Metal-Organic Frameworks in Monolithic Structures
金属有机

Chemical Engineering Journal 171 (2011) 517–525Contents lists available at ScienceDirectChemical EngineeringJournalj o u r n a l h o m e p a g e :w w w.e l s e v i e r.c o m /l o c a t e /c ejSynthesis,characterization and hydrogen adsorption on metal-organic frameworks Al,Cr,Fe and Ga-BTBDipendu Saha ∗,Renju Zacharia,Lyubov Lafi,Daniel Cossement,Richard ChahineInstitut de recherche sur l’hydrogène,Universitédu Québec àTrois-Rivières,Trois-Rivières,QC G9A 5H7,Canadaa r t i c l ei n f oArticle history:Received 21February 2011Received in revised form 7April 2011Accepted 8April 2011Keywords:Metal-organic framework (MOF)BTB ligand Pore textureSpecific surface area Hydrogen adsorptiona b s t r a c tBenzenetribenzoate (BTB)ligand is combined with four trivalent metals,Al,Cr,Fe and Ga by solvothermal synthesis to form four different metal-organic frameworks (MOFs),abbreviated as M-BTB,where M stands for the metal.Each of the MOFs is characterized with pore texture,scanning electron microscopic images (SEM),X-ray diffraction (XRD),Fourier transform infra-red spectroscopy (FT-IR)and thermogravimetric analysis (TGA).Pore texture reveals the highest BET surface area belongs to Al-BTB (1045m 2/g)and decreases in the order of Cr >Fe >Ga.Hydrogen adsorption at 77K and up to ambient pressure indicates that Al-BTB adsorbs highest amount of H 2(0.98wt.%)and decreases in the same order as the specific surface areas.High pressure H 2adsorption at room temperature (298K)and pressure up to 80bar reveals that Fe-BTB adsorbs highest amount of hydrogen (0.51wt.%or 2.75g L −1,absolute)and the adsorption amount decreases in the order of Cr >Al >Ga.© 2011 Elsevier B.V. All rights reserved.1.IntroductionMetal-organic frameworks (MOFs)are highly promising adsor-bents because of their very high specific surface area,tunable pore size and case-specific tailoring of basic molecular architec-ture leading to the large and selective adsorption capacities of several gas molecules.A large volume of MOFs has been reported in the literature;most of them were synthesized and decorated accordingly with an aim towards gas storage [1–3],separation [4],heterogeneous catalysis [5],drug delivery [6]or molecular sens-ing [7].Topologically,all the MOFs consist of metal centers,more precisely known as secondary building units (SBUs)connected with each other by the organic molecules,commonly known as organic linkers [8].Different types of metals have been employed and examined for the structure forming capacity of MOFs;typical examples are zinc [9–15,28],copper [16,17],chromium [18–20],aluminum [21,22],iron [23,24],scandium [25],manganese [26],zirconium [27],vanadium [29]or cadmium [42].Organic linker is probably the far most important part in tai-loring the architecture of metal-organic frameworks.The linker molecule plays the role to tune the pore size and specific sur-face area of the MOFs.Most versatile usages of different organic molecules as linkers were noticed in synthesizing different species of IRMOFs where zinc was employed as part of secondary build-ing units [8,28].Benzenedicarboxylic acid (BDC)or terephthalic∗Corresponding author.Tel.:+18652422221;fax:+18655768424.E-mail address:dipendus@ (D.Saha).acid is most common in synthesizing different species of MOFs,including MOF-5[9,13,28],MIL-53(Cr,Al or Fe)[19,29]or MIL-101[20,30,31].However,the reported large surface area and the maxi-mum gas (H 2and CO 2)uptake is observed for benzenetribenzoic acid (BTB)as organic linker that formed metal-organic frame-work,MOF-177with zinc as SBU former [10–12,14,15,33–35].Besides hydrogen and carbon dioxide,methane [36],nitrous oxide [36]and carbon monoxide [37]adsorption was also exam-ined on MOF-177.In recent time,Furukawa et al.incorporated few other ligands,like 4,4 ,4 -(benzene-1,3,5-triyl-tris(ethyne-2,1-diyl))tribenzoate (BTE),4,4 ,4 -(benzene-1,3,5-triyl-tris(benzene-4,1-diyl))tribenzoate (BBC)or biphenyl-4,4 -dicarboxylate (BPDC)that demonstrated even larger surface area than BTB containing ligands [38].Apart from the usage of pure or only one type of ligand,employing more than one ligand to form a single MOF was reported recently.Koh et al.[39]combined BDC and BTB lig-ands in different proportions to form different species of MOFs and it was reported that between the ratio of 6:4and 5:5of BDC over BTB,a new type of mesoporous MOF was generated and has been named as UMCM-1.Saha and Deng [40]also gen-erated two types of hybrid MOFs consisting of BDC and BTB by employing two different solvents,DMF (N,N,dimethylformaide)and DEF (N,N,diethylformaide).In other work,Koh et al.[41],syn-thesized the hybrid MOF (UMCM-2)with the combination of BTB and thieno[3,2-b]thiophene-2,5-dicarboxylate (T 2DC)in 1:1ratio,that possesses the BET surface area of more than 5000m 2/g.Klein et al.[43]synthesized the hybrid mesoporous MOF DUT-6with BTB and NDC (2,6-naphthalenedicarboxylate)in 3:2mole ratio that possesses high pore volume of 2.02cm 3/g.Despite the ubiquitous1385-8947/$–see front matter © 2011 Elsevier B.V. All rights reserved.doi:10.1016/j.cej.2011.04.019518 D.Saha et al./Chemical Engineering Journal 171 (2011) 517–525Table 1Synthesis conditions of the metal-organic frameworks.MOF identityMetal saltsSalts amount (g)BTB amount (g)Thermal conditionsAl-BTB Al(NO 3)3·9H 2O 0.1710.290◦C,24h Cr-BTB Cr(NO 3)3·9H 2O 0.1820.290◦C,24h Fe-BTB Fe(NO 3)3·9H 2O 0.2700.280◦C,3days Ga-BTBGa(NO 3)3·x H 2O0.2550.2100◦C,24hevidence that BTB ligand could provide high surface area and gas adsorption properties,it was not employed to form MOFs with any other metal,till today.In this work,we combined BTB ligand with four differ-ent trivalent metals,aluminium,chromium,iron and gallium to form four types of metal-organic frameworks.Each type of MOF was performed materials characterization with pore tex-ture,density measurement,scanning electron microscopy (SEM),Fourier-transform infra-red (FT-IR)spectra,thermogravimetric analysis (TGA)and X-ray diffraction to reveal the identity of the crystals.Hydrogen adsorption measurement was performed at 77K and room temperature to examine the hydrogen sorption capacity of those MOFs.2.Experimental methods2.1.Synthesis of Al,Cr,Fe and Ga-BTBAll metal-organic frameworks of this present work were syn-thesized by solvothermal technique.In general,the corresponding metal salts or the metal precursors were dissolved in 25mL ethanol,where as the BTB ligand was dissolved in 10mL N,N-dimethylformamide (DMF)followed by mixing the two solutions and subjecting to thermal treatment.For Ga-BTB,both the pre-cursor and the ligand were dissolved in 35mL of DMF as the Ga precursor was sparingly soluble in ethanol.The exact identity of metal precursor,amounts of reagents and the thermal conditions are revealed in details in Table 1.After the thermal treatment,the crystals were separated from the solution and washed twice with DMF in order to remove any unreacted reagent.Finally,the DMF treated samples were washed several times with chloroform min-imize the DMF level within the crystals and stored inside glovebox under argon atmosphere in closed container.2.2.Materials characterizationsThe materials characterizations techniques employed for each sample include pore textural properties,density measurement,Fourier-transform infra-red spectroscopy (FT-IR),thermo gravi-metric analysis (TGA),scanning electron microscopy (SEM)and X-ray diffraction technique.The pore textural properties were calculated by nitrogen adsorption–desorption study at liquid nitrogen temperature (77K)and pressure up to 1bar in Micromeritics ASAP 2020instrument.The pore textural properties BET surface area and pore size distribu-tion by density functional theory (DFT)were obtained by analyzing the nitrogen adsorption and desorption isotherms with the built-in software in the ASAP 2020surface area and porosity analyzer.The adsorbent samples were degassed ex-situ at 373K for 24h toa bcd10.80.60.40.20Relative pressure (P/Po)N i t r o g e n a d s o r b e d (m m o l /g )10.80.60.40.20Relative pressure (P/Po)N i t r o g e n a d s o r b e d (m m o l /g )10.80.60.40.20Relative pressure (P/Po)N i t r o g e n a d s o r b e d (m m o l /g )10.80.60.40.2Relative pressure (P/Po)N i t r o g e n a d s o r b e d (m m o l /g )Fig.1.N 2adsorption–desorption plot of Al-BTB (a),Cr-BTB (b),Fe-BTB (c),Ga-BTB (d).D.Saha et al./Chemical Engineering Journal171 (2011) 517–525519remove the guest molecules from the samples before the nitrogen adsorption measurements.The FT-IR spectra of the samples were measured in Thermo-Scientific Nicolet iN10-MX FT-IR chemical imaging microscope within the wave numbers of4000–800cm−1.The sample prepa-rations include grinding and mixing with KBr followed by pelletization before introducing to the laser.Scanning electron microscopy images(SEM)images were recorded by employing JEOL JSM-5500instrument by using an accelerating voltage of18kV.The thermogravimetric analysis(TGA)was performed in Perkin Elmer TGA7Instrument.The temperature ramp rate employed for this study was10◦C/min up to800◦C in an inert gas(Ar)flow.The X-ray data were recorded in Bruker D8Advance X-ray diffractometer with Cu K␣emission( =1.54056˚A).For each sample,the XRD scan was performed from2◦to75◦with0.02◦width and1s count time.Pro-cessing of all diffraction data including structure refinement was performed using JADE8+software supplied by Materials Data Inc. (Livermore,CA,USA).2.3.Hydrogen adsorption measurementHydrogen adsorption at low(up to1bar)pressure and at77K was measured volumetrically in ASAP2020instrument.About 50mg of each of the sample was used in this experiment.The adsor-bent sample was degassed under a vacuum and at373K for24h before the hydrogen adsorption measurement.Ultra-high purity hydrogen(Praxair Inc.)was introduced into a separate gas port of the adsorption unit for the hydrogen adsorption measurements.The high pressure hydrogen adsorption was measured in Sieverts-type volumetric apparatus,built and calibrated in our laboratory.About100mg of sample was introduced within the sample container and it was subjected to room temperature out-gassing at10−3Torr by employing a turbomolecular pump before any measurement.The skeleton density of the samples were mea-sured by admitting ultra-high purity helium gas(Praxair Inc.) in to the system and performing the density measurement at ambient temperature and equilibrium pressure less than20bar in order to minimize the effect of helium adsorption.The tem-perature and pressure of the gas were monitored by employing calibrated Guildline9540digital platinum resistance temperature detector(accuracy=±0.01◦C)and Paroscientific740digiquartz high accuracy digital pressure gauge(accuracy=0.01%at f.s.).The real gas densities were obtained from the NIST-12standard ref-erence database.The sample skeleton densities were calculated from the linear regression of sample mass versus gas density plots. Hydrogen adsorption isotherms were measured by using ultra-high purity hydrogen gas(Praxair Inc.).The excess gas adsorption was measured at room temperature(298K)and pressure up to80bar. To estimate the order of uncertainties that might arise from our adsorption measurement,we performed a skeleton density and hydrogen adsorption measurement of similar masses of activated carbon AX-21,whose adsorption characteristics are well-known. The maximum uncertainty of our experiments was found to be not more than±3%.The measured leak rate on this system is practically negligible:10−6MPa/s with He gas at4MPa and room temperature. Leak measured using Mathewson Leak hunter plus8066yielded no leak with hydrogen gas at5MPa and room temperature(minimum detectable leak of the instrument is8.1×10−6mL s−1of hydrogen).3.Results and discussions3.1.Materials characterizations3.1.1.Pore texture and densityThe pore texture properties including BET specific surface area and pore size distribution were calculated from nitrogen Table2Pore texture properties.MOF identity BET SSA(m2g−1)Bulk density, b(g cm−3)Skeleton density,s(g cm−3)Al-BTB10450.30 1.72Cr-BTB5520.54 1.96Fe-BTB3620.33 1.17Ga-BTB620.29 2.865adsorption–desorption plot by employing the built-in software of Micromeritics ASAP2020porosity and surface area analyzer(shown in Fig.1(a)–(d)).The bulk density was measured in ASTM standard D2854-96where as the skeleton density was measured by helium expansion experiment at ambient temperature.The pore texture and density values of all the samples are shown in details in Table2. It is observed that the highest BET SSA(1045m2g−1)were achieved for aluminum(Al)sample.The surface areas decrease in the order of Cr>Fe>Ga.The pore size distribution calculated by density func-tional theory(DFT)for all the samples are shown in Fig.2(a)and (b)for differential and cumulative pore volume,respectively.It is observed almost all the MOFs possess very narrow distribution in the microporous region,though majority of the pore volumes con-tribute in the mesopore region.Al-BTB possesses two peaks,8.58˚A and11.79˚A though the large pore volume arises from pores in the region of120˚A.Cr-BTB shows the presence of pores in8.58˚A and 12.69˚A but also shares large pore volume in less than100˚A.Fe-BTB is having very low pore volume in microporous region of8˚A and 12.69˚A but having very large pore volume in the range of160˚A. Amongst all the MOFs,Ga-BTB shows the lowest available pore volume,narrow micropore in12.69˚A,but larger pore volume in <200˚A.It is also clear that these MOFs posses the micropore width in the range of8–12˚A along with large mesopores which may arise due to possible crystalline defects.The total pore volume is highestabPore width (Å)Differentialporevolume(cc/g-Å)Pore width (Å)Cumulativeporevolume(cc/g)Fig.2.(a)Differential pore size distribution by DFT theory.(b)Cumulative pore size distribution by DFT theory.520 D.Saha et al./Chemical Engineering Journal 171 (2011) 517–525Fig.3.Scanning electron images,Al-BTB (a),Cr-BTB (b),Fe-BTB (c)and Ga-BTB (d).for Al-BTB followed by Cr-BTB,Fe-BTB and Ga-BTB as observed in Fig.2(b).It is noticeable that the specific surface areas of all the samples are lower than MOF-177[11,12]or other BTB contain-ing hybrid MOFs [39,41,43].Most probably,the presence of two or more interwoven three-dimensional nets within MOF structures lowered their porosity as observed in the case of PCN-6[44]or MOF-14[Cu 3(BTB)2][45].However,the specific surface areas of Al-BTB is higher than several other mesoporous MOFs reported till today,like JUC-48[42].The Cr-BTB sample attained the largest bulk density of 0.54g cm −3.For all the remaining samples,the bulk density lies in the close region of 0.29(Ga)to 0.33g cm −3(Fe).The skeleton den-sity was observed to be highest for Ga sample (2.86g cm −3).Lower values of skeleton were densities achieved for Al (1.72g cm −3),Fe (1.17g cm −3)and Cr (1.96g cm −3)based samples.3.1.2.Scanning electron microscopy (SEM)The scanning electron microscopic (SEM)images for Al,Fe,Cr and Ga samples are shown in Fig.3(a)–(d),respectively.All the images were taken after outgassing the MOFs at elevated tem-perature.The morphology of the crystallites is not quite well distinguishable for all samples,most probably because of the lower magnification power of our SEM microscope.For Ga sample,the crystallites look quite close to the hexagonal profile with size range from 0.5m in the face to 0.13m in width.The crystallites of Fe sample resemble cubic or orthogonal nature with average size 0.33m.The exact morphology of Al and Cr samples was not possi-ble to determine with the present SEM image,however,the average size of the crystals could be approximated as 0.1–0.15m for Cr and 0.07–0.13m for Al samples.3.1.3.X-ray diffractionThe X-ray diffraction patterns of the four samples are shown in Fig.4.It is observed that the sharpest peak of all the MOFsisAngle(2θo)I n t e n s i t y (c o u n t s )Fig.4.X-ray diffraction patterns.D.Saha et al./Chemical Engineering Journal 171 (2011) 517–525521I n t e n s i t y (a .u .)located at around 6◦followed by a shorter peak at an angle of 11◦.There are also some broad peaks located at higher angles of all the samples.Al and Cr-BTB possess the broad peak at an angle 19–20◦,where as Ga sample shows two small but broad peaks at 35◦and 64◦.Al-BTB possesses a broad peak at an angle of 44◦and a small peak at the shorter angle of 3.4◦.For Fe-BTB,two broader peak formations are also located at 33◦–34◦and 44◦–45◦.Unlike MOF-177or UMCM-1,none of our samples shows the largest peak at 4◦–5◦(MOF-177[12])or 2◦–3◦(UMCM-1[39]),however,all the samples possess the largest peak at 6◦–7◦,similar to that of UMCM-2[41].It is also noticeable that almost all of the peaks of each of the pattern are quite broad in nature accompanied by quite heavy noise and low intensity.Most probably,very thin layer of chloro-form was still present in the inter-lattice spaces of crystals that prohibited the penetration of X-ray within it as described by Saha and Deng [32].The wide pore opening of the mesoporous mate-rials may also caused the partial collapse of the crystalline lattice after the removal guest species during the outgassing phase at ele-vated temperature,as suggested by Koh et al.[39]or observed in the XRD pattern of the mesoporous MOF composed of Al III with one or bidentate ligand comprising of six membered aro-matic rings [46].Due to the poor peak profile and possible lack in accuracy in the overall pattern,we did not attempt to index the peaks and hence did not report the crystal phase identification data.3.1.4.FT-IR spectraThe FT-IR spectra of the four metal-organic frameworks are pro-vided in Fig.5.The overall patterns are in quite well agreement with other BTB containing MOFs,reported elsewhere [14,47].The sharp peak at 1400cm −1region is attributed to the symmetric stretching of C O bond that belongs to the carboxylate group of the BTB ligand,where as the peak at 1600cm −1is originated from the asymmetric stretching of the same bond [47].The few weak peaks at 1300–1000cm −1can be attributed to the in-plane bend-ing vibrations of aromatic C–H bonds and the remaining smaller angle peaks (1000–800cm −1)could be contributed by the out of plane bending vibration of C–H bonds [14,47].The C C stretch-ing vibration from the benzene ring of the BTB ligand appears as a weak peak at 1520–1570cm −1.Few weak peaks starting after 1600cm −1till 2000cm −1are attributed to the first overtone of in-plane and out of plane vibrations of C–H bonds of BTB ligand,where as the second overtone appears at 2600–2100cm −1.Very broad and weak peak formation in the region of 3000cm −1is attributed to the aromatic C–H stretching of the BTB ligand [14].Finally,the absence of any strong peak at 1700cm −1provides the clear indi-0102030405060708090100ab0200400600800w t .%-8-7-6-5-4-3-2-100100200300400500600700800Tempe rature (o C)D i f f e r e n t i a l -w t .% (d w t .%/d t )Fig.6.Thermogravimetric analysis (TGA),linear form (a)and differential form (b).cation of absence of any free carboxylic acid in the MOF samples[14].3.1.5.Thermogravimetric analysis (TGA)The thermogravimetric plots in linear and differential form are shown in Fig.6(a)and (b).From the differential plot,the losses in weight can be localized in the three discrete regions of 50–100◦C,150–250◦C and 500–600◦C.Very minute loss is observed around in the first region of 50–100◦C (1–2wt.%)that can be contributed to the desorption of adsorbed gas from their pore spaces.In the sec-ond region,150–250◦C,the cause of mass loss is attributed to the removal of guest species,mostly N,N dimethylformamide (DMF).For Cr,Fe and Ga based samples,the loss is in this region is lim-ited to 6–7wt.%unlike Al species that suffered a significant loss of 19wt.%.This higher loss is a clear indication of larger occupancy of guests within the Al based MOF that could provide better pore texture if it were outgassed at elevated temperature and/or with elongated time period.The final region of loss at 500–600◦C can be attributed to the disintegration of framework,i.e.,the decomposi-tion of BTB ligand itself.From the differential plot,the loss can be quantified approximately as 31,15,49and 34wt.%for Al,Cr,Fe and Ga based MOFs,respectively.The final residue amount was within 30–45wt.%for all the samples that can be attributed to the oxides of the corresponding metals.The weight loss due to the decompo-sition BTB ligand is much smaller compared to the possible overall proportion of BTB in the MOF resulting in quite higher final residue than expected for a metal oxide.Most probably,there was a sig-nificant amount of carbon deposition,originated from the organic ligand,on the metal oxides as the TGA measurement was performed in an inert atmosphere.522D.Saha et al./Chemical Engineering Journal 171 (2011) 517–525Pressure (Torr)H 2 a d s o r b e d (w t .%)Fig.7.Low pressure hydrogen adsorption isotherms.4.Hydrogen adsorption properties4.1.Low pressure hydrogen adsorptionThe low pressure hydrogen adsorption for all the MOFs were measured at liquid nitrogen temperature (77K)and pressure up to 800Torr in ASAP 2020instrument.The hydrogen adsorption isotherms are shown in Fig.7.All the isotherms are typically type-I according to IUPAC classifications.The highest adsorption is exhib-ited by Al-MOF,around 0.98wt.%,followed by Cr (0.76wt.%),Fe(0.67wt.%)and Ga (0.36wt.%).It is observed that the hydrogen uptake at ambient pressure range was dictated by BET specific sur-face area as the hydrogen adsorption amount decreases exactly in the same as BET SSA (Al >Cr >Fe >Ga)as observed in Table 2.The lower hydrogen uptake of all of these samples compared to MOF-177or several other BTB containing MOFs can be attributed to the lower porosity of the materials that is probably caused by the interwoven 3D nets within the structures as described earlier.All the hydrogen adsorption isotherms were modeled by four well-known equations,Langmuir,Freundlich,Sips (Langmuir–Freundlich)and Toth models [12,13].The Langmuir isotherm can be written as:q =a m bP 1+bP(1)where q (wt.%)is the adsorbed hydrogen amount,p is the hydro-gen pressure (Torr),a m (wt.%)is the monolayer adsorption capacity and b (Torr −1)is the other Langmuir isotherm equation parameter.Both equation parameters can be determined from the slope and intercept of a linear Langmuir plot of (1/q )versus (1/p ).Freundlich isotherm is given by:q =kP 1/n(2)where k and n are the Freundlich isotherm equation parameters that can be determined by the slope and intercept of ln P versus ln q plot.The Sips (Langmuir–Freundlich)model can be written asq =a m bP (1/n )1+bP (1/n )(3)where a m ,b and n are equations constants.a cb dPressue (Torr)H 2 a d s o r b e d (w t %)00.10.20.30.40.50.60.70.8800700600500400300200100Pressure (Torr)H 2 a d s o r b e d (w t .%)00.10.20.30.40.50.60.70.8Pressure (Torr)H 2 a d s o r b e d (w t .%)Pressure (Torr)H 2 a d s o r b e d (w t .%)Fig.8.Isotherm model fitting,Al-BTB (a),Cr-BTB (b),Fe-BTB (c)and Ga-BTB (d).D.Saha et al./Chemical Engineering Journal 171 (2011) 517–525523Table 3Parameters of isotherm model fitting.Isotherm modelModelparameters Parametervalues (Al-BTB)Parameter values (Cr-BTB)Parameter values (Fe-BTB)Parameter values (Ga-BTB)ARE%(Al-BTB)ARE%(Cr-BTB)ARE%(Fe-BTB)ARE%(Ga-BTB)Langmuir modela m 1.1580.82510.7120.378 1.4561.631.5940.622b0.0060.0090.0100.016Freundlich modelk 0.0660.0840.0910.082 1.7010.8030.4870.367n2.4272.9833.2974.401Sips modela m 1.533 2.473 2.526 1.2880.2510.4140.2390.257b 0.0120.0260.0300.059n1.3322.3582.6723.483Toth model˛T 5.340 4.972 4.919 5.2680.8290.3270.1630.257k T 2.595 1.347 1.0250.463t0.2450.1810.1560.086The Toth model can be given byq =˛T p (k T +p t )(1/t )(4)where ˛T ,k T and t are Toth equation constants.All the equation parameters of Sips and Toth model can be calculated by non-liner regression techniques.The degree of model fitting was compared by the absolute relative error (ARE)percent,calculated asARE%=Nn =1|x exp −x mod |N×100%(5)where x exp is the experimental point,x mod is the modeling point and N is the number of points in the isotherm.These parameters are given in Table 3and model fitting plots are shown in Fig.8(a)–(d)for Al,Cr,Fe and Ga samples,respectively.ARE values confirmed that Sips model fit better for Al-BTB,however,Toth model fits best for the rest of MOFs.4.2.High pressure hydrogen adsorptionThe high pressure adsorption of four MOFs at room tempera-ture (298K)and pressure up to 80bar is shown in Fig.9(a)and (b)for gravimetric and volumetric capacities,respectively.The excess adsorption amount was directly obtained from the instru-ment shown as the symbols in the plots.Assuming the adsorbed the gas density is equivalent to the liquid density of the same species (hydrogen),the absolute adsorption amount can be calculated as [11,12]m abs =m excess1−( (T,P )/ (l ))(6)where (T ,P )is density of the adsorptive gas (hydrogen)at the particular temperature and pressure and (l )is the density of the same gas in the liquid phase.The absolute adsorption was repre-sented as continuous curve in the plots.It is clearly observed that the Fe-BTB performs highest hydrogen uptake both gravimetri-cally (abs:0.51wt.%,excess:0.465wt.%)and volumetrically (abs:2.75g L −1,excess:2.51g L −1).The hydrogen uptake amounts of the remaining samples lie in the similar range,however,minute observation reveals that the uptake capacity decreases in the order of Cr (0.42wt.%,1.38g L −1)>Al (0.25wt.%,0.85g L −1)>Ga (0.27wt.%,0.8g L −1),all absolute amount.It is also noticeable that the hydrogen adsorption increases linearly with pressure similar to that of many other types of MOFs,which are caused by the poor adsorbate–adsorbent interactions at the ambient temperature level.It is evident that the hydrogen adsorption amounts at elevated pressure and at ambient temperature were not controlled by the pore texture properties unlike the adsorption at ambient pressureabPressure (bar)H 2 a d s o r b e d (w t .%)Pressure (bar)H 2 a d s o r b e d (g L -1)Fig.9.High pressure hydrogen adsorption,gravimetric adsorption amount (a)andvolumetric uptake amount (b).and 77K temperature which are quite obvious due to the associ-ated mesoporosity of these MOFs.The significant higher adsorption by Fe-BTB over the rest of the MOFs is most probably caused by the possible open or unsaturated metal sites that could be created during the evacuation step by the elimination of one or more sol-vent molecules from the MOF cavities [48].The unsaturated metal sites can increase the electrostatic attraction between hydrogen and partial charges on metal-organic framework atoms thereby dominating the key adsorption mechanism.5.ConclusionIn this work,we synthesized four metal-organic frameworks by the incorporation of benzenetribenzoate (BTB)ligand with four。
一种高收率uio-66金属有机框架材料的制备方法及应用
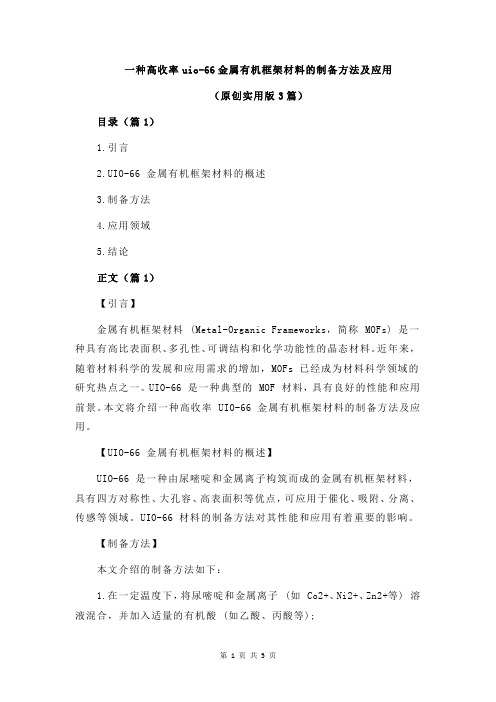
一种高收率uio-66金属有机框架材料的制备方法及应用(原创实用版3篇)目录(篇1)1.引言2.UIO-66 金属有机框架材料的概述3.制备方法4.应用领域5.结论正文(篇1)【引言】金属有机框架材料 (Metal-Organic Frameworks,简称 MOFs) 是一种具有高比表面积、多孔性、可调结构和化学功能性的晶态材料。
近年来,随着材料科学的发展和应用需求的增加,MOFs 已经成为材料科学领域的研究热点之一。
UIO-66 是一种典型的 MOF 材料,具有良好的性能和应用前景。
本文将介绍一种高收率 UIO-66 金属有机框架材料的制备方法及应用。
【UIO-66 金属有机框架材料的概述】UIO-66 是一种由尿嘧啶和金属离子构筑而成的金属有机框架材料,具有四方对称性、大孔容、高表面积等优点,可应用于催化、吸附、分离、传感等领域。
UIO-66 材料的制备方法对其性能和应用有着重要的影响。
【制备方法】本文介绍的制备方法如下:1.在一定温度下,将尿嘧啶和金属离子 (如 Co2+、Ni2+、Zn2+等) 溶液混合,并加入适量的有机酸 (如乙酸、丙酸等);2.搅拌一段时间后,沉淀出 UIO-66 晶体;3.将晶体分离、洗涤、干燥,得到高收率的 UIO-66 金属有机框架材料。
【应用领域】UIO-66 金属有机框架材料具有广泛的应用领域,包括但不限于以下几个方面:1.催化:UIO-66 材料具有可调结构和化学功能性,可作为催化剂或催化剂载体,应用于各种催化反应;2.吸附:UIO-66 材料具有良好的孔容和表面积,可作为吸附剂,应用于气体吸附、分离和储存等领域;3.分离:UIO-66 材料具有可调结构和化学功能性,可作为分离剂,应用于分离和提纯混合物;4.传感:UIO-66 材料具有良好的传感性能,可应用于各种传感器件的制备。
目录(篇2)一、引言二、UIO-66 金属有机框架材料的概述三、制备方法1.溶胶 - 凝胶法2.水热法3.微波法四、应用领域1.催化剂2.吸附剂3.电化学器件五、总结与展望正文(篇2)【引言】随着科技的发展,新型材料在各领域中的应用越来越广泛,UIO-66 金属有机框架材料(Metal-Organic Frameworks, MOFs)作为一种高收率的新型材料,在催化剂、吸附剂和电化学器件等领域具有广泛的应用前景。
阴离子金属有机框架
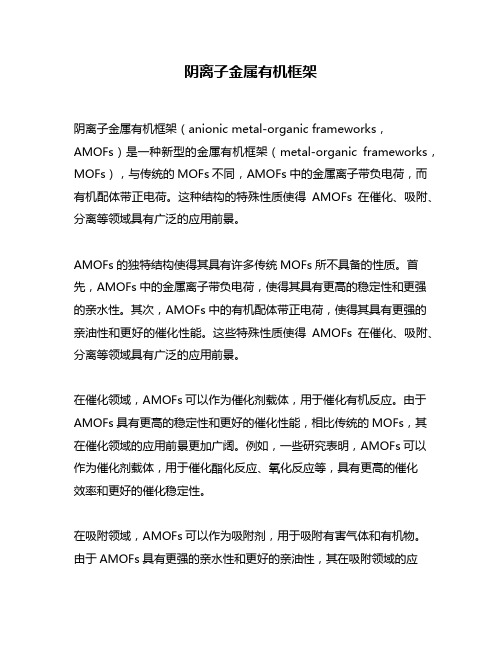
阴离子金属有机框架阴离子金属有机框架(anionic metal-organic frameworks,AMOFs)是一种新型的金属有机框架(metal-organic frameworks,MOFs),与传统的MOFs不同,AMOFs中的金属离子带负电荷,而有机配体带正电荷。
这种结构的特殊性质使得AMOFs在催化、吸附、分离等领域具有广泛的应用前景。
AMOFs的独特结构使得其具有许多传统MOFs所不具备的性质。
首先,AMOFs中的金属离子带负电荷,使得其具有更高的稳定性和更强的亲水性。
其次,AMOFs中的有机配体带正电荷,使得其具有更强的亲油性和更好的催化性能。
这些特殊性质使得AMOFs在催化、吸附、分离等领域具有广泛的应用前景。
在催化领域,AMOFs可以作为催化剂载体,用于催化有机反应。
由于AMOFs具有更高的稳定性和更好的催化性能,相比传统的MOFs,其在催化领域的应用前景更加广阔。
例如,一些研究表明,AMOFs可以作为催化剂载体,用于催化酯化反应、氧化反应等,具有更高的催化效率和更好的催化稳定性。
在吸附领域,AMOFs可以作为吸附剂,用于吸附有害气体和有机物。
由于AMOFs具有更强的亲水性和更好的亲油性,其在吸附领域的应用前景也更加广阔。
例如,一些研究表明,AMOFs可以用于吸附二氧化碳、甲醛等有害气体,具有更高的吸附效率和更好的吸附稳定性。
在分离领域,AMOFs可以作为分离剂,用于分离混合物中的有机物。
由于AMOFs具有更好的亲水性和亲油性,其在分离领域的应用前景也更加广阔。
例如,一些研究表明,AMOFs可以用于分离混合物中的芳香烃、酚类化合物等有机物,具有更高的分离效率和更好的分离稳定性。
总之,阴离子金属有机框架是一种新型的金属有机框架,具有更高的稳定性、更强的亲水性和亲油性,以及更好的催化、吸附、分离性能。
其在催化、吸附、分离等领域具有广泛的应用前景,是一种非常有前途的新型材料。
材料科学领域新突破金属有机框架结构
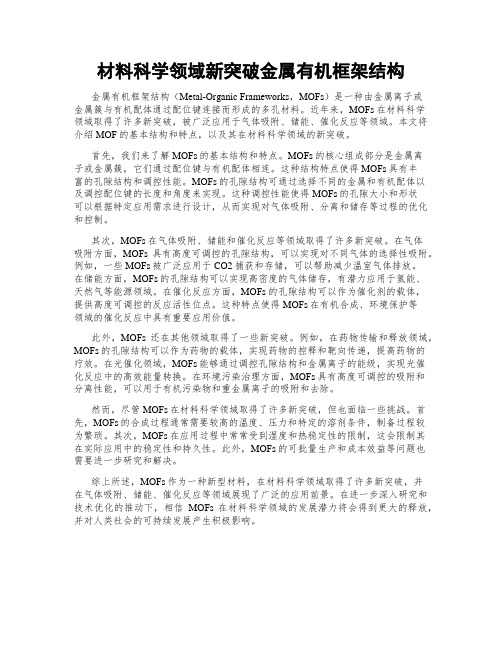
材料科学领域新突破金属有机框架结构金属有机框架结构(Metal-Organic Frameworks,MOFs)是一种由金属离子或金属簇与有机配体通过配位键连接而形成的多孔材料。
近年来,MOFs在材料科学领域取得了许多新突破,被广泛应用于气体吸附、储能、催化反应等领域。
本文将介绍MOF的基本结构和特点,以及其在材料科学领域的新突破。
首先,我们来了解MOFs的基本结构和特点。
MOFs的核心组成部分是金属离子或金属簇,它们通过配位键与有机配体相连。
这种结构特点使得MOFs具有丰富的孔隙结构和调控性能。
MOFs的孔隙结构可通过选择不同的金属和有机配体以及调控配位键的长度和角度来实现。
这种调控性能使得MOFs的孔隙大小和形状可以根据特定应用需求进行设计,从而实现对气体吸附、分离和储存等过程的优化和控制。
其次,MOFs在气体吸附、储能和催化反应等领域取得了许多新突破。
在气体吸附方面,MOFs具有高度可调控的孔隙结构,可以实现对不同气体的选择性吸附。
例如,一些MOFs被广泛应用于CO2捕获和存储,可以帮助减少温室气体排放。
在储能方面,MOFs的孔隙结构可以实现高密度的气体储存,有潜力应用于氢能、天然气等能源领域。
在催化反应方面,MOFs的孔隙结构可以作为催化剂的载体,提供高度可调控的反应活性位点。
这种特点使得MOFs在有机合成、环境保护等领域的催化反应中具有重要应用价值。
此外,MOFs还在其他领域取得了一些新突破。
例如,在药物传输和释放领域,MOFs的孔隙结构可以作为药物的载体,实现药物的控释和靶向传递,提高药物的疗效。
在光催化领域,MOFs能够通过调控孔隙结构和金属离子的能级,实现光催化反应中的高效能量转换。
在环境污染治理方面,MOFs具有高度可调控的吸附和分离性能,可以用于有机污染物和重金属离子的吸附和去除。
然而,尽管MOFs在材料科学领域取得了许多新突破,但也面临一些挑战。
首先,MOFs的合成过程通常需要较高的温度、压力和特定的溶剂条件,制备过程较为繁琐。
金属有机框架材料的设计与合成

金属有机框架材料的设计与合成金属有机框架材料(Metal-Organic Frameworks,简称MOFs)是一种由金属离子或金属簇与有机配体通过配位键连接而成的三维结构材料。
MOFs具有高度可调性和多样性,因此在吸附分离、催化反应、气体存储等领域具有广泛的应用前景。
本文将探讨金属有机框架材料的设计与合成方法。
首先,金属有机框架材料的设计是关键。
设计一个具有理想性能的MOF材料需要考虑多个因素。
首先是金属离子的选择,不同的金属离子具有不同的配位性质和催化活性。
例如,铜离子常用于气体吸附和催化反应,而锌离子则适用于气体存储。
其次是有机配体的选择,有机配体的结构和功能可以调控MOF的孔径大小、表面性质和化学反应活性。
因此,有机配体的合理设计对于构建高效的MOF材料至关重要。
此外,还需要考虑MOF的稳定性和可扩展性,以满足实际应用的需求。
其次,金属有机框架材料的合成方法也是研究的重点之一。
目前,MOF的合成方法主要包括溶剂热法、水热法、气相法等。
溶剂热法是一种常用的合成方法,通过在有机溶剂中加热反应混合物,使金属离子和有机配体发生配位反应,形成MOF晶体。
水热法则是将反应混合物置于高温高压的水中反应,利用水的溶解性和热力学性质来促进反应的进行。
气相法则是通过气相反应将金属离子和有机配体在高温下反应,形成MOF薄膜或纤维。
这些合成方法各有优劣,研究人员可以根据实际需求选择合适的方法。
此外,金属有机框架材料的表征技术也是研究的重要内容。
常用的表征方法包括X射线衍射、扫描电子显微镜、透射电子显微镜等。
X射线衍射可以用于确定MOF的晶体结构和孔隙结构,通过分析衍射图谱可以得到MOF的晶胞参数、晶体结构和孔隙大小等信息。
扫描电子显微镜和透射电子显微镜可以用于观察MOF的形貌和微观结构。
这些表征技术可以帮助研究人员了解MOF的结构性质,为进一步的应用研究提供基础。
最后,金属有机框架材料的应用前景广阔。
由于MOF具有高度可调性和多样性,可以通过调控金属离子和有机配体的选择和合成方法,设计出具有特定功能的MOF材料。
固态锂电池用MOF聚氧化乙烯复合聚合物电解质
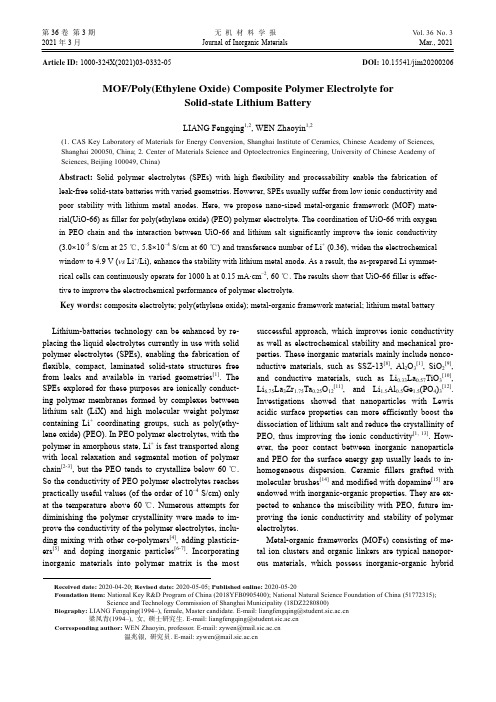
第36卷 第3期 无 机 材 料 学 报Vol. 36No. 32021年3月Journal of Inorganic Materials Mar., 2021Received date: 2020-04-20; Revised date: 2020-05-05; Published online: 2020-05-20Foundation item: National Key R&D Program of China (2018YFB0905400); National Natural Science Foundation of China (51772315);Science and Technology Commission of Shanghai Municipality (18DZ2280800)Biography: LIANGFengqing(1994–),female,Mastercandidate.E-mail:*************************梁凤青(1994–), 女, 硕士研究生.E-mail:*************************Corresponding author:WENZhaoyin,professor.E-mail:**************温兆银, 研究员.E-mail:**************Article ID: 1000-324X(2021)03-0332-05 DOI: 10.15541/jim20200206MOF/Poly(Ethylene Oxide) Composite Polymer Electrolyte for Solid-state Lithium BatteryLIANG Fengqing 1,2, WEN Zhaoyin 1,2(1. CAS Key Laboratory of Materials for Energy Conversion, Shanghai Institute of Ceramics, Chinese Academy of Sciences, Shanghai 200050, China; 2. Center of Materials Science and Optoelectronics Engineering, University of Chinese Academy of Sciences, Beijing 100049, China)Abstract: Solid polymer electrolytes (SPEs) with high flexibility and processability enable the fabrication ofleak-free solid-state batteries with varied geometries. However, SPEs usually suffer from low ionic conductivity and poor stability with lithium metal anodes. Here, we propose nano-sized metal-organic framework (MOF) mate-rial(UiO-66) as filler for poly(ethylene oxide) (PEO) polymer electrolyte. The coordination of UiO-66 with oxygen in PEO chain and the interaction between UiO-66 and lithium salt significantly improve the ionic conductivity (3.0×10–5 S/cm at 25 ℃, 5.8×10–4 S/cm at 60 ℃) and transference number of Li + (0.36), widen the electrochemical window to 4.9 V (vs Li +/Li), enhance the stability with lithium metal anode. As a result, the as-prepared Li symmet-rical cells can continuously operate for 1000 h at 0.15 mA·cm –2, 60 ℃. The results show that UiO-66 filler is effec-tive to improve the electrochemical performance of polymer electrolyte.Key words: composite electrolyte; poly(ethylene oxide); metal-organic framework material; lithium metal battery Lithium-batteries technology can be enhanced by re-placing the liquid electrolytes currently in use with solid polymer electrolytes (SPEs), enabling the fabrication of flexible, compact, laminated solid-state structures free from leaks and available in varied geometries [1]. The SPEs explored for these purposes are ionically conduct-ing polymer membranes formed by complexes between lithium salt (LiX) and high molecular weight polymer containing Li + coordinating groups, such as poly(ethy-lene oxide) (PEO). In PEO polymer electrolytes, with the polymer in amorphous state, Li + is fast transported along with local relaxation and segmental motion of polymer chain [2-3], but the PEO tends to crystallize below 60 ℃. So the conductivity of PEO polymer electrolytes reaches practically useful values (of the order of 10–4 S/cm) only at the temperature above 60 ℃. Numerous attempts for diminishing the polymer crystallinity were made to im-prove the conductivity of the polymer electrolytes, inclu-ding mixing with other co-polymers [4], adding plasticiz-ers [5] and doping inorganic particles [6-7]. Incorporating inorganic materials into polymer matrix is the mostsuccessful approach, which improves ionic conductivity as well as electrochemical stability and mechanical pro-perties. These inorganic materials mainly include nonco-nductive materials, such as SSZ-13[8], Al 2O 3[1], SiO 2[9], and conductive materials, such as Li 0.33La 0.57TiO 3[10], Li 6.75La 3Zr 1.75Ta 0.25O 12[11], and Li 1.5Al 0.5Ge 1.5(PO 4)3[12]. Investigations showed that nanoparticles with Lewis acidic surface properties can more efficiently boost the dissociation of lithium salt and reduce the crystallinity of PEO, thus improving the ionic conductivity [1, 13]. How-ever, the poor contact between inorganic nanoparticle and PEO for the surface energy gap usually leads to in-homogeneous dispersion. Ceramic fillers grafted with molecular brushes [14] and modified with dopamine [15] are endowed with inorganic-organic properties. They are ex-pected to enhance the miscibility with PEO, future im-proving the ionic conductivity and stability of polymer electrolytes.Metal-organic frameworks (MOFs) consisting of me-tal ion clusters and organic linkers are typical nanopor-ous materials, which possess inorganic-organic hybrid第3期 LIANGFengqing,et al: MOF/Poly(ethylene oxide) Composite Polymer Electrolyte for Solid-state Lithium Battery 333property and high specific surface area, thus being ideal fillers to polymer electrolytes. In 2013, Y uan, et al.[16] used Zn4O(1,4-benzenedicarboxylate)3 metal-organic frame-work(MOF-5) as filler for PEO electrolyte obtaining high ionic conductivity of 3.16×10–5 S·cm–1 (25 ℃) due to the uniformly dispersion. But the weak metal-organic coordination bonds of MOF-5 are easy to be attacked, leading to crystal transition or structure collapse and poor stability for lithium battery.In this work, nano-sized UiO-66, one of the extensive investigated MOFs, was introduced as filler into PEO electrolyte. The UiO-66 with outstanding hydrothermal and chemical stability does not contain transition metals which provide redox-active centers, so the electronic conduction can be avoided when contact with metallic Li.1 Experimental1.1 Synthesis of nano-sized UiO-66Nano-sized UiO-66 was synthesized according to the reported two-step synthesis[17]. (1) 207 mg ZrCl4 (98%, Aladdin) was dissolved in 40 mL N,N-dimethylformamide (DMF) (99.9%, Aladdin) under stirring, and the solution was heated to about 120 ℃for 2 h. Then 1 mL acetic acid was added and stirred for additional 0.5 h at 120 ℃.(2) 147 mg 1,4-benzenedicarboxylic acid (H2BDC) (99%, Aladdin) was added into the solution. And the resulting mixture was introduced into a 50 mL Teflon-lined stain-less-steel autoclave and placed in an oven at 120 ℃ for 24 h. After cooling to room temperature, the resulting precipitates were centrifuged, washed with DMF, puri-fied in methanol and then dried at 60 ℃ under vacuum for 24 h.1.2 Preparation of UiO-66/PEO composite polymer electrolytes (CPEs)PEO (M w = ~600,000, 99.9%, Aladdin) was dried at 50 ℃, and lithium bis(trifluoromethanesulfonyl)imide (LiTFSI) (99%, Aladdin) was dried at 100 ℃ for 24 h under vacuum and stored in an Ar-filled glove box. Firstly, LiTFSI was dissolved in anhydrous acetonitrile, and UiO-66 and PEO were added under magnetic stirring to afford homogeneous solution, in which the molar ratio of EO : Li+ was kept 16 : 1, and the content of nano-sized UiO-66 fillers was designed to be 0, 5%, 10%, 15%, 20%, 25%, naming the corresponding electrolytes as SPE, CPE-(5%, 10%, 15%, 20%, 25%). Afterwards, the solu-tion was cast on polytetrafluoroethylene template to vo-latilize the solvent at ambient temperature. Finally, the membranes were dried at 60 ℃for 12 h under vacuum to volatilize the residual solvent. 1.3 Sample characterizationThe crystalline structures of ingredients were col-lected from X-ray diffraction (XRD) with Cu-Kα radia-tion (λ=0.1542 nm) at room temperature (2θ=5°–50°) with the step of 0.1 (°)/s. The structure morphologies of UiO-66 and CPE were revealed by the scanning electron microscopy (SEM, Hitachi, S-3400N).1.4 Electrochemical measurement and cells assemblyThe ionic conductivity was measured at temperature from 25 to 80 ℃in symmetric cell with stainless steel (SS) electrodes by the AC impedance analysis (Autolab, Model PGSTAT302N) in the frequency range from 1 Hzto 1 MHz and at an amplitude of 50 mV. Linear sweep voltammetry (LSV) was employed to examine the elec-trochemical window in SS/electrolyte/Li cells, conduct-ing from 3 to 5.5 V at a scan rate of 10 mV/s. The trans-ference number of Li+ (t+) was tested in Li/electrolyte/Li cells and calculated according to t+ =00(Δ)(Δ)I V I RI V I R∞∞∞--, where ΔV is the applied DC polarization voltage (10 mV),I0 and I∞are the initial and steady current values during polarization, respectively. R0 and R∞are the resistance values before and after polarization, respectively. For inhibition ability of lithium dendrites growth test, a symmetric cell with solid electrolyte sandwiched be-tween two lithium metal electrode was assembled, and the test was carried out at 60 ℃。
金属有机框架物简介

金属-有机框架化合物简介金属-有机框架化合物(Metal-Organic Frameworks,MOFs)通常是指以有机配体为连接体(linkers)和以金属离子或簇为节点(nodes),通过配位键组装形成的具有周期性结构的配位化合物。
由于MOFs材料在荧光、催化、气体吸附与分离、质子导体、药物运输等方面具有潜在的应用价值,近十几年来,发展非常迅速,大量结构新颖的MOFs被不断的设计合成出来。
随着现代配位化学和晶体工程的发展,MOFs之间的键合作用已经不再仅局限于配位键作用,还囊括了其他作用力,比如:氢键作用,范德华力,芳香环之间的π-π作用等。
这些丰富的作用力使得MOFs结构和功能更加多元化、复杂化。
近几年来,计算机技术和仿真技术被应用到MOFs的研究中,在它们的帮助下,越来越多的新型MOFs材料不断的被合成出来。
与传统的多孔材料相比,MOFs材料的优势在于结构和功能的可设计性和调控性。
在理想情况下,通过合理设计配体和选择金属离子构筑的次级构建单元(SBUs),就可以合成目标结构和功能的MOFs。
虽然,目前每年有很多结构新颖性能特别的MOFs被合成报道,然而,在很多情况下,看似合理的设计,却很难实现。
这与MOFs的自主装过程有关。
在MOFs的合成过程中,除了配体和金属离子的影响外,还有其他的影响因素,比如:反应温度、溶剂、pH值、压力、配体和金属盐的比例与浓度等,每一个反应条件的改变,都有可能影响MOFs 的自主装过程,从而影响MOFs的结构,进而可能影响MOFs的性能。
总之,在通常情况下,根据金属离子构筑的SBUs和有机配体的几何构型可以预测MOFs最终的框架结构。
例如:平面方格结构可以通过4-连接平面构型SBU和直线型2-连接配体形成,如:MOF-118;类金刚石结构则可以通过四面体构型的4-连接SBU和直线型2-连接配体形成;立方结构框架则可以通过6-连接的SBU和直线型2-连接配体形成,如:MOF-5;T d八面体结构可以通过3-连接配体和轮桨状的4-连接SBU构筑,如:HKUST-1 (Figure1.1)。
金属有机框架ZIFs的应用研究进展
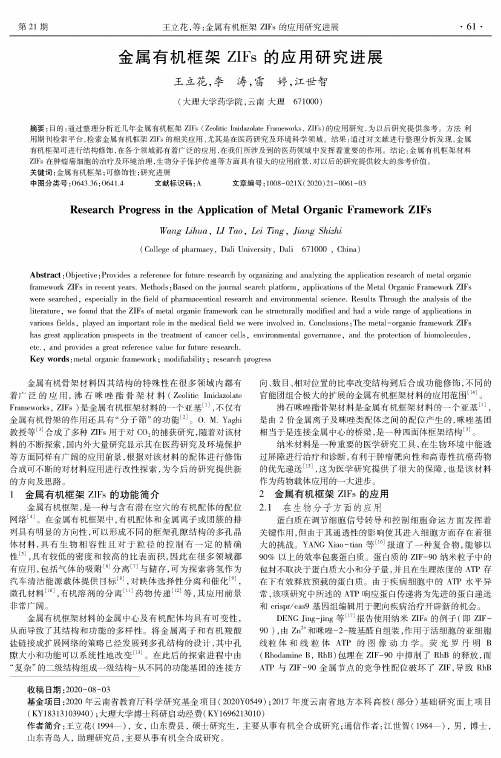
第21期王立花,等:金属有机框架ZIPs的应用研究进展-61-金属有机框架ZIPs的应用研究进展王立花,李涛,雷婷,江世智(大理大学药学院,云南大理671000)摘要:目的:通过整理分析近几年金属有机框架ZIPs(Zeolitic Imidazo—te Frameworks,ZIPs)的应用研究,为以后研究提供参考&方法利用期刊检索平台,检索金属有机框架ZIF的相关应用,尤其是在医药研究及环境科学领域&结果:通过对文献进行整理分析发现,金属有机框架可进行结构修饰,在各个领域都有着广泛的应用,在我们所涉及到的医药领域中发挥着重要的作用&结论:金属有机框架材料ZIPs在肿瘤癌细胞的治疗及环境治理,生物分子保护传递等方面具有很大的应用前景,对以后的研究提供较大的参考价值&关键词:金属有机框架'可修饰性'研究进展中图分类号:0643.36;06413文献标识码:A文章编号:1008-021X(2020)21-0061-03Research Progress in the Application of Metal Organic Framework ZIFsWang LiPua,LI Tao,Lei Ting,Jiang Shizhi(Co e e geoophaemacy,DaeoUnoeeesoty,Daeo671000,Chona)AbstracC:Objective:Provides a reference for future research by oryanizing and analyzing the application research of metal oryanic framework ZIPs in recent years.Methods:Based on the journal search pahorm,applications of the Metal Oryanic Framework ZIPs were searched,especial—in the field of pharmaceutical research and environmental science.Results Through the analysis of the —terature,we found that the ZIPs of metal oryanic framework can be structural—modified and had a wide range of applications in various fielUs,p—yed an important role in the medical field we were involved in.Conclusions:The metal-oryanic framework ZIPs has great application prospects in the Weatwent of cancer cells,environmental governance,and the protection of biomolecuXs, etc.,and provides a great reference value for future research.Key words:mGtaeoeganocoeamGwoek'modoooaboeoty'eGsGaech peoge s金属有机骨架材料因其结构的特殊性在很多领域内都有着广泛的应用,沸石咪瞠酯骨架材料(Zeoli-e Imidazolate Frameworks,ZIPs"是金属有机框架材料的一个亚基[1],不仅有金属有机骨架的作用还具有“分子筛”的功能0i Mi Yaghi 教授等⑶合成了多种ZIPs用于对C02的捕获研究,随着对该材料的不断探索,国内外大量研究显示其在医药研究及环境保护等方面同样有广阔的应用前景,根据对该材料的配体进行修饰合成可不断的对材料应用进行改性探索,为今后的研究提供新的方向及思路&1金属有机框架ZIPs的功能简介金属有机框架,是一种与含有潜在空穴的有机配体的配位网络⑷。
- 1、下载文档前请自行甄别文档内容的完整性,平台不提供额外的编辑、内容补充、找答案等附加服务。
- 2、"仅部分预览"的文档,不可在线预览部分如存在完整性等问题,可反馈申请退款(可完整预览的文档不适用该条件!)。
- 3、如文档侵犯您的权益,请联系客服反馈,我们会尽快为您处理(人工客服工作时间:9:00-18:30)。
Metal-Organic Frameworks in Monolithic StructuresPia Ku sgens,z Alina Zgaverdea,y Hans-Gerhard Fritz,y Sven Siegle,z and Stefan Kaskel w ,zzDepartment of Inorganic Chemistry,Dresden University of Technology,01069Dresden,GermanyyInstitut fu r Kunststofftechnik,Universitat Stuttgart,70199Stuttgart,Germany zMahle Filtersysteme GmbH,70376Stuttgart,GermanyFor the first time,the manufacturing of metal-organic frame-work-based monoliths using a two-step process is reported.In afirst experiment,the in situ synthesis of Cu 3(BTC)2(benzene tricarboxylate [BTC])on cordierite monoliths was chosen to immobilize Cu 3(BTC)2.As this approach turned out to be of major disadvantages,the manufacturing of Cu 3(BTC)2mono-lithic structures was chosen.The two-step fabrication process included the manufacturing of a molding batch in a lab-scale kneader followed by extrusion in a ram-extruder.As additives,methyl hydroxyl propyl cellulose and methoxy functionalized siloxane ether were chosen.The resulting monolithic structures have a specific inner surface area of 370m 2/g and show a high mechanical stability of 320N.I.IntroductionRECENTLY ,a new class of microporous materials known asmetal-organic frameworks (MOFs)has received remark-able attention.1–4MOFs consist of metal clusters linked by polyfunctional or-ganic linkers forming porous three-dimensional networks with large pore volumes and high inner surface areas.The chemistry of MOFs has provided an outstanding class of porous materials with remarkable results regarding storage of gases such as hy-drogen,5,6methane,7and carbon dioxide.8Other promising ap-plications are catalysis,9gas separation,10and even medical applications.11,12Porous materials synthesized hydrothermally are mostly gen-erated as fine-particle powders.For the use in any process and chemical engineering facility or apparatus,it is indispensable to provide the material as an appropriate shape or form,for ex-ample as beads,pellets,monoliths,or as thin films on suitable carrier materials.In an earlier work,we proposed to deposit the material on pulp fibers,which can be molded to paper sheets.13Other groups proposed the deposition on a -alumina 14or on copper mesh.15The chosen shape has to provide both appropriate mechan-ical stability and high secondary surface area to ensure a low-pressure drop and therewith enhanced performance.Another important point is a simple and low-cost production.Therefore,extensive use of expensive materials has to be avoided as well as extensive production processes and pricey carrier materials.In our work,we completely abandoned the use of any carrier material and choose to extrude the material with cheap addi-tives.The most popular and most investigated MOF so far is Cu 3(BTC)2,which is among the first MOFs that are commer-cially available 16and therefore a suitable candidate for a larger scale experiment.In Cu 3(BTC)2,a binuclear copper complex is linked in a paddle-wheel fashion by carboxylate linkers forming a cubic network.17Cu 3(BTC)2was extensively studied regarding its adsorptive properties.18Other investigations for potential use in catalysis were reported by Krawiec et al .,5who studied the cyanosilylation of benzaldehyde.Cu 3(BTC)2is also a promising material for hydrogen storage as discussed among others by Krawiec et al .5and Rowsell and Yaghi.6In the following,we describe two different approaches for the generation of MOF monoliths.Monolithic structures are essential supports for catalytic applications,for example as catalyst carriers for exhaust gas re-duction in three-way catalytic converters.They are usually mac-roporous themselves and have a high surface area due to their thin honeycomb-like channels.The advantage of monoliths is the high mechanical stability and the advantageous volume-to-surface ratio.High mechanical stability leads to low abrasion,which can be a problem in packed beds where beads are used.Another benefit of this structure is the low flow resistance and the resulting low-pressure drop.To the best of our knowledge,no other group has hitherto reported on the manufacturing of pure MOF monoliths.II.Experimental Procedure(1)Deposition of Cu 3(BTC)2on Cordierite MonolithsThe synthetic procedures used to prepare the Cu 3(BTC)2cor-dierite samples are based on the methods according to Schlichte et al .19and Yaghi et al .4with only slight modifications.(2)Extrusion of Cu 3(BTC)2MonolithsThe fabrication of Cu 3(BTC)2monoliths was based on the work of Trefzger.20In this work,Silres MSE 100(CH 3Si(O)1.1(OCH 3)0.8,Wacker-Chemie GmbH,Burghausen,Germany)was used as a binding agent.Culmial MHPC 20000P (methyl hydroxyl propyl cellulose,Hercules-Aqualon,Du sseldorf,Germany)was used as plasticizer.Cu 3(BTC)2was first mixed with the binding agent and plastification additive in a lab-scale kneader until the molding batch was of homogeneous appear-ance.In a second step,the molding batch was extruded to a monolithic strang in a ram extruder.The strang was cut into 200-mm-long pieces,which were treated by microwave drying for 20min.The monoliths were finally dried at an ambient pressure at 1201C for several hours.Figure 1shows the as-made MOF monolith.Several molding batches with differing ratios of the chemicals had been prepared and extruded in the ram extruder yield-ing different results.The final composition,batch No.2in Table I,was used for the extrusion for all samples.All other T.Vanderah—contributing editorThis work was financially supported by the MAHLE Filtersysteme GmbH.wAuthor to whom correspondence should be addressed.e-mail:stefan.kaskel@chemie.tu-dresden.deManuscript No.27092.Received December 16,2009;approved March 24,2010.J ournalJ.Am.Ceram.Soc.,93[9]2476–2479(2010)DOI:10.1111/j.1551-2916.2010.03824.x r 2010The American Ceramic Society2476compositions were either too soft or sticky for the forming pro-cess or the monolith deformed after having passed the extrusion tool.Samples were analyzed by X-ray powder diffraction (XRD)using a Stoe Stadi-P diffractometer (Darmstadt,Germany)and Cu K a 1.Nitrogen physisorption was measured at 77K using a Quantachrome NOVA 2000or a Quantachrome Quadrasorb (Odelzhausen,Germany).Before the measurement,the samples were activated at 1201–2001C for at least 8h.Thermal gravimetric analysis was performed using a Perkin Elmer (Waltham,MA)TGA7apparatus with a heating rate of 10K/min and a gas stream of 20mL/min (synthetic air).Scanning electron microscopy (SEM)and energy-dispersive X-ray spectroscopy (EDX)were performed using a Tescan Vega TS5136XM (Brno,Czech Republic).Before the recordings,the samples were vapor coated with carbon using a Biorad Polar-izon Divison SEM Coating System (Hercules,CA).The kinetic performance was evaluated using a Setaram In-strumentation (Caluire,France)TG-DSC with a B111micro-balance.Nitrogen gas streams were regulated using Wagner mass flow controllers (50mL flow type F-201CV-050_RA and 100mL flow type F-201C-RAD).The mechanical stability was measured using a Zwick 1455(Ulm,Germany)(1000N force sensor)with a test speed of 20mm/min.The preliminary test force was set to 0.5N.Samples were cut in small pieces (dimensions:3.5mm Â5mm Â8mm).III.Results and DiscussionIn a first strategy,cordierite was used as an MOF support using a solution deposition approach.To confirm the formation ofCu 3(BTC)2on the cordierite honeycomb,all samples were finely ground and analyzed.The patterns could not confirm the pres-ence of Cu 3(BTC)2.However,SEM images of the cordierite samples before and after the synthesis of Cu 3(BTC)2show a deposition of crystals only on the cutting edge of the honeycomb (Fig.2).Specific inner surface areas (S A )showed a slightly enhanced inner surface area of 50m 2/g.Apparently,the amount of formed Cu 3(BTC)2was not large enough to detect the peaks of Cu 3(BTC)2in the XRD patterns.As the deposition of Cu 3(BTC)2on cordierite samples turned out to be difficult,we decided to move to a different approach,namely the manufacturing of Cu 3(BTC)2monolithic samples.Compared with the deposition of Cu 3(BTC)2on cordierite honeycombs,the extrusion process requires a binding agent in order to provide a certain mechanical stability of the monolithic structure.The use of additives decreases the solid fraction of the monoliths and therewith its performance by reducing the acces-sible inner surface area.However,shaped bodies are advanta-geous compared with beads or pellets due to lower abrasion and low pressure drop.21The binder used for extrusion should not hinder the mass transport between the particles and the adsorbate.Liquid sub-stances are advantageous,as they are easily distributable with the active material during the kneading process.Silicone resins are suitable binding agents as they are available as liquids,due to the only partly cross-linked structure.Thus,the blending with the molding batch is possible and after forming the mono-liths,they are heated to induce the cross-linking.Additionally,they decompose at about 2001C,thus in the range of the thermal stability of Cu 3(BTC)2that decomposes at about 2801C.The structure of Cu 3(BTC)2has active copper sites,which represent hydrophilic centers.The surface of Cu 3(BTC)2carries some already coordinated water molecules to which the hyd-roxyl groups of the silicone resin can coordinate and yieldtheFig.1.Picture of the Cu 3(BTC)2monolith.Table position of the Different Molding BatchesBatch Water (mL)MHCP 20000P (g)Silres MSE 100(g)Cu 3(BTC)2(g)Result1802550180Sticky 2802025180Best result 3701520180Too soft 4501212180Deformation after extrusion 5401212180ToosoftFig.2.Scanning electron microscopic images of the cordierite honey-comb before (a)and after (b)the synthesis of Cu 3(BTC)2.September 2010Rapid Communications of the American Ceramic Society 2477desired mechanical stability.The same is valid for the zeolite surface that carries silanol groups,which also coordinate to the silicone resin.However,so far very little is known about inter-actions of MOFs with siloxanes and further studies are needed for a better understanding.Because MOF powders like in the case of Cu 3(BTC)2are typically not plastic when mixed with water,the addition of a plasticizer is needed.The main task of a plastification additive is to transform the powder suspensions to a molding batch with suitable flow characteristics.The plastic behavior of methyl cellulose is based on the interaction of the hydrated layers that are found on the surface of zeolite particles.The same should be valid for the Cu 3(BTC)2particles that are also highly hydro-philic due to the copper coordination sites.The water solubility of methylcellulose and the resulting interaction with the water layers support the plasticization properties of methylcellulose.22The function of the plasticizer is no longer necessary after the forming step and it can be burnt off leading to the forma-tion of a secondary pore structure,which promotes a good mass transport.Methylcellulose starts to decompose at 2001C.This was one reason to choose methyl cellulose as the plasticizing agent for zeolite A molding batches,as it easily tolerates temperatures >2001C.Cu 3(BTC)2decomposes at lower temperatures and a complete burn-off in this case is not possible.As a burn-off is not obligatory,methyl cellulose is still a suitable additive for the manufacturing of Cu 3(BTC)2monoliths.The kinetic performance of the monolith was assessed with dynamic water adsorption experiments.The result of the exper-iment is shown in Fig.3.The MOF monolith was compared with a zeolite NaA monolith that was manufactured using the same ram extruder and tool.The MOF monolith showed both a better kinetic performance and a higher total adsorption capac-ity of water vapor compared with the zeolite monolith.In order to evaluate the mechanical stability of the monoliths,the crushing strength of the samples was determined using a Zwick material testing equipment yielding very good results.The as-made samples showed a lower stability with averaged 281N.Activated samples (1501C)were slightly harder with 320N.Tests with the cordierite commercial honeycomb yielded a crushing strength of only 104N.The XRD pattern clearly confirmed the existence of Cu 3(BTC)2in the monoliths as shown in Fig.4.Even after activation,the peaks are clearly observable in the XRD exper-iment.Nevertheless,to determine the quality of the material,nitrogen physisorption experiments are more meaningful.The S A measured was 484m 2/g,which is an excellent result.However,the value decreased after several months to about 287m 2/g,which hints at partial degradation.Even though Cu 3(BTC)2is an MOF standard material and a good choice due to good characterization in the literature,there is still some ambiguity in terms of storage stability and decomposition under highly humid or hydrothermal conditions.23The outgassing temperature was also of great importance.For the first measurement,1501C was chosen.Lower activation temperatures showed a better result for the second series of measurements.As the plasticizer is only needed during the extrusion process,it can be removed or burnt off after the form-ing and drying process.As methylcellulose starts to decompose at 2001C,an activation temperature above this value should be advantageous,as the resulting burn off results in a secondary porous structure that promotes a fast mass transfer.Experi-ments showed that at elevated activation temperatures,values for the inner surface area decreased.The most suitable temperature for outgassing is 1201C.At this temperature,no removal of the plasticizer occurs.However,for future fabrication,the molding batch composition should be further optimized to achieve a higher surface area.As the mold-ing batch contains water,a certain degree of degradation of Cu 3(BTC)2cannot be avoided.IV.ConclusionFor the first time,we have produced pure MOF monoliths with reasonable mechanical stability,an essential step toward the use of this new class of porous solids in industrial separation processes,gas storage,and catalysis.A two-step manufacturing of Cu 3(BTC)2using a ram-extruder yielded stable monolithic structures with specific surface areas up to 484m 2/g.The in situ synthesis of Cu 3(BTC)2on cordierite honeycombs was per-formed as an alternative approach for MOF immobilization,but turned out to be disadvantageous due to the low achievable loading.AcknowledgmentsThe cordierite samples were supplied by the NGK company.The BASF Group is thanked for providing the Cu 3(BTC)2powder.References1S.Kaskel,‘‘Porous Metal-Organic Frameworks’’;pp.1190–249in Handbook of Porous Solids ,Vol.3,Edited by F.Schu th,K.Sing,and J.Weitkamp.Wiley VCH,Weinheim,2002.2M.Eddaoudi,D.Moler,H.Li,T.Reineke,M.O’Keeffe,and O.Yaghi,‘‘Modular Chemistry:Secondary Building Units as a Basis for the Design of a Highly Porous and Robust Metal-Organic Carboxylate Frameworks,’’Acc.Chem.Res.,34,319–30(2001).3S.Kitagawa,R.Kitaura,and S.Noro,‘‘Funktionale Poro se Koordi-nationspolymere,’’Angew.Chem.,116,2388–430(2004).4O.Yaghi,H.Li,C.Davis,D.Richardson,and T.Groy,‘‘Synthetic Strategies,Structure Patterns,and Emerging Properties in the Chemistry of Modular Porous Solids,’’Acc.Chem.Res.,31,474–84(1998).5P.Krawiec,M.Kramer,S.Sabo,R.Kunschke,H.Fro de,and S.Kaskel,‘‘Improved Hydrogen Storage in the Metal-Organic Framework Cu 3(BTC)2,’’Adv.Eng.Mater.,8,293–6(2006).6J.Rowsell and O.Yaghi,‘‘Strategies for Hydrogen Storage in Metal-Organic Frameworks,’’Angew.Chem.Int.Ed.,44,4670–9(2005).7I.Senkovska and S.Kaskel,‘‘High Pressure Methane Adsorption in the Metal-Organic Frameworks Cu 3(btc)2,Zn 2(bdc)2dabco,and Cr 3F(H 2O)O(bdc)3,’’Microporous Mesoporous Mater.,112,108–15(2009).Fig.3.Dynamic water adsorption of zeolite NaA and Cu 3(BTC)2monolithic structures (33.3%RH,251C).Fig.4.X-ray diffraction pattern of the as made Cu 3(BTC)2monolith,the Cu 3(BTC)2monolith after activation at 1201C,and the calculated pattern of Cu 3(BTC)2powder.2478Rapid Communications of the American Ceramic Society Vol.93,No.9lward and O.Yaghi,‘‘Metal-Organic Frameworks with Exeptionally High Capacity for Storage of Carbon Dioxide at Room Temperature,’’J.Am. Chem.Soc.,127,17998–9(2005).9R.Zhou,H.Sakurai,and Q.Xu,‘‘Preparation,Adsorption Properties,and Catalytic Activity of3D Porous Metal-Organic Frameworks Composed of Cubuc Building Blocks and Alkali-Metal Ions,’’Angew.Chem.Int.Ed.,45,2542–6(2006). 10J.Li,R.Kuppler,and H.Zhou,‘‘Selective Gas Adsorption and Separation in Metal-Organic Frameworks,’’Chem.Soc.Rev.,38,1477–504(2009).11P.Horcajada,C.Serre,G.Maurin,N.Ramsahye,F.Ballas,M.Vallet-Regı, M.Sebban,F.Taulelle,and G.Fe rey,‘‘Flexibel Porous Metal-Organic Frame-works for a Controlled Drug Delivery,’’J.Am.Chem.Soc.,130,6774–80(2009). 12R.Morris and P.Wheatley,‘‘Gas Storage in Nanoporous Materials,’’Angew. Chem.Int.Ed.,47,4966–81(2008).13P.Ku sgens,S.Siegle,and S.Kaskel,‘‘Crystal Growth of the Metal-Organic Framework Cu3(BTC)2on the Surface of Pulp Fibers,’’Adv.Eng.Mater.,11,93–5 (2009).14J.Gascon,S.Aguado,and F.Kapteijn,‘‘Manufacture of Dense Coatings of Cu3(BTC)2(HKUST-1)on a-Alumina,’’Microporous Mesoporous Mater.,113, 132–8(2009).15H.Guo,G.Zhu,I.Hewitt,and S.Qiu,‘‘Twin Copper Source:Growth of Metal-Organic Framework Membrane:Cu3(BTC)2with High Permeability and Selectivity for Recycling H2,’’J.Am.Chem.Soc.,113,646–7(2009).16U.Mu ller,M.Schubert,F.Teich,H.Puetter,K.Schierle-Arndt,and J.Pastre,‘‘Metal-Organic Frameworks—Prospective Industrial Application,’’J.Mater. Chem.,16,626–36(2006).17S.Chui,M.Lo,J.Charmant,A.Orpen,and I.Williams,‘‘A Chemically Functionalizable Nanoporous Material[Cu3(TMA)2(H2O)3]n,’’Science,283, 1148–50(1999).18Q.Wang,D.Shen,M.Bu low,u,S.Deng,F.Fitch,N.Lemcoff,and J. Semanscin,‘‘Metallo-Organic Molecular Sieve for Gas Separation and Purifica-tion,’’Microporous Mesoporous Mater.,55,217–30(2002).19K.Schlichte,T.Kratzke,and S.Kaskel,‘‘Improved Synthesis,Thermal Sta-bility and Catalytic Properties of the Metal-Organic Framework Cu3(BTC)2,’’Microporous Mesoporous Mater.,73,81–8(2004).20C.Trefzger,Herstellung zeolithischer Wabenko¨rper.Institut fu r Ku-nststofftechnik,Stuttgart,2003.21H.-G.Fritz and J.Hammer,‘‘Aufbereitung zeolithischer Formmassen und ihre Ausformung zu Adsorptionsformteilen,’’Chem.Ing.Tech.,77,1588–600 (2005).22J.Schuetz,‘‘Methylcellulose Polymers as Binders for Extrusion of Ceramics,’’Am.Ceram.Soc.Bull.,65[12]1556–9(1986).23P.Ku sgens,M.Rose,I.Senkovska,H.Fro de,A.Henschel,S.Siegle,and S. Kaskel,‘‘Characterization of Metal-Organic Frameworks by Water Adsorption,’’Microporous Mesoporous Mater.,120,325–30(2009).&September2010Rapid Communications of the American Ceramic Society2479。