金刚石镀镍
金刚石CBN磨头适合打磨哪些材质工件

金刚石CBN适合打磨哪些材质工件
文/GRINDMAX.格林美斯
金刚石——这里所说的金刚石是石墨在高温、高压下形成人造金刚石,由纯碳组成,如工业中的切割打磨工具等。
立方氮化硼——Cubic Boron Nitride立方氮化硼,缩写为:CBN,是人工合成的一种超硬材料,由氮和硼组成。
其硬度仅次于金刚石,它不但具有金刚石的许多优良特性,而且有更高的热稳定性和对铁族金属及其合金的化学惰性。
其电镀的打磨精修工具主要用在精密磨削、研磨、抛光和超精加工等以达到高精度的表面加工效果。
硬度:
金刚石材料硬度比CBN材料硬度高一半。
由于具备较高的硬度,金刚石十分适用于加工以下材料:
-所有的硬质合金
-金属陶瓷、氧化/非氧化物陶瓷
-硬度高的合金
-石墨、铁素体
-玻璃及非金属材料
-蓝宝石及珍贵石材
-增强纤维合成物
*由于金刚石由纯碳组成,所以不适用于加工钢材,因其在研磨中产生的高温会使钢中的碳
和金刚石反应,从而腐蚀金刚石颗粒。
(立方氮化硼)CBN由硼、氮两元素组成,和金刚石相比,CBN没有碳原子,很适合加工钢。
-硬度在54HRC以上的钢
-高速钢(HSS)
-钨铬钴合金
-表面镀镍合金
其硬度在高温状态下保持较强的稳定性,而金刚石则在温度超过700度时,其硬度大大降低。
以下是部分金刚石CBN工具的实物展示:。
电镀金刚砂工艺毕业设计

1.前言1.1 课题的提出如今随着科学技术的飞速发展,单一的金属材料不足以满足某些特殊需求,而复合材料的兴起可以满足许多特殊的性能及功能,在现代科学技术中发挥着重要的作用;复合镀层是国内外近十几年来高速发展起来的材料科学的新兴材料;复合电镀是提高金属材料表面机械性能的重要方法之一1,复合电镀就是把一种或多;,越、23尼龙、聚四氟乙烯、氟化石墨和云母微粉等一些有机物质;一般来讲,凡是能电沉积出镀层或能得到化学镀镀层的金属或合金都可以作为形成复合镀层的基质金属;目前较常使用的基质金属有:铜、镍、铬、铁、锌、锡、金、银等;复合电镀最大的优点是可以通过选用具有不同性质的一种或多种微粒,通过电沉积而形成具有各种所需性能的复合镀层,这些不溶性的微粉均匀地弥散在镀层中,赋予镀层以各种功能1.2 课题研究的意义由于复合镀层由基质金属盒分散微粒两相组成,因此复合镀层兼具各组成的优点;以镍为基质金属,以金刚石微粒为分散相,通过电沉积得到的复合镀层具有高的硬度和良好的耐磨性,广泛的用在刀具,磨具中;在镍-金刚石复合镀中,由于金刚石微粒具有特有的表面性能和磁性,在电沉积过程中极易发生粒子团聚和沉降现象,不仅影响其在镀层中的均匀分布和粒子、3、金刚石微粉等;基质金属有镍、铜、钴、铬和一些合金等; SiC、WC、TiC、SiN2这一类复合镀层不仅具有良好的耐磨性,同时也具有良好的抗高温能力,所以也有人称之为“金属陶瓷复合镀层”;比如,镍基复合镀层的耐磨性比钝镍镀层高70%,因此可以用于汽车或飞机发动机的汽缸壁、汽缸喷嘴或活塞环上;在这方面,武汉材保所、南京航空学院、啥尔滨工大、天津大学、武汉一个部队的工厂等许多单位做了大量工作;为了比较镍-碳化硅复合镀层和镀铬层的耐磨性能,国外有人用泰伯磨损试验机进行试验,所得结果表明:这种复合镀层的磨损量仅为铬层的1/2.因此,早在1966年就在西德成功利用与转子发动机缸体型面上,以及部分冲压模具上;金刚石硬度极高,它与镍等基质金属组成的复合镀层,可用于工具,模具的精加工,宝石加工,牙科医疗器械等;例如:武汉材料研究保护所在七十年代末开展了镍-钴合金与金刚石复合电镀工艺的研究并用于轴窝磨头上,八十年代初期,天津大学,武汉部队712厂研制的镍一金刚石复合镀层曾用于切,磨削工具及滚轴上;武汉地质学院研究的镍一结果表明:镍基聚四氟乙烯复合镀层的磨损量为双镍+铬镀层的1/3-1/8 氟化石墨复合镀层,即使是在高温、高压、高速的摩擦状态下,仍能保持良好的减摩性能;它的摩擦系数并不随温度的变化而显著改变;这一类的复合镀层可用于无法添加液体润滑油的特殊条件下的摩擦件上,如高空、高真空条件下卫星、航天飞机,或是高温条件下等;随着表面镀层摩擦剥落,固体润滑剂能自动补加进去起到润滑作用,因此这一类镀层叫“自润滑减摩复合镀层;武汉材保所和天津大学在这方面都做了很多的工作;国外从七十年代开始,就研究了氟化石墨与金属镍、铜、铅的共沉积以及这类复合镀层的摩擦磨损性能;这类复合镀层有很好的抗擦伤性能,可用于汽缸型面、发动机内壁、活塞环、活塞杆,轴承以及其他机器的滑动部件上;日本还在水平连铸机结晶器内壁上电镀镍-氟化石墨复合镀层以提高结晶器的使用寿命;电镀这种复合镀层的结晶器的拉坯阻力比电镀铬层下降1/4.武汉材保3所在七十年代末、八十年代初开始研究镍基氟化石墨及铜基氟化-该1.3.4 能够形成热扩散合金的复合镀层这种工艺是首先将金属微粉与金属共沉积,得到复合镀层,然后,进行热处理,得到新组成的合金镀层;例如电镀不锈钢时,铬的沉积比较困难,如果把铬粉按一定比例悬浮于Ni-Fe合金镀液中,使Cr与Ni—Fe共沉积,形成复合镀层;然后将复合镀层进行热处理,最后得到不锈钢镀层;天津大学曾对这种镀层进行过研究;使用同样的方法可以得到Cr-W 10%、Cr-Mo5%合金镀层.1.3.5 其他特殊功能的复合镀层这方面的应用也很多,如抗电蚀功能的金基或银基复合镀层;我们知道,金银都是良好的导电材料,常用作电接触元件的表面镀层;但是纯金、纯银镀层耐磨、耐电蚀性差,而且易粘连;现在研制出的Au-WC、Au—Sic、Ag—WC、Ag一石墨、Ag-La2O3、Ag—MoS2等许多复合镀层不仅具有良好的导电性、较低的接触电阻,而且硬度适中,耐磨、减摩性能好,抗电蚀能力强;因此可以用很薄的复合镀层来代替整体的纯银材料而广泛用于低压电器和家用电器产品上;天津大学研制的,2.复合电镀镍-金刚石的工艺评述2.1 复合电镀镍-金刚石的工艺流程镀液配置→镀前处理→电镀→镀后处理→热处理→性能测试2.1.1 各种镀液配方特点pH子水中溶解,然后依次加入到上述溶液中,并不断搅拌;3 将计量的金刚石微粉加入适量去离子水中,搅拌,然后加入适量的分散剂,超声5min后,加入到前面配制的电镀液中,再超声lOmin,去离子水调整镀液至规定体积;复合电镀镍-铁-金刚石镀液组成5镀液成分浓度NiSO4·7H2O 200g/lNiCl 2·6H 2O 60g/lFeSO 4·7H 2O 30g/lNa 3C 6H 6O 7·2H 2O 30g/lH 3BO 3 40g/lC 6H 4COSO 2NH 3g/l791光亮剂 3ml/lC 12H 25SO 4Na 0.2g/l温度 30-65℃PH 3.0-5.5溶液超声频率 40-100KHz2.1.3 镀前处理基体的镀前处理:机械打磨→抛光→化学除油→弱酸活化→电镀金刚石粉的预处理:丙酮浸泡→去离子水洗→稀硝酸浸泡→去离子水洗→稀氢氧化钠浸泡→去离子水冲洗至PH值约为7→浸泡在镀液中待用2.1.4 电镀过程7电镀中用WYJ-3B型晶体管直流双路稳压电源提供电压,串接100mA直流电表:~,,1)结合力测定镀件经400℃保温1 h,水冷处理后,观察镀层是否碎裂,然后用冲击法作破坏性实验,观察金刚石微粒是否脱落;2)金刚石微粒含量测定用称量法测定金刚石微粒含量.镀前在1/10000 g天平上称出经冲洗烘干后基体镀件的重量,镀后再称出镀件的重量,得到镀层和金刚石微粒的重量.用1∶4的硝酸溶液38%的浓硝酸与水的体积比加热溶解镀层,残留金刚石微粒经冲洗、过滤、烘干等处理后,称出量瓶、滤纸、金刚石微粒总重量,按下式计算镀层内金刚石微粒含量;W t = W2-W1/W×100%式中:Wt——镀层内金刚石微粒质量百分比;W——镀层质量;W1——量瓶、滤纸质量;下:d=M2-M1×104/p×A其中 d—镀层的厚度,μm;M1—镀件电沉积前的重量,g;M2—镀件电沉积后的重量,g;P—镀层的平均密度,g/cm3;A—镀件的被镀表面积,cm2;5)镀层显微硬度的测定采用HX-1000型显微硬度计测定镀层的显微硬度,加载载荷为100g,加载时间为15s,物镜放大倍率为40倍,每个试样测量5个不同部位的点,结果取其平均值8;利用仪器所附带的金刚石压头加一定负荷,在被测试样表面压出压痕,通过光学放大测出压痕的对角线长度,经计算或查表求的被测试样表面镀层的硬度;计算公式如下:HV=2sinα/2/d2=1854.4p/d2微D减少;在D= 3A/dm2时,虽然微粒含量最大,但此时镀层表面出现细密麻坑,表面平整性变差,结合力减弱;综合考虑,电流密度为2-2.5A/dm2为宜;2.2.2 温度对微粒含量的影响镀液温度与镀层微粒含量的关系如图.在T=45℃时,镀层微,粒含量在9%左右,低于45℃时虽然微粒含量高,镀层的平整性和结合力变差;当T>45℃时微粒含量随温度的增加而减少;这种现象是热运动与微粒悬浮性能的反应;当温度升高,离子运动加剧,离子的剧烈运动将使阴极对微粒的吸附能力降低,不利于粒子的共沉积;另外,温度升高,镀液粘度下降,悬浮力变差,微粒快速下降到镀槽底部;实验中发现,当T<45℃时,微粒悬浮时间为3-4分钟;T为50-60℃时,微粒悬浮时间为1-2分钟,当温度超过65℃时,悬浮时间为l分钟,75℃时为30秒左右;镀液内悬浮的微粒减少,阴极表面可吸附的微粒少,从而使镀层内微粒含量降低;、也相应的增大,当金刚石浓度达到40g/L时镀层中金刚石的复合质量为57.24%-继续增加镀液中金刚石的浓度,镀层中金刚石的复合量基本保持不变9;这是因为镀液中金刚石颗粒浓度越大,即颗粒的悬浮量越高,在单位时间内通过搅拌被输送到阴极表面的颗粒数量也越多,被沉积在镀层中的几率也越大;在搅拌速度适当的情况下,随着金刚石颗粒在镀液内浓度的增加,复合鍍层中金刚石颗粒的复合量也会相应地增大,直到达到一个极限值;当金刚石颗粒浓度超过50g/L时,一方面由于镀液中颗粒浓度较大,颗粒团聚或相互聚集的倾向增大,颗粒的自沉淀现象严重,实际悬浮的分散颗粒量下降,镀槽底部会有部分颗粒沉淀下来;另一方面,根据有关共沉积理论10,在电镀过程中,均匀悬浮在镀液中的微粒首先被离子吸附,然后通过搅拌作用被传输到阴极表面,在分散双电层的紧密层外侧形成一层密度和覆盖率较高但较为松散的吸附层,此步为弱吸附,可逆过程;随后微粒在强的界面电场力作用下进入紧密层发生电化学强吸附,随着微粒表面吸附的金属离子被还原,该微粒才会被沉积的金属埋入,此步为不可逆过程;若分散微粒浓度越大,在阴极表面产生弱吸附的微粒数越多,但鍍液中的微粒对其冲刷作用也增有,镀处微粒之间的排斥作用小吸附在阴极表面的金刚石微粒多,从而沉积在镀层中金刚石的含量就高;分散剂的量较高时,金刚石表面分散剂吸附量增大,颗粒之间由于排斥作用和空间位阻作用较大,降低了悬浮液的流动性,不利于镍金属和金刚石粒子的共沉积12;分散剂的添加量对镀层显微硬度的影响趋势也与此一致,先升高后降低;当分散剂的添加量为10%时,虽然镀层金刚石的复合量不是最高但镀层的显微硬度最高,这是因为分散剂的量较高,金刚石颗粒在镀层中分散的非常均匀,这种分布状态直接影响到鍍层的显微硬度;分散剂的添加量对镀层厚度的影响不显著,厚度基本保持在16.3μm左右;2.3.3 电流密度的影响随着电流密度的增大,镀层中金刚石含量呈直线下降趋势;这是因为阴极电流密度的提高,意味着基质金属镍沉积速度加快,这时,基质镍金属沉积速度会远大于金刚石颗粒被输送到阴极表面并被嵌入复合镀层中的速度,这样就会导致镀会,,;,度为20rpm时复合镀层中金刚石复合质量和镀层硬度都达到最大值,分别为54.92%和935HV;当继续增大搅拌速度时,沉积在鍍层中的微粒急剧减少14;出现这种规律的原因在于:搅拌速度低,不能使金刚石微粒充分悬浮在鍍液中,镀液中有效利用金刚石颗粒量较少,也不利于金刚石微粒和镍离子传输到阴极表面,反应速率慢,使金刚石微粒的复合量和镍的沉积速率减少;搅拌速度慢慢增大,金刚石颗粒在镀液中悬浮性变好且有利于金刚石的传输,颗粒吸附并沉积在阴极的概率也增大;搅拌速度过大,镀液与微粒都处于剧烈运动之中,微粒和镀液对阴极表面频冲击过大,不仅使微粒在阴极表面难于吸附,而且会把已吸附的微粒冲刷下来重新落入镀液中,不利于镍与金刚石的共沉积,故复合量降低;复合镀层的硬度随金刚石含量的增加而增大,所以镀层的硬度与镀层中金刚石的复合量的变化趋势基本上呈现出一致性;搅拌速度对复合镀层的厚度影响很小,镀层的厚度始终保持在16.5μm左右;2.3.5 镀覆时间的影响,时,℃到达阴极表面的微粒增加,使镀层中金刚石含量增加,在40℃时金刚石的复合质量达到最大值51.82%;当温度大于40℃时,镀层中金刚石复合量随着温度的增加而减少;因为温度继续升高,金属离子运动加剧,使阴极对微粒的吸附能力降低,不利于微粒的共沉积;此外,温度升高,镀液黏度会下降,悬浮力变差,微粒很快沉降到镀槽底部,使得镀层中金刚石的复合量降低15;镀层的显微硬度在45°C时达到最大值1093HV,温度继续增大,镀层的硬度反而降低,因为温度继续升高加快了离子在阴极附近的运动速率,减少了因离子的扩散速度带来的浓差极化,从而使得镍沉积的结晶变粗,又由于金刚石复合量的降低,最终导致复合镀层的显微硬度降低;当温度超过55°C,镀液的挥发严重,影响有效成分在阴极的沉积;温度对镀层的厚度影响不大,但随着温度的升高镀层厚度稍微增加;2.3.7 PH值的影响由于H+或0H—离子能够改变微粒的电荷性质,并且阴极析出的氢气影响微pH从;镀液pH值对复合镀层的厚度影响不大,但pH值过高时,由于溶液中产生了不溶性的氢氧化镍沉淀,导致主盐浓度降低,因此,镀层厚度有所降低;2.3.8 溶液超声频率的影响溶液超声处理是在复合电镀前对电镀溶液施加超声波,超声波对金刚石颗粒表面的活化,可以使颗粒均匀的悬浮于溶液中并且提高颗粒与基质金属之间的结合力;溶液超声频率主要影响金刚石颗粒在镀层中的分布状态,进而影响鍍层硬度和鍍层中金刚石的复合量;随着超声频率的增大,金刚石的复合量明显增大,金刚石颗粒在镀层中的分布越来越均匀,镀层的显微硬度也随着增大;当超声频率为40KHZ和80KHZ时,镀层中金刚石的复合量几乎相等,但是超声频率为80KHZ时金刚石颗粒在镀层中分布更均匀;当超声频率继续增大到lOOKHz时,颗粒虽然均匀分布于复合镀层中,但镀层中金刚石的复合量和硬度都显著降低了;因此,电鍍前对镀层显微硬度影响主次顺序为:金刚石浓度〉搅拌速度〉溶液超声频率〉分散剂的量〉电流密度;对镀层中金刚石的质量含量影响主次顺序为:搅拌速度〉金刚石浓度〉溶液超声频率〉分散剂的量〉电流密度;2.5 目前复合电镀镍-金刚石的最佳工艺条件下所得镀层数据复合镀层平均厚度值 16.18μm复合镀层平均显微硬度 1927HV复合镀层中金刚石的平均复合量 63.13%2.6 复合电镀镍-金刚石工艺的常见故障及处理方法除针孔大多是气体在镀件表面停留而造成的,可以使用润湿剂和强搅拌来减小它的影响;除此之外,造成针孔的原因还有:表面润湿剂少、阴极电流密度过大等;1)表面润湿剂少电镀过程中阴极有氢气析出,如果镀液pH值过低、阴极移动过缓、润湿剂的质量浓度不足都会使氢气吸附在镀件表面,阻碍镀层金属的沉积,而在镀层表面形成针孔、麻点;由于润湿剂在电镀过程中被不断消耗,故应经常补充;2)阴极电流密度过大针孔、麻点如出现在镀件的凸出部分面向阳极,则表明阴极电流密度过大,调低阴极电流密度即可避免;2.6.3 镀层表面粗糙粗糙是由于溶液中的微粒在电镀过程中留置在镀层中而形成的;镀层粗糙的主要原因:主盐的质量浓度过高;它也是镀液不稳定因素之一;当阳极面积过大,在,,不仅降低阴极效率,而且使工件表面产生大量氢气,部分氢气泡附在工件表面,影响金属沉积,容易造成镀层花斑;所以,应该严格控制氯化物和硼酸的质量浓度,将其控制在所需范围内;2)前处理不良前处理不良会引起花斑,除油不净是主要因素;另外还有其它的一些因素,如:待镀工件有变色氧化现象;工件经酸洗、化学除油后放置时间长而氧化变色;用手接触工件容易有人体的油脂分泌物;经前处理后的工件在空气中放置一段时间再镀也要发花等;因此,一定要严格控制前处理的每一个环节,工件除油后不得接触其它污染源,前处理完毕后应尽快实施电镀,以减少镀层发花的可能性;3.复合电镀镍-金刚石的性能评述3.1 镀层性能测定方法181 镀层的表面形貌及成分分析镍-金刚石复合镀层的表面形貌和镀层中各元素百分含量是采用日立S-3400N扫描电子显微镜及其附属EDS能谱仪来进行分析;2 镀层的组织结构分析镍-金刚石复合镀层的组织结构是采用日本理学3015升;镀为5g·L-1、20 g·L-1、 30 g·L-1、 40 g·L-1、50g·L-1和60g·L-1时电镀lOmin制备的镍-金刚石复合镀层的表面形貌从图可以看出,随着镀液中金刚石浓度由5 g·L-1;1增大到50 g·L-1时,通过搅拌作用单位时间内被输送到阴极表面的微粒数量增多,微粒被沉积在鍍层中的几率也增大,所以镀层表面的金刚石的分布量明显增多;观察图a到d可见复合镀层的表面平整,无裂纹和孔洞现象;当金刚石浓度超过50 g·L-1而继续增大时,镀层中金刚石分布不均匀且会出现扎堆现象如图f所示;另外,随着金刚石浓度的增大,复合镀层表面粗糙度和脆性都有所增加;由此可知,在复合电沉积过程中,镀液中金刚石粉末的浓度必须适宜,并不是越大越好;2)电流密度对镀层表面形貌的影响下图是电流密度分别是3A ·dm-2、5.5A ·dm-2 、8 A ·dm-2 、10 A ·dm-2 、13 A ·dm-2 和15.5 A ·dm-2 时电镀10min制备的镍-金刚石复合镀层的表面形貌;从图可以看出随着电流密度的增加,镀层中金刚石的复合量先增加后减少;在低电流区,增加电流密度就会使镍金属沉积速率加快,对共沉积的金刚石粉末包裹性变好,使其更牢固的镶嵌在镀层中;电流密度继续增大,镍的沉积速率远远大于金刚石颗粒的共沉积速率,导致镀层中颗粒的含量减少;由f可以看出,当电流密度为15.5 A ·dm-2时,镀层表面平整但金刚石的复合量非常低;但是如果电流密度太大,会使镍金属晶体生长太快,金属颗粒粗大且镀层易剥落.3.3 镀层的结合力分析金,,体结合力良好;3.4 镀层的硬度分析镀层的硬度采用HX-1000显微硬度仪测定21,如图为镀层经硬度检测之后相应的压痕图,所得硬度值如表所示;从图可知,镀层压痕呈菱形,镍-金刚石复合镀层硬度压痕的对角线远小于纯镍镀层的;结合表可知,镍-金刚石复合镀层的硬度值为1861HV,而纯镍镀层的硬度值只有195HV,复合镀层的硬度值远远高于纯镍的硬度值,说明均勾、弥散的分布在镀层中的金刚石颗粒起到了弥散强化作用22;因为这些硬质颗粒主要沉积在基质金属晶界以及晶体结构不完整处,与镀层金属结合紧密,对晶粒之间的滑移起到了很大的阻碍作用,有效阻碍了镀层内为错移动,从而使金属获得了有效强化;镀层硬度值样品号纯镍HV 镍-金刚石镀层HV1 200 19572 177 20393 210 1589平均值195 18613.5 镀层的耐蚀性分析1)镀层在酸性介质中的耐蚀性将镍-金刚石复合镀层和纯镍镀层浸入质量分数为5%H2S04溶液中,待电位稳定后,在开路电位下测得镀层的交流阻抗谱图和Tafel曲线,结果分别为图3.5.1和图3.5.2所示;由图3.5.1可知,两种镀层的交流阻抗均呈半圆形,在谱图的高频区出现的半圆均是由腐蚀反应电阻和双电层电容形成的,在低频区出现的弧线表现为电感的特性23;其原因可能是在镀层的表面会生成镍氧化膜,在测镀层的交流阻抗时这些氧化膜覆盖在阳极上形成了保护膜,抑制了金属向H2SO4溶液中溶解;镍-金刚石复合镀层的半圆直径大于纯镍镀层,说明镍-金刚石复合镀层在5%H2S04溶液中的耐蚀性大于纯镍镀层;图3.5.1 镀层在5%wH2S04溶液中的交流阻抗谱图3.5.2 镀层在5 %wH2S04溶液中的Tafel曲线2)镀层在中性介质中的耐蚀性能在开路电位下,测得镍-金刚石复合镀层在质量分数为5%NaCl溶液中的交流阻抗谱图和Tafel曲线,结果分别为图3.5.3和图3.5.4所示;从图3.5.3可知,在5%NaCl溶液中,镍-金刚石复合镀层和纯镍镀层均表现出单一容抗弧,形状为规则的半圆,但镍-金刚石复合镀层的阻抗谱图的半径大于纯镍镀层,说明在5%NaCl溶液中,镍-金刚石复合镀层的耐蚀性优于纯镍镀层24;图3.5.3 镀层在5%wNaCl溶液中的交流阻抗谱图3.5.4 镀层在5 %wH2S04溶液中的Tafel曲线3)镀层在碱性介质中的耐蚀性能在开路电位下,测定镍-金刚石复合镀层和纯镍镀层在5 %NaOH溶液中的交流阻抗谱图和和Tafel曲线,结果分别为图3.5.5和图3.5.5所示;从图3.5.5可知,两种镀层的交流阻抗曲线均出现了两个容抗弧;其中,在高频容抗弧对应着阳极表面上覆盖的镍氧化膜的迟豫过程,而低频容抗弧着阳极表面处发生的电荷传递过程25,说明腐蚀现象发生;镍-金刚石复合鍍层的阻抗谱图直径大于纯镍镀层,说明镍-金刚石复合镀层在5 %wNaOH溶液中的耐蚀性优于纯镍镀层;图3.5.5 镀层在5%wNaOH溶液中的交流阻抗谱图3.5.6 镀层在5 %wNaOH溶液中的Tafel曲线两种镀层在碱性介质中的耐蚀性都最差,总体来说,金刚石微粒的加入使镍镀层的耐蚀性提高;总结本文综合叙述了复合电镀镍-金刚石的发展历史以及我国在该领域的发展状况;通过电沉积工艺制备的镍-金刚石复合镀层,硬度高,金刚石超细粉与镍的结合度好,耐磨,耐腐蚀性强,在减摩机械部件、金刚石刀具、磨具上应用十分广泛;本文也对能够影响复合镀层以及电镀过程的因素进行了系统性的归纳总结,使读者能够清晰的了解什么因素能够使镀层产生影响,让读者知道怎么做能得到-参考文献1张辽远,姜洪涛.电镀金刚石工艺的研究J.沈阳工业学院学报,2002,212:43-462杨先佳.我国复合电镀技术的现状及其发展前景D.武汉材料保护研究所:33-353唐致远,郭鹤桐.复合电镀在国内的应用J.Electroplating&Pollution Control,1991,116:14-164王永秀.镍-金刚石复合镀层的制备及其性能的研究D.广东:广东工业大学,2012:38-405王敏.复合电镀Ni-Fe-金刚石工艺J.电镀与精饰,2008,303:28-292O319胡如南.电镀手册K.北京:国防工业出版社,1979.20李云东,江辉,李根生等.电镀金刚石工具中新型镀层的研究J.材料保护,2002, 3512:31-32.21余焜,施智祥.银基金刚石复合镀层的性能研究J.功能材料,2001, 322: 169-171.22方莉俐,张兵临,姚宁,等.电铸金刚石-镍复合膜微观应力分析J.金刚石与磨料磨具工程,2005, 5: 34-37.23王立平,高燕,薛群基等.纳米金刚石对电沉积镍基复合镀层微观结构及抗磨性能的影响J.摩擦学报.2004, 246: 488-492.24王森林,曹学功.镍-金刚石复合电镀的研究J.华侨大学学报自然科学版,1998,。
化学镀镍及其原理
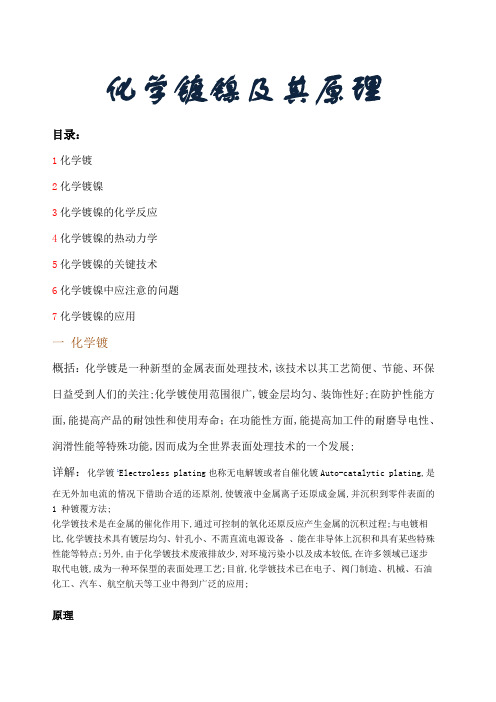
化学镀镍及其原理目录:1化学镀2化学镀镍3化学镀镍的化学反应4化学镀镍的热动力学5化学镀镍的关键技术6化学镀镍中应注意的问题7化学镀镍的应用一化学镀概括:化学镀是一种新型的金属表面处理技术,该技术以其工艺简便、节能、环保日益受到人们的关注;化学镀使用范围很广,镀金层均匀、装饰性好;在防护性能方面,能提高产品的耐蚀性和使用寿命;在功能性方面,能提高加工件的耐磨导电性、润滑性能等特殊功能,因而成为全世界表面处理技术的一个发展;详解:化学镀1Electroless plating也称无电解镀或者自催化镀Auto-catalytic plating,是在无外加电流的情况下借助合适的还原剂,使镀液中金属离子还原成金属,并沉积到零件表面的1 种镀覆方法;化学镀技术是在金属的催化作用下,通过可控制的氧化还原反应产生金属的沉积过程;与电镀相比,化学镀技术具有镀层均匀、针孔小、不需直流电源设备、能在非导体上沉积和具有某些特殊性能等特点;另外,由于化学镀技术废液排放少,对环境污染小以及成本较低,在许多领域已逐步取代电镀,成为一种环保型的表面处理工艺;目前,化学镀技术已在电子、阀门制造、机械、石油化工、汽车、航空航天等工业中得到广泛的应用;原理简称化学镀技术的原理是:化学镀是一种不需要通电,依据氧化还原反应原理,利用强还原剂在含有金属离子的溶液中,将金属离子还原成金属而沉积在各种材料表面形成致密镀层的方法;化学镀常用溶液:化学镀银、镀镍、镀铜、镀钴、镀镍磷液、镀镍磷硼液等;目前以次亚磷酸盐为还原剂的化学镀镍的自催化沉积反应,已经提出的理论有“原子氢态理论”、“氢化物理论”和“电化学理论”等;在这几种理论中,得到广泛承认的是“原子氢态理论”;二化学镀镍概念:通过电解或化学方法在金属或某些非金属上镀上一层镍的方法,称为镀镍;镀镍分电镀镍和化学镀镍;电镀镍是在由镍盐称主盐、导电盐、pH缓冲剂、润湿剂组成的电解液中,阳极用金属镍,阴极为镀件,通以直流电,在阴极镀件上沉积上一层均匀、致密的镍镀层;从加有光亮剂的镀液中获得的是亮镍,而在没有加入光亮剂的电解液中获得的是暗镍;化学镀镍是在加有金属盐和还原剂等的溶液中,通过自催化反应在材料表面上获得镀镍层的方法;化学镀镍经过多年的不断探索与研究,近几年已发展极成熟了;如Q/贻顺化学镀镍水几乎适用于所有金属表面镀镍;如:钢铁镀镍,不锈钢镀镍,铝镀镍,铜镀镍等等,它同样适用于非金属表面镀镍;比如:陶瓷镀镍,玻璃镀镍,金刚石镀镍,碳片镀镍,塑料镀镍,树脂镀镍等等;使用范围是非常广泛的;发展史的历史与相比,比较短暂,在国外其真正应用到工业仅仅是70年代末80年代初的事; 1844年,发现金属镍可以从金属镍盐的水溶液中被次盐还原而沉积出来;镍技术的真正发现并使它应用至今是在1944年,的和的发现,弄清楚了形成涂层的催化特性,发现了沉积非粉末状镍的方法,使化学技术工业应用有了可能性;但那时的化学镀镍溶液极不稳定,因此严格意义上讲没有实际价值;化学镀镍工艺的应用比实验室研究成果晚了近十年;以后,美国通用运输公司对这种工艺发生了兴趣,他们想在运输烧碱筒的内表面镀镍,而普通的方法无法实现,五年后他们研究了发展了化学镀镍磷合金的技术、公布了许多专利;1955年造成了他们的第一条试验生产线,并制成了商业性有用的化学镀镍溶液,这种化学镀镍溶液的商业名称为“Kanigen”;在国外,特别是美国、日本、化学镀镍已经成为十分成熟的高新技术,在各个工业部门得到了广泛的应用;中国的化学镀镍工业化生产起步较晚,但近几年的发展十分迅速,不仅有大量的论文发表,还举行了全国性的化学镀会议,据第五届化学镀年会发表文章的统计就已经有300多家厂家,但这一数字在当时应是极为保守的;据推测国内每年的化学镀镍市场总规模应在300亿元左右,并且以每年10%~15%的速度发展;三化学镀镍中的化学反应目前,化学镀镍镍磷合金有四种沉积机理,即原子氢理论、氢化物传输理论、电化学理论及羟基—镍离子配位理论;最为人接受的是原子氢理论: 1 化学镀镍溶液加温后,在催化作用下,次亚磷酸根脱氢形成亚磷酸根,同时析出初生态原子氢 2 初生态原子氢被吸附在催化金属表面上使其活化,使溶液中的镍阳离子还原,在催化金属表面上沉积金属镍: Ni2+ + 2H- → Ni + 2H↑ 3 催化金属表面上的初生态原子氢使次亚磷酸根还原成磷;同时,由于催化作用使次亚磷酸根分解,形成亚磷酸;原子态的氢还会合成氢气放出: H+ + H- → H2+ 其总反应为:Ni2+ + H2PO2- + H2O → HPO3 2- +3H+ + Ni 4 镍原子和磷原子共沉积,形成镍磷-合金层: Ni + P → NI-P合金固溶体或非晶态四.化学镀镍的热动力学化学镀起源于化学镀镍;化学镀镍已有 66年的历史, 但至今仍然作为一种高新技术而成为国内外的研究热点 ;化学镀镍镀液的基本成分由主盐镍盐、还原剂、络合剂、缓冲剂和稳定剂组成;化学镀反应进行的必要条件是镀液中还原剂的氧化电位必须低于氧化剂 N i2+的氧化电位, 满足这一条件的常用还原剂有次磷酸钠、肼、氨基硼烷和硼氢化钠等;络合剂是镀液中除了主盐与还原剂外的最重要的组分, 它的主要作用是在镀液中形成镍的络合物, 降低游离镍离子的浓度, 稳定镀液, 抑制氢氧化镍和亚磷酸镍沉淀的析出, 保持镀液有一定的沉积速率和较长的循环周期;络合反应能否自发地朝着目标方向进行, 对整个化学镀过程能否顺利进行起着关键性作用;因此进行络合反应的热力学研究对化学镀镍过程的理论和实践均有着重要的意义;有关化学镀镍中多元有机酸络合反应的热力学模型及其分析仅在文献 8 中报道过;但该文献存在不足的一是对不同酸根离子数 n = 1, 2, 3 的有机酸络合反应分别建立热力学模型, 而不是通式模型, 使得模型繁多和使用不便; 二是对模型进行计算时, 未考虑平衡时反应物和产物浓度对吉布斯自由能 G值和镀液pH 值当 G > 0时的影响, 使之计算误差较大; 三是未对模型中各有关参数对G 值的影响进行较为系统的理论计算和分析;针对以上不足, 本文采用热力学函数吉布斯自由能 G 为判据, 以次磷酸钠为还原剂, 取一元酸乳酸、二元酸琥珀酸、三元酸硼酸和四元酸焦磷酸 4种络合剂为例,建立了n 元酸与镍盐络合反应的热力学通式模型,并着重分析了pH 值、温度、络合率和络合剂种类对化学镀镍中络合反应热力学过程的影响;热学模型的建立在化学镀镍过程中, n 元酸性络合剂与镍盐的和H L 、热力学配位平衡中G 值不仅与化学镀镍的工艺条件如硫酸镍盐和络合剂的初始摩尔浓度 N i2+施镀温度T、n 元酸的络合率x 和镀液的pH 值有关, 而且还与络合剂的种类不同的络合剂具有不同的电离常数K 和酸根离子数 n 有关;但凡镀镍的化学反应,必定存在以下步骤:反应物向表面扩散;反就硪在催化表面上吸附;在催化表面上发生化学反应;产物从表面层脱附;产物扩散离开表面这些步骤中按化学动力学基本原理,最慢的步骤是整个沉积反应的控制步骤;五化学镀镍的关键技术1 化学镀镍液可实现再生循环利用,并可节省大量镍盐和其它成分;此外, 连续使用还可大大减少镀镍废水的排放量, 这对于提高经济效益、保护环境都有着重要的意义;2旧镀液施镀过程pH 值的降低与新镀液相比有所减少, 镀层中P 含量也有所下降;这可能是由于随着调整 pH使镀液的缓冲能力增加随着施镀次数的增加, 旧镀液镍盐的利用率在逐步提高, 镀速的增加也更快, 相应地劳动生产率也会提高, 所得镀层的外观比相同条件下新镀液的还要好一些;3镀液离子浓度;首先遇到的问题是, 镀件面积大,所需镀液容积太大;镀槽中不同位置镀液中的Ni离子浓度不均匀: 靠近镀件表面处, 因为Ni已经发生化学反应, 生成了镍磷合金镀层, 附着在设备的表面, 因而镀件周围的镀液离子浓度偏低; 而其它地方镀液离子浓度偏高,造成生产中的检测和控制困难;为此进行了一些试验;开始试验将镀件平放在镀槽底部, 换热器的管内镀液的流动是强制性的, 用封头把换热器的一头封住,与循环水泵连在一起,用循环水泵的抽吸力来带动管内镀液流动;但是结果因为镀件管内镀液流速太快, 导致形成的NiP 合金颗粒无法沉积到镀件日表面,最后镀件的两个端头没有镀好;后来发现,化学镀镍的反应过程中会产生大量的氢气, 这些气体自然会上浮到水面, 从而带动镀液发生循环流动;因此就将换热器的一端提高, 形成一定倾斜角度,反应过程中生成的气体在浮力的作一定倾斜角度,反应过程中生成的气体在浮力的作一定倾斜角度,反应过程中生成的气体在浮力的作件的面积较大,反应激烈, 因而产生的气体量巨大这样大量气泡的流动就带动了镀液的流动,使镀液换热器管内的这一端流动到了那一端,然后从换热器的管外再循环到这一端,形成了对流; 这样, 镀液的浓度就均匀了;六化学镀镍中应注意的问题化学镀镍与电镀相比,缺点是:所用的溶液稳定性较差,且溶液的维护、调整和再生都比较麻烦, 材料成本较高;但是化学镀镍得到的镀层是一种非晶态镍磷合金,结晶细致、孔隙率低、硬度高、镀层厚度均匀、可焊性好, 镀液深镀能力好, 化学稳定性高;1 镀镍液离子浓度应均匀;由于粒子浓度的差异,会导致最后被镀物两端没有镀好,因此应加强镀液的整体对流, 又采用循环水泵抽吸的办法,把镀液从镀槽的这一端抽起, 另一端流入, 方向与化学镀反应自动形成的对流循环方向一致, 加强了镀液在镀槽内的整体流动性,使镀液中的离子浓度分布更加均匀一致;2 镀镍面积问题由于镀件大, 液体多, 因此化学反应不易控制致使生产的镀件产品容易形成阴阳面, 这是指镀件和的上表面与下表面的镀层光亮程度、致密性和孔隙率不一致:上表面镀层粗糙、金属颗粒大、孔隙率高、易生锈; 下表面手感光滑, 孔隙率低、致密性良好;形成这一现象的原因有几个方面, 在后来的生产中采取多种措施进行了改进; 改进了配制镀液的用水用加热到90并经过沉淀以后的水取代自来水;由于所用的自来沉淀;如果这种颗粒在镀液中产生,伴随它的生成, 颗粒表面具有很大的表面活性和能量, 能起到高效催化作用, 使Ni 和H2PO2 在它的表面发生化学反应,生成NiP 合金小颗粒,产生沉积, 小颗粒在镀液中漂浮生长,再沉积到镀件的上表面;3 渡槽内衬材料要及时更换原来的镀槽是橡胶内衬, 在使用一段时间后会自然老化;考虑橡胶成本较高, 在试验室用镀液对847 涂料涂装件进行水煮试验, 经历36 h 的连续煮沸, 847 涂层无溶解变化;据此改用 847 涂料涂在镀槽内侧,代替橡胶内衬;但是用 847 涂料做内衬, 需要进行高温烘烤固化, 工艺复杂麻烦;于是再经过试验, 改用901 涂 .七化学镀镍的应用航空航天工业航空天工业为化学镀的使用大户之一比较突出的应用实是: 文献区价绍美国俄克荷马航空后中心 197 9, 西北空公司 1983 以来空前的发展平均净增镀厚 27 到75微米以防止燃气腐蚀,其疲劳强度的降低比电镀铬减少百分之二十五,经化学镀镍表面耐腐蚀耐磨切可焊;化学镀镍在航空航天中发挥着重要作用;汽车工业使用乙醇和汽油等混合燃料产生了燃油系统的腐蚀,应用化学镀镍技术保护锌压镀镍成为了汽化器的保护手段;汽车工业利用化学镀镍层非常均匀的特点,在形状复杂的零件上进行镀镍保护可以提供良好的抗燃油腐蚀和磨损性能;化学镀镍可有效的防止喷油器磨损,提高了可靠性和使用寿命;化学工业化学工业运用化学镀镍技术代替昂贵的耐腐蚀合金去解决问题,以便改善化学纯度以及环境提高操作安全性和生产运输可靠性,获得有利的技术经济竞争能力;石油和天然气油田采油和输油管道设备广泛的采用化学镀镍的技术,可以使抽油泵筒制成整体件,显着地提高抽油泵品质,降低了生产成本;食品加工业目前,食品包装机械中不直接与食品接触的零件为化学镀镍在食品加工中的重要应用;采矿工业某些露天采矿生产中要使用高压泵和喷射泵嘴,腐蚀和冲蚀相当严重耐蚀耐腐的化学镀镍可防止机械零件过早损坏;。
从电镀金刚石工具看金刚线

从电镀金刚石工具看金刚线金刚线是一种典型的金刚石锯切工具,但许多刚进入金刚线领域的企业,对金刚石锯切工具、电镀金刚石工具的了解很少,这会对产品开发带来一定的影响。
为此,我们特意写了篇文章,从电镀金刚石工具的角度带大家认识一下金刚线产品。
希望对大家有帮助!电镀金刚线,主要应用于光伏级硅片的开方和切片,属于金刚石锯切制品,也是电镀金刚石工具。
与金刚线类似的锯切工具还有金刚石绳锯、金刚石丝锯。
比如金刚石丝锯,它也是在钢丝表面镀上金刚石磨粒,一般用于手工往复拉加工玉石、玛瑙、水晶工艺品的内孔面,也可以用在台式丝锯机上作往复运动,用于曲线、直线切割,还可像金刚石绳锯那样,将它绕到两个绞轮上,张紧后用于切断作业。
从上面的描述,是不是感觉到它们很像呢?所以,岱勒、三超,与许多做金刚石锯片的企业一样,都是中国机床工具工业协会超硬材料分会的会员。
由于多晶硅线切市场的爆发,金刚线今年异常火爆,预期这种局面还会延续一段时间,所以很多钢丝、碳化硅、金刚石、光伏企业也纷纷进入了这个领域,欲分一杯羹。
为了让大家更好地认识金刚线,本文从电镀金刚石工具的角度浅析下金刚线的结构特点和使用性能。
1、电镀金刚石工具的特点既然金刚线属于电镀金刚石工具,那我们就先了解一下电镀金刚石工具的结构及特点。
图1是电镀金刚石工具的结构,可见其结构包括三部分组成:基体、镀层(多是电镀镍)、磨料。
其中,磨料弥散分布在金属镀层里,共同组成工作层,起磨削作用;基体具有一定的几何形状、尺寸精度和表面粗糙度,起支持电镀层的作用。
图1 电镀金刚石工具的结构示意图电镀金刚石工具具有以下特点:结构特点电镀金刚石工具只有钢基体和电镀工作层两个部分,电镀层沉积金属厚度一般为金刚石粒径的1/2~2/3,同烧结金刚石工具相比(钎焊工具除外)是非常薄的。
由于电沉积工艺的特殊性,采用电镀方法可以制造出各种复杂型面或者特别小、特别薄的金刚石工具,且制造出来的工具精度特别高。
镀层特点电镀金刚石工具的电镀层金属是通过电结晶形成的,在电镀预处理、工艺控制适当的情况下,镀层十分致密,几乎没有气孔。
金刚石表面特性及表面金属化

• 连生体进一步分成不规则连生体、平行连生体和双 晶(有连生双晶、穿插双晶、板状双晶等)。 • 多晶体有圆粒金刚石(波尔特型)、浅红金刚石和黑 金刚石等几种。 • 圆粒金刚石是由颗粒连生体和不规则连生体等微 晶形成的球状集合体,呈乳白色到钢灰色,常有裂 缝,硬度很大。 • 浅红金刚石是一种由中心向外放射状排列的微晶 金刚石组成的集合体,外形呈圆球状。这种多晶体 外壳坚硬,内核较软,硬度比圆粒金刚石和黑金刚 石低,强度比圆粒的高。 • 黑金刚石由更细金刚石组成的微密或多孔的集合 体,呈黑色、灰色或绿色,外形不规则。有的黑金 刚石表面有珐琅光泽,硬度略低于圆粒金刚石,但 韧性好。
金刚石表面特性及 表面金属化
—— 金刚石表面处理专题报告——
傅圣利
前 言
• 金刚石由于具有高硬度、低摩擦系数、高热导率、 低膨胀系数、低放射性等许多优异的物理特性, 在许多工业领域都得到应用。尤其是由金刚石和 金属、陶瓷或高分子树脂结合在一起做成的金刚 石工具,不仅被广泛用于民用建筑与土木工程、 石材加工业、汽车工业、交通工业、地勘与国防 工业等领域和其它现代高新技术领域,而且在宝 石、医疗器械、木材、玻璃钢、石材工艺品、陶 瓷、复合金属和硬脆材料等众多新领域不断出现, 社会对金刚石工具的需求也逐年增加。
3.1 基本原理
• 在金刚石表面镀覆或增加涂层以改变金刚 石表面粗糙镀对于树脂基金刚石工具也是 常用的变法,但其结合强度没有化学结合 显著。 • 金刚石表面金属化不仅能使金刚石与金属 粘接剂产生化学键合,而且能改变金刚石 表面形状,增加物理嵌合作用,提高金刚 石把持力,是金刚石最普遍采用的表面处 理方法。
• 空气中温度高于650℃时,-NO2、-NO3、 -SO3H基吸收带消失,桥接的含氧基吸收带强 度降低; • 用氢处理甚至在20℃时,呈现不同C-H基的 特征吸收带,同时-C=O、-COOH、-CHO和 -CO-O-OC-消失;900℃时用氢处理导致 -OH基脱除和C-H键含量增加。 • 化学改性处理对金刚石与水的表面接触角 影响很大(表3):
镀层摩擦系数

镀层摩擦系数
镀层摩擦系数(Coefficient of friction of a coating)是指在两个表面之间,其中一个表面经过涂覆或镀层处理后的摩擦特性。
不同类型的涂覆或镀层可以对摩擦系数产生不同的影响。
以下是一些常见涂覆和镀层的摩擦系数范围:
1.硬质涂层:
•金刚石涂层(Diamond-like carbon, DLC): 0.05 - 0.2
•碳化硅涂层(Silicon carbide, SiC): 0.2 - 0.6
•氮化硼涂层(Boron nitride, BN): 0.1 - 0.3
2.金属涂层:
•铬涂层(Chromium, Cr): 0.15 - 0.35
•镀镍涂层(Nickel, Ni): 0.5 - 0.7
•镀锌涂层(Zinc, Zn): 0.2 - 0.3
需要注意的是,涂覆或镀层的摩擦系数并非固定不变的数值,它可以受到多种因素的影响,包括表面粗糙度、润滑条件、压力、温度等。
此外,涂覆或镀层的摩擦系数也可能因不同的测试方法和实验条件而有所不同。
在实际应用中,选择合适的涂覆或镀层以及与之配合的基材是根据具体需求来决定的。
摩擦系数的低值通常有助于降低摩擦和磨损,提高涂层的耐磨性能,但也需要综合考虑其他性能指标,如耐腐蚀性、表面硬度、附着力等。
因此,在涂覆或镀层选择时,需根据具体应用场景综合考虑各种因素。
化学镀镍及其原理

化学镀镍及其原理 This manuscript was revised on November 28, 2020化学镀镍及其原理目录:1化学镀2化学镀镍3化学镀镍的化学反应4化学镀镍的热动力学5化学镀镍的关键技术6化学镀镍中应注意的问题7化学镀镍的应用一化学镀概括:化学镀是一种新型的金属表面处理技术,该技术以其工艺简便、节能、环保日益受到人们的关注。
化学镀使用范围很广,镀金层均匀、装饰性好。
在防护性能方面,能提高产品的耐蚀性和使用寿命;在功能性方面,能提高加工件的耐磨导电性、润滑性能等特殊功能,因而成为全世界表面处理技术的一个发展。
详解:化学镀[1](Electroless plating)也称无电解镀或者自催化镀(Auto-catalyticplating),是在无外加电流的情况下借助合适的还原剂,使镀液中金属离子还原成金属,并沉积到零件表面的 1 种镀覆方法。
化学镀技术是在金属的催化作用下,通过可控制的氧化还原反应产生金属的沉积过程。
与电镀相比,化学镀技术具有镀层均匀、针孔小、不需直流电源设备、能在非导体上沉积和具有某些特殊性能等特点。
另外,由于化学镀技术废液排放少,对环境污染小以及成本较低,在许多领域已逐步取代电镀,成为一种环保型的表面处理工艺。
目前,化学镀技术已在电子、阀门制造、机械、石油化工、汽车、航空航天等工业中得到广泛的应用。
原理(简称化学镀)技术的原理是:化学镀是一种不需要通电,依据氧化还原反应原理,利用强还原剂在含有金属离子的溶液中,将金属离子还原成金属而沉积在各种材料表面形成致密镀层的方法。
化学镀常用溶液:化学镀银、镀镍、镀铜、镀钴、镀镍磷液、镀镍磷硼液等。
目前以次亚磷酸盐为还原剂的化学镀镍的自催化沉积反应,已经提出的理论有“原子氢态理论”、“氢化物理论”和“电化学理论”等。
在这几种理论中,得到广泛承认的是“原子氢态理论”。
二化学镀镍概念:通过电解或化学方法在金属或某些非金属上镀上一层镍的方法,称为镀镍。
化学镀镍技术及其工业应用

第26卷第4期Vol 126 NO.4 重庆工商大学学报(自然科学版)J Chongqing Technol Business Univ 1(Nat Sci Ed ) 2009年8月Aug 12009 文章编号:1672-058X (2009)04-0399-04化学镀镍技术及其工业应用廖西平,夏洪均(重庆工商大学机械工程学院,重庆400067) 摘 要:化学镀镍技术具有工艺比较简单,镀层性能优良,是一种新兴发展的表面处理技术,由于化学镀镍层硬度高,耐磨性能好,减摩系数低。
镀态结构为非晶态,耐腐蚀性极佳。
广泛应用在各种工业中,如石油化工工业、机械模具工业、电子工业、航空航天工业等。
最突出的是应用在计算机硬盘镀底层和各种化工耐腐蚀阀门上。
多元化学镀镍和化学复合镀进一步提升和丰富了普通化学镀镍技术,使之应用范围更加广泛。
关键词:化学镀镍;镀层性能;工业;应用 中图分类号:X703文献标志码:A1 化学镀镍基本技术化学镀镍是利用还原镀液中金属离子沉积于金属零件表面上的一种自催化反应过程。
使金属零件表面牢固镀上一层镍磷合金层。
镀层成分为镍、磷元素,磷占5%~12%。
镀态硬度为500~700HV 。
左右,非晶态结构,经过热处理后析出N i 3P 金属化合物,硬度可上升到1000HV 左右。
化学镀镍分为酸性化学镀、碱性化学镀、多元化学镀和化学复合镀。
最常见的是酸性化学镀镍。
1.1 化学镀镍配方镀液配方有许多种,主要组成为:(1)主盐:硫酸镍N i 2S O 4,25~27g/L (以1L 蒸馏水为准);(2)还原图1 化学镀镍实验示意图剂:次磷酸钠NaH 2P O 2,25~28g/L;(3)缓冲剂:乙酸钠Na Ac,20~22g/L;(4)络合剂:乙酸CH 3COOH,15~18g/L;(5)稳定剂:硫脲,微量;(6)光亮剂:乙酸铅,微量。
镀液用稀碱液或系酸液调整pH 值为4.2~4.5,施镀温度控制在84℃左右,施镀时不停地搅拌镀液。
- 1、下载文档前请自行甄别文档内容的完整性,平台不提供额外的编辑、内容补充、找答案等附加服务。
- 2、"仅部分预览"的文档,不可在线预览部分如存在完整性等问题,可反馈申请退款(可完整预览的文档不适用该条件!)。
- 3、如文档侵犯您的权益,请联系客服反馈,我们会尽快为您处理(人工客服工作时间:9:00-18:30)。
金刚石表面化学镀Ni工艺研究摘要:由于金刚石表面能较高,在热压成型时很难与金属基体牢固的结合起来,因此刀具受到高的切削载荷时,金刚石很容易脱落,致使出现刀具寿命明显降低的问题,采用对金刚石的表面进行金属化处理。
本文研究了在金刚石表面金属化的各种处理方法及优化了在金刚石表面进行化学镀Ni的工艺。
关键词:金刚石;化学镀;增重率0前言金刚石具有高的热导率、低的密度、高的硬度、高的抗压强度及热膨胀系数与半导体材料好匹配等优点,但由于目前金刚石锯切工具和钻机工具多用粉末冶金的方法生产,烧结温度一般可以高达900℃,然而金刚石在空气中加热到700℃左右的时候,就开始出现氧化失重,抗压能力下降的问题;在1000℃以上时金刚石会发生石墨化,同时因为金刚石表面能很高,而且金刚石与基体润湿性比较差,与基体粘合力较弱,金刚石一般与金属基体的连接仅仅靠机械镶嵌力,却不能形成强的化学键粘合力,使金刚石在工作过程中容易脱落。
为了达到增强金刚石和金属之间的润湿性的目的,本文采用以次亚磷酸钠做为还原剂在金刚石表面进行化学镀镍的方法来降低金刚石和基体的界面能,改善他们之间的润湿性。
同时分析了金刚石表面镀覆前后不同的增重率对金刚石性能的影响。
研究了金刚石表面化学镀镍,给出了化学镀前的预处理过程和化学镀的工艺流程,并确定了化学镀镍的合理配方。
用金刚石单颗粒抗压强度测定仪测试镀覆前后单颗金刚石的抗压强度,利用扫描电镜(SEM)分析镀覆前后金刚石表面形貌、疏松致密程度等,利用X射线衍射仪(XRD)分析特征峰判断晶型非晶型、镀覆金属与金刚石有无界面生成物等。
1金刚石表面处理的发展及应用目前,在金刚石表面镀层中使用的材料主要是金属材料,所以又称之为金刚石的表面金属化处理。
在这其中根据使用地方的差异又可分为两种不同的情况:(1)表面镀钛、镀钨、镀铬等的金刚石适用于使用金属结合剂和陶瓷结合剂的砂轮;(2)镀镍和镀铜的金刚石适用于使用树脂结合剂的砂轮;1.1金刚石表面镀覆条件在金刚石表面进行镀覆时,存在非常多的形成条件和影响因素,主要有:成分条件、结构条件、工艺条件。
(1)成分条件按金属与金刚石的相互作用可将金属分为三类:①石墨化元素:元素周期表中第ⅧB族元素如Fe、Ni、Co等是碳的溶剂,在高温超高压条件下,此类元素能促进石墨转变成金刚石,是触媒元素。
但其触媒作用是双向的,即在高温常压下,这些元素会促进金刚石石墨化。
烧结的过程中,在石墨化元素的作用下,金刚石在700℃时开始发生石墨化现象,1000℃时发生严重的石墨化。
包含有石墨化元素的结合剂在热压的过程中会出现严重侵蚀金刚石的问题,导致金刚石强度迅速下降。
根据钛镀层纯度实验结果表明:钛镀层中在含有有不到1%的Fe、Co、Ni等石墨化元素存在时,就会强烈降低镀层与金刚石之间的结合强度。
②碳化物形成元素:碳可与一些过渡族金属(Ti、Mo、Nb、W、V、Cr等)形成碳化物,且3d空轨道愈多,愈易于结合。
这些碳化物形成元素及合金在合适的工艺条件下与金刚石中的碳发生反应形成碳化物,外延生长在金刚石表面,可实现这些过渡金属与金刚石之间的化学键合。
③不作用的“惰性”元素主要有:Sn、Cu、Zn等低熔点元素及其合金是金刚石工具中比较常用的结合剂成分,但他们与金刚石之间不发生化学反应,而且其浸润角大于900,与金刚石的粘结性非常差。
金刚石只有机械地镶嵌在这类结合剂中,易脱落流失。
(2)结构条件为了实现金刚石与金属的良好的冶金结合,在金刚石颗粒表面形成碳化物层,只有Ti、V、Cr、Mo、Nb、W等强碳化物形成元素才能达到这样的目的,同时还必须避免Fe、Co、Ni等一些石墨化元素与金刚石表面的直接接触,否则碳化物层就会生长在石墨层上,从而不能达到强力冶金结合的目的。
所以金刚石与金属冶金结合的结构条件碳化物层直接外延生长在金刚石上。
(3)工艺条件金刚石表面形成碳化层的过程为实际上是原子在金刚石表面扩散的过程,碳化物形成量是有反应过程的温度与时间以及PH决定的。
胎体与金刚石之间的结合依靠的是碳化物形成在金刚石上,但是碳化物的形成是受原子扩散迁移控制的,需要在一定温度下经过较长时间的界面反应。
金刚石与镀覆金属产生冶金结合的前提条件是必须使金刚石表面外延生长-即形成均匀、连续、轻薄的碳化物层,此过程需一定时间、温度,对PH也有一定的要求,且不能有石墨化元素存在。
由于在结合剂中通过直接加入碳化物形成元素进行真空液相烧结的方法不仅流程工艺条件苛刻,不适合进行大规模工业化生产。
因此在烧结之前,生产表面镀覆金属的金刚石即金刚石表面镀覆Ti、V、Cr、Mo、Nb、W及合金的金刚石是非常必要的。
在镀覆金属过程中,一定的真空、温度、时间PH条件下使金刚石表面外延生长在可控厚度的碳化物层。
作为中间产物,带有镀层的金刚石与结合剂在短时间热压烧结后即可顺利实现金属镀层与结合剂胎体之间的钎焊结合,也就实现了金刚石与结合剂之间的冶金结合。
金刚石与碳化物形成元素反应生成化合物的成分、结构及生成条件:Ti/金刚石:>873K(600℃),TiCCr/金刚石:>873K(600℃),Cr3C2、Cr7C3W/金刚石:>973K(700℃),WC、W2CMo/金刚石:>923K(650℃),MoC、M02C由于合成金刚石晶体所含包裹体为触媒元素,温度较高(>800℃)时由于触媒的双向作用,金刚石开始有石墨化倾向,使金刚石的强度出现下降趋势,且随着时间延长而加剧,但是如果温度过低,则很难形成碳化物。
因此,要使镀后金刚石与镀层形成强力结合,界面必须形成相应的碳化物,这样镀覆温度应该高于600℃。
为了避免对金刚石表面的热损伤,镀覆温度又必须低于900℃。
可见最理想的镀覆温度为600~900℃。
1.2金刚石表面镀覆的金属化原理金刚石表面金属化定义为使金刚石表层具有金属性,金刚石经表面镀覆处理会使金刚石表面金属化。
金刚石的金属性主要指优良的导电导热性和良好的延展性,通常金属性的含义由金刚石表面之金属、合金或金属碳化物乃至它们的混合物的性质来确定。
对金刚石进行表面金属化的原因是因为金刚石与金属之间靠共价键结合,他们之间有很高的界面能,因此其表面不能被低熔点金属或合金所浸润,并且金刚石热膨胀系数远远小于金属基体结合剂的热膨胀系数,使得金刚石磨料与一般金属的粘结能力很差。
金刚石与基体结合剂之间没有界面结合力,仅靠基体对金刚石的机械镶嵌作用,在使用过程中金刚石磨粒易脱落、流失,造成极大的浪费。
因此,提高金属合金和金刚石的粘结能力,增强结合剂与金刚石之间的结合能力,改善金刚石晶粒外观,找到产生金刚石与基体间化学结合的方法,就成为普遍关注并迫切需要解决的问题。
1.3金刚石表面镀覆金属化的模型金刚石表面金属化模型如图1所示,金属化表面层由3层材料叠合而成。
从内到外共有三层,最里面一层是碳化物层,一般厚度在几百至上千埃,强固地附着在金刚石表面,这层结构的完美是金刚石表面金属化的关键。
第二层为合金化层,是针对碳化物层而设计的,它对碳化物层有很好的粘结性,可以选取Ni、CO、Cu等合金。
合金化层的形成使金刚石表面呈现完美的金属特性,如:可导电性、可焊接性、可烧结性。
该层的厚度可以是几微米。
最外面一层是电镀层,主要是考虑到金刚石工具中合金胎体与金刚石线膨胀系数的极大的差异性而设计,热压后金刚石固块在冷却中会产生很大的内应力,为了使内应力得到一定程度的缓解,对于刚性较大的胎体,增加几十微米厚的电镀层是非常有益的。
图1金刚石表面金属化模型1.4金刚石表面金属化作用(1)提高各种结合剂对金刚石的粘结能力,镀层在金刚石和结合剂之间起结合层的作用,将金刚石与结合剂非常牢固地结合起来,提高了金刚石与结合剂之间的结合强度,提高了相应的把持力,避免了金刚石提前脱落;(2)起到隔离保护作用,在金刚石工具高温烧结和高温磨削时,合金镀层可以隔离保护金刚石,使金刚石不发生石墨化反应、氧化反应及侵蚀,有效的减少了高温时金刚石强度的下降。
(3)提供磨料的强度和韧性,镀层起补强、增韧作用,金刚石内部缺陷、线缺陷,面缺陷,微裂纹、微小孔洞等情况可通过镀层得到弥补,提高了强度。
(4)改善了热传递作用,镀覆材料一般导热性比未镀覆的材料要好,使用过程中可以降低材料的温度升高升,改善了金刚石工具的工作环境。
1.5金刚石表面金属化的方法目前金刚石表面金属化的常用途径有:化学镀加电镀;真空蒸镀;等离子溅射;磁控溅射;化学气相沉积;物理气相沉积;机械包覆等.1.5.1化学镀后再电镀化学镀是在不通电流的情况下,通过自催化过程的氧化-还原反应在金刚石表面沉积金属.金刚石是绝缘体,不能进行电镀,但经过敏化、活化和化学镀后,其表面具有金属性,可以继续电镀,获得所需的镀层品种及厚度.其工艺流程方框图如图2所示。
金刚石表面化学镀和电镀金属镀层在900℃空气气氛中对金刚石有良好的高温保护作用,在1 050℃时,空气中的氧将穿透镀层与金刚石表面碳原子发生氧化反应,使金刚石受到严重的热腐蚀;金刚石表面化学镀和电镀金属镀层在900℃真空中受热时,与未镀覆金刚石类似,只受到微弱的热腐蚀,而在1 050℃时,由于化学镀层中的Ni、Fe等合成金刚石的触媒元素的存在,金刚石反而受到较强的热腐蚀。
图2金刚石表面化学镀-电镀覆层金属化实验过程示意图1.5.2真空镀将强碳化物形成元素(如W、啊、Cr、V、Mo、Nb等)通过真空镀覆的方法沉积于金刚石表面,此方法需要真空设备,工艺复杂。
目前常用的真空镀覆技术有以下几种:(1)真空物理气相沉积镀(PVD)在真空条件下,将金属气化成原子、分子或离子直接沉积到镀件表面上。
利用真空蒸发、磁控溅射和离子束等方法对金刚石表面镀覆钛、铬钛合金等进行试验,并研究了镀层与金刚石的界面反应和粘结等问题。
①磁控溅射镀覆技术磁控溅射是在真空条件下导入一定压力的惰性气体(Ar),阴阳极间形成一定强度的电场,并引入强磁场施加影响,使被阳离子轰击而溅射出的靶材金属阴离子加速射向欲镀覆目标位。
此方法单次镀覆量低、镀层不均匀,容易出现漏镀,镀层与金刚石之间只是物理附着,无化学冶金结合等,为了得到最佳镀层结构要反复多次镀覆,价格较高,操作复杂,难以实现工业化应用。
②真空蒸发镀技术真空蒸发镀是在真空条件下,将镀层材料置于料舟之中,并将料舟通电迅速升温至镀层材料汽化温度,镀层材料汽化后形成金属蒸汽,在脱离料舟并冷却后,沉积到镀覆目标。
由于此类方法做不到大批量的镀覆,没有工业化应用前景,镀层与磨粒之间的结合力仍未达到理想目标。
③真空微蒸发镀覆技术真空微蒸发镀覆是将超硬磨料与某些能够与其表面形成稳定化合物并经过高度纯化、活化的金属近距离接触,在一定的真空和温度(金刚石低于760"C)条件下,这些高度活化的金属表层原子获得外部能量支持而使振幅增大,与磨粒表面发生反应,生成两者间的化合物。