汽车轮毂的制造工艺
轮毂设计标准要求规范有哪些

轮毂设计标准要求规范有哪些
轮毂是指汽车车轮的金属辅助的部分,一般由钢铁材料制成。
轮毂的设计标准要求规范主要包括以下几个方面:
1. 轮毂的尺寸标准:轮毂的尺寸应符合相应的标准规范,包括轮毂的直径、宽度、孔径等尺寸要求。
这些尺寸要求主要是为了确保轮毂能够与车轮匹配,保证安全可靠的运行。
2. 材料要求:轮毂一般由钢铁材料制成,所以需要符合相应的材料标准要求。
对于材料的选择要求有强度高、韧性好、耐腐蚀等特性。
3. 轮毂的工艺要求:轮毂的制造过程需要符合一系列的工艺要求,包括热处理、铸造、焊接等工艺。
这些工艺要求主要是为了保证轮毂的结构强度、耐久性和可靠性。
4. 轮胎安装要求:轮毂与轮胎的安装要求也需要符合相应的标准规范,确保轮毂与轮胎完全契合,防止轮胎在行驶过程中出现脱落、爆胎等安全问题。
5. 表面处理要求:轮毂的表面处理通常包括喷涂、电镀等工艺,这些工艺的要求主要是为了增加轮毂的美观性、抗腐蚀能力和耐久性。
6. 轮毂的检测标准:轮毂在制造过程中需要进行各种质量检测,以确保其质量合格。
常见的检测项目包括外观检查、尺寸测量、材料检测、力学性能测试等。
7. 安全性能要求:轮毂作为汽车的关键部件之一,其安全性能要求尤为重要。
轮毂在设计、制造和使用过程中必须符合相应的安全标准要求,以确保车辆行驶的安全可靠。
综上所述,轮毂设计标准要求规范包括轮毂的尺寸标准、材料要求、工艺要求、轮胎安装要求、表面处理要求、检测标准和安全性能要求等方面。
这些标准规范的制定和执行,有助于提高轮毂的质量和可靠性,确保汽车行驶的安全。
《汽车轮毂用A356铝合金的精炼及净化》范文
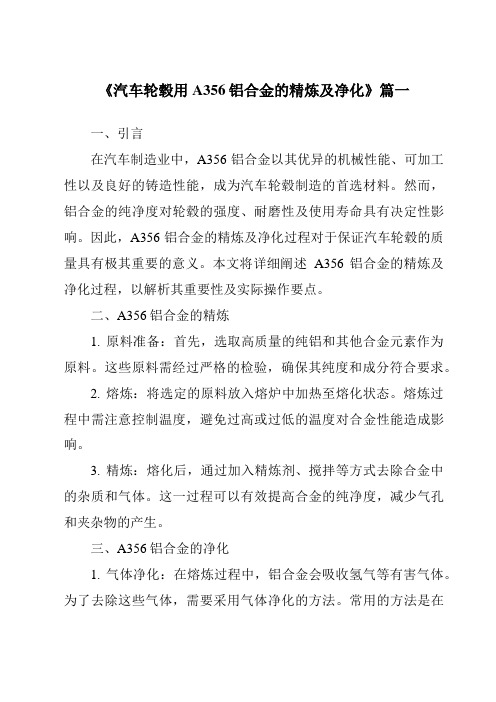
《汽车轮毂用A356铝合金的精炼及净化》篇一一、引言在汽车制造业中,A356铝合金以其优异的机械性能、可加工性以及良好的铸造性能,成为汽车轮毂制造的首选材料。
然而,铝合金的纯净度对轮毂的强度、耐磨性及使用寿命具有决定性影响。
因此,A356铝合金的精炼及净化过程对于保证汽车轮毂的质量具有极其重要的意义。
本文将详细阐述A356铝合金的精炼及净化过程,以解析其重要性及实际操作要点。
二、A356铝合金的精炼1. 原料准备:首先,选取高质量的纯铝和其他合金元素作为原料。
这些原料需经过严格的检验,确保其纯度和成分符合要求。
2. 熔炼:将选定的原料放入熔炉中加热至熔化状态。
熔炼过程中需注意控制温度,避免过高或过低的温度对合金性能造成影响。
3. 精炼:熔化后,通过加入精炼剂、搅拌等方式去除合金中的杂质和气体。
这一过程可以有效提高合金的纯净度,减少气孔和夹杂物的产生。
三、A356铝合金的净化1. 气体净化:在熔炼过程中,铝合金会吸收氢气等有害气体。
为了去除这些气体,需要采用气体净化的方法。
常用的方法是在熔炉中通入惰性气体(如氩气),通过置换熔融金属中的气体,将氢气等有害气体从金属中排出。
2. 机械净化:通过离心分离机等设备对熔融金属进行离心分离,进一步去除杂质和夹杂物。
离心分离可以有效分离密度较大的夹杂物和颗粒物,提高合金的纯净度。
四、精炼及净化过程中的注意事项1. 控制温度:在精炼及净化过程中,需严格控制温度。
过高的温度可能导致合金元素挥发,影响合金性能;过低的温度则可能导致精炼及净化效果不佳。
2. 添加适量精炼剂:精炼剂的添加量需根据实际情况进行调整。
过多或过少的精炼剂都会影响精炼及净化效果。
3. 定期检查设备:定期对熔炉、离心分离机等设备进行检查和维护,确保其正常运行和良好的工作状态。
五、结论A356铝合金的精炼及净化过程对于保证汽车轮毂的质量具有至关重要的作用。
通过精炼和净化过程,可以有效去除合金中的杂质和气体,提高合金的纯净度,从而保证汽车轮毂的强度、耐磨性及使用寿命。
《7A04高强铝合金轮毂锻造成形工艺研究》范文

《7A04高强铝合金轮毂锻造成形工艺研究》篇一一、引言随着汽车工业的快速发展,轮毂作为汽车的重要部件,其性能和制造工艺越来越受到关注。
7A04高强铝合金因其优异的力学性能和良好的加工性能,被广泛应用于汽车轮毂的制造。
本文旨在研究7A04高强铝合金轮毂的锻造成形工艺,以提高轮毂的制造质量和生产效率。
二、材料与设备本研究采用7A04高强铝合金作为轮毂的原材料。
该合金具有较高的强度、良好的耐腐蚀性和加工性能。
锻造设备主要包括加热炉、锻造机、冷却设备等。
在生产过程中,需要对设备进行定期检查和维护,以确保生产的顺利进行。
三、锻造成形工艺7A04高强铝合金轮毂的锻造成形工艺主要包括原材料准备、加热、锻造、冷却和后处理等步骤。
1. 原材料准备:选择合适的7A04高强铝合金板材,进行切割、打磨等预处理,以去除表面缺陷和杂质。
2. 加热:将预处理后的原材料放入加热炉中,加热至锻造温度范围内。
加热过程中需控制温度和加热速度,以避免材料过热或过烧。
3. 锻造:将加热后的材料放入锻造机中,通过模具进行锻造。
锻造过程中需控制锻造压力、锻造速度和锻造温度,以保证轮毂的成形质量和性能。
4. 冷却:锻造完成后,需要对轮毂进行冷却处理。
冷却过程中需控制冷却速度和冷却介质,以避免轮毂产生裂纹或变形。
5. 后处理:冷却后的轮毂需进行后处理,包括去除表面氧化皮、进行机械加工等。
后处理过程中需控制加工参数和加工精度,以保证轮毂的尺寸精度和表面质量。
四、工艺优化及质量控制在研究过程中,我们对锻造成形工艺进行了优化,通过调整加热温度、锻造压力、冷却速度等参数,提高了轮毂的成形质量和性能。
同时,我们还采用了先进的检测设备和方法,对轮毂的尺寸精度、表面质量、力学性能等进行检测,确保轮毂的质量符合要求。
五、实验结果与分析通过实验,我们得到了不同工艺参数下7A04高强铝合金轮毂的成形质量和性能数据。
数据分析表明,通过优化工艺参数,可以显著提高轮毂的成形质量和性能。
钢制车轮的内容
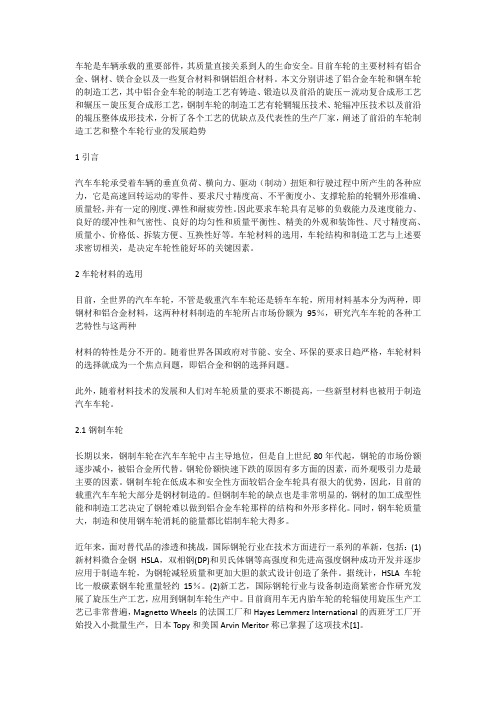
车轮是车辆承载的重要部件,其质量直接关系到人的生命安全。
目前车轮的主要材料有铝合金、钢材、镁合金以及一些复合材料和钢铝组合材料。
本文分别讲述了铝合金车轮和钢车轮的制造工艺,其中铝合金车轮的制造工艺有铸造、锻造以及前沿的旋压-流动复合成形工艺和辗压-旋压复合成形工艺,钢制车轮的制造工艺有轮辋辊压技术、轮辐冲压技术以及前沿的辊压整体成形技术,分析了各个工艺的优缺点及代表性的生产厂家,阐述了前沿的车轮制造工艺和整个车轮行业的发展趋势1引言汽车车轮承受着车辆的垂直负荷、横向力、驱动(制动)扭矩和行驶过程中所产生的各种应力,它是高速回转运动的零件、要求尺寸精度高、不平衡度小、支撑轮胎的轮辋外形准确、质量轻,并有一定的刚度、弹性和耐疲劳性。
因此要求车轮具有足够的负载能力及速度能力、良好的缓冲性和气密性、良好的均匀性和质量平衡性、精美的外观和装饰性、尺寸精度高、质量小、价格低、拆装方便、互换性好等。
车轮材料的选用,车轮结构和制造工艺与上述要求密切相关,是决定车轮性能好坏的关键因素。
2车轮材料的选用目前,全世界的汽车车轮,不管是载重汽车车轮还是轿车车轮,所用材料基本分为两种,即钢材和铝合金材料,这两种材料制造的车轮所占市场份额为95%,研究汽车车轮的各种工艺特性与这两种材料的特性是分不开的。
随着世界各国政府对节能、安全、环保的要求日趋严格,车轮材料的选择就成为一个焦点问题,即铝合金和钢的选择问题。
此外,随着材料技术的发展和人们对车轮质量的要求不断提高,一些新型材料也被用于制造汽车车轮。
2.1钢制车轮长期以来,钢制车轮在汽车车轮中占主导地位,但是自上世纪80年代起,钢轮的市场份额逐步减小,被铝合金所代替。
钢轮份额快速下跌的原因有多方面的因素,而外观吸引力是最主要的因素。
钢制车轮在低成本和安全性方面较铝合金车轮具有很大的优势,因此,目前的载重汽车车轮大部分是钢材制造的。
但钢制车轮的缺点也是非常明显的,钢材的加工成型性能和制造工艺决定了钢轮难以做到铝合金车轮那样的结构和外形多样化。
《2024年低压铸造A356合金轮毂的组织与性能研究》范文
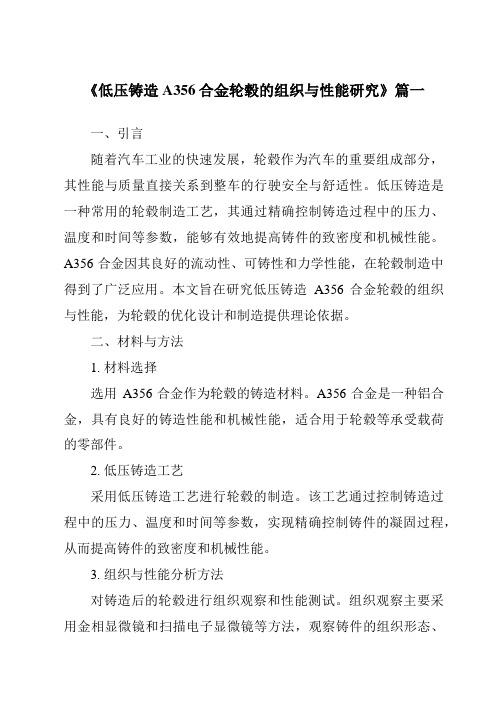
《低压铸造A356合金轮毂的组织与性能研究》篇一一、引言随着汽车工业的快速发展,轮毂作为汽车的重要组成部分,其性能与质量直接关系到整车的行驶安全与舒适性。
低压铸造是一种常用的轮毂制造工艺,其通过精确控制铸造过程中的压力、温度和时间等参数,能够有效地提高铸件的致密度和机械性能。
A356合金因其良好的流动性、可铸性和力学性能,在轮毂制造中得到了广泛应用。
本文旨在研究低压铸造A356合金轮毂的组织与性能,为轮毂的优化设计和制造提供理论依据。
二、材料与方法1. 材料选择选用A356合金作为轮毂的铸造材料。
A356合金是一种铝合金,具有良好的铸造性能和机械性能,适合用于轮毂等承受载荷的零部件。
2. 低压铸造工艺采用低压铸造工艺进行轮毂的制造。
该工艺通过控制铸造过程中的压力、温度和时间等参数,实现精确控制铸件的凝固过程,从而提高铸件的致密度和机械性能。
3. 组织与性能分析方法对铸造后的轮毂进行组织观察和性能测试。
组织观察主要采用金相显微镜和扫描电子显微镜等方法,观察铸件的组织形态、晶粒大小和分布等情况。
性能测试主要包括硬度测试、拉伸试验和疲劳试验等,评估铸件的机械性能。
三、结果与分析1. 组织观察结果通过金相显微镜和扫描电子显微镜观察发现,低压铸造A356合金轮毂的组织致密,晶粒大小均匀,没有明显的气孔、夹渣等缺陷。
组织中存在一定数量的第二相颗粒,这些颗粒对提高合金的机械性能具有重要作用。
2. 机械性能测试结果硬度测试表明,低压铸造A356合金轮毂的硬度较高,具有较好的耐磨性能。
拉伸试验结果显示,铸件具有较高的抗拉强度和屈服强度,表明其具有较好的抗变形能力。
疲劳试验结果表明,铸件具有良好的疲劳性能,能够承受长时间的交变载荷。
3. 组织与性能关系分析组织观察和机械性能测试结果表明,低压铸造A356合金轮毂的组织与性能之间存在密切关系。
致密的组织和均匀的晶粒分布是保证铸件具有较高机械性能的基础。
第二相颗粒的存在能够进一步提高合金的硬度、抗拉强度和屈服强度等性能。
轮毂基础知识

轮毂基础知识目录1. 轮毂基础知识介绍 (2)1.1 定义与分类 (3)1.2 功能与作用 (4)1.3 发展历程 (5)2. 轮毂的结构与材质 (6)2.1 基本结构 (8)2.1.1 内圈与外圈 (9)2.1.2 轮胎安装与拆卸接口 (9)2.2 常用材质 (10)2.2.1 钢铁材质 (11)2.2.2 铝合金材质 (12)2.2.3 锻造轮毂 (14)2.3 防腐与涂装工艺 (15)3. 轮毂的制造工艺 (17)3.1 铸造成型 (18)3.1.1 熔炼与浇注 (19)3.1.2 冷却与定型 (20)3.2 锻造技术 (21)3.2.1 高温处理 (22)3.2.2 热处理工艺 (23)3.3 表面处理技术 (25)4. 轮毂的性能要求与评估 (26)4.1 性能参数 (27)4.2 设计标准 (29)4.3 测试方法 (30)5. 轮毂的安装与维护 (32)5.1 安装步骤 (33)5.2 维护与保养 (33)5.3 常见问题与解决方法 (35)6. 市场趋势与新型材料 (36)6.1 全球市场分析 (37)6.2 材料创新 (39)6.3 环保与生物降解材料研究 (40)7. 轮毂的未来发展趋势 (41)7.1 智能轮毂 (42)7.2 制造技术革新 (44)7.3 新能源车用轮毂 (45)1. 轮毂基础知识介绍作为汽车传动系统中的重要组成部分,承载着至关重要的角色。
它连接着轮胎与轮圈,不仅影响着汽车的行驶性能、安全性和燃油经济性,还直接关系到车辆的耐用性和维修成本。
轮毂的基本结构包括轮毂体、轴承座、紧固件等关键部件。
轮毂体是承载重量和传递扭矩的主要部分,通常由高强度铝合金或钢材制成。
轴承座则是用来支撑轴承,确保车轮能够平稳、高效地旋转。
紧固件如螺栓和螺母则用于将轮毂牢固地连接到轮圈上。
轮毂的表面处理也至关重要,为了提高耐磨性和耐腐蚀性,轮毂表面常采用电镀、喷涂或化学镀等处理方式。
这些处理方式不仅能延长轮毂的使用寿命,还能提升其外观质量。
轮毂基础知识PPT课件

发展历史
4. 后来爱美的人发明了一种东西叫“轮毂罩”,一般用塑料制 成,
盖在钢轮毂外层。轮毂罩开始是为了“遮丑”,后来发现挺好 看,
就叫做“美化”,现在,铝合金轮毂成为主流,轮毂罩有了更 高层
次的意义:“冒充”。
7
发展历史
5. 20世纪30年代,德国人将钢制辐条与铝质轧制轮辋相结合的 车轮装载气车上,为铝合金车轮的发展奠定了基础。二战后, 铝合金轮毂开始在普通汽车上得到应用。
尺寸-换算
“英寸” 与 系:
“毫米”
的换算关 1
(in)
=
25.4
(mm)
16 X 6.5 J (JJ)
17.5(18.0)的数据查表得到
× C:6.5 (in) = 6.5*25.4 = 165.1(mm)
√ D:6.5 (in) = 165.0 (mm)
数据查表得到
× A:16 (in) = 16*25.4 = 406.4 (mm)
1. 正偏距就是紧固面靠外 →正偏距的轮毂常用于前驱和部分后驱 车型,例如轿车和乘用车
2. 负偏距就是紧固面比轮毂中心线更 靠里(即靠近制动系统) →负偏距的轮毂常用于SUV、高档轿车 和跑车
3. 零偏距就是两个面重合
注:轮毂的偏距不对,会导致吃胎、胎 壁磨损、妨碍转向,对安全性产生严重 影响
17
结构-偏距(OFFSET)
铝合金轮毂
Flange
凸缘
OFFSET
偏距
Center Bore
中心孔
P.C.D(Pitch Circle Diameter) 螺栓孔径
Rim Diameter
胎环直径
Rim Width
胎环宽
Outer Rim
《7A04高强铝合金轮毂锻造成形工艺研究》范文

《7A04高强铝合金轮毂锻造成形工艺研究》篇一一、引言随着汽车工业的快速发展,轮毂作为汽车的重要部件,其性能和制造工艺对汽车的整体性能有着重要的影响。
7A04高强铝合金以其出色的力学性能、抗腐蚀性能以及良好的加工性能,广泛应用于轮毂制造。
因此,研究7A04高强铝合金轮毂的锻造成形工艺,对提升轮毂制造技术和产品质量具有重要意义。
二、7A04高强铝合金的特性和应用7A04高强铝合金是一种铝、锌、镁、铜等元素构成的合金,具有优良的机械性能和抗腐蚀性能,其强度高、塑性好、耐腐蚀。
由于其优秀的物理和化学性能,7A04高强铝合金广泛应用于航空航天、汽车制造等领域,特别是轮毂等重要部件的制造。
三、锻造成形工艺研究(一)材料准备首先,选择优质的7A04高强铝合金原材料,经过严格的检验和测试,确保其符合制造要求。
此外,还需要准备好必要的模具、工具和设备。
(二)锻造工艺流程锻造工艺主要包括坯料加热、锻造变形、热处理等步骤。
在坯料加热阶段,需要控制好加热温度和时间,以避免材料的过热或过烧。
在锻造变形阶段,通过控制模具和压力,使材料发生塑性变形,形成所需的轮毂形状。
在热处理阶段,通过淬火、回火等工艺,进一步提高材料的机械性能和抗腐蚀性能。
(三)工艺参数优化针对7A04高强铝合金的锻造成形工艺,需要进行工艺参数的优化。
主要包括模具设计、锻造温度、锻造压力、热处理工艺等方面的优化。
通过实验和模拟,找出最佳的工艺参数组合,以提高轮毂的成形质量和生产效率。
四、实验与结果分析(一)实验方法采用实验的方法,对7A04高强铝合金轮毂的锻造成形工艺进行研究。
通过改变模具设计、锻造温度、锻造压力等工艺参数,观察轮毂的成形质量和机械性能的变化。
(二)实验结果通过实验,发现当模具设计合理、锻造温度和压力适当时,可以获得成形质量好、机械性能优良的轮毂。
同时,通过优化热处理工艺,可以进一步提高轮毂的抗腐蚀性能。
此外,还发现通过合理的工艺参数组合,可以提高生产效率,降低生产成本。
- 1、下载文档前请自行甄别文档内容的完整性,平台不提供额外的编辑、内容补充、找答案等附加服务。
- 2、"仅部分预览"的文档,不可在线预览部分如存在完整性等问题,可反馈申请退款(可完整预览的文档不适用该条件!)。
- 3、如文档侵犯您的权益,请联系客服反馈,我们会尽快为您处理(人工客服工作时间:9:00-18:30)。
1 汽车轮毂制造技术 班级:机电1302班 学号: 姓名:师世健 指导教师:邢书明 目录 一、摘要································3 二、汽车轮毂的选材···························3 1. 钢铁材料 ····························3 1.1 球墨铸铁···························3 1.2 其他钢铁材料·························3 2.合金材料·····························3 3.复合材料·····························3 三、铸造方法······························3 1.压力铸造·····························3 2.金属型铸造····························4 3.熔模铸造·····························4 4.低压铸造·····························5 5.离心铸造·····························5 四、工艺方案······························6 1.零件图······························6 2.浇注位置·····························6 3.分型面······························7 4.砂芯·······························7 2
5.浇注系统·····························7 6.主要工艺参数的确定························7 7.冒口·······························7 8.铸造工艺图····························8
汽车轮毂制造技术
一、摘要 轮毂,作为汽车一个重要组成结构,起着支撑车身重量的作用,对汽车节能、环保、安全性、操控性都有着极其重要的影响。对其工作环境及使用要求予以充分分析,对其结构进行合理设计,选取性能优良的材料及适当的加工方法,都是汽车轮毂制造中不可或缺的环节。
二、汽车轮毂的选材
1.钢铁材料 1.1 铸铁、铸钢 球墨铸铁以其优良的综合力学性能应用在轮毂上,如铁素体球墨铸铁、高韧性球墨铸铁等。但是,由于类似碳素钢轮毂的缺点,以及铸造过程的复杂性和铸造模型所限,轮毂形状难于控制,限制了其应用。 1.2 其他钢铁材料 一些合金钢如加入钛元素的低合金钢,合金元素可以细化晶粒,提高钢的力学性能,使钢具有强度高、塑韧性好、加工成形性和焊接性良好,可以作为轮毂用钢;此外,低合金高强度双相钢,如低碳含铌钢,提高贝氏体含量,可以提高屈服强度,提高扩孔率,也可以用作轮辐和轮辋用钢。在实际应用中的多数钢制轮毂是通过已成型的轮缘和轮盘焊接而成,尽量使自重降低。
2.合金材料 汽车采用铝合金轮毂后减重效果明显,轻型车使用铝合金轮毂比传统钢制轮毂轻30%-40%,中型汽车可轻30%左右。美国森特来因·图尔公司用分离旋压法制出的整体板材(6061合金)车轮,比钢板冲压车轮重量减轻达50%,旋压加工时间不到90s/个,不需要组装作业,适宜大批量生产。另外,相同外径尺寸的轮毂使用铝合金轮毂抗压强度还有所提高。
3.复合材料 复合材料是应现代科学技术发展而出现的具有强大生命力的材料。由于复合材料具有特殊的振动阻尼特性,可减振和降低噪声、抗疲劳性能好,损伤后易修理,便于整体成形,故可用于制造汽车车身、受力构件、传动轴、发动机架及其内部构件。
三、铸造方法 3
1.压力铸造 压力铸造的实质是使液态金属在高压作用下以极高的速度充填型腔,并在压力作用下凝固而获得铸件的一种方法。采用压铸工艺生产的铸件组织致密、机械性能好、强度和表面硬度较高、铸件的尺寸精确、表面光洁。但传统压铸工艺生产的铝轮毂最大的缺点是不能通过热处理来进一步提高性能,由于液体金属充型速度极快,型腔中的气体很难完全排除,常以气孔形式存留在铸件中,这些铸件孔隙中的气体在热处理过程中会发生膨胀,使得铸件“起泡”。为使压铸件也能适用于汽车保安件。 近年来出现了一些无气孔压铸新工艺,最有代表的是充氧压铸法。充氧压铸法是使压室和压型型腔内的金属液相间的空间充氧置换,并在高速高压下进行压铸,当液体金属充填时,一方面通过排气槽排出氧气,另一方面喷散的铝液与未排出的氧气发生反应,形成氧化铝小微粒,分散在铸件内部,使铸件内不产生气孔。用充氧压铸法生产的铸件,含气量为只有普通压铸法的1/10,可进行固溶处理和焊接。与传统压铸法相比,充氧压铸的铝轮毂具有成品率高,组织致密,良好的拉伸强度和耐疲劳性能等优点。国外该方法已广泛用于铝轮毂的生产,日本轻金属株式会社于1983年开始用此方法大批量生产轿车铝合金轮毂,较采用其它铸造方法生产的同类产品重量减少了15%机加工切削量由原来的2~3mm减少到0.75mm,轮毂价格降低了10%。美国铸锻公司于1982年开始用充氧压铸法生产汽车铝合金轮毂,代替了原来的低压铸造法,并使铝轮毂的重量减轻了18%。由于有较高的机械性能和较轻的重量,充氧压铸铝轮毂用于紧急救援车和高级车辆是十分理想的。
2.金属型铸造 金属型铸造又称硬模铸造,它是将液体金属浇入金属铸型,以获得铸件的一种铸造方法。铸型是用金属制成,可以反复使用多次(几百次到几千次)。金属型铸造目前所能生产的铸件,在重量和形状方面还有一定的限制,如对黑色金属只能是形状简单的铸件;铸件的重量不可太大;壁厚也有限制,较小的铸件壁厚无法铸出。 与砂型铸造比较:在技术上与经济上有许多优点。金属型生产的铸件,其机械性能比砂型铸件高。同样合金,其抗拉强度平均可提高约25%,屈服强度平均提高约20%,其抗蚀性能和硬度亦显著提高;铸件的精度和表面光洁度比砂型铸件高,而且质量和尺寸稳定;铸件的工艺收得率高,液体金属耗量减少,一般可节约15~30%;不用砂或者少用砂,一般可节约造型材料80~100%;此外,金属型铸造的生产效率高;使铸件产生缺陷的原因减少;工序简单,易实现机械化和自动化。 金属型铸造虽有很多优点,但也有不足之处。如:金属型制造成本高;金属型不透气,而且无退让性,易造成铸件浇不足、开裂或铸铁件白口等缺陷;金属型铸造时,铸型的工作温度、合金的浇注温度和浇注速度,铸件在铸型中停留的时间,以及所用的涂料等,对铸件的质量的影响甚为敏感,需要严格控制。解决这些缺陷可以尽量选用成本较低的金属制造模型,并在型腔内留出透气孔,但因为其制造成本太高,还是不宜应用于汽车轮毂的制造。
3.熔模铸造 熔模铸造又称失蜡法。失蜡法是用腊制作所要铸成器物的模子,然后在蜡模上涂以泥浆,这就是泥模。泥模晾干后,在焙烧成掏模。一经焙烧,蜡模全部熔化流失,只剩陶模。一般制泥模时就留下了浇注口,再从浇注口灌入铜液,冷却后,所需的器物就制成了。 熔模铸件尺寸精度较高,当然由于熔模铸造的工艺过程复杂,影响铸件尺寸精度的因素较多,例如模料的收缩、熔模的变形、型壳在加热和冷却过程中的线量变化、合金的收缩率以及在凝固过程中铸件的变形等,所以普通熔模铸件的尺寸精度虽然较高,但其一致性仍需提 4
高。压制熔模时,采用型腔表面光洁度高的压型,因此,熔模的表面光洁度也比较高。此外,型壳由耐高温的特殊粘结剂和耐火材料配制成的耐火涂料涂挂在熔模上而制成,与熔融金属直接接触的型腔内表面光洁度高。所以,熔模铸件的表面光洁度比一般铸造件的高。熔模铸造最大的优点就是由于熔模铸件有着很高的尺寸精度和表面光洁度,所以可减少机械加工工作,只是在零件上要求较高的部位留少许加工余量即可,甚至某些铸件只留打磨、抛光余量,不必机械加工即可使用。由此可见,采用熔模铸造方法可大量节省机床设备和加工工时,大幅度节约金属原材料。熔模铸造方法的另一优点是,它可以铸造各种合金的复杂的铸件,特别可以铸造高温合金铸件。如喷气式发动机的叶片,其流线型外廓与冷却用内腔,用机械加工工艺几乎无法形成。用熔模铸造工艺生产不仅可以做到批量生产,保证了铸件的一致性,而且避免了机械加工后残留刀纹的应力集中。熔模铸造的缺点是工序繁杂,生产周期长,原辅材料费用比砂型铸造高,生产成本较高,铸件不宜太大、太长,一般限于25kg以下。 而且铸造出来的零件强度不高,所以该方法不适合制造汽车轮毂。
4.低压铸造 低压铸造是用干燥、洁净的压缩空气将保温炉中的铝液自下而上通过升液管和浇注系统平稳地向上压到铸造机模具型腔中,保持一定压力,一般为20~60kPa直到铸件凝固后释放压力。因在压力下充型和凝固,所以充填性好、铸件缩松少、致密性高。该法中,坩埚表面的氧化膜不会被破坏,与其它铸造方法比较,气孔和夹渣缺陷少,产品内部质量好。由于低压铸造利用压力充型和补充,大大简化了浇冒系统的结构,使金属液收得率大大提高,一般可达90%,而金属型重力铸造仅40%~60%。目前低压铸造已成为铝轮毂生产的首选工艺、日 本的丰田汽车公司、东京轻合金制作所、美国福特汽车公司等均采用此工艺生产铝轮毂,国内的铝合金轮毂制造企业多数也采用此工艺生产,现有数十家企业用低压铸造工艺生产铝合 金汽车及摩托车轮毂。低压铸造法的缺点是铸造时间较长、加铝料、换模具费时间、设备投资大、低压铸造机使用的升液管成本较高且易损坏。
5.离心铸造 离心铸造是将液体金属注入高速旋转的铸型内,使金属液在离心力的作用下充满铸型和形成铸件的技术和方法。离心力使液体金属在径向能很好地充满铸型并形成铸件的自由表面;不用型芯能获得圆柱形的内孔;有助于液体金属中气体和夹杂物的排除;影响金属的结晶过程,从而改善铸件的机械性能和物理性能。 优点是几乎不存在浇注系统和冒口系统的金属消耗,提高工艺出品率;生产中空铸件时可不用型芯,故在生产长管形铸件时可大幅度地改善金属充型能力,降低铸件壁厚对长度或直径的比值,简化套筒和管类铸件的生产过程;铸件致密度高,气孔、夹渣等缺陷少,力学性能高;便于制造筒、套类复合金属铸件,如钢背铜套、双金属轧辊等;成形铸件时,可借离心力提高金属的充型能力,故可生产薄壁铸件。缺点是用于生产异形铸件时有一定的局限性。铸件内孔直径不准确,内孔表面比较粗糙,质量较差,加工余量大;铸件易产生比重偏析,因此不适合于合金易产生比重偏析的铸件(如铅青铜),尤其不适合于铸造杂质比重大于金属液的合金。所以不适合汽车轮毂的制造。