提高转炉废钢比
转炉炼钢知识问答
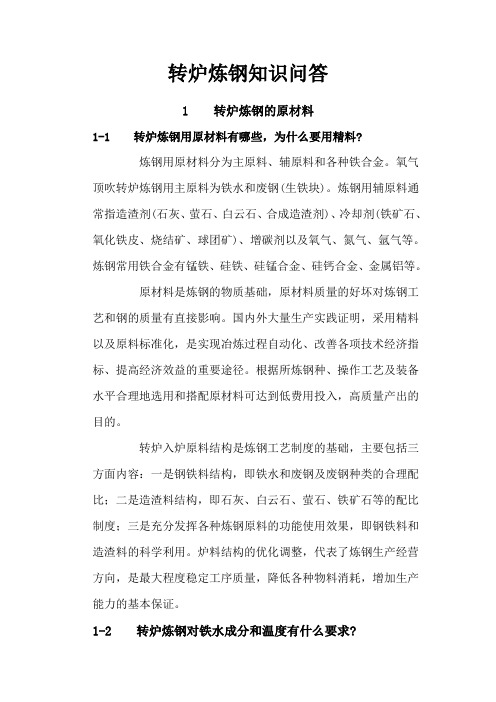
转炉炼钢知识问答1 转炉炼钢的原材料1-1 转炉炼钢用原材料有哪些,为什么要用精料?炼钢用原材料分为主原料、辅原料和各种铁合金。
氧气顶吹转炉炼钢用主原料为铁水和废钢(生铁块)。
炼钢用辅原料通常指造渣剂(石灰、萤石、白云石、合成造渣剂)、冷却剂(铁矿石、氧化铁皮、烧结矿、球团矿)、增碳剂以及氧气、氮气、氩气等。
炼钢常用铁合金有锰铁、硅铁、硅锰合金、硅钙合金、金属铝等。
原材料是炼钢的物质基础,原材料质量的好坏对炼钢工艺和钢的质量有直接影响。
国内外大量生产实践证明,采用精料以及原料标准化,是实现冶炼过程自动化、改善各项技术经济指标、提高经济效益的重要途径。
根据所炼钢种、操作工艺及装备水平合理地选用和搭配原材料可达到低费用投入,高质量产出的目的。
转炉入炉原料结构是炼钢工艺制度的基础,主要包括三方面内容:一是钢铁料结构,即铁水和废钢及废钢种类的合理配比;二是造渣料结构,即石灰、白云石、萤石、铁矿石等的配比制度;三是充分发挥各种炼钢原料的功能使用效果,即钢铁料和造渣料的科学利用。
炉料结构的优化调整,代表了炼钢生产经营方向,是最大程度稳定工序质量,降低各种物料消耗,增加生产能力的基本保证。
1-2 转炉炼钢对铁水成分和温度有什么要求?铁水是炼钢的主要原材料,一般占装入量的70%~100%。
铁水的化学热与物理热是氧气顶吹转炉炼钢的主要热源。
因此,对入炉铁水化学成分和温度必须有一定的要求。
A铁水的化学成分氧气顶吹转炉炼钢要求铁水中各元素的含量适当并稳定,这样才能保证转炉冶炼操作稳定并获得良好的技术经济指标。
(1)硅(Is)。
硅是转炉炼钢过程中发热元素之一。
硅含量高,会增加转炉热源,能提高废钢比。
有关资料表明,铁水中WSi每增加0.1%,废钢比可提高约1.3%。
铁水硅含量高,渣量增加,有利于去除磷、硫。
但是硅含量过高将会使渣料和消耗增加,易引起喷溅,金属的收得率降低。
Si含量高使渣中SiO2含量过高,也会加剧对炉衬的冲蚀,并影响石灰渣化速度,延长吹炼时间。
转炉废钢综合收得率测算研究
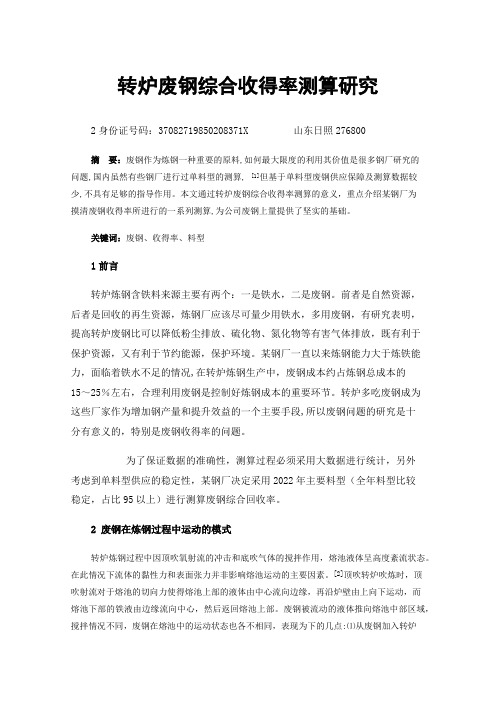
转炉废钢综合收得率测算研究2身份证号码:******************山东日照276800摘要:废钢作为炼钢一种重要的原料,如何最大限度的利用其价值是很多钢厂研究的问题,国内虽然有些钢厂进行过单料型的测算,[1]但基于单料型废钢供应保障及测算数据较少,不具有足够的指导作用。
本文通过转炉废钢综合收得率测算的意义,重点介绍某钢厂为摸清废钢收得率所进行的一系列测算,为公司废钢上量提供了坚实的基础。
关键词:废钢、收得率、料型1前言转炉炼钢含铁料来源主要有两个:一是铁水,二是废钢。
前者是自然资源,后者是回收的再生资源,炼钢厂应该尽可量少用铁水,多用废钢,有研究表明,提高转炉废钢比可以降低粉尘排放、硫化物、氮化物等有害气体排放,既有利于保护资源,又有利于节约能源,保护环境。
某钢厂一直以来炼钢能力大于炼铁能力,面临着铁水不足的情况,在转炉炼钢生产中,废钢成本约占炼钢总成本的15~25%左右,合理利用废钢是控制好炼钢成本的重要环节。
转炉多吃废钢成为这些厂家作为增加钢产量和提升效益的一个主要手段,所以废钢问题的研究是十分有意义的,特别是废钢收得率的问题。
为了保证数据的准确性,测算过程必须采用大数据进行统计,另外考虑到单料型供应的稳定性,某钢厂决定采用2022年主要料型(全年料型比较稳定,占比95以上)进行测算废钢综合回收率。
2 废钢在炼钢过程中运动的模式转炉炼钢过程中因顶吹氧射流的冲击和底吹气体的搅拌作用,熔池液体呈高度紊流状态。
在此情况下流体的黏性力和表面张力并非影响熔池运动的主要因素。
[2]顶吹转炉吹炼时,顶吹射流对于熔池的切向力使得熔池上部的液体由中心流向边缘,再沿炉壁由上向下运动,而熔池下部的铁液由边缘流向中心,然后返回熔池上部。
废钢被流动的液体推向熔池中部区域,搅拌情况不同,废钢在熔池中的运动状态也各不相同,表现为下的几点:⑴从废钢加入转炉后,呈无序状态堆积在炉底,在冶炼状态下,转炉熔池内的铁液是以“涌泉”状的形式形成环流,并且推动废钢的运动。
转炉炼钢的原材料
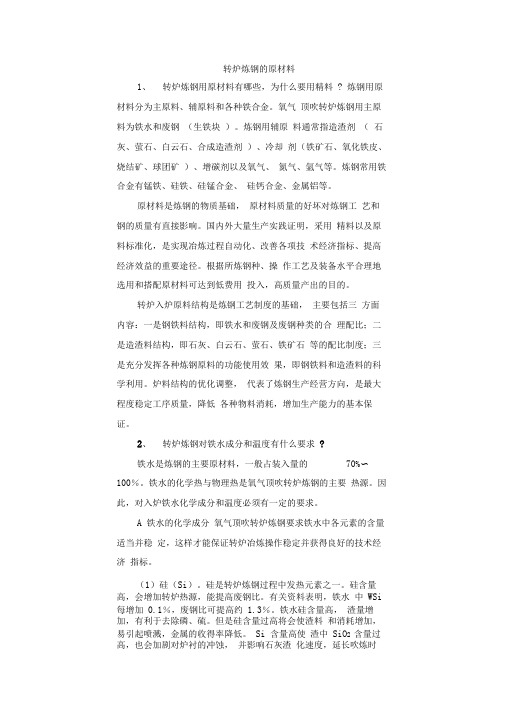
转炉炼钢的原材料1、转炉炼钢用原材料有哪些,为什么要用精料? 炼钢用原材料分为主原料、辅原料和各种铁合金。
氧气顶吹转炉炼钢用主原料为铁水和废钢(生铁块)。
炼钢用辅原料通常指造渣剂(石灰、萤石、白云石、合成造渣剂)、冷却剂(铁矿石、氧化铁皮、烧结矿、球团矿)、增碳剂以及氧气、氮气、氩气等。
炼钢常用铁合金有锰铁、硅铁、硅锰合金、硅钙合金、金属铝等。
原材料是炼钢的物质基础,原材料质量的好坏对炼钢工艺和钢的质量有直接影响。
国内外大量生产实践证明,采用精料以及原料标准化,是实现冶炼过程自动化、改善各项技术经济指标、提高经济效益的重要途径。
根据所炼钢种、操作工艺及装备水平合理地选用和搭配原材料可达到低费用投入,高质量产出的目的。
转炉入炉原料结构是炼钢工艺制度的基础,主要包括三方面内容:一是钢铁料结构,即铁水和废钢及废钢种类的合理配比;二是造渣料结构,即石灰、白云石、萤石、铁矿石等的配比制度;三是充分发挥各种炼钢原料的功能使用效果,即钢铁料和造渣料的科学利用。
炉料结构的优化调整,代表了炼钢生产经营方向,是最大程度稳定工序质量,降低各种物料消耗,增加生产能力的基本保证。
2、转炉炼钢对铁水成分和温度有什么要求?铁水是炼钢的主要原材料,一般占装入量的70%〜100%。
铁水的化学热与物理热是氧气顶吹转炉炼钢的主要热源。
因此,对入炉铁水化学成分和温度必须有一定的要求。
A 铁水的化学成分氧气顶吹转炉炼钢要求铁水中各元素的含量适当并稳定,这样才能保证转炉冶炼操作稳定并获得良好的技术经济指标。
(1)硅(Si)。
硅是转炉炼钢过程中发热元素之一。
硅含量高,会增加转炉热源,能提高废钢比。
有关资料表明,铁水中WSi 每增加0.1%,废钢比可提高约1.3%。
铁水硅含量高,渣量增加,有利于去除磷、硫。
但是硅含量过高将会使渣料和消耗增加,易引起喷溅,金属的收得率降低。
Si 含量高使渣中SiO2 含量过高,也会加剧对炉衬的冲蚀,并影响石灰渣化速度,延长吹炼时间。
转炉炼钢题库
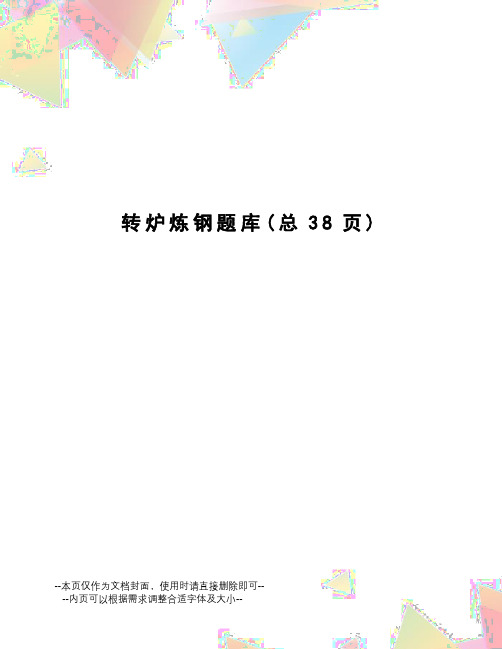
转炉炼钢题库(总38页)--本页仅作为文档封面,使用时请直接删除即可----内页可以根据需求调整合适字体及大小--第一章第一部分单项选择题1-1-1 1.可以增加废钢比的情况是( )。
A.铁水温度低 B.铁水硅含量高C.采三孔直筒型氧枪喷头D.铁水锰含量高答案:B1-1-1 2.为利于转炉的热行,成渣迅速,减少喷溅,我国规定入炉铁水温度应大于( )。
A.1120℃ B.1240℃ C.1539℃℃答案:B1-1-1 3. 磷是强发热元素,磷会使钢产生的现象是( )。
A.冷脆 B.热脆 C.断裂 D.弯曲答案:A1-1-1 4.炼钢用铁水硅含量高,热来源增多,能够 ( )。
A.提高废钢比B.降低废钢比C.减少渣量消耗D.减少炉衬冲蚀答案:A1-1-1 5.吹炼低磷铁水,转炉可采用( )。
A.单渣法操作 B.双渣法操作 C.留渣法操作 D.无渣法操作答案:A1-1-1 6.铁水温度是铁水带入转炉物理热多少的标志,铁水物理热约占转炉热量总收入的( )。
A.42% B.52% C.62% D.32%答案:A1-1-3 7.废钢是氧气转炉炼钢的金属料之一,冷却效应比较稳定,一般占装入量的( )。
%以下 %以下 %~40% D.40%以上答案:B1-1-3 8. 炼钢炉料还要求少锈蚀。
锈的化学成分是Fe(OH)2或Fe2O3·H2O,在高温下会分解出一种使钢中产生白点,降低钢的机械性能(特别是塑性严重恶化)的物质,它是( )。
A.[O]B.[C]C.[N]D. [H]答案:D1-1-3 9.入炉废钢的块度要适宜。
对转炉来讲,一般要小于炉口直径的()。
2 4 6 8答案:A1-1-3 10.转炉用废钢严禁混入密封容器,因为它容易造成()。
A.渣量增大B.钢水流动性差C.碱度升高D.爆炸答案:D1-2-1 11.萤石的主要成分是( )。
B. CaF2C. CaCO3答案:B1-2-1 12.我国石灰活性度的测定采用()。
LF钢包精炼炉加废钢试验
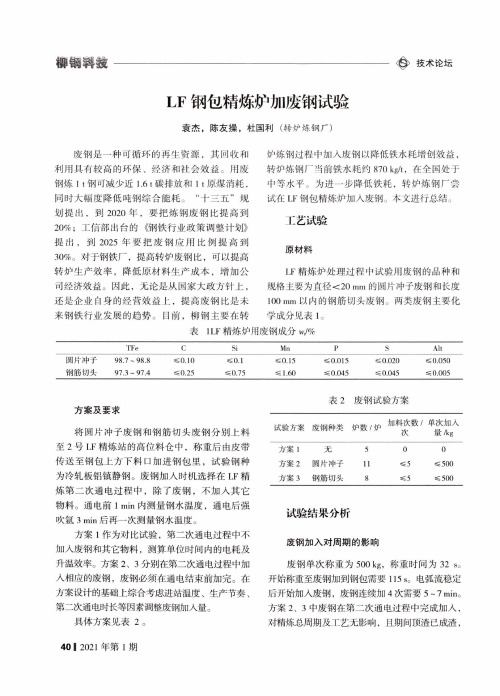
榔镟轉截技术论坛LF钢包精炼炉加废钢试验袁杰,陈友操,杜国利(转炉炼钢厂)废钢是一种可循环的再生资源,其回收和 利用具有较高的环保、经济和社会效益。
用废 钢炼1t钢可减少近1.6t碳排放和1t原煤消耗,同时大幅度降低吨钢综合能耗。
“十三五”规 划提出,到2020年,要把炼钢废钢比提高到 20%;工信部出台的《钢铁行业政策调整计划》提出,到2025年要把废钢应用比例提高到30%。
对于钢铁厂,提高转炉废钢比,可以提高 转炉生产效率,降低原材料生产成本,增加公 司经济效益。
因此,无论是从国家大政方针上,还是企业自身的经营效益上,提高废钢比是未 来钢铁行业发展的趋势。
目前,柳钢主要在转炉炼钢过程中加人废钢以降低铁水耗增创效益,转炉炼钢厂当前铁水耗约870 k g/t,在全国处于 中等水平。
为进一步降低铁耗,转炉炼钢厂尝 试在LF钢包精炼炉加入废钢。
本文进行总结。
工艺试验原材料LF精炼炉处理过程中试验用废钢的品种和 规格主要为直径<20mm的圆片冲子废钢和长度 100 mm以内的钢筋切头废钢。
两类废钢主要化 学成分见表1。
表1LF精炼炉用废钢成分w/%T F e C S i Mn P S A lt 圆片冲子98.7 ~ 98.8 矣0.10 矣0.1 矣0.15 矣0.015 <0.020 矣0.050钢筋切头97.3 ~ 97.4 «0.25(0.75 矣1.60 矣0.045 «0.045 矣0.005方案及要求将圆片冲子废钢和钢筋切头废钢分别上料 至2号LF精炼站的高位料仓中,称重后由皮带 传送至钢包上方下料口加进钢包里,试验钢种 为冷轧板铝镇静钢。
废钢加人时机选择在LF精 炼第二次通电过程中,除了废钢,不加人其它 物料。
通电前1min内测量钢水温度,通电后强 吹氩3 min后再一次测量钢水温度。
方案1作为对比试验,第二次通电过程中不 加人废钢和其它物料,测算单位时间内的电耗及 升温效率。
提高转炉生铁加入比对转炉冶炼优化的影响

提高转炉生铁加入比对转炉冶炼优化的影响氧气顶吹转炉炼钢主要原料为铁水和废钢,配比由炼铁与炼钢能力比、铁水成分、转炉容量、钢种、废钢价格等多种因素决定。
氧气转炉炼钢中富余热通常采用加入冷料来平衡,主要使用废钢及铁矿石,使吹炼过程熔池维持正常的升温和所需的出钢温度。
有时冷料也采用一部分生铁块,一般情况生铁的加入量在5%以下,增加生铁比在生产中出现了一些问题,如前期熔池温度低、废钢和石灰不易熔化、炉口溢渣、金属消耗增加、脱硫困难、终点命中率低等。
因此提高转炉生铁加入比需要优化转炉冶炼控制,保证转炉正常生产。
一、预防冶炼前期温度低的措施(1)严格规定装入制度,避免过量增加冷料量。
根据热平衡计算及结合现场实际,稳定装入量。
(2)提高入炉金属料Si含量和保证铁水温度高于1300℃。
适当提高Si含量,有利于冶炼初期快速升温,可采购高Si生铁。
缩短铁水转运时间,可有效保证铁水入炉温度。
(3)采用留渣操作,减少头批石灰用量。
转炉在溅渣护炉后留约1/3的残渣,这样可减少头批石灰量,并有利于冶炼初期快速形成具有一定碱度、一定流动性的初渣,利于快速提温。
二、加入废钢的工艺措施废钢的外形尺寸和块度应保证能从炉口顺利进入转炉。
废钢单重不能过重,轻型废钢和重型废钢合理搭配。
按照国标要求废钢的长度不大于1000mm,最大单件重量不大于800kg。
三、预防石灰不熔化及炉口溢渣的措施(1)使用活性石灰的水活性度大于310ml,体积密度小,约为1.7~2.0g/cm3,气孔率高达40%以上,比表面积为0.5~1.3cm2/g;晶粒细小,熔解速度快,反应能力强。
使用活性石灰能减少石灰和转炉渣量,在石灰表面也很难形成致密的CaO、SiO2硬壳,有利于加速石灰的渣化。
(2)使用轻烧白云石代替白云石,减少头批渣料加入量。
(3)留渣操作可有效降低石灰加入量,并有利于石灰渣化。
(4)确定合适的枪位减少炉口溢渣。
四、控制金属消耗的办法加强冶炼过程控制,要求控制好熔池温度,前期温度不过低,中后期温度不过高,防止熔池温度突然降低,保证脱碳反应均衡进行,控制好渣中ΣFeO,不使渣中氧化铁过高,消除爆发性喷溅。
转炉炼钢知识问答
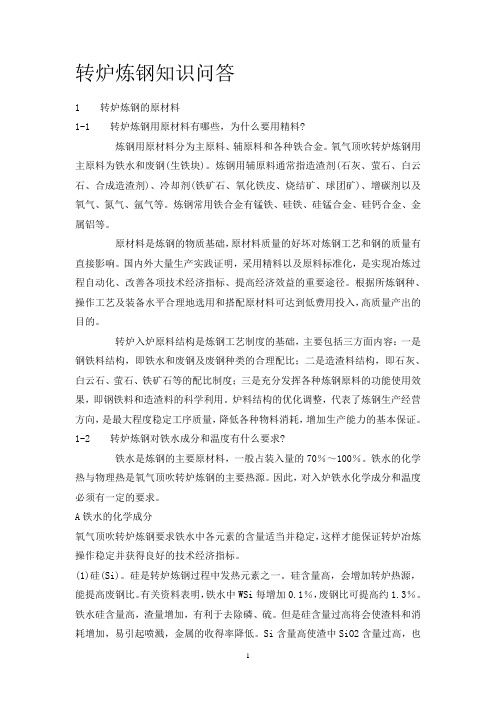
转炉炼钢知识问答1 转炉炼钢的原材料1-1 转炉炼钢用原材料有哪些,为什么要用精料?炼钢用原材料分为主原料、辅原料和各种铁合金。
氧气顶吹转炉炼钢用主原料为铁水和废钢(生铁块)。
炼钢用辅原料通常指造渣剂(石灰、萤石、白云石、合成造渣剂)、冷却剂(铁矿石、氧化铁皮、烧结矿、球团矿)、增碳剂以及氧气、氮气、氩气等。
炼钢常用铁合金有锰铁、硅铁、硅锰合金、硅钙合金、金属铝等。
原材料是炼钢的物质基础,原材料质量的好坏对炼钢工艺和钢的质量有直接影响。
国内外大量生产实践证明,采用精料以及原料标准化,是实现冶炼过程自动化、改善各项技术经济指标、提高经济效益的重要途径。
根据所炼钢种、操作工艺及装备水平合理地选用和搭配原材料可达到低费用投入,高质量产出的目的。
转炉入炉原料结构是炼钢工艺制度的基础,主要包括三方面内容:一是钢铁料结构,即铁水和废钢及废钢种类的合理配比;二是造渣料结构,即石灰、白云石、萤石、铁矿石等的配比制度;三是充分发挥各种炼钢原料的功能使用效果,即钢铁料和造渣料的科学利用。
炉料结构的优化调整,代表了炼钢生产经营方向,是最大程度稳定工序质量,降低各种物料消耗,增加生产能力的基本保证。
1-2 转炉炼钢对铁水成分和温度有什么要求?铁水是炼钢的主要原材料,一般占装入量的70%~100%。
铁水的化学热与物理热是氧气顶吹转炉炼钢的主要热源。
因此,对入炉铁水化学成分和温度必须有一定的要求。
A铁水的化学成分氧气顶吹转炉炼钢要求铁水中各元素的含量适当并稳定,这样才能保证转炉冶炼操作稳定并获得良好的技术经济指标。
(1)硅(Si)。
硅是转炉炼钢过程中发热元素之一。
硅含量高,会增加转炉热源,能提高废钢比。
有关资料表明,铁水中WSi每增加0.1%,废钢比可提高约1.3%。
铁水硅含量高,渣量增加,有利于去除磷、硫。
但是硅含量过高将会使渣料和消耗增加,易引起喷溅,金属的收得率降低。
Si含量高使渣中SiO2含量过高,也会加剧对炉衬的冲蚀,并影响石灰渣化速度,延长吹炼时间。
转炉工作原理及结构设计要点

本科课程设计攀枝花学院转炉工作原理及结构设计学生姓名:学生学号::院(系)年级专业:指导教师:二〇一三年十二月攀枝花学院本科课程设计转炉工作原理及结构设计 1.1 前言氧气顶吹转炉炼钢车间在首钢建成投产。
其后,30t1964年,我国第一座上钢三厂二转炉车间等相继将原侧吹转炉改为氧气顶吹转上钢一厂三转炉车间、大型氧气顶120t世纪60年代中后期,我国又自行设计、建设了攀枝花炉。
20在改革开放方年代后,世纪801971并于年建成投产。
进入20吹转炉炼钢厂,由于氧气转炉炼钢和连铸的我国氧气转炉炼钢进入大发展时期,针策的指引下, t,成为世界第一产钢大国。
亿迅速发展,至1996年我国钢产量首次突破11.2 转炉概述)炉体可转动,用于吹炼钢或吹炼锍的冶金炉。
转炉炉体转炉(converter用钢板制成,呈圆筒形,内衬耐火材料,吹炼时靠化学反应热加热,不需外加热源,是最重要的炼钢设备,也可用于铜、镍冶炼。
转炉按炉衬的耐火材料性质分为碱性(用镁砂或白云石为内衬)和酸性(用硅质材料为内衬)转炉;按气体吹分为空气转炉和按吹炼采用的气体,顶吹和侧吹转炉;入炉内的部位分为底吹、靠转其主要特点是:氧气转炉。
转炉炼钢主要是以液态生铁为原料的炼钢方法。
炉内液态生铁的物理热和生铁内各组分(如碳、锰、硅、磷等)与送入炉内的氧炉料主要为铁使金属达到出钢要求的成分和温度。
进行化学反应所产生的热量,,为调整温度,可加入废钢及少量的冷生水和造渣料(如石灰、石英、萤石等)铁块和矿石等。
转炉分类1.2.11.2.1.1 炼钢转炉早期的贝塞麦转炉炼钢法和托马斯转炉炼钢法都用空气通过底部风嘴鼓入炼钢转炉按不同侧吹转炉容量一般较小,从炉墙侧面吹入空气。
钢水进行吹炼。
耳轴架置通过托圈、需要用酸性或碱性耐火材料作炉衬。
直立式圆筒形的炉体,于支座轴承上,操作时用机械倾动装置使炉体围绕横轴转动。
年代发展起来的氧气转炉仍保持直立式圆筒形,随着技术改进,发展成 50;(见氧气顶吹转炉炼钢)即因而得名氧气顶吹转炉,L-D转炉顶吹喷氧枪供氧,用带吹冷却剂的炉底喷嘴的,称为氧气底吹转炉(见氧气底吹转炉炼钢)。
- 1、下载文档前请自行甄别文档内容的完整性,平台不提供额外的编辑、内容补充、找答案等附加服务。
- 2、"仅部分预览"的文档,不可在线预览部分如存在完整性等问题,可反馈申请退款(可完整预览的文档不适用该条件!)。
- 3、如文档侵犯您的权益,请联系客服反馈,我们会尽快为您处理(人工客服工作时间:9:00-18:30)。
1 废钢比低的原因:
1.1铁水的成分及温度
铁水温度低、硅含量低是导致废钢比低的主要原因。铁水的温度低:运输时间长、脱硫
扒渣的比率大,使铁水温度降低。
1.2炉型
炉型过于矮胖时,炉内喷溅物容易喷出炉外,热量和金属损失较大。因此,矮胖型的炉
子比瘦高型的热损失大,影响废钢比。
1.3留渣操作
留渣操作有利于热量的保存和化渣,减少炉渣成渣消耗的热量,有利于废钢的加入,提
高废钢比。
2 采取措施 (邯钢数据)
2.1减少铁水带渣量
铁渣的碱度平均约为0.8,远远低于钢渣的碱度,转炉炉渣的碱度大约在2.2~3.5之间。
低碱度的铁渣进入转炉后,为了满足吹炼过程需要要增加白灰的用量,使渣量增加,这就会
使吹炼时喷溅增加,喷溅时炉渣带走了一部分热量降低了转炉热效率,影响转炉脱S、P的
操作。有关资料报道表明每降低1% 的高炉渣可以降低钢铁料消耗0.5% ,减少白灰加入量
10~15 kg/t钢。
2.2采用留渣操作
转炉终点倒炉时倒掉一部分炉渣,出完钢后通过加料溅渣调节炉渣的氧化性,溅完渣后
直接加废钢、兑铁水。采用留渣操作一方面可以利用留渣的碱度使吹炼前期尽快形成具有一
定碱度的炉渣,对前期去S、P 非常有利;另一方面由于初期渣中的MnO、MgO特别是FeO
的存在,使石灰的溶解速度加快还减少了白灰等造渣剂的用量,减少了化渣时需要的热量。
另外,留渣带入了大量的物理热,使吹炼初期迅速升温,也有利于石灰的溶解促进成渣,提
高了转炉的热效率,有利于废钢加入量从而提高废钢比。
2.3实行少渣炼钢
实行精料方针,提高白灰的活性度,转炉采取少渣炼钢。采用活性白灰造渣,白灰的反
应性好,CaO利用率高,终渣游离CaO可降到5%以下。每减少1 kg的白灰用量可熔化1. 5
kg的废钢,而使渣量减少3~ 4 kg。据计算,渣量每减少1% 可以使钢铁料消耗降低5 kg。
减少渣量不但可以提高转炉废钢比,而且还可以直接降低吹损率。炉渣热焓与钢水热焓的比
值为1. 56,即吨钢减少渣50 kg而节约的热量相当于多吃78 kg的废钢。
2.4降低转炉出钢温度
降低转炉出钢温度有利于转炉操作,可以降低钢水的氧化性,降低吹损率提高金属收得
率,同时有利于保护炉衬。降低出钢温度可以通过提高废钢比来消耗转炉内富余的温度,减
少了热量支出。在转炉操作过程中由于降低了出钢温度使喷溅和返干现象减少,优化了操作。
为了使钢水能够浇完保证生产的顺行必须采取钢水保温措施,减少钢水的热量损失。采取的
措施主要有:在钢包中加保温剂、中间包加保温盖、减少钢水待浇时间、加强混铁炉保温、
降低铁水预处理和钢水精炼时间、减少转炉空炉时间、完善钢包在线烘烤制度、加强生产组
织和调度等。
2.5提高煤气回收时间和使用效率
转炉煤气中含有较高的CO 气体,还有O2、CO2和N2,提高转炉煤气回收量,不仅
能有效降低炼钢工序生产成本,为实现负能炼钢打下基础, 而且能极大降低钢厂污染物排放
总量,实现清洁生产。所以在吹炼的同时要兼顾煤气的回收工作,当煤气中CO含量大于
35%且O2 含量小于2% 时开始回收,要求每炉钢的回收时间要大于11 min,开新炉前5炉
和补炉后第一炉可以不回收。转炉节能降耗的途径之一就是利用煤气的显热和潜热的回收和
利用,转炉煤气的平均温度为1 355℃,炉气带走热量为220. 66微焦/t钢,占热支出的9.
78%,一般占到8%~10%。回收后的煤气可以用来烘烤钢包和预热废钢以提高转炉热利用率,
提高废钢比。
3 提高废钢比措施的发展方向
3.1通过高位料仓加热压铁
由于废钢资源日益减少,热压铁将是废钢的有效替代品。鞍钢目前也在使用热压铁替代
废钢,只是在废钢槽内随废钢一次加入炉内,没有进行二次调整的机会。通过料仓加热压铁
后,可以根据铁水条件随时补加废钢,充分利用铁水的内在资源,最大限度加入废钢。
3.2使用提温剂
向炉内加入SiC或焦炭碎末等其它廉价的提温剂,增加炼钢系统的外部热源,抵消废钢
的冷却作用,增加废钢加入量。提温剂的加入形式有两种:一种是随废钢一起加入,这种形
式的灵活性小,要求不允许有任何计算失误,否则浪费铁水热资源或造成过氧化操作;另一
种形式是高位料仓加入,可以根据铁水情况随机加入。这种形式最理想,能够完全利用铁水
资源,而且不造成过氧化操作。
3.3进行废钢预热
利用外部热源加热废钢,减弱废钢的冷却效果,增加废钢的加入量,这种方法设备投资
较大,维护和使用费用也比较昂贵。如果有废弃余热可以利用,这种方法是一个提高废钢比
的好方法。
总结:
在冶炼钢种一定的情况下,提高转炉废钢比主要应从以下两方面入手: 一方面提供外部
热源,即采用加入提温剂或进行废钢预热的措施;另一方面提高操作水平,即提高生产组织
紧凑程度,提高留渣操作比率,合理利用现有资源。