摩擦材料综述
湿式铜基摩擦材料
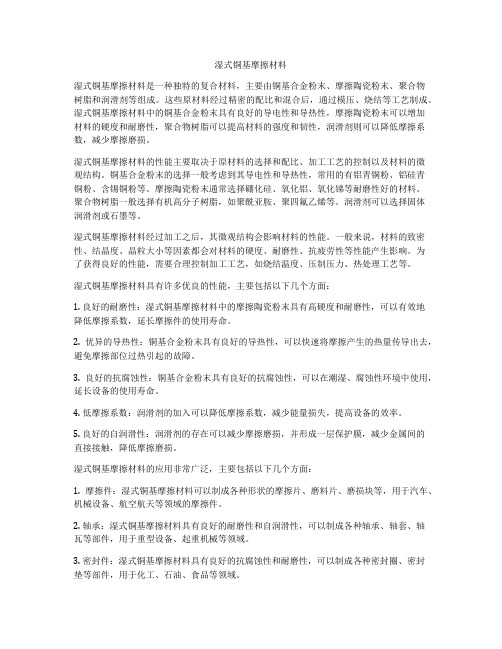
湿式铜基摩擦材料湿式铜基摩擦材料是一种独特的复合材料,主要由铜基合金粉末、摩擦陶瓷粉末、聚合物树脂和润滑剂等组成。
这些原材料经过精密的配比和混合后,通过模压、烧结等工艺制成。
湿式铜基摩擦材料中的铜基合金粉末具有良好的导电性和导热性,摩擦陶瓷粉末可以增加材料的硬度和耐磨性,聚合物树脂可以提高材料的强度和韧性,润滑剂则可以降低摩擦系数,减少摩擦磨损。
湿式铜基摩擦材料的性能主要取决于原材料的选择和配比、加工工艺的控制以及材料的微观结构。
铜基合金粉末的选择一般考虑到其导电性和导热性,常用的有铝青铜粉、铝硅青铜粉、含锡铜粉等。
摩擦陶瓷粉末通常选择硼化硅、氧化铝、氧化锑等耐磨性好的材料。
聚合物树脂一般选择有机高分子树脂,如聚酰亚胺、聚四氟乙烯等。
润滑剂可以选择固体润滑剂或石墨等。
湿式铜基摩擦材料经过加工之后,其微观结构会影响材料的性能。
一般来说,材料的致密性、结晶度、晶粒大小等因素都会对材料的硬度、耐磨性、抗疲劳性等性能产生影响。
为了获得良好的性能,需要合理控制加工工艺,如烧结温度、压制压力、热处理工艺等。
湿式铜基摩擦材料具有许多优良的性能,主要包括以下几个方面:1. 良好的耐磨性:湿式铜基摩擦材料中的摩擦陶瓷粉末具有高硬度和耐磨性,可以有效地降低摩擦系数,延长摩擦件的使用寿命。
2. 优异的导热性:铜基合金粉末具有良好的导热性,可以快速将摩擦产生的热量传导出去,避免摩擦部位过热引起的故障。
3. 良好的抗腐蚀性:铜基合金粉末具有良好的抗腐蚀性,可以在潮湿、腐蚀性环境中使用,延长设备的使用寿命。
4. 低摩擦系数:润滑剂的加入可以降低摩擦系数,减少能量损失,提高设备的效率。
5. 良好的自润滑性:润滑剂的存在可以减少摩擦磨损,并形成一层保护膜,减少金属间的直接接触,降低摩擦磨损。
湿式铜基摩擦材料的应用非常广泛,主要包括以下几个方面:1. 摩擦件:湿式铜基摩擦材料可以制成各种形状的摩擦片、磨料片、磨损块等,用于汽车、机械设备、航空航天等领域的摩擦件。
摩擦材料研究报告
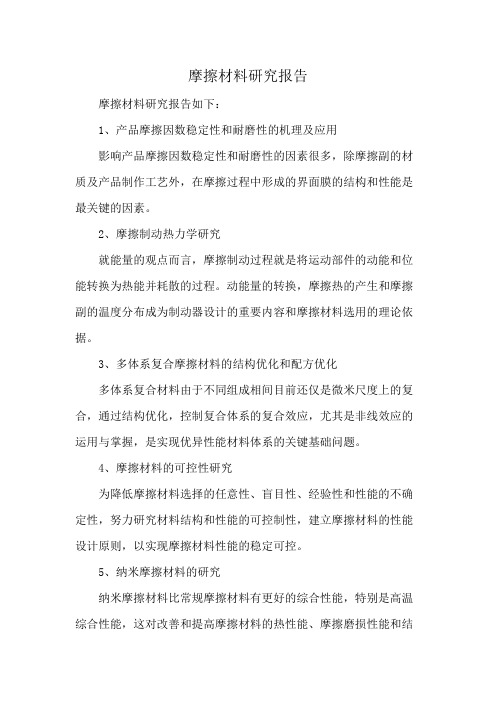
摩擦材料研究报告
摩擦材料研究报告如下:
1、产品摩擦因数稳定性和耐磨性的机理及应用
影响产品摩擦因数稳定性和耐磨性的因素很多,除摩擦副的材质及产品制作工艺外,在摩擦过程中形成的界面膜的结构和性能是最关键的因素。
2、摩擦制动热力学研究
就能量的观点而言,摩擦制动过程就是将运动部件的动能和位能转换为热能并耗散的过程。
动能量的转换,摩擦热的产生和摩擦副的温度分布成为制动器设计的重要内容和摩擦材料选用的理论依据。
3、多体系复合摩擦材料的结构优化和配方优化
多体系复合材料由于不同组成相间目前还仅是微米尺度上的复合,通过结构优化,控制复合体系的复合效应,尤其是非线效应的运用与掌握,是实现优异性能材料体系的关键基础问题。
4、摩擦材料的可控性研究
为降低摩擦材料选择的任意性、盲目性、经验性和性能的不确定性,努力研究材料结构和性能的可控制性,建立摩擦材料的性能设计原则,以实现摩擦材料性能的稳定可控。
5、纳米摩擦材料的研究
纳米摩擦材料比常规摩擦材料有更好的综合性能,特别是高温综合性能,这对改善和提高摩擦材料的热性能、摩擦磨损性能和结
构强度提供了新的技术途径。
6、工艺的研发
研发“优质、高效、节能、低耗、少或无污染”的摩擦材料制品生产工艺,对提高技术经济效益意义重大
7、摩擦材料表面工程研究
通过表面工程处理,可有效提高相对运动的两物体即摩擦副的耐磨性和减少运动时的摩擦损耗,到达减少摩擦和控制磨损的目的。
干式桥摩擦片材料

干式桥摩擦片材料
干式桥摩擦片材料是一种常见的摩擦材料,广泛应用于桥梁、建筑和工程领域。
它具有优异的摩擦性能、耐磨性和耐高温性能,能够有效提高设备的工作效率和使用寿命。
干式桥摩擦片材料通常由多种材料组成,包括金属纤维、有机纤维和填料等。
这些材料的组合可以根据不同的使用需求进行调整,以满足不同工作条件下的摩擦性能和耐磨性要求。
干式桥摩擦片材料具有优异的摩擦性能。
摩擦是指两个物体之间相对运动时产生的阻力。
干式桥摩擦片材料在摩擦过程中可以产生较大的摩擦力,从而实现有效的制动或牵引作用。
同时,它还具有较低的摩擦系数,可以减少能量损失和磨损,提高设备的工作效率和使用寿命。
干式桥摩擦片材料具有良好的耐磨性。
在桥梁、建筑和工程领域,设备经常需要经受高强度的工作环境和频繁的运动摩擦,因此耐磨性是一个重要的考虑因素。
干式桥摩擦片材料通常采用高强度的纤维材料和耐磨填料,可以有效抵抗磨损和严酷工作环境的侵蚀,延长设备的使用寿命。
干式桥摩擦片材料还具有优异的耐高温性能。
在桥梁和工程领域,设备通常需要长时间工作在高温环境下,因此耐高温性能是一个重要的考虑因素。
干式桥摩擦片材料通常采用高温稳定的有机纤维和
填料,能够在高温下保持稳定的摩擦性能和强度,确保设备的正常运行。
总的来说,干式桥摩擦片材料是一种优秀的摩擦材料,具有优异的摩擦性能、耐磨性和耐高温性能。
它在桥梁、建筑和工程领域的应用广泛,能够提高设备的工作效率和使用寿命。
随着科技的发展和材料的不断创新,干式桥摩擦片材料将会越来越好地适应各种工作环境和需求,为人们的生活和工作提供更加可靠和高效的支持。
摩擦材料分类

摩擦材料分类
摩擦材料是指用于制造摩擦部件的材料,通常用于制造摩擦副(如刹车、离合器、变速器等)。
根据不同的使用环境和要求,摩擦
材料可以分为以下几类:
1. 有机摩擦材料
有机摩擦材料主要由有机高分子材料制成,如酚醛树脂、聚苯乙烯、聚酰亚胺等。
这种材料具有摩擦系数稳定、噪音小、制造工艺简单等优点,但其摩擦性能受温度、湿度等环境因素影响较大,因此适用于一些较为温和的使用环境,如汽车刹车片、摩托车离合器等。
2. 金属摩擦材料
金属摩擦材料主要由金属及其合金制成,如铸铁、铜、钢等。
这种材料具有热稳定性好、寿命长等特点,适用于高温、高压等恶劣环境下的应用,如飞机制动系统、高速列车制动系统等。
3. 复合摩擦材料
复合摩擦材料是指将有机高分子材料、金属等多种材料组合使用,以取长补短,达到更好的摩擦性能。
这种材料具有摩擦系数高、磨损率低、使用寿命长等特点,适用于高负荷、高速度等严苛环境下的使用,如飞机襟翼、导弹制动系统等。
4. 陶瓷摩擦材料
陶瓷摩擦材料主要由氧化铝、碳化硅等材料制成,具有硬度高、抗磨损性能好等特点,适用于高速度、高温度、高压力等极端环境下的使用,如高速列车制动系统、摩托车刹车片等。
总之,不同种类的摩擦材料各有千秋,应根据实际使用环境和要求进行选择。
汽车摩擦材料

摩擦材料
制动 -- 汽车摩擦材料
Brake Friction Products
汽车的摩擦材料
★摩擦材料是: 1.作用:一种以摩擦为主要功能、兼有结构性 能要求的复合材料。 2.用途:汽车用摩擦材料主要是用于制造制动 摩擦片和离合器片。 3.性能要求:由于摩擦材料在汽车上主要用 于制造制动系和传动系的零件 (决定汽车安全性使用性) 1)有足够高而稳定的摩擦因数 (2)有良好的耐磨性 (3)具有良好的导热性 (5)不产生过大的噪声
摩擦材料
定义(组成): 是一种由骨架材料(基体)、粘结剂、 填充剂组成的复合材料 粘结剂: ★ 酚醛树脂 ★ 橡胶 ★ 橡胶和酚醛树脂共混 骨架材料:无机或有机纤维 填料:摩擦性能调节剂和配合剂组成
骨架材料分类
陶瓷纤维 石棉纤维金属源自维碳纤维玻璃纤维摩擦材料
摩擦材料制品的分 类
★ 盘式制动片 ★鼓式制动片 ★离合器面片 ★火车制动闸瓦 ★石油钻井刹车块 ★制动带 ★飞机摩擦片 ★摩托车摩擦片 ★船用摩擦片 ★工程机械摩擦片 ★切割片 ★砂轮 ★抛光片
刹车片材料基本知识、摩擦材料和发展方向要点
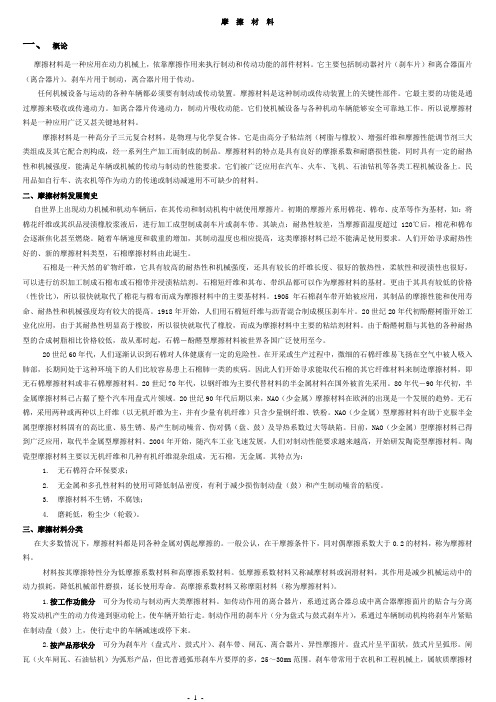
摩擦材料一、概论摩擦材料是一种应用在动力机械上,依靠摩擦作用来执行制动和传动功能的部件材料。
它主要包括制动器衬片(刹车片)和离合器面片(离合器片)。
刹车片用于制动,离合器片用于传动。
任何机械设备与运动的各种车辆都必须要有制动或传动装置。
摩擦材料是这种制动或传动装置上的关键性部件。
它最主要的功能是通过摩擦来吸收或传递动力。
如离合器片传递动力,制动片吸收动能。
它们使机械设备与各种机动车辆能够安全可靠地工作。
所以说摩擦材料是一种应用广泛又甚关键地材料。
摩擦材料是一种高分子三元复合材料,是物理与化学复合体。
它是由高分子粘结剂(树脂与橡胶)、增强纤维和摩擦性能调节剂三大类组成及其它配合剂构成,经一系列生产加工而制成的制品。
摩擦材料的特点是具有良好的摩擦系数和耐磨损性能,同时具有一定的耐热性和机械强度,能满足车辆或机械的传动与制动的性能要求。
它们被广泛应用在汽车、火车、飞机、石油钻机等各类工程机械设备上。
民用品如自行车、洗衣机等作为动力的传递或制动减速用不可缺少的材料。
二、摩擦材料发展简史自世界上出现动力机械和机动车辆后,在其传动和制动机构中就使用摩擦片。
初期的摩擦片系用棉花、棉布、皮革等作为基材,如:将棉花纤维或其织品浸渍橡胶浆液后,进行加工成型制成刹车片或刹车带。
其缺点:耐热性较差,当摩擦面温度超过120℃后,棉花和棉布会逐渐焦化甚至燃烧。
随着车辆速度和载重的增加,其制动温度也相应提高,这类摩擦材料已经不能满足使用要求。
人们开始寻求耐热性好的、新的摩擦材料类型,石棉摩擦材料由此诞生。
石棉是一种天然的矿物纤维,它具有较高的耐热性和机械强度,还具有较长的纤维长度、很好的散热性,柔软性和浸渍性也很好,可以进行纺织加工制成石棉布或石棉带并浸渍粘结剂。
石棉短纤维和其布、带织品都可以作为摩擦材料的基材。
更由于其具有较低的价格(性价比),所以很快就取代了棉花与棉布而成为摩擦材料中的主要基材料。
1905年石棉刹车带开始被应用,其制品的摩擦性能和使用寿命、耐热性和机械强度均有较大的提高。
同步环摩擦材料介绍
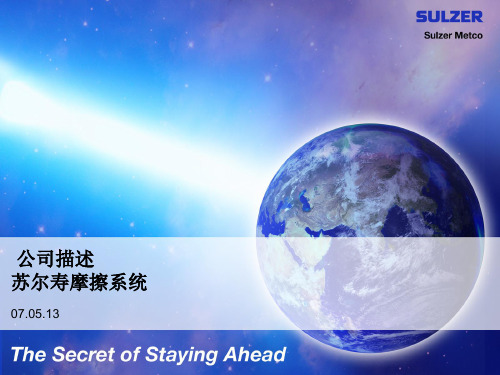
HB
>120
g/cm3 6.8 -7.2
C35 / AISI1035
620 500 12 200000 >180 (>350 HV
氮化) 7.8
黄铜
600 380 13 105000
max. 200
8.4
田 / 2/29/2020 / 21
在直径73mm情况下,不同材料同步环基体的对比
粉末冶金
冲压钢
Niederwürschnitz 德 金奈 印度
国
文索基特 美国
上海 中国
制造工厂 Lomm 荷兰 德布勒森 匈牙利 Marple 英国
Sales 2007: 753.1 Million CHF; Headcount: 2054 田 / 2/29/2020 / 4
苏尔寿优若凡
马德里 西班牙
Padstow AUS
米兰 意大利
Tokyo J
布莱达 荷兰
Shanghai PRC
Bron 法国
Wohlen 瑞士 Salzgitter 德国 Stalybridge 英国 Weissenborn 德国 Barboursville WV,
设计验证和确认能力
▪ 设计和基本计算 性能 几何尺寸 材料负荷 配合公差分析
▪ 3D 建模 可视化 空间需求研究 drawings
▪ FE 分析 材料应力 接触压力分布 温度分布
▪ 试验
▪ 质量认证:
DIN ENISO9001:2000,
VDA 6.1 , ISO/TS 16949
S. Augustin 同步环设计
欧洲
H. Lehr 样品
U. Göhner 试验设备
摩擦材料配方

摩擦材料配方
摩擦材料的配方因其用途和应用领域而有所不同。
以下是一些常见的摩擦材料配方:
1. 刹车片配方:
- 金属粉末(如铜、钢):提供摩擦性能和热传导性能。
- 碳纤维:增加摩擦系数和耐磨性。
- 树脂基体:提供强度和稳定性。
- 石墨或其他固体润滑剂:减少摩擦热和磨损。
- 硬化剂和填充剂:调整刹车片的硬度和摩擦性能。
2. 高温摩擦材料配方(用于摩擦离合器等高温环境):
- 陶瓷纤维:提供高温稳定性和耐磨性。
- 碳纤维:增加摩擦系数和耐磨性。
- 金属粉末(如铜、钢):提供高温摩擦性能和热传导性能。
- 有机或无机粘结剂:将材料粘结在一起,并提供强度。
- 硬化剂和填充剂:调整材料的硬度和摩擦性能。
3. 摩擦润滑材料配方(用于轴承等摩擦部件):
- 固体润滑剂(如石墨、二硫化钼):减少摩擦系数和磨损。
- 金属粉末(如铜、铝):提供摩擦性能和热传导性能。
- 基体材料(如聚合物或金属):提供强度和稳定性。
- 抗氧化剂和防腐剂:增加材料的耐久性和稳定性。
注意的是,不同的应用领域和特定要求可能需要不同的配方组合。
此外,具体的摩擦材料配方还受到专利保护,因此详细的配方可能无
法完全公开。
对于特定的摩擦材料需求,建议咨询专业的材料制造商或相关领域的专家以获取更准确的信息和建议。
- 1、下载文档前请自行甄别文档内容的完整性,平台不提供额外的编辑、内容补充、找答案等附加服务。
- 2、"仅部分预览"的文档,不可在线预览部分如存在完整性等问题,可反馈申请退款(可完整预览的文档不适用该条件!)。
- 3、如文档侵犯您的权益,请联系客服反馈,我们会尽快为您处理(人工客服工作时间:9:00-18:30)。
1 文献综述 1.0摩擦材料简介 摩擦材料是一类应用在各种交通工具(如汽车,火车,摩托车,飞机,轮船,自行车等)及各类动力机械(如石油钻机,拖拉机,电梯,挖掘机,坦克等)上,依靠摩擦作用来完成制动和传动功能的部件材料,它主要包括用于制动的制动器衬片(俗称刹车片)和用于传动的离合器面片(俗称离合器片)。 它是所有车辆和大部分动力机械组成的不可或缺部件,发挥着不可替代的作用。在使用上要求其要有一定的摩擦系数,足够的机械强度、稳定性,低的制动噪音,以及较低的磨损率以并很好的耐高温性能。一般的单一材料往往不能达到性能要求,故决定它是必须是一类由增强纤维、粘结剂、摩擦性能调节剂和填料等原材料混合压制成型的三元复合材料。这不仅克服了单一的原料缺陷,而且可以通过不同原料之间的性能偶合来发挥单一组分本身没有的性能。 它的主体复合成分为粘结剂(树脂与橡胶)、增强纤维和摩擦性能调节剂三大类以及其他的钢背等附件,摩擦材料的制备方法分为干式和湿式两种。干式制备的摩擦材料主要采用无石棉的有机材料和烧结摩擦材料;湿式制备的摩擦材料主要有纸基摩擦材料、石墨基摩擦材料和烧结摩擦材料。
1.1摩擦材料组成
1.1.1 增强纤维 增强纤维是一类常见的增强体材料,增强纤维的使用主要使制动材料具有一定的强度和韧性,耐得住冲击、剪切、拉伸等机械作用而不会出现了裂纹、断裂、崩溃等损伤。因此应有足够的强韧性,良好的摩擦磨损性能,与树脂的分散黏附能力好,耐热性好。 摩擦材料按增强纤维出现次序可分为先期使用的石棉材料增强纤维和后期兴起的无石棉摩擦材料。 石棉材料因具有良好的分散性和结合性,有较高的比模量,耐磨并且在高温环境下力学性能不衰退等优良特性并且由于其分布广,成本低廉、价格便宜,性价比高起初被公认为最理想的增强材料被广泛应用于摩擦材料及其他行业,但石棉纤维会被无限分割成非常细小的人肉眼观察不到的纤维很容易被人通过呼吸 2
系统吸收沉积在肺部,引发肺部疾病乃至癌变。因此石棉已被国际癌症研究中心确定为致癌物。现石棉原料已被好多国家限制使用并逐渐被其他的一些人工合成的矿物纤维,有机纤维,金属纤维,陶瓷纤维所替代。 无石棉摩擦材料研究始于上世纪80年代中期,至1989年国内已有多家厂商和科研单位相继推出无石棉摩擦材料,主要集中于轿车用盘式刹车片,其构成多数以别的纤维作为石棉的替代物。1990年杭城摩擦材料有限公司从德国Pagod公司引进上海大众汽车公司桑塔纳轿车配套的720GG无石棉盘式刹车片生产技术,这是我国首次从国外引进的无石棉摩擦材料生产技术。总的来说,我国的汽车工业起步较晚,摩擦材料的发展也相对滞后,研发部门也不健全缺乏资金投入和协作,未能与汽车主管部门及主要汽车制造厂家取得共识,致使无石棉、低噪声的新型摩擦材料的研制开发工作受到制约,落后于国外。【1】
1.1.2目前主要使用的非石棉增强纤维主要有以下数种: (1)碳纤维 碳纤维是一种新型纤维材料,它是由有机纤维或低分子烃气体原料加热至1500 ℃所形成的纤维状材料,碳含量在90%以上。由于碳纤维既具有碳素材料固有本质,又具有金属材料的导电和导热性、陶瓷材料的耐热和耐腐蚀性、纺织纤维的柔软可编性以及高分子材料的轻质、易加工性能,是一种多能和一材多用的功能材料和结构材料。因此广泛应用于航天、航空、军工、汽车、医疗、化工、文化体育用品等领域。按原料分类碳纤维可分为聚丙烯腈基碳纤维、沥青基碳纤维、胶粘基碳纤维和酚醛树脂碳纤维。目前,主要为聚丙烯腈基碳纤维和沥青基碳纤维,其它碳纤维很少。沥青基碳纤维又分为通用型沥青基碳纤维和高性能沥青基碳纤维两种。 碳纤维有如下优良特性: 比重轻; 比模量高; 耐磨、耐疲劳、减振吸能等物理机械性能优异; 耐酸、碱和盐腐蚀,可形成多孔、表面活性强的活性碳纤维; 热膨胀系数小,导热性好;高温环境下性能不衰退; 具有润滑性,不沾润在熔融金属中,可使磨损率降低;如此的优良特性在摩擦材料领域表现出了非常大的开发应用前景,碳纤维的使用在很大程度上提高了摩擦材料的综合性能,常加入到树脂、金属或陶瓷、碳、水泥等基体中,构成碳纤维增强复合材料,是一种极为有用的结构材料。 虽然碳纤维有很多的优点,但目前阶段由于其生产条件苛刻,工艺复杂,价格昂贵,故在目前只在飞机的传制动部件以及部分高配制轿车和部分赛车的摩擦材料构件的生产制造中应用。其他方面的应用尚处于研究阶段。【2】
(2)海泡石纤维 海泡石纤维是一种稀有非金属矿,是我国新兴矿种之一,经多年地质探测证 3
实,探明储量在1000万吨以上。我国的海泡石矿藏主要分布于湖南、陕西、江苏、河北、天津等地。其结构分散性良好,而且取向随机,具有良好的填充性,已被广泛应用于各个各个领域。海泡石按其形态分为α海泡石和β海泡石两种,前者成大束的纤维状晶体产出,即通常成为纤维状海泡石,后者呈土状产出,是由非常细且短的纤维或纤维状集合体组成。由于产地不同,海泡石矿物有白、黄、灰等数种颜色,纯净的海泡石多呈现白色至浅白灰色,粉末状的海泡石质轻,易浮于水面,溶于水中后吸水迅速成絮凝状,且吸水量较大,润湿的海泡石具有极强的粘结性。【7】 海泡石纤维具有优良的摩擦性能,主要得益于海泡石纤维独特的结构。其一是海泡石具有良好的耐热性能,在高温下其结构仍能保持稳定。在250℃高温下纤维结构依然稳定,耐温达1500-1700℃道孔隙结构的“分子筛”在860℃时,才会遭到破坏。由此可知,海泡石的热力学性能稳定。其二是由于其具有极大的表面积和极强的吸附能力会充分的和其他的复合组分结合在结合界面上形成很强的结合力。 海泡石所特有的结构决定它有很好的吸附性能、流变性能和催化性能。吸附剂的吸附能力与其表面积大小有直接关系,经计算海泡石的表面积可达到900m2 / g,其中内表面积为500 m2 / g,外表面积为400 m2 / g,如此大的比表面积是海泡石有较强吸附能力的直接原因。α海泡石纤维具有极大的比表面积和孔隙率(比表面积为203. 3~362. 8 m2 / g ,孔隙率为32. 18 %~46. 87 %) ,因而具有很强的吸附能力;且海泡石的微观形貌成束状,每束直径为0.1~0.3微米,平均0.2微米,长径比为1:60~100微米,通过于摩阻材料复合,能充分发挥基体强度,改善基体于界面的关系,提高材料的剪切强度,达到不连续纤维混杂效应的增强效果。材料因密度小,硬度低,对对偶损伤小,热传导低,制动噪音小。同时,海泡石纤维能在极性溶剂、液态树脂中高度分散,形成纤维网状结构,在复合材料中起到了随机增强的作用;再者,海泡石纤维与粘结剂界面上的物理吸附和化学键合(以共价键方式联结) 增强了界面上的粘结力,提高了这种摩擦材料的整体强度。当摩擦材料的基体受热分解时,海泡石能吸附分解产生的水和小分子化合物及气体,避免因混合摩擦而产生的热衰退现象;海泡石的价格约为钢纤维、碳纤维、玻璃纤维价格的1/ 6 左右,可与各种填料和粘结剂充分混合,制造同一规格的摩擦片可节省原料近40 % ,因此成本大大降低。 (3)陶瓷纤维 陶瓷纤维具有强度高,耐化学腐蚀,耐高温等特性。是一种较为理想的摩擦材料增强纤维,但它目前还是存在自身的一些缺陷,在制动时会产生较大的噪音,对对偶材质的损伤也较其他矿物纤维和有机纤维大。还有待继续改进,一下以硅酸盐纤维为例做以介绍,硅酸盐纤维是一种人造陶瓷纤维,它的渣球含量非常低, 4
在质量要求高,并要求低噪音、低磨损(摩擦材料与盘/鼓)的摩擦材料中,这一点是很重要的。 纤维耐温高,最高耐温在1000℃,具有良好的热稳定性,可减少摩擦片的热衰退现象;佷低的热传导率可防止急刹车时出现的超高温对制动管和刹车油的影响。比重小,比表面积大;表面吸附性强;纤维强度高,其增强效果可满足盘式刹车片和鼓式刹车片的基本要求。硅酸盐纤维全面通过放射性测试,绝无石棉成分,完全符合绿色环保要求。 硅酸盐纤维有以下优良特性: 1)耐磨 良好的耐磨性,表明产品使用寿命长,也是衡量摩擦材料耐用程度的重要技术经济指标,与半金属配方相比,使用寿命可以提高1.5倍以上。 2)具有良好的机械强度和物理性能 硅酸盐纤维具有的强度﹑韧性等特点,从而使制品在恶劣的刹车条件下也能具有非常好的强度特性。 3)有良好的性能价格比和市场竞争力 硅酸盐纤维比表面积大﹑吸附性强﹑具有很好的填料保持能力,在摩擦材料中有极佳的纤维分布性,在单位体积上大大的节省了成本。 4)制动舒适﹑环保 良好的制动性能及理化机械性能等特点,使刹车时脚感舒适;全面通过放射性测试,绝无石棉成分,完全符合日益提高的环保要求。 (4)金属纤维 在摩擦材料生产研发领域中,金属纤维同有机和无机纤维一样具有独特的性能和广泛的用途。金属纤维具有良好的导热和耐高温性能,而且制造方法较简单,成本价格便宜。但相对于其他纤维材料,其有质硬,易损伤对偶盘且易生锈等本质缺陷。然而缺点归缺点,不会在较大程度上影响其使用。以金属纤维为填充剂的复合材料在民用行业如电子、化工、机械、纺织、食品、医药部门开拓了广阔的应用前景。在民用工业上应用金属纤维复合材料也势在必行。金属纤维作为一种新兴的纤维材料已经受到各行各业的重视。 金属纤维在外观上看有多种多样。按材质分有不锈钢、碳钢、铸铁、铜、铝、镍、铁铬铝合金、高温合金等。按形状分为长纤维、短纤维、粗纤维、细纤维、钢绒、异型纤维等。 金属纤维的生产方法有传统的拉丝切断法、还有熔抽法、集束拉拔法、刮削法、切削法等。 目前纤维最小的直径达0.5微米,最长可达几十米甚至几百米。 目前各国生产的金属纤维、碳钢纤维居多,其次是不锈钢、铝、黄铜