金属磷化技术的回顾与展望
金属磷化技术的回顾与展望

2. 1. 2 磷化处理 生产中常采用各种磷化处理技术满足不同的要求。 依据化
学溶液中参与成膜的金属离子同异, 分为不同体系的磷化, 常用 的有锌系、锌钙系、锌锰系、锰系、铁系、非晶相轻铁系类, 其一般 性能及磷化膜微观结构见表 1、图 2、图 3。
表 1 常用磷化体系的一般性能
磷化
槽液
体系
主要组成
表2目前工业领域磷化技术的应用情况用途常用磷化体系后处理工序性能h室内防锈期及应用范例工序间防锈库存防锈锌系锌锰系1020钝化或浸油824312长效防锈锌系锌锰系1030浸防锈油涂脂48120硼砂或皂化处理冷加工皂化处理冷加工挤压1030皂化处理精密配合承载活塞环压缩机等大配合承载齿轮离合器片等阳极电泳80400自行车农机车等阴极电泳无或铬钝化720200汽车等静电喷漆零部件仪表等粉末涂装500电器办公具等空气喷漆4其他有色金属磷化锌及其合金的表面处理主要是铬钝和磷化主要作用是涂装打底增强漆膜附着力
摩) 的 SEM 图谱 500×
的 SEM 图谱 500×
防锈磷化的后处理非常重要, 因为靠磷化膜本身防锈能力
是非常有限的, 而且盐雾试验只能到几小时。 一般要进行涂油涂
漆, 最好是涂防锈油, 经过涂油涂脂等后处理, 防锈能力甚至可提
高几十倍。
冷加工润滑型磷化必须进行皂化后处理, 以提高磷化膜的
润滑性。 皂化可采用工业肥皂粉、硬脂酸钠。 耐磨减摩磷化是否
树 枝 状, 针状, 片状, 孔隙较多
漆前打 底、防 锈 和冷加工 减摩润滑
呈紧密颗 粒状, 柱状, 孔隙较少
涂装前打 底及防锈
Zn2+ ,M n2+ , NO 3锌锰系 H 2PO 4- , H 3PO 4,
促进剂
铝合金磷化工艺的研究

铝合金磷化工艺的研究随着现代工业的快速发展,铝合金作为一种轻质、高强度、耐腐蚀性能优异的材料,被广泛应用于航空航天、汽车制造、建筑工程等领域。
然而,铝合金在实际应用过程中,常常会受到腐蚀的侵蚀,降低了其使用寿命和性能。
为了改善铝合金的抗腐蚀性能,提高其耐用性,研究人员开始探索铝合金磷化工艺。
铝合金磷化工艺是一种通过在铝表面形成磷化物层来提高其抗腐蚀性能的方法。
磷化物层具有较高的硬度、耐磨性和耐腐蚀性,可以有效地保护铝合金表面免受腐蚀的侵蚀。
磷化工艺可以分为化学磷化和电化学磷化两种方式。
化学磷化是将铝合金表面浸泡在含有磷酸盐和其他助剂的溶液中,通过表面化学反应,在铝表面形成一层磷化物覆盖层。
化学磷化工艺简单、成本低廉,可以在常温下进行。
然而,磷化层的厚度和质量受到多种因素的影响,如酸性溶液浓度、温度、浸泡时间等,需要进行严格的工艺控制。
电化学磷化是利用电化学方法,在铝合金表面形成磷化物覆盖层。
通过在溶液中施加电流,使铝表面发生氧化还原反应,生成磷化物层。
电化学磷化可以控制磷化层的厚度和质量,具有较高的工艺可控性。
然而,电化学磷化工艺相对复杂,需要专门的设备和技术支持。
铝合金磷化工艺的研究主要集中在以下几个方面:1. 工艺参数的优化。
磷化工艺的效果受到多种因素的影响,如溶液成分、温度、pH值等。
研究人员通过对不同工艺参数的调整和优化,寻找最佳的磷化工艺条件,以获得最佳的磷化效果。
2. 研究磷化机理。
理解磷化过程中的化学反应机理对于优化磷化工艺具有重要意义。
研究人员通过表面分析技术和材料科学方法,深入探究磷化过程中的物理化学现象,揭示磷化机理,为磷化工艺的改进和控制提供理论依据。
3. 磷化层的性能评价。
磷化层的性能评价是研究铝合金磷化工艺的重要一环。
研究人员通过对磷化层的显微结构、硬度、耐磨性、耐腐蚀性等性能进行测试和分析,评价磷化层的质量和性能,为磷化工艺的应用提供依据。
铝合金磷化工艺的研究对于提高铝合金的耐腐蚀性能,延长其使用寿命具有重要意义。
紧固件磷化处理的发展

紧固件磷化处理的发展磷化处理就是将金属浸在由磷酸、磷酸盐和其他成分组成的磷化液中,经过化学作用而在金属表面生成一种不溶性的磷酸盐层,俗称磷化膜。
磷化膜主要由磷酸铁、锌、锰、钙等组成,厚度一般在5~20μm颜色一般由暗灰色到黑灰色,它的基体结合牢固,具有良好的润滑性、耐蚀性及较高的电绝缘性等。
磷化处理所需设备简单,操做方便,成本低,生产效率高,被广泛地应用于机械、车辆、船舶、航空航天及家电等行业。
近年来,紧固件行业迅猛发展,越来越重视紧固件表面处理技术,为此,磷化处理也得到极大的发展。
①磷化处理温度由高温向中温、低温、常温发展。
一般情况下,高温磷化工艺形成的磷化膜结晶粗大,膜厚,磷化中产生的沉渣很多,消耗的热能大,挂灰严重。
中温、低温、常温磷化形成的磷化膜均匀致密、膜薄,能耗低,物料消耗小。
②磷化工艺向简单化发展。
有的磷化产品可直接刷涂,如“四合一”、“三合一”等常温磷化产品。
有的简化了工艺流程,磷化、钝化并为一道工序,而且产品的品质技术指标仍能达到、甚至有的指标超过了国家标准。
③磷化产品组分复杂化。
这样提高了磷化的品质,降低了磷化温度,加强了磷化工作液的稳定性。
④减少污染、降低成本。
重点解决磷化产品中的亚硝酸盐、重金属、磷酸盐、高温、酸雾给环境造成的污染,降低了为改善环境所付出的成本。
磷化工艺的确定,主要是以下两个方面。
第一,优选磷酸液。
磷化膜的品质优劣主要表现在晶体粗细和致密程度、表面有无沉淀物及膜厚等方面,它们的差异直接影响磷化膜的品质。
目前普遍采用磷化膜主要由铁系、锌系、锰系、锌钙系等磷酸盐溶液进行磷化,其中锌钙系性能最优良。
第二,控制工艺参数。
关键要控制磷化温度(25~40℃),时间(3~20min),促进剂含量(3~5气点)及总酸度(20~40点)和游离酸度(0.8~3点)。
温度过太低则不能成膜或成膜速度慢,膜不完整,易泛黄;反之,膜粗大,耐蚀性低,同时槽液稳定性变差,沉渣增多。
促进剂含量低,成膜慢,膜层泛黄;反之,沉渣明显增多,膜层带彩色。
磷化技术研究现状及展望

价值工程1介绍现代磷化技术起源于上世纪初,第一个铁盐磷化是将铁屑与磷酸反应制得磷化剂[1],与之类似又出现了锰系磷化[2,3]、锌系磷化[4]等磷化体系。
磷化技术用途广泛,主要用于防锈、耐磨与涂漆底层[5]。
为了起到完全覆盖金属表面达到减少氧化作用,防锈磷化需要更紧密厚实的磷化膜,多采用重型磷化技术,例如中温锌系、锰系、锌锰系磷化。
锰系磷化因其自身耐磨及多孔特点,可提高结构件表面存储润滑油脂进而改善润滑性、抗热性、吸震性,以及耐磨性能。
此外,在冷加工成形过程中,金属与模具间将产生相对摩擦运动,影响模具使用寿命。
锌系和锌钙系磷化[6]提供的润滑层覆盖在金属表面起到润滑作用,可减少冷加工过程中摩擦力,提高模具的使用寿命。
涂漆底层是磷化技术的最大应用场景,一般为薄型磷化,但要求磷化膜均匀、细致。
对磷化膜品质的测定和分析在宏观上可用划擦法试验并用肉眼观察其颜色和宏观质量,在微观层面上可用SEM 进行观察磷化膜的形貌以及金属表面磷化膜的覆盖率,磷化膜晶体结构可借助X 射线衍射仪进行测试,孔隙率可用电化学测量的方法计算得到[7]。
2磷化原理磷化过程是在金属表面通过金属与酸性磷化液反应形成转化膜的复杂过程,包括化学与电化学反应[8]。
首先发生的是金属原子在酸性环境下的氧化:(1)阴极还原反应:阳极氧化反应:同时在金属表面,磷化液中的促进剂加速氧化作用:(2)此时磷化工作液中存在游离磷酸的三级电离平衡以及可溶性重金属磷酸盐的水解平衡:(3)(4)其中Me x+为锌、铁、锰、钙等金属离子。
随着反应的进行,溶液酸度下降(即H +浓度下降),公式(3)向右反应进行,促进公式(2)反应的进行。
当金属表面附近溶液中PO 3-4的浓度与金属离子Me x+(如Zn 2+、Ca 2+、Mn 2+、Fe 2+、Al 3+等)浓度超过其各自的溶度积常数Ksp 时,公式(4)在金属表面最终形成致密的磷化膜[9]。
3磷化技术磷化技术按实施过程可分为:磷化前处理,磷化和磷化后处理三个部分。
钢铁件磷化处理技术的应用及发展趋势

钢铁件磷化处理技术的应用及发展趋势摘要:本文就钢铁的磷化处理做了较为详细的叙述,包括磷化处理的分类、工艺、磷化液的选取原则,以及钢铁磷化处理发展过程,最后主要从磷化药剂和磷化设备两方面来简述了磷化处理未来的发展趋势。
关键词:钢铁磷化处理;工艺;原理;磷化剂;发展趋势Abstract: In this paper, phosphate processing steel do a more detailed description, including the classification of phosphate processing, process, selection principle phosphate solution, as well as iron and steel phosphate processing development process, the last major pharmaceutical and phosphate from phosphate both devices to briefly phosphating future trends.Key words: Iron phosphate treatment; Principle; Bonderite; Development trends.1、引言目前随着国民经济的快速发展,钢铁已变成现代生产生活中必不可少的金属材料。
由于铁的物理化学性质决定了它极易受环境的影响,与周围的介质发生化学反应生成锈蚀,使后处理的质量无法保证,从而减少使用寿命。
为解决这个问题,研究金属的防护措施,采用磷化处理技术。
钢铁表面磷化处理,是用化学的方法对要涂装的金属制品进行的必要的预处理。
将金属表面与含磷酸二氢盐的酸性溶液接触,通过化学与电化学反应形成一种稳定的、不溶性的无机化合物膜层[]1。
其主要作用是:通过对金属表面的磷化预处理。
浅析金属常温磷化及其发展趋势
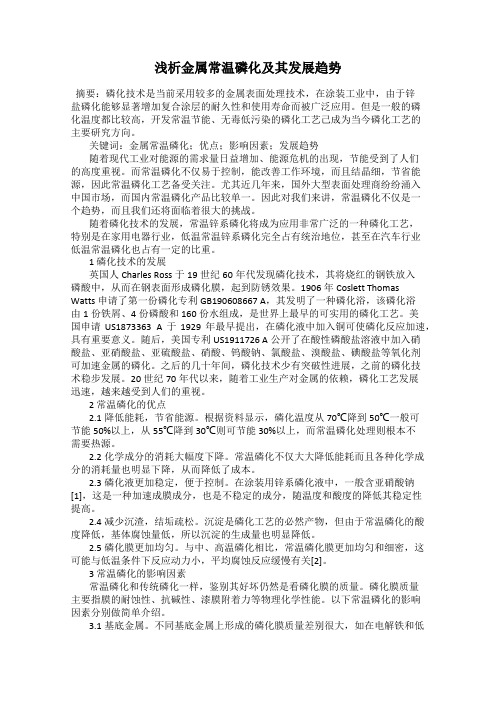
浅析金属常温磷化及其发展趋势摘要:磷化技术是当前采用较多的金属表面处理技术,在涂装工业中,由于锌盐磷化能够显著增加复合涂层的耐久性和使用寿命而被广泛应用。
但是一般的磷化温度都比较高,开发常温节能、无毒低污染的磷化工艺己成为当今磷化工艺的主要研究方向。
关键词:金属常温磷化;优点;影响因素;发展趋势随着现代工业对能源的需求量日益增加、能源危机的出现,节能受到了人们的高度重视。
而常温磷化不仅易于控制,能改善工作环境,而且结晶细,节省能源,因此常温磷化工艺备受关注。
尤其近几年来,国外大型表面处理商纷纷涌入中国市场,而国内常温磷化产品比较单一。
因此对我们来讲,常温磷化不仅是一个趋势,而且我们还将面临着很大的挑战。
随着磷化技术的发展,常温锌系磷化将成为应用非常广泛的一种磷化工艺,特别是在家用电器行业,低温常温锌系磷化完全占有统治地位,甚至在汽车行业低温常温磷化也占有一定的比重。
1 磷化技术的发展英国人Charles Ross于19世纪60年代发现磷化技术,其将烧红的钢铁放入磷酸中,从而在钢表面形成磷化膜,起到防锈效果。
1906年Coslett ThomasWatts申请了第一份磷化专利GB190608667 A,其发明了一种磷化浴,该磷化浴由1份铁屑、4份磷酸和160份水组成,是世界上最早的可实用的磷化工艺。
美国申请US1873363 A于1929年最早提出,在磷化液中加入铜可使磷化反应加速,具有重要意义。
随后,美国专利US1911726 A公开了在酸性磷酸盐溶液中加入硝酸盐、亚硝酸盐、亚硫酸盐、硝酸、钨酸钠、氯酸盐、溴酸盐、碘酸盐等氧化剂可加速金属的磷化。
之后的几十年间,磷化技术少有突破性进展,之前的磷化技术稳步发展。
20世纪70年代以来,随着工业生产对金属的依赖,磷化工艺发展迅速,越来越受到人们的重视。
2 常温磷化的优点2.1降低能耗,节省能源。
根据资料显示,磷化温度从70℃降到50℃一般可节能50%以上,从55℃降到30℃则可节能30%以上,而常温磷化处理则根本不需要热源。
钢铁件磷化处理技术的应用及发展趋势

钢铁件磷化处理技术的应用及发展趋势摘要:本文就钢铁的磷化处理做了较为详细的叙述,包括磷化处理的分类、工艺、磷化液的选取原则,以及钢铁磷化处理发展过程,最后主要从磷化药剂和磷化设备两方面来简述了磷化处理未来的发展趋势。
关键词:钢铁磷化处理;工艺;原理;磷化剂;发展趋势Abstract: In this paper, phosphate processing steel do a more detailed description, including the classification of phosphate processing, process, selection principle phosphate solution, as well as iron and steel phosphate processing development process, the last major pharmaceutical and phosphate from phosphate both devices to briefly phosphating future trends.Key words: Iron phosphate treatment; Principle; Bonderite; Development trends.1、引言目前随着国民经济的快速发展,钢铁已变成现代生产生活中必不可少的金属材料。
由于铁的物理化学性质决定了它极易受环境的影响,与周围的介质发生化学反应生成锈蚀,使后处理的质量无法保证,从而减少使用寿命。
为解决这个问题,研究金属的防护措施,采用磷化处理技术。
钢铁表面磷化处理,是用化学的方法对要涂装的金属制品进行的必要的预处理。
将金属表面与含磷酸二氢盐的酸性溶液接触,通过化学与电化学反应形成一种稳定的、不溶性的无机化合物膜层[]1。
其主要作用是:通过对金属表面的磷化预处理。
国内磷化技术现状与发展趋势

表 l 采 用低温 磷化 能耗 的消 减率 , %
磷 化 温度 ( ) —\ ℃
55
步 , 而 大 大 提 高 了磷 化 膜 的耐 蚀 性 及 漆 膜 的配 套 从
性 。 目前 , 随着 社 会 的 发 展 与 进 步 , 们 对 磷 化 产 人
品的 要 求 也 愈 来 愈 高 , 不 但 希 望 它 性 能 优 良 , 即 更 希望它能满足社会的环境要求 、 人们 的健 康 要 求 及 经 济 要 求 。所 以 , 无毒 环 保 、 成 本 , 性 能 就 成 为 低 高
磷 酸 盐溶 液 反应 而 在 其 表 面 形 成 磷 酸 盐 保 护 膜 的
谋 求 降 低 其 成本 , 了调 整 配 方 , 短 磷 化 成 分 的 除 缩
药剂 用 量 以外 , 降低 磷 化 温 度 、 少 能 耗 也 成 为 降 减 低成 本 的 重 要 手 段 。 根 据 资 料 显 示 , 化 温 度 从 磷 7 ℃ 降 到 5 ℃ 一般 可 以节 能 5 % 以上 , 5 C 降 0 0 0 从 5
Ke r s: o ph tng a c l r t r s a us t nd nc y wo d ph s a i c ee a o t t e e e
前
言
1 低 温低 成 本磷化
自磷 化 技术 实 现 工 业 应用 以来 , 们 一直 都 在 人
钢 铁 磷 化 技 术 就 是 金 属 通 过 与 稀 磷 酸 或 酸 性
t eq ai fp o p a ig fl , e m e wo l e t e d v lp n a s c rma i o u u e h u l y o h s h t i we d e d, ud b h e eo me tlap tp i rl f rf t r . t n m e y
- 1、下载文档前请自行甄别文档内容的完整性,平台不提供额外的编辑、内容补充、找答案等附加服务。
- 2、"仅部分预览"的文档,不可在线预览部分如存在完整性等问题,可反馈申请退款(可完整预览的文档不适用该条件!)。
- 3、如文档侵犯您的权益,请联系客服反馈,我们会尽快为您处理(人工客服工作时间:9:00-18:30)。
金属磷化技术的回顾与展望武汉材料保护研究所(430030) 李新立 李安忠 万 军[摘 要] 论述了各种磷化技术的现状、工业用途、常用磷化体系的性能及其工艺流程和具体要求,对磷化的发展前沿(提高质量,降低污染和节省能源)进行了展望。
[关键词] 磷化; 回顾; 展望[中图分类号] T G 174.4; T G 170 [文献标识码] A [文章编号] 1001-1560(2000)01-0071-03 [收稿日期] 1999-12-011 前 言金属在含有磷酸盐的溶液中进行处理,在其表面形成的磷酸盐化学转化膜,称之为磷化膜。
100多年来,磷化技术广泛应用于汽车、军工、电器、机械等领域,其主要用途是防锈、耐磨减摩、润滑、涂漆底层等(见图1)。
防锈作用——钢铁磷化后其表面覆盖一层磷化膜,起防止钢铁生锈的作用,主要用于工序间和库存等室内的防锈,防锈期较短,一般不用于户外。
耐磨减摩、润滑作用——磷化膜的特殊晶粒结构和硬度用于齿轮、压缩机、活塞环等运动承载件,起耐磨减摩作用。
磷化膜具有的润滑功能,在拉丝、拉管、深冲、冷墩等加工行业中用途较广泛,其主要作用是提高拉丝拉管速度,减少模具损伤。
涂漆底层——此是磷化的最大用途所在,约占磷化总工业用途的60%~70%。
磷化膜作为涂漆前的底层,能提高漆膜附着力和整个涂层体系的耐腐蚀能力。
磷化处理得当,可使漆膜附着力提高2~3倍,整体耐腐蚀性提高1~2倍。
在世界范围内,金属表面装饰与保护约有2 3是通过表面涂装实现的,涂装前一般都要进行磷化处理。
2 磷化技术的应用2.1 工艺流程2.1.1 预处理预处理的目的是除掉金属表面的油脂、油污、锈蚀物、氧化皮、机械杂质等,为磷化提供洁净的表面。
预处理包括机械法和化学法两种,用得最多的是化学法。
两种方法工序如下:(1)机械法:喷砂、抛丸除油、除锈、除氧化皮(2)化学法除油、脱脂有机溶剂清洗碱性清洗剂清洗酸性清洗剂清洗除锈、除氧化皮盐酸常温除锈硫酸中温除锈磷酸除锈有机酸除锈表面调整草酸表面调整胶体钛表面调整2.1.2 磷化处理生产中常采用各种磷化处理技术满足不同的要求。
依据化学溶液中参与成膜的金属离子同异,分为不同体系的磷化,常用的有锌系、锌钙系、锌锰系、锰系、铁系、非晶相轻铁系类,其一般性能及磷化膜微观结构见表1、图2、图3。
表1 常用磷化体系的一般性能磷化体系槽液主要组成磷化膜主要成分磷化膜形貌主要用途锌系Zn 2+,H 2PO 3-,NO 3-,H 3PO 4,促进剂Zn 3(PO 4)・4H 2O ,Zn 2Fe (PO 4)2・4H 2O 树枝状,针状,片状,孔隙较多漆前打底、防锈和冷加工减摩润滑锌钙系Zn 2+,Ca 2+,NO 3-H 2PO 4-,H 3PO 4,促进剂Zn 2Ca (PO 4)2・4H 2OZn 2Fe (PO 4)2・4H 2OZn 3(PO 4)2・4H 2O 呈紧密颗粒状,柱状,孔隙较少涂装前打底及防锈锌锰系Zn 2+,M n 2+,NO 3-H 2PO 4-,H 3PO 4,促进剂Zn 2Fe (PO 4)2・4H 2O ・Zn 3(PO 4)2・4H 2O ,(M n ,Fe )5H 2(PO 4)4・4H 2O 颗粒2针状2块状混合晶型漆前打底、防锈及冷加工减摩润滑锰系M n 2+,NO 3-,H 2PO 4-,H 3PO 4(M n ,Fe )5H 2・(PO 4)4・4H 2O 晶粒呈密集颗块片状防锈、减摩铁系Fe 2+,H 2PO 4,H 3PO 4Fe 5H 2(PO )4・4H 2O 晶粒呈密集颗粒状 防锈非晶相铁系N a +(N H 4+),H 2PO 4-,H 3PO 4,M oO 4-Fe 3(PO 4)2・8H 2O Fe 2O 3 非晶相平面结构漆前打底2.1.3 后处理后处理是磷化后所做的进一步处理,与用磷化防锈、减摩、润172000年1月 材 料 保 护 第33卷 第1期 滑、涂漆底层相对应的后处理是:涂油涂脂增强防锈性能;硼砂或皂化处理,进一步增加润滑降低加工摩擦力;涂漆形成长期的防腐蚀、防护、装饰性表面涂层体系。
(a )锰系(膜重:16g m 2)(a )常规锌系(膜重:2.8g m 2)(b )锌系(膜重:22g m 2)(b )锌钙系(膜重:3.5g m 2)(c )锌钙系(膜重:8.6g m 2)图2 重型磷化(防锈、润滑、减摩)的SE M 图谱 500×(c )锌(锰镍)系(膜重:2.6g m 2)图3 薄型磷化(涂装打底)的SE M 图谱 500×防锈磷化的后处理非常重要,因为靠磷化膜本身防锈能力是非常有限的,而且盐雾试验只能到几小时。
一般要进行涂油涂漆,最好是涂防锈油,经过涂油涂脂等后处理,防锈能力甚至可提高几十倍。
冷加工润滑型磷化必须进行皂化后处理,以提高磷化膜的润滑性。
皂化可采用工业肥皂粉、硬脂酸钠。
耐磨减摩磷化是否要后处理不太重要,因为常规的浸油处理也可提高其耐磨和防锈性能,故并不严格要求涂防锈油。
涂装打底磷化的后处理一般用铬酸盐封闭处理,以使整体的防腐蚀性提高10%左右。
由于环保问题,很多国家都取消了后处理,特别是铬酸盐后处理。
现在已有无铬后处理封闭技术,据说可达到铬酸盐效果,但工业应用十分有限。
2.2 工业用途2.2.1 防锈磷化技术1906年就用于防锈,目前仍在广泛应用。
防锈磷化大部分为重型磷化,膜重为5~30g m 2。
早期防锈磷化主要是无促进剂型铁系磷化,现在常用中温锌系、锰系、锌锰系磷化,以NO 3-作主体促进剂,磷化温度70℃左右,磷化时间5~20m in 。
2.2.2 耐磨减摩,冷加工润滑承载运动件,如齿轮、轴承套、活塞环等在承载运动过程中,将会产生摩擦发热振动,其上覆盖一层磷化膜后,提供的润滑性、抗热性、吸震性都能使运动件的摩擦性能大为改观,因而这项技术一直在广泛使用。
通常,只有锰系磷化才具备上述性能。
在冷加工成形过程中,金属与金属间将产生相对摩擦运动,如果没有一层润滑层阻隔,冷加工是难以完成的。
结晶型磷化膜覆盖在金属表面,提供润滑隔层,使得冷加工过程中摩擦力减少,模具使用寿命提高。
这一技术自1934年至今仍在广泛使用。
润滑型磷化主要是锌系和锌钙系磷化,而锰系磷化几乎不用,这是因为锌系磷化在皂化时与硬脂酸钠反应形成润滑性非常好的硬脂酸锌,以NO 3-,NO 3- NO 2-为促进体系,磷化温度70℃左右,磷化时间5~15m in 。
2.2.3 涂漆打底磷化的最大应用领域在于涂漆打底,因而对磷化的研究也主要集中在此。
涂漆前打底用的磷化一般是薄型磷化,要求磷化膜细致、密实,膜重不超过4.5g m 2。
磷化体系包括锌系、锌锰镍系、锌钙系、非晶相轻铁系等,磷化温度30~70℃(也有极少数不加温),时间1~10m in 。
目前工业领域磷化技术的应用情况见表2。
表2 目前工业领域磷化技术的应用情况用途常用磷化体系膜重范围(g m 2)后处理工序耐盐雾性能(h )室内防锈期及应用范例 工序间防锈锌系、锌钙系5~10无或钝化0.5~3.0月库存防锈锌系、锌锰系10~20钝化或浸油8~24 3~12月长效防锈锌系、锌锰系10~30浸防锈油、涂脂48~120 1~2年拉丝拉管锌系、锌钙系5~15硼砂或皂化处理 冷加工深冲锌系、锌钙系1~15皂化处理 冷加工挤压 锌系10~30皂化处理精密配合 承载 锰系1~3 浸油 活塞环压缩机等 大配合承载 锰系5~30 浸油 齿轮离合器片等阳极电泳 锌系非晶轻铁系0.5~3.0 无 80~400自行车农机车等阴极电泳 锌系锌锰镍系2.0~3.5无或铬钝化720~1200 汽车等静电喷漆锌系、锌钙1.0~3.5 无 零部件仪表等粉末涂装锌系、非晶 轻铁系0.5~3.0 无 >500电器办公具等空气喷漆锌系、锌钙系2.0~4.5 无 零部件电柜等2.2.4 其他有色金属磷化锌及其合金的表面处理主要是铬钝和磷化,主要作用是涂装打底,增强漆膜附着力。
锌及其合金于表面处理不宜用强酸强碱处理,否则极易产生过腐蚀。
锌金属比铁活泼,即使在低温下磷化速度也很快,往往易形成磷化膜晶粒粗大现象,因此磷化处理要防止锌及其合金磷化时的粗化现象。
对热镀锌材料磷化比较难,漆膜附着也不易控制,要特别考虑。
铝及其合金的磷化处理与钢铁件基本相同,形成晶粒型磷化膜,用于铝材冷加工和涂装打底。
铝及其合金磷化技术主要是防止A l 3+进入处理液中,因为A l 3+会使磷化液“中毒”,完全不能27 Jan 2000 M ATER I AL S PROTECT I ON V o l .33 N o .1形成磷化膜。
因此,在常规钢铁磷化槽液中应加入大量氟化合物,络合A l3+并形成沉淀除去。
3 展 望磷化技术领域的研究方向主要是围绕提高质量、减少环境污染、节省能源进行。
首先考虑的应是提高质量,同样减少环境污染也非常重要。
磷化处理中产生化学物质污染,只能通过随后的治理来实现。
磷化技术及领域研究发展的三大内容如下:(1)提高质量中温致密型磷化技术提高防锈能力锌锰镍三元系磷化阴极电泳配套性圆柱形密集晶粒磷化技术高耐碱性磷化技术提高漆膜附着力镀锌板磷化技术(2)降低污染预处理、后处理技术无磷清洗剂生物降解表面活性剂无残酸腐蚀除锈技术无铬磷化封闭技术磷化技术无毒促进剂技术无镍无锌磷化技术(3)节省能源重型磷化技术(95→60℃)薄型磷化技术(50→30℃)脱脂技术(60→30℃)3.1 提高质量高温(>95℃)重型磷化的防锈性能非常好,应用非常广泛,已有几十年,现场硫酸铜点滴可达5m in以上。
中温(60℃,5~8 m in)磷化,目前一般达到2~3m in点滴,要达到5m in点滴还有相当一段差距。
对涂装打底的磷化而言,提高磷化与涂装层的整体防腐蚀性仍是磷化研究的主要方向。
锌锰镍三元体系磷化已在较大范围内应用,但在表面耐碱性、提高阴极电泳漆或其他漆种的整体防腐蚀性方面还有发展前景,从提高质量方向考虑,含镍磷化仍是一种有效的途径。
镀锌板在汽车及其他行业的应用越来越多,其防腐蚀性能可以得到显著提高,但漆层的附着力保持性比不上钢板,在腐蚀介质或大气中暴露一段时间后会下降。
因此,解决镀锌板磷化漆膜的“湿”附着力的研究是当今十分迫切的问题。
3.2 降低污染磷化处理产生的污染源主要是重金属、磷酸盐、表面活性剂、有毒物质等。
脱脂处理中磷酸盐排放水的“肥化”生物耗氧问题、表面活性剂的化学耗氧问题等,都是严重的污染。
现在已研究出无磷脱脂剂,正在研究应用中的生物可降解表面活性剂技术,但成本高,应用还有一定的阻力。
因此,脱脂技术的发展是研究低污染、低成本的清洗技术,应用将日益广泛。
无残酸腐蚀除锈技术、无铬磷化封闭技术都是生产中还没有完全解决的问题。