轴承甩油及轴瓦间隙控制
轴瓦油位标准

轴瓦油位标准一、轴瓦安装高度轴瓦安装高度是影响润滑效果的重要因素。
一般而言,轴瓦的高度应与轴颈相匹配,以保证轴瓦与轴颈之间的间隙合理。
通常,轴瓦高度的调整是通过垫片来实现的,垫片的厚度要根据实际需要进行选择。
二、顶隙和侧隙顶隙是指轴瓦顶部与轴颈之间的间隙,侧隙是指轴瓦侧面与轴颈之间的间隙。
这两个间隙的大小对润滑效果和散热效果都有重要影响。
一般来说,顶隙和侧隙的大小应根据轴颈直径、转速以及润滑油粘度等因素来确定。
三、接触角和接触面接触角是指轴瓦与轴颈接触点的切线与垂直线之间的夹角,接触面是指轴瓦与轴颈接触的面积。
接触角的大小和接触面的分布对润滑油的分布和流动性都有影响。
通常,接触角越小,润滑油的流动性越好,但接触面也会相应减小。
因此,在选择接触角和接触面时需要综合考虑润滑效果和结构稳定性。
四、润滑油粘度润滑油粘度是影响润滑效果的重要因素。
粘度高的润滑油流动性差,但能够形成较厚的油膜,提供更好的润滑效果;粘度低的润滑油流动性好,但形成的油膜较薄,润滑效果相对较差。
因此,在选择润滑油粘度时需要综合考虑轴颈转速、负载以及工作环境等因素。
五、油膜厚度油膜厚度是指润滑油在轴瓦与轴颈之间形成的油膜的厚度。
油膜厚度对润滑效果和稳定性都有重要影响。
过薄的油膜容易破裂,导致轴瓦与轴颈直接接触,产生磨损;过厚的油膜会阻碍热量传导,导致轴瓦温度升高,影响润滑效果。
因此,在选择油膜厚度时需要综合考虑轴颈转速、负载以及工作环境等因素。
六、润滑油供应量润滑油供应量是影响润滑效果的重要因素。
供应量不足会导致轴瓦与轴颈之间润滑不足,产生磨损;供应量过多会导致油膜过厚,阻碍热量传导,影响润滑效果。
因此,在选择润滑油供应量时需要综合考虑轴颈转速、负载以及工作环境等因素。
同时,为了保证润滑油的供应量稳定,通常会使用润滑油泵进行供油。
七、油循环冷却在高速运转的情况下,轴瓦产生的热量会很高。
为了降低轴瓦的温度,保证润滑效果,通常会采取循环冷却的方式将润滑油通过冷却器进行冷却后再循环至轴瓦。
轴瓦及油挡间隙测量调整

建设单位:监理单位:质检部门:工地:班组:
年月日填
优良
轴承盖
油挡间隙
主要
mm
0.65~0.85
0.70
优良
0.45~0.65
左:0.55
右:0.55
优良
0.25~0.45
0.30
优良
分项工程质量检验评定表
工程编号:1-1-19分项工程名称:#1机组轴瓦及油挡间隙测量调整性质:主要续1
检验指标
性质
单位
质量标准
质量检验记录
单项评定
合格
优良
#4
轴
瓦
轴向间隙
B:0.84
优良
紧力
0.03~0.08
A:0.03
B:0.03
优良
轴承洼窝接触面
主要
≥75%,且均匀
接触面积≥75%,且均匀
优良
轴承盖
油挡间隙
上部
主要
mm
0.65~0.85
0.80
优良
两侧
0.45~0.65
左:0.45
右:0.50
优良
下部
0.25~0.45
0.30
优良
#2
轴
瓦
轴向间隙
调端EGV
mm
56.50±1.50
分项工程质量检验评定表
工程编号:1-1-19分项工程名称:#1机组轴瓦及油挡间隙测量调整性质:主要
检验指标
性质单位质量标准质 Nhomakorabea检验记录
单项评定
合格
优良
#1
轴
瓦
轴向间隙
调端EGV
mm
水轮发电机轴承防甩油设计和措施

・ <’ ・
小水电
"+!% 年第 " 期(总第 !)" 期)
运行与维护
!:上稳油环;":下堵气环;#:停机状态时的油位;$:运行油位 图! 轴承密封
!:上密封腔;":磁轭通风产生的密封空气进入上密封腔; #:磁轭通风产生的密封空气进入下密封腔; :密封空气由轴承排出; $ %:密封空气进入轴承; :经过通气孔和下密封腔的气流; & ’:空气 ( 油雾被吸收;):真空泵;*:油过滤器; !+:洁净空气排出机坑;!!:油回收 图 " 轴承密封方案 !
推力轴承而言,影响润滑性能的主要是油量和油形成 的油膜,油膜厚度与润滑油动力粘度的平方根成正 比,油膜内摩擦损耗与润滑油的动力粘度成正比,油 槽内搅拌损耗与润滑油动力粘度的平方根成正比。 如果油槽经常发生甩油或油气进入空气冷区系 统,会造成以下危害: (#)容易造成污染。油槽甩油或油气进入冷却 系统,会造成发电机磁极、磁轭和定子线棒的污 染。油气或灰尘进入冷却系统沉积,会导致冷却效 果变差。油污附着在绝缘层上,会加速其老化,影 响绝缘性能,威胁发电机的寿命。 (!)长期甩油造成浪费。由于油位必须在合理 位置,所以运行人员必须经常巡视油槽,不时添 加,既浪费人力也浪费物力。 (:)地面积油。会给日常运行和设备维护人员 带来不便,容易在处理缺陷时滑倒。
施,取得不错的效果。图 : 幅。 关键词:水轮发电机;轴承;防甩油设计;措施
!
轴承甩油危害性
水轮发电机推力轴承一般采用汽轮机油润滑。对
减少油雾的产生和甩油,将搅动产生的损耗和甩油 的可能性控制在一个很低的水平。 为防止油或油气进入发电机或空气冷却系统, 在发电机的转动部分和静止部分之间,油槽都进行 了很好地密封。 静止部分的密封有:推力轴承油槽有很多把合 面,都需要密封。在轴向,所有在油面以下、用螺 栓把合的结合面均采用 ; 型密封圈密封;而在圆 周方向,所有的分瓣面均采用胶水来密封。所有自 动化元件的引线电缆出口均高于油面,以防止油通 过线缆渗出油槽,并且出口的孔洞也将采用填充材 料密封。管路与油槽的连接法兰采用 ; 型密封圈 密封。 转动部分的密封有:位于油槽油位以下的所有 转动部件均增加稳油环,以减少油雾的产生和甩 油。如下所示为位于推力头外圈、推力头和推力镜 板内圈处的密封结构(见图 #) 。金属结构部件设 计成可以阻止润滑油沿着推力头、推力镜板内壁爬 升的结构,推力头外圈密封设计成允许空气进入油 槽的结构。一旦油雾产生,来自下机架底部的密封 空气和来自于通气孔由旋转产生的气流将把油雾限 制在油槽上部的腔室内,然后再由排油雾装置将油 雾吸出。允许压力空气进入的腔室将采用密封齿环 密封,保证油雾无法由此溢出。 以下推荐 ! 种有成熟运行经验的防止油气溢出 的轴承密封方式,这 ! 种方式均采用压力空气密封 (见图 !、图 :) 。
汽轮机2号轴承油档甩油原因分析及治理
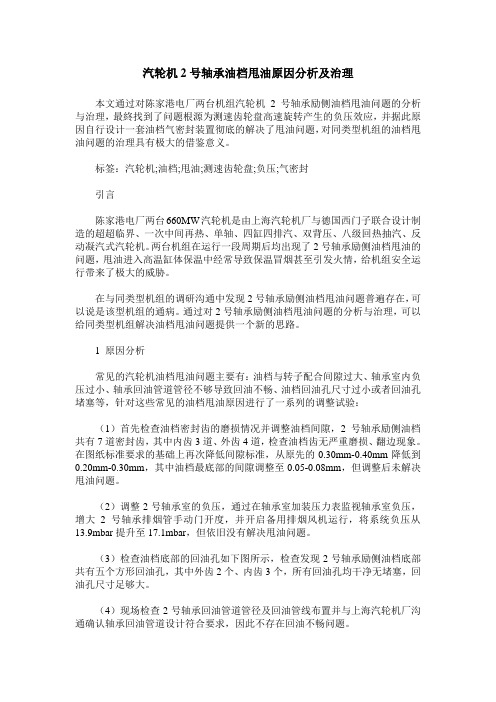
汽轮机2号轴承油档甩油原因分析及治理本文通过对陈家港电厂两台机组汽轮机2号轴承励侧油档甩油问题的分析与治理,最終找到了问题根源为测速齿轮盘高速旋转产生的负压效应,并据此原因自行设计一套油档气密封装置彻底的解决了甩油问题,对同类型机组的油档甩油问题的治理具有极大的借鉴意义。
标签:汽轮机;油档;甩油;测速齿轮盘;负压;气密封引言陈家港电厂两台660MW汽轮机是由上海汽轮机厂与德国西门子联合设计制造的超超临界、一次中间再热、单轴、四缸四排汽、双背压、八级回热抽汽、反动凝汽式汽轮机。
两台机组在运行一段周期后均出现了2号轴承励侧油档甩油的问题,甩油进入高温缸体保温中经常导致保温冒烟甚至引发火情,给机组安全运行带来了极大的威胁。
在与同类型机组的调研沟通中发现2号轴承励侧油档甩油问题普遍存在,可以说是该型机组的通病。
通过对2号轴承励侧油档甩油问题的分析与治理,可以给同类型机组解决油档甩油问题提供一个新的思路。
1 原因分析常见的汽轮机油档甩油问题主要有:油档与转子配合间隙过大、轴承室内负压过小、轴承回油管道管径不够导致回油不畅、油档回油孔尺寸过小或者回油孔堵塞等,针对这些常见的油档甩油原因进行了一系列的调整试验:(1)首先检查油档密封齿的磨损情况并调整油档间隙,2号轴承励侧油档共有7道密封齿,其中内齿3道、外齿4道,检查油档齿无严重磨损、翻边现象。
在图纸标准要求的基础上再次降低间隙标准,从原先的0.30mm-0.40mm降低到0.20mm-0.30mm,其中油档最底部的间隙调整至0.05-0.08mm,但调整后未解决甩油问题。
(2)调整2号轴承室的负压,通过在轴承室加装压力表监视轴承室负压,增大2号轴承排烟管手动门开度,并开启备用排烟风机运行,将系统负压从13.9mbar提升至17.1mbar,但依旧没有解决甩油问题。
(3)检查油档底部的回油孔如下图所示,检查发现2号轴承励侧油档底部共有五个方形回油孔,其中外齿2个、内齿3个,所有回油孔均干净无堵塞,回油孔尺寸足够大。
汽轮机轴承油挡甩油的分析及处理

汽轮机轴承油挡甩油的分析及处理汽轮机主油箱排烟风机主要给主油箱及各轴承形成微负压状态,以利于轴承回油,防止轴承油挡漏油。
某电厂350MW机组因主油箱排烟风机原因,导致了个别轴承油挡向外渗油。
本文针对此异常现象,对排油烟风机进行了治理,消除了轴承油挡漏油,取得了明显的效果。
概述某电厂发电机为空冷发电机汽轮机型号为C330/N350-17.75/0.981/540/540亚临界、单轴、双缸、双排汽、一次中间再热可调抽汽凝汽式汽轮机。
每台机组整个轴系支承在6个轴承上,其中汽轮机4个,发电机2个。
#1、#2轴承为可倾瓦支持轴承,#3、#4轴承为椭圆支持轴承,推力轴承位于高中压转子后端,为转子和汽缸的相对死点,近期出现了#4机大机4-2、4-6轴承油档处渗油严重的情况,影响机组的安全、经济运行。
1、轴承油挡渗油现象:汽轮机轴承油档渗油现象有以下几种:⑴4-6轴承外缘轻微甩油滴,造成轴承及周围有污垢,漏油靠近发电机励磁系统容易引起火灾。
⑵4-2轴承油挡出同样存在渗油的问题,造成周围有油污,且4-2轴承靠近中压后轴封处,此处温度较高且地方狭窄,漏油不容易清理,极易发生火灾事故。
2、轴承油挡漏油原因分析:造成油档渗油的原因:(1)轴承油档间隙调整不合适,超出厂家设计范围,甚至轴承油档损坏,导致渗油。
轴承固定外油档是固定在轴承箱上,与轴承同心,可调整量小。
而在轴运行时,其运行轨迹为椭圆形状,椭圆的长轴方向必然磨损油挡齿片,使得间隙变大,轴承箱内四处喷溅的透平油顺着间隙往外溢流。
⑵轴承箱内负压较小或者形成正压,导致油气向外喷射,凝结成油滴。
经过技术人员长时间的观察,发现外油档处存在的轻微渗油现象可能不是渗油,而是冒出的油烟凝结成油滴。
因为油烟是轴与轴承摩擦生热使润滑油产生的,其比重较轻,自然留在轴承箱的上部空间,若轴承座有负压,便可以随着回油管返回主油箱,但现在轴承座内负压太小,使得滞留的油烟密度越来越大,当压力达到一定值时,必然从间隙处往外冒出。
白沙河电站水导轴承甩油的原因分析及处理措施

白沙河电站水导轴承甩油的原因分析及处理措施摘要:白沙河水电站位于湖北省十堰市竹溪县兵营镇境内,电站安装两台混流式水轮发电机组,从投入运行以来,两台水轮机相继出现了水导轴承转动油盆甩油现象,甩油后油量不够,使得水导瓦温升高,为了保证机组安全运行,需要定期向水导轴承加油。
通过本次对1号机组A级检修,经分析、计算、试验等方法,找到了油盆甩油的真正原因并进行了处理,取得很好的效果。
关键词:水导轴承;转动油盆;甩油;处理1 概述白沙河水电站位于湖北省十堰市竹溪县兵营镇境内,距离十堰市竹溪县65公里,距离竹溪县兵营镇6.5公里,电站建设有2台25MW水轮发电机组,总装机容量50MW。
电站两台机组2013年正式投产发电,至今已运营9年。
水轮机主要技术参数如下:水轮机型号: HLD294-LJ-186额定水头:82m最高水头:91.6m最低水头:66m额定转速:375 r/min飞逸转速:725r/min吸出高程:H S≤-3.0m额定流量:32.25m³/s额定功率:25000KW标准编号:GB/T15468—2006水轮机水导轴承为稀油自润滑导轴承,水导瓦由四瓣组成,瓦面呈抛物线形状。
由转动油盆、油盆盖、轴瓦、轴承体、外置冷却器、上油箱、毕托管等组成(见图1)。
水导轴承油路循环情况如下:当机组在运行状态时,转动油盆和主轴一起转动,转动油盆内的润滑油在离心力的作用下,通过毕托管进入外置冷却器,冷却后的润滑油进入上油箱,上油箱的油经过水导瓦热交换后流回转动油盆,转动油盆的油在离心力作用下,再次通过毕托管进入外置冷却器,如此循环。
图1 水轮机水导轴承主要结构2转动油盆甩油现象2013年,1号、2号机组相继投入运行,运行后不久,在两台机组顶盖上发现有大量的油迹,在水导轴承支架内表面和主轴密封排水管表面附着有油迹。
从水导上油箱油位观察孔观察,发现上油箱油位不高,油位有下降趋势。
运行一段时间后停机检查,发现转动油盆油位从135mm(水导转动油盆设计正常油位是135mm)下降到110mm,机组每运行一周左右时间,就需加1次润滑油,停机检查转动油盆油位均有下降现象。
卧式机组推力轴承甩油问题的分析与改造

卧式机组推力轴承甩油问题的分析与改造云创通手机[摘要]文章介绍潘家口防汛自备电站两台卧式机组推力轴承甩油问题的分析改造方法,及其在机组生产运行中的效用。
[关键词]推力轴承;甩油;分析;改造1. 概况潘家口防汛自备电站是利用潘家口大坝1号泄洪底孔,在泄洪道铺设钢管,安装两台4000KW卧式混流水轮发电机组,水轮机型号为HLA296-WJ-96,发电机型号为SFW4000-10/1250,额定转速600rpm。
1996年10月投产,主要在防汛、供水期发电,多年平均发电量1979万千瓦时。
该机组ф320推力轴承九块巴氏合金推力瓦和一个巴氏合金筒式导瓦共用一个油箱,其储油量60L,稀油润滑。
轴瓦与轴颈两侧设计间隙为0.24,0.32mm,其顶部设计间隙为0.48,0.64mm,设计要求轴向串动量不大于0.5mm。
安装后轴瓦与轴颈两侧间隙为0.25mm,其顶部间隙为0.41mm。
轴向串动量为0.81,0.91mm。
轴承端盖与主轴之间为梳齿密封,安装后其上、下间隙分别为0.5mm、0.2mm。
机组投入运行的前几年里,推力轴承导瓦一侧端盖甩油问题严重影响机组正常运行。
2.甩油问题分析机组投入运行后,由于推力轴承端盖存在甩油问题,导致轴承端处集电环与碳刷接触不良,产生火花,而且烧损集电环表面,污染周围设备,每运行一至二天需停机清扫一次集电环,严重影响机组安全运行和效益。
因此,对问题存在的原因进行分析:卧式机组推力轴承润滑油是在大推力盘运转与刮油板作用下,不断地将润滑油从冷却腔泵入润滑腔,与此同时,润滑腔就产生了一定的油压,在油压力的作用下,加之推力盘运转中的轴向振动和机组的高速运转,使润滑油沿着主轴经导瓦和端盖间隙呈螺旋状带出,在离心力的作用下,洒落于周围设备。
在油槽注油量过量的情况下,甩油问题会更加严重。
3.改造方案机组运转,轴承端盖与主轴之间即使有密封也会有间隙,油就会源源不断地被甩出。
要有效地解决甩油问题,就必须依附轴承端盖设计一个与油源隔离的密封环腔。
轴承间隙常用的调整方法

轴承间隙常用的调整方法
滚动轴承的间隙分径向间隙和轴向间隙两类﹐轴向间隙就是当一个套圈固定时﹐另一套圈沿轴向的最大活动量﹔径向间隙就是当一个套圈固定时﹐另一套圈沿径向的最大活动量。
滚动轴承应具有必要的间隙﹐如轴承间隙过大﹐将使用时承受负荷的滚动体减少﹐轴承寿命降低﹐轴承的旋转精度也随之降低﹐引起振动和噪声﹐在有冲击负荷时﹐这种影响尤为显著﹔如轴承间隙过小﹐工作中容易发热和磨损﹐同时会降低轴承正常工作﹐延长使用寿命的重要措施之一。
轴承间隙常用的调整方法有两种:
<1>用垫片调整通过改变轴承盖处的垫片厚度﹐调整轴承的轴向间隙。
<2>用调整螺钉调整先拧紧调整螺钉﹐使轴承无间隙﹐然后根据所需要的轴向间隙﹐将螺钉拧到一定角度a
a=s/p*360度
其中S为轴承所要求的间隙 P为调整螺钉的螺距
调好后把调整螺钉锁紧即可。
滚动轴承的预紧
在装配角接触球轴和深沟球轴承时﹐如果给轴承内外圈以一定的轴向负荷﹐这时内外圈将发生相对位移﹐结果消除了内外圈与滚动体间的间隙﹐产生了初始的弹性变形。
这种方法称为轴承预紧。
预紧能提高轴承的旋转精度和使用寿命﹐减少机器在工作时的振动。
轴承预紧方法有三种﹕
<1>用轴承内外垫环厚度来实现预紧。
<2>摩擦成对使用的轴承内圈或外圈实现预紧﹐当夹紧内圈或外圈时即可实现预紧。
<3>调节轴承锥形孔内圈的轴向位置进行预紧。
- 1、下载文档前请自行甄别文档内容的完整性,平台不提供额外的编辑、内容补充、找答案等附加服务。
- 2、"仅部分预览"的文档,不可在线预览部分如存在完整性等问题,可反馈申请退款(可完整预览的文档不适用该条件!)。
- 3、如文档侵犯您的权益,请联系客服反馈,我们会尽快为您处理(人工客服工作时间:9:00-18:30)。
轴承甩油及轴瓦间隙控制王艳红湖南零陵发电设备有限公司 (425007)分块瓦式水导轴承与筒式水导轴承相比,具有以下特点:①轴瓦间隙调整灵活、方便;②瓦与轴的接触面小,瓦温不易上升,润滑条件好;③适应顶盖的能力较强,对顶盖的刚度要求相对低些;④零部件较轻,制造容易,安装方便。
随着水电机组向高转速、大容量方面发展,可以预计,将会有越来越多的机组采用分块瓦式水导轴承。
但甩油和轴瓦间隙运行时增大,一直是影响分块瓦式轴承安全使用的两大因素。
本文通过分析轴承甩油与轴间隙运行过程中增大的原因,寻求解决的方法,以求通过努力,保证轴承的安全运行。
1 甩油机组运行时,水导轴承中的油或油雾跑出轴承油槽的现象,称为轴承甩油。
这不仅浪费润滑油、污染环境,有时机组因甩油严重,而致使运行油位下降造成油位过低,引起烧瓦。
因此,轴承的甩油一直是轴承设计时的一个需重点考虑的问题。
轴承甩油有两种情况:一是润滑油通过主轴轴领内壁与挡轴筒之间的间隙,甩向主轴表面,这种甩油称为轴承内甩油;另一种情况是润滑油通过旋转部件与轴承盖板间的间隙甩向盖板外部,这称之为外甩油。
1.1 内甩油内甩油形成的原因:机组在运行时,由于主轴密封上的护罩旋转鼓风,使主轴轴内下侧至油面之间,容易形成局部负压,使油吸高或涌溢而甩溅到挡油筒外部,形成内甩油。
这是内甩油形成的一个主要原因;另一个形成内甩油的主要原因是:由于挡油管与主轴轴领圆壁之间,因制造、运输、安装时的原因,产生不同程度的偏心,使工件之间的油环不均匀。
如果该处间隙设计时取得很小,则相对偏心率就增大,这时主轴轴领内壁带动其间静油旋转时,出现油泵效应,使润滑油产生较大的压力脉动,导致润滑油上行而出现甩油。
内甩油的处理:根据内甩油的产生原因,在设计时可采取以下的措施来减少或消除甩油。
在主轴轴领颈部上钻均压斜孔,孔径为20~40mm,按圆周等分,布置3~6个孔,使轴领内外通气平压,防上因内部负压而使油面被吸高甩油。
在主轴密封的护罩上加焊一层平板,降低密封护罩搅拌而在轴承下部而形成负压,减小内甩油发生的可能性。
加大轴领内侧与挡油管之间的间隙,使相对偏心率减小,从而降低了油面的压力脉动值,保持了油面的平衡,防上了润滑油的上窜。
实际使用情况表明,轴领内侧与挡油管之间的距离增大,可使润滑油的搅动造成的甩油大幅度降低。
加大挡油筒顶端与油面的距离,避免运行中的润滑油在离心力作用下翻过油筒溢出。
加装稳油挡油环。
运行时,稳油挡油环起着阻旋作用,增大了内甩油的阻力。
部分甩出来的油通过挡油环上环板上的小孔回到轴承槽中,挡油环与挡油筒之间呈静止状态,不会因主轴轴领的旋转运动而使油面波动。
上述措施经过在电站中的运用,证明是有效的、可行的,能满足电站安全运行的需要。
但在使用过程中,也发现上述措施的不足之处。
由于挡油筒加高,使挡油筒的刚性成为一个突出问题。
由于刚性问题,造成挡油筒存在不同程度的变形。
这样,一方面合缝面的密封受到影响;另一方面,在安装时,受轴领结构的限制,挡油筒圆度的调整、测量比较困难,结果是油泵效应还有不同程度的存在。
由于轴领内侧与挡油筒的距离加大,相应轴瓦直径加大,轴承径向尺寸变大。
但同时,轴承油槽体积不变或变小,这对降低轴瓦瓦温不利。
在轴领内侧与挡油筒结构设计方面,在交流学习时,我们发现其它厂家在这方面的结构设计值得借鉴。
在日本伊吹电站水轮机设计过程中,日立公司提供了水导轴承的结构参考图。
该轴承挡油筒处结构紧凑,整个轴承体积不大,但其油槽储油量较大。
我们认为日立公司在挡油筒设计上采取了如下措施:挡油筒设计时选择等刚性截面,根部壁厚,随着挡油筒高度增加,圆筒壁厚随之降低,从而通过选择合理的壁厚,控制刚性。
在分轴领内侧根部对应在挡油筒处设挡油环,抑制润滑油的液面波动,阻止润滑油上窜形成甩油。
部分越过挡油环的润滑油,由于轴领内侧根部台阶的作用,无法上移,在重力作用下流回油槽,这样整个挡油筒设计就紧凑。
二滩水电站设计的水导轴承,为防止轴承内甩油,其挡油筒结构设计方面也很有特色。
该挡油筒设计独特之处在于其导流叶栅与挡油环的布置。
其导流叶栅位于正常工作油面以下,与油筒壁成10°下压角。
旋转的润滑油流经叶栅后形成一个下压分力而使油上窜受阻,有效减少内甩油,并且该挡油筒还在正常工作油面以下布置有伞型挡油环(目前,我厂的挡油环均置于正常油面以上,相对比较而言,就显得挡油筒较高)。
这样,由于挡油环的存在,即使少量润滑油通过叶栅上爬后也难通过两道伞型挡油环,故内甩油得到有效控制。
如果将上述新结构运用于我厂水导轴承上,能有效降低挡油筒高度,简化加工与安装技术要求,并且还可以为解决已运行水导轴承出现的内甩油,提供借鉴。
1.2 外甩油外甩油形成的原因:对于水导轴承,润滑油从轴承盖板处以油珠的形式逸出形成甩油的情况很少,更多的是以油雾形式,从轴承盖板缝隙处逸出,形成甩油。
主轴轴领下部开有径向进油孔或开有与径向成某一角度的进油孔。
当主轴旋转时,这些进油孔起着油泵的作用,把润滑油输送到轴瓦与轴领之间的空隙内及轴瓦之间的轴承油槽中。
如果进油孔呈斜向布置,高速射油碰上工件后,一部分油会因其粘性而附着在工件上,另一部分会朝另一方向反射出去,到处飞溅,形成大量的雾状油珠。
同时,由于主轴轴领的高速旋转,造成轴承油槽内油面波动加剧,从而产生许多油泡。
当这些油泡破裂时,也会形成很多油雾。
另外,随着轴承温度的升高,使油槽内的油和空气体积逐渐膨胀,从而产生一个内压。
在内压的作用下,油槽内的油雾随气体从轴承盖板缝隙处逸出,形成外甩油。
外甩油的处理:在主轴轴领根部开径向进油孔,避免了开斜向孔,由于产生射油,造成油面紊乱、飞溅大、易甩油的缺陷。
合理确定进油孔中心与轴瓦中心的距离,这是因为进油也的吸油点,如果太高,容易产生大量的气泡,从而增加甩油的可能性。
在油槽内设稳流板。
它的作用是将润滑油与旋转的轴领分隔开,使润滑油不受旋转件粘附作用的影响(油槽内的润滑油不跟轴领一起旋转或不被搅动),使油面较平稳,减少油泡的产生,并且稳流板还可以避免循环热油短路,这对控制轴承温度也有好处。
合理确定轴领所形成润滑油的动压头。
润滑油的动压头过大,会造成油流飞溅且产生大量油泡,不但易造成甩油,同时也会降低润滑油的热传导能力。
润滑油的动压头大小与机组和轴领尺寸有关,因此,在机组确定整体方案时,选择合适的轴领尺寸,对减小甩油有利。
合理的选择油位,不要将油面加得过高。
一般而言,水导轴承正常静止油面不应高于轴瓦中心。
油位过高,既对降低轴瓦温度无益,又会增大轴承甩油出现的可能性。
在轴承盖板与主轴配合处迷宫式密封。
通过密封部位形成多次扩大与缩小的局部流体阻力,使渗漏的油气混合体的压力减小,从而防止油雾从密封盖与旋体之间泄漏。
2 轴瓦间隙增大原因及其处理2.1 轴瓦间隙运行时增大原因目前,我厂设计生产的分块瓦导轴承多是调整螺钉支承导轴瓦的结构,该结构制造简单,调整方便。
不足之处在于:轴承受外载荷能力不如楔子板式分块瓦轴承,而且随着运行时间的加长,导瓦间隙会逐步增大,导致水导轴承处的摆度过大,影响机组的安全运行。
轴瓦间隙增大的主要原因是由作用在机组转动部分上的不平衡外力反复作用所引起的。
在机组刚开启时,圆周方向暂不稳定的水流很容易使转轮连着主轴偏心受力,该不平衡交变力使水导轴承处的承重部件受作用力加剧。
另外,机组在非最佳工况运行时,不平衡的水流冲击力也将使水导轴承处的受力恶化,由于水导轴承支承部件受交变力的过大作用,其结果是:·调节螺钉出现松动;·承重工件间隙被压缩;·调节螺钉头部及铬钢块上有压伤、磨损;·支承螺套与挡油箱焊接处出现裂纹等。
这些情况,导致轴领与轴瓦间的间隙出现增大,主轴水导轴承处的摆度超标。
由于摆度超标的影响,使运行中的水轮发电机组的主轴摆度,固定部件的振动增大,反过来,又引起水导轴瓦处交变力增大,导致支承部件出现更大的损坏,影响机组安全运行。
另外,由于支承部件材质缺陷,加工处存在应力集中也将加剧水导轴瓦间隙的增大。
2.2 轴瓦间隙运行时增大的处理措施轴瓦采用窄长型的条状瓦:这是因为,窄长型条状瓦的刚性好,可减小轴瓦运行时变形。
调节螺钉采用锻40Cr,其头部的淬火处理改为氮化处理,氮化层深不低于1.3mm,使其硬度为HRC40~50,调节螺钉截面变化处采用圆弧过渡。
调节螺钉、支承螺套处采用高精度的细牙螺纹,提高调节螺钉的防松能力。
轴瓦背面的工艺孔边缘是应力集中区,加工时将此孔堵塞铣平,从而减小对铬钢垫板的损坏。
增加铬钢垫板直径,加大其厚度。
优化设计支承体与挡油箱的配合处结构,以减小焊缝的受力。
同时将支承体与挡油箱的焊接点改为V型坡口圆周满焊,提高焊缝的抗拉强度。
改进调节螺钉的锁锭方式和结构,提高锁紧扁螺母与止动垫片等配合接触表面粗糙,减小承重部件的游动间隙。
合理选择挡油箱截面形状,使其具有良好的刚性,减小运行时的受力变形。
将轴承瓦的间隙适当调小。
采用非同心型导轴瓦:我厂目前使用的导轴瓦基本上全是同心型导轴瓦。
与同心型导轴瓦相比,非同心型导轴瓦具有受力特性良好,承载能力高的优点,并可适当缩小轴瓦平均瓦隙,以改善机组的稳定性能。
采用楔子板支承导轴瓦结构:在机组承受较大径向载荷的情况下,与调节螺钉支承导轴瓦结构相比,楔子板结构轴瓦间隙相对稳定,目前,楔子板结构在我厂水导轴承应用上还是一个新领域。