SKS炼铅工艺降低鼓风炉渣含铅生产实践
KSK炼铅工艺降低鼓风炉熔渣含铅生产实践

312 炉渣的性质及成份选择 ..
炉渣的主要成份为Fo 50 Co Zo 还含有少量的Mo A2等。 e、 12 a、 n 等, 、 g、 1 3 0 其中Po 50 e、 1 、 2
C 、Zo o a n 的总和约占总渣量的 8 ̄9 。 5 0 %
K 炼 sS 铅工艺降 低鼓风炉 含铅生产实 熔渣 践一 袁培新 李初立
件。为了确保炉内的还原气氛,提高还原能力,采取如下措施:
( 提高焦率 (  ̄巧 ) 低风焦比, ) 1 3 1 %,降 控制较高的 C/压比。 O C 操作时尽量使焦点区集 中, 保持较厚的焦炭层, 使熔体渣与 焦炭接触更充分。
( 采取高料柱作业。 ) 2 控制料柱高度35 . , . ̄4o 鼓风强度2 ̄ 耐/ 耐n 风压n ̄ m 4 2 扩. , 8 1 a 6 ,降低熔解速度, P k 床能力控制在4 ̄5 斌 ・ ,以 5 5 t d 便延长还原时间。
含铅高等。为此,该厂经过不断摸索,从合理选择渣型、强化炉内 还原气氛、 优化工艺参数控
制及加强操作入手, 将渣含铅降至4以 本文结合该厂的生产实践对如何降低鼓风炉渣含 己 % 下。
铅作一个初步探讨。
2 高铅渣鼓风炉熔炼的 特点
由 于高铅块Байду номын сангаас和铅烧结块在物理结构与化学成份方面的差异, 在熔炼上有一定区别。
23 4
a : 于c Co 由 z a离子半径大, 低金属与 渣之间的 + 能降 炉 表面张力, 有利于金属 渣的 铅与 分离;
适当的提高渣中C 的 o a 量, 可获得较高的炉温,降低炉渣的比 重;提高炉渣中的C 能破坏熔 o a
渣中 硅氧复合离子, 低炉 降 渣粘度; a 作为强 氧化物, c o 碱性 可置换 硅酸铅中 b, 的P 增大PO o b
降低铅鼓风炉炉渣含铅的途径
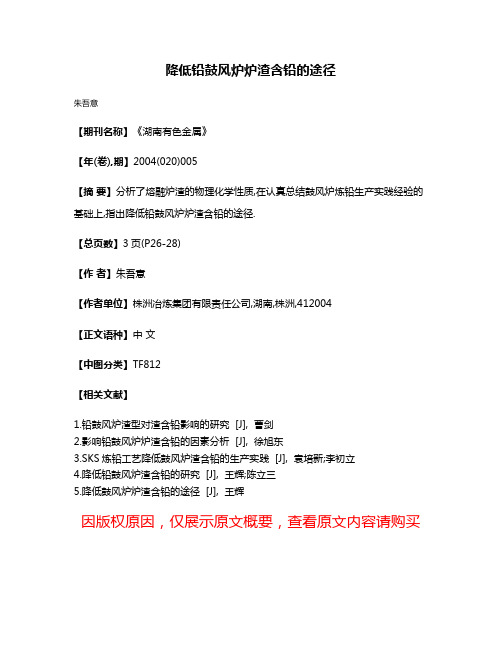
降低铅鼓风炉炉渣含铅的途径
朱吾意
【期刊名称】《湖南有色金属》
【年(卷),期】2004(020)005
【摘要】分析了熔融炉渣的物理化学性质,在认真总结鼓风炉炼铅生产实践经验的基础上,指出降低铅鼓风炉炉渣含铅的途径.
【总页数】3页(P26-28)
【作者】朱吾意
【作者单位】株洲冶炼集团有限责任公司,湖南,株洲,412004
【正文语种】中文
【中图分类】TF812
【相关文献】
1.铅鼓风炉渣型对渣含铅影响的研究 [J], 曹剑
2.影响铅鼓风炉炉渣含铅的因素分析 [J], 徐旭东
3.SKS炼铅工艺降低鼓风炉渣含铅的生产实践 [J], 袁培新;李初立
4.降低铅鼓风炉渣含铅的研究 [J], 王辉;陈立三
5.降低鼓风炉炉渣含铅的途径 [J], 王辉
因版权原因,仅展示原文概要,查看原文内容请购买。
降低鼓风炉渣含铜的措施及生产实践

一、引言鼓风炉是冶炼铜的重要设备之一,而渣中的铜含量则对冶炼工艺和铜的回收率具有重要影响。
降低鼓风炉渣含铜,是提高冶炼效率和减少资源浪费的关键环节。
本文将从鼓风炉渣的含铜问题入手,探讨降低渣中铜含量的相关措施及生产实践。
二、鼓风炉渣含铜的影响因素1. 原料含铜率- 鼓风炉渣中的铜含量主要受原料含铜率影响。
高含铜率的原料进入炉内,会直接导致渣中铜含量升高。
2. 熔炼温度和氧化性- 熔炼温度和氧化性对渣中铜含量也有重要影响。
过高的熔炼温度和氧化性会加速铜在渣中的溶解和迁移。
3. 渣液比- 渣液比的大小与渣中铜含量密切相关。
适当的渣液比可以有效降低渣中铜含量。
1. 调整原料配比- 合理调整原料配比,减少高含铜率原料的使用,以降低鼓风炉渣中的铜含量。
2. 控制熔炼温度和氧化性- 严格控制熔炼温度和氧化性,避免过高的温度和氧化性对渣中铜含量的提高。
3. 合理控制渣液比- 优化渣液比,确保炉内渣液比的合理性,减少渣中铜含量。
4. 渣的再利用- 对含铜的渣进行合理的再利用,可以降低渣中铜含量,提高冶炼效率。
五、总结和展望降低鼓风炉渣中的铜含量,是冶炼铜过程中的关键环节。
针对原料含铜率、熔炼温度和氧化性、渣液比等因素,采取合理的措施和生产实践,是降低渣中铜含量的有效途径。
未来,可以进一步研究新型的降铜技术和设备,提高冶炼效率,降低资源消耗,促进铜工业的可持续发展。
个人观点:降低鼓风炉渣含铜是铜冶炼过程中的重要环节,需要综合运用物理、化学及工艺方面的知识。
只有深入研究并实践相关措施,才能更好地降低渣中铜含量,提高冶炼效率。
我希望通过不断学习和积累经验,为我国铜冶炼工艺的提升和创新做出更多贡献。
在这篇文章中,我们深入探讨了降低鼓风炉渣含铜的措施及生产实践,并根据指定主题进行了多次提及。
希望这篇文章能够帮助您更深入地理解这一主题,并在生产实践中取得更好的效果。
关于鼓风炉渣含铜的措施及生产实践,还有一些值得进一步探讨的方面。
降低炼铅鼓风炉渣铅含量的探索与实践

降低炼铅鼓风炉渣铅含量的探索与实践炼铅是一种重要的化学工艺,用来从金属矿石提取有用的金属元素。
炼铅过程中,会产生温度达到一千多度的渣滓,而这种渣滓中会含有大量的铅。
由于铅的毒性,因此现在人们对它的危害有越来越大的认识,降低渣滓中的铅含量,对节约能源、减少污染、保护环境都有着重要的意义。
首先,必须明确减少炼铅鼓风炉渣中铅的措施。
一是采取有效的技术措施来控制蒸汽温度,减少渣滓的产生;二是采取合适的蒸汽鼓风诱导系统,提高鼓风炉的热效率;三是实施技术改造,在鼓风炉喷口处安装射流器,促使炉渣能均匀地被热风吹走;四是加大排放排气量,让温度更容易达到放射性温度;五是采取有效的冷却措施,减少渣滓中铅的沉淀;六是采取有效的分离技术,把渣滓中的铅分离出来,防止其流入环境。
其次,要对降低炼铅鼓风炉渣中铅的实施效果进行反复试验测量。
在反复的试验中,使用GC-MS(气相色谱-质谱联用仪)可以清楚地了解渣滓中铅元素的含量,从而把多余的铅元素抽除出来;研究人员也可以通过SPME(快速提取静电纺织芯片)对渣滓进行快速提取,检测出渣滓中的铅元素;此外,还可以通过ICP-OES(电感耦合等离子体发射光谱)来检测渣滓中的铅浓度,同时也可以用FTIR(Fourier 变换红外光谱)来获取铅元素的结构和特征。
最后,要按照法律法规的规定进行渣滓的处理,采用合适的技术对渣滓进行处理,以限制其产生的污染。
这里,最有效的处理方法是进行闪蒸处理,即把渣滓放入高温环境中,用高温产生的水蒸气穿透渣滓,把大量铅提取出来。
此外,渣滓处理过程中还需要采取移动式真空蒸发器、固体物料搅拌设备等设备,这样就能有效地降低渣滓中的铅含量。
综上所述,减少炼铅鼓风炉渣中铅含量是一个重要的环保措施,在其实施过程中,需要采取有效的技术措施、反复的实验测量,以及按照法律法规的规定来处理渣滓,确保炼铅过程中不会对环境造成污染。
只有把降低炼铅鼓风炉渣铅含量这项重大任务完成好,才能为保护环境、节约能源、改善人类的生活状况做出贡献。
SKS法铅冶炼鼓风炉炉压控制系统研究的开题报告

SKS法铅冶炼鼓风炉炉压控制系统研究的开题报告一、研究背景铅冶炼是一项能够从废弃的铅酸电池、铅管、电缆等废旧物品中回收铅资源的技术,因其污染严重而备受关注。
而SKS法铅冶炼技术是一种较为成熟的铅冶炼工艺,其利用高温熔化铅质矿物,从中提取纯铅进行再利用。
SKS法铅冶炼鼓风炉是SKS法铅冶炼过程中的重要设备,其肩负着将物料和空气充分混合、将煤气燃烧产生的高温气体送入高炉、加热炉料等任务。
而SKS法铅冶炼鼓风炉的炉压控制对整个铅冶炼过程是至关重要的,其能够保证炉内稳定的气氛和充足的进风量,同时还能避免煤气爆炸等安全隐患。
基于目前SKS法铅冶炼鼓风炉炉压控制技术存在的问题,本文拟开展一系列研究,以提高SKS法铅冶炼鼓风炉炉压控制的精度和稳定性,为铅冶炼工业的可持续发展做出贡献。
二、研究内容1.了解目前SKS法铅冶炼鼓风炉炉压控制技术的现状及存在的问题。
2.设计一套SKS法铅冶炼鼓风炉炉压控制系统,该系统应能够实现自动化控制、方便操作、准确控制炉压以及具备一定的智能化能力。
3.完成SKS法铅冶炼鼓风炉炉压控制系统的硬件组成和软件编程工作,并进行调试和优化。
4.通过实际操作和试验,测试SKS法铅冶炼鼓风炉炉压控制系统的精度、稳定性和安全性,评估其在实际生产中的应用效果。
三、研究意义本研究将通过对SKS法铅冶炼鼓风炉炉压控制技术的研究,设计一套适用性更好、精度更高、稳定性更强的控制系统,为铅冶炼工业提供了一条新的技术路线,有利于实现铅冶炼工业的可持续发展。
同时,优化铅冶炼鼓风炉炉压控制系统的研究成果,也可以在其他冶炼行业的高炉、转炉等领域得到推广应用,具有广阔的应用前景。
烟化法综合处理铅锑鼓风炉渣的工艺实践

烟化法综合处理铅锑鼓风炉渣的工艺实践引言铅锑鼓风炉渣是一种含有铅和锑等有害物质的废弃物,对环境造成严重污染。
为了综合处理这种废弃物,烟化法被广泛应用。
本文将详细介绍烟化法综合处理铅锑鼓风炉渣的工艺实践。
工艺概述烟化法是一种将固体废弃物通过高温加热分解的方法。
在处理铅锑鼓风炉渣时,通过加热使其发生分解反应,产生可回收的金属和无害的固体残渣。
整个工艺包括预处理、烟化反应、冷却和分离四个步骤。
工艺流程1. 预处理首先需要对铅锑鼓风炉渣进行预处理,包括去除杂质和调节成分。
常见的预处理方法包括筛分、洗涤和酸洗等。
通过这些步骤可以提高后续工艺的效果。
2. 烟化反应将经过预处理的铅锑鼓风炉渣送入烟化炉中进行高温加热。
一般采用电炉或者高温燃烧器进行加热,将温度控制在800-1000°C之间。
在这个温度下,铅锑鼓风炉渣发生分解反应,产生可回收的金属和气体。
3. 冷却将从烟化炉中产生的气体通过冷却设备进行降温处理。
冷却设备可以采用水冷、风冷或者其他方式。
通过降温,气体中的金属蒸汽会凝结成固体颗粒,并与其他固体残渣一同被收集。
4. 分离经过冷却后,固体颗粒和其他固体残渣被分离出来。
常见的分离方法包括重力分离、筛分和电磁分离等。
通过这些方法可以将金属颗粒和无害固体残渣分别收集起来。
工艺优势1. 资源回收通过烟化法综合处理铅锑鼓风炉渣,可以将其中的金属回收利用。
这些金属可以经过进一步的冶炼和精炼,得到高纯度的铅和锑等有价值的物质。
2. 环境友好烟化法能够将有害废弃物转化为无害的固体残渣,减少对环境的污染。
通过合理控制工艺条件和采用有效的排放处理措施,可以达到环保要求。
3. 经济可行综合处理铅锑鼓风炉渣可以实现资源回收和废物减量,从而降低生产成本。
金属回收的销售也可以带来经济效益。
工艺改进与展望在实际应用中,还存在一些问题需要解决。
如何提高金属回收率、如何降低能耗和减少二次污染等。
未来可通过改进烟化反应设备、优化工艺条件和加强环境监管等方式进一步完善该工艺。
铅冶炼氧气底吹资料
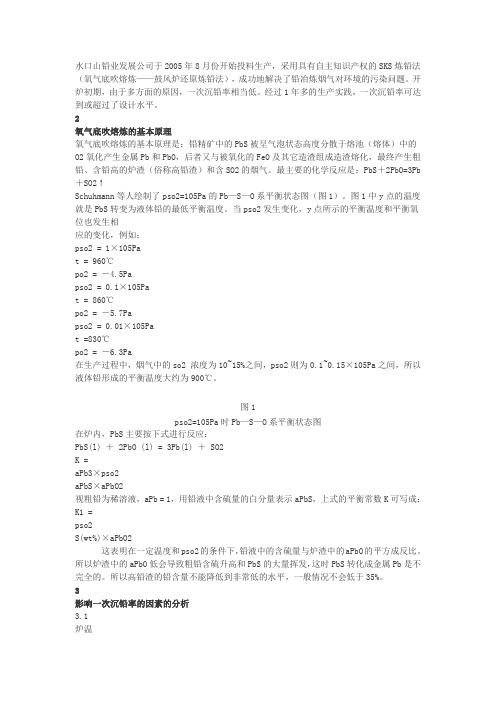
水口山铅业发展公司于2005年8月份开始投料生产,采用具有自主知识产权的SKS炼铅法(氧气底吹熔炼——鼓风炉还原炼铅法),成功地解决了铅冶炼烟气对环境的污染问题。
开炉初期,由于多方面的原因,一次沉铅率相当低。
经过1年多的生产实践,一次沉铅率可达到或超过了设计水平。
2氧气底吹熔炼的基本原理氧气底吹熔炼的基本原理是:铅精矿中的PbS被呈气泡状态高度分散于熔池(熔体)中的O2氧化产生金属Pb和PbO,后者又与被氧化的FeO及其它造渣组成造渣熔化,最终产生粗铅、含铅高的炉渣(俗称高铅渣)和含SO2的烟气。
最主要的化学反应是:PbS+2PbO=3Pb +SO2↑Schuhmann等人绘制了pso2=105Pa的Pb—S—O系平衡状态图(图1)。
图1中y点的温度就是PbS转变为液体铅的最低平衡温度。
当pso2发生变化,y点所示的平衡温度和平衡氧位也发生相应的变化,例如:pso2 = 1×105Pat = 960℃po2 = -4.5Papso2 = 0.1×105Pat = 860℃po2 = -5.7Papso2 = 0.01×105Pat =830℃po2 = -6.3Pa在生产过程中,烟气中的so2 浓度为10~15%之间,pso2则为0.1~0.15×105Pa之间,所以液体铅形成的平衡温度大约为900℃。
图1pso2=105Pa时Pb—S—O系平衡状态图在炉内,PbS主要按下式进行反应:PbS(l) + 2PbO (l) = 3Pb(l) + SO2K =aPb3×pso2aPbS×aPbO2视粗铅为稀溶液,aPb = 1,用铅液中含硫量的白分量表示aPbS,上式的平衡常数K可写成:K1 =pso2S(wt%)×aPbO2这表明在一定温度和pso2的条件下,铅液中的含硫量与炉渣中的aPbO的平方成反比。
所以炉渣中的aPbO低会导致粗铅含硫升高和PbS的大量挥发,这时PbS转化成金属Pb是不完全的。
基于SKS炼铅系统的有色冶炼过程余热利用研究

统 计 显 示 ,2 0 0 8年 ,我 国有 色 冶 炼 与 加 工
平 均 单 耗 为 0 66e , 比 国 际 先 进 水 平 的 .0 t e 05 te 高 出近 2 % ;我 国密 闭 鼓 风炉 炼 锌 的 . 0c 要 0 平 均 能耗 比国 际 先 进 水 平 高 3. % ,铅 冶 炼 的 34
平均能耗 比国际先进水平高 8. %【 。 42 3 J S S炼 铅 法 ( 口山炼 铅 法 ) 为 氧 气 底 吹 K 水 ‘
熔 炼 —— 鼓 风炉 还原 炼铅 法 ,是 我 国 自行 开发具 有 知 识产 权 的先 进炼铅 方 法 。S S炼铅 法 不 仅彻 K
因此 ,加 强 提高 有色 企业 的资 源综 合利 用对 实现 国家节 能 减 排 约 束 性 目标 具 有 重 要 作 用 。近 年
平相比仍有一定 差距 。20 06年 ,我国 电解铝直 流 电 耗 为 15 6 Wht 比 国 际 先 进 水 平 的 3 0k /,
130 W / 要高 16 Wh t 国铜闪速炉冶炼 35 k h t 5 k /;我
湖 南 省 科 技 计 划 攻 关 重 大 专 项 项 目支 持 , 目号 : 项
施。
关键词
有色冶炼
余热
综合利用
节能
Dic s fr c ci e i a ne g n s e lpr du to o e s s u s o e y l ng r sdu le r y i t e o c i n pr c s
J n iu J n i i Y u n S i h n m n i gA h a・ i gX n e a a j uH a g h Z a g ig
(.中南 大 学能 源科 学与工 程学 院 ,2 南节 能评 价 技术研 究 中心 ) 1 .湖
- 1、下载文档前请自行甄别文档内容的完整性,平台不提供额外的编辑、内容补充、找答案等附加服务。
- 2、"仅部分预览"的文档,不可在线预览部分如存在完整性等问题,可反馈申请退款(可完整预览的文档不适用该条件!)。
- 3、如文档侵犯您的权益,请联系客服反馈,我们会尽快为您处理(人工客服工作时间:9:00-18:30)。
SKS炼铅工艺降低鼓风炉熔渣含铅生产实践袁培新李初立(湖南水口有色金属集团有限公司,湖南衡阳421513)[摘要]:本文介绍了SKS炼铅法鼓风炉还原段在水口山八厂的生产实践,并从渣型、鼓风炉还原能力及操作等方面探讨了降低鼓风炉渣含铅的途径和方法。
[关键词]:SKS炼铅法;高铅渣;铅鼓风炉;渣含铅Plant Practice on Lowering Lead Containing in Blast Furnace Slag in SKS Lead Smelting ProcessYUAN Pei-xin,LI Chu-liAbstract:It presents the plant practice of blast furnace in SKS Lead Smelting Process in the eighth smelter in Shuikoushan,and analyses the effect of slag type, reducing ability, operation on lowering lead containing in blast furnace slag.Keywords:SKS Lead Smelting Process; High Lead Slag;Lead Blast Furnace;Lead Containing in Slag1、前言我厂采用的是底吹氧化——鼓风炉还原炼铅工艺(SKS炼铅法),该工艺是我公司与中国有色工程设计研究总院共同研发的、具有自主知识产权的一种炼铅方法。
该法具有环保好、能耗低、对原料适应性强、自动化程度高、工艺可靠性强等特点。
自2005年8月投产以来,生产正常,各项技术经济指标平稳上升。
但是,由于底吹炉所产出的高铅渣具有与烧结块不同的特性,高铅渣进鼓风炉处理存在一定的难度,主要表现为易形成炉缸炉结,渣含铅高等。
为此,我厂经过不断摸索,从合理选择渣型、强化炉内还原气氛、优化工艺参数控制及加强操作入手,已将渣含铅降至4%以下。
本文结合我厂的生产实践对如何降低鼓风炉渣含铅作一个初步探讨。
2、高铅渣鼓风炉熔炼的特点由于高铅块渣和铅烧结块在物理结构与化学成份方面的差异,在熔炼上有一定区别。
铅烧结块为多孔结构的块状物,孔隙率一般为50~60%,堆比重1.8~2.2,块度一般为50~150mm。
烧结块中以硅酸铅形态存在的铅约占总铅量的40%。
在鼓风炉还原熔炼时,游离PbO在600℃时已大量被还原,而未被还原的PbO 及硅酸铅在700~800℃时开始熔化,在流向炉缸的过程中被加热并溶解其它金属氧化物。
熔体中的铅化合物在熔化区被上升热气流中的CO所还原。
在焦点区,C直接参与了从熔体中还原硅酸铅中的铅。
由于铅烧结块的表面积大,CO的气固反应和碳的直接还原反应比较活跃,还原过程进行得很彻底,故渣含铅小于3%。
高铅渣为致密的熔结物,堆比重约3.0。
与多孔疏松的铅烧结块相比,比表面积大大降低。
高铅渣中硅酸铅占总铅量的70%以上,游离的氧化铅和铁酸铅也完全溶解于炉渣中。
在上部还原区中,CO与高铅渣之间的气固反应机率较小,只有在进入下部还原区,高铅渣开始熔化,铅的还原反应将同时进行。
高铅渣中的铅化合物的还原主要依靠焦点区的炭与熔渣的直接还原反应和造渣组分的置换反应。
因此,降低物料的熔解速度,提高焦点区的还原强度,选择合理渣型和增加渣、铅分离的时间将是熔炼过和程顺利进行,且获得低的渣含铅的必要条件。
3、降低渣含铅的主要途径和措施3.1渣型选择有色金属的冶炼过程实际是一个以炉渣作媒介提纯金属的过程,炉渣的组成及性质决定着熔炼过程的还原程度、燃料的消耗量、炉座的生产率及金属的回收率。
所以渣型的选择对于降低渣含铅意义非常重大。
3.1.1渣型的选择应满足如下要求:⑴渣型应既能满足冶金过程的要求,包括炉况顺行,渣铅分离好,渣含铅低,流动性合适,不浸蚀炉衬等,又能节约造渣费用,得到良好的冶炼技术经济指标。
⑵充分考虑底吹炉、鼓风炉对渣型的不同要求,底吹炉高铅渣尽量向终渣所需成分靠拢,鼓风炉不加或少加熔剂为宜。
⑶底吹炉渣熔点控制在950~1000℃,防止熔池温度超过1100℃,减少金属铅、硫化铅、氧化铅挥发,降低烟尘率。
而鼓风炉渣熔点应控制在1100~1150℃,以保证较高的炉温,有利于还原反应的进行。
⑷方便生产管理,硅熔剂全部由底吹炉加入,铁、钙熔剂部分由底吹炉加入。
鼓风炉只作铁、钙熔剂的适当补充。
3.1.2炉渣的性质及成份选择炉渣的主要成份为FeO、SiO2、CaO、ZnO等,还含有少量的MgO、Al2O3等。
其中FeO、SiO2、CaO、ZnO的总和约占总渣量的85~90%。
CaO:由于Ca2+离子半径大,能降低金属与炉渣之间的表面张力,有利于金属铅与渣的分离;适当的提高渣中CaO的量,可获得较高的炉温,降低炉渣的比重;提高炉渣中的CaO能破坏熔渣中硅氧复合离子,降低炉渣粘度;CaO作为强碱性氧化物,可置换硅酸铅中的PbO,增大PbO的活度,有利于的PbO还原。
因此选用高钙渣,能够很好降低鼓风炉渣铅金属损失。
FeO:与CaO一样,可置换硅酸铅中的PbO,增大PbO的活度,有利于的PbO还原,因此选用含铁较高的渣型,也可降低渣含铅,同时增大炉渣对ZnO 的溶解度,有利于炉况顺行。
SiO2:能减小炉渣的比重,但会增加渣的粘度和提高渣的熔点。
含铁较高的情况下,为了尽量减少Fe3O4的生成,SiO2的含量必须保证能形成2FeO·SiO2的量。
ZnO:全是由原料中带入,当渣中ZnO含量过高时,炉渣的熔点急剧上升,所以鼓风炉渣中Zn含量以不超过15%为宜。
综上所述,同时考虑到技术和经济两个方面,即既要尽量降低熔剂的消耗,从而减少产渣量和渣含金属的绝对损失,又满足熔炼对炉渣成分的基本要求。
故确定渣型为:22~26%; CaO 17~19%; Zn<15%。
FeO 28~32%; SiO2实践证明:采用此种渣型,能保证鼓风炉炉况顺行,且渣含铅较低。
3.2提高鼓风炉还原能力如前所述,高铅渣中硅酸铅占总铅量的70%以上,其余游离的PbO和PbO·Fe2O3也完全溶解于炉渣中。
因此,鼓风炉还原高铅渣时,铅几乎完全是从炉渣中被还原出来。
与烧结块的还原过程相比较,高铅渣中的铅是可以较彻底地被还原出来,但高铅渣的还原需要更强的还原条件。
为了确保炉内的还原气氛,提高还原能力,我们采取如下措施:⑴提高焦率(13~15%),降低风焦比,控制较高的CO/CO2比。
操作时尽量使焦点区集中,保持较厚的焦炭层,使熔体渣与焦炭接触更充分。
⑵采取高料柱作业。
控制料柱高度3.5~4.0米,鼓风强度24~28Nm3/m2.min,风压11~16Kpa,降低熔解速度,床能力控制在45~55t/m2d,以便延长还原时间。
3.3减缓和控制炉缸炉结的形成生产实践中我们发现,鼓风炉炉缸很容易形成横隔膜,严重影响渣、铅分离,导致渣含铅急剧上升,如果不及时采取措施,炉缸炉结会越来越严重,最终不得不停炉来进行处理。
通过对高铅渣、鼓风炉渣及炉缸炉结物的物相分析(见表1),结果表明,鼓风炉炉缸炉结中的难熔物主要为Fe3O4。
Fe3O4的主要来源于高铅渣,高铅渣中的铁很大一部分以Fe3O4形态存在,这与底吹炉的强氧化气氛有关。
表1 高铅渣、鼓风炉渣及炉缸炉结中铁物相分配比例(%)物相硫化铁金属铁磁性铁赤铁矿硅酸铁总铁高铅渣 1.7 11.81 51.25 18.25 16.99 100鼓风炉渣9.28 16.94 40.58 36.47 5.08 100炉缸炉结9.69 16.40 51.65 25.90 5.08 100 注:表中数据为各物相铁含量的质量百分比为了减轻、消除Fe3O4带来的危害,我们主要采取了以下措施:⑴加入硫铁矿还原磁性铁。
其主要反应方程式为:3Fe3O4+FeS===10FeO+SO2↑①△G0=761329-455T3Fe3O4+FeS+5SiO2===5(2FeO·SiO2)+SO2↑②△G0=625.28-0.44T由以上两反应方程式吉布斯自由能变化和平衡常数与温度关系得知,反应①在1400℃以上才能向右进行。
而对于反应②来说,由于SiO2的存在,Fe3O4的还原显得容易得多,在1100℃时反应即可进行。
如能提高炉温和FeS的活度,降低FeO的活度及SO2的分压,有利于反应向破坏Fe3O4的方向进行。
在正常的熔炼温度下(1150~1250℃),加之鼓风炉炉气中极低的SO2浓度,只要有足够的SiO2来生成2FeO·SiO2,渣中的磁性铁会大大减少。
⑵定期从后渣口将粘渣排出。
为了顺利地将含Fe3O4高的粘渣排出,我们特将后渣口位置作了调整,取得了预期效果。
⑶炉缸内有横隔膜形成时,要经常从前后渣口用氧气捅烧,保证铅液顺利落入炉缸。
3.4加强操作,确保炉况稳定,尽量降低渣含铅:⑴均匀合理布料,严格控制料柱高度。
⑵加强铅井管理,确保铅井灵活。
⑶保持铅坝、渣坝相对稳定,确保炉缸不积渣,同时金属铅不从咽喉口带出。
⑷按规定放黄渣及开后渣口放粘渣。
⑸尽量减少停风时间,要求处理上部炉结、渣坝的停风时间控制在两小时以内。
⑹加强电热前床操作,保证铅、冰铜、熔渣正常澄清分离。
3.5严抓底吹炉生产管理,为鼓风炉提供合格高铅渣降低鼓风炉渣含铅是一个系统工程,除了抓好鼓风炉系统自身技术参数的控制及加强操作外,底吹炉系统所产出高铅渣成份也是一个非常重要的影响因素。
生产实践中我们发现当高铅渣含铅超过50%时,鼓风炉渣含铅也相应提高;而且当高铅渣成份不稳定时,会导致鼓风炉渣成份的波动,使得鼓风炉渣含铅升高。
为此我们规范了以下工作:⑴严抓底吹炉的配料及进料管理。
堆配由专人负责,并严格按配料单进行;配料工应根据配料单及底吹炉需料量要求进行配料,确保混合料成份均匀,供料稳定可靠;底吹炉进料操作工应勤清下料口,做到进料连续均匀,氧料比控制得当,保证高铅渣成份基本稳定。
⑵对高铅渣、鼓风炉渣成份跟班化验,并及时报出化验结果,以便于随时调整渣型。
⑶要求高铅渣成份:Pb40~48%,FeO/ SiO21.3~1.5,CaO/ SiO20.5~0.6。
4、生产实践自2005年8月30日正式投料至今,可分为三个阶段(具体指标见表2):表2 控制参数与技术经济指标一览表项目单位第一阶段第二阶段第三阶段1、鼓风炉渣成份% FeO30~33CaO12~14SiO222~24Zn10~13FeO30~33CaO16~19SiO222~24Zn10~13FeO28~32CaO17~19SiO222~26Zn<152、高铅渣含铅% 56.23 48.81 45.603、鼓风强度Nm3/m2.min 22 24~26 26~294、鼓风富氧度% 24 24 244、鼓风风压kpa 10~12 11~13 12~175、焦率% 16.28 14.61 14.256、料柱高度m 2.5~3.0 2.5~3.0 3.5~4.07、床能力t/m2d 32.4 43.92 51.28、鼓风炉渣含铅% 6.66 5.54 4.30注:鼓风炉渣含铅是指在鼓风炉咽喉口所取渣的化验结果。