QR(quasi-resonant) Control Technology
准谐振变换器的变结构控制
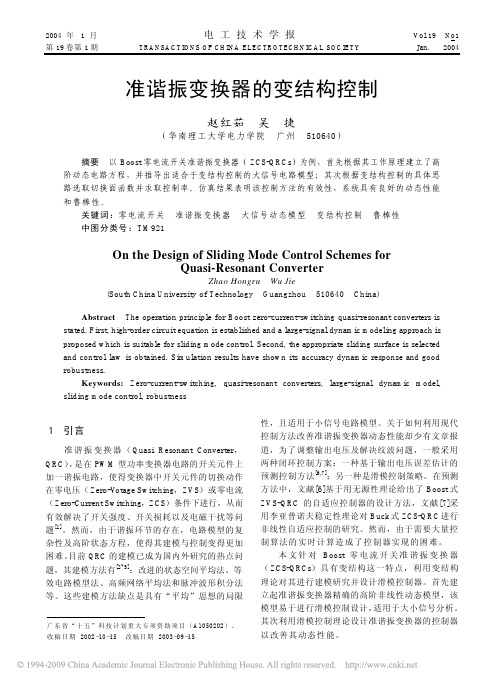
0 − 1 RC f 0 0 −
0 0 0 1 Cr
−
1 Lf I 1 L 0 Lf V o 0 ⋅ + ⋅V 1 I Lr s 0 Lr VC r 0 0 ( 2)
初始条件为 I Lr (t1 ) = I L ,VC r (t1 ) = Vo 。开关模态 2 所持续的时间为 T2 =
Zhao Hongru (South China University of Technology Wu Jie Guangzhou 510640 China)
Abstract The operation principle for Boost zero-current-switching quasi-resonant converters is stated. First, high-order circuit equation is established and a large-signal dynamic modeling approach is proposed which is suitable for sliding mode control. Second, the appropriate sliding surface is selected and control law is obtained. Simulation results have shown its accuracy dynamic response and good robustness. Keywords: Zero-current-switching, quasi-resonant converters, large-signal dynamic model, sliding mode control, robustness 性,且适用于小信号电路模型。关于如何利用现代 控制方法改善准谐振变换器动态性能却少有文章报 道,为了调整输出电压及解决纹波问题,一般采用 两种闭环控制方案:一种基于输出电压误差估计的 预测控制方法[6,7];另一种是滑模控制策略。在预测 方法中,文献[6]基于用无源性理论给出了 Boost 式 ZVS-QRC 的自适应控制器的设计方法,文献 [7]采 用李亚普诺夫稳定性理论对 Buck 式 ZCS-QRC 进行 非线性自适应控制的研究。然而,由于需要大量控 制算法的实时计算造成了控制器实现的困难。 本 文 针 对 Boost 零 电 流 开 关 准 谐 振 变 换 器 ( ZCS-QRCs )具有变结构这一特点,利用变结构 理论对其进行建模研究并设计滑模控制器。首先建 立起准谐振变换器精确的高阶非线性动态模型,该 模型易于进行滑模控制设计, 适用于大小信号分析。
OB2202_Datasheet

GENERAL DESCRIPTIONOB2202 is a highly integrated Quasi-Resonant (QR) controller optimized for high performance offline flyback converter applications. At normal load condition, it operates in QR mode with minimum drain voltage switching. To meet the CISPR-22 EMI starting at 150KHz, the maximum switching frequency is internally limited to 130KHz. It operates in PFM mode for high power conversion efficiency at light load condition. When the loading is very small, the IC operates in ‘Extended Burst Mode’ to minimize the switching loss. As a result, lower standby power consumption and higher conversion efficiency can be achieved. OB2202 offers comprehensive protection coverage including Cycle-by-Cycle Current Limiting, VCC Under Voltage Lockout(UVLO), Programmable Output Over Voltage Protection(OVP), VCC Clamp, Gate Clamp, Over Load Protection(OLP), On-chip Thermal Shutdown, Programmable Soft Start, ProgrammableBrownout Protection, Programmable Over Power Protection (OPP) Compensation, and ExternalLatch Triggering, Max On-time Limit, etc.OB2202 is offered in SOP-8 and DIP-8 packages.FEATURES■ Multi-Mode Operation Quasi-Resonant Operation at Normal Loading Pulse Frequency Modulation (PFM) Operation at Light Load Burst Mode at No Load ■ Programmable Brownout Protection and Line OVP Protection■ Excellent OPP Compensation ■ 130KHz Maximum Frequency Limit■ Internal Minimum T_off for Ringing Suppression■ 30us Maximum On Time Limit ■ 50us Maximum Off Time Limit ■ Internal Leading Edge Blanking ■ Programmable Soft-start■ Cycle-by-cycle Current Limiting ■ External Latch Triggering ■ Internal Thermal Shutdown ■ 1A Peak Current Sink/Source Capability ■ Programmable Output OVP APPLICATIONS Offline AC/DC flyback converter for ■ Power Adaptor and Open-frame SMPS ■ LCD Monitor/TV/PC/Set-Top Box Power Supplies■ NB/DVD/Portable DVD Power SuppliesTYPICAL APPLICATIONProduct SpecificationGENERAL INFORMATIONPin ConfigurationThe pin map of OB2202 in DIP8 and SOP8Ordering Information Part Number Description OB2202AP 8 Pin DIP, Pb free in Tube OB2202CP 8 Pin SOP, Pb free in Tube OB2202CPA 8 Pin SOP, Pb free in T&R Note: All Devices are offered in Pb-free Package if nototherwise noted.Package Dissipation Rating PackageR θJA (℃/W)DIP8 90 SOP8 150Absolute Maximum Ratings Parameter ValueVCC ZenerClamp Voltage 34 V VCC Clamp ContinuousCurrent10 mASS Input Voltage -0.3 to 7V FBInput Voltage -0.3 to 7VCS Input Voltage-0.3 to 7V DEM Input Voltage-0.3 to 7V BO Input Voltage -0.3 to 7V Maximum OperatingJunction Temperature T J150 o CMin/Max Storage Temperature T stg-55 to 150 oCLead Temperature(Soldering, 10secs)260 o CNote: Stresses beyond those listed under “absolutemaximum ratings” may cause permanent damage to the device. These are stress ratings only, functional operation of the device at these or any other conditions beyond those indicated under “recommended operating conditions” is not implied. Exposure to absolute maximum-rated conditions for extended periods may affect device reliability.Marking InformationSOP8Y: Year Code (0-9) WW: Week Code (1-52)C: SOP8P:lead-free s: internal codeDIP8Y: Year Code (0-9) WW: Week Code (1-52)A: DIP8P:lead-free s: internal codeL T Y W W O B 2202A PsTERMINAL ASSIGNMENTSPin Num Pin NameI/ODescription1 SS I/O Multi-functional pin. One function is for soft-start programming byconnecting a capacitor from SS to GND. Another function is forexternal latch triggering by pulling SS up to a voltage higher than 3.8V.2 FB I/O Feedback input pin. PWM duty cycle is determined by voltage level into this pin and current-sense signal level at Pin 3. The voltage levelat this pin also controls the mode of operation in one of the threemodes: quasi-resonant (QR), pulse frequency modulation mode (PFM) and burst mode (BM).3 CS I Current sense input.4 GND P Ground for internal circuitry.5 GATE O Totem-pole gate drive output for power MOSFET.6 VCC P Chip DC power supply pin.7 DEM I/OInput from auxiliary winding for demagnetization timing. Also this pin isused for output over voltage protection (Load OVP).8 BO I/O Brownout and Line OVP detection pin. Connect a resistor divider from line voltage to this pin to detect line voltage. If this pin drops below0.5V and lasts for 50ms, brownout protection will be triggered andPWM output will be disabled. This pin is also used as line OVP sense input.BLOCK DIAGRAMRECOMMENDED OPERATING CONDITIONSymbol ParameterMin Max Unit VCC VCC Supply Voltage11 28 V T AOperating Ambient Temperature-2085o CELECTRICAL CHARACTERISTICS(T A = 25O C, VCC=18V, if not otherwise noted) Symbol Parameter Test Conditions Min Typ Max Unit Supply Voltage (VCC) SectionIstartup VCC Start up CurrentVCC =UVLO(OFF)-1.5V,Measure current into VCC5 15 uA I_VCC_quiet Operation Currentwithout switchingFB=3V 2.0 3.5 mAI_VCC_operation Operation currentwith switchingFB=3V, 1nF load at GATE 3.0 5.0 mAUVLO(ON) VCC Under VoltageLockout Enter7.8 8.8 9.8 VUVLO(OFF)VCC Under VoltageLockout Exit (Startup) 14.815.8 16.8 V OVP(ON)VCC Over VoltageProtection Enter33 V VCC_Clamp VCC Zener ClampVoltageI(VCC ) = 5 mA 34 VFeedback Input Section(FB Pin) A VCS PWM Input Gain ΔV FB /ΔV cs 4.75 V/V V FB_Open FB Open Voltage5.3 V I FB _ShortFB pin short circuit current Short FB pin to GND,measure current 1.5 mA V TH _PFM_on PFM mode onthreshold1.6 VV TH _PFM_off PFM mode offthreshold1.5 VV TH _BM_onBurst Mode onthreshold0.9 V V TH _BM_offBurst Mode offthreshold0.7 V V TH _PLPower Limiting FBThreshold Voltage4.4 V T D _PL Power limitingDebounce Time80 mSecZ FB _IN Input Impedance 4 Kohm Current Sense Input(CS Pin) SectionT_blankingCS Input LeadingEdge Blanking Time350 nSec Vcs_max Maximum CS voltage 0.570.60 0.63 V0V<V(BO)<0.4V 0 uA 0.4V<V(BO)<1.05V 77×[V(BO)-0.4] uA I CS Internal sourcecurrent to CS pin for OPP compensation 1.05V<V(BO)<3V 50+16×[V(BO)-1.05] uA T D _OC Over CurrentDetection and Control DelayCL=1nf at GATE, 100 nSecDemagnetization Detection SectionV TH _DEM Demagnetizationcomparator threshold voltage1075 150 mV V TH _DEM_hystHysteresis for DEMcomparator20 mV V DEM _clamp(neg) Negative clampvoltage-0.7 VV DEM _clamp(pos) Positive clampvoltage5.8 VT supp Suppression of the transformer ringing atstart of secondary stroke2 uSecT OUT Timeout after lastdemag transistion5 uSecT DEM_delay Demag propagationdelay250 nSecV TH _OVP Output OVP triggerpoint3.75 VT_OVP_delay Output OVP deglitchtime constant4Switching Cycle Soft Start Section Iss Soft start chargecurrent8 10 12 uAV TH _ss_exit Soft start terminationthreshold2.2 VI SS _clamp_sink Maximum sinkcurrent capabilitywhen SS is clamped 120 uA V SS _clamp SS pin high clampvoltage5.8 VTimer Section F _burstBurst mode switchingfrequency22 KHzF_QR_clamp_h Frequency highclamp in QR mode 115130 145 KHzF_QR_clamp_l Frequency low clampin QR mode17 22 27 KHzTon_max Maximum on time 20 30 40 uSec Toff_max Maximum off time 40 50 60 uSec Thermal ProtectionT_shutdown Thermal shutdowntemperature155 ◦CLatch ProtectionV_latch_trigger External latch trigger threshold voltage at SS pin SS pin pull up currentshould be larger than 200uA 3.8V V_latch_release VCC latch releasevoltage6.3 VIvdd(latch)VCC current whenlatch offVCC =V_latch_release+1V 45 uA Brownout Protection and Line OVP ProtectionVth_BOBrownout comparatorthreshold0.5 V Vth_line_OVPLine OVP comparatorthreshold2 V T D _BO Brownout debouncetime50 mSecIBO_hys BO output current forBO hysteresis programming1 uAGate Drive OutputVOL Output Low Level Io = 100 mA (sink) 1 VVOH Output High Level Io = 100 mA (source)VCC=20V7.5 VVG_Clamp Output ClampVoltage LevelVCC=20V16.5VT_r Output Rising Time CL = 1nf 50 nSec T_f Output Falling Time CL = 1nf 20 nSecCHARACTERIZATION PLOTSOPERATION DESCRIPTIONQuasi-Resonant (QR) converter typically features lower EMI and higher power conversion efficiency compared to conventional hard-switched converter with a fixed switching frequency. OB2202 is a highly integrated QR controller optimized for offline flyback converter applications. The built-in advanced energy saving with high level protection features provide cost effective solutions for energy efficient power supplies.z Startup Current and Start up ControlStartup current of OB2202 is designed to be very low so that VCC could be charged up above UVLO(OFF) threshold level and device starts up quickly. A large value startup resistor can therefore be used to minimize the power loss yet reliable startup in application. For a typical AC/DC adaptor with universal input range design,a 2 MΩ, 1/8 W startup resistor could be used together with a VCC capacitor to provide a fast startup and yet low power dissipation design solution.z Operating CurrentThe operating current of OB2202 is very low. Good efficiency is achieved by the low operating current together with extended burst mode control schemes at No/light conditions.z Multi-Mode Operation for High EfficiencyOB2202 is a multi-mode QR controller. The controller changes the mode of operation according to FB voltage, which reflects the line and load conditions.■ Under normal operating conditions (FB>Vth2, Figure 1), the system operates in QR mode. The frequency varies depending on the line voltage and the load conditions. Therefore, the system may actually work in DCM when 130KHz frequency clamping is reached. System design should be optimized such that the operation frequency is within the range specified at full loading conditions and in universal AC line input range.■ At light load condition (Vth1<VFB<Vth2, Figure 1), the system operates in PFM (pulse frequency modulation) mode for high power conversion efficiency. In PFM mode, the “ON” time in a switching cycle is fixed and the system modulates the frequency according to the load conditions. Generally, in flyback converter, the decreasing of loading results in voltage level decreasing at FB pin. The controller monitors the voltage level at FB and control the switching frequency. However, the valley switching characteristic is still preserved in PFM mode. That is, when loading decreases, the system automatically skip more and more valleys and the switching frequency is thus reduced. In such way, a smooth frequency foldback is realized and high power conversion efficiency is achieved.■ At zero load or very light load conditions (VFB<Vth1), the system operates in On-Bright’s proprietary “extended burst mode”. In this condition, voltage at FB is below burst mode threshold level, Vth1. The Gate drive output switches only when VCC voltage drops below a preset level or FB input is active to output an on state. Otherwise the gate drive remains at off state to minimize the switching loss thus reduce the standby power consumption to the greatest extend. In extended burst mode, the switching frequency is fixed to 22KHz, in this way, possible audio noise is eliminated.130KHzFigure 1z Demagnetization DetectionThe transformer core demagnetization is detected by monitoring the voltage activity on the auxiliary windings through DEM pin. This voltage features a flyback polarity. A new cycle starts when the power switch is activated. After the on time (determined by the CS voltage and FB), the switch is off and the flyback stroke starts. After the flyback stroke, the drain voltage shows an oscillation with a frequency of approximately dpCLπ2/1, wherepL is the primary selfinductance of the transformer and d C is the capacitance on the drain node, as shown in Fig.2.Figure 2The typical detection level is fixed at 75mV at the DEM pin. Demagnetization is recognized by detection of a possible “valley” when the voltage at DEM is below 75mV in falling edge. DEM detection is suppressed during the ringing suppression time Tsupp (please refer to “Ringing Suppression Timer ” section).z Current Sensing and Leading EdgeBlankingCycle-by-Cycle current limiting is offered in OB2202 current mode control. The switch current is detected by a sense resistor into the CS pin. An internal leading edge blanking circuit chops off the sense voltage spike at initial MOSFET on state due to snubber diode reverse recovery so that the external RC filtering on sense input is no longer needed. The current limit comparator is disabled and cannot turn off the external MOSFET during the blanking period. The PWM duty cycle is determined by the current sense input voltage and the FB input voltage.z Maximum and Minimum On-TimeThe minimum on-time of the system is determined by the LEB time (typical 350ns). The IC limits the on-time to a maximum time of 30us (typical).z Ringing Suppression TimerA ringing suppression timer Tsupp is implemented in OB2202. In normal operation, Tsupp starts when CS reaches the feedback voltage FB, the external power switch is set to off state. During Tsupp, the external power switch remains in off state and cannot be turned on gain. The ringing suppression time is necessary in applications where the transformer has a large leakage inductance, particularly at low output voltages orstartup. In OB2202, the ringing suppression timer Tsupp is set to 2us internally.z Programmable Brownout Protection andLine OVP ProtectionBy monitoring the level on pin BO during normal operation, the controller protects the SMPS against low main condition, as shown in Fig.3. When BO level falls below 0.5V, brownout is triggered, the controller stops pulsing and disable internal source current for brownout hysteresis. BO pin is also used for line OVP sense input, when BO level is above 2.0V, line OVP isz Maximum/Minimum Frequency ClampAccording to the QR operation principle, the switching frequency is inversely proportional to the output power. Therefore, when the output power decreases, the switching frequency can become rather high without limiting. To meet the CISPR-22 EMI limit starting at 150KHz, the maximum switching frequency in OB2202 is internally limited to 130KHz. To prevent audio noise issue, the minimum switching frequency in QR mode is clamped to 20KHz.z On chip Thermal ShutdownOB2202 provides an on chip thermal shutdown. The IC will stop switching when the junction temperature exceeds the thermal shutdown temperature, typically 155 °C. The IC resumes normal operation when the junction temperature decreased below this temperature.z External Latch TriggeringBy externally forcing a level on pin SS (e.g.., with a signal coming from a temperature sensor) greater than 3.8V, OB2202 can be permanentlylatched-off. To resume normal operation, VCC voltage should go below 6.3V (typical), which implies to unplug the SMPS form the mains.z Programmable Over Power Protection (OPP) CompensationThe variation of max. output power in QR system can be rather large if no compensation is provided. In OB2202, an internal current which is a function of BO voltage is sourced out for Over Power Protection (OPP) compensation. By adjusting the external resistor Rcomp in series with CS pin (Pleae refer to Page 1), an excellent OPP performance can be realized in the universal input range.z Output Over voltage protection (OVP)An output over voltage protection (OVP) is implemented by sensing the auxiliary winding voltage at DEM pin during the flyback phase. The auxiliary winding voltage is a well-defined replica of the output voltage. The OVP works by sampling the plateau voltage at DEM pin during the flyback phase, as shown in Fig.4. A 2 us internal delay (plateau sampling) guarantees a clean plateau, provided that the leakage inductance ringing has been fully damped.If the sampled plateau voltage exceeds the OVP trip level (3.75V), an internal counter starts counting subsequent OVP events. If OVP events are detected in successive 4 cycles, the controller assumes a true OVP and it enters a latch off mode and stops all switching operations. The counter has been added to prevent incorrect OVP detection which might occur during ESD or lightning events. If the output voltage exceeds the OVP trip level less than 4 successive cycles, the internal counter will be cleared and no fault is asserted. z Overload OperationWhen over load (for example, short circuit) occurs, the feedback current is below minimum value and a fault is detected. If this fault is present for more than 80ms, the controller enters an auto-recovery soft burst mode. All pulses are stopped, VCC will drops below UVLO and the controller will try to restart with the power on soft start. The SMPSenters the burst sequence and it resumes operation once the fault disappears.z Programmable Soft StartOB2202 features a programmable soft start to soften the constraints in the power supply during the startup. It is activated during the power on sequence. As soon as VCC reaches UVLO(OFF), an internal trimmed 10uA current is sourced from SS pin and charges the external programming capacitor, the peak current of CS pin is then gradually increased from zero. When SS pin reaches 2.2V, soft start process is over. After soft start process is over, SS pin is clamped to 2V. Every restart attempt is followed by soft start sequence.Figure 5SS pin is also is used for external latch triggering (Please refer to “External Latch Triggering” section).z Gate DriveThe GATE pin is connected to the gate of an external MOSFET for power switch control. Too weak the gate drive results in higher conduction and switch loss of MOSFET while too strong gate drive output compromises the EMI. Good tradeoff is achieved through the built-in totem pole gate drive design with right output strength and dead time control. The low idle loss and good EMI system design is easier to achieve with this dedicated control scheme. An internal 16.5V clamp is added for MOSFET gate protection at high VCC voltage.PACKAGE MECHANICAL DATA8-Pin Plastic DIPDimensions In Millimeters Dimensions In Inches SymbolMin Max Min MaxA 3.710 5.334 0.146 0.210 A1 0.381 0.015 A2 3.175 3.600 0.125 0.142B 0.350 0.650 0.014 0.026 B1 1.524 (BSC) 0.06 (BSC)C 0.200 0.360 0.008 0.014D 9.000 10.160 0.354 0.400E 6.200 6.600 0.244 0.260 E1 7.320 7.920 0.288 0.312 e 2.540 (BSC) 0.1 (BSC)L 2.921 3.810 0.115 0.150 E2 8.200 9.525 0.323 0.3758-Pin Plastic SOPDimensions In Millimeters Dimensions In Inches SymbolMin Max Min MaxA 1.350 1.750 0.053 0.069A1 0.050 0.250 0.002 0.010 A2 1.250 1.650 0.049 0.065b 0.310 0.510 0.012 0.020c 0.170 0.250 0.006 0.010D 4.700 5.150 0.185 0.203E 3.800 4.000 0.150 0.157E1 5.800 6.200 0.228 0.244e 1.270 (BSC) 0.05 (BSC)L 0.400 1.270 0.016 0.050 θ 0º 8º 0º 8ºIMPORTANT NOTICERIGHT TO MAKE CHANGESOn-Bright Electronics Corp. reserves the right to make corrections, modifications, enhancements, improvements and other changes to its products and services at any time and to discontinue any product or service without notice. Customers should obtain the latest relevant information before placing orders and should verify that such information is current and complete.WARRANTY INFORMATIONOn-Bright Electronics Corp. warrants performance of its hardware products to the specifications applicable at the time of sale in accordance with its standard warranty. Testing and other quality control techniques are used to the extent it deems necessary to support this warranty. Except where mandated by government requirements, testing of all parameters of each product is not necessarily performed.On-Bright Electronics Corp. assumes no liability for application assistance or customer product design. Customers are responsible for their products and applications using On-Bright’s components, data sheet and application notes. To minimize the risks associated with customer products and applications, customers should provide adequate design and operating safeguards.LIFE SUPPORTOn-Bright Electronics Corp.’s products are not designed to be used as components in devices intended to support or sustain human life. On-bright Electronics Corp. will not be held liable for any damages or claims resulting from the use of its products in medical applications.MILITARYOn-Bright Electronics Corp.’s products are not designed for use in military applications. On-Bright Electronics Corp. will not be held liable for any damages or claims resulting from the use of its products in military applications.。
基于改进P-Q控制的光伏准Z源T型逆变器并网控制系统

基于改进P-Q控制的光伏准Z源T型逆变器并网控制系统程启明;李涛;程尹曼;孙伟莎;陈路【摘要】针对传统两电平逆变器与三电平逆变器所需要的开关数量多、损耗大的问题,采用T型逆变器不仅可以克服传统多电平逆变器的缺点,还可提高系统的效率,将Z源网络用于T型逆变器提升了逆变器直流侧的电压水平.为此,将准Z源T型逆变器拓扑结构应用于P-Q并网控制系统中,其中P-Q控制器的电流控制环采用准比例谐振(quasi proportional resonant,qPR)控制策略,实现对电流的无静差跟踪,从而更好地控制并网系统有功与无功的输出.最后,通过MATLAB/Simulink软件仿真实验和实际硬件样机试验验证改进P-Q控制策略的光伏准Z源逆变器并网系统的可行性和有效性.相比于传统的双闭环控制策略,所提出的改进P-Q控制策略可以降低逆变器输出电流谐波,提高系统的经济性;相比于控制器电流环采用比例-积分(proportion integration,PI)控制,所采用的qPR控制能够更好实现对电流与功率的追踪,提高系统的稳定性.【期刊名称】《广东电力》【年(卷),期】2018(031)009【总页数】8页(P54-61)【关键词】准Z源拓扑;T型逆变器;改进P-Q控制;准比例谐振控制;比例-积分控制【作者】程启明;李涛;程尹曼;孙伟莎;陈路【作者单位】上海市电站自动化技术重点实验室(上海电力大学),上海200090;上海市电站自动化技术重点实验室(上海电力大学),上海200090;国网上海市电力公司市北供电分公司,上海200041;上海市电站自动化技术重点实验室(上海电力大学),上海200090;上海市电站自动化技术重点实验室(上海电力大学),上海200090【正文语种】中文【中图分类】TM464传统Z源拓扑存在电容压力大、电感启动电流高以及升压能力有限等缺陷。
为了解决传统Z源拓扑缺陷,国内外学者进行了大量的研究,提出了多种改进型Z源拓扑[1-8]。
OB2202 Datasheet

GENERAL DESCRIPTIONOB2202 is a highly integrated Quasi-Resonant (QR) controller optimized for high performance offline flyback converter applications. At normal load condition, it operates in QR mode with minimum drain voltage switching. To meet the CISPR-22 EMI starting at 150KHz, the maximum switching frequency is internally limited to 130KHz. It operates in PFM mode for high power conversion efficiency at light load condition. When the loading is very small, the IC operates in ‘Extended Burst Mode’ to minimize the switching loss. As a result, lower standby power consumption and higher conversion efficiency can be achieved. OB2202 offers comprehensive protection coverage including Cycle-by-Cycle Current Limiting, VCC Under Voltage Lockout(UVLO), Programmable Output Over Voltage Protection(OVP), VCC Clamp, Gate Clamp, Over Load Protection(OLP), On-chip Thermal Shutdown, Programmable Soft Start, ProgrammableBrownout Protection, Programmable Over Power Protection (OPP) Compensation, and ExternalLatch Triggering, Max On-time Limit, etc.OB2202 is offered in SOP-8 and DIP-8 packages.FEATURES■ Multi-Mode Operation Quasi-Resonant Operation at Normal Loading Pulse Frequency Modulation (PFM) Operation at Light Load Burst Mode at No Load ■ Programmable Brownout Protection and Line OVP Protection■ Excellent OPP Compensation ■ 130KHz Maximum Frequency Limit■ Internal Minimum T_off for Ringing Suppression■ 30us Maximum On Time Limit ■ 50us Maximum Off Time Limit ■ Internal Leading Edge Blanking ■ Programmable Soft-start■ Cycle-by-cycle Current Limiting ■ External Latch Triggering ■ Internal Thermal Shutdown ■ 1A Peak Current Sink/Source Capability ■ Programmable Output OVP APPLICATIONS Offline AC/DC flyback converter for ■ Power Adaptor and Open-frame SMPS ■ LCD Monitor/TV/PC/Set-Top Box Power Supplies■ NB/DVD/Portable DVD Power SuppliesTYPICAL APPLICATIONProduct SpecificationGENERAL INFORMATIONPin ConfigurationThe pin map of OB2202 in DIP8 and SOP8Ordering Information Part Number Description OB2202AP 8 Pin DIP, Pb free in Tube OB2202CP 8 Pin SOP, Pb free in Tube OB2202CPA 8 Pin SOP, Pb free in T&R Note: All Devices are offered in Pb-free Package if nototherwise noted.Package Dissipation Rating PackageR θJA (℃/W)DIP8 90 SOP8 150Absolute Maximum Ratings Parameter ValueVCC ZenerClamp Voltage 34 V VCC Clamp ContinuousCurrent10 mASS Input Voltage -0.3 to 7V FBInput Voltage -0.3 to 7VCS Input Voltage-0.3 to 7V DEM Input Voltage-0.3 to 7V BO Input Voltage -0.3 to 7V Maximum OperatingJunction Temperature T J150 o CMin/Max Storage Temperature T stg-55 to 150 oCLead Temperature(Soldering, 10secs)260 o CNote: Stresses beyond those listed under “absolutemaximum ratings” may cause permanent damage to the device. These are stress ratings only, functional operation of the device at these or any other conditions beyond those indicated under “recommended operating conditions” is not implied. Exposure to absolute maximum-rated conditions for extended periods may affect device reliability.Marking InformationSOP8Y: Year Code (0-9) WW: Week Code (1-52)C: SOP8P:lead-free s: internal codeDIP8Y: Year Code (0-9) WW: Week Code (1-52)A: DIP8P:lead-free s: internal codeL T Y W W O B 2202A PsTERMINAL ASSIGNMENTSPin Num Pin NameI/ODescription1 SSI/O Multi-functional pin. One function is for soft-start programming by connecting a capacitor from SS to GND. Another function is forexternal latch triggering by pulling SS up to a voltage higher than 3.8V.2 FB I/O Feedback input pin. PWM duty cycle is determined by voltage level into this pin and current-sense signal level at Pin 3. The voltage level at this pin also controls the mode of operation in one of the threemodes: quasi-resonant (QR), pulse frequency modulation mode (PFM) and burst mode (BM). 3 CS I Current sense input. 4 GND P Ground for internal circuitry. 5 GATE O Totem-pole gate drive output for power MOSFET. 6VCCP Chip DC power supply pin.7 DEMI/OInput from auxiliary winding for demagnetization timing. Also this pin is used for output over voltage protection (Load OVP).8 BOI/O Brownout and Line OVP detection pin. Connect a resistor divider from line voltage to this pin to detect line voltage. If this pin drops below 0.5V and lasts for 50ms, brownout protection will be triggered andPWM output will be disabled. This pin is also used as line OVP sense input.BLOCK DIAGRAMRECOMMENDED OPERATING CONDITIONSymbol Parameter Min Max Unit VCC VCC Supply Voltage 11 28 VT A Operating Ambient Temperature -20 85 o CELECTRICAL CHARACTERISTICS(T A = 25O C, VCC=18V, if not otherwise noted)Symbol Parameter Test Conditions Min Typ Max Unit Supply Voltage (VCC) SectionIstartup VCC Start up Current VCC=UVLO(OFF)-1.5V,Measure current into VCC5 15uAI_VCC_quiet Operation Currentwithout switchingFB=3V 2.0 3.5 mAI_VCC_operation Operation current withswitchingFB=3V, 1nF load at GATE 3.0 5.0 mAUVLO(ON) VCC Under VoltageLockout Enter7.8 8.8 9.8 VUVLO(OFF) VCC Under VoltageLockout Exit (Startup)14.8 15.8 16.8 VOVP(ON)VCC Over VoltageProtection Enter33VVCC_Clamp VCC Zener ClampVoltageI(VCC) = 5 mA 34 VFeedback Input Section(FB Pin)A VCS PWM Input Gain ΔV FB /ΔV cs 4.75V/V V FB_Open FBOpen Voltage 5.3 VI FB_Short FB pin short circuitcurrentShort FB pin to GND,measure current1.5 mAV TH_PFM_enter Enter PFM modethreshold1.4VV TH_PFM_exit Exit PFM modethreshold1.5VV TH_BM_enter Enter Burst Modethreshold0.5VV TH_BM_exit Exit Burst Modethreshold0.7VV TH_PL Power Limiting FBThreshold Voltage4.4VT D_PL Power limitingDebounce Time80mSecZ FB_IN InputImpedance 4 Kohm Current Sense Input(CS Pin) SectionT_blanking CS Input Leading EdgeBlanking Time350nSecV TH_OC Internal current limitingthreshold0.57 0.60 0.63 VT D_OC Over Current Detectionand Control DelayCL=1nf at GATE, 100 nSecDemagnetization Detection SectionV TH_DEM Demagnetizationcomparator thresholdvoltage75mVV TH_DEM_hyst Hysteresis for DEMcomparator20mVV DEM_clamp(neg) Negative clamp voltage -0.5 V V DEM_clamp(pos) Positive clamp voltage 5.8 VT supp Suppression of thetransformer ringing atstart of secondarystroke2 uSecT OUT Timeout after lastdemag transistion5 uSecT DEM_delay Demag propagationdelay250 nSecV TH _OVP Output OVP triggerpoint3.75 VT_OVP_delayOutput OVP deglitch time constant 4SwitchingCycleSoft Start SectionIss Soft start charge current 8 10 12 uAV TH _ss_exit Soft start terminationthreshold2.2 VI SS _clamp_sink Maximum sink currentcapability when SS is clamped120 uAV SS _clampSS pin high clampvoltage5.8 V Timer SectionF _burst Burst mode switchingfrequency22 KHzF_QR_clamp_hFrequency high clampin QR mode115 130 145 KHz F_QR_clamp_lFrequency low clamp inQR mode17 22 27 KHz Ton_max Maximum on time 20 30 40 uSec Toff_max Maximum off time 40 50 60 uSec Thermal ProtectionT_shutdown Thermal shutdowntemperature155 ℃Latch ProtectionV_latch_trigger External latch trigger threshold voltage at SS pin SS pin pull up currentshould be larger than 200uA 3.8V V_latch_releaseVCC latch releasevoltage6.3 V Ivdd(latch)VCC current when latchoffVCC =V_latch_release+1V 45 uA Brownout Protection and Line OVP ProtectionVth_BOBrownout comparatorthreshold0.5 V Vth_line_OVPLine OVP comparatorthreshold2 V T D _BOBrownout debouncetime50 mSec IBO_hys BO output current forBO hysteresis programming1 uAGate Drive Output VOL Output Low Level Io = 100 mA (sink) 1 VVOH Output High LevelIo = 100 mA (source)VCC=20V7.5 V VG_Clamp Output Clamp VoltageLevelVCC =20V 16.5 VT_r Output Rising Time CL = 1nf 50 nSec T_f Output Falling Time CL = 1nf 20 nSecCHARACTERIZATION PLOTSOPERATION DESCRIPTIONQuasi-Resonant (QR) converter typically features lower EMI and higher power conversion efficiency compared to conventional hard-switched converter with a fixed switching frequency. OB2202 is a highly integrated QR controller optimized for offline flyback converter applications. The built-in advanced energy saving with high level protection features provide cost effective solutions for energy efficient power supplies.z Startup Current and Start up ControlStartup current of OB2202 is designed to be very low so that VCC could be charged up above UVLO(OFF) threshold level and device starts up quickly. A large value startup resistor can therefore be used to minimize the power loss yet reliable startup in application. For a typical AC/DC adaptor with universal input range design,a 2 MΩ, 1/8 W startup resistor could be used together with a VCC capacitor to provide a fast startup and yet low power dissipation design solution.z Operating CurrentThe operating current of OB2202 is very low. Good efficiency is achieved by the low operating current together with extended burst mode control schemes at No/light conditions.z Multi-Mode Operation for High EfficiencyOB2202 is a multi-mode QR controller. The controller changes the mode of operation according to FB voltage, which reflects the line and load conditions.■ Under normal operating conditions (FB>Vth2, Figure 1), the system operates in QR mode. The frequency varies depending on the line voltage and the load conditions. Therefore, the system may actually work in DCM when 130KHz frequency clamping is reached. System design should be optimized such that the operation frequency is within the range specified at full loading conditions and in universal AC line input range.■ At light load condition (Vth1<VFB<Vth2, Figure 1), the system operates in PFM (pulse frequency modulation) mode for high power conversion efficiency. In PFM mode, the “ON” time in a switching cycle is fixed and the system modulates the frequency according to the load conditions. Generally, in flyback converter, the decreasing of loading results in voltage level decreasing at FB pin. The controller monitors the voltage level at FB and control the switching frequency. However, the valley switching characteristic is still preserved in PFM mode. That is, when loading decreases, the system automatically skip more and more valleys and the switching frequency is thus reduced. In such way, a smooth frequency foldback is realized and high power conversion efficiency is achieved.■ At zero load or very light load conditions (VFB<Vth1), the system operates in On-Bright’s proprietary “extended burst mode”. In this condition, voltage at FB is below burst mode threshold level, Vth1. The Gate drive output switches only when VCC voltage drops below a preset level or FB input is active to output an on state. Otherwise the gate drive remains at off state to minimize the switching loss thus reduce the standby power consumption to the greatest extend. In extended burst mode, the switching frequency is fixed to 22KHz, in this way, possible audio noise is eliminated.130KHzFigure 1z Demagnetization DetectionThe transformer core demagnetization is detected by monitoring the voltage activity on the auxiliary windings through DEM pin. This voltage features a flyback polarity. A new cycle starts when the power switch is activated. After the on time (determined by the CS voltage and FB), the switch is off and the flyback stroke starts. After the flyback stroke, the drain voltage shows an oscillation with a frequency of approximately dpCLπ2/1, wherepL is the primary selfinductance of the transformer and d C is the capacitance on the drain node, as shown in Fig.2.Figure 2The typical detection level is fixed at 75mV at the DEM pin. Demagnetization is recognized by detection of a possible “valley” when the voltage at DEM is below 75mV in falling edge. DEM detection is suppressed during the ringing suppression time Tsupp (please refer to “Ringing Suppression Timer ” section).z Current Sensing and Leading EdgeBlankingCycle-by-Cycle current limiting is offered in OB2202 current mode control. The switch current is detected by a sense resistor into the CS pin. An internal leading edge blanking circuit chops off the sense voltage spike at initial MOSFET on state due to snubber diode reverse recovery so that the external RC filtering on sense input is no longer needed. The current limit comparator is disabled and cannot turn off the external MOSFET during the blanking period. The PWM duty cycle is determined by the current sense input voltage and the FB input voltage.z Maximum and Minimum On-TimeThe minimum on-time of the system is determined by the LEB time (typical 350ns). The IC limits the on-time to a maximum time of 30us (typical).z Ringing Suppression TimerA ringing suppression timer Tsupp is implemented in OB2202. In normal operation, Tsupp starts when CS reaches the feedback voltage FB, the external power switch is set to off state. During Tsupp, the external power switch remains in off state and cannot be turned on gain. The ringing suppression time is necessary in applications where the transformer has a large leakage inductance, particularly at low output voltages orstartup. In OB2202, the ringing suppression timer Tsupp is set to 2us internally.z Programmable Brownout Protection andLine OVP ProtectionBy monitoring the level on pin BO during normal operation, the controller protects the SMPS against low main condition, as shown in Fig.3. When BO level falls below 0.5V, brownout is triggered, the controller stops pulsing and disable internal source current for brownout hysteresis. BO pin is also used for line OVP sense input, when BO level is above 2.0V, line OVP isz Maximum/Minimum Frequency ClampAccording to the QR operation principle, the switching frequency is inversely proportional to the output power. Therefore, when the output power decreases, the switching frequency can become rather high without limiting. To meet the CISPR-22 EMI limit starting at 150KHz, the maximum switching frequency in OB2202 is internally limited to 130KHz. To prevent audio noise issue, the minimum switching frequency in QR mode is clamped to 20KHz.z On chip Thermal ShutdownOB2202 provides an on chip thermal shutdown. The IC will stop switching when the junction temperature exceeds the thermal shutdown temperature, typically 155 °C. The IC resumes normal operation when the junction temperature decreased below this temperature.z External Latch TriggeringBy externally forcing a level on pin SS (e.g.., with a signal coming from a temperature sensor) greater than 3.8V, OB2202 can be permanentlylatched-off. To resume normal operation, VCC voltage should go below 6.3V (typical), which implies to unplug the SMPS form the mains.z Programmable Over Power Protection (OPP) CompensationThe variation of max. output power in QR system can be rather large if no compensation is provided. In OB2202, an internal current which is a function of BO voltage is sourced out for Over Power Protection (OPP) compensation. By adjusting the external resistor Rcomp in series with CS pin (Pleae refer to Page 1), an excellent OPP performance can be realized in the universal input range.z Output Over voltage protection (OVP)An output over voltage protection (OVP) is implemented by sensing the auxiliary winding voltage at DEM pin during the flyback phase. The auxiliary winding voltage is a well-defined replica of the output voltage. The OVP works by sampling the plateau voltage at DEM pin during the flyback phase, as shown in Fig.4. A 2 us internal delay (plateau sampling) guarantees a clean plateau, provided that the leakage inductance ringing has been fully damped.If the sampled plateau voltage exceeds the OVP trip level (3.75V), an internal counter starts counting subsequent OVP events. If OVP events are detected in successive 4 cycles, the controller assumes a true OVP and it enters a latch off mode and stops all switching operations. The counter has been added to prevent incorrect OVP detection which might occur during ESD or lightning events. If the output voltage exceeds the OVP trip level less than 4 successive cycles, the internal counter will be cleared and no fault is asserted. z Overload OperationWhen over load (for example, short circuit) occurs, the feedback current is below minimum value and a fault is detected. If this fault is present for more than 80ms, the controller enters an auto-recovery soft burst mode. All pulses are stopped, VCC will drops below UVLO and the controller will try to restart with the power on soft start. The SMPSenters the burst sequence and it resumes operation once the fault disappears.z Programmable Soft StartOB2202 features a programmable soft start to soften the constraints in the power supply during the startup. It is activated during the power on sequence. As soon as VCC reaches UVLO(OFF), an internal trimmed 10uA current is sourced from SS pin and charges the external programming capacitor, the peak current of CS pin is then gradually increased from zero. When SS pin reaches 2.2V, soft start process is over. After soft start process is over, SS pin is clamped to 2V. Every restart attempt is followed by soft start sequence.Figure 5SS pin is also is used for external latch triggering (Please refer to “External Latch Triggering” section).z Gate DriveThe GATE pin is connected to the gate of an external MOSFET for power switch control. Too weak the gate drive results in higher conduction and switch loss of MOSFET while too strong gate drive output compromises the EMI. Good tradeoff is achieved through the built-in totem pole gate drive design with right output strength and dead time control. The low idle loss and good EMI system design is easier to achieve with this dedicated control scheme. An internal 16.5V clamp is added for MOSFET gate protection at high VCC voltage.PACKAGE MECHANICAL DATA8-Pin Plastic DIPMin Max Min MaxA 3.710 5.334 0.146 0.210A1 0.381 0.015A2 3.175 3.600 0.125 0.142B 0.350 0.650 0.014 0.026B1 1.524 (BSC) 0.06 (BSC)C 0.200 0.360 0.008 0.014D 9.000 10.160 0.354 0.400E 6.200 6.600 0.244 0.260E1 7.320 7.920 0.288 0.312e 2.540 (BSC) 0.1 (BSC)L 2.921 3.810 0.115 0.150 E2 8.200 9.525 0.323 0.3758-Pin Plastic SOPDimensions In Millimeters Dimensions In Inches SymbolMin Max Min MaxA 1.350 1.750 0.053 0.069A1 0.050 0.250 0.002 0.010 A2 1.250 1.650 0.049 0.065b 0.310 0.510 0.012 0.020c 0.170 0.250 0.006 0.010D 4.700 5.150 0.185 0.203E 3.800 4.000 0.150 0.157E1 5.800 6.200 0.228 0.244e 1.270 (BSC) 0.05 (BSC)L 0.400 1.270 0.016 0.050 θ 0º 8º 0º 8ºIMPORTANT NOTICERIGHT TO MAKE CHANGESOn-Bright Electronics Corp. reserves the right to make corrections, modifications, enhancements, improvements and other changes to its products and services at any time and to discontinue any product or service without notice. Customers should obtain the latest relevant information before placing orders and should verify that such information is current and complete.WARRANTY INFORMATIONOn-Bright Electronics Corp. warrants performance of its hardware products to the specifications applicable at the time of sale in accordance with its standard warranty. Testing and other quality control techniques are used to the extent it deems necessary to support this warranty. Except where mandated by government requirements, testing of all parameters of each product is not necessarily performed.On-Bright Electronics Corp. assumes no liability for application assistance or customer product design. Customers are responsible for their products and applications using On-Bright’s components, data sheet and application notes. To minimize the risks associated with customer products and applications, customers should provide adequate design and operating safeguards.LIFE SUPPORTOn-Bright Electronics Corp.’s products are not designed to be used as components in devices intended to support or sustain human life. On-bright Electronics Corp. will not be held liable for any damages or claims resulting from the use of its products in medical applications.MILITARYOn-Bright Electronics Corp.’s products are not designed for use in military applications. On-Bright Electronics Corp. will not be held liable for any damages or claims resulting from the use of its products in military applications.。
OB2202_Datasheet_Raiser_081014

OB2202Quasi-Resonant Flyback PWM Controller GENERAL DESCRIPTIONOB2202 is a highly integrated Quasi-Resonant (QR) controller optimized for high performance offline flyback converter applications. At normal load condition, it operates in QR mode with minimum drain voltage switching. To meet the CISPR-22 EMI starting at 150KHz, the maximum switching frequency is internally limited to 130KHz. It operates in PFM mode for high power conversion efficiency at light load condition. When the loading is very small, the IC operates in ‘Extended Burst Mode’ to minimize the switching loss. As a result, lower standby power consumption and higher conversion efficiency can be achieved. OB2202 offers comprehensive protection coverage including Cycle-by-Cycle Current Limiting, VCC Under Voltage Lockout(UVLO), Programmable Output Over Voltage Protection(OVP), VCC Clamp, Gate Clamp, Over Load Protection(OLP), On-chip Thermal Shutdown, Programmable Soft Start, Programmable Brownout Protection, ProgrammableOver Power Protection (OPP) Compensation, and External Latch Triggering, Max On-time Limit, etc.OB2202 is offered in SOP-8 and DIP-8 packages.FEATURES■ Multi-Mode Operation Quasi-Resonant Operation at Normal Loading Pulse Frequency Modulation (PFM) Operation at Light Load Burst Mode at No Load■ Programmable Brownout Protection and Line OVP Protection■ Excellent OPP Compensation ■ 130KHz Maximum Frequency Limit ■ Internal Minimum T_off for Ringing Suppression ■ 35us Maximum On Time Limit ■ 50us Maximum Off Time Limit ■ Internal Leading Edge Blanking ■ Programmable Soft-start■ Cycle-by-cycle Current Limiting ■ External Latch Triggering ■ Internal Thermal Shutdown■ 1A Peak Current Sink/Source Capability ■ Programmable Output OVP APPLICATIONS Offline AC/DC flyback converter for■ Power Adaptor and Open-frame SMPS■ LCD Monitor/TV/PC/Set-Top Box PowerSupplies■ NB/DVD/Portable DVD Power SuppliesTYPICAL APPLICATIONO nf i de nt i a l toR a is e rOB2202Quasi-Resonant Flyback PWM Controller GENERAL INFORMATIONPin ConfigurationThe pin map of OB2202 in DIP8 and SOP8 packageOrdering Information Part Number Description OB2202AP 8 Pin DIP, Pb free in Tube OB2202CP 8 Pin SOP, Pb free in Tube OB2202CPA 8 Pin SOP, Pb free in T&R Note: All Devices are offered in Pb-free Package if not otherwise noted.Package Dissipation Rating PackageR θJA (°C/W)DIP8 90 SOP8 150Absolute Maximum RatingsParameter Value VCC Zener Clamp Voltage31 VVCC Clamp ContinuousCurrent10 mA SSInput Voltage-0.3 to 7VFB Input Voltage -0.3 to 7V CS Input Voltage-0.3 to 7V DEM Input Voltage -0.3 to 7V BO Input Voltage-0.3 to 7V Min/Max Operating JunctionTemperature TJ-20 to 150oCMin/Max Storage Temperature T stg-55 to 150 o C Lead Temperature (Soldering, 10secs)260 o C Note: Stresses beyond those listed under “absolute maximumratings” may cause permanent damage to the device. These are stress ratings only, functional operation of the device at these or any other conditions beyond those indicated under “recommended operating conditions” is not implied. Exposure to absolute maximum-rated conditions for extended periods may affect device reliability.O n -B ri g ht Co nf i de nt i a l toR a is e rOB2202Quasi-Resonant Flyback PWM Controller Marking InformationSOP8Y: Year Code (0-9) WW: Week Code (1-52)C: SOP8P:lead-free s: internal codeDIP8Y: Year Code (0-9) WW: Week Code (1-52)A: DIP8P:lead-frees: internal codeL T Y W WO B 2202A PsTERMINAL ASSIGNMENTSPin Num Pin Name I/O Description 1 SS I/O Multi-functional pin. One function is for soft-start programming byconnecting a capacitor from SS to GND. Another function is for external latch triggering by pulling SS up to a voltage higher than 3.8V.2FBI/O Feedback input pin. PWM duty cycle is determined by voltage level into thispin and current-sense signal level at Pin 3. The voltage level at this pin also controls the mode of operation in one of the three modes: quasi-resonant (QR), pulse frequency modulation mode (PFM) and burst mode (BM). 3 CS I Current sense input. 4 GND P Ground for internal circuitry.5 GATE O Totem-pole gate drive output for power MOSFET.6 VCC P Chip DC power supply pin.7 DEMI/O Input from auxiliary winding for demagnetization timing. Also this pin isused for output over voltage protection (Load OVP).8 BOI/O Brownout and Line OVP detection pin. Connect a resistor divider from linevoltage to this pin to detect line voltage. If this pin drops below 0.5V and lasts for 50ms, brownout protection will be triggered and PWM output will be disabled. This pin is also used as line OVP sense input.O n -B ri g ht Co nf i de nt i a l toR is e rBLOCK DIAGRAMRECOMMENDED OPERATING CONDITIONSymbol Parameter Min Max UnitVCC VCC Supply Voltage 11 28 VT A Operating Ambient Temperature-20 85 oCO n -B ri g ht Co nf iELECTRICAL CHARACTERISTICS(T A = 25O C, VCC=16V, if not otherwise noted)V TH _DEM_hystHysteresis for DEMcomparator20 mVV DEM _clamp(neg) Negative clampvoltage -0.7 VV DEM _clamp(pos) Positive clampvoltage5.8 VT supp Suppression of thetransformer ringing atstart of secondary stroke2 usecT OUT Timeout after lastdemag transistion5 usecT DEM_delay Demag propagationdelay150 nsecV TH _OVP Output OVP triggerpoint3.75 VT_ovp_plateau OVP plateausampling after switching off2 usec N_true_OVP Number ofsubsequent cycles to be true OVP4 Soft Start Section Iss Soft start charge current8.5 10 11.5 uAV TH _ss_over Soft start over threshold voltage2.05 2.2 2.4 VV TH _ss_clamp SS clamp voltage after soft start is over2 VI SS _clamp_sink Maximum sink current capability when SS is clamped200 uAV SS _clamp SS pin high clamp voltage5.8 VTimer Section F _burst Burst mode switching frequency20 KHzF_QR_clamp_h Frequency high clamp in QR mode115 130 145 KHzF_QR_clamp_l Frequency low clamp in QR mode17 20 27 KHzTon_max Maximum on time 25 35 42 usec Toff_max Maximum off time 40 50 60 usec Thermal ProtectionT_shutdown Thermal shutdown temperature140 ◦CLatch ProtectionV_latch_trigger External latch trigger threshold voltage atSS pinSS pin pull up currentshould be larger than 200uA 3.75 V V_latch_release VCC latch release voltage6 VBrownout Protection and Line OVP Protection Vth_BO Brownout comparator 0.5 VO n -B ri g ht Co nf i de nt i a l toR a is e rthresholdVth_line_OVP Line OVP comparator threshold2 VT D _BO Brownout debounce time50 msIBO_hys BO output current for BO hysteresis programming1 uAGate Drive Output VOL Output Low Level Io = 20 mA (sink) 0.3 V VOH Output High Level Io = 20 mA (source) 11 V VG_Clamp Output Clamp Voltage LevelVCC =20V 15 VT_r Output Rising Time CL = 1nf 20 80 120 nSec T_f Output Falling Time CL = 1nf 10 20 70 nSecOn -B ri g ht Co nf i de nt i a l toR ais e rCHARACTERIZATION PLOTSOPERATION DESCRIPTIONQuasi-Resonant (QR) converter typically features lower EMI and higher power conversion efficiency compared to conventional hard-switched converter with a fixed switching frequency. OB2202 is a highly integrated QR controller optimized for offline flyback converter applications. The built-in advanced energy saving with high level protection features provide cost effective solutions for energy efficient power supplies. z Startup Current and Start up ControlStartup current of OB2202 is designed to be very low so that VCC could be charged up above UVLO(OFF) threshold level and device starts up quickly. A large value startup resistor can therefore be used to minimize the power loss yet reliable startup in application. For a typical AC/DC adaptor with universal input range design, a 2 M Ω, 1/8 W startup resistor could be used together with a VCC capacitor to provide a fast startup and yet low power dissipation design solution.z Operating CurrentThe operating current of OB2202 is very low. Good efficiency is achieved by the low operating current together with extended burst mode control schemes at No/light conditions.z Multi-Mode Operation for High Efficiency OB2202 is a multi-mode QR controller. The controller changes the mode of operation according to FB voltage, which reflects the line and load conditions.■ Under normal operating conditions (FB>Vth2, Figure 1), the system operates in QR mode. Thefrequency varies depending on the line voltage andthe load conditions. Therefore, the system mayactually work in DCM when 130KHz frequencyclamping is reached. System design should beoptimized such that the operation frequency iswithin the range specified at full loading conditionsand in universal AC line input range.■ At light load condition (Vth1<VFB<Vth2, Figure1), the system operates in PFM (pulse frequencymodulation) mode for high power conversionefficiency. In PFM mode, the “ON” time in aswitching cycle is fixed and the system modulates the frequency according to the load conditions.Generally, in flyback converter, the decreasing ofloading results in voltage level decreasing at FB pin.The controller monitors the voltage level at FB andcontrol the switching frequency. However, the valley switching characteristic is still preserved inPFM mode. That is, when loading decreases, the system automatically skip more and more valleys and the switching frequency is thus reduced. In such way, a smooth frequency foldback is realized and high power conversion efficiency is achieved. ■ At zero load or very light load conditions (VFB<Vth1), the system operates in On-Bright’s proprietary “extended burst mode”. In thiscondition, voltage at FB is below burst mode threshold level, Vth1. The Gate drive output switches only when VCC voltage drops below a preset level or FB input is active to output an on state. Otherwise the gate drive remains at off state to minimize the switching loss thus reduce thestandby power consumption to the greatest extend. In extended burst mode, the switching frequency is fixed to 22KHz, in this way, possible audio noise is eliminated.Figure 1 z Demagnetization Detection The transformer core demagnetization is detected by monitoring the voltage activity on the auxiliary windings through DEM pin. This voltage features a flyback polarity. A new cycle starts when the power switch is activated. After the on time (determined by the CS voltage and FB), the switch is off and the flyback stroke starts. After the flyback stroke, the drain voltage shows an oscillation with a frequency of approximately d p C L π2/1, where p L is the primary self inductance of the transformer and d C is the capacitance on the drain node, as shown in Fig.2. O n -B ri g ht Co nf i de nt i a l toR a is e rFigure 2The typical detection level is fixed at 75mV at the DEM pin. Demagnetization is recognized by detection of a possible “valley” when the voltage at DEM is below 75mV in falling edge. DEM detection is suppressed during the ringing suppression time T supp (please refer to “Ringing Suppression Timer ” section).z Current Sensing and Leading EdgeBlankingCycle-by-Cycle current limiting is offered in OB2202 current mode control. The switch current is detected by a sense resistor into the CS pin. An internal leading edge blanking circuit chops off the sense voltage spike at initial MOSFET on state due to snubber diode reverse recovery so that the external RC filtering on sense input is no longer needed. The current limit comparator is disabled and cannot turn off the external MOSFET during the blanking period. The PWM duty cycle is determined by the current sense input voltage and the FB input voltage.z Maximum and Minimum On-TimeThe minimum on-time of the system is determined by the LEB time (typical 350ns). The IC limits the on-time to a maximum time of 35us.z Ringing Suppression TimerA ringing suppression timer T supp is implemented in OB2202. In normal operation, T supp starts when CS reaches the feedback voltage FB, the external power switch is set to off state. During T supp , the external power switch remains in off state and cannot be turned on gain. The ringing suppression time is necessary in applications where the transformer has a large leakage inductance, particularly at low output voltages or startup. In OB2202, the ringing suppression timer T supp is set to 2us internally.z Programmable Brownout Protection andLine OVP ProtectionBy monitoring the level on pin BO during normal operation, the controller protects the SMPS against low main condition, as shown in Fig.3. When BO level falls below 0.5V, brownout is triggered, the controller stops pulsing and disable internal source current for brownout hysteresis. BO pin is also used for line OVP sense input, when BO level is above 2.0V, line OVP is triggered and stops pulsing.z Maximum Frequency ClampAccording to the QR operation principle, the switching frequency is inversely proportional to the output power. Therefore, when the output power decreases, the switching frequency can become rather high without limiting. To meet the CISPR-22 EMI limit starting at 150KHz, the maximum switching frequency in OB2202 is internally limited to 130KHz.z On chip Thermal ShutdownOB2202 provides an on chip thermal shutdown. The IC will stop switching when the junction temperature exceeds the thermal shutdown temperature, typically 140 °C. The IC resumes normal operation when the junction temperature decreased below this temperature.z External Latch TriggeringBy externally forcing a level on pin SS (e.g.., with a signal coming from a temperature sensor) greater than 3.75V, OB2202 can be permanently latched-off. To resume normal operation, VCC voltage should go below 6V, which implies to unplug the SMPS form the mains.z Programmable Over Power Protection(OPP) CompensationO n -B ri g ht Co nf i do e rThe variation of max output power in QR system can be rather large if no compensation is provided. In OB2202, an internal current which is a function of BO voltage is sourced out for Over Power Protection (OPP) compensation. By adjusting the external resistor Rcomp in series with CS pin (Pleae refer to Page 1), an excellent OPP performance can be realized in the universal input range.z Output Over voltage protection (OVP)An output over voltage protection (OVP) is implemented by sensing the auxiliary winding voltage at DEM pin during the flyback phase. The auxiliary winding voltage is a well-defined replica of the output voltage. The OVP works by sampling the plateau voltage at DEM pin during the flyback phase, as shown in Fig.4. A 2 us internal delay (plateau sampling) guarantees a clean plateau, provided that the leakage inductance ringing has been fully damped.Figure 4If the sampled plateau voltage exceeds the OVP trip level (3.75V), an internal counter starts counting subsequent OVP events. If OVP events are detected in successive 4 cycles, the controller assumes a true OVP and it enters a latch off mode and stops all switching operations. The counter has been added to prevent incorrect OVP detection which might occur during ESD or lightning events. If the output voltage exceeds the OVP trip level less than 4 successive cycles, the internal counter will be cleared and no fault is asserted.zOverload OperationWhen over load (for example, short circuit) occurs,the feedback current is below minimum value and a fault is detected. If this fault is present for more than 80ms, the controller enters an auto-recovery soft burst mode. All pulses are stopped, VCC willdrops below UVLO and the controller will try to restart with the power on soft start. The SMPS enters the burst sequence and it resumes operation once the fault disappears.z Programmable Soft StartOB2202 features a programmable soft start to soften the constraints in the power supply during the startup. It is activated during the power on sequence. As soon as VCC reaches UVLO(OFF), an internal trimmed 10uA current is sourced from SS pin and charges the external programmingcapacitor, the peak current of CS pin is then gradually increased from zero. When SS pin reaches 2.2V, soft start process is over. After soft start process is over, SS pin is clamped to 2V. Every restart attempt is followed by soft start sequence.Figure 5SS pin is also is used for external latch triggering (Please refer to “External Latch Triggering ” section).z Gate DriveThe GATE pin is connected to the gate of an external MOSFET for power switch control. Too weak the gate drive results in higher conduction and switch loss of MOSFET while too strong gate drive output compromises the EMI.Good tradeoff is achieved through the built-in totem pole gate drive design with right output strength and dead time control. The low idle loss and good EMI system design is easier to achieve with this dedicated control scheme. An internal 16.5V clamp is added for MOSFET gate protection at high VCC voltage.O n -B ri g ht a l oR a is e rPACKAGE MECHANICAL DATA8-Pin Plastic DIPDimensions In Millimeters Dimensions In InchesSymbolMin Max Min MaxA 3.710 5.334 0.146 0.210 A1 0.381 0.015 A2 3.175 3.600 0.125 0.142B 0.350 0.650 0.014 0.026 B1 1.524 (BSC) 0.06 (BSC)C 0.200 0.360 0.008 0.014D 9.000 10.160 0.354 0.400E 6.200 6.600 0.244 0.260 E1 7.320 7.920 0.288 0.312 e 2.540 (BSC) 0.1 (BSC)L 2.921 3.810 0.115 0.150 E2 8.200 9.525 0.323 0.375O n -B ri g ht Co nf i de nt i a l toR a is e r8-Pin Plastic SOPDimensions In Millimeters Dimensions In InchesSymbolMin Max Min MaxA 1.350 1.750 0.053 0.069 A1 0.050 0.250 0.002 0.010 A2 1.250 1.650 0.049 0.065 b 0.310 0.510 0.012 0.020 c 0.170 0.250 0.006 0.010D 4.700 5.150 0.185 0.203E 3.800 4.000 0.150 0.157 E1 5.800 6.200 0.228 0.244 e 1.270 (BSC) 0.05 (BSC)L 0.400 1.270 0.016 0.050 θ 0º 8º 0º 8ºO n -B ri g ht Co nf i de nt i a l toR a is e rIMPORTANT NOTICERIGHT TO MAKE CHANGESOn-Bright Electronics Corp. reserves the right to make corrections, modifications, enhancements, improvements and other changes to its products and services at any time and to discontinue any product or service without notice. Customers should obtain the latest relevant information before placing orders and should verify that such information is current and complete.WARRANTY INFORMATIONOn-Bright Electronics Corp. warrants performance of its hardware products to the specifications applicable at the time of sale in accordance with its standard warranty. Testing and other quality control techniques are used to the extent it deems necessary to support this warranty. Except where mandated by government requirements, testing of all parameters of each product is not necessarily performed.On-Bright Electronics Corp. assumes no liability for application assistance or customer product design. Customers are responsible for their products and applications using On-Bright’s components, data sheet and application notes. To minimize the risks associated with customer products and applications, customers should provide adequate design and operating safeguards.LIFE SUPPORTOn-Bright Electronics Corp.’s products are not designed to be used as components in devices intended to support or sustain human life. On-bright Electronics Corp. will not be held liable for any damages or claims resulting from the use of its products in medical applications.MILITARYOn-Bright Electronics Corp.’s products are not designed for use in military applications. On-Bright Electronics Corp. will not be held liable for any damages or claims resulting from the use of its products in military applications.O n -B ri g ht Co nf i de nt i a l toR a is e r。
quasi-proportional-resonant翻译

quasi-proportional-resonant翻译"Quasi-proportional-resonant"的翻译是"准比例谐振"。
这个术语是用来描述控制系统中一种特殊的控制策略。
在准比例谐振控制中,控制系统的输入信号通过一个准比例谐振滤波器进行滤波处理,以提取出特定频率范围内的信号。
这种控制策略常用于工程中的振动控制、噪声抑制和多频谐振控制等应用领域。
以下是12个使用准比例谐振控制相关词汇和双语例句:1. Quasi-proportional-resonant controller:准比例谐振控制器Example: The quasi-proportional-resonant controller effectively suppresses the vibrations in the system.2. Resonance frequency:谐振频率Example: The resonance frequency of the system can be tuned using a quasi-proportional-resonant filter.3. Control strategy:控制策略Example: The quasi-proportional-resonant control strategy provides better performance compared to traditional control methods.4. Vibration control:振动控制Example: The quasi-proportional-resonant technique is widely used for vibration control in mechanical systems.5. Noise suppression:噪声抑制Example: The quasi-proportional-resonant approach effectively suppresses noise for improved signal quality.6. Multi-frequency resonance control:多频谐振控制Example: The quasi-proportional-resonant method allowsfor simultaneous control of multiple resonance frequencies.7. Filtering:滤波处理Example: The quasi-proportional-resonant filter removes unwanted frequency components from the input signal.8. Frequency range:频率范围Example: The quasi-proportional-resonant technique focuses on a specific frequency range for optimal control.9. System stability:系统稳定性Example: The quasi-proportional-resonant control ensures system stability even under varying operating conditions.10. Harmonic suppression:谐波抑制Example: The quasi-proportional-resonant algorithm effectively suppresses harmonic distortions for improved power quality.11. Adaptive control:自适应控制Example: The quasi-proportional-resonant approach allows for adaptive control based on real-time system conditions.12. Control performance:控制性能Example: The quasi-proportional-resonant technique improves the control performance of the system by reducing unwanted vibrations.。
昂宝PFC+QR电源IC OB6663 Data

Loop Protection for PFC and QR Stage (OLP), Programmable Brownout Protection (BOP), AC
n Line Over Voltage Protection(Line OVP),
correction (TM PFC) controller and a Quasi-
Controller and Quasi-Resonant (QR) PWM
Resonant (QR) controller in one chip. TM PFC provides a cost effective solution for optimizing the power factor of 75W+ off line SMPS. QR provides
On ■ Notebook
©On-Bright Electronics
Confidential -1-
Preliminary Datasheet OB_DOC_DS_666301
TYPICAL APPLICATION
OB6663
High Performance TM PFC/QR Combo Controller
■ Cycle-by-Cycle Current Limiting for Both Converters
■ 130KHz Max Frequency Clamping for Both Converters
■ Programmable Brownout Protection (BOP) ■ AC Line Over Voltage Protection(Line OVP) ■ External Programmable Over Temperature
电力电子相关英文缩写

意义 专用集成电路 连续导电模式 恒定导通时间 临界导电模式 断续导电模式 破坏性物理分析 扩展反电动势电压模型 电磁干扰 等效串联电阻 柔性交流输电系统 可编辑逻辑门阵列 复用导通模式 最大功率点跟踪 负温度系数 储能变流器 功率因数校正 脉冲宽度调制 准谐振 角度域重复学习控制器 射频干扰 递推最小二乘法 总谐波失真 不间断电源 可变导通时间 电流过零 电压过零
英文缩写 ASIC CCM COT CRM DCM DPAபைடு நூலகம்EEMF EMI ESR FACTS FPGA MCM MPPT NTC PCS PFC PWM QR RC RFI RLS THD UPS VOT ZCS ZVS
英文全称 application-specific integrated circuit continuous conduction mode constant on-time critical conduction mode discontinuous conduction mode destructive physical analysis extended electromotive force electromagnetic interference equicalent series resistance flexible AC transmission systems field programmable gate array multiplexing-inductor conduction mode maximum power point tracking negative temperature coefficient power control system power factor correction pulse width modulation quasi-resonant repetitive learning control radio frequency interference recursive least square algorithm total harmonic distortion uninterruptible power supply variable on-time zero current switching zero voltage switching