压力铆接牢固。复位螺塞3和防退杆4起防止工作时转轴倒退的作用。5结束语托架组件控制的重点是保证基准面即托架母体大平面的平面度为0.1mm,转轴相对于基准面的
垂直度为0.05mm。因设计初期考虑比较周到,经过
几次试模后,组件达到图纸要求,模内铆接机构工作
顺利。该组件月需求量为几十万件,模具冲次可超过
50次/min,达到了预期设计要求,对提高生产率有
很大的帮助。
切角切边压半包双工位模具设计
梁春玲1,胡晓东
2
(1.上海大学嘉定通用机械厂,上海200072;2.上海大学热处理厂,上海200072)
摘要:介绍了某车型第2、第3片主钢板弹簧切角压半包、切边压半包双工位模具的设计要点及注意事
项。该模具使用后,提高了钢板弹簧的生产效率,降低了生产成本,并推广应用于其他车型钢板弹簧的
生产中。
关键词:双工位;模具;设计
中图分类号:TQ385.2文献标识码:B文章编号:1001-2168(2002)10-0022-03
DesignoftheTwo_PositionDieforTrimming/Cutting_Off
andArcShapePressin
g
LIANGChun-ling1,HUXiao-don
g
2
(1.JiadingGeneralMachineryFactoryofShanghaiUniversity,Shanghai200072,China;
2.HeatTreatmentFactoryofShanghaiUniversity,Shanghai200072,China)
Abstract:Themaindesignpointsandattentionpointsfordesigningthetwo_positiondieforcut-
ting_off(ortrimming)andarcshapepressingforformingthe2ndand3rdmainsteelspringsofa
typeofautomobilewereintroduced.Withthedie,theproductionefficiencyofthesteelsprings