金属工艺学下学期课件第三章-课件
合集下载
金属工艺学课件(PPT49页).pptx
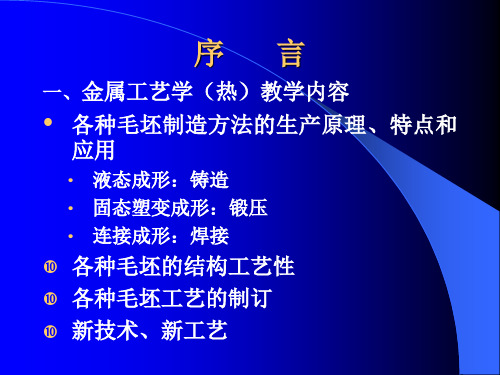
铸造的特点
(1)可以铸造出内腔、外形很复杂的毛 坯。
(2)工艺灵活性大、适应性广。铸件重 量可由几克到几百吨,壁厚可由0.5mm 到1m左右;铸件材料可用铸铁、铸钢、 碳钢和有色金属等。
(3)铸件成本低。 (4)有铸造缺陷,机械性能不如锻件等。
二、砂型铸造生产工艺流程
三、铸造方法分类
Clasfication of foundry Methods
Pouring Melt in the Mold→Solidification→Casting
优点:complex in shape adaptability in technology cheap in production
缺点:lower mechanical properties unstable quality worse work condition
在铸件上从远离冒口或 浇口到冒口或浇口之 间建立一个递增的温 度梯度,从而实现由 远离冒口的部分向冒 口的方向顺序地凝固。
同时凝固原则:
Simultaneously Solidification
是采取工艺措施保 证铸件结构上各部 分之间没有温差或 温差尽量小,使各 部分同时凝固。如 图所示。
二、金属和合金的铸造性能
体收缩率rate of =v0_-v1/v0*100%
volume
Contraction:εv
线收缩率 rate of linear Contraction:
εl=l0-l1/l0*100%
⑵ 收缩的阶段 Contraction Stages
液态收缩 Liquid Contraction 凝固收缩 Solidification Contraction 固态收缩 Solid Contraction 前两个阶段的收缩使合金体积减少,
金属工艺学 课件

应用:铸件、锻件、 应用:铸件、锻件、焊接及其它毛
坯的热处理。 坯的热处理。
1、完全退火:将亚共析钢加热到Ac3线以上 、完全退火:将亚共析钢加热到 线以上20—30℃,保温后缓慢冷却 线以上 ℃ 保温后缓慢冷却. 2、球化退火 将过共析钢加热到 线以上20—30℃,保温后缓慢冷却 、球化退火: 将过共析钢加热到Ac1线以上 线以上 ℃ 保温后缓慢冷却. 3、低温退火 将钢加热到 线以下, 、低温退火: 将钢加热到Ac1线以下,保温后缓慢冷却 线以下 保温后缓慢冷却. 再结晶退火:消除冲压件冷变形所产生的加工硬化(再结晶温度以上150— 再结晶退火:消除冲压件冷变形所产生的加工硬化(再结晶温度以上 250℃),降低硬度,恢复塑性。 降低硬度, ℃),降低硬度 恢复塑性。
第4 章
12/26/2010 2:47 AM
非金属材料
自学
3 碳氮共渗
12/26/2010 2:47 AM
复习思考题
某汽车齿轮选用20CrMnTi制造,其工艺路线为: 20CrMnTi制造 1 某汽车齿轮选用20CrMnTi制造,其工艺路线为: 下料→锻造→正火① 切削加工→渗碳② 下料→锻造→正火①→切削加工→渗碳②→淬 低温回火④ 喷丸→磨削。请说明① 火③→低温回火④→喷丸→磨削。请说明①、 四项热处理工艺的目的。 ②、③、④四项热处理工艺的目的。 说明固溶强化的强化原理。 2 说明固溶强化的强化原理。
12/26/2010 2:47 AM
正火
将钢加热到Ac3 将钢加热到 线以上30—50 ℃ 线以上 亚共析钢) (亚共析钢)或 Accm以上 以上30——50 过共析钢) ℃ (过共析钢) ,保温后在空气中 冷却。 冷却。得到的是细 珠光体组织( 珠光体组织(索氏 体)。
金属工艺学压力加工上课
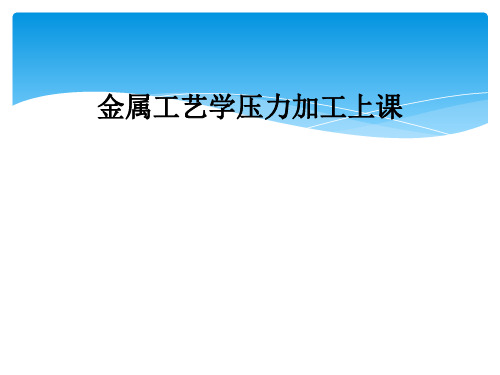
3.模锻斜度
模锻件上平行于锤击方向 ( 垂直于分模面 ) 的外表必须具有斜度 ,以便于从模膛中取出锻件。
工作时,上模与锤头一起作上下往复运动,以迫使 模膛内的金属受压变形,从而获得锻件。
上下模的接触面叫分模面-8。
模膛按其功能分模锻模膛、制坯模膛。
〔一〕模锻模膛:包括预锻模膛和终锻模膛
⑴终锻模膛:使金属坯料最终变形到所要求的形状与尺 寸。
特点:
a.由于模锻需要加热后进展,锻件冷却后尺寸会有 所缩减,所以终锻模膛的尺寸应比实际锻件尺寸放大一 个收缩量。
三、多晶体的塑性变形 1.金属晶粒越细,强度就越大,塑韧性越好。
因此细晶强化是金属的一种很重要的强韧化手段。 2.多晶体塑性变形不均匀。
第二节 塑性变形对金属组织和性能的影响
一、加工硬化
金属发生塑性变形, 随变形度的增大, 金属的强度和硬度显 著提高, 塑性和韧性明显下,这种现象称为加工硬化, 也叫形变 强化。
3. 应力状态的影响 在三向应力状态下,压应力的数目越多,那么
其塑性越好;拉应力的数目越多,那么其塑性越差。
第二章 锻造
❖ 第一节 锻造方法 ❖ 第二节 锻造工艺规程的制订 ❖ 第三节 锻件构造的工艺性
第一节 锻造方法
一、自由锻 自由锻:利用冲击力,使金属在上、下砧铁之间,
产生塑性变形而获得所需形状、尺寸以及内部质量锻件 的一种加工方法。
(2)滚挤模膛
减小坯料某局部的横截面积,以增大另一局部 的横截面积。主要是使金属坯料能够按模锻件的形 状来分布。
⑶弯曲模膛 使坯料弯曲,弯曲后坯料将翻转90°。
⑷切断模膛 在上模与下模的角部组成一对刃口,用来切断金属。
可用于从坯料上切下锻件或从锻件上切钳口,也可用于 多件锻造后别离成单个锻件。
金属工艺学课件(PPT 45页)

金属工艺发展历史
春秋时期 战国时期
铁器开始使用 出现炼钢技术
金属工艺发展历史
铸造技术
中国古代三大铸造技术 泥范(砂型)铸造 铁范(金属型)铸造 失蜡铸造
商周(3000年前) 发明失蜡铸造技术 战国中期 出现金属型铸造 隋唐以后 掌握大型铸件生产技术
金属工艺发展历史
铸造技术实例1
河南安阳武官村出土, 体积庞大,重875kg, 花纹精细,造型精美。
•
每天都是美好的一天,新的一天开启 。20.12.820.12.810:5410:54:0010:54:00Dec- 20
•
人生不是自发的自我发展,而是一长 串机缘 。事件 和决定 ,这些 机缘、 事件和 决定在 它们实 现的当 时是取 决于我 们的意 志的。2020年12月8日 星期二 10时54分0秒 Tuesday, December 08, 2020
•
做专业的企业,做专业的事情,让自 己专业 起来。2020年12月上 午10时54分20.12.810:54December 8, 2020
•
时间是人类发展的空间。2020年12月8日星期 二10时 54分0秒10:54:008 December 2020
•
科学,你是国力的灵魂;同时又是社 会发展 的标志 。上午10时54分0秒上 午10时 54分10:54:0020.12.8
锻造技术和焊接技术
锻造技术和焊接技术在中国有着攸久的历史 3000年前,商朝就用锻造技术制作兵刃 战国时期,扩大到日常用品 战国时期,应用了钎焊技术
金属工艺发展历史
锻造技术和焊接技术
秦皇陵中铜车马上的金银饰件用无机粘接挤固 定
金属工艺发展历史
世界上金属加工工艺最早专著-《天工开物》
《金属工艺学》课件
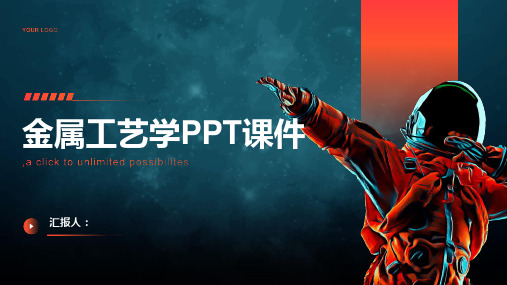
金属的加工工艺
金属的铸造工艺
铸造工艺简介:将熔融的金属倒入模具中,冷却后形成所需形状的工艺 铸造方法:砂型铸造、金属型铸造、离心铸造等 铸造材料:铁、钢、铝、铜、锌等 铸造工艺特点:可生产复杂形状的零件,成本低,生产效率高
金属的锻造工艺
锻造方法:自由锻造、模锻、 冲压、挤压等
锻造工艺:将金属加热到一 定温度,通过锤打、挤压等 方式改变其形状和性能
切削工具:包括车刀、铣刀、钻头、 锯片等
切削方法:包括车削、铣削、钻削、 锯削等
切削参数:包括切削速度、进给量、 切削深度等
切削质量:包括表面粗糙度、尺寸精 度、形位精度等
切削效率:包括生产效率、能耗、刀 具寿命等
金属的热处理工艺
热处理的原理和分类
热处理的原理:通过改变金属的微观结构, 提高其力学性能和耐腐蚀性
金属的表面处理技术
表面涂装技术
目的:保护金 属表面,提高 耐腐蚀性、耐
磨性等性能
主要方法:电 镀、喷涂、热
浸镀等
电镀:利用电 解原理,在金 属表面形成一 层金属或合金
镀层
喷涂:利用高 压气流将涂料 喷涂到金属表 面,形成一层
保护层
热浸镀:将金 属加热到一定 温度,使其表 面形成一层金 属或合金镀层
智能化:利用人工智能技术, 实现金属加工的自动化、智 能化
数字化:利用数字化技术, 实现金属加工的精确控制和
优化
绿色化:采用环保技术和材 料,实现金属加工的绿色化
和可持续发展
绿色环保和可持续发展要求
减少能源消耗:提高能源利用效率, 降低生产过程中的能源消耗
循环利用:提高金属材料的回收利 用率,实现资源的循环利用
添加标题
添加标题
金属工艺学第3章

上一页 下一页 返回
第二节 铁碳合金相图
• 2.亚共析钢 • 根据Fe-Fe3C相图,含碳量小于0.77%的亚共析钢从液态到
结晶终了的结晶过程与共析钢相同,合金全部转变为单相奥氏体。当 亚共析钢继续冷却到与GS线相交的温度时,从奥氏体中开始析出铁 素体,获得铁素体和奥氏体组织。由于铁素体只能溶解很少的碳,所 以合金中大部分的碳留在了奥氏体中,使剩余奥氏体的溶碳量有所增 加。随着温度的不断下降,析出的铁素体逐渐增多,剩余的奥氏体量 逐渐减少,而奥氏体的溶碳量沿GS线逐渐增加。当温度下降到与P SK线相交的温度(727℃)时,奥氏体的溶碳量达到0.77% ,此时剩余的奥氏体发生共析转变,转变成珠光体。
• 3.渗碳体 • 渗碳体是铁和碳相互作用而形成的一种具有复杂斜方晶体结构的金属
化合物,常用分子式Fe3C表示。渗碳体中碳的质量分数为6.69 %,熔点为1227℃,硬度很高(800HBW),塑性和韧性极 低,硬而脆。渗碳体分布在钢中主要起强化作用,它以多种晶粒形态 存在于钢中,其数量、形状、大小及分布状况对钢的性能影响很大。
• 3.过共析钢 • 当含碳量大于0.77%的过共析钢冷却到与AE线相交的结晶终了
温度时,获得单相奥氏体组织。
上一页 下一页 返回
第二节 铁碳合金相图
• 继续冷却到与ES线相交的温度时,由于温度的降低,碳在奥氏体中 的溶解度降低,过剩的碳以渗碳体(这种从奥氏体中析出的渗碳体称 为二次渗碳体)的形式从奥氏体共析钢的显微组织中沿晶界析出,随 着温度的下降,析出的Fe3CⅡ不断增多,并沿晶界呈网状分布, 奥氏体中的溶碳量逐渐下降,当温度降低到727℃时,剩余奥氏体 的溶碳量正好为0.77%,于是发生共析转变而形成珠光体。温度 再继续下降,合金的组织基本不变,最终获得珠光体和二次渗碳体组 织。图3-11所示为过共析钢的显微组织(图3-11中黑色为层 片状的珠光体,白色为网状的二次渗碳体)。过共析钢的室温平衡组 织为珠光体和二次渗碳体,但随着含碳量的增加,钢中的二次渗碳体 量也逐渐增多。过共析钢结晶组织转变过程如图3-12所示。
第二节 铁碳合金相图
• 2.亚共析钢 • 根据Fe-Fe3C相图,含碳量小于0.77%的亚共析钢从液态到
结晶终了的结晶过程与共析钢相同,合金全部转变为单相奥氏体。当 亚共析钢继续冷却到与GS线相交的温度时,从奥氏体中开始析出铁 素体,获得铁素体和奥氏体组织。由于铁素体只能溶解很少的碳,所 以合金中大部分的碳留在了奥氏体中,使剩余奥氏体的溶碳量有所增 加。随着温度的不断下降,析出的铁素体逐渐增多,剩余的奥氏体量 逐渐减少,而奥氏体的溶碳量沿GS线逐渐增加。当温度下降到与P SK线相交的温度(727℃)时,奥氏体的溶碳量达到0.77% ,此时剩余的奥氏体发生共析转变,转变成珠光体。
• 3.渗碳体 • 渗碳体是铁和碳相互作用而形成的一种具有复杂斜方晶体结构的金属
化合物,常用分子式Fe3C表示。渗碳体中碳的质量分数为6.69 %,熔点为1227℃,硬度很高(800HBW),塑性和韧性极 低,硬而脆。渗碳体分布在钢中主要起强化作用,它以多种晶粒形态 存在于钢中,其数量、形状、大小及分布状况对钢的性能影响很大。
• 3.过共析钢 • 当含碳量大于0.77%的过共析钢冷却到与AE线相交的结晶终了
温度时,获得单相奥氏体组织。
上一页 下一页 返回
第二节 铁碳合金相图
• 继续冷却到与ES线相交的温度时,由于温度的降低,碳在奥氏体中 的溶解度降低,过剩的碳以渗碳体(这种从奥氏体中析出的渗碳体称 为二次渗碳体)的形式从奥氏体共析钢的显微组织中沿晶界析出,随 着温度的下降,析出的Fe3CⅡ不断增多,并沿晶界呈网状分布, 奥氏体中的溶碳量逐渐下降,当温度降低到727℃时,剩余奥氏体 的溶碳量正好为0.77%,于是发生共析转变而形成珠光体。温度 再继续下降,合金的组织基本不变,最终获得珠光体和二次渗碳体组 织。图3-11所示为过共析钢的显微组织(图3-11中黑色为层 片状的珠光体,白色为网状的二次渗碳体)。过共析钢的室温平衡组 织为珠光体和二次渗碳体,但随着含碳量的增加,钢中的二次渗碳体 量也逐渐增多。过共析钢结晶组织转变过程如图3-12所示。
金属工艺及实训03PPT课件

模块十 铁碳合金组织与铁碳合金相图
⑴ 特性点 Fe-Fe3C相图中各个特性点的温度、成分及含义见表4-1。
1.相图分析
模块十 铁碳合金组织与铁碳合金相图
⑵ 特性线 ① ACD线——液相线,是不同成分合金开始结晶的温度线。 此线以上合金处于液态;AC线对应的液态合金缓冷到AC线所对应的温度,开始结晶出奥氏体,CD线对应的液态合金缓冷到CD线所对应的温度时开始结晶出一次渗碳体,用Fe3CI表示。 ② AECF线——固相线,是各种成分合金结晶温度的终止线。 此线以下合金均为固态。
模块十 铁碳合金组织与铁碳合金相图
⑵ 特性线 ④ ES线——又称Acm线,是碳在奥氏体中的溶解度曲线(随温度变化,奥氏体的溶碳量将沿ES线变化);是冷却时由奥氏体中析出二次渗碳体的开始线。 凡是含碳量在0.77%以上的铁碳合金,自1148℃冷却到727℃的过程中,都将从奥氏体中析出二次渗碳体,用符号Fe3CⅡ表示。
模块十 铁碳合金组织与铁碳合金相图
1.铁素体 碳溶于α-Fe形成的间隙固溶体,称为铁素体,用F表示。 铁素体的显微组织与纯铁相同,在显微镜下呈明亮的多边体晶粒组织(图1-30) α-Fe是体心立方晶格,其晶格间隙的直径很小,溶碳能力极差。(727℃时ω(C)=0.0218%) 铁素体的力学性能与纯铁相近,强度、硬度较低,塑性、韧性较好。 铁素体在770℃以下具有铁磁性,在770℃以上则失去铁磁性。
模块十 铁碳合金组织与铁碳合金相图
2.奥氏体 碳溶于γ-Fe中形成的间隙固溶体,称为奥氏体,用A表示。 奥氏体存在于727℃以上的高温范围内,高温下奥氏体的显微组织(图1-32),其晶粒也呈多边形,但晶界较平直。 由于γ-Fe是面心立方晶格,致密度虽然高于体心立方晶格的α-Fe,但由于其晶格间隙的直径比α-Fe大,所以溶碳能力较强。(ω(C)=0.77%~2.11%) 随温度的下降,溶碳能力逐渐降低。
《金属工艺学》课件
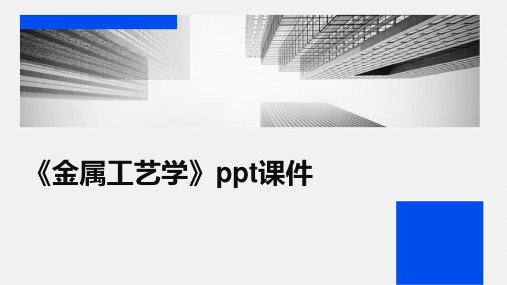
金属工艺学分类
金属工艺学可以根据加工对象和应用 领域分为多种分支,如铸造、锻造、 焊接、切削加工、热处理等。
金属工艺学的应用领域
机械制造业
航空航天业
金属工艺学在机械制造业中应用广泛,涉 及各种零件的加工、装配和维修。
航空航天器制造需要高精度和高性能的金 属材料和加工技术,金属工艺学在航空航 天业中发挥着重要作用。
汽车制造业
电子工业
汽车制造业需要大量金属材料和加工技术 ,包括车身、底盘、发动机等部件的制造 和装配。
电子工业中,金属材料广泛应用于电路板 、连接器、散热器等部件的制造。
金属工艺学的历史与发展
01
古代金属工艺
早在公元前,人类就开始使用金属材料,如青铜、铁等,用于制造工具
、武器和饰品。
02
工业革命时期的金属工艺
退火与正火工艺
退火工艺
退火是一种将金属加热到适当温度,保温一段时间,然后缓慢冷却至室温的热 处理工艺。其主要目的是消除金属内部的应力,提高其塑性和韧性,以便于进 一步加工。
正火工艺
正火是将金属加热到适当温度,保持一定时间后,在静止空气中冷却的热处理 工艺。其主要目的是细化金属的晶粒,提高其机械性能,如强度和韧性。
。
焊接缺陷及防止
03
焊接过程中可能出现气孔、夹渣、裂纹等缺陷,需采取相应措
施进行防止。
金属的切削加工工艺
切削加工原理
通过刀具对金属工件进行切削,以去除多余的金属材料,实现工 件形状和尺寸的加工。
切削加工方法分类
根据切削加工的特点和应用,可分为车削、铣削、钻削、磨削等 。
切削加工技术要求
切削加工过程中需要考虑刀具材料、切削液、切削参数等因素, 以确保加工质量和效率。
金属工艺学可以根据加工对象和应用 领域分为多种分支,如铸造、锻造、 焊接、切削加工、热处理等。
金属工艺学的应用领域
机械制造业
航空航天业
金属工艺学在机械制造业中应用广泛,涉 及各种零件的加工、装配和维修。
航空航天器制造需要高精度和高性能的金 属材料和加工技术,金属工艺学在航空航 天业中发挥着重要作用。
汽车制造业
电子工业
汽车制造业需要大量金属材料和加工技术 ,包括车身、底盘、发动机等部件的制造 和装配。
电子工业中,金属材料广泛应用于电路板 、连接器、散热器等部件的制造。
金属工艺学的历史与发展
01
古代金属工艺
早在公元前,人类就开始使用金属材料,如青铜、铁等,用于制造工具
、武器和饰品。
02
工业革命时期的金属工艺
退火与正火工艺
退火工艺
退火是一种将金属加热到适当温度,保温一段时间,然后缓慢冷却至室温的热 处理工艺。其主要目的是消除金属内部的应力,提高其塑性和韧性,以便于进 一步加工。
正火工艺
正火是将金属加热到适当温度,保持一定时间后,在静止空气中冷却的热处理 工艺。其主要目的是细化金属的晶粒,提高其机械性能,如强度和韧性。
。
焊接缺陷及防止
03
焊接过程中可能出现气孔、夹渣、裂纹等缺陷,需采取相应措
施进行防止。
金属的切削加工工艺
切削加工原理
通过刀具对金属工件进行切削,以去除多余的金属材料,实现工 件形状和尺寸的加工。
切削加工方法分类
根据切削加工的特点和应用,可分为车削、铣削、钻削、磨削等 。
切削加工技术要求
切削加工过程中需要考虑刀具材料、切削液、切削参数等因素, 以确保加工质量和效率。
- 1、下载文档前请自行甄别文档内容的完整性,平台不提供额外的编辑、内容补充、找答案等附加服务。
- 2、"仅部分预览"的文档,不可在线预览部分如存在完整性等问题,可反馈申请退款(可完整预览的文档不适用该条件!)。
- 3、如文档侵犯您的权益,请联系客服反馈,我们会尽快为您处理(人工客服工作时间:9:00-18:30)。
第三章 特种加工
3.1 电火花加工
二、电火花加工的基本工艺规律 1.加工速度和工具损耗速度
当电火花加工时,工具和工件(正、负极)同时遭到不 同程度的电蚀,单位时间内工件的电蚀量称为加工速度, 即生产率;单位时间内工具的电蚀量称为损耗速度,它们 是一个问题的两个方面。 (1)加工速度
一般采用体积加工速度来表示,有时也用质量加工速度 来表示,以方便测量正负极的蚀除速度与单个脉冲能量、 脉冲频率成正比
第三章 特种加工
3.1 电火花加工
三、电火花加工的应用范围 3.电火花线切割加工
电火花线切割加工原理图 1-储丝筒 2-工作台驱动电机 3-导轮 4-电极丝
5-工件 6-脉冲电源
第三章 特种加工
3.1 电火花加工
三、电火花加工的应用范围 3.电火花线切割加工
与成型穿孔加工比较,有如下特点: 1)由于加工表面的轮廓是由CNC控制的复合运动所获得,所
第三章 特种加工
3.1 电火花加工
三、电火花加工的应用范围 3.电火花线切割加工
Dk6825数控旋转电火花机床 加工范围
电火花镗磨
第三章 特种加工
3.2 电解加工
一、电解加工的原理和特点 1.电解加工的原理
电解加工示意图 1-直流电源 2-工具阴极 3-工件阳极
4-电解液泵 5-电解液
电解加工成型原理
3.1 电火花加工
一、电火花加工的原理和特点
2.电火花加工的特点 (1)可加工任何高强度、高硬度、高韧性、高熔点的难切削加工
的导电材料,不受被加工材料的物理机械性能影响 (2)工具的硬度可以低于被加工材料的硬度。 (3)加工时无显著机械切削力,工具电极并不回转,有利于小孔
、窄槽、型孔、曲线孔及薄壁零件加工,也适合于精密细微 加工。 (4)脉冲参数可任意调节,加工中只要更换工具电极或采用阶梯 形工具电极就可以在同一机床上连续进行粗、半精和精加工 。 (5)通常效率低于切削加工,可先用切削加工粗加工,再用电火 花精加工。 (6)放电过程中有一部分能量消耗于工具电极而导致电极消耗,
加工斜度的产生
尖角变圆现象
a)加工外表面 b)加工内表面
1-工件电极
2-工具电极
第三章 特种加工
3.1 电火花加工
二、电火花加工的基本工艺规律
3.影响表面质量的因素
电火花加工的表面质
量主要包括三个方面:
(1)表面粗糙度
影响表面粗糙度的主
要因素是单个脉冲能量
(2) 表面变质层
(3)表面力学性能
电火花加工后的工件
精品
金属工艺学下学期课件第三章
第三章 特种加工
3.1 电火花加工
一、电火花加工的原理和特点 1.电火花加工原理
进行电火花加工应具备如下条件: (1)工具电极和工件电极之间必须保持一定的间隙。 (2)必须采用脉冲电源。 (3)必须在有一定绝缘性能的工作液中进行火花放电
脉冲电源电压波形
第三章 特种加工
第三章 特种加工
3.2 电解加工
二、电解加工的基本工艺规律 1.生产率极其影响因素
电解加工的生产率,以单位时间内去除的金属体积或质 量来衡量,用mm3/min或g/min来表示 (1)电化学当量对生产率的影响
由实践得知,电解时工件阳极上溶解或析出的物质的量 与电解电流I 和电解时间t 成正比 (2)电流密度对生产率的影响 (3)加工间隙对生产率的影响
表面易形成残余应力,且 大多为拉应力
放电痕剖面显示的表面变质层
第三章 特种加工
3.1 电火花加工
三、电火花加工的应用范围 1.穿孔加工
常指贯通的等截面或变截 面的二维型孔的电火花加工
电
圆孔
方槽
火 花
小
孔
加
工
异电火花加工
三、电火花加工的应用范围 2.电火花型腔加工
电火花型腔加工 a)普通工作电极 b)工具电极开有冲油孔
第三章 特种加工
3.1 电火花加工
二、电火花加工的基本工艺规律 1.加工速度和工具损耗速度 (2)工具的相对损耗 1) 极性效应 2) 覆盖效应 3) 传热效应 4) 沉积效应 5) 选择合适的工具电极材料
第三章 特种加工
3.1 电火花加工
二、电火花加工的基本工艺规律 2.影响加工精度的主要因素 (1) 放电间隙的大小和一致性 (2) 工具电极的损耗及“二次放电”
第三章 特种加工
3.3 超声波加工
一、超声波加工的原理和特点 1.超声波加工(ultrasonic machining,USM)的原理
利用工具端面作超声频振动,通过磨料悬浮液加工硬脆 材料的一种加工方法
第三章 特种加工
3.3 超声波加工
一、超声波加工的原理和特点 2.超声波加工的特点
(1) 由于去除被加工材料是靠机械撞击、抛磨和空化作用, 适合于加工各种硬脆材料 (2) 可获得较高的加工精度(尺寸精度可达0.005~0.02mm) 和较低的表面粗糙度(Ra值为0.05~0.2 ) (3) 加工过程中不需要工具和工件作比较复杂的相对运动, 易于加工各种复杂形状的型孔、型腔和成型表面等,超声 波加工设备结构一般比较简单,操作维修方便。 (4) 工具可用较软的材料做成较复杂的形状。
第三章 特种加工
3.2 电解加工
一、电解加工的原理和特点 2.电解加工的特点
电解加工有如下特点: (1)不受材料本身强度、硬度和韧性的限制,可加工高强 度、高硬度和高韧性等难切削的金属材料 (2)能以简单的进给运动一次加工出形状复杂的型面和型 腔。 (3)加工中无切削力和切削热的作用,适合于加工易变形 或薄壁零件。 (4)加工过程中工具电极理论上无损耗,可长期使用。 (5)生产率较高,约为电火花加工的5~10倍以上,在某些 情况下比切削加工的生产率还高。 (6)电解液对机床有腐蚀作用,电解产物的处理和回收困难
以可切割复杂表面。 2)可加工细微的几何形状,切缝和很小的内角半径。 3)无需特定形状的工具电极,降低、节约生产成本及准备工
时。 4)在电参数相同情况下,比穿孔加工生产率高,自动化程度
高,操作使用方便。 5)加工同样的工件,其总蚀除量少,材料利用率高,对加工
贵重金属有着重要意义。 6)线切割的缺点是不能加工盲孔类零件和阶梯成形表面。
第三章 特种加工
3.2 电解加工
二、电解加工的基本工艺规律 2.加工精度及其影响
目前生产中提高加工精度的主要措施如下: (1) 脉冲电流电解加工 (2) 小间隙电解加工 (3) 改进电解液 (4) 混气电解加工 3.表面质量及其影响因素 (1) 工件材料的合金成分、金相组织和热处理 (2) 工艺参数 (3) 工具阴极的表面质量