汽车铝合金控制臂的模锻成形
汽车铝合金板件成形工艺及模具结构设计
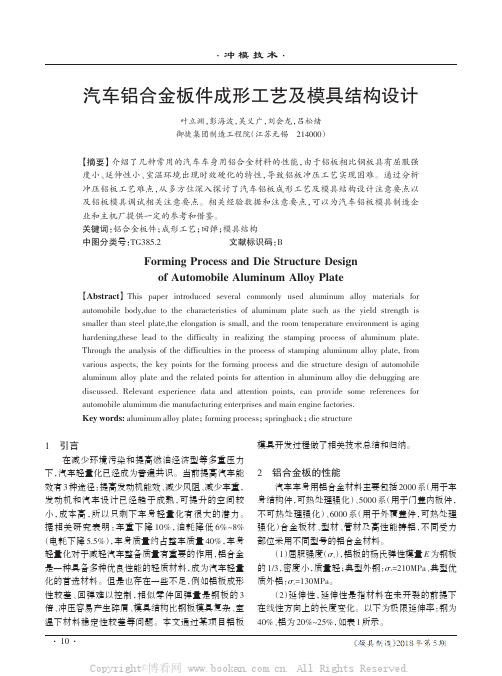
(4)由于铝板密度小,上模容易吸料,冲孔也容易
带料,废料滑出比钢板困难。结构设计时需要注意:
它没有用,铝板自动化生产中,需要在线首设置吹气
①在上模非成形部位加弹顶销,在让空部位及上下模
式分张装置,采用不间断吹气模式,吹气压力至少
周边工艺补充面上加足够多的排气孔,选用顶料型冲
起皱严重致不能压到下死点,解决相关问题后再压
件;成形性调试完成后制件外观应无明显起皱与较大
开裂;④调试完成后,做好相应记录,将调整参数反馈
给相关技术人员。
边间隙(7%~8%)t,铝板修边间隙(5%~7%)t;刀块拼
(4)型面研合:①模具倒装,以成形性调试所得样
缝间隙,钢板模具刀块拼缝间隙+0.04~0.1mm、铝板模
大补偿 5mm
图 1 CAE 数据补偿
图 5 修边碎屑多
图 2 数据补偿后仍回弹
(2)容易开裂:延伸率比钢板小,钢为 40%,铝为
20%~25%,故变形量比钢板小,极易开裂,如图 3、图 4
图 6 翻边有碎屑
《模具制造》2018 年第 5 期
Copyright©博看网 . All Rights Reserved.
系列(6022)的铝合金板材为例:新置材料的屈服强度
为 113.6MPa,存放 3 个月后的屈服强度为 126.5MPa,
所示,成形圆角和拔模角度相比钢板类零件有更高的
要求。
存放 6 个月后的屈服强度为 154.5MPa,如表 2 所示。
如果存放时间超过 6 个月,
将过硬以至于成形困难。
表1
钢板
极限延
加工时方便加垫片;②整形模具设计时要考虑后期整
形镶块后面与底面加垫片的操作可行性。
高强度异形臂一次模锻成型技术探析

针 对 锻 件 特 点 ,结 合工 厂 实 际 情 况 ,确 定 了 辊 锻 机 制 坯 、 摩擦压力机模锻的锻造工艺,其流程为:下料→ 中频感应加 热 → 辊 锻 制 坯 → 弯 曲 → 锻 造 → 切 边 → 校 正(弯 曲)。15 种 异 形 臂制作共用一副模锻通用模具,如图2所示。15种异形臂模锻 压时分别只需通过调整通用模具上模(图3)的件2及件3来调 整 异 形 臂 尺 寸 ,在 模 锻 工 序 中 不 需 要 大 量 模 具 ,也 不 需 要 大
3 高强度异形臂一次模锻成型技术方案论述
3.1 项目产品生产工艺流程 异形臂生产工艺流程:锻坯料→ 铣坯料平面→数控气割
外形 (按不同种类异形臂)→模锻工艺设计→模具设计→模 具加工及各种辅助装置的设计,加工坯料→ 加热→ 模锻(通 用模具,15种异形臂共用一副模具)→ 热处理→ 机械加工→ 探伤检验及其他各项理化检测→渗氮处理→检测→入库。
采用一次模锻成型技术的异形臂抗拉强度≥980 MPa, 屈服强度≥650 MPa,抗压能力强,产品不易变形,提高了汽
图2 通用模具 3.2.2 模
汽车零部件超塑性成形

超塑性是指在特定的条件下,即在低的应变速率,一定的变形温度(约 为热力学熔化温度的一半)和稳定而细小的晶粒度(0.5~5μ m)的条件下, 某些金属或合金呈现低强度和大伸长率的一种特性。其伸长率可超过100% 以上,如钢的伸长率超过500%,纯钛超过300%,铝锌合金超过1000%。 目前常用的超塑性成形的材料主要有铝合金、镁合金、低碳钢、不锈 钢及高温合金等。
试验温度: 从400℃开始,每25℃为一个梯度,到550℃ 止。
温度对5083铝合金真应力-真应变的影响
温度对5083铝合金延伸率的影响
试验结果表明: 未经细晶处理的铝合金5083板材,也具有非 常好的超塑性,在 和 应变速率下, 其延伸率最大可超过450%,最小也超过200%, 即使在较高应变速率( )条件下,在试验 温度范围内,其延伸率也超过200%,只有温度 在550℃的情况下,延伸率才低于200%,但达到 了180%。
图1-1
吹塑成形的5083铝合金墙面装饰浮雕
2 超塑性的分类
1.微晶组织超塑性(即恒温超塑性或结构超塑性)
其产生的第一个条件是材料具有均匀的微细等轴晶粒,晶粒尺寸通常小于 10μ m,并且在超塑性温度下晶粒不易长大,即所谓热稳定性好;第二个条件是变 形温度T>0.5Tm,并且在变形时保持恒定温度;第三个条件是应变速率比较低,一 般=10-4~10-1/s。目前已发现共晶型和共析型合金具有超塑性,但也不限于此,而 在许多的二相合金中相当一部分呈现超塑性。一般说来,晶粒越细越有利于超塑性 变形,但对有些材料来说,例如钛合金,其晶粒尺寸达几十微米时仍有良好的超塑 性能。
2.相变超塑性(即变温超塑性或动态超塑性) 材料在变动频繁的温度环境下,受到应力作用时经多次循环相变或同素异形转 变而得到的超塑性。
汽车用铝合金副车架成形工艺及应用现状
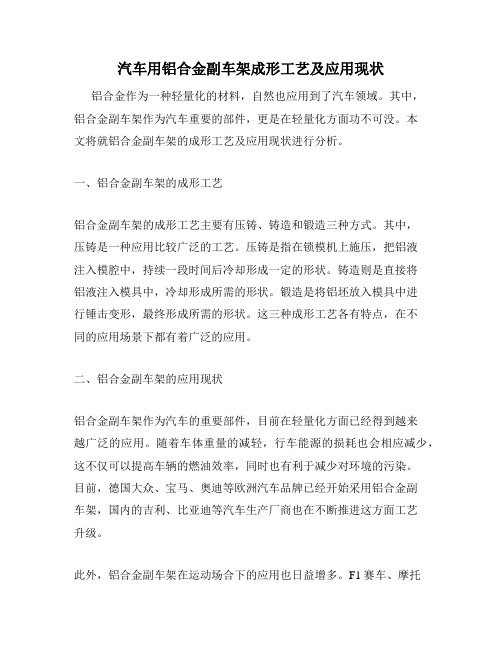
汽车用铝合金副车架成形工艺及应用现状铝合金作为一种轻量化的材料,自然也应用到了汽车领域。
其中,
铝合金副车架作为汽车重要的部件,更是在轻量化方面功不可没。
本
文将就铝合金副车架的成形工艺及应用现状进行分析。
一、铝合金副车架的成形工艺
铝合金副车架的成形工艺主要有压铸、铸造和锻造三种方式。
其中,
压铸是一种应用比较广泛的工艺。
压铸是指在锁模机上施压,把铝液
注入模腔中,持续一段时间后冷却形成一定的形状。
铸造则是直接将
铝液注入模具中,冷却形成所需的形状。
锻造是将铝坯放入模具中进
行锤击变形,最终形成所需的形状。
这三种成形工艺各有特点,在不
同的应用场景下都有着广泛的应用。
二、铝合金副车架的应用现状
铝合金副车架作为汽车的重要部件,目前在轻量化方面已经得到越来
越广泛的应用。
随着车体重量的减轻,行车能源的损耗也会相应减少,这不仅可以提高车辆的燃油效率,同时也有利于减少对环境的污染。
目前,德国大众、宝马、奥迪等欧洲汽车品牌已经开始采用铝合金副
车架,国内的吉利、比亚迪等汽车生产厂商也在不断推进这方面工艺
升级。
此外,铝合金副车架在运动场合下的应用也日益增多。
F1赛车、摩托
车等运动车辆都采用铝合金副车架,这有利于提高运动车辆的速度和灵活性,同时也更加安全。
对于普通消费者而言,铝合金副车架的应用也将使车辆更加安全可靠。
总的来说,铝合金副车架作为汽车轻量化的关键部件,在未来的发展中将越来越广泛地受到重视和应用。
铝合金副车架的成形技术也将不断地进步和完善,更好地满足人们对轻量化汽车的需求。
汽车用铝合金副车架成形工艺及应用现状
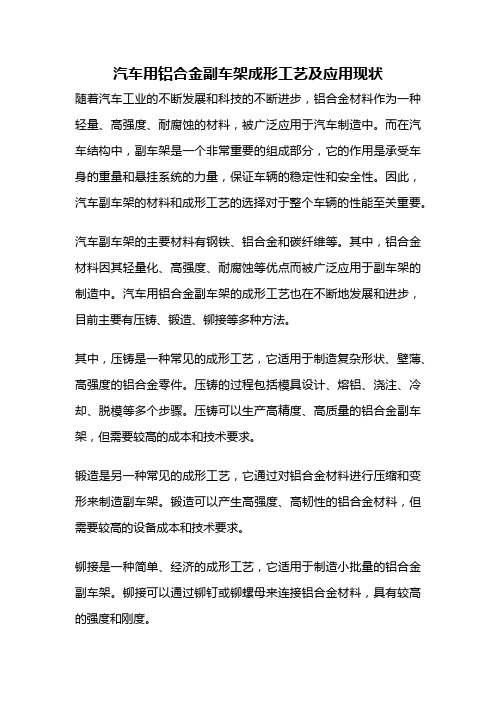
汽车用铝合金副车架成形工艺及应用现状随着汽车工业的不断发展和科技的不断进步,铝合金材料作为一种轻量、高强度、耐腐蚀的材料,被广泛应用于汽车制造中。
而在汽车结构中,副车架是一个非常重要的组成部分,它的作用是承受车身的重量和悬挂系统的力量,保证车辆的稳定性和安全性。
因此,汽车副车架的材料和成形工艺的选择对于整个车辆的性能至关重要。
汽车副车架的主要材料有钢铁、铝合金和碳纤维等。
其中,铝合金材料因其轻量化、高强度、耐腐蚀等优点而被广泛应用于副车架的制造中。
汽车用铝合金副车架的成形工艺也在不断地发展和进步,目前主要有压铸、锻造、铆接等多种方法。
其中,压铸是一种常见的成形工艺,它适用于制造复杂形状、壁薄、高强度的铝合金零件。
压铸的过程包括模具设计、熔铝、浇注、冷却、脱模等多个步骤。
压铸可以生产高精度、高质量的铝合金副车架,但需要较高的成本和技术要求。
锻造是另一种常见的成形工艺,它通过对铝合金材料进行压缩和变形来制造副车架。
锻造可以产生高强度、高韧性的铝合金材料,但需要较高的设备成本和技术要求。
铆接是一种简单、经济的成形工艺,它适用于制造小批量的铝合金副车架。
铆接可以通过铆钉或铆螺母来连接铝合金材料,具有较高的强度和刚度。
国内外的汽车厂商都在研发和应用铝合金副车架。
以国内为例,一汽大众、上汽通用、上汽大众等公司都已经开始在自主生产的车型中应用铝合金副车架。
而国外的汽车厂商如奥迪、宝马、奔驰等也都在不断地研发和应用铝合金副车架。
汽车副车架的材料和成形工艺的选择,不仅影响到汽车的性能和安全性,也对环保和节能产生了积极的影响。
铝合金副车架的轻量化和高韧性,可以大大降低车辆的燃油消耗和废气排放,符合现代汽车工业的发展趋势和环保要求。
因此,铝合金副车架将成为未来汽车制造的重要发展方向。
汽车用铝合金副车架的成形工艺和应用已经取得了显著的进展和成果。
随着科技的不断进步和工艺的不断优化,铝合金副车架将会在未来的汽车制造中发挥越来越重要的作用。
汽车用6016铝合金板材预时效工艺研究及冲压成形数值模拟

摘要6016铝合金板材主要制造汽车覆盖件,特别是乘用车内外罩、后行李箱和门框等汽车外板,是汽车轻量化的关键材料。
而目前国内的铝合金板材仍存在着成形性、抗凹性及零件成形后质量差等问题,无法满足使用要求。
因此开展6016铝合金板材关键的预时效工艺和冲压成形工艺研究,对提高板材的成形质量十分重要。
本文将545 o C固溶30 min的6016铝合金(Al-0.55%Mg-1.0%Si-0.18%Cu)板材水淬后,经60 o C~160 o C×5 min~30 min预时效,室温停放25天后,进行185 o C×20 min的模拟烤漆处理。
采用硬度、拉伸试验,结合示差扫描量热法(DSC)、扫描电子显微镜(SEM)等分析技术,研究预时效工艺对合金的力学性能及微观组织的影响规律。
通过数值模拟仿真实际的冲压过程,并预估零件成形后可能出现的质量缺陷,优化关键成形工艺参数。
结果表明:①固溶淬火后立即进行预时效可以抑制自然时效过程,T4P态合金的成形性和烘烤硬化性能都得到改善。
烤漆前后的硬度随着预时效温度升高,出现先缓慢增加后迅速增加的趋势。
预时效温度为100 o C,预时效时间为20 min合金烘烤前屈服强度低于120 MPa,延伸率在25%左右;烘烤后屈服强度高于180 MPa(预变形2%合金烘烤硬化值达到104 MPa),烘烤后的延伸率在22%左右,综合比较优于其他预时效工艺。
②结合DSC曲线对β”析出温度和激活能进行计算,研究发现,随预时效温度升高,β”析出峰左移,激活能也降低。
说明预时效可以抑制合金自然时效过程,提高合金T4P态成形性能,而且促进烘烤过程中β”的析出,增强烘烤硬化效果。
③以铝制汽车发动机罩内板为对象,建立冲压CAE模型,对板料冲压过程仿真,研究了不同成形工艺对成形后最大减薄率、最大增厚率及最大回弹量的影响规律。
④对多因素的优化问题,首先通过灰色关联分析法,获得较优的工艺参数为:压边力500 KN,摩擦系数0.1,凹凸模间隙1.1t(1.32 mm)、凸模速度3 m/s,仿真试验后出现了少量拉裂缺陷。
汽车用铝合金副车架成形工艺及运用
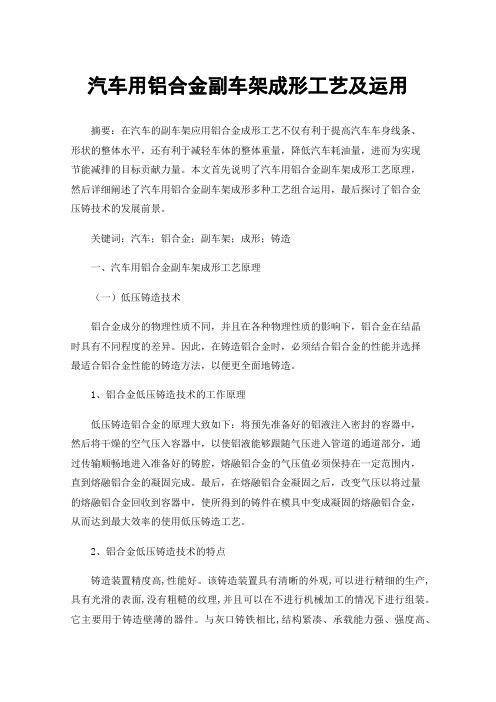
汽车用铝合金副车架成形工艺及运用摘要:在汽车的副车架应用铝合金成形工艺不仅有利于提高汽车车身线条、形状的整体水平,还有利于减轻车体的整体重量,降低汽车耗油量,进而为实现节能减排的目标贡献力量。
本文首先说明了汽车用铝合金副车架成形工艺原理,然后详细阐述了汽车用铝合金副车架成形多种工艺组合运用,最后探讨了铝合金压铸技术的发展前景。
关键词:汽车;铝合金;副车架;成形;铸造一、汽车用铝合金副车架成形工艺原理(一)低压铸造技术铝合金成分的物理性质不同,并且在各种物理性质的影响下,铝合金在结晶时具有不同程度的差异。
因此,在铸造铝合金时,必须结合铝合金的性能并选择最适合铝合金性能的铸造方法,以便更全面地铸造。
1、铝合金低压铸造技术的工作原理低压铸造铝合金的原理大致如下:将预先准备好的铝液注入密封的容器中,然后将干燥的空气压入容器中,以使铝液能够跟随气压进入管道的通道部分,通过传输顺畅地进入准备好的铸腔,熔融铝合金的气压值必须保持在一定范围内,直到熔融铝合金的凝固完成。
最后,在熔融铝合金凝固之后,改变气压以将过量的熔融铝合金回收到容器中,使所得到的铸件在模具中变成凝固的熔融铝合金,从而达到最大效率的使用低压铸造工艺。
2、铝合金低压铸造技术的特点铸造装置精度高,性能好。
该铸造装置具有清晰的外观,可以进行精细的生产,具有光滑的表面,没有粗糙的纹理,并且可以在不进行机械加工的情况下进行组装。
它主要用于铸造壁薄的器件。
与灰口铸铁相比,结构紧凑、承载能力强、强度高、导热系数高、使用寿命长。
可以使用特殊的铸造方法来优化组装过程并简化制造过程,例如镶铸法,可以使用钢、铸铁、铜等材料制作铸件。
(二)液压成形工艺众所周知,液压成形工艺并非最初就使用于汽车领域,而是随着汽车的蓬勃发展加之汽车零部件结构复杂多变,这才将其应用于汽车行业。
据了解,航空航天领域是液压成形工艺最早使用的领域,通过借助其重量轻、刚度高、精度高等优势,为形状复杂的薄壁件提供路径,使得在具体生产过程中可减少零部件种类、焊缝长度、机械加工工序等内容,有效地降低了部件生产成本,缩短了加工工序的周期,进而为工作人员的加工工作降低了难度,提高了其工作效率。
铝合金热成型

铝合金热成型是一种利用高温和压力将铝合金板材或薄壁管材加工成所需形状的工艺。
该工艺具有高效、精确、可重复性好等优点,广泛应用于航空航天、汽车制造、建筑等领域。
铝合金热成型的过程通常包括以下几个步骤:首先,将铝合金材料加热至一定温度,使其变得柔软易变形;然后,将加热后的铝合金放置在模具中,施加一定的压力,使其按照模具的形状进行变形;最后,冷却后取出成型件并进行后续处理。
铝合金热成型的优点在于其可以制造出复杂形状的零件,而且成型件具有较高的强度和刚性。
此外,由于铝合金材料的密度较低,因此热成型后的零件重量较轻,有利于降低整个产品的重量和能耗。
然而,铝合金热成型也存在一些挑战和限制。
例如,由于铝合金材料的熔点较高,因此需要使用特殊的加热设备和技术来确保材料能够均匀地加热到所需的温度。
此外,由于铝合金材料的热传导性能较差,因此在成型过程中需要控制好温度和压力等因素,以避免产生缺陷和变形等问题。
综上所述,铝合金热成型是一种重要的金属加工工艺,具有广泛的应用前景。
随着技术的不断进步和发展,相信这种工艺将会在未来得到更广泛的应用和发展。
- 1、下载文档前请自行甄别文档内容的完整性,平台不提供额外的编辑、内容补充、找答案等附加服务。
- 2、"仅部分预览"的文档,不可在线预览部分如存在完整性等问题,可反馈申请退款(可完整预览的文档不适用该条件!)。
- 3、如文档侵犯您的权益,请联系客服反馈,我们会尽快为您处理(人工客服工作时间:9:00-18:30)。
积 ,如 图3 中的 曲线所示 。
10 6 0 10 4 0 兰 10 2 0
J
、
l
制 臂是 汽车转向系统 中的关键部件 ,其 要求性能稳定 、
强度高 。为提高生产的稳定和 高效性 ,采用辊锻制坯工 艺替 代传统的 自由锻制坯工艺 ,可减 少 自由锻制坯的随
10 0 0
2 辊锻工 艺的确定 .
( )控制 臂截面 面积 的计算 1 采用 三维造 型软 件
中段 最小 截 面 面积 F… =3 0 7 mm ,原 始截 面 面
积 =31 2 mm 0 . 4× 0 X2 mm=15 mm 26 , 。 1 。代 取 . 5
造 型 ( 图2 见 )后 ,用 平 面剖 切 截面 面 积 , 自动计 算 各个截面 ,导入 ̄ E j I XCE 软件 中作 出锻 件各个 截面面 L
4 实际生产 与模拟 的对比 .
根据数 值模拟情 况Βιβλιοθήκη ,进行辊 锻和模锻 模具 的设计 与
制 造。 图1 和 图l分 别为制坯模 拟成形与 实际生产成形 0 1
图7 辊锻第3 道次温 度分布
的结 果 对 比 。
参磊
热工 加
垫 型 堕 堕 et!rki 950.l 丝 堡 笪 . al 主ng塑■o1 !童 1 c m ‘ www m wo
4 mm,长 为 15 m。 0 6r a
()辊 锻道次 和坯料 的确定 由于 中 间段截 面面 3
积变化最大 ,辊锻道次数按 中间段 来计 算 ,公式 如下 :
月=1 / 。 g l g
式中
图 l 上控制 臂毛坯
——总延伸 系数 ,
。 — —
= o ; F
为平均延伸 系数 ,取 。 . .。 =1 4~1 6
5 辊锻第 l 次温度分布 道
中坯料温度 的分 布状态 。
一篓
6 辊 锻第2 道次 温度分布
图9 模锻温度分 布
由模 拟得 出的模锻成形温 度分布可知 ,模锻后坯料
温 度在本体 温度 由分 布均匀 。在终锻温 度范 围内,杆 部 飞边桥及飞边仓部位 的温 度较高 ,但在过烧温 度之 下。
图2 锻件三维造 型
所示 。
■ 一 丝! 塑 垫竺 堡生笪生 ! 童
www m e a w r ig 1 5 . o t l o kn 9 0 c r n
磊
热工 加
汽车零部件翻造技术专题
RPhAl 壅 壁 er& pn I 皇 里 sc pc ! i 砌
由模拟得 出的温度 分布可知 ,辊 锻过程 中变形程度
入上式 中 ,计算结果 为 :n 3叭 。因此 中段辊锻次数 定 =. 为3 道次 。同样计算左段 的辊锻次 数为1 道次 。 ( )辊锻坯 件形状 的确定 4 根 据截面 图及上述 道
次 的计 算 ,将 中段的辊 锻 截面形 状 变化 定为 :圆 一椭 圆一方形 一菱形 ;左端的辊锻截面形状变化定为 :圆一 圆 ( 变 )一椭 圆一椭 圆 。最终 确定辊锻 坯形状如 图4 不
1 控制臂的结构及工艺分析 .
图1 所示为转 向系统 中的一上 控制 臂设计 图样 ,其 属于连 接杆状控 制臂 ,中间杆郜截面 为T 字形 ,呈高肋 状 ,此部位 截面面积最小 。左端为 扁平 形 ,右端 成 圆柱
长度 L m , m
图3 控制臂截面 面积 分布
( )原始坯料 尺寸 的确定 2
4 . 0 1
16 8
G 4 I 2
卞J
— —
一
G\ I
大 的 中间段温 度较高 ,辊 锻第 1 、3 、2 道次 的温度 变化
在成形温 度范 围内 ,即坯料 在此范 围有 较高 的塑性 ,利 于成形 。
J I
( )模锻 成形 模拟 2
该控 制 臂锻件 模锻 成形 的设
根据 控制臂锻 件截面
形 ,此部位 截面 面积最大 。此锻件采用辊锻 制坯 工艺 ,
具体生 产工艺流 程为 :圆棒下料 一清洗 一感应加 热一辊 锻制坯 一模锻成形 一切边 一固溶热处理 一时效强化 。
面积的分布情况 ,将辊锻 坯件分为3 段,如图3 中的折线 所示 。左端截面面 积居中 ,中部为斜线 ,截面最小 ,右 端 截 面面 积最 大 ( 留为 机械手 夹持 位 )。根据 计算 所 得的 右端 截面 面积 及体 积 ,选 取原 始棒 料坯料 直径 为
恒
80 ^ 0
. 1
I
| I t
| l t
要 o 6 o
颦 40 0
J \
l
5 0 l0 O l0 5 2 0 0 20 5 3 0 0
意性和 高劳动强度 ,同时可大幅提高生 产效率。
f 2 0 0
0
1 I
\
3O 5
备采用双盘螺旋 摩擦压 力机 ,模 锻成形模具 的3 D造型如
图8 示 。 所
图4 最终辊 锻坯
3 辊 锻成形及模锻成形数值模拟 分析 .
( )辊 锻 成 形 模拟 1 按 实 际 设 备情 况 ,辊锻 采 用 1 5 辊锻 机 。采 用 三维 软 件建 立 辊 锻成 形 模具 的 2型 3 型 。用有 限元软 件进 行数值 模拟 分析 ,坯料 选用 D造
墨 壁 鼢 & nn 兰 …h铆 娃 o
汽 车 铝 合 金 控 制臂 的 模 锻 成 形
芜湖禾 田汽车工 业有限公司技术 中心 ( 安徽芜湖 2 10 ) 包其华 4 10 潘 琦俊 吴 生绪 程 俊
随 着 汽 车 工 业 的 发 展 ,汽 车 已逐 步 成 为主 要 的 代步 工具 。汽车 轻 量化 的要求 日益 提 高 ,以 “ ” 代 铝 “ 铁”的结构件在汽车零部件 上的应用越来越广泛 。控
Al Sl Mg i材料模 型 ,模具视为 刚性 。采 用粘塑性有 限元
分析 ,定义坯料温度 和模具温度 。由于 铝合金锻造对温
度有较高的要求 ,因此对 成形过程 的温 度进 行分析 。模
拟 过程 中坯料温度分布状 态见 图5 、图6 、图7 。
() b
图8 模锻成形 模具
同样对 模锻 成形 进行 成形温 度 的分析 ,图9 是模 拟