超声振动切削的优势特点及应用范围
超声波加工技术

比方:采用超声波与电化学加工相结合的方法加 工喷油嘴、喷丝板上的小孔或窄缝,能极大的 进步加工速度和加工质量。
4、超声波清洗
超声波清洗的原理主要是利用超声波频振动在 液体中产生的交变冲击波和空化作用。
空化效应产生的强烈冲击波,产生的空化气泡 浸透到污物与被清洗部位外表之间,促使污物 脱落;
四、超声波加工的应用:
1、型孔、型腔加工
a)加工微细孔; b)加工型腔;c)加工异形孔
套料;
切圆;
复杂沟槽
弯曲孔;
刻槽
2、切割加工 超声精细
切割半导体、 铁氧体、石英、 宝石、陶瓷、 金刚石等硬脆 材料,
a)切片;b)多个圆片落料;c)多片圆板落料 ;d〕切割单晶硅片
3、复合加工
超声波加工与其它加工方法相结合。 利用超声波加工硬质合金、耐热合金等金属材料
整个振动系统的联接部分应接触严密,否则 超声波传递过程中将损失很大能量。在螺纹 联接处应涂以凡士林油,绝不可存在空气间 隙,因为超声波通过空气时会很快衰减。
3 、机床本体
CSJ-2型超声波加工机床 l--工作台;2--上具;3--变幅杆;4--换能器 5--导轨;6--支架;7--平衡重锤
4、 磨料工作液及其循环系统
二、超声加工的特点
1〕合适加工各种硬脆材料,尤其是玻璃、陶 瓷、宝石、石英、锗、硅、石墨等不导电的 非金属材料。也可加工淬火钢、硬质合金、 不锈钢、钛合金等硬质或耐热导电的金属材 料,但加工效率较低。
二、超声加工的特点
1〕合适加工各种硬脆材料,尤其是玻璃、陶瓷、宝石、石 英、锗、硅、石墨等不导电的非金属材料。也可加工淬火钢、 硬质合金、不锈钢、钛合金等硬质或耐热导电的金属材料, 但加工效率较低。 2〕由于去除工件材料主要依靠磨粒瞬时部分的冲击作用, 故工件外表的宏观切削力很小,切削应力、切削热更小,不 会产生变形及烧伤,外表粗糙度也较低,可达Ra0.630.08um,尺寸精度可达正负0.03mm,也适于加工薄壁、 窄缝、低刚度零件。 3〕工具可用较软的材料、做成较复杂的形状,且不需要工 具和工件作比较复杂的相对运动,便可加工各种复杂的型腔 和型面。一般,超声加工机床的构造比较简单,操作、维修 也比较方便。 4〕超声加工的面积不够大,而且工具头磨损较大,故消费 率较低。
探讨超声在材料中的作用和效应
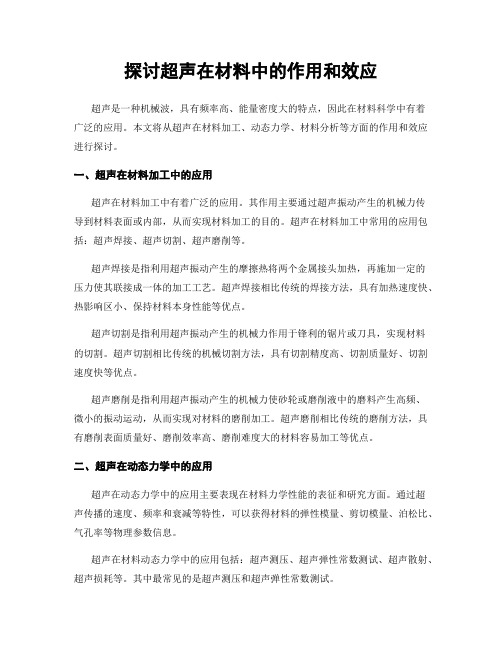
探讨超声在材料中的作用和效应超声是一种机械波,具有频率高、能量密度大的特点,因此在材料科学中有着广泛的应用。
本文将从超声在材料加工、动态力学、材料分析等方面的作用和效应进行探讨。
一、超声在材料加工中的应用超声在材料加工中有着广泛的应用。
其作用主要通过超声振动产生的机械力传导到材料表面或内部,从而实现材料加工的目的。
超声在材料加工中常用的应用包括:超声焊接、超声切割、超声磨削等。
超声焊接是指利用超声振动产生的摩擦热将两个金属接头加热,再施加一定的压力使其联接成一体的加工工艺。
超声焊接相比传统的焊接方法,具有加热速度快、热影响区小、保持材料本身性能等优点。
超声切割是指利用超声振动产生的机械力作用于锋利的锯片或刀具,实现材料的切割。
超声切割相比传统的机械切割方法,具有切割精度高、切割质量好、切割速度快等优点。
超声磨削是指利用超声振动产生的机械力使砂轮或磨削液中的磨料产生高频、微小的振动运动,从而实现对材料的磨削加工。
超声磨削相比传统的磨削方法,具有磨削表面质量好、磨削效率高、磨削难度大的材料容易加工等优点。
二、超声在动态力学中的应用超声在动态力学中的应用主要表现在材料力学性能的表征和研究方面。
通过超声传播的速度、频率和衰减等特性,可以获得材料的弹性模量、剪切模量、泊松比、气孔率等物理参数信息。
超声在材料动态力学中的应用包括:超声测压、超声弹性常数测试、超声散射、超声损耗等。
其中最常见的是超声测压和超声弹性常数测试。
超声测压是指利用超声波在材料中传播的速度和频率与材料的应力和压力相关联,从而实现对材料内部应力和压力的非破坏性检测。
超声测压广泛应用于金属材料、混凝土材料等领域的结构健康监测和质量检测。
超声弹性常数测试是指利用超声波在材料中传播的特性和材料的力学性质相关联,从而实现对材料弹性常数的测量。
通过超声弹性常数测试,可以获得材料的弹性模量、剪切模量、泊松比等力学参数,提高材料性能的研究和开发的效率。
旋转超声加工
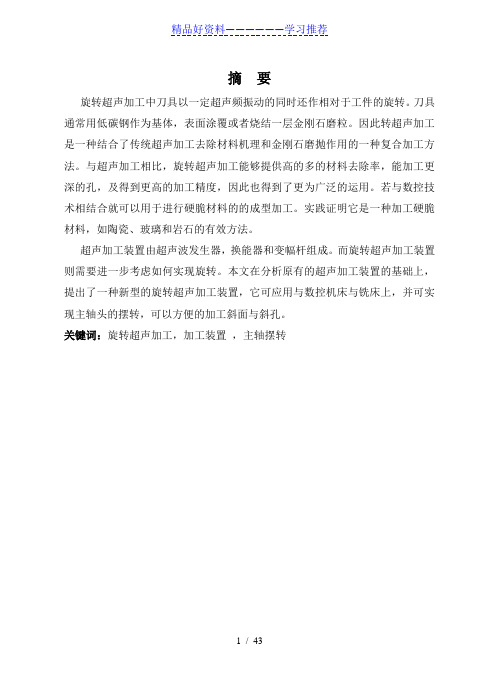
摘要旋转超声加工中刀具以一定超声频振动的同时还作相对于工件的旋转。
刀具通常用低碳钢作为基体,表面涂覆或者烧结一层金刚石磨粒。
因此转超声加工是一种结合了传统超声加工去除材料机理和金刚石磨抛作用的一种复合加工方法。
与超声加工相比,旋转超声加工能够提供高的多的材料去除率,能加工更深的孔,及得到更高的加工精度,因此也得到了更为广泛的运用。
若与数控技术相结合就可以用于进行硬脆材料的的成型加工。
实践证明它是一种加工硬脆材料,如陶瓷、玻璃和岩石的有效方法。
超声加工装置由超声波发生器,换能器和变幅杆组成。
而旋转超声加工装置则需要进一步考虑如何实现旋转。
本文在分析原有的超声加工装置的基础上,提出了一种新型的旋转超声加工装置,它可应用与数控机床与铣床上,并可实现主轴头的摆转,可以方便的加工斜面与斜孔。
关键词:旋转超声加工,加工装置,主轴摆转AbstractRotary ultrasonic machining superimpose rotational movement on the tool head that vibrates simultaneously at ultrasonic freqency .The tool is made of mild steel coated or bonded with diamond abrasive.so is a hybrid machining process which combines the material removal mechanisms of conventional ultrasonicmachining and diamond pared with ultrasonic machining ,it can provide a much high material removol,deep holes,and fine precision,which leads to its further application. And it has been proved to be a promising and cost-effective machining method or hard and brittle materials, such as engineering ceramic, glass, stone,.Ultrasonic machining equipment consists of ultrasonic generator,transducer and horn.Rotary ultrasonic machining need to consider how to realize the rotate of the device.In this paper ,I analyse the device which have be designed,and put forward a newt vibrating system of rotary ultrasonic machiningequipment.It can be assembled on the numerical control machine, vertical milling machine. And it also can realize the wiggle of the device,in order to machine inclined hole and face conveniently.KEY WORDS:rotary ultrasonic machining process device spindle swinging目录第1章绪论51.1超声加工的提出及其分类51.2超声振动装置及机床的研制进展61.3选题的目的、意义及工作任务91.3.1选题的目的、意义91.3.2课题主要工作内容及任务111.1本章小结12第2章旋转超声加工装置的总体设计132.1超声波加工原理及其特性132.2旋转超声加工的基本原理152.2.1 超声振动的捶击作用152.2.2 金刚石工具的磨抛作用162.2.3 超声空化作用162.2.4液压冲击和旋转运动促进了碎屑的排出162.3旋转超声振动加工装置的主要组成172.3.1 超声波发生器172.3.2超声换能器192.3.3超声变幅杆202.4 各组成部分的连接与固定222.4.1变幅杆和换能器的连接222.4.2变幅杆的固定232.4.3超声波发生器与超声振动系统的连接232.5旋转超声振动系统的设计232.5.1对已有的超声加工装置进行分析242.5.2旋转超声加工机构装置结构上的实现方法272.5.3 旋转超声加工装置的整体结构的初步设计273.6本章总结28第3章旋转超声加工装置细节性设计计算293.1已知条件:293.2超声换能器设计293.2.1压电陶瓷片的设计293.2.2前后盖板的选材303.2.3夹心式换能器计算313.3变幅杆设计323.3.1 变幅杆的材料323.3.2变幅杆参数设计333.3.3连接及定位方式设计383.4内外桶,端盖及密封装置设计393.4.1 内外筒设计393.4.2端盖及密封装置的设计393.4.3 法兰盘设计393.5主轴的设计403.6主轴头摆转功能实现的设计41 致谢42参考文献:431.绪论1.1超声加工的提出及其分类随着生产发展和科学实验的需要,很多工业部门,尤其是宇航、国防工业部要求产品向高精度、高速度、高温、高压、大功率、小型化等方向发展,所用的材料愈来愈难加工,如硬质合金、钛合金、耐热钢、不锈钢、淬硬钢、金刚石、宝石、石英以及钨、硅等各种高硬度、高强度、高韧性、高脆性的金属及非金属材料的加工;工件形状愈来愈复杂,精度、表面租糙度和某些特殊要求也愈来愈高。
超声波切割刀原理

超声波切割刀原理
超声波切割刀是利用超声波振荡波的高频振动冲击作用,达到切割材料的目的。
超声波切割刀由振盘、转换器、增强器和刀具组成。
超声波切割刀的原理是将交变电压信号传送到振盘上,振盘会因谐振产生固有频率的振动,把机械振动能量传递给转换器,再转换成高频振荡波。
经过增强器的放大,最终通过刀具的角度调整和材料之间的接触面,将能量释放到切割部位。
超声波切割刀的优点是可精确控制切割线路。
传统的机械切割方式容易产生失误和浪费,而超声波切割刀不仅可以达到精确的切割效果,还能减少材料的浪费和污染。
超声波切割刀的切割速度和效率高。
由于超声波振动产生的能量大,一次性可以切割多个材料。
而且,它可以轻松切割各种类型的材料,包括塑料、橡胶、纸、织物、食品等。
超声波切割刀没有热变形。
由于切割是通过冲击力完成的,不会产生热能,因此不会导致材料局部变形。
这对于需要保持材料精度的行业如医疗、精密机械、刀具等至关重要。
超声波切割刀是一种高效的切割工具,其原理和应用已被广泛应用于各个行业,如医疗、汽车、电子和纺织等高精度和高效率的制造领域。
超声波切割机工作原理

超声波切割机工作原理超声波切割机是一种利用超声波振动原理进行切割的设备。
它利用超声波的高频振动产生的能量,将切割刀具传递给被切割物体,从而实现高精度、高效率的切割作业。
超声波切割机主要由发生器、换能器、切割刀具和控制系统组成。
下面将详细介绍每个部分的工作原理。
1. 发生器:发生器是超声波切割机的核心部件,它能够将电能转化为超声波振动能。
发生器通过电路将交流电能转化为高频电能,并将其传送给换能器。
2. 换能器:换能器是将发生器输出的高频电能转化为机械振动能的装置。
它由压电陶瓷和金属块组成。
当发生器输出高频电能时,压电陶瓷会产生压电效应,使其振动。
振动的压电陶瓷会传递给金属块,从而产生机械振动。
这种机械振动就是超声波振动,其频率通常在20kHz到40kHz之间。
3. 切割刀具:切割刀具是超声波切割机的切割工具,它由振动刀片和固定刀片组成。
振动刀片通过换能器传递的超声波振动能,将其转化为切割能量。
固定刀片则用于夹持被切割物体,使其与振动刀片接触。
4. 控制系统:控制系统是超声波切割机的智能化部分,它通过对发生器和换能器的控制,实现对切割过程的调节和监控。
控制系统可以根据切割物体的性质和要求,调整超声波的频率、振幅和切割速度等参数,以达到最佳的切割效果。
超声波切割机的工作原理可以总结为以下几个步骤:1. 发生器产生高频电能,并传送给换能器。
2. 换能器将高频电能转化为超声波振动能,并传递给振动刀片。
3. 振动刀片通过与固定刀片接触,将超声波振动能转化为切割能量。
4. 切割能量将被切割物体切割或分离。
5. 控制系统对切割过程进行监控和调节,以实现最佳的切割效果。
超声波切割机具有以下优点:1. 高精度:超声波振动频率高,切割精度可达到微米级别。
2. 高效率:超声波切割速度快,可以大幅提高切割效率。
3. 无热变形:超声波切割过程中,切割区域几乎不会受到热影响,避免了热变形问题。
4. 适用范围广:超声波切割机适用于各种硬度和脆性材料的切割,如金属、塑料、陶瓷等。
超声波切割刀原理

超声波切割刀原理
超声波切割刀是一种利用超声波振动来实现切割的设备。
其原理是利用高频振动产生的机械波能够聚焦到刀刃上,形成高能密度区域,从而实现对各种材料的切割。
超声波切割刀主要由发生器、换能器、振动系统、夹具、切割刀等组成。
发生器将电能转化为高频电信号,通过换能器将电信号转化为高频机械振动,振动传到切割刀上,使其在切割时产生高能密度区域。
超声波切割刀的切割效果非常优异,可用于各种材料的切割,如金属、陶瓷、玻璃、塑料等。
同时,超声波切割刀具有精度高、效率高、对材料无损伤等优点,广泛应用于医疗、电子、机械等行业。
- 1 -。
振动切削加工技术

• 振动切削的分类
按振动质量:自激振动切削和强迫振动切削
按刀具振动方向:吃刀抗力方向、进给抗力 方向、主切削方向 按所加频率:高频振动和低频振动
• 普通切削与振动切削的对比
-------普通切削中,切削靠刀具与工具的相对 运动来完成。产生较大切削力,使刀具磨损、 产生切削振动的有害现象。 --------振动切削中,在切削刀具上施加某种有 规律的可控的振动,使切削速度、切削深度 产生周期性的改变,从而使切削力减小、切 削热降低。
• 振动切削的特点
1、切削力大大减小 2、切削温度明显降低 3、切削液的作用得到了充分发挥 4、可提高刀具使用寿命 5、可控制切屑的形状和大小 6、提高加工精度和表面质量 7、可提高已加工表面的耐磨性和耐蚀性
• 振动切削技术的应用
1、难切削材料的加工。如:不锈钢、钛合金、 陶瓷、玻璃等采用超声振动切削来大大降低加 工难度;加工石墨与氧化铝等材料只有采用超 声振动才能产生微粒式的切削分离得到整齐的 加工表面
金刚石刀具可以切削含铁工件
振动切削加工技术
振动加工技术是从20世纪60年代发展起来的 一种优于普通切削的先进的制造技术。
• 它通过在常规的切削刀具上施加高 频振动,使刀具和工件发生间断性 的接触。改变了工件与刀具之间的 时间与空间分配,从而改变了切削 加工机理达到了减小切削力和切削 热并提高加工质量和效率的目的。
2、难加工零件的切削加工
如易弯曲变形的细长杆类零件、薄壁零件、排屑断屑比较困难的切削加工 如用于钻孔、饺孔、攻丝、拉削等
Thank you!
振动切削技术特点及其应用研究

( . oeeo mm n ai ahnr n il ni en S uh e fr t nvrt, u mi un n 52 4 C i 1 Clg c u i t nm ci yadc iegn r g, otws o syu i sy K n n Y na 6 0 2 , hn l fo c o e v e i t er ei g a; 2 Sho o eh n a n p w r n i e n , e npl eh iu i rt, iou ea 4 4 0 , hn ) . colfm ca i l d o e gn r g H n o t n n esy J zoH n n 50 0 C i c a e ei a yc c v i a a
1 前
言
和摩擦 作用 , 将不 可 避 免 地产 生 较 大 的切 削 力 , 高 较
振 动 切削加 工 是 2 O世 纪 6 0年 代 发 展 起来 的一 种先进 制 造技术 , 通过 在常规 的切削刀 具上 施加 高 它
的切削温度, 使刀具产生磨损 和切削振动等有 害现 象 。普 通 切削 如图 1所示 。
Fe u e fv br i n a h n ng t c at r s o i ato m c i i e hnoog d e e r h o t plc to l y an r s a c f r is ap ia n i
W a ng— b a ,U u Chu n — s a ,Ya n —f ng Yi io a ho ng Yo g a
31振动切削的特点4振动切削技术的应用振动切削可以使切削力大幅度降低使摩擦热减振动切削技术是在研究切削加工本质的基础上小刀具耐用度提高已加工表面粗糙度减少它有以所提出的一种精密加工方法它弥补了普通切削加工下特点
- 1、下载文档前请自行甄别文档内容的完整性,平台不提供额外的编辑、内容补充、找答案等附加服务。
- 2、"仅部分预览"的文档,不可在线预览部分如存在完整性等问题,可反馈申请退款(可完整预览的文档不适用该条件!)。
- 3、如文档侵犯您的权益,请联系客服反馈,我们会尽快为您处理(人工客服工作时间:9:00-18:30)。
超声振动切削的优势特点及应用范围
一、超声波振动切削
振动切削是20世纪60年代发展起来的一种先进制造技术,它
通过在常规的切削刀具上施加高频振动,使刀具和工件发生间断性的
接触,从而使传统切削模式发生了根本性的变化。由此变化解决了传
统的切削加工中固有的难题,如切削中的振动和切削热变形等,从而
得到了优良的切削效果。
超声波振动切削能改善零超声振动切削技术,是把超声波振动的
力有规律地加在刀具上,使刀具周期性地切削和离开工件的加工技
术,是结合超声波技术和传统切削工艺的一种新型切削技术。
工件加工表面质量与加工精度,能延长刀具寿命、提高切削效率、
扩大切削加工应用范围,可广泛地用于车、刨、铣、磨、螺纹加工及
不锈钢、淬硬钢、高速钢、钛合金、高温合金、冷硬铸铁以及陶瓷、
玻璃、石材等非金属材料加工等。
二、超声波振动切削原理
超声振动切削,是使刀具以20-40KHz的频率,沿切削方向高速振
动的一种特种切削技术。超声振动切削从微观上看是一种脉冲切削,
在一个振动周期中,刀具的有效切削时间很短,一个振动周期内绝大
部分时间里刀具与工件切屑完全分离,刀具与工件切屑断续接触,切
削热量大大减少,并且没有普通切削时的“让刀”现象。利用这种振
动切削,在普通机床上就可以进行精密加工,圆度、圆柱度、平面度、
平行度、直线度等形位公差主要取决于机床主轴及导轨精度,最高可
达到接近零误差,使以车代磨、以钻代铰、以铣代磨成为可能。与高
速硬切削相比,不需要过高的机床刚性,并且不破坏工件表面组织,
在曲线轮廓零件的精加工中,可以借助数控车床、加工中心等进行仿
形加工,可以节约高昂的数控磨床购置费用。
超声波振动切削用于各种难以磨削而对表面质量及精度要求较
高的零件的精加工,具有很大的优越性。超声波振动切削装置由超声
波发生器、换能器、变幅杆及刀具等四部分组成,由超声波发生器发
出的高频电讯号经换能器转化为高频机械振动,再由变幅杆将振动的
振幅放大并施加到道具上,一般将换能器与变幅杆组成的部件称为声
学头。
三、超声振动切削的优势特点
1.切削力小,约为普通刀具切削力的1/3—1/10;
2.加工精度高;
3.切削温度低,工件保持室温状态;
4.不产生积屑瘤,工件变形小,没有毛刺;
5.粗糙度低,可接近理论粗糙度值;
6.被加工零件的“刚性化”,即与普通切削相比,相当于工件刚
性提高;
7.加工过程稳定,有效消除颤振;
8.切削液的冷却,润滑作用提高;
9.刀具耐用度呈几倍到几十倍提高;
10.工件表面呈压应力状态,耐磨性、耐腐蚀性提高;
11.切削后的工件表面呈彩虹效果。
四、超声振动切削的应用范围
(一)难切削材料的加工
不锈钢、淬硬钢、高速钢、钛合金、高温合金、冷硬铸铁以及陶
瓷、玻璃、石材等非金属材料,由于力学、物理、化学等特性而难以
加工,如采用超声振动切削则可化难为易。
(二)难加工零件的切削加工
如易弯曲变形的细长轴类零件、小径深孔、薄壁零件、薄盘类零
件与小径精密螺纹以及形状复杂、加工精度与表面质量要求又较高的
零件。
(三)高精度、高表面质量工件的切削加工
(四)排屑、断屑比较困难的切削加工
五、超声振动切屑的应用领域
广泛应用于航空、航天、军工等领域。