提高转炉废钢比对标
影响转炉废钢比原因的分析及对策
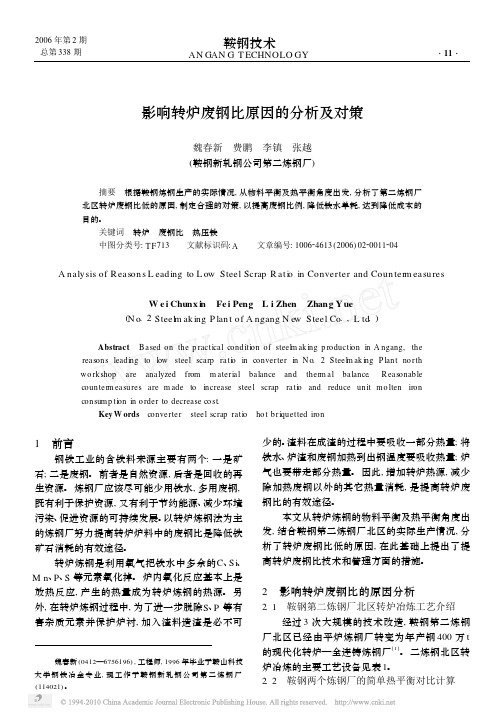
(1) 铁水的硅含量低 铁水硅含量的高低主要受分配铁水的高炉情 况的限制, 分配给二炼钢北区铁水的高炉都是大 高炉, 其铁水硅含量低于小高炉铁水。 (2) 铁水的温度低 供给第二炼钢厂北区铁水温度低的原因如 下: ① 运输时间长 铁水运到第二炼钢厂北区南端需要 1h, 运到 北端需要 2h, 比一炼钢和二炼钢南区的运输时间 都长。 铁水在运输过程中温降为 1℃ m in, 因此到 达第二炼钢厂北区的铁水温度低。 ② 三罐兑铁 二炼钢厂北区三罐兑铁, 兑铁时间长, 导致铁 水温降大。 第一炼钢厂和第二炼钢厂南区都是兑 一罐铁, 兑铁的温降小于二炼钢北区。 ③ 脱硫扒渣的比率大 脱硫扒渣操作引起铁损和温度损失, 每罐铁 水脱硫扒渣后平均温度至少损失 20℃ (实测)。 脱 硫扒渣操作对铁水的温度影响较大, 统计结果如 表3 所示。北区铁水的脱硫扒渣处理率比南区高, 铁损也比南区大。
大 学 钢 铁 冶 金 专 业, 现 工 作 于 鞍 钢 新 轧 钢 公 司 第 二 炼 钢 厂 (114021)。
少的。渣料在成渣的过程中要吸收一部分热量; 将 铁水、炉渣和废钢加热到出钢温度要吸收热量; 炉 气也要带走部分热量。 因此, 增加转炉热源, 减少 除加热废钢以外的其它热量消耗, 是提高转炉废 钢比的有效途径。
关键词 转炉 废钢比 热压铁 中图分类号: T F 713 文献标识码: A 文章编号: 100624613 (2006) 0220011204
A na lysis of R ea son s L ead ing to L ow Steel Scrap R a t io in Converter and Coun term ea su res
炼钢工—简答题 207

1.什么是溅渣护炉技术?答案:溅渣护炉技术是向炉渣中加入含MgO的造渣剂造粘渣补炉技术的基础上, 采用氧枪喷吹高压N2在2-4mm 内将出钢后留在炉内的残余炉渣喷溅涂敷在转炉内衬表面上,生成炉渣保护层的护炉技术。
2.炉渣来源何处?它在炼钢中起什么作用?答案:来源:(1)钢铁料中夹杂氧化的产物。
(2)造渣材料(石灰、白云石、萤石等)。
(3)冷却剂(氧化铁皮、矿石等)。
(4)被浸蚀和冲刷下来的炉衬耐火材料。
(5)各种原料带来的泥沙。
作用:(1)去夹杂(P、S);(2)传氧媒介;(3)清洁钢液;(4)对熔池保温;(5)影响金属损失;(6)影响炉衬浸蚀。
3.脱碳反应对炼钢过程的重要意义是什么?答案:(1)铁水中C氧化到钢种所要求的范围。
(2)氧化产生CO气泡对熔池起着循环搅拌作用,均匀钢液成份、温度, 改变各种化学反应的动力学条件。
(3)CO气泡有利于去除N2、H2等。
(4)利于非金属夹杂物上浮。
(5)提供炼钢的大部分热源。
(6)CO气泡使炉渣形成泡沫渣。
4.造成钢包回磷的原因是什么?如何防止?答案:原因:(1)出钢下渣;(2)脱氧产物SiO2;(3)氧含量降低。
防止措施:(1)挡渣出钢,尽量减少出钢带渣。
(2)采用碱性钢包或渣线部位用碱性材料。
(3)出钢过程中投入钢包中石灰粉。
(4)减少钢水在钢包中停留时间。
5.为什么兑铁时,有时会发生大喷?答案:因为转炉吹炼到终点,钢中氧含量和炉渣氧化性高, 留渣或未倒净的渣子和钢水,兑铁时炉内碳含量急剧增加且铁水温度低及钢水温度骤然下降, 促使碳氧反应剧烈进行在炉内产生强烈沸腾,如果兑铁水过猛且炉内残留钢渣较多就会大喷。
6.为什么转炉炼钢脱硫比脱磷困难?答案:碱性转炉渣中含有较高的(FeO),炉渣脱硫的分配比较低,降低了炉渣的脱硫能力,高(FeO)对脱磷工艺是一个相当有利的因素, 转炉炼钢条件下钢渣间磷的分配比较高, 一般可达100-400,而硫的分配比一般为6-15,此外,脱磷反应速度快,很快可达到平衡,而脱硫速度较慢,一般达不到平衡。
低铁耗条件下提高转炉废钢比的冶炼工艺研究
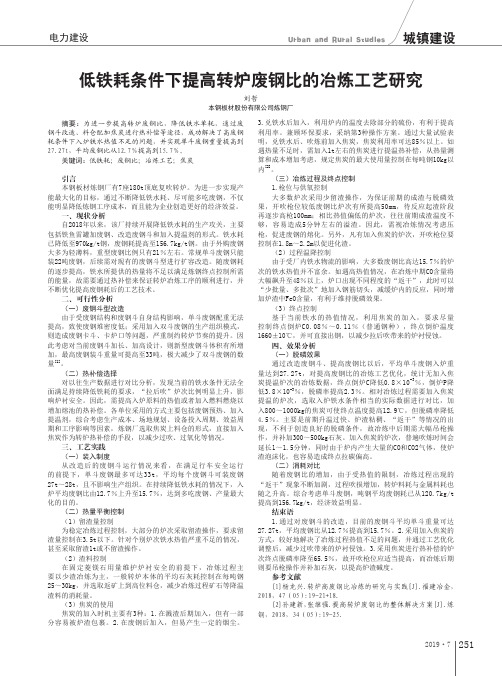
2512019·7摘要:为进一步提高转炉废钢比,降低铁水单耗,通过废钢斗改造、料仓配加焦炭进行热补偿等途径,成功解决了高废钢耗条件下入炉铁水热值不足的问题,并实现单斗废钢重量提高到27.27t,平均废钢比从12.7%提高到15.7%。
关键词:低铁耗;废钢比;冶炼工艺;焦炭引言本钢板材炼钢厂有7座180t顶底复吹转炉。
为进一步实现产能最大化的目标,通过不断降低铁水耗、尽可能多吃废钢,不仅能明显降低炼钢工序成本,而且能为企业创造更好的经济效益。
一、现状分析自2018年以来,该厂持续开展降低铁水耗的生产攻关,主要包括铁鱼雷罐加废钢、改造废钢斗和加入提温剂的形式。
铁水耗已降低至970kg/t钢,废钢耗提高至156.7kg/t钢。
由于外购废钢大多为轻薄料,重型废钢比例只有21%左右。
常规单斗废钢只能装22吨废钢,后续需对现有的废钢斗型进行扩容改造。
随废钢耗的逐步提高,铁水所提供的热量将不足以满足炼钢终点控制所需的能量,故需要通过热补偿来保证转炉冶炼工序的顺利进行,并不断优化提高废钢耗后的工艺技术。
二、可行性分析(一)废钢斗型改造由于受废钢结构和废钢斗自身结构影响,单斗废钢配重无法提高,致使废钢堆密度低;采用加入双斗废钢的生产组织模式,则造成废钢卡斗、卡炉口等问题,严重制约转炉节奏的提升。
因此考虑对当前废钢斗加长、加高设计,则新型废钢斗体积有所增加,最高废钢装斗重量可提高至33吨,极大减少了双斗废钢的数量[1]。
(二)热补偿选择对以往生产数据进行对比分析,发现当前的铁水条件无法全面满足持续降低铁耗的要求,“拉后吹”炉次比例明显上升,影响炉衬安全。
因此,需提高入炉原料的热值或者加入燃料燃烧以增加熔池的热补偿。
各单位采用的方式主要包括废钢预热、加入提温剂,综合考虑生产成本、场地规划、设备投入周期、效益周期和工序影响等因素,炼钢厂选取焦炭上料仓的形式,直接加入焦炭作为转炉热补偿的手段,以减少过吹、过氧化等情况。
降低铁耗提高废钢比措施

降低铁耗提高废钢比措施
一、优化生产工艺
1.采用高炉炼铁技术:高炉炼铁技术具有炉温高、炉渣碱度高、炉渣碱度稳定等优点,可以提高炉内还原反应速度,降低炉渣对铁的腐蚀,从而减少铁耗。
2.增加高温炉渣处理设备:通过增加高温炉渣处理设备,可以将废渣中的铁分离出来,提高废渣的回收利用率。
3.提高炼钢效率:通过提高炼钢工艺的效率,减少炼钢过程中的损耗,降低铁耗。
二、提高废钢回收利用率
1.完善废钢回收体系:建立完善的废钢回收体系,加强对废钢的收集、分类和回收利用工作,提高废钢回收利用率。
2.优化废钢处理工艺:采用先进的废钢处理设备,如废钢磁选机、废钢破碎机等,将废钢进行分离和加工,提高废钢的回收利用率。
3.加强废钢回收管理:加强对废钢回收企业的管理,严格监督废钢回收质量,确保回收的废钢符合要求,提高废钢的回收利用价值。
三、加强管理
1.优化原料配比:合理调整原料配比,降低铁耗,提高废钢比。
可以采用增加废钢用量、降低矿石用量、合理控制配料比例等方法。
2.加强生产过程控制:加强对生产过程的控制,确保生产工艺稳定,减少因操作不当导致的铁耗增加。
3.推广节能技术:采用节能技术,如余热回收利用、燃料替代等,降低能源消耗,减少铁耗。
4.加强员工培训:加强对员工的技术培训,提高员工的操作技能和意识,减少操作失误,降低铁耗。
通过上述措施,可以有效降低铁耗,提高废钢比,实现资源的有效利用。
同时,这些措施也有助于减少对自然资源的开采,降低环境污染,实现可持续发展。
因此,企业应加大对这些措施的研究和推广力度,不断优化生产工艺,提高废钢回收利用率,加强管理,实现降低铁耗和提高废钢比的目标。
浅谈提高转炉废钢比的措施

浅谈提高转炉废钢比的措施作者:汪培来源:《西部论丛》2019年第01期摘要:中国逐渐进入工业化后期,势必会降低对钢铁产品的需求,随着时间的推移,废钢可用量将接近甚至大于粗钢产量。
另外,废钢是可限循环利用的铁资源,提高转炉废钢比,有助于降低铁水消耗,将大幅降低环境污染和综合能耗,具有较高的经济、环保和社会效益。
所以,提高废钢比是历史发展的必然,同时也是钢铁企业发展的最佳选择。
本文主要对目前国内外成功应用的提高转炉废钢比的技术进行概述和比较,希望可以为相关从业者提供一些有价值的参考和借鉴。
关键词:转炉废钢比废钢加热近十年来,全球废钢比维持在35-40%的水平,平均在37%左右。
废钢比最高的为土耳其,达到85-90%的水平,发达国家中,美国的废钢比最高,在75%上下,波动较大。
欧盟也较高,大体在55~60%的水平,此外韩国平均也能达到50%左右。
中国由于“地条钢”的存在扰乱了废钢市场,造成转炉废钢比偏低,不仅浪费转炉热量,而且使吨钢综合能耗大幅上升,环境污染严重。
2016年国内炼钢废钢比为11%,2017年我国政府严厉打击地条钢,淘汰1~1.5亿吨落后产能,短期内使废钢市场价格大幅跌落,也使各钢厂开始大幅增加转炉废钢比,2017年国内废钢比约为17%。
虽然2017年国内转炉炼钢废钢比大幅增加,但仍有很大的提升空间,如果不进行热补偿,仅通过向转炉多加废钢的方式增加废钢比,范围极其有限,以湘钢五米板厂为例,极限情况下转炉综合废钢比也才25%。
目前国内外利用热补偿成功应用的增加转炉废钢比的方法主要有:炉气二次燃烧、熔池增碳、废钢预热。
一、炉气二次燃烧二次燃烧的思路是利用炉气中的CO二次燃烧放热加热金属熔池,随着当前新型二次燃烧氧枪的发展,二次燃烧效率有了明显提高。
新型二次燃烧氧枪通过对枪体及出口处新型设计,提高了喷出氧气与脱碳反应产生的CO之间的反应效率,将产生更多的二次燃烧热。
提高CO 的二次燃烧有助于增加炉内热量,其效果与炉子大小、二次燃烧氧枪类型有关。
转炉炼钢工艺

转炉炼钢工艺转炉炼钢工艺绪论1、转炉炼钢法的分类转炉是以铁水为主要原料的现代炼钢方法。
该种炼钢炉由圆台型炉帽、圆柱型炉身和球缺型炉底组成。
炉身设有可绕之旋转的耳轴,以满足装料和出钢、倒渣操作,故而得名。
酸性空气底吹转炉——贝塞麦炉〔英国1856年〕空气转炉{ 碱性空气底吹转炉——托马斯炉〔德国1878年〕碱性空气侧吹转炉〔中国1952年〕转炉{ 氧气顶吹转炉——LD〔奥地利1952年〕氧气转炉{ 氧气底吹转炉——OBM〔德国1967年〕顶底复吹转炉〔法国1975年〕2、氧气顶吹转炉炼钢法简介(1) 诞生的布景及简称现代炼钢出产首先是一个氧化精炼过程,最初的贝氏炉和托马斯炉之所以采用空气吹炼正是操纵此中的氧。
二次世界大战以后,工业制氧机在美国问世,使操纵纯氧炼钢成为可能,但本来的底吹方式炉底及喷枪极易烧坏。
美国联合碳化物公司于1947年在尝试室进行氧气顶吹转炉的尝试并获成功,定名为BOF。
奥地利闻之即派有关专家前往参不雅学习,回来后于1949年在2吨的转炉长进行半工业性尝试并获成功,1952年、1953年30吨氧气顶吹转炉别离在Linz和Donawitz建成投产,故常简称LD。
1967年12月德国与加拿大合作缔造了氧气底吹转炉,使用双层套管喷嘴并通以气态碳氢化合物进行冷却。
1975年法国研发了顶底复吹转炉,综合了LD和OBM的长处,77年在世界年会上颁发。
(2) 氧气顶吹转炉的特点1〕长处氧气顶吹转炉一经问世就显示出了极大的优越性,世界各国竟相开展,目前成为最主要的炼钢法。
其长处主要暗示在:〔1〕熔炼速度快,出产率高〔一炉钢只需20分钟〕;〔2〕热效率高,冶炼中不需外来热源,且可配用10%~30%的废钢;〔3〕钢的品种多,质量好〔上下碳钢都能炼,S、P、H、N、O及夹杂含量低〕;〔4〕便于开展综合操纵和实现出产过程计算机控制。
2〕错误谬误当然,LD尚存在一些问题,如吹损较高〔10%,〕、所炼钢种仍受必然限制〔冶炼含大量难熔元素和易氧化元素的高合金钢有必然的困难〕等。
转炉炼钢最佳废钢比计算模型

转炉炼钢最佳废钢比计算模型
转炉炼钢最佳废钢比计算模型,是指根据物料的成分、生铁的品位及转炉各项参数,结合钢(炉)冶金炉料理论、渣金属生成理论及冶炼过程热力学规律量化计算,确定转炉作业期间最佳的废钢比的一种模型。
该模型采用计算机程序对转炉炼钢过程的各个过程参数进行优化设计,能够模拟转炉实际运行状况,根据实际生产要求,从正负公差范围内,变更物料计量、空气30N、有效铁水比、钢水温度等参数,设置优化计算目标,在优化计算中能够对原料煤块、铁水、废钢比等数据做最佳调整,以此达到最佳钢(炉)冶金效果。
炼钢与连铸若干新技术
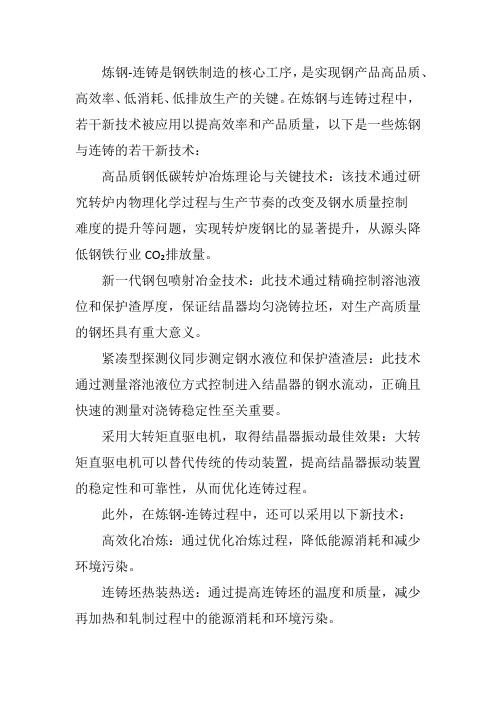
炼钢-连铸是钢铁制造的核心工序,是实现钢产品高品质、高效率、低消耗、低排放生产的关键。
在炼钢与连铸过程中,若干新技术被应用以提高效率和产品质量,以下是一些炼钢与连铸的若干新技术:高品质钢低碳转炉冶炼理论与关键技术:该技术通过研究转炉内物理化学过程与生产节奏的改变及钢水质量控制难度的提升等问题,实现转炉废钢比的显著提升,从源头降低钢铁行业CO₂排放量。
新一代钢包喷射冶金技术:此技术通过精确控制溶池液位和保护渣厚度,保证结晶器均匀浇铸拉坯,对生产高质量的钢坯具有重大意义。
紧凑型探测仪同步测定钢水液位和保护渣渣层:此技术通过测量溶池液位方式控制进入结晶器的钢水流动,正确且快速的测量对浇铸稳定性至关重要。
采用大转矩直驱电机,取得结晶器振动最佳效果:大转矩直驱电机可以替代传统的传动装置,提高结晶器振动装置的稳定性和可靠性,从而优化连铸过程。
此外,在炼钢-连铸过程中,还可以采用以下新技术:高效化冶炼:通过优化冶炼过程,降低能源消耗和减少环境污染。
连铸坯热装热送:通过提高连铸坯的温度和质量,减少再加热和轧制过程中的能源消耗和环境污染。
近终形化生产:通过采用先进的工艺和技术,生产更小断面的连铸坯,提高成材率和生产效率。
精确控制结晶器液面和保护渣厚度:通过精确控制结晶器液面和保护渣厚度,提高连铸坯的质量和稳定性。
电磁搅拌技术:通过采用电磁搅拌技术,改善连铸坯的凝固过程,提高产品质量和生产效率。
自动化的物流系统:通过采用先进的物流系统和技术,实现生产过程中物料的自动化运输和跟踪管理,提高生产效率和产品质量。
高效节能的轧制技术:通过采用高效节能的轧制技术,降低轧钢过程中的能源消耗和提高产品质量。
环保型轧制工艺:通过采用环保型轧制工艺和技术,减少轧钢过程中的环境污染和资源浪费。
集成化工艺控制技术:通过采用集成化工艺控制技术,将炼钢、连铸和轧制等工艺过程进行优化和控制,提高生产效率和产品质量。
这些新技术的应用可以显著提高炼钢-连铸生产的效率和产品质量,同时降低能源消耗和环境污染。
- 1、下载文档前请自行甄别文档内容的完整性,平台不提供额外的编辑、内容补充、找答案等附加服务。
- 2、"仅部分预览"的文档,不可在线预览部分如存在完整性等问题,可反馈申请退款(可完整预览的文档不适用该条件!)。
- 3、如文档侵犯您的权益,请联系客服反馈,我们会尽快为您处理(人工客服工作时间:9:00-18:30)。
√ 5
20~40求低 出混铁炉 1340 积铁少,铁 温稳定 混铁炉 1260~1290 来铁折后 1210~1400 混铁炉大、侧 兑温降大,铁 水多积压铁温 不稳定
√ 4
20~22分钟 27~30分钟 单线3个 单线3个 双线6个 双线6个 无 无 连铸四流: 1640~1650 1640~1650 1580~1585 1580~1585 足量供应降温废钢
废钢消耗指标考察对标
XXXPKXX,X
项 目 一、原料消耗指标 钢铁料 铁水 废钢 自产废钢 生铁块 渣钢 钢渣粉 二、渣料消耗指标 白灰 轻烧白云石 镁球 石子 白云石子 烧结矿返粉 红矿 三、铁水情况 铁包 一罐到底 全进混铁炉 一半折包 一半进混铁炉 XXX 1082 859 223 * * * * 36.87 * 7.76 4.33 * * 1.96 XX 1062 947 57 0 58 9.19 14.76 16.95/37.09 0 * 当日0/15.19 18.69 16.95/28.04 * 改进点 目标和措施 √ 1 1、铁水消耗950/900/850kg 1062 综合废钢消耗100/150/200kg 含生铁块15~30kg,自产废钢 1002 5~10kg,相应钢铁料消耗指标由1055调 56.60/39.36 整为1075/1080/1085kg,具体指标可由生 6.98 产稳定、体系相对平衡后确定。 13.7 废钢类型为重废,渣钢毛铁等自循环 18.46 较少,钢渣粉均送烧结使用 4.74 √ 2 2、渣料结构调整:白灰+镁球,少量石 31.22 子降温、少量烧结矿返粉化渣/降温 21.84 × 基本原则:降温大的不加少加,采用 * √ 镁球代替轻烧白云石减少温降,石子、 烧结矿不用少用 √ 0/累计1.82 0/6.11 × 26.41/34.30 √ * √ 3 3、改造铁包实施一罐制,来铁不合则进 混铁炉,如铁量、成分硅锰硫、温度, 应对3座转炉生产,尤为重要;需提前做 两件工作,一是改铁包嘴可兑转炉,二 是出铁轨道在线称重、铁包准确控重满 足转炉直接兑铁、一次性入炉要求 4、适当提高硅数不过低,快速消铁不积 压,要求: Si30~40,混铁炉1300~1350用好煤气 烘烤,合理存量400~600吨,折包后温度 1300~1350,折前1350~1400。 提高存铁和入炉铁水温度40~50℃,可 提高废钢消耗40~50kg,目前裕华铁况, 较合信一罐制入炉少加入70~100kg废钢 量,即综合废钢消耗可150~180kg 5、推行双线减包方案,双线5个钢包运 转,减少出钢温降,降低出钢温度 / 出钢温降高10~20℃,钢包温降大,上钢 温度相当,钢包-连铸系统温降基本相当 不暴吹、不延时降温 X
混铁炉 检修未投,倾向常用
பைடு நூலகம்
Si含量 30~40不过低保热量 铁水温度 混铁炉1300~1330 来铁包1350~1370 混铁炉小、直兑温降 小,铁水少不积压铁温 稳定 XX铁水到厂1260,单 炉8吨合182kg,低的 1110,废钢量加不进去 冶炼周期26~30分钟 四、钢包周转 单线2个 双线5个 在线烘烤 有,未投用 五、温度制度 1620~1640℃ Q235出钢温度 1580~1585℃ Q235氩后温度 氩站调温 吹氩加废钢不浪费热量