超硬材料刀具在机械制造中的应用
超硬材料行业分析
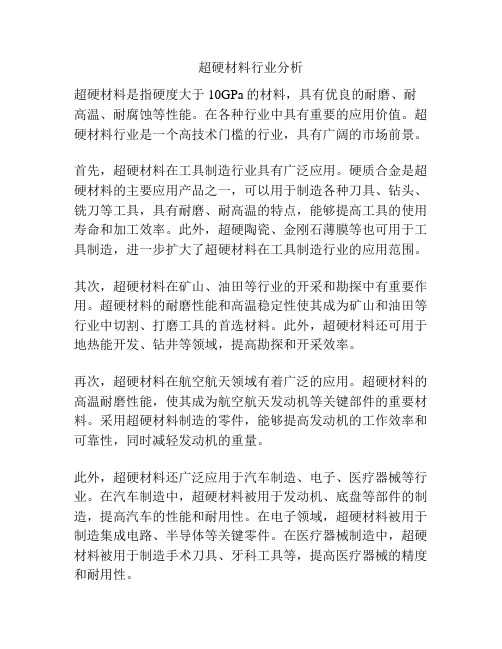
超硬材料行业分析
超硬材料是指硬度大于10GPa的材料,具有优良的耐磨、耐高温、耐腐蚀等性能。
在各种行业中具有重要的应用价值。
超硬材料行业是一个高技术门槛的行业,具有广阔的市场前景。
首先,超硬材料在工具制造行业具有广泛应用。
硬质合金是超硬材料的主要应用产品之一,可以用于制造各种刀具、钻头、铣刀等工具,具有耐磨、耐高温的特点,能够提高工具的使用寿命和加工效率。
此外,超硬陶瓷、金刚石薄膜等也可用于工具制造,进一步扩大了超硬材料在工具制造行业的应用范围。
其次,超硬材料在矿山、油田等行业的开采和勘探中有重要作用。
超硬材料的耐磨性能和高温稳定性使其成为矿山和油田等行业中切割、打磨工具的首选材料。
此外,超硬材料还可用于地热能开发、钻井等领域,提高勘探和开采效率。
再次,超硬材料在航空航天领域有着广泛的应用。
超硬材料的高温耐磨性能,使其成为航空航天发动机等关键部件的重要材料。
采用超硬材料制造的零件,能够提高发动机的工作效率和可靠性,同时减轻发动机的重量。
此外,超硬材料还广泛应用于汽车制造、电子、医疗器械等行业。
在汽车制造中,超硬材料被用于发动机、底盘等部件的制造,提高汽车的性能和耐用性。
在电子领域,超硬材料被用于制造集成电路、半导体等关键零件。
在医疗器械制造中,超硬材料被用于制造手术刀具、牙科工具等,提高医疗器械的精度和耐用性。
综上所述,超硬材料行业具有广阔的市场前景和应用价值。
虽然行业门槛较高,但随着技术的不断进步和市场需求的增加,超硬材料行业有望取得更大的发展。
超高速磨削技术在机械制造中的分析

超高速磨削技术在机械制造中的分析【摘要】随着科学技术不断发展与进步,为了提高机械制造的质量与效率,我国已经逐渐引进了超高速磨削技术。
随着这些年的应用逐渐增加,超高速磨削技术在机械制造中的应用经验越来越丰富。
本文首先概述了超高速磨削技术,对其原理及优势等进行了分析,然后就其在机械制造中的应用进行了详细分析。
【关键词】超高速;磨削技术;机械制造1.超高速磨削技术概述1.1技术分析超高速磨削技术属于超高速加工技术中主要的一种,而超高速加工技术指的是利用超硬材料的刃具,通过提高其切削速度与进给速度来实现材料加工精度、切除率及加工质量提高的一种技术。
就目前来看,超高速加工切削速度往往随着不同的材料及切削方式而不同。
超高速加工技术包括了很多方面,比如说超高速进给单元制造技术、超高速加工用刀具制造技术、超高速切削与磨削机理研究等,其在我国制造业中的应用越来越深入。
其中,最为先进的一种技术为超高速磨削技术。
1.2磨削技术原理在高速或超高速磨削加工中,其余参数保证不便的情况下,砂轮速度大幅度提高,单位时间中磨削区产生的磨粒数就会增加,而磨粒切下之后的磨屑厚度则会相应减小,这样就会使得每颗磨粒被切削后厚度也会变薄。
加之在超高速磨削过程中,磨速极高,每颗磨粒形成时间十分短,在上述情况下,每颗磨粒承受的磨削力则会大大减小,使得总磨削力大大降低。
这样,短暂的时间内所形成的高应变率往往与普通磨削之间有着天壤之别,主要表现在磨削工件表面时,弹性变形层会逐渐变浅,而磨削沟痕的两侧因为塑性流动而产生的隆起高度会降低。
当然,由于上述机理作用,也会使得磨屑形成中的滑擦距离变小,工件表面层的残余及硬化应力倾向也会逐渐减小。
1.3超高速磨削技术优势就目前我国使用超高速磨削技术相关经验效率来看,其主要有以下几个方面的优势:1.3.1磨削效率得到了大大的提升。
1.3.2磨削力得到了明显的降低,同时零件加工的精度也得到了一定的提高。
1.3.3砂轮的耐用度得到了提高,从而延长了机械的使用寿命。
硬质材料刀具在机械加工中的应用

硬质材料刀具在机械加工中的应用摘要:当前,我国的机械加工业迅速发展,一些切割难度比较大的材料在材料工业和精密机械工业中得到了广泛的应用。
而要想满足现代机械加工业的发展需求,还需要科学使用一些强度高、韧性好的工具。
因此,硬质材料刀具便逐渐应用到机械加工业中。
本篇文章针对硬质材料刀具的发展历程,着重探讨了硬质材料刀具在机械加工中的应用,以供同行业朋友相互参考借鉴。
关键词:硬质材料刀具;机械加工;应用中图分类号:s756文献标识码: a 文章编号:现代制造技术随着激烈的市场竞争迅速发展,机械制造业对机械设备零件的要求也日益提高,尤其是对于机械零件结构性能的要求不断提升。
因此,社会上便逐渐出现了具备各种性能的新材料,这些新材料不仅对传统的机械加工刀具提出了严峻的挑战,而且加工难度相当大。
这时,先进的切削刀具便成为机械加工业发展的关键,而硬质材料刀具无可厚非地应用到了现代机械加工中。
一、硬质材料刀具的发展历程上世纪五十年代,美国科学家将人造金刚石、结合剂,以及碳化硼微粉作为原材料,在高温高压的条件下进行反应,将烧结出的聚晶块作为刀具的主要材料。
发展到上世纪七十年代之后,人们逐渐研究出复合片材料,这样的材料是对金刚石与硬质合金结合生产的,或者是氮化硼与硬质合金结合生产的。
这样的技术将硬质合金视为基体,使用压制或者烧结等方法在基体的表面形成一层金刚石而得到的,金刚石大约厚0.5到1毫米。
这样的材料不仅能够提升材料的抗弯性,而且将传统材料不易焊接的问题有效解决。
这便促进了硬质材料刀具进入应用阶段。
二、硬质材料刀具在机械加工中的应用(一)单晶金刚石刀具的应用单晶金刚石通常又被分为人工合成金刚石与天然金刚石。
通常情况下,如果使用单晶金刚石制作刀具,那么就需要选择那些颗粒较大、质量大于0.1克,直径长度大于3毫米的金刚石。
天然金刚石是目前矿物中坚硬程度最高的材料,其不仅耐磨性好,而且使用其制作的刀具非常锋利,同时抗粘结性高,导热率低,加工出的刀具既光滑,质量又好。
超硬材料刀具的研究和应用
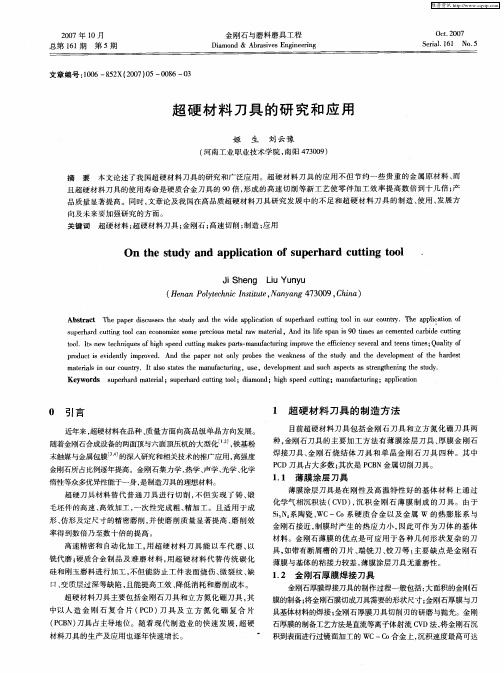
s p r a d c t n o lc n e o o z o rc o s mea a ma e a ,A d i i p n i 9 i s a e n e a b d ut g u e h u t gt o a c n mie s mep e iu tlrw tr l n t l e s a 0 t r i i s f s me sc me t d c r i e c t n i
mae asi u o n r . I a s t ts t e ma u a t r g,u e e eo me t d s c s e t a te gh n n h t d . tr l n o rc u t i y tl o sae h n f cu n i s ,d v l p n u h a p cs ssr n te ig t e su y n a K e wo d s p r a d ma e a ;s p r a d c t n o l imo d;hg p e u t g y rs u e h r t r l u e h r u t g to ;d a n i i ih s e d c t n ;ma u a t r g p lc t n i n f cu n ;a p ia i i o
Oቤተ መጻሕፍቲ ባይዱ引言
近年来 , 超硬材料在品种 、 质量方面 向高品级单晶方向发展。
浅析超硬材料刀具在机械加工中的应用
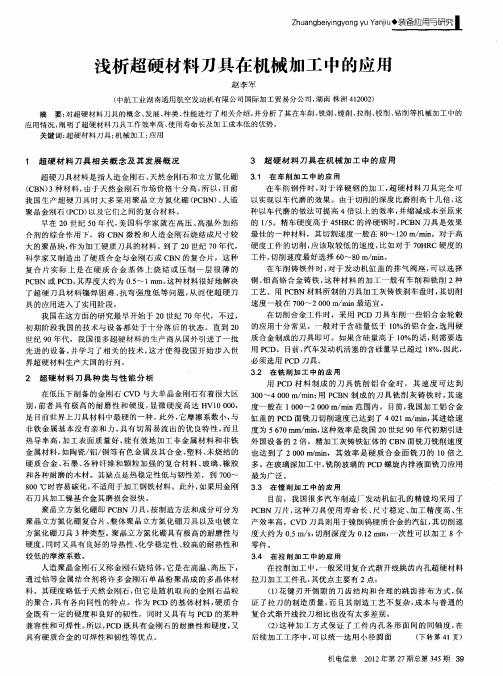
是 目前 世界上刀具材料 中最硬的~种 。 此外 , 它摩擦系数小 , 与 缸盖 的 P D面铣 刀切削速度 己达到 了 40 1 rm, 进给速 C 2 a 其 m/ 非铁金属基 本没 有亲和 力 , 具有 切屑 易流 出的优 良特性 , 而且 度为 56 0m mi, 7 m/ n 这种效率是我 国 2 O世纪 9 O年代初期 引进 热 导率高 , n - 3 q 表面质 量好 , 能有 效地加 工非 金属材 料和 非铁 外 国设备 的 2倍 。精加工 灰铸铁缸体 的 C N面铣 刀铣削速度 B 金 属 材 料 , 陶 瓷 / / 等 有 色 金 属 及 其 合 金 、 料 、 烧 结 的 也 达 到 了 20 0m/ n 其 效 率 是 硬 质 合 金 面 铣 刀 的 1 之 如 铝 铜 塑 未 0 mi, 0倍 硬 质合金 、 石墨、 各种 纤维和颗 粒加 强 的复合材 料 、 玻璃 、 胶 多 。在 玻 璃 深 加 工 中 , 削 玻 璃 的 P D 螺 旋 内排 液 面 铣 刀应 用 橡 铣 C 和 各 种 耐 磨 的木 材 。其 缺 点 是 热 稳 定 性 低 与 韧 性 差 ,到 70 0 最为广泛 。
应 比如对于 7 H C硬度 的 0R 大 的聚 晶块, 为加 工硬 质刀具 的材料 。到了 2 作 0世纪 7 0年代 , 硬 度工件 的切 削 , 该取较低 的速 度 , 切 0 O m/ n 科 学 家 又 制 造 出 了硬 质 合 金 与 金 刚 石 或 C N 的 复 合 片 ,这 种 工 件 , 削 速 度 最好 选 择 6 ~8 mi。 B
我 国在这方面 的研 究最早 开始于 2 0世纪 7 0年代 ,不过 ,
初 期 阶 段 我 国 的技 术 与 设 备 都 处 于 十 分 落 后 的状 态 。直 到 2 的应用十分常 见。一般对于含硅量 低于 1%的铝合金 , 0 0 选用硬 0 则 世 纪 9 代 , 我 国很 多 超 硬 材 料 的 生 产 商 从 国 外 引 进 了 一 批 质 合 金 制 成 的 刀具 即 可 。如 果 含 硅 量 高 于 1%的 话 , 需 要 选 0年
2023年超硬材料行业市场调查报告

2023年超硬材料行业市场调查报告超硬材料是一类具有极高硬度的材料,常见的有金刚石和立方氮化硼。
由于其特殊的物理和化学性质,超硬材料在工业生产和科学研究中有着广泛的应用。
本文将对超硬材料行业进行市场调查,分析其发展趋势和市场潜力。
一、行业概况超硬材料行业是一种新兴的高技术产业,目前市场规模较小,但发展潜力巨大。
超硬材料广泛应用于切削、磨削、钻孔、抛光等工艺,是制造业的重要基础材料。
随着工业升级和科技进步,超硬材料市场需求不断增加。
二、市场需求分析1.汽车制造业随着汽车产业的发展,对汽车零部件的要求越来越高,超硬材料在汽车制造中具有重要的应用价值。
例如,刀具、钻头等使用超硬材料可以提高切削精度和效率。
预计未来几年汽车制造业对超硬材料的需求将持续增长。
2.机械制造业超硬材料在机械制造业中应用广泛,例如,在模具制造、加工精密零部件等领域。
机械制造业的发展需要超硬材料提供高质量的切削和磨削工具,对超硬材料的市场需求也将不断增长。
3.航空航天工业航空航天工业是超硬材料行业的重要应用领域之一。
超硬材料在航空航天领域的应用包括切削工具、机械零部件等。
随着航空航天工业的发展,对超硬材料的需求也将不断增加。
4.电子工业随着电子工业的迅速发展,对高硬度和高热稳定性材料的需求也在不断增加。
超硬材料可用于制作电子元器件,并可提供高精度、高效率的加工工具,对电子工业的发展具有重要意义。
三、发展趋势分析1.技术升级超硬材料行业将继续进行技术创新和升级,提高材料的质量和性能,以满足市场的需求。
例如,开发新型的金刚石合成方法,提高合成效率和纯度,降低成本。
2.市场规模扩大随着各个行业对超硬材料需求的增加,超硬材料行业的市场规模将不断扩大。
据市场分析,未来几年超硬材料行业的年均复合增长率将达到10%以上。
3.行业竞争加剧随着市场需求的增加,超硬材料行业的竞争也将越来越激烈。
新进入市场的企业将与现有企业展开竞争,技术和质量成为企业竞争的重要因素。
超硬材料的制备与应用
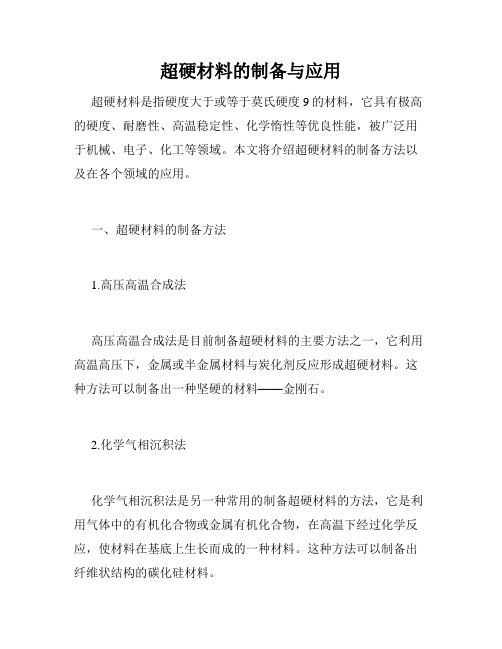
超硬材料的制备与应用超硬材料是指硬度大于或等于莫氏硬度9的材料,它具有极高的硬度、耐磨性、高温稳定性、化学惰性等优良性能,被广泛用于机械、电子、化工等领域。
本文将介绍超硬材料的制备方法以及在各个领域的应用。
一、超硬材料的制备方法1.高压高温合成法高压高温合成法是目前制备超硬材料的主要方法之一,它利用高温高压下,金属或半金属材料与炭化剂反应形成超硬材料。
这种方法可以制备出一种坚硬的材料——金刚石。
2.化学气相沉积法化学气相沉积法是另一种常用的制备超硬材料的方法,它是利用气体中的有机化合物或金属有机化合物,在高温下经过化学反应,使材料在基底上生长而成的一种材料。
这种方法可以制备出纤维状结构的碳化硅材料。
3.快速凝固法快速凝固法是另一种制备超硬材料的方法,它的特点是在凝固过程中产生高浓度的固溶体,这些固溶体的原子排列非常紧密,从而形成超硬材料。
这种方法产生的超硬材料包括氮化硼和碳化硼等。
二、超硬材料的应用1.机械加工领域超硬材料可以用于机械加工领域中的刀具、切割头等工具的制作。
由于超硬材料的硬度极高,可以在很高的速度下切削,大大提高生产效率。
2.电子领域超硬材料可以用于电子领域中的半导体加工、显示器制造等。
由于超硬材料具有高温稳定性、化学惰性等特点,能够更好地满足电子行业的需求。
3.化工领域超硬材料可以用于化工领域中的催化剂、炉膛制造等。
由于超硬材料的热稳定性和耐腐蚀性很高,可以在极端的高温、高压、腐蚀等恶劣环境下工作。
4.医疗领域超硬材料可以用于医疗领域中的牙科、骨科等。
由于超硬材料的硬度高、耐用性高,可以用于制造各种医疗器械,更好地保护患者的健康。
五、结语超硬材料是一种非常重要的材料,它的制备方法和应用领域非常广泛。
随着科技的不断发展,超硬材料将会在更多的领域得到应用,为人类的生产和生活带来更多的便利和效益。
机械制造的新工艺和新方法

机械制造与自动化的新工艺和新方法随着机械工业的发展和科学技术的进步,机械制造工艺的内涵和外延不断发生变化常规工艺不断优化并普及,原来十分严格的工艺界限和分工,如下料和加工、毛坯制造和零件加工,粗加工和精加工、冷加工和热加工等在界限上逐步趋于淡化,在功能上趋于交叉,各种先进加工方法不断出现和发展。
以下为一些机械制造的新工艺和新方法:1、超高速加工技术超高速加工技术是指采用超硬材料刀具磨具和高速运动的自动化制造设备,以极大的切削速度来达到提高材料切除率、加工精度和加工质量的现代加工技术.超高速加工能使被加工金属材料在切除过程中的剪切滑移速度达到或超过某个极限值,使切削加工过程所消耗的能量、切削力、加工表面温度、刀具磨具磨损、加工表面质量、加工效率等明显优于常规切削速度下的指标,它是提高切削和磨削效果、提高加工质量、加工精度和降低加工成本的重要手段。
与常规切削加工相比,超高速加工有以下优点:(1)随着进给速度的提高,单位时间内材料的切除率可以增加3-6倍,可以大幅度缩短零件加工的切削工时,显著提高生产率。
(2)切削力可以降低30%以上。
(3)切削过程极其迅速,95%以上的切削热被切屑带走,来不及传给工件,故特别适合加工容易热变形的零件。
(4)机床作高速运转,振动频率特别高,工作平稳振动小,因而能加工非常精密、非常光洁的零件。
2、超精密加工技术超精密加工是指加工精度和表面质量达到极高程度的精密加工工艺.目前超精密加工的主要手段有:金刚石刀具超精切削,金刚石砂轮和CBN砂轮超精密磨削、超精密研磨和抛光、精密特种加工和复合加工。
金刚石砂轮超精密磨削是当前超精密加工的重要研究方向之一,其主要加工方式有外圆磨、无心磨、、沟槽磨和切割等,被加工材料有陶瓷、半导体等难加工材料,其关键技术包括金刚石砂轮的修整、微粉金刚石砂轮超精密磨削等。
金刚石砂轮的修整包括整形和修锐两部分,对于密实型无气孔的金刚石砂轮,如金属结合剂金刚石砂轮,一般在整形后还需要修锐;有气孔型陶瓷结合剂金刚石砂轮在整形后即可使用。
- 1、下载文档前请自行甄别文档内容的完整性,平台不提供额外的编辑、内容补充、找答案等附加服务。
- 2、"仅部分预览"的文档,不可在线预览部分如存在完整性等问题,可反馈申请退款(可完整预览的文档不适用该条件!)。
- 3、如文档侵犯您的权益,请联系客服反馈,我们会尽快为您处理(人工客服工作时间:9:00-18:30)。
超硬材料刀具在机械制造中的应用
一、超硬材料刀具在机械制造业中的应用
超硬材料刀具不仅是加工高硬度材料的理想刀具,而且适用于高速精密和自动化加工,尤其是用超硬材料刀具进行以车代磨、以铣代磨,更具有高效、低耗。
适应性强、缩短制造周期等优点,目前已在要求精度高、批量大的汽车零部件加工中得到广泛应用。
虽然这类刀具的价格比硬质合金类贵,但只要加工对象和条件选择得适当,分摊到每个工件的刀具成本反而低于硬质合金刀具。
如一汽公司用PCD刀具精镗硅铝合金材料的活塞销孔(V=160m/min,f=0.08-0.10mm/r,a=0.05mm。
),刀具耐用度达 42500件,是原来硬质合金刀具的90倍,加工表面粗糙度值由原来的*,每班可减少装调刀具等辅助时间30min,分摊到每个工件的刀具成本比硬质合金刀具下降了约85%。
PCBN刀具的耐磨性比末涂层的硬质合金刀具高50倍,比涂层的硬质合金刀具高刀倍,比陶瓷刀具高25倍,但只接近金刚石刀具的一半。
二、超硬材料磨具在机械制造业中的应用
金属材料的加工。
不仅可以替代普通磨具的磨削,而且可以实现铸、锻毛坯件的高速、高效加工,一次性完成粗、精磨削。
尤其适用于成形、仿形及定尺寸的精密磨削,可使磨削质量和磨削效率得到数倍乃至数十倍的提高。
硬质合金制品及难磨材料的加工。
硬质合金硬度高、耐磨性强,用超硬材料代替传统碳化硅和刚玉磨料加工硬质合金工件,可防止工件表面烧伤、微裂纹。
缺口或变质层过深等缺陷,提高加工效率和节约磨削成本。
超硬材料硬度比普通磨料高得多,其磨削能力用复合式渐开线跳齿内孔拉刀来加工工件孔,优点为:(1)用这种技刀加工工件的花键孔,由于能够可靠地保证工件内孔各形面间的同轴度,因而可以在工件的后续加工工序中统一用小径圆面作为定位基准,大大地方便了工件后续加工工序定位心轴和检验心轴的制作,又能够可靠地保证工件所有加工表面的位置精度。
(2)复合式渐开线跳齿内孔拉刀是一种质量、经济都比较好的拉刀。
由于这种技刀的刀齿采用了合理的跳齿排布方式和花键刃开侧隙的刀齿结构,可以可靠地保证技刀的制造质量,大大方便了拉刀的制造,这种技刀的制造成本几乎和普通复合式渐开线拉刀相同。
为普通磨料的2000-10000)倍,因此硬质合金的各种形式的磨削均可用超硬材料来实现。
陶瓷材料加工。
近年来陶瓷已作为一种技术进步产品,新陶瓷材料可作为金属和WC的替代材料获得工业应用。
作为工程陶瓷产品,必须具备良好的表面粗糙度和准确的尺寸公差,但由于这些陶瓷有高硬度、高强度、抗磨损等特性,用普通工具加工十分困难,而用超硬材料工具加工则是唯一经济而科学的方法。
铁氧体材料加工。
铁氧体又称黑色陶瓷,是重要的电子元件。
从20世纪60年代开始用超硬材料加工,至今已获全面应用。
如平面磨削磁芯、双端面磨削扬声器磁钢、R成形磨瓦形磁钢等。
应用超硬材料磨具磨削铁氧体的优点是工效高、节能节材、减少废品。
提高工件质量减少环境污染及减轻劳动强度。
宝石加工。
人工合成的红宝石、水晶等是工业用元器件原料,它们的切、磨、钻、抛、研都是用超硬材料来完成的。
半导体材料加工。
半导体硅等硬、脆,价值极贵重,随着计算机技术进入超大规模集成化,对硅片的精。
度要求愈益严格,用传统的普通磨具加工已不能满足需要,而必须改用超硬材料磨具。
电气绝缘材料加工。
电气绝缘材料具有导热性和耐热性差、非均质性和摩擦性强等特点。
因此其切割、钻孔、表面加工所用的传统的金属工具,存在崩口。
起层、毛刺、烧伤等缺陷,从而使介电性能和物理机械性能下降。
采用超硬材料工具加工不仅可消除上述缺陷,而且综合成本也低。
以CBN砂轮为例,因其硬度高(比普通磨料刚玉和碳化硅高出2-3倍),切削刃耐磨,且在很高的磨削温度下,不与铁族金属反应,是磨削铁基和镍基材料理想的超硬磨具。
在使用普通磨具磨削难以达到较高的生产率和较低的生产成本时,尤其是需要加工硬质材料或其它难加工材料时,或是对加工件质量要求较高时,都考虑采用CBN磨具磨削。
一般说来,采用CBN磨具磨削可以提高效率数十倍,降低生产总成本25%-50%。
三、制约超硬材料刀具应用的因素及对策
加强超硬材料刀具制造技术的系统研究。
对刀具的配方应以开发专用配方为主,并加以系统化。
加强超硬材料刀具应用技术的研究。
包括刀具选择的原则、工艺参数的优化、修整、刃磨和冷却技术。
加强宏观管理,合理引导。
鼓励企业联合、组建大型集团,形成规模化生产。
加强超硬材料刀具的推广应用和普及。
超硬材料刀具制造企业应积极与使用单位紧密联系,加大宣传力度,正确引导用户合理使用。