第四章普通注射模具
合集下载
项目四 普通注射模具4.6

图4-112 螺纹塑件的止转结构
根据塑件上螺纹精度要求和生产批量的不同, 塑件上的螺纹常用以下三种方法来脱模。
1.强制脱模 . 这种脱模方式多用于螺纹精度要求不高的场合,采用强制脱 模,可使模具的结构比较简单。 图4-113 利用塑件的弹性强制脱模 2.手动脱模 . 手动脱出螺纹主要有两种形式,一种为机内型,另一种为机 外型。 图4-114 手动脱螺纹机构 3.机动脱模 . 这种机构是利用开合动作使螺纹型芯脱出和复位,下面举一 个齿轮、齿条脱螺纹型芯的机构。如图4-115所示。
4.6.4 二级推出机构 . .
在一般情况下,塑件的推出动作都是一次完 成的。但是由于塑件的形状特殊或生产自动 化的需要,一次推出动作完成后,塑件难以 全部脱出模外,如顶出力太大,易使塑件产 生变形、甚至破坏,此时可采用二次推出, 以分散脱模力,使塑件自动脱落。这类推出 机构称为二级推出机构,这类推出机构的结 构形式有很多,现举例如下:
2.推管推出机构
图4-101 推管推出机构 1—推管 2—型芯 3—复位杆
3.推件板推出机构
图4-102 推件板推出机构 1—推件板2—推杆3—导柱
4.活动镶块
图4-105 活动镶块推出机构 1—螺纹型芯2—弹簧3—活动镶块
5.综合推出机构
图4-106 推管、推件板综合推出机构 1—推管2—推件板
4.6.3 推出机构的导向与复位 . .
1.导向零件 . 对卧式注射机使用的模具来说,当推杆较细时,固 定它的固定板及垫板的重量.容易使推杆弯曲,以 至在推出时不够灵活,甚至折断,故常设导向零件。 导柱的数量一般不少于两个。常见的形式如图4107所示,图(a)所示的导柱,除了起导向作用外, 还起支撑作用,可以减小注射成型时支承板的弯曲。 当推杆的数量较多,塑件的产量较大时,光有导柱 是不够的,还需装配导套,以延长导向零件的寿命 及使用的可靠性。如图(b)所示。
第4章 普通注射模具4.1结构 《塑料成型工艺与模具设计》课件

图4-8 带有活动镶件的注射模 1—导套 2一定模板 3一导柱 4一活动镶件 5一型芯 6一动模板 7一支承板 8一支架 9一弹簧 10一推杆 11一推杆固定板 12一推板
图4-9 带有活动镶件的另一种形式的注射模 1一动模座板 2一推板 3一推杆固定板 4一垫块 5一弹簧 6一支承板 7一复位杆 8一导柱 9一推杆 10—导套11一定模座板 12一活动镶件 13一型芯 14一浇口套 15一定模板 16一动模板 17一定距导柱 18一推杆
4.1.2 注射模具的分类 . .
按生产的塑料材料分:可分为热塑性塑料注射模和热固性 塑料注射模。 按注射机类型分:可分为立式注射机用注射模、卧式注射 机用注射模、角式注射机用注射模。 按浇注系统形式分:可分为普通流道注射模及热流道注射 模。 按模具结构特征分:可分为单分型面注射模、双分型面注 射模、斜导柱(或弯销、斜滑块、齿轮齿条)侧向分型与抽芯 注射模、带有活动镶件的注射模、推出机构设在定模一侧的 注射模和自动卸螺纹注射模等。
(1)工作原理 开模时,注射机开合模系统带动动模 后移,如图4-2所示。由于弹簧7的作用,模具首先 在A分型面分型,定模型腔板14随动模一起后移, 主浇道凝料随之拉出。当动模部分移动—定距离后, 固定在定模型腔板14上的限位销6与定距拉板左端 接触,使中间板停止移动。动模继续后移,B分型 面分型。因塑件包紧在型芯18上,这时浇注系统凝 料在浇口处自行拉断,然后在A分型面之间自行脱 落或由人工取出。动模部分继续后移,当注射机的 推杆接触推板9时,推出机构开始工作,推件板4在 推杆11的推动下将塑件从型芯上推出,塑件在B分 型面间落下。
第4章 普通注射模具 章
本章主要讲解了热塑性塑料注射成型模具的 结构特点、注射模设计的基本知识、模架的 国家标准及选用方法以及注射模与注射机之 间的关系,最后运用实例,介绍了注射模典 型结构设计的全过程。
塑料成型机械及模具 第四章 注射机
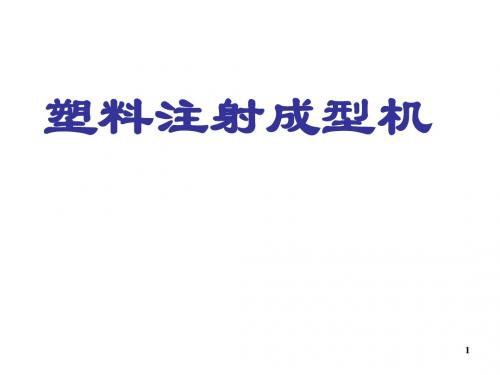
条件
容易成型的 制品 一般制品 高粘度、有 精度要求的 制品 高粘度、高 精度、充模 难的制品
P模腔=40~70%P注射
实 例 模腔平均压 力 25MPa PE、PP、PS等壁厚均 匀的日用品容器类制品 30MPa 在模具温度较高的条件 下,薄壁容器类制品 35MPa ABS等有精度要求的工 业零件,如壳体、齿轮 等 40MPa 高精度的工业零件
7
4.1.3注射成型机的工作过程及组成
?
一 注射成型机的工艺过程
a) 闭模和锁紧
b) 注射装置前移和注射
c) 压力保持
d) 制品冷却和预塑化
e) 注射装置后退和开模顶出装置
8
注射成型机工作循环周期图
闭模
试合模 发信
高压低速锁紧
注座前移
注射
制品落下检测发信
开模
冷却 塑化退回
保压
注 射 动 作 选 择
41
4.1.7
• • • • • • •
注射部分主要性能参数
1、注射量 2、注射压力 3、注射速度和注射速率 4、锁模力 5、塑化能力 6、合模装置基本尺寸 7、工作效率参数
42
1、注射量
• 定义:机器在对空注射条件下,注射螺杆 (柱塞)作一次最大注射行程时,注射装 置所能达到的最大注射量 • 注射量由注射机的螺杆直径和螺杆移动行 程决定。
57
•
螺杆的塑化能力,应该在规定的时间内,保 证提供足够量的塑化均匀的熔料 塑化能力应满足: G>=3.6×W/t 其中: t---制件最短冷却时间(s) W--机器注射量(g) G---螺杆塑化能力(Kg/h)
58
6、合模装置基本尺寸
• 合模装置的尺寸直接关系到机器所能加工制品的范 围,如制品的面积,高度 • 1 模板尺寸和拉杆有效间距 模板尺寸(H*V) 拉杆有效间距(Ho*Vo) 一般模板面积大约是拉杆有效面积的2.5倍。
容易成型的 制品 一般制品 高粘度、有 精度要求的 制品 高粘度、高 精度、充模 难的制品
P模腔=40~70%P注射
实 例 模腔平均压 力 25MPa PE、PP、PS等壁厚均 匀的日用品容器类制品 30MPa 在模具温度较高的条件 下,薄壁容器类制品 35MPa ABS等有精度要求的工 业零件,如壳体、齿轮 等 40MPa 高精度的工业零件
7
4.1.3注射成型机的工作过程及组成
?
一 注射成型机的工艺过程
a) 闭模和锁紧
b) 注射装置前移和注射
c) 压力保持
d) 制品冷却和预塑化
e) 注射装置后退和开模顶出装置
8
注射成型机工作循环周期图
闭模
试合模 发信
高压低速锁紧
注座前移
注射
制品落下检测发信
开模
冷却 塑化退回
保压
注 射 动 作 选 择
41
4.1.7
• • • • • • •
注射部分主要性能参数
1、注射量 2、注射压力 3、注射速度和注射速率 4、锁模力 5、塑化能力 6、合模装置基本尺寸 7、工作效率参数
42
1、注射量
• 定义:机器在对空注射条件下,注射螺杆 (柱塞)作一次最大注射行程时,注射装 置所能达到的最大注射量 • 注射量由注射机的螺杆直径和螺杆移动行 程决定。
57
•
螺杆的塑化能力,应该在规定的时间内,保 证提供足够量的塑化均匀的熔料 塑化能力应满足: G>=3.6×W/t 其中: t---制件最短冷却时间(s) W--机器注射量(g) G---螺杆塑化能力(Kg/h)
58
6、合模装置基本尺寸
• 合模装置的尺寸直接关系到机器所能加工制品的范 围,如制品的面积,高度 • 1 模板尺寸和拉杆有效间距 模板尺寸(H*V) 拉杆有效间距(Ho*Vo) 一般模板面积大约是拉杆有效面积的2.5倍。
第四章 注塑机和注塑模具的关系

注塑机需要设计加料系统(料筒)及注射系统。 成型时,先闭紧模具,熔融塑料通过浇注系统注入型腔里面。 每一模成型中产生的浇注系统凝料为废料,它将损耗部分原料。
⑵成型制品精度较高。生产批量较大时,模具应当设有 温度控制系统。
⑶对制品成型的适应性很强。 ⑷成型周期短,生产效率最高,便于实现自动化操作, 因此便于大批量制品的生产。
第四章 注塑机和注塑模具的关系
本章重点: 掌握注塑机主要参数与模具结构之间的关系 注塑机的主要参数: 最大注射量、最大注射压力、最大锁模力、最大成型
面积、模具最大和最小厚度、最大开模行程、安装位置 尺寸、喷嘴球径和孔径、顶杆位置。
第四章 注塑机和注塑模具的关系
用注塑模来生产制品主要有以下特点: ⑴塑料的加热和塑化是在注塑机的高温料筒内完成的,
注塑机的主要参数:
最大注射量、最大注射压力、最大锁模力、最大成型面积、模具最大 和最小厚度、最大开模行程、安装位置尺寸、喷嘴球径和孔径、顶杆位置。
一、最大注射量的校核:
注塑机最大注射量的标定:通常用常温下注射机一次注射
聚苯乙烯PS (1.06g/cm³) 的最大容积量为注射机公称注射量。 -----体积(cm³)
一 、注塑机的种类及应用
㈠注塑机的种类及其应用: 按成型塑料性质:有热塑性塑料注塑机和热固性塑料注塑机。
按塑化方式:有柱塞式注塑机和螺杆式注塑机。
柱塞式注塑机一般在公称注射量60cm3 以下;
螺杆式注塑机,是目前产量最大,应用最广的类型。
按锁模机构驱动方式:有液压式和液压-机械联合式。 按操作方式:有全自动、半自动和手动式。 按结构形式:有立式、卧式和直角式
直角式注塑机:
如图所示,其注射装置轴线与锁模机构轴线相互正交垂直。 优点:结构简单,便于自制,适于一模仅成型一件,
⑵成型制品精度较高。生产批量较大时,模具应当设有 温度控制系统。
⑶对制品成型的适应性很强。 ⑷成型周期短,生产效率最高,便于实现自动化操作, 因此便于大批量制品的生产。
第四章 注塑机和注塑模具的关系
本章重点: 掌握注塑机主要参数与模具结构之间的关系 注塑机的主要参数: 最大注射量、最大注射压力、最大锁模力、最大成型
面积、模具最大和最小厚度、最大开模行程、安装位置 尺寸、喷嘴球径和孔径、顶杆位置。
第四章 注塑机和注塑模具的关系
用注塑模来生产制品主要有以下特点: ⑴塑料的加热和塑化是在注塑机的高温料筒内完成的,
注塑机的主要参数:
最大注射量、最大注射压力、最大锁模力、最大成型面积、模具最大 和最小厚度、最大开模行程、安装位置尺寸、喷嘴球径和孔径、顶杆位置。
一、最大注射量的校核:
注塑机最大注射量的标定:通常用常温下注射机一次注射
聚苯乙烯PS (1.06g/cm³) 的最大容积量为注射机公称注射量。 -----体积(cm³)
一 、注塑机的种类及应用
㈠注塑机的种类及其应用: 按成型塑料性质:有热塑性塑料注塑机和热固性塑料注塑机。
按塑化方式:有柱塞式注塑机和螺杆式注塑机。
柱塞式注塑机一般在公称注射量60cm3 以下;
螺杆式注塑机,是目前产量最大,应用最广的类型。
按锁模机构驱动方式:有液压式和液压-机械联合式。 按操作方式:有全自动、半自动和手动式。 按结构形式:有立式、卧式和直角式
直角式注塑机:
如图所示,其注射装置轴线与锁模机构轴线相互正交垂直。 优点:结构简单,便于自制,适于一模仅成型一件,
第4章普通注射模具4243

PPT文档演模板
第4章普通注射模具4243
4.3.1 浇注系统的组成与作用
v 1.浇注系统的组成 v 注射模的浇注系统是指熔体从注射机的喷嘴
开始到型腔为止流动的通道。图4-16所示为 卧式注射机用模具的普通浇注系统。图4-17 所示为角式注射机用模具的普通浇注系统。 它们都由主流道、分流道、浇口、冷料穴几 部分组成。
•图4-15 分型面对排气效果的影响
第4章普通注射模具4243
•尽量减少塑件在分型面上的投影面积
PPT文档演模板
第4章普通注射模具4243
•实例:灯罩模具设计
PPT文档演模板
第4章普通注射模具4243
•分型面的选择:
•该塑件为灯座,外形要求美观,无斑点和熔接痕,表面质量要求较高。 在选择分型面时,根据分型面的选择原则,考虑不影响塑件的外观质量 以及成型后能顺利取出塑件,有两种分型面的选择方案。
PPT文档演模板
•图
•图
1
2
第4章普通注射模具4243
PPT文档演模板
•分型面位置和形状的选择 ➢注射模设计第一步:根据塑件结构特点选择分型面位置
➢塑件特征:
▪内孔带螺纹的盖形件; ▪外圆面带直槽防滑装 饰纹;
▪外圆带有一定的锥度。
➢可选分型面位置: ▪A-A或B-B; ▪合理应在B-B。
第4章普通注射模具4243
PPT文档演模板
第4章普通注射模具4243
•主浇道
•分浇道
•浇口
PPT文档演模板
• 流道系统的设计是否适当,直接影响成形品的外观、 物性、尺寸精度和成形周期。
第4章普通注射模具4243
•
图4-16 卧式注射机用模具的浇注系统
•1一主流道衬套2一主流道3一冷料穴 4一分流道5一浇口6一塑件
项目四 普通注射模具410

❖ 另加3~5mm的抽芯安全系数,可取抽芯距S轴=4.9mm。 ❖ ②确定斜导柱倾角 斜导柱的倾角是斜抽芯机构的主要技术
参数之一,它与抽拔力以及抽芯距有直接关系,—般取 α=15°~20°,本例中选取α=20°。 ❖ ③确定斜导柱的尺寸 斜导柱的直径取决于抽拨力及其倾斜 角度,可按设计资料的有关公式进行计算,本例采用经验估 值,取斜导柱的直径d=14mm。斜导柱的长度根据抽芯距、 固定端模板的厚度、斜销直径及斜角大小确定(参见本章第 六节斜导柱长度计算公式)。 ❖ 由于上模板座和上凸模固定板尺寸尚不确定,初定δ= 25mm,D=20mm,计算后,取L=55mm。如果以后δ,有 变化,则)
0.26 59 104 60 103 4.187 103 (30 20)
0.61104 (m3
/ min)
❖ 由上述计算可知,因为模具每分钟所需的冷却水体 积流量较小,故可不设冷却系统,依
❖ 靠空冷的方式冷却模具即可。
7.模具闭合高度的确定
❖ 根据支承与固定零件设计中提供的经验数据 确定,定模座板:H1=25mm;上固定板: H2=25mm;下固定板:H3=40mm;支承 板:H4=25mm;动模座板:H5=25mm; 根据推出行程和推出机构的结构尺寸确定垫 块:H6=50mm。因而模具的闭合高度
❖ ⑵塑件的结构和尺寸精度、表面质量分析 ❖ ①结构分析 从零件图上分析,该零件总体形状为长方形,
在宽度方向的一侧有两个高为8.5mm,半径为R5mm的两 个凸耳,在两个高度为12mm、长、宽分别为17×14mm的 凸台上,一个带有凹槽对称分布,另一个带有4Xlmm的凸台 对称分布,因此,模具设计时必须设置侧向分型抽芯机构, 该零件属于中等复杂程度。 ❖ ②尺寸精度分析 该零件重要尺寸如:12.1mm、12.1 mm、15.1mm、 ❖ 15mm等精度为3级,次重要尺寸如:13.5 mm、17mm、 10.5mm、14mm等的尺寸精度为4~5级。 ❖ ③从塑件的壁厚上来看,壁厚最大处为1.3mm,最小处为 0.95mm,壁厚差为0.35mm,较均匀,有利于零件的成 型。 ❖ ④表面质量分析 该零件的表面除要求没有缺陷、毛刺,内 部不得有导电杂质外,没有特别的表面质量要求,故比较容 易实现。
参数之一,它与抽拔力以及抽芯距有直接关系,—般取 α=15°~20°,本例中选取α=20°。 ❖ ③确定斜导柱的尺寸 斜导柱的直径取决于抽拨力及其倾斜 角度,可按设计资料的有关公式进行计算,本例采用经验估 值,取斜导柱的直径d=14mm。斜导柱的长度根据抽芯距、 固定端模板的厚度、斜销直径及斜角大小确定(参见本章第 六节斜导柱长度计算公式)。 ❖ 由于上模板座和上凸模固定板尺寸尚不确定,初定δ= 25mm,D=20mm,计算后,取L=55mm。如果以后δ,有 变化,则)
0.26 59 104 60 103 4.187 103 (30 20)
0.61104 (m3
/ min)
❖ 由上述计算可知,因为模具每分钟所需的冷却水体 积流量较小,故可不设冷却系统,依
❖ 靠空冷的方式冷却模具即可。
7.模具闭合高度的确定
❖ 根据支承与固定零件设计中提供的经验数据 确定,定模座板:H1=25mm;上固定板: H2=25mm;下固定板:H3=40mm;支承 板:H4=25mm;动模座板:H5=25mm; 根据推出行程和推出机构的结构尺寸确定垫 块:H6=50mm。因而模具的闭合高度
❖ ⑵塑件的结构和尺寸精度、表面质量分析 ❖ ①结构分析 从零件图上分析,该零件总体形状为长方形,
在宽度方向的一侧有两个高为8.5mm,半径为R5mm的两 个凸耳,在两个高度为12mm、长、宽分别为17×14mm的 凸台上,一个带有凹槽对称分布,另一个带有4Xlmm的凸台 对称分布,因此,模具设计时必须设置侧向分型抽芯机构, 该零件属于中等复杂程度。 ❖ ②尺寸精度分析 该零件重要尺寸如:12.1mm、12.1 mm、15.1mm、 ❖ 15mm等精度为3级,次重要尺寸如:13.5 mm、17mm、 10.5mm、14mm等的尺寸精度为4~5级。 ❖ ③从塑件的壁厚上来看,壁厚最大处为1.3mm,最小处为 0.95mm,壁厚差为0.35mm,较均匀,有利于零件的成 型。 ❖ ④表面质量分析 该零件的表面除要求没有缺陷、毛刺,内 部不得有导电杂质外,没有特别的表面质量要求,故比较容 易实现。
注射模具概述
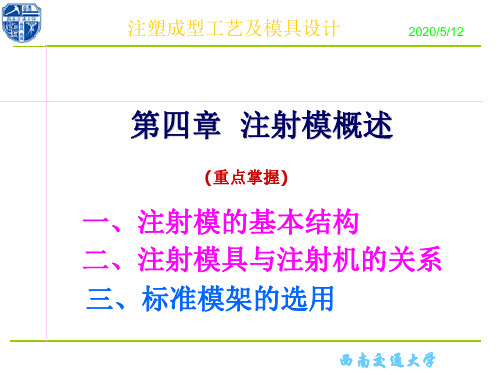
4.推出机构
作用:开模过程中,将塑件及其在流道内的凝料推出或拉出。 组成:图5—1,推杆11、推出固定板8、推板9及主流道的拉料杆10。 其中,推出固定板和推板的作用是夹持推杆。在推板中一般还固定有复 位杆,复位杆的作用是在动模和定模合模时使推出机构复位。
西南交通大学
注塑成型工艺及模具设计
5.调温系统
西南交通大学
注塑成型工艺及模具设计
1.成型部件
组成:型芯和凹模。
2018/10/14
作用:型芯形成制品的内表面形状,凹模形成制品的外表面形状。 合模后型芯和凹模便构成了模具的型腔,该模具的型腔由件13和 件14组成) 。 结构:按制造工艺要求,有时型芯或凹模由若干拼块组成,有 时做成整体,在易损坏、难加工的部位采用镶件。
2.浇注系统
又称为流道系统。 作用:将塑料熔体由注射机喷嘴引向型腔的一组进料通道。 组成:主流道、分流道、浇口和冷料穴。浇注系统的设计十分重要, 它直接关系到塑件的成型质量和生产效率。
西南交通大学
注塑成型工艺及模具设计
3.导向部件
2018/10/14
作用:①确保动模与定模合模时能准确对中; ②避免制品推出过 程中推板发生歪斜现象;③支撑移动部件重量。 组成:常采用导柱与导套,有时还需在动模和定模上分别设置互相 吻合的内、外锥面来辅助定位。
西南交通大学
注塑成型工艺及模具设计
二、注射模具按结构特征分类
2018/10/14
从模具设计的角度出发,注射模按总体结构特征分为以下几类。
1.单分型面注射模具
又称为两板式模具,是注射模具中最简单、最常用的一类,约占 全部注射模具的70%。 结构:(图5-l)型腔的一部分(型芯)在动模板上,另一部分(凹模) 在定模板上。主流道设在定模一侧,分流道设在分型面上。开模后由 于动模上拉料杆的拉料作用以及塑件因收缩包紧在型芯上,制品连同 流道内的凝料一起留在动模一侧,动模上设置有推出机构,用以推出 制品和流道内的凝料。 单分型面注射模具结构简单、操作方便,但是除采用直接浇口外, 型腔的浇口位置只能选择在制品的侧面。
第4章 普通注射模具4.4

计算模具成型零件最基本的公式为:
Lm =LS (1+S ) (4-7) 式中 Lm——模具成型零件在常温下的实际尺 寸; LS——塑件在常温下的实际尺寸; S ——塑料成型的收缩率,%。 从附表中可查到常用塑料的最大收缩率Smax和 最小收缩率 Smin,由此该塑料的平均收缩率 为: S max S min S cp 100 % (4-8)
2
在型腔、型工作尺寸计算公式的导出过程中,所涉 及到的尺寸,凡孔都是按基孔制,公差下限为零, 公差等于上偏差;凡轴都是按基轴制,公差上限为 零,公差等于下偏差,如图4-63所示。
图4-63 模具零件工作尺寸与塑件尺寸的关系
2.型腔和型芯径向工作尺寸的计算
(1)型腔径向尺寸计算
3 Lm ( LS LS S cp ) 4
会产生一定的内应力及变形。 若型腔或底板壁厚不够,当内应力超过材料 的许用应力时,型腔会因强度不够而破裂。 若型腔刚度不足也会发生过大的弹性变形, 因此导致溢料、影响塑件尺寸和精度、脱模 困难。 型腔或底板的强度与刚度计算见表4-5
(3)模具成型零件的磨损
中小型塑件模具: δc =Δ/6 大型塑件模具: δc <Δ/6 成型零件磨损的原因: 塑件脱模时的摩擦(型腔变大、型芯变小、中心距尺 寸不变);(决于塑料品种、模具材料及热处理。小 批量生产时,δc取小值,甚至可以不考虑。玻璃纤 维塑料磨损大,δc应取大值,模具材料耐磨,表面 强化好,δc应取小值。) 料流的冲刷; 腐蚀性气体的锈蚀; 模具的打磨抛光。
图4-62 成型零件的工作尺寸
1. 计算成型零件的工作尺寸要考虑的因素
(1)塑料收缩率波动 与塑料的品种、塑件的形状、尺寸、壁厚、成型工艺条件、 模具的结构等因素有关。 其塑料收缩率波动误差为: δ s = (Smax —Smin) Ls (4-5)
- 1、下载文档前请自行甄别文档内容的完整性,平台不提供额外的编辑、内容补充、找答案等附加服务。
- 2、"仅部分预览"的文档,不可在线预览部分如存在完整性等问题,可反馈申请退款(可完整预览的文档不适用该条件!)。
- 3、如文档侵犯您的权益,请联系客服反馈,我们会尽快为您处理(人工客服工作时间:9:00-18:30)。
塑料成型工艺与模具设计
4.3.3 普通浇注系统的设计
避免产生熔接痕:浇口数量多,产生熔接痕机 会也多,无特殊要求浇口不要太多;但大型板 状制品,必要时可设置多浇口减少内应力和变 形;利用溢料槽等工艺措施避免熔接痕;正确 设置浇口位置来防止熔接痕和控制熔接痕位置; 浇口位置与熔接痕位置 防止料流将型芯或嵌件挤压变形 考虑高分子取向对塑料制品性能的影响
塑料成型工艺与模具设计
4.4.4齿轮型腔的结构设计
外齿轮和型腔的关系 型腔结构:齿轮型腔加工方式有机械切削、冷 挤压成型、电火花加工、线切割、电铸、浇注 锌基合金等,不同加工方法应采用不同结构。
塑料成型工艺与模具设计
4.4.5成型零件工作尺寸计算
成型零件工作尺寸:包括外形(型腔)尺寸、内 形(型芯)尺寸、孔间距尺寸 1.计算模具成型零件工作尺寸要考虑的要素 影响塑件尺寸精度的因素包括材料、结构、成型 工艺、模具结构、制造、模具磨损等。 1)塑料收缩率波动:实际收缩率与理论收缩率 不同会引起塑件误差,小于塑件公差1/3 2)模具及成型零件制造误差:取塑件公差的1/3
塑料成型工艺与模具设计
第四章 普通注射模具
塑料成型工艺与模具设计
4.1 注射模具基本结构、分类
4.1.1注射模具的基本结构 注射模具一般由定模和动模组成。根据模具零部 件的作用,一般注射模具由以下几部分组成 (1)成型零部件 用来成型塑件形状。型腔用于成型塑件外形,型 芯用于成型塑件内腔或孔。 (2)浇注系统 熔融塑料由喷嘴到型腔的流动通道
塑料成型工艺与模具设计
4.3.3 普通浇注系统的设计
4.冷料穴和拉料杆的设计 冷料穴用于容纳冷料和拉住主流道凝料,一般开 在主流道对面动模板上。 冷料穴有多种结构形式,有底部带推杆的冷料穴、 适用推件板形式等,分别适用于不同场合。
塑料成型工艺与模具设计
4.3.4 排气与引气系统设计
1.排气系统的设计 1)为什么需要排气? 2)通过试模确定气阻的位置,然后确定排气槽 位置。 3)排气方式 间隙排气:中小型模具常用,间隙 0.02~0.04mm。
塑料成型工艺与模具设计
4.1 注射模具基本结构、分类
4.1.2注射模具的分类 1.按成型的塑料材料分:热塑性塑料和热固性塑 料模具 2.按注射机类型分:卧式、立式、角式 3.按浇注系统形式分:普通流道和热流道 4.按模具结构特征分:单分型面、双分型面、侧 向分型抽芯、带活动嵌件模具等
塑料成型工艺与模具设计
2、成型零件工作尺寸计算方法 1)只考虑塑料收缩率:Lm=Ls(1+S)适用于小 型零件 2)考虑成型过程收缩率误差、成型零件制造误 差、成型零件磨损等因素影响,按平均收缩率、 平均磨损量、平均制造误差为基准,则计算方 法如下:
塑料成型工艺与模具设计
4.4.5工作尺寸计算
注意:计算时要将塑件的基本尺寸公差转化为标 准形式,即孔标注按基孔制,下偏差为零;轴 标注用基轴制,上偏差为零;中心距标注为± 偏差。同时注意计算公式中各个参数的含义。
塑料成型工艺与模具设计
4.4.2 凸模和型芯的结构设计
2.小型芯的结构设计 小型芯单独制造后嵌入模板。常用固定方式、异 形小型芯固定、多个靠近小型芯固定
塑料成型工艺与模具设计
4.4.3 螺纹型芯和螺纹型环设计
1.螺纹型芯的结构设计 分为成型塑件上螺纹孔和固定螺母嵌件两种 设计要求 安装形式:成型螺纹孔及固定嵌件 2.螺纹型环的结构设计 结构形式:整体式和组合式
塑料成型工艺与模具设计
4.1 注射模具基本结构、分类
(3)合模、导向机构 保证合模准确,确保塑件精度 (4)侧向分型与抽芯机构 形成塑件侧面凹孔 (5)推出机构 推出塑件的机构
塑料成型工艺与模具设计
4.1 注射模具基本结构、分类
(6)加热冷却系统 实现温度调节保证成型质量,控制成型时间 (7)排气系统 排出型腔中的气体 (8)支承零部件 用来安装、固定、支撑各部分零件
塑料成型工艺与模具设计
4.3.3 普通浇注系统的设计
2)分流道的长度 分流道可分为一次分流、二次分流、三次分流等, 应尽可能短,L1=6~10mm,L2=3~6mm 3)分流道的表面粗糙度 4)分流道在分型面上的布置形式 分流道布置形式与型腔布置有关。有平衡布置和 非平衡布置两种形式
塑料成型工艺与模具设计
塑料成型工艺与模具设计
4.3.3 普通浇注系统的设计
④点浇口:用于材料黏度较低的壳形、箱型制品 是尺寸很小的特殊形式直浇口。需要两次分型, 进料口直径φ0.3~2mm ⑤潜伏式浇口:用于轴套类或外表面质量要求高 的塑件,由点浇口演变,分流道设置在分型面 上,浇口潜入分型面下面斜向进入型腔,浇口 直径0.8~2mm,斜角30°~45° ⑥护耳浇口:用于透明度高和无内应力制品
塑料成型工艺与模具设计
4.3.3 普通浇注系统的设计
3)浇口位置选择原则 避免制品产生缺陷:浇口不要正对宽大型腔 有利于熔体流动和补缩:壁厚相差较大时,浇 口应开在制品截面壁厚最大处 浇口设在能量损失最小部位,流程最短,流向 变化少,必要时进行流动比校核,如表4-2 有利于排气,不要过早封闭排气系统,形成封 闭气囊
②中心浇口:是直接浇口的变异形式,用于单型 腔,成型圆筒形、圆环形或中心带孔制品 ③侧浇口:一般用于一模多件 侧浇口又称为边缘浇口,一般开设在分型面上, 其尺寸见表4-1。有两种变异形式,扇形浇口 厚度一般0.25~1mm或1/3~2/3壁厚,宽度以不 产生涡流为准;薄片式浇口厚度0.25~0.65, 宽度取型腔宽75%~100%
塑料成型工艺与模具设计
4.3 浇注系统设计
4.3.1浇注系统的组成和作用 1.浇注系统组成 1)注塑模具的浇注系统是指熔体从注塑机的喷 嘴开始到型腔为止的流动通道。 2)浇注系统由主流道、分流道、浇口、冷料穴 组成。 主流道是指注塑机喷嘴到分流道的通道
塑料成型工艺与模具设计
4.3 浇注系统设计
型腔深度和型芯高度计算:一般可以不考虑磨 损量
塑料成型工艺与模具设计
4.4.5工作尺寸计算
(2)中心距计算: (3)螺纹型环和螺纹型芯的工作尺寸计算: 螺纹型环及型芯分别属于型腔类尺寸、型芯类 尺寸,计算时分别计算大、中、小径尺寸,但 均以塑件的螺纹中经公差b为依据;塑件螺纹 公差b参照金属螺纹公差标准中最低者选用, 型芯和型环制造过程δz取b/5或查表4-3。 螺距尺寸相当于中心距尺寸,制造公差表4-3
(1)型腔和型芯尺寸计算
型腔径向尺寸的计算: Lm=(Ls+ LsScp-3Δ/4)
塑料成型工艺与模具设计
4.4.5工作尺寸计算
型芯径向尺寸的计算: Lm=(Ls+ LsScp+3Δ/4)
注意带嵌件的塑件,Ls值应为塑件外形尺寸减去 嵌件外形尺寸;型腔尺寸以大端为准,型芯尺 寸以小端尺寸为准。
塑料成型工艺与模具设计
4.1 注射模具基本结构、分类
2.双分型面注射模具 主要用于点浇口进料的注射模具 (1)工作原理 (2)设计注意事项 浇口一般为点浇口,截面直径0.5~1.5mm 分型面分型距离应保证塑件、凝料顺利取出 通常将导柱设置在型芯凸出分型面最长的那一 侧
塑料成型工艺与模具设计
塑料成型工艺与模具设计
4.4.1 型腔的结构设计
3)底部镶拼式凹模:形状复杂的型腔底部,为 了加工方便采用 4)侧壁镶拼式凹模:较少使用,便于加工 5)四壁拼合式凹模:大型和形状复杂凹模,便 于加工;侧壁可以采用锁扣连接 组合式主要用于复杂或大型塑件。其特点是便 于加工、维修,利于排气,节省贵重金属。
塑料成型工艺与模具设计
4.3.3 普通浇注系统的设计
2.分流道的设计 分流道用于改变熔体流向,使其平稳、均衡地分 配到各个型腔。 1)分流道的截面形状与尺寸 圆形截面直径2~10mm;梯形截面按经验公式 确定,计算结果b应在3.2~9.5mm,也可在 5~10mm内选取,梯形侧面斜角α为5~10°; U型截面b=5~10mm。
塑料成型工艺与模具设计
4.4.5成型零件工作尺寸计算
3)模具成型零件磨损:熔体流动、腐蚀气体锈 蚀、脱模摩擦以及重新打磨抛光等,会造成成 型零件尺寸变化,称为磨损。一般垂直脱模方 向不考虑磨损,平行方向考虑磨损。磨损量取 塑件公差的1/6 4)模具安装配合误差:大概占1/6 塑件成型过程产生的尺寸误差为累计误差,等 于各项误差之和。
4.4 成型零件结构设计
设计内容:计算成型零件型 腔尺寸;确定型腔组合形式; 确定加工、装配等要求;关 键部位校核
塑料成型工艺与模具设计
4.4.1 型腔的结构设计
型腔也称为凹模,用于成型塑件外表面。 1.整体式凹模:用于中小型简单模具 2.组合式凹模:由两个以上零件组合形成。 1)整体嵌入式凹模:用于中小型、简单塑件模 具。通孔台肩式、无台肩、盲孔式 2)局部镶嵌式凹模:为了加工方便或易损件经 常更换场合
4.1 注射模具基本结构、分类
4.1.3注射模具的典型结构 1.单分型面注射模具 (1)工作原理:读懂装配图,在了解模具结构 的基础上分析工作原理,因为机器工作时往往 有相对运动,在分析工作原理时可以沿运动传 递的路线分析。
塑料成型工艺与模具设计
4.1 注射模具基本结构、分类
(2)设计注意事项 分流道:开设在分型面上 推出机构:使塑件在分型后留在动模一侧 主流道凝料拉料杆 分型时使主流道凝料留在动模一侧 推杆复位 确保合模时推杆回到准确位置
4.1 注射模具基本结构、分类
常见的两次分型方法: 弹簧定距拉板式、4-2 定距拉杆式 定距导柱式 摆钩式
塑料成型工艺与模具设计
4.1 注射模具基本结构、分类
3.斜导柱侧向分型与抽芯注射模具 4.斜滑块侧向分型与抽芯注射模具 5.带有活动嵌件的注射模具