座体铸造工艺设计及其模拟优化
座体铸造工艺设计及其模拟优化
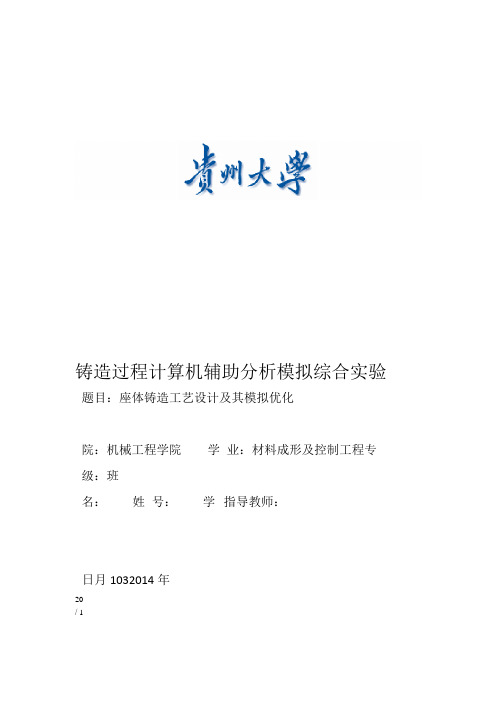
铸造过程计算机辅助分析模拟综合实验题目:座体铸造工艺设计及其模拟优化院:机械工程学院学业:材料成形及控制工程专级:班名:姓号:学指导教师:日月1032014年20/ 1目录第一章.零件简介 (2)1.1 零件基本信息 (2)1.2技术要求 (5)第二章.基于UG零件的三维造型 (6)2.1软件简介 (6)2.2 零件的三维造型图 (6)第三章.铸造工艺方案的拟定 (7)3.1工艺方案的确定 (7)3.2型(芯)砂配比 (7)3.3混砂工艺 (8)3.4 铸造用涂料、分型剂及胶补剂 (8)3.5熔炼设备及熔炼工艺 (9)3.6分型面的选择 (6)3.7 砂箱大小及砂箱中铸件数目的确定 (7)3.8铸造工艺参数的确定 (7)第四章.砂芯设计及排气 (8)4.1芯头的基本尺寸 (8)4.2砂芯设计尺寸见下工艺图 (9)第五章.浇注系统设计.................... 错误!未定义书签。
5.1浇注系统的类型及选择............... 未定义书签。
!误错.5.2浇注位置的选择..................... 错误!未定义书签。
5.3浇注系统各部分尺寸的计算........... 错误!未定义书签。
5.4合金铸造性能分析................... 错误!未定义书签。
5.5 设计计算步骤....................... 错误!未定义书签。
5.6出气孔 (14)5.7铸件工艺出品率 (14)第六章.模拟仿真部分 (15)6.1充型模拟 (15)6.2凝固模拟 (15)第七章.结论及优化方案 (16)第八章.小结 (16)主要参考文献: (19)要摘本文通过对座体零件图的深入分析,根据零件的形状、尺寸、材料等特点,采用传统设计方法与计算机辅助设计相结合的方式对零件的铸造工艺进行设计。
分析并确定采用卧式造型合箱,底注式浇注的砂型铸造工艺方案;确定了铸铁件的凝固原则、浇注位置和分型面等;确定了座体铸铁件的铸造工艺参数并计算了其体积和重量;设计并计算了箱盖砂型铸造的浇注系统;绘制了座体砂型铸造工艺图、UG20/ III铸件图、合箱图等;并采用华铸CAE模拟软件进行模拟分析。
CAE仿真指导铸造关键工艺参数优化设计
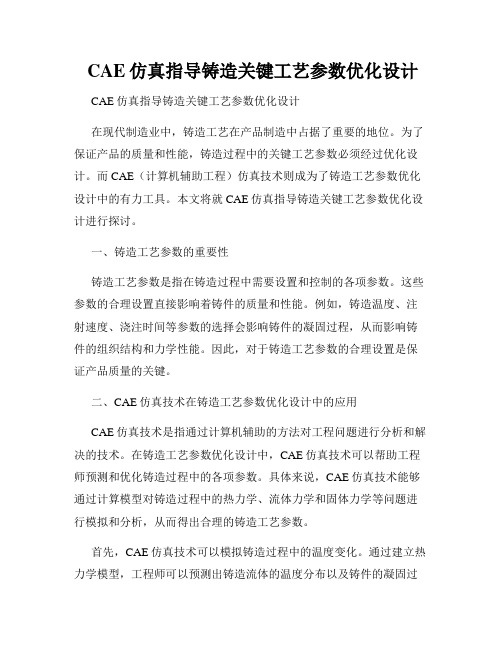
CAE仿真指导铸造关键工艺参数优化设计CAE仿真指导铸造关键工艺参数优化设计在现代制造业中,铸造工艺在产品制造中占据了重要的地位。
为了保证产品的质量和性能,铸造过程中的关键工艺参数必须经过优化设计。
而CAE(计算机辅助工程)仿真技术则成为了铸造工艺参数优化设计中的有力工具。
本文将就CAE仿真指导铸造关键工艺参数优化设计进行探讨。
一、铸造工艺参数的重要性铸造工艺参数是指在铸造过程中需要设置和控制的各项参数。
这些参数的合理设置直接影响着铸件的质量和性能。
例如,铸造温度、注射速度、浇注时间等参数的选择会影响铸件的凝固过程,从而影响铸件的组织结构和力学性能。
因此,对于铸造工艺参数的合理设置是保证产品质量的关键。
二、CAE仿真技术在铸造工艺参数优化设计中的应用CAE仿真技术是指通过计算机辅助的方法对工程问题进行分析和解决的技术。
在铸造工艺参数优化设计中,CAE仿真技术可以帮助工程师预测和优化铸造过程中的各项参数。
具体来说,CAE仿真技术能够通过计算模型对铸造过程中的热力学、流体力学和固体力学等问题进行模拟和分析,从而得出合理的铸造工艺参数。
首先,CAE仿真技术可以模拟铸造过程中的温度变化。
通过建立热力学模型,工程师可以预测出铸造流体的温度分布以及铸件的凝固过程。
根据模拟结果,工程师可以调整铸造温度和凝固时间等参数,以实现理想的凝固结构和性能。
其次,CAE仿真技术可以模拟铸造过程中的流体流动情况。
通过建立流体力学模型,工程师可以预测出浇注过程中的金属液流动速度和压力分布。
根据模拟结果,工程师可以调整注射速度和浇注时间等参数,以优化铸造工艺,避免产生缺陷,提高铸件的质量。
此外,CAE仿真技术还可以对铸件的固态变形进行模拟和分析。
通过建立固体力学模型,工程师可以预测出铸件在凝固和冷却过程中的应力和变形情况。
根据模拟结果,工程师可以调整铸造温度和冷却速率等参数,以减少应力集中和变形产生,提高铸件的整体性能。
三、CAE仿真技术的优势和挑战CAE仿真技术在铸造工艺参数优化设计中具有许多优势。
CAE仿真指导优化铸造关键工艺参数设计
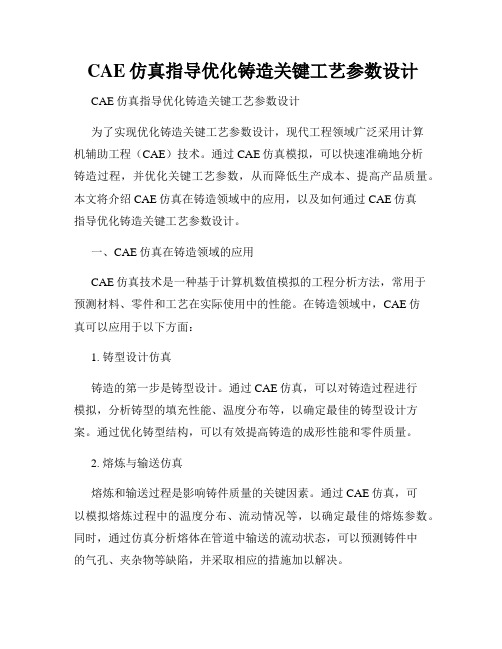
CAE仿真指导优化铸造关键工艺参数设计CAE仿真指导优化铸造关键工艺参数设计为了实现优化铸造关键工艺参数设计,现代工程领域广泛采用计算机辅助工程(CAE)技术。
通过CAE仿真模拟,可以快速准确地分析铸造过程,并优化关键工艺参数,从而降低生产成本、提高产品质量。
本文将介绍CAE仿真在铸造领域中的应用,以及如何通过CAE仿真指导优化铸造关键工艺参数设计。
一、CAE仿真在铸造领域的应用CAE仿真技术是一种基于计算机数值模拟的工程分析方法,常用于预测材料、零件和工艺在实际使用中的性能。
在铸造领域中,CAE仿真可以应用于以下方面:1. 铸型设计仿真铸造的第一步是铸型设计。
通过CAE仿真,可以对铸造过程进行模拟,分析铸型的填充性能、温度分布等,以确定最佳的铸型设计方案。
通过优化铸型结构,可以有效提高铸造的成形性能和零件质量。
2. 熔炼与输送仿真熔炼和输送过程是影响铸件质量的关键因素。
通过CAE仿真,可以模拟熔炼过程中的温度分布、流动情况等,以确定最佳的熔炼参数。
同时,通过仿真分析熔体在管道中输送的流动状态,可以预测铸件中的气孔、夹杂物等缺陷,并采取相应的措施加以解决。
3. 铸造工艺仿真铸造工艺参数对铸件质量起着决定性作用。
通过CAE仿真,可以模拟铸造过程中的铸件填充、凝固过程,分析温度变化、应力分布等,以指导优化铸造工艺参数的设计。
通过合理调整工艺参数,可以降低缺陷率、提高产品质量。
二、CAE仿真指导优化铸造关键工艺参数设计的方法实施CAE仿真指导优化铸造关键工艺参数设计,需要遵循以下步骤:1. 确定铸造关键工艺参数根据具体铸造工艺的特点,确定需要优化的关键工艺参数,例如铸型温度、浇注速度、浇注温度等。
2. 建立仿真模型基于CAE软件,建立铸造过程的仿真模型。
包括铸型结构、材料性质、初始条件等。
3. 设置边界条件根据实际情况,设置仿真模型的边界条件,如环境温度、初始温度、填充时间等。
4. 进行仿真分析运行仿真模型,进行铸造工艺的仿真分析。
铸造工艺设计优化

铸造工艺设计模拟优化CASTsoft在核屏蔽箱体铸钢件的生产应用市沙湾长兴铸钢有限责任公司(614900)罗建君北方恒利科技发展(100089)宋彬摘要:本文介绍北方恒利科技开发的铸造工艺设计及模拟优化CASTsoft CAD/CAE在核屏敝箱体铸钢件工艺设计及优化方面的应用,同时介绍了水玻璃七0砂型(石灰石水玻璃砂型)在核屏敝箱体铸钢件上的应用;证明了用先进的科学技术,合理的铸造工艺,控制生产关健环节,采用铬铁矿砂作坭芯面砂能生产出要求较高的探伤核屏敝铸钢件。
关键词:铸造工艺设计 CASTsoft 铸造工艺模拟浇注温度工艺优化核屏蔽铸钢件水玻璃七0砂型漂珠保温冒口套The casting process simulation and optimization CASTsoft in the nuclear shielding box of steelcasting production applicationsLeshan City, Sandy Bay, Changxing Cast Steel Co., Ltd.(614900)Luo JianjunBeijing North Fangheng Li Technology Development Co., Ltd. (100089) Song Bin Abstract :This article describes the casting process design and simulation and optimization of Beijing North the Hengli Technology Co., Ltd. developed CASTsoft CAD / CAE in the design and optimization of the nuclear shielding box for Steel Casting, also introduced water glass 70 sand (limestone water glass sand) on the nuclear shielding box steel castings; proved that advanced science and technology, casting process, production of key aspects of the use of chromite sand Cement core surface sand can produce higherflaw nuclear shielding steel castings.Keywords:Casting Process Design CASTsoft Casting process simulation Pouring temperature Process optimization Nuclear shielding of steel castings Floating Beadsriser一、前言目前,在川多数铸造企业采用传统水玻璃七0砂型(石灰石水玻璃砂型)工艺进行铸件生产。
拉杆座(二)铸造工艺优化及数值模拟
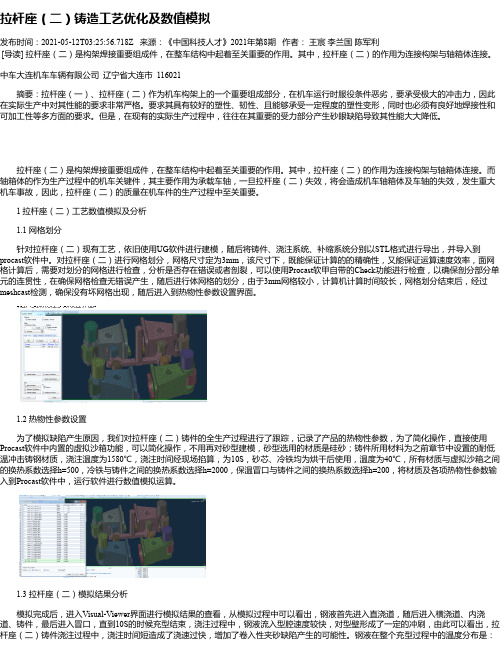
拉杆座(二)铸造工艺优化及数值模拟发布时间:2021-05-12T03:25:56.718Z 来源:《中国科技人才》2021年第8期作者:王宸李兰国陈军利[导读] 拉杆座(二)是构架焊接重要组成件,在整车结构中起着至关重要的作用。
其中,拉杆座(二)的作用为连接构架与轴箱体连接。
中车大连机车车辆有限公司辽宁省大连市 116021摘要:拉杆座(一)、拉杆座(二)作为机车构架上的一个重要组成部分,在机车运行时服役条件恶劣,要承受极大的冲击力,因此在实际生产中对其性能的要求非常严格。
要求其具有较好的塑性、韧性、且能够承受一定程度的塑性变形,同时也必须有良好地焊接性和可加工性等多方面的要求。
但是,在现有的实际生产过程中,往往在其重要的受力部分产生砂眼缺陷导致其性能大大降低。
拉杆座(二)是构架焊接重要组成件,在整车结构中起着至关重要的作用。
其中,拉杆座(二)的作用为连接构架与轴箱体连接。
而轴箱体的作为生产过程中的机车关键件,其主要作用为承载车轴,一旦拉杆座(二)失效,将会造成机车轴箱体及车轴的失效,发生重大机车事故,因此,拉杆座(二)的质量在机车件的生产过程中至关重要。
1 拉杆座(二)工艺数值模拟及分析1.1 网格划分针对拉杆座(二)现有工艺,依旧使用UG软件进行建模,随后将铸件、浇注系统、补缩系统分别以STL格式进行导出,并导入到procast软件中。
对拉杆座(二)进行网格划分,网格尺寸定为3mm,该尺寸下,既能保证计算的的精确性,又能保证运算速度效率,面网格计算后,需要对划分的网格进行检查,分析是否存在错误或者剖裂,可以使用Procast软甲自带的Check功能进行检查,以确保剖分部分单元的连贯性,在确保网格检查无错误产生,随后进行体网格的划分,由于3mm网格较小,计算机计算时间较长,网格划分结束后,经过meshcast检测,确保没有坏网格出现,随后进入到热物性参数设置界面。
1.2 热物性参数设置为了模拟缺陷产生原因,我们对拉杆座(二)铸件的全生产过程进行了跟踪,记录了产品的热物性参数,为了简化操作,直接使用Procast软件中内置的虚拟沙箱功能,可以简化操作,不用再对砂型建模,砂型选用的材质是硅砂;铸件所用材料为之前章节中设置的耐低温冲击铸钢材质,浇注温度为1580℃,浇注时间经现场掐算,为10S,砂芯、冷铁均为烘干后使用,温度为40℃,所有材质与虚拟沙箱之间的换热系数选择h=500,冷铁与铸件之间的换热系数选择h=2000,保温冒口与铸件之间的换热系数选择h=200,将材质及各项热物性参数输入到Procast软件中,运行软件进行数值模拟运算。
轴承座铸造工艺方案研究及模拟
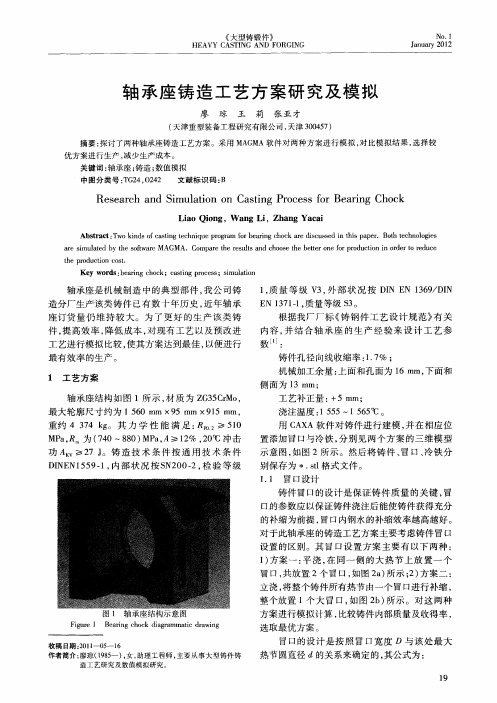
关键词 : 轴承座 ; 铸造 ; 数值模拟
中 图 分 类 号 :G 4 0 4 T 2 ,22 文 献 标 识 码 : B
Re e rh a d S mu ain o si g P o e sfrBe rn o k s ac n i lto n Ca tn r c s 0 a ig Ch c
一
个半 径 的长 度 。即 总 长 度 为 15 .D。其 高 度 日
=
2 MAGMA 模 拟分 析
(. 09 D 0 7~ . )
MA MA是 一套 基 于有 限差 分原 理 编 制 的用 G
同 时 , 了保 证 冒 口对铸 件有 良好 的补 缩 能 为
力 , 冒 口周 围撞 一层保 温 材料 , 冒 口上表 面要 在 在 覆盖 发热 剂 和保 温剂 。
轴承座 是 机 械制 造 中 的典 型 部件 , 公 司铸 我 造 分 厂生产 该类 铸 件 已有 数 十 年 历史 , 年 轴 承 近 座 订货 量 仍 维 持 较 大 。为 了更 好 的 生 产 该 类 铸 件, 提高 效 率 , 低成 本 , 现 有 工艺 以及 预 改进 降 对 工 艺进 行模 拟 比较 , 使其 方案 达 到最佳 , 以便进 行 最 有效 率 的生 产 。
下:
从 图 3中可 以看 出 , 3 c 所 示 为 去 除 冒 口 图 () 后从 浇 注方 向俯 视 图 , 口下 以及 轴 承座 孔 中心 冒
部位铸件表面质量均较好 , 基本不会产生缺陷。
方案 二 : IA NY MA 判 据 , 示 结 果 如 图 4所 显
示。
从 图 4中可 以看 出 , 轴 承 座 孔 中心 底 部 产 在
铸造过程仿真及优化方法的研究
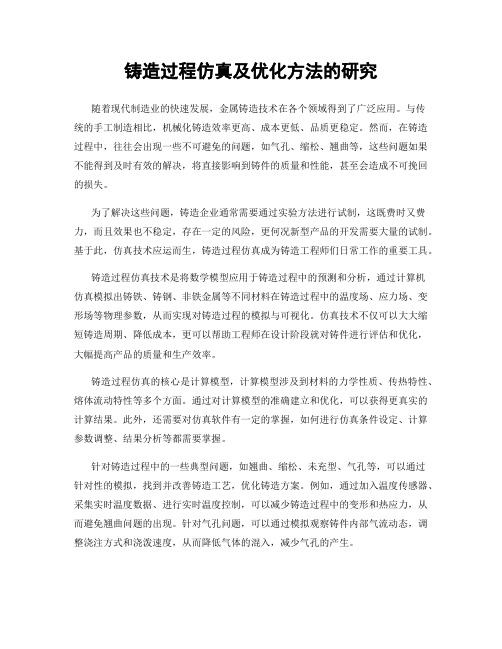
铸造过程仿真及优化方法的研究随着现代制造业的快速发展,金属铸造技术在各个领域得到了广泛应用。
与传统的手工制造相比,机械化铸造效率更高、成本更低、品质更稳定。
然而,在铸造过程中,往往会出现一些不可避免的问题,如气孔、缩松、翘曲等,这些问题如果不能得到及时有效的解决,将直接影响到铸件的质量和性能,甚至会造成不可挽回的损失。
为了解决这些问题,铸造企业通常需要通过实验方法进行试制,这既费时又费力,而且效果也不稳定,存在一定的风险,更何况新型产品的开发需要大量的试制。
基于此,仿真技术应运而生,铸造过程仿真成为铸造工程师们日常工作的重要工具。
铸造过程仿真技术是将数学模型应用于铸造过程中的预测和分析,通过计算机仿真模拟出铸铁、铸钢、非铁金属等不同材料在铸造过程中的温度场、应力场、变形场等物理参数,从而实现对铸造过程的模拟与可视化。
仿真技术不仅可以大大缩短铸造周期、降低成本,更可以帮助工程师在设计阶段就对铸件进行评估和优化,大幅提高产品的质量和生产效率。
铸造过程仿真的核心是计算模型,计算模型涉及到材料的力学性质、传热特性、熔体流动特性等多个方面。
通过对计算模型的准确建立和优化,可以获得更真实的计算结果。
此外,还需要对仿真软件有一定的掌握,如何进行仿真条件设定、计算参数调整、结果分析等都需要掌握。
针对铸造过程中的一些典型问题,如翘曲、缩松、未充型、气孔等,可以通过针对性的模拟,找到并改善铸造工艺,优化铸造方案。
例如,通过加入温度传感器、采集实时温度数据、进行实时温度控制,可以减少铸造过程中的变形和热应力,从而避免翘曲问题的出现。
针对气孔问题,可以通过模拟观察铸件内部气流动态,调整浇注方式和浇泼速度,从而降低气体的混入,减少气孔的产生。
除了利用仿真技术进行铸造工艺优化,还可以结合多项优化策略,如优化铸造设计、改进模具结构、采用提高材料液态流动性能的铸造材料等,综合提高铸造产品的质量和生产效率。
总之,铸造过程仿真技术的应用可以大大降低铸造过程中的损失,提高产品质量,同时节约时间和成本,是铸造生产过程中不可或缺的重要工具。
利用三维模拟软件优化轴承座铸造工艺

利用三维模拟软件优化轴承座铸造工艺作者:万兴龙来源:《科学与财富》2015年第22期摘要:采用Solidworks三维软件对美卓矿山机械轴承座及工艺方案进行实体造型,用华铸模拟软件进行模拟,通过比较冒口尺寸及摆放方式,预测了形成缩孔缺陷的不同倾向,比较不同工艺缩孔分布及工艺出品率,优化冒口工艺设计,并解决了原工艺切除冒口后精整的困难,缩短了轴承座精整时间,降低了生产成本,保证了产品工期。
关键词:轴承座数值模拟出品率铸造工艺1、铸件结构特点及技术要求该件为美卓颚式破碎机用轴承座,材质为ZG20Mn2,要求不得有缩孔缩松及影响强度性能的铸造缺陷,铸件要求磁粉和超声波探伤,达到磁粉EN1369 (level 3)和超声波EN12680-1检验标准,铸件结构如图1:2、工艺方案模拟优化根据铸件结构特点,我们设计了多种工艺方案,并利用模拟软件进行模拟。
下面介绍原工艺方案及改进工艺方案。
2.1原方案:按照常规操作方法设置腰型冒口4个,冒口规格为180mm×270mm×235mm,如图2所示。
按此冒口方案进行纯凝固数值模拟,模拟结果如图3所示,铸件本体没有缩孔缩松,工艺出品率为58%,但A面不加工,切割冒口后,精整很困难,耗时耗力,不仅增加了生产成本,而且延长了生产工期,成为该产品的一个生产瓶颈,针对这种情况,我们优化工艺,设计了另一套方案。
2.2改进后方案:为避免A面放置冒口,减少精整阶段不必要的修磨,设计放置2个圆形冒口和2个冷铁,冒口尺寸为φ200mm×500mm,冷铁尺寸为100mm×60mm×40mm,如图4所示。
按此方案进行纯凝固数值模拟,模拟结果如图5所示,铸件本体没有缩孔缩松,工艺出品率为65%,模拟结果表明,改进后的工艺可行,不仅提高产品出品率,而且大大的较低了A面精整阶段的修磨量。
3、生产过程控制模具制作出口美卓的轴承座为我公司定型产品,产品订单较多,模具采用整体木模,为保证吊运、起模方便,在模具上安装起模鼻。
- 1、下载文档前请自行甄别文档内容的完整性,平台不提供额外的编辑、内容补充、找答案等附加服务。
- 2、"仅部分预览"的文档,不可在线预览部分如存在完整性等问题,可反馈申请退款(可完整预览的文档不适用该条件!)。
- 3、如文档侵犯您的权益,请联系客服反馈,我们会尽快为您处理(人工客服工作时间:9:00-18:30)。
铸造过程计算机辅助分析模拟综合实验题目:座体铸造工艺设计及其模拟优化学院:机械工程学院专业:材料成形及控制工程班级:姓名:学号:指导教师:2014年3月10日1 / 20目录第一章.零件简介 (2)1.1 零件基本信息 (2)1.2技术要求 (5)第二章.基于UG零件的三维造型 (6)2.1软件简介 (6)2.2 零件的三维造型图 (6)第三章.铸造工艺方案的拟定 (7)3.1工艺方案的确定 (7)3.2型(芯)砂配比 (7)3.3混砂工艺 (8)3.4 铸造用涂料、分型剂及胶补剂 (8)3.5熔炼设备及熔炼工艺 (9)3.6分型面的选择 (6)3.7 砂箱大小及砂箱中铸件数目的确定 (7)3.8铸造工艺参数的确定 (7)第四章.砂芯设计及排气 (8)4.1芯头的基本尺寸 (8)4.2砂芯设计尺寸见下工艺图 (9)第五章.浇注系统设计.................... 错误!未定义书签。
5.1浇注系统的类型及选择 ............... 错误!未定义书签。
5.2浇注位置的选择..................... 错误!未定义书签。
5.3浇注系统各部分尺寸的计算 ........... 错误!未定义书签。
5.4合金铸造性能分析 ................... 错误!未定义书签。
5.5 设计计算步骤....................... 错误!未定义书签。
5.6出气孔 (14)5.7铸件工艺出品率 (14)第六章.模拟仿真部分 (15)6.1充型模拟 (15)6.2凝固模拟 (15)第七章.结论及优化方案 (16)第八章.小结 (16)主要参考文献: (19)摘要本文通过对座体零件图的深入分析,根据零件的形状、尺寸、材料等特点,采用传统设计方法与计算机辅助设计相结合的方式对零件的铸造工艺进行设计。
分析并确定采用卧式造型合箱,底注式浇注的砂型铸造工艺方案;确定了铸铁件的凝固原则、浇注位置和分型面等;确定了座体铸铁件的铸造工艺参数并计算了其体积和重量;设计并计算了箱盖砂型铸造的浇注系统;绘制了座体砂型铸造工艺图、UGIII / 20铸件图、合箱图等;并采用华铸CAE模拟软件进行模拟分析。
整体得到了一套生产该灰铸铁箱盖的砂型铸造工艺文件。
关键词:座体;砂型铸造;工艺设计;模拟分析。
箱盖铸造工艺设计及其模拟优化第一章.零件简介1.1 零件基本信息零件名称:座体铸件。
零件材料:HT200。
产品生产纲领:单件小批量生产。
结构:属厚、薄均匀的小型座体。
根据相关资料查得HT200具体成分及其含量如表所示。
表1.1.1 HT200化学成分表(质量分数,%)CSi Mn P S Cr3.3~3.5 51.95~2.150.60~0.90≤0.08≤0.120.15~0.30表1.1.1 HT200材料的力学性能抗拉强度/MPa硬度/HB延伸率/%≥200170~241≥10座体零件图:图1-1 座体零件图 1.2技术要求5 / 20(1) 结构特点及使用要求该零件结构简单,壁厚均匀为10mm,座体外形整体较大长约255mm,宽190mm,高172.5mm。
材料为灰铁,流动性较较好,收缩大,所以在浇注时容易产生浇不足、冷隔、缩孔和缩松、热裂、内应力以及变形和冷裂等缺陷。
(铸件体积V=1791168.0543mm3 ,质量m=13.824kg。
(2) 铸件技术要求铸造圆角R3~R5;第二章.基于UG零件的三维造型2.1软件简介UG NX[2]是由Siemens PLM Software发布的集CAD/CAM/CAE 一体化解决方案软件,它涵盖了产品设计、工程和制造中的全套开发流程。
NX 产品开发解决方案完全支持制造商所需的各种工具。
NX 与 UGS PLM 的其他解决方案的完整套件无缝结合,这些对于 CAD 、 CAM 和 CAE 在可控环境下的协同、产品数据管理、数据转换、数字化实体模型和可视化都是一个补充。
本件采用UG NX进行三维立体建模使工艺设计直观形象,便于后续分析、模拟及加工等过程的管理与控制。
2.2 零件的三维造型图通过运用NX8.5对零件进行立体建模得到如图2-1所示三维图。
图2-1零件的三维造型图第三章. 铸造工艺方案的拟定3.1工艺方案的确定[1]座体材质为灰铸铁HT200,该铸件属于薄壁小型件,无需开设冒口,成品率高。
生产纲领为单件小批量生产可采用砂型铸造,铸型和型芯都采用呋喃树脂自硬砂,每箱一件,乙醇涂料,造型时按模型材质选择合适的脱模剂。
采用树脂砂的优点有:强度高,可自硬,精度高,铸件易清理,生产效率高等特点。
3.2型(芯)砂配比根据零件结构及生产要求,该铸件采用呋喃树脂自硬砂造型、造芯即可,具体数值参考型、芯砂配比如表3.1和表3.2所示。
表3.1 型砂配比(配比重量Wt%)成新砂再生F700呋喃树固化剂附加物氧化7 / 20表3.2芯砂配比(配比重量Wt%)表中催化剂含量为占树脂砂的百分比。
3.3混砂工艺合理地选用混砂机,采用正确的加料顺序和恰当的混砂时间有助于得到高质量的树脂砂。
树脂砂各种原料称量要准确,其混砂工艺如下:砂+出砂上述顺序不可颠倒,否则局部发生剧烈的硬化反应,缩短可使用时间,影响到树脂砂的使用性能。
砂和催化剂的混合时间应以催化剂能均匀的覆盖住沙粒表面所需的时间为准。
3.4 铸造用涂料、分型剂及胶补剂铸造涂料在铸型和砂芯的表面上形成耐火的保护层,避免铸件产生表面粗糙、机械粘砂、化学粘砂以及减少铸件产生与砂子有关的其它铸造缺陷,是改善铸件表面质量的重要手段之一。
虽然采用涂料增加了工序和费用,但使用涂料之后,不仅铸件表面光洁,也减少了缺陷降低了清理费用,增加了铸件在市场上的竞争力,综合效益得以提高。
为满足要求可选水溶性涂料,根据生产纲领选用手工刷涂的方式施涂。
铸造用分型剂可在造型造芯过程中在模样、芯盒工作表面覆盖一薄层可以减少或者防止型砂、芯砂对模样或芯盒的粘附,降低起模力,以便得到表面光洁、轮廓清晰的砂型或砂芯,可手工涂涂柴油。
如砂型或砂芯出现裂纹、孔洞、掉角以及不平整等缺陷可用胶补剂进行修补,以提升生产效率。
对自硬树脂砂可用同种自硬砂+修补膏+胶合剂进行修补。
3.5熔炼设备及熔炼工艺熔炼设备:为保证获得化学成分均匀、稳定且温度较高的铁液,满足生产需要这一前提,在大批量流水生产中,宜采用冲天炉-电炉双联熔炼工艺。
它可以保证出炉铁液温度在1500℃以上,温度波动范围小于等于+(-)10℃,化学成分(质量分数)精度达到△C小于等于+(-)0.05%,△Si小于等于+(-)0.10%。
9 / 20熔炼工艺:(1) 废钢加废钢可明显提高灰铸铁基体中D型石墨和初生奥氏体的数量;加废钢能促进初生奥氏体的形核及长大;可增加铸件的强度和孕育。
(2)出炉温度和浇注温度出炉温度一般都控制在1400~1450℃之内,浇注温度一般控制在1370~1440℃。
(3)孕育处理为改善石墨形态和材质的均匀性,孕育处理是十分重要的。
孕育的作用为消除白口、改善加工性能,细化共晶团、获得A型石墨,使石墨细化及分布均匀,改善基体组织、提高力学性能,减小断面敏感性。
综合孕育剂选择的主要两个因素:满足工艺性及性能、金相组织的需要;避免铸件产生气孔、缩松、渗漏等缺陷。
由于75SiFe瞬时孕育效果好,溶解性能优良,故此铸铁熔炼采用此方法。
第四章铸造工艺设计4.1、铸件零件图图4-1-1 铸件零件图4.2、分型面与浇注方式的确定4.2.1、分型面的选择该零件几何结构较为简单,采用底浇注式的方式浇注,既满足要求,又使得浇注系统的设计简化,充型平稳,减少夹渣、缩孔,有利于浮渣。
不需要再设计冒口,同时可以提高工艺出品率,合箱简单,非常适合单件、小批量的造型成型。
分型面选择如图4-2-1所示:图4-2-1 分型面的选择位置4.2.2、浇注位置的选择该零件大体轮廓属于环形构造,根据型芯情况,结合分型面的选择,决定采用底注式的浇注方式,浇注位置如图4-2-2所示。
11 / 20图4-2-2 铸件浇注位置4.2.3、主要的铸造工艺参数(1)铸件尺寸公差和重量公差该铸件材质为HT200,手工造型,经查得,铸件的尺寸公差等级为11级;重量公差等级为13级,该铸件的重量公差为24%[3]。
(2)机械加工余量该铸件为铸铁(HT200)件,砂型人工造型,经查加工余量等级为H,经查得,加工余量取7。
(3)铸造收缩率由于铸件的固态收缩(线收缩)将使铸件各部分尺寸小于模样原来的尺寸,因此,为了使铸件冷却后的尺寸与铸件图示尺寸一致,则需要在模样或芯盒上加上其收缩的尺寸。
加大的这部分尺寸为铸件的收缩量,一般用铸造收缩率表示。
经查可知该铸件的线收缩率为1.0%。
(4)不铸出孔因为采用的是单件小批量生产,零件图中的螺纹孔太小,需铸出孔要大于或等于30-50,所以该零件的孔都不能铸出,铸件图如图4-2-3所示:图4-2-3 铸件图三维图4.3、砂芯设计对于该零件有中空结构,因此需要在铸造时使用砂芯成型。
对于砂芯的要求,应具有足够的强度和刚度。
型芯设计和浇注系统放置如图4-3-1所示:如图4-3-1 型芯和浇注系统的位置4.4浇注系统设计13 / 204.4.1、浇注系统的选择原则该铸件为铸铁中小型铸件,壁厚均匀,根据铸铁件生产要求及特点,根据铸造工艺学表3-4-12选择封闭式(Ⅱ)浇注系统。
取∑S内:∑S横:∑S直=1:1.1:1.154.4.2 浇注系统的尺寸确定每个铸件质量13.824kg,共布置1件。
铸件出品率按30%估计,则型腔内金属质量为13.824/0.3=45.16kg。
(1)、确定浇注时间和浇注速度q=Bбpmn—浇注时间(S)m—铸件质量或浇注金属质量(kg)б—铸件壁厚(mm)查表计算可得浇注时间为15s(2)、计算内浇道截面积由公式:G—包括浇冒口在内的铸件总重量;一充填一个型腔的时间;一每个铸件的平均计算压力头,查表得到取值为30cm。
根据铸件情况,n取0.05经过上面公式计算和结合铸造工艺手册可得到内浇道最小总截面积约为61.2,所以取内浇道的截面积为60,一共两个内浇道,每个内浇道为30。
采用梯形断面内浇口主要考虑到是从铸件后凝固处引入,内浇口可以很好的起到补缩的作用。
采用a=h的体形尺寸,可得出内浇道截面尺寸如下表:表4-4-1 内浇道截面尺寸内浇道截面积()h(mm)a(mm) b (mm)3082428图4-4-1 内浇道界面形状(3)直浇道及横浇道尺寸该铸件属于中小型铸件,采用封闭式浇注系统,根据铸造工艺手册可得直、横、内浇道截面积比为1.15:1.1:1。
根据浇注质量为45.16Kg可得直浇道总截面积为50-60,所以取直浇道截面积为25。