如何提高压铸模具寿命
如何提高压铸模的使用寿命
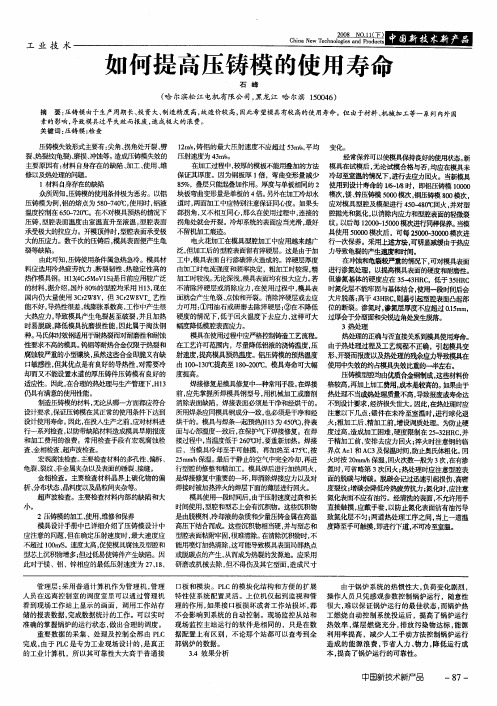
在加工过程中, 较厚的模板不能用叠加的方法 模具在试 模后 , 无论试模合格与否 , 均应在曲变形量减少 倍 8%,叠层只能起叠加作用。厚度与单板相同的 2 5 块板弯曲变形量是单板的 4 另外在加工冷却水 倍。 道时 , 两面加工中应特别注意保证同心度。如果头 部拐角 , 又不相互同心 , 那么在使用过程中, 连接的 拐角处就会开裂。冷却系统的表面应 当 光滑 , 最好
不留机加工痕迹。
具使用 500 00 模次后,可每2o0 oo 5o o0 模次进
电火花加工在模具型腔加工中应用越来越广 行—次保养。采用 匕 述方法, 可明显减缓由于热应 泛, 但加工后的型腔表面留有淬硬层。这是由于加 力导致龟裂的 产生速度和时间。 工中, 模具表面 自 行渗碳淬火造成的。淬硬层厚度 在冲蚀和龟裂较严重的情况下 , 可对模具表面 由加工时电流强度和频率决定, 粗加工时较深 , 精 进行渗氮处理 ,以提高模具表面的硬度和耐磨性。 加工时较浅。 无论深浅, 模具表面均有极大应力。 若 但渗氮基体的硬度应在 3- 3 R ,低于 3 H C 54H C 5 R 不清除淬硬层或消除应力 , 在使用过程 中, 模具表 时氮化层不能牢 固与基体结合。 使用—段时间后会 面就会产生龟裂、 点蚀和开裂。消除淬硬层或去应 大片脱落 : 4 H C则易引起型腔表面凸起部 高于 3 R . 力可用 : ①用油石或研磨去除淬硬层; ②在不降低 位的断裂。渗氮时, 渗氮层厚度不应超过 05 m .m 。 1 硬度的情况下 , 低于回火温度下去应力 , 这样可大 幅度降低模腔表面应力。 3热 处理 模具在使用过程中 应严格控制铸造工艺流程。 在工艺许可范围内,尽量降低铝液的浇铸温度, 压 射速度 , 提高模具预热温度。铝压铸模的预热温度 由 101O 0-3℃提高至 1020 ,模具寿命可大幅 8 0 ̄ - C 度提高。 焊接修复是摸具修复中一种常用手段。 在焊接 前, 应先掌握所焊模具钢型号 , 用机械加工或磨削 消除表面缺陷,焊接表面必须是干净和经烘干的。 所用焊条应同模具钢成分一致 , 也必须是干净和经 烘干的。模具与焊条一起预热 1 为 4 00 待表 3 5z , 面与心部温度一致后 , 在保护气下焊接修复。在焊 接过程中, 当温度低于 2 O 6℃时, 要重新加热 。焊接 后 ,当模具冷却至手可触摸 , 再加热至 4 5 按 7 ℃, 2 nn 保温 。 5u / h 最后于静止的空气中完全冷却 , 再进 行型腔的修整和精加工。模具焊后进行加热 回 , 火 是焊接修复中重要 的一环 , 即消除焊接应力以及对
压铸模具热处理工艺流程

压铸模具热处理工艺流程压铸模具热处理工艺流程是指对压铸模具进行加热处理,以改善其组织结构和性能,并提高其使用寿命和耐磨性。
热处理工艺流程主要包括退火、正火和淬火等步骤。
首先是退火工艺。
退火是为了消除模具加工过程中的应力,使模具表面平整,提高模具的硬度和韧性。
退火工艺有两种方式,分别是工艺退火和全退火。
工艺退火是将模具加热至一定温度,保持一定时间,然后冷却。
全退火是将模具加热至临界温度,保持一段时间,然后缓慢冷却至室温。
接下来是正火工艺。
正火是指将退火后的模具再次加热至一定温度,并持续一段时间,然后快速冷却。
正火可以提高模具的硬度和耐磨性,使其能够承受较大的压力。
正火的温度和保持时间根据具体模具的材料和要求进行确定。
最后是淬火工艺。
淬火是指将模具加热至高温,然后迅速冷却,使模具的组织结构发生相变,从而提高模具的硬度和强度。
淬火温度和冷却速度根据具体模具的材料和要求进行确定。
常用的淬火介质有水、油和盐浴等。
在进行热处理工艺流程时,还需要注意以下几个方面。
首先是控制加热温度和保持时间,保证模具能够达到所需的组织结构和性能要求。
其次是选择合适的冷却介质和冷却速度,以保证模具的硬度和强度。
同时,还需要进行适当的淬火后处理,如回火、沉淀硬化等,以消除淬火应力和提高模具的韧性和强度。
总之,压铸模具热处理工艺流程是一个复杂而关键的工艺过程,它直接影响到模具的使用寿命和耐磨性。
通过合理选择退火、正火和淬火等工艺步骤,控制加热温度和保持时间,以及进行适当的淬火后处理,可以有效提高模具的性能,减少模具的变形和磨损,从而提高模具的使用寿命。
压铸模具的失效形式及提高其使用寿命的途径
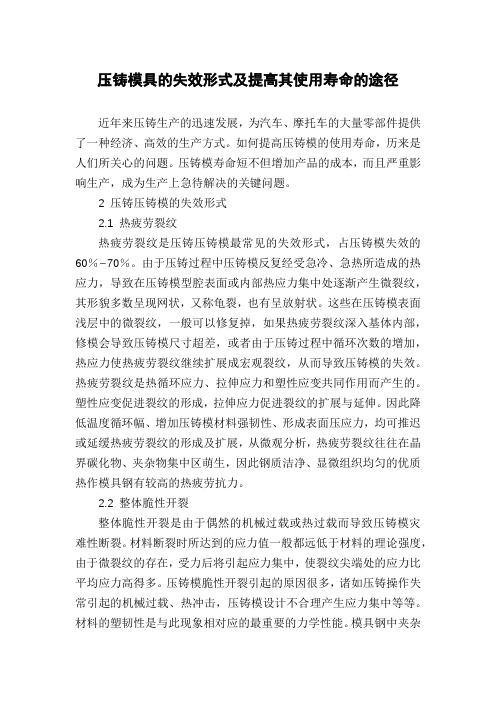
压铸模具的失效形式及提高其使用寿命的途径近年来压铸生产的迅速发展,为汽车、摩托车的大量零部件提供了一种经济、高效的生产方式。
如何提高压铸模的使用寿命,历来是人们所关心的问题。
压铸模寿命短不但增加产品的成本,而且严重影响生产,成为生产上急待解决的关键问题。
2 压铸压铸模的失效形式2.1 热疲劳裂纹热疲劳裂纹是压铸压铸模最常见的失效形式,占压铸模失效的60%~70%。
由于压铸过程中压铸模反复经受急冷、急热所造成的热应力,导致在压铸模型腔表面或内部热应力集中处逐渐产生微裂纹,其形貌多数呈现网状,又称龟裂,也有呈放射状。
这些在压铸模表面浅层中的微裂纹,一般可以修复掉,如果热疲劳裂纹深入基体内部,修模会导致压铸模尺寸超差,或者由于压铸过程中循环次数的增加,热应力使热疲劳裂纹继续扩展成宏观裂纹,从而导致压铸模的失效。
热疲劳裂纹是热循环应力、拉伸应力和塑性应变共同作用而产生的。
塑性应变促进裂纹的形成,拉伸应力促进裂纹的扩展与延伸。
因此降低温度循环幅、增加压铸模材料强韧性、形成表面压应力,均可推迟或延缓热疲劳裂纹的形成及扩展,从微观分析,热疲劳裂纹往往在晶界碳化物、夹杂物集中区萌生,因此钢质洁净、显微组织均匀的优质热作模具钢有较高的热疲劳抗力。
2.2 整体脆性开裂整体脆性开裂是由于偶然的机械过载或热过载而导致压铸模灾难性断裂。
材料断裂时所达到的应力值一般都远低于材料的理论强度,由于微裂纹的存在,受力后将引起应力集中,使裂纹尖端处的应力比平均应力高得多。
压铸模脆性开裂引起的原因很多,诸如压铸操作失常引起的机械过载、热冲击,压铸模设计不合理产生应力集中等等。
材料的塑韧性是与此现象相对应的最重要的力学性能。
模具钢中夹杂物的减少,韧性将明显提高。
在实际生产中,整体脆断的情况较少发生。
2.3 溶蚀或冲蚀熔融的金属液以高压、高速进入型腔,对压铸模成形零件的表面产生激烈的冲击和冲刷,造成型腔表面的机械冲蚀,高温使压铸模硬度下降,导致型腔软化,产生塑性变形和早期磨损。
提高压铸模具寿命—细节决定成败
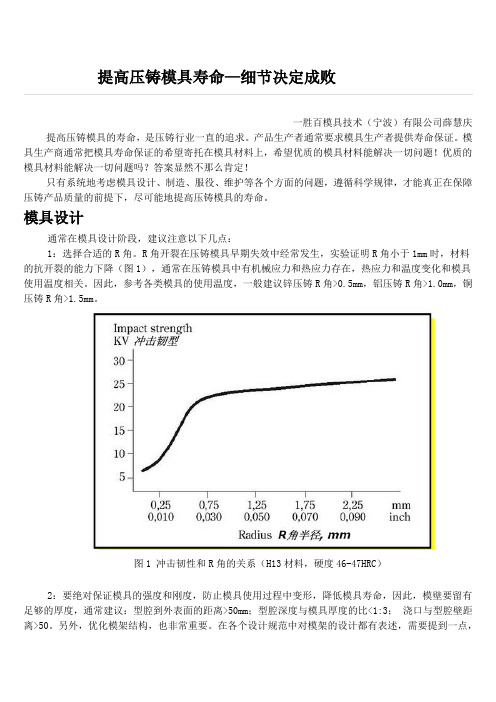
提高压铸模具寿命—细节决定成败一胜百模具技术(宁波)有限公司薛慧庆提高压铸模具的寿命,是压铸行业一直的追求。
产品生产者通常要求模具生产者提供寿命保证。
模具生产商通常把模具寿命保证的希望寄托在模具材料上,希望优质的模具材料能解决一切问题!优质的模具材料能解决一切问题吗?答案显然不那么肯定!只有系统地考虑模具设计、制造、服役、维护等各个方面的问题,遵循科学规律,才能真正在保障压铸产品质量的前提下,尽可能地提高压铸模具的寿命。
模具设计通常在模具设计阶段,建议注意以下几点:1:选择合适的R角。
R角开裂在压铸模具早期失效中经常发生,实验证明R角小于1mm时,材料的抗开裂的能力下降(图1),通常在压铸模具中有机械应力和热应力存在,热应力和温度变化和模具使用温度相关。
因此,参考各类模具的使用温度,一般建议锌压铸R角>0.5mm,铝压铸R角>1.0mm,铜压铸R角>1.5mm。
图1 冲击韧性和R角的关系(H13材料,硬度46-47HRC)2:要绝对保证模具的强度和刚度,防止模具使用过程中变形,降低模具寿命,因此,模壁要留有足够的厚度,通常建议:型腔到外表面的距离>50mm;型腔深度与模具厚度的比<1:3;浇口与型腔壁距离>50。
另外,优化模架结构,也非常重要。
在各个设计规范中对模架的设计都有表述,需要提到一点,对于长寿命模具,使用预硬钢(如ASTM 4140、4340(对应GB 42CrMo、40CrNiMoA),ASSAB 718 )能有效提高模架的抗压塌性能。
3:采用镶件,对于易损坏或强度较少的部分分开成为下镶块,并且对于长寿模具建议推杆孔采用镶套。
4:浇口要远离型腔壁,型芯,镶块。
5:要在型腔面和冷却水道之间留有足够的距离,较短的距离会加大由于温度剧烈变化导致的热应力,过大的距离则没有冷却效果(参见图二)。
水孔壁离型腔一般建议为25mm,浇口处为28mm;角部型腔面距冷却水道的距离>50mm。
提高模具使用寿命的实用方法

③ 点火化表面强化:这是一种直接利用电能的高能量密度 对模具表面进行强化处理的工艺。它是通过火花放电的作 用,把作为电极的导电材料溶渗进金属工件表层,从而形 成合金化的表面强化层,使工作表面的物理、化学性能和 机械性能得到改善。例如采用WC、TiC等硬质合金电极材 料强化高速钢或合金工具钢表面,可形成显微硬度HV11 00以上的耐磨、耐蚀和具有红硬性的强化层,使模具的 使用寿命明显得到提高。点火花表面强化的优点是设备简 单、操作方便,处理后的模具耐磨性提高显著;缺点是强 化表面较粗糙,强化层厚度较薄,强化处理的效率低。
计小孔凸模时采用自身导向结构,可延长模具寿命。 ② 对夹角、窄槽等薄弱部位,为了减少应力集中,要以
圆弧过渡,圆弧半径R可取3~5mm。 ③ 对于结构复杂的凹模采用镶拼结构,也可减少应力集
中。和推件力下降,凸、凹模刃口磨损减少。
⑥ CVD法(化学气相沉积):将模具放在氢气(或 其它保护气体)中加热至900℃~1200℃后, 以其为载气,把低温气化挥发金属的化合物气体如 四氯化钛(TiCI4)和甲苯CH4(或其它碳氢化合物) 蒸气带入炉中,使TiCI4中的钛和碳氢化合物中的碳 (以及钢表面的碳分)在模具表面进行化学反应, 从而生成一层所需金属化合物涂层(如碳化钛)。
① 气体软氮化:使氮在氮化温度分解后产生活性氮原子, 被金属表面吸收渗入钢中并且不断自表面向内扩散,形成 氮化层。模具经氮化处理后,表面硬度可达HV950~1 200,使模具具有很高的红硬度和高的疲劳强度,并提 高模具表面光洁的度和抗咬合能力。
② 离子氮化:将待处理的模具放在真空容器中,充以一 定压力的含氮气体(如氮或氮、氢混合气),然后以被处 理模具作阴极,以真空容器的罩壁作阳极,在阴阳极之间 加400~600伏的直流电压,阴阳极间便产生辉光放 电,容器里的气体被电离,在空间产生大量的电子与离子。 在电场的作用下,正离子冲向阴极,以很高速度轰击模具 表面,将模具加热。离能正离子冲入模具表面,获得电子, 变成氮原子被模具表面吸收,并向内扩散形成氮化层。应 用离子氮化法可提高模具的耐磨性和疲劳强度。
压铸模具保养

保养周期与保养计划的制定
定期检查
根据模具的使用情况和材质,制 定合理的保养周期,定期对模具
进行检查和维护。
预防性保养
采取预防性保养措施,如定期润滑 、清洁和防锈等,以延长模具的使 用寿命。
保养计划
制定详细的保养计划,包括保养项 目、时间、人员和工具等,确保保 养工作的顺利进行。
保持模具存放环境的干燥和清洁 ,防止锈蚀和氧化,延长模具的
使用寿命。
保证产品质量
良好的模具保养可以保证压铸件尺寸的稳定性和精度,减少产品缺陷和不良率。
定期清理模具内的残留物和杂质,避免对产品表面和内部质量的影响。
保养过程中对模具进行检测和调整,确保模具处于良好的工作状态,提高产品的合 格率。
降低生产成本
模具维修与更换
总结词
模具维修是指对损坏或磨损的部位进行修复,而模具更换则是指整副模具的替换。
详细描述
对于损坏或磨损的部位,应根据实际情况进行维修或更换。在维修过程中,应遵循正确的工艺流程,确保维修质 量。如无法修复或修复成本过高,则需考虑整副模具的更换。在更换模具时,应选择质量可靠、性能稳定的模具 ,以确保生产效率和产品质量。
详细描述
在生产过程中,应控制模具温度,避免长时间的高温状态。 同时,要确保模具在使用过程中不受外力冲击,保持稳定的 生产环境。发现裂纹后,应及时停止使用,进行修复或更换 。
模具变形
总结词
模具变形通常是由于热处理不当或使用过程中受力不均所导致的。
详细描述
在进行热处理时,应遵循正确的工艺流程,确保热处理质量。在使用过程中, 要确保受力均匀,避免局部受力过大的情况。如发现模具变形,可采用适当的 矫形工艺进行修复。
一般压铸模具的寿命
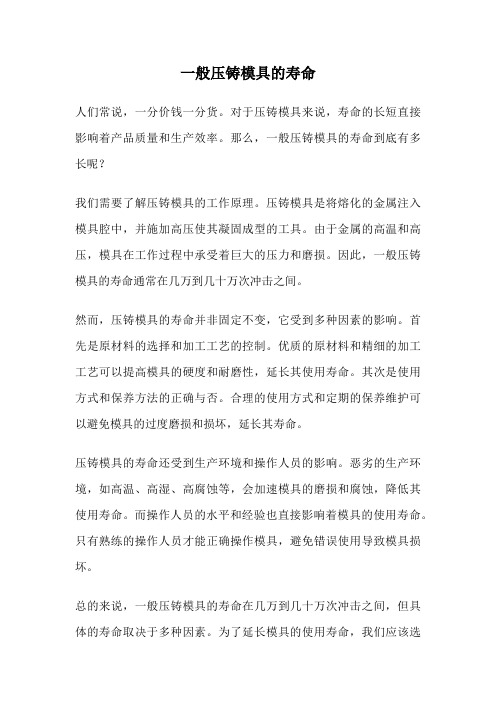
一般压铸模具的寿命
人们常说,一分价钱一分货。
对于压铸模具来说,寿命的长短直接影响着产品质量和生产效率。
那么,一般压铸模具的寿命到底有多长呢?
我们需要了解压铸模具的工作原理。
压铸模具是将熔化的金属注入模具腔中,并施加高压使其凝固成型的工具。
由于金属的高温和高压,模具在工作过程中承受着巨大的压力和磨损。
因此,一般压铸模具的寿命通常在几万到几十万次冲击之间。
然而,压铸模具的寿命并非固定不变,它受到多种因素的影响。
首先是原材料的选择和加工工艺的控制。
优质的原材料和精细的加工工艺可以提高模具的硬度和耐磨性,延长其使用寿命。
其次是使用方式和保养方法的正确与否。
合理的使用方式和定期的保养维护可以避免模具的过度磨损和损坏,延长其寿命。
压铸模具的寿命还受到生产环境和操作人员的影响。
恶劣的生产环境,如高温、高湿、高腐蚀等,会加速模具的磨损和腐蚀,降低其使用寿命。
而操作人员的水平和经验也直接影响着模具的使用寿命。
只有熟练的操作人员才能正确操作模具,避免错误使用导致模具损坏。
总的来说,一般压铸模具的寿命在几万到几十万次冲击之间,但具体的寿命取决于多种因素。
为了延长模具的使用寿命,我们应该选
择优质的原材料,精细加工,合理使用模具,定期进行保养维护,并提高操作人员的技术水平。
压铸模具是现代工业生产中不可或缺的工具,其寿命的长短直接关系到产品质量和生产效率。
只有合理使用和保养模具,才能延长其寿命,提高生产效率,为企业带来更多的利益。
让我们共同努力,为压铸模具的寿命增添更多的光彩!。
压铸模的保养对提高模具使用寿命的影响
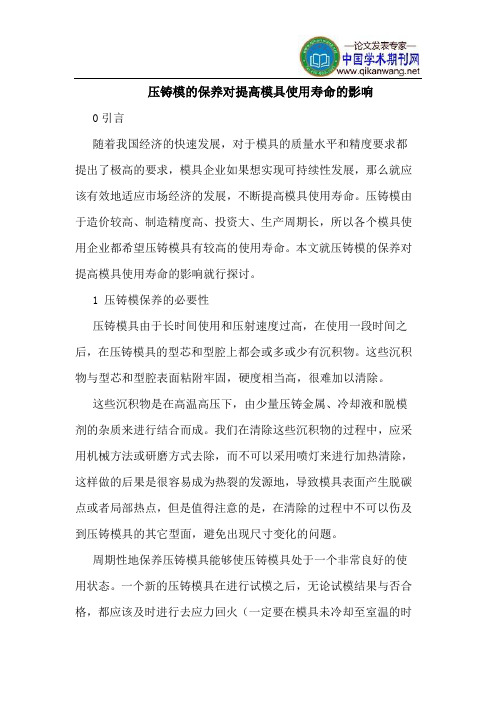
压铸模的保养对提高模具使用寿命的影响0引言随着我国经济的快速发展,对于模具的质量水平和精度要求都提出了极高的要求,模具企业如果想实现可持续性发展,那么就应该有效地适应市场经济的发展,不断提高模具使用寿命。
压铸模由于造价较高、制造精度高、投资大、生产周期长,所以各个模具使用企业都希望压铸模具有较高的使用寿命。
本文就压铸模的保养对提高模具使用寿命的影响就行探讨。
1 压铸模保养的必要性压铸模具由于长时间使用和压射速度过高,在使用一段时间之后,在压铸模具的型芯和型腔上都会或多或少有沉积物。
这些沉积物与型芯和型腔表面粘附牢固,硬度相当高,很难加以清除。
这些沉积物是在高温高压下,由少量压铸金属、冷却液和脱模剂的杂质来进行结合而成。
我们在清除这些沉积物的过程中,应采用机械方法或研磨方式去除,而不可以采用喷灯来进行加热清除,这样做的后果是很容易成为热裂的发源地,导致模具表面产生脱碳点或者局部热点,但是值得注意的是,在清除的过程中不可以伤及到压铸模具的其它型面,避免出现尺寸变化的问题。
周期性地保养压铸模具能够使压铸模具处于一个非常良好的使用状态。
一个新的压铸模具在进行试模之后,无论试模结果与否合格,都应该及时进行去应力回火(一定要在模具未冷却至室温的时候)。
在进行压铸模10 000模次之后,就应该消除型腔表面中的轻微裂纹和残余内应力,对模架和模具型腔进行回火、氮化、抛光,温度设置在450℃~480℃。
同样保养应该在以后压铸模每进行12 000~15 000模次后进行。
如果压铸模具在使用50 000模次之后,可以延长保养时间,可以在每25 000~30 000模次进行一次。
总之,压铸模保养十分必要,能够有效减缓模具龟裂的产生时间和延伸速度,提高模具使用寿命。
2 如何加强压铸模的保养来提高模具使用寿命2.1建立模具档案,做好准备第一,给每一套模具在入厂时建立一套完整的使用记录,这是保证以后保养和维护的一个重要依据,每一条都要做得细致,清晰,包括每日的生产模次在内;第二,作为一名模具管理人员,模具自入厂以后,模具每一部分的结构配件必须要详细记入模具档案里,并且要根据需要,把模具内的易损部分列出,提前准备配件,比如顶杆,型芯等。
- 1、下载文档前请自行甄别文档内容的完整性,平台不提供额外的编辑、内容补充、找答案等附加服务。
- 2、"仅部分预览"的文档,不可在线预览部分如存在完整性等问题,可反馈申请退款(可完整预览的文档不适用该条件!)。
- 3、如文档侵犯您的权益,请联系客服反馈,我们会尽快为您处理(人工客服工作时间:9:00-18:30)。
oC 400 500 600 700 800 900 1000 1100
不要过长时间的喷脱模剂
脱模剂的作用 : ? 减少黏结 ? 减少磨损 ? 容易清理模具 ? 延长模具维修之间的时间 有些脱模剂减少模具寿命 by: ? 与模具钢材发生反应 ? 使压铸金属黏结在模具表面 .
采用间歇喷脱模剂的方法
用正确的方法冷却模具
选择合适的圆角半径
冲击韧型
ft. - lbs.
25
20
15
10
5
0
0.5
1.0
1.5
R角半径, mm
Fillet Radii
Zinc
Aluminum
>0.5 mm >1.0 mm
2.0
Brass >1.5 mm
采用镶件
浇口要远离型腔壁,型芯,镶块
增加侵蚀和龟裂风险。
减少侵蚀和龟裂风险。
要在型腔面和冷却水道之间留有足够的距离
100-150 °C 150-200 °C 180-300 °C 180-300 °C 300-350 °C
100 200 300 400 500 °C
可以采用气体火焰或电加热器进行 加热。
在开始阶段降低活塞速度 开始的 5-10 次采用比较低的注入速度
不要采用过高的注入速度
注入速度不要高于 55m/s (180feet/s) ,过高的注入速度会 加剧侵蚀.
? 如果用水冷却,预热水温到 50°C.
? 在压铸间隙停机时,减少脱模剂喷涂量, 这样可以避免模温降的太低。 ? 在模具热的时候不要打开冷却水.
在模具使用过程中保证在使用一段时间后进行去应力处 理
去应力处理可以降低模具残余应力, 延长模具寿命。
去应力处理 , 当: ? running-in period ? 1000 – 2000 shots ? 5000 – 10,000 shots ? 每 10,000 – 20,000 shots.
4
3 24 4 6.4 12.8 12.5
5
4
5
18
9
1
0.5
3.2
1.63.23.2 Nhomakorabea5
4
避免表面过度抛光
低抛光表面: ? 喷砂表面 ? 氧化表面 ? 220-600 砂纸打磨表面
优点: ? 脱模剂粘附比较好并且分布
均匀 ? 减少粘结,容易脱模
镜面表面容易造成黏结 (Al 与 Fe之间), 黏 结造成模具表面针孔。
型腔表面氧化
材料损失 (mg/cm 2)
800 700
Aluminium 732°C
600 500 400
Zinc 499°C
300
200
100
0 Zn 500C
AL 735C
没有氧化表面 氧化表面 499°C in air for 2h
Brass 954°C
Cu 950C
如果进行氮化处理,避免过厚的氮化层
型腔到外表面的距离>2英寸(50mm) 型腔深度与模具厚度的比<1:3 型腔距冷却水道的距离>1英寸(25mm) 型腔面距冷却水道的距离>1英寸(25mm) 角部型腔面距冷却水道的距离>2英寸(50mm) 圆角半径 锌合金 铝合金 铜合金
>0.02英寸 >0.04英寸 >0.06英寸 (0.05mm) (1mm) (1.5mm) 浇口距型腔面的距离>2 英寸(50mm)
采用推荐的模具加工流程
1. 粗加工 2. 去应力回火 3. 半精加工 4. 热处理 5. 精加工/EDM加工 6. 去应力回火/ 氧化 / 表面处理
避免在型腔表面残留 EDM白层
热处理后钢材的EDM加工
A. 传统机加工. B. 热处理. C. 粗 EDM加工, 避免“打火”和过大的金属去
除速度。 用低电流,高频率进行精EDM加 工。 D. (i) 打磨和抛光去除 EDM层. (ii) 用低于前面回火温度 25°C 的温度进行 去应力回火。
镶块 型芯 滑块
推荐氮化层厚度
max. 0.05 mm max. 0.13 mm max. 0.30 mm
过厚的氮化层会在分型面和尖角部位脱落,造成铸件在脱模时划伤
氮化和碳氮共渗
处理过程
气体氮化 at 510 °C
离子氮化 * at 470 °C 气体碳氮共渗 at 580 °C
在盐浴中碳氮共渗
时间 h 10 30 60 10 30 60
EDM 参数对 EDM白层的影响
8407 S, 1030 C+590 C/2x2 hr, 50-51 HRC, 400x
1
2
3
样品号
1
2
VDI no
42
33
峰值电流, IP (A)
32
12
脉冲时间 (us)
80
100
间歇时间 (us)
200
50
白层深度 (um)
40
20
EDM machine: Agie Charmilles
** 52% N 2, 43% NH 3, 5% CO 2
采用正确的方法将模具预热到足够高的温度
Preheating Range
DIEVAR
8407 SUPREME
QRO 90 SUPREME
根据压铸合金种类选择合适的预热温度, 一般在150 和 350 °C之间。
推荐预热温度:
? Tin, Lead alloys ? Zinc alloys ? Magnesium alloys ? Aluminum alloys ? Copper alloys
以低于先前最高回火温度 25°C的 温度进行去应力回火,保温: 2h
2.5
氮化层深度 , mm.
8407
QRO 90
DIEVAR SUPREME SUPREME
0.16
0.12
0.16
0.22
0.20
0.27
0.26
0.15
0.12
0.18
0.24
0.18 00.27
0.13
0.11
0.20
at 590 °C
1
0.08
0.006
0.13
* 25% N 2, 75% H 2
在保证压铸质量的前提下,尽量降低金属液温度
侵蚀 /腐蚀程度
腐蚀增加的临界温度:
? Zinc ? Aluminium
~480oC ~720oC
铜合金没有明显的临界温度, 但随温度的增加侵蚀 加剧.
Zn
Al
Brass
Not
Not
Not
recommended recommended recommended
模壁要有足够的厚度
B = ~3 x A C = f (machine size) D = 1.2 x C E = 2xB
Machine size C
(tons) 5-160 200-400 500-630 800-2000
(mm) 35 - 65 65 - 90 90 - 110 110 –150
模壁厚度参考尺寸: