04X射线检测工艺守则
射线检测标准及工艺技术要求及说明

射线检测标准及工艺技术要求及说明一、射线检测标准射线检测的标准是确保检测结果准确性和可靠性的重要依据。
常见的射线检测标准包括国际标准(如 ISO 标准)、国家标准(如 GB 标准)以及行业标准。
这些标准通常涵盖了以下方面:1、检测设备的性能要求:包括射线源的能量、焦点尺寸、辐射剂量等参数的规定,以保证检测设备能够提供足够的穿透能力和清晰度。
2、检测技术的分类和适用范围:例如,根据被检测物体的材质、厚度、形状等因素,确定适合的射线检测技术,如 X 射线检测、γ射线检测等。
3、图像质量要求:规定了检测图像的对比度、清晰度、不清晰度等指标,以确保能够清晰地显示缺陷。
4、缺陷评定标准:明确了不同类型和尺寸的缺陷的评定方法和验收标准,以便对检测结果进行准确判断。
二、射线检测工艺技术要求(一)射线源的选择射线源的选择取决于被检测物体的材质、厚度和检测要求。
一般来说,X 射线适用于较薄的物体和对图像质量要求较高的检测,而γ射线则适用于较厚的物体和野外检测等场合。
(二)胶片的选择胶片的性能对检测结果的质量有重要影响。
应根据射线源的能量、被检测物体的材质和厚度等因素选择合适类型和感光度的胶片。
(三)曝光参数的确定曝光参数包括管电压、管电流、曝光时间等。
这些参数的选择需要综合考虑被检测物体的厚度、材质、射线源的强度以及胶片的特性,以获得最佳的检测图像。
(四)散射线的控制散射线会降低检测图像的质量,因此需要采取有效的措施进行控制。
常见的方法包括使用铅屏、滤波板、背散射防护等。
(五)像质计的使用像质计用于评估检测图像的质量和灵敏度。
应根据标准要求选择合适类型和规格的像质计,并正确放置在被检测物体上。
(六)标记与标识在检测过程中,需要对被检测物体进行清晰的标记和标识,包括工件编号、检测部位、透照方向等信息,以便于对检测结果进行追溯和分析。
三、射线检测工艺技术说明(一)检测前的准备工作在进行射线检测之前,需要对被检测物体进行表面处理,去除污垢、氧化皮、油漆等可能影响检测结果的物质。
射线检测工艺守则

射线检测工艺守则1、主题内容适用范围1.1本守则适用不锈钢材料制压力容器焊缝及钢管对接环缝的射线透照检测。
1.2本规程适用于2-250mm板厚的碳素钢、低合金钢、不锈钢压力容器对接焊缝射线检测;适用于管壁厚大于或等于2mm的碳素钢、低合金和不锈钢管焊缝射线检测;适用于壁厚小于或等80mm的铝及铝合金焊缝射线探伤,适用于壁厚小于50mm的钛及钛合金焊缝射线检测。
1.3透照等级采用AB级2、防护2.1射线对人体有不良影响,应尽量避免射线的直接照射和散射线的影响;2.2放射防护应符合《放射性同位素与射线装置放射防护条例》第十一条规定;2.3射线曝光室应获得辐射安全许可证,方可启用;2.4室外射线检测,检测人员须穿防护服、佩戴个人计量仪,设立警戒区,并有明确的警告标志;2.5射线检测人员应每年到指定医院进行体检。
3、检测人员3.1应符合总则4.1条的有关规定。
3.2射线探伤的拍片操作应由已取得RT-Ⅰ级或Ⅰ级以上资格证书的人员担任,而评片(初评)由取得RT-Ⅱ级或Ⅱ级以上资格证书的人员担任,复评、签发和审核报告(与初评不得为同一个人),必须由无损检测责任人负责。
无证人员不得独立从事无损检测的工作。
4、表面要求4.1焊缝的表面质量应符合NB/T47013.2-2015标准中5.3的要求。
4.2焊缝的表面质量具体要求如下:在射线检测之前,焊接接头的表面应经目视检测并合格。
表面的不规则状态在底片上的影像不得掩盖或干扰缺陷影像,否则应对表面作适当修整。
4.3对有裂纹倾向的材料至少应在焊后24小时进行探伤。
如果产品技术文件有要求,以产品技术文件为准。
5、射线源、胶片、增感屏5.1射线源和能量的选择应按工件要求、透照方式和器材条件来决定,但最终要满足AB级透照质量要求。
5.2为提高底片的对比度,应尽可能选用能量较低的射线,但如果焊缝余高或厚度差较大,为使焊缝有效透照区两端及中心热影响区的黑度均在规定范围内,也可适当提高射线的能量。
x光机作业指导书

1..根据JJG744---2004《医用诊断X射线辐射源检定规程》要求,将剂量仪的电离室放在距X射线管焦点距离30cm处X射线照射野的中心, 选择最大的照射野,电离室的中心轴与射线束垂直。
2等候15分钟使剂量仪主机充分预热,选择测量时间(通常情况下选择5s~10s). 3将X射线机调整到规程要求的工作条件(医用诊断透视机管电压调至70kV,无影像增强器的管电流调至3 mA,有影像增强器的管电流调至1 mA)。
4主机在复位状态下按启动键开始测量,此时显示窗中计时器部分开始计时,剂量部分显示积分剂量。
5测量时间到时,积分剂量的测量结果和时间均停止变化并保留在显示窗上。
6在上述规定条件下,连续测量3次以上,取其平均值,按下面公式计算空气比释动能率=8.76 KTPNK,单位是mGymin-1.式中:8.76 ---伦琴R与mGy的换算关系----诊断水平剂量计测量三次以上的平均示值,单位R/(5s~10s)KTP----电离室温度、气压密度修正。
NK----电离室空气比释动能率的校准因子,上级校准证书给出。
7.用贝塞尔公式计算出辐射输出的重复性V.8改变辐照时间、X射线管的电流或电流时间积(mAs)任意连续两档,加载因素的预选值之比≤2.9.每点测量3次以上,取其平均值,用线性公式求出辐射输出性L。
辐射输出的质(半值层吸收片)的测量1将电离室置于规程中规定的距X射线管焦点的相应距离(40cm~60cm)。
2.X射线机管电压、管电流(电流时间积)调至规程规定的工作条件,.测量未加吸收铝片的照射量率。
3.将吸收铝片盒置于射线束与电离室之间(一般为中间),让射线束轴心与吸收片盒平面上圆窗的圆心重合,并使吸收片盒平面与射线束垂直。
4.在吸收片盒内加不同厚度的铝片,测量射线束通过不同厚度铝片的照射量率。
5.用计算器的回归计算功能求出照射量率降至初始(无吸收片)一半的铝片厚度,即为有用射线束的半值层厚度值(HVL)。
射线检测通用工艺守则

射线检测通用工艺守则1.主题内容及适用范围本守则规定了起重设备X射线检测的人员资格、设备器材、检测工艺和技术、底片质量和结果评定的要求。
本守则适用于碳素钢、低合金钢和不锈钢的名义厚度2~40mm的起重设备全熔化焊对接接头的X射线检测技术和质量分级要求。
2.引用标准GB/T3323—2005 金属熔化焊焊接接头射线照相GB/T19384.2~2003 工业射线照相胶片第二部分:用参考值方法控制胶片处理GB/T16375—1996 工业X射线探伤放射卫生防护标准JB/T7902—1999 线型象质计HB7684—2000 射线照相用线型象质计JB/T7903—1999 工业X射线照相底片观片灯3.射线检测人员要求3.1从事射线检测的人员应按照《特种设备无损检测人员考核与监督管理规则》的要求取得射线检测资格证书,评片人员必须持有中级制格证书。
3.2从事射线检测人员上岗前应进行辐射安全知识的培训,并取得放射工作人员证。
3.3射线检测人员必须身体健康,经体检合格,评片人员视力应每年检查一次。
未经矫正或经矫正的近(距)视力和远(距)视力应不低于 5.0(小数记录值为 1.0)3.4射线检测人员应能熟练操作射线机,正确选用透照工艺,合理使用暗室处理方法,并应熟悉焊接工艺、金属材料等知识。
4.检测设备、器材和材料4.1检测设备4.1.1本工艺采用XXQ2505和XXQ3005等型号的X射线探伤机。
4.1.2X射线照相应尽量选用较低的管电压。
在采用较高管电压时,应保证适当的曝光量,不同透照厚度允许采用的最高管电压应符合GB/T3323—2005的规定。
4.1.3对截面厚度变化大的工件透照时,在保证灵敏度要求的前提下,允许采用超过图20的X射线管电压,但其增量不应超过50KV。
4.2射线胶片4.2.1AB级射线检测技术应采用T3或更高类别的胶片。
胶片的本底灰雾度应不大于0.3。
4.2.2使用的胶片应取得胶片制造商的胶片主要特性指标和预先曝光的胶片测试片。
04X射线检测工艺守则
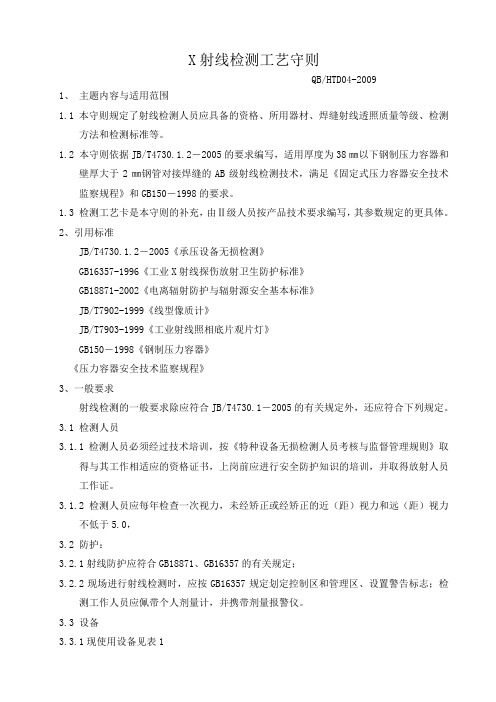
X射线检测工艺守则QB/HTD04-20091、主题内容与适用范围1.1本守则规定了射线检测人员应具备的资格、所用器材、焊缝射线透照质量等级、检测方法和检测标准等。
1.2 本守则依据JB/T4730.1.2-2005的要求编写,适用厚度为38㎜以下钢制压力容器和壁厚大于2㎜钢管对接焊缝的AB级射线检测技术,满足《固定式压力容器安全技术监察规程》和GB150-1998的要求。
1.3 检测工艺卡是本守则的补充,由Ⅱ级人员按产品技术要求编写,其参数规定的更具体。
2、引用标准JB/T4730.1.2-2005《承压设备无损检测》GB16357-1996《工业X射线探伤放射卫生防护标准》GB18871-2002《电离辐射防护与辐射源安全基本标准》JB/T7902-1999《线型像质计》JB/T7903-1999《工业射线照相底片观片灯》GB150-1998《钢制压力容器》《压力容器安全技术监察规程》3、一般要求射线检测的一般要求除应符合JB/T4730.1-2005的有关规定外,还应符合下列规定。
3.1 检测人员3.1.1检测人员必须经过技术培训,按《特种设备无损检测人员考核与监督管理规则》取得与其工作相适应的资格证书,上岗前应进行安全防护知识的培训,并取得放射人员工作证。
3.1.2 检测人员应每年检查一次视力,未经矫正或经矫正的近(距)视力和远(距)视力不低于5.0,3.2 防护:3.2.1射线防护应符合GB18871、GB16357的有关规定;3.2.2现场进行射线检测时,应按GB16357规定划定控制区和管理区、设置警告标志;检测工作人员应佩带个人剂量计,并携带剂量报警仪。
3.3 设备表13.4 胶片和增感屏3.4.1 胶片:为满足灵敏度要求,应选用T3类或更高类别的胶片(本公司采用AGFA C7型胶片),且胶片的本底灰雾度不大于0.3。
3.4.2增感屏:采用铅箔增感屏,前、后屏厚度为0.03㎜。
3.4.3胶片和增感屏在透照过程中应始终紧密接触。
X射线探伤工艺守则
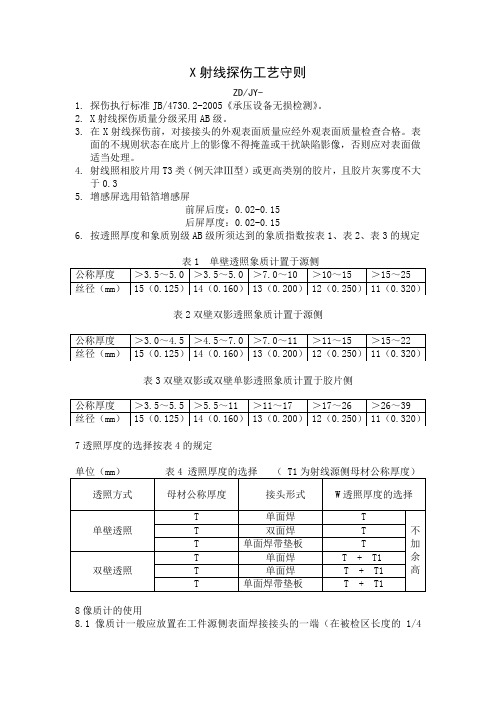
X射线探伤工艺守则ZD/JY-1.探伤执行标准JB/4730.2-2005《承压设备无损检测》。
2.X射线探伤质量分级采用AB级。
3.在X射线探伤前,对接接头的外观表面质量应经外观表面质量检查合格。
表面的不规则状态在底片上的影像不得掩盖或干扰缺陷影像,否则应对表面做适当处理。
4.射线照相胶片用T3类(例天津Ⅲ型)或更高类别的胶片,且胶片灰雾度不大于0.35.增感屏选用铅箔增感屏前屏后度:0.02-0.15后屏厚度:0.02-0.156.按透照厚度和象质别级AB级所须达到的象质指数按表1、表2、表3的规定表2双壁双影透照象质计置于源侧表3双壁双影或双壁单影透照象质计置于胶片侧7透照厚度的选择按表4的规定8像质计的使用8.1 像质计一般应放置在工件源侧表面焊接接头的一端(在被检区长度的1/4左右位置),金属丝应横跨焊缝,细丝置于外侧。
当一张胶片上同时透照多条焊接接头时,像质计应放置在透照区最边缘的焊缝处。
8.2 像质计放置原则a)单壁透照规定像质计放置在源侧。
双壁单影透照规定像质计放置在胶片侧。
双壁双影透照规定像质计可放置在源侧,也可放置在胶片侧。
b)单壁透照中,如果像质计无法放置在源侧,允许放置在胶片侧。
c)单壁透照中像质计放置在胶片侧时,应进行对比实验。
对比实验方法是在射源侧和胶片侧各放一个像质计,用与工件相同的条件,测定出像质计放置在源侧和胶片侧的灵敏度差异,以此修正应识别像质计丝号,以保证实际透照的底片灵敏度符合要求。
d)当像质计放置在胶片侧时,应在像质计上适当位置放置铅字“F”作为标记,“F”标记的影像应与像质计的标记同时出现在底片上,且应在检测报告中注明。
8.3 原则上每张底片上都应有像质计的影像。
当一次曝光完成多张胶片照相时,使用的像质计数量允许减少但应符合以下要求:a)环形对接焊接接头采用源置于中心周向曝光时,至少在圆周上等间隔地放置3个像质计。
B)一次曝光连续排列多张胶片时,至少第一张、中间一张、最后一张胶片放置1个像质计。
射线检测暗室处理工艺守则
射线检测暗室处理工艺守则1范围本工艺守则适用于射线检测胶片暗室处理。
2引用标准JB4730-94《压力容器无损检测》GB6846《确定暗室照明安全时间》3胶片射线检测用胶片是射线检测工作重要材料,选定后若要改换型号,生产厂家必须经主任或责任工程师批准,通知有关人员。
3.1胶片性能必须符合JB4730-94标准3.2胶片应放在防有害气体侵蚀,防辐射的低温避光容器中,先进先出,有效期内使用。
3.3胶片切装前,检查所有暗袋、裁刀,工作台洁净,暗袋不漏光,增感屏无划伤,污染。
3.4胶片切装前检查暗室关闭状态下安全通风、无光,有关设备好用。
3.5胶片切装,应戴干净的手套,不得用手直接接触胶片,不可以从暗袋中抽取胶片,以免发生静电感光,裁切胶片要连同衬纸一同裁切,以免划伤胶片。
3.6取、装、切胶片均应无光进行,若在安全灯下进行,应在距安全灯1m以外。
4显定液4.1显影液、定影液应按胶片生产厂家的推荐配方进行配制。
4.2新配制药液必须放置24小时后,方可用于胶片冲洗。
4.3所有药品应存放在避光、干燥处,温度应在10-30°范围。
4.4药液应始终处于防氧化和防污染状态,温度应能控制,显、定影应在槽内进行。
5显影、定影5.1胶片显影前,测量药液温度,使其保持在20℃5.2观察药液面高度不得低于胶片上端5.3显影时间5分钟,定影时间15分钟5.4显影时,应将胶片置于洗片架上,两架间距不小于20mm,以免划伤胶片,显定影时,应不断使胶片上下移动,防止气泡附着,以使胶片均匀显影、定影。
6停显和水洗6.1胶片显影终止后,立即交将胶片取出浸入停显液中,停止显影约30秒后,再置于定影中。
6.2水洗温度应在20℃6.3水面高度不应低于底片上端高度6.4底片应在洁净、流动水中冲洗,时间为30-50分钟,以确保底片无残留药液。
7底片干燥、收藏7.1底片水洗后,置于洁净无尘的环境中进行常温下或60℃以下干燥7.2干燥后的底片,不得印上手迹,存放在底片袋内移送质量评定人员。
X射线检测规程
X射线检测规程1人员资格和职责1.1从事射线照相人员必须持有国家有关部门颁发的资格证书,级证书具有评片、审核和签发报告的权利。
1.2 评片人员的视力应每年检查一次,校正视力不低于1.0。
1.3 射线人员应努力学习专业理论和技术法规,不断提高技术水平。
1.4射线人员应严格坚持质量标准,保证工程质量,实事求是,认真负责,忠于职守。
1.5认真做好无损检测设备的维护保养工作,严格执行安全防护措施。
2 检测操作流程图33.1 透照原理射线在穿透物体过程中会与物质发生相互作用,因吸收和散射而使其强度减弱。
强度衰减程度取决于物质的衰减系数和射线在物质中穿越的厚度。
如果被透照物体的局部存在缺陷,且构成的物质的衰减系数又不同于该试件,该局部区域的透过射线强度就会与周围产生差异。
把胶片放在适当的位置使其在透过射线的作用下感光,经暗室处理后得到底片。
底片上各点的黑化程度取决于射线透照量(射线强度乘以时间),由于缺陷部位和完好部位的透射射线强度不同,底片上相应部位就会出现黑度差异。
底片上相邻区域的黑度差定义为对比度。
把底片放在观片屏上借助透过光线观察,可以看到由对比度构成的不同形状的影象,评片人员据此判断缺陷情况并评价焊缝质量。
3.2 定向机透照。
选用80×150胶片透照,每张底片的标记如下图3.3曝光量选择定向X射线机拍片时,曝光量推荐应不低于15·。
焦距选择6003.4检测设备与材料采用2505定向X光机检测。
管线与法兰连接处,采用着色磁粉方法进行检测。
3.5 选择原则根据47013-2015和4109-2013标准对K值的要求,考虑缺陷的检出率,其次要考虑到工作效率并应结合现场条件的可能,选用单壁透照和双壁单影透照技术,根据实际应选择内透法。
3.6 象质计:选择线形象质计(5618-85、4109-2013、47013-2015)4 胶片保存4.1 胶片、底片不可接近氨、硫化氢、煤气、乙块、酸等有害气体,否则会产生灰雾。
X光无损检测操作规程
X光无损检测操作规程1. 引言X光无损检测是一种非破坏性检测方法,通过利用X射线的穿透性能对目标物体进行内部缺陷的检测和分析。
本文档旨在规范X光无损检测的操作流程和注意事项,以确保检测结果的准确性和安全性。
2. 设备准备在进行X光无损检测前,需要确保以下设备和材料齐全并正常工作:•X光无损检测仪器及配件•目标物体•辅助工具(如标尺、夹具等)•防护设备(如铅背心、安全眼镜等)•检测记录表格和文案3. 操作流程3.1 准备工作1.穿戴防护设备:检测人员应穿戴铅背心、安全眼镜、手套等防护设备,确保个人安全。
2.确认设备状态:检测人员应检查X光无损检测仪器及配件的状态,确保其正常工作。
3.准备目标物体:检测人员应将目标物体放置在检测区域,并确保其固定稳定。
3.2 检测操作1.设定检测参数:根据目标物体的材料和尺寸,合理设定X光无损检测仪器的参数,如电压、电流、曝光时间等。
2.对准检测位置:采用辅助工具(如标尺、夹具)将X光无损检测仪器对准目标物体的检测位置。
3.进行检测:按下X光无损检测仪器的启动按钮,开始对目标物体进行内部缺陷的检测。
4.观察结果:通过X光无损检测仪器的显示屏,观察检测结果。
如发现异常情况,应停止检测并记录下来。
5.记录数据:将检测结果记录在检测记录表格上,并注明相关的检测参数和检测时间。
3.3 结束工作1.关闭仪器:完成检测后,将X光无损检测仪器关闭,确保安全。
2.清理工作区:清理检测区域,将设备和辅助工具归位,并清除目标物体上的任何标记或夹具。
3.整理和归档检测记录:将检测记录表格和相关文案整理归档,以备查阅和分析。
4. 注意事项1.操作人员应严格遵守相关安全规定,正确佩戴防护设备,以防遭受X射线辐射带来的危害。
2.在操作过程中,应注意X光无损检测仪器的工作状态,如有异常应停止操作并检修。
3.目标物体应正确固定,以避免在检测过程中产生误差。
4.在操作过程中,应注意X射线对人体和其他物体的穿透性,避免对周围环境产生危害。
X射线检测工艺及操作规程
X射线检测工艺及操作规程本规程适用于压力容器焊缝X射线检测。
检测标准为NB/T47013.2-2015《承压设备无损检测》。
从事承压设备无损检测的人员,应按照国家特种设备无损检测人员考核的相关规定取得相应无损检测人员资格。
取得不同无损检测方法不同资格级别的人员,只能从事与该方法和该资格级别相应的无损检测工作。
本规程规定了X射线检测必须遵循的程序:1 准备2 布片3对照曝光4 记录5 暗室处理6.评片、签发报告1.准备1.1查看委托单,了解被检物的材质、结构、焊接工艺、坡口、厚度等情况,确定被检工件与委托单相符。
1.2确定摄片规格、透照方式、增感方式、象质计规格及射线机型号,一次透照有效长度,管电压、管电流、焦距等参数。
1.3 开启X射线机,已停用过一段时间的X射线机应按相应规定进行训机。
1.4根据工作量准备所需规格和数量的胶片。
2.布片:2.1根据图样要求和实物进行划线2.2标记底片上必须有下列标记影像:(1)定位标记(中心标记、搭接标记、检测区标记等)(2)识别标记(产品编号、焊接接头编号、部位编号和透照日期)(3)扩拍标记Z,返修标记R(焊缝一次性合格,则无此条标记)。
(4)像质计(原则上每张底片上都应有像质计的影像)a.像质计放在胶片一侧工件表面上时,应附加“F”标记以示区别。
b.采用射线源置于圆心位置的周向曝光技术时,像质计应放在内壁,应至少在圆周上等间隔的放置3个像质计。
各条标记应放在适当位置,数码字母等离焊缝边缘至少≥5mm,工件表面应作出永久性定位标记,以便为每张底片重新定位提供依据,当产品不适合打钢印时,应在透照部位图上详细标记。
底片上各种标记影像如下图:2.3布片注意:(1)检测比例为100%时,相邻两段必须保证10%左右覆盖区。
(2)根据产生射线可能性考虑采用铅板等屏蔽。
(3)暗袋在透照过程中应始终与被检物紧贴。
3对焦曝光3.1根据摄片规范对焦,使射线束中心方向尽可能垂直于被检物表面或曲面的切面。
- 1、下载文档前请自行甄别文档内容的完整性,平台不提供额外的编辑、内容补充、找答案等附加服务。
- 2、"仅部分预览"的文档,不可在线预览部分如存在完整性等问题,可反馈申请退款(可完整预览的文档不适用该条件!)。
- 3、如文档侵犯您的权益,请联系客服反馈,我们会尽快为您处理(人工客服工作时间:9:00-18:30)。
04X射线检测工艺守则X射线检测工艺守则QB/HTD04-20091、主题内容与适用范围1.1本守则规定了射线检测人员应具备的资格、所用器材、焊缝射线透照质量等级、检测方法和检测标准等。
1.2 本守则依据JB/T4730.1.2-2005的要求编写,适用厚度为38㎜以下钢制压力容器和壁厚大于2㎜钢管对接焊缝的AB级射线检测技术,满足《固定式压力容器安全技术监察规程》和GB150-1998的要求。
1.3 检测工艺卡是本守则的补充,由Ⅱ级人员按产品技术要求编写,其参数规定的更具体。
2、引用标准JB/T4730.1.2-2005《承压设备无损检测》GB16357-1996《工业X射线探伤放射卫生防护标准》GB18871-2002《电离辐射防护与辐射源安全基本标准》JB/T7902-1999《线型像质计》JB/T7903-1999《工业射线照相底片观片灯》GB150-1998《钢制压力容器》《压力容器安全技术监察规程》3、一般要求射线检测的一般要求除应符合JB/T4730.1-2005的有关规定外,还应符合下列规定。
3.1 检测人员3.1.1检测人员必须经过技术培训,按《特种设备无损检测人员考核与监督管理规则》取得与其工作相适应的资格证书,上岗前应进行安全防护知识的培训,并取得放射人员工作证。
3.1.2 检测人员应每年检查一次视力,未经矫正或经矫正的近(距)视力和远(距)视力不低于5.0,3.2 防护:3.2.1射线防护应符合GB18871、GB16357的有关规定;3.2.2现场进行射线检测时,应按GB16357规定划定控制区和管理区、设置警告标志;检测工作人员应佩带个人剂量计,并携带剂量报警仪。
3.3 设备3.3.1现使用设备见表1表13.4 胶片和增感屏3.4.1 胶片:为满足灵敏度要求,应选用T3类或更高类别的胶片(本公司采用AGFA C7型胶片),且胶片的本底灰雾度不大于0.3。
3.4.2增感屏:采用铅箔增感屏,前、后屏厚度为0.03㎜。
3.4.3胶片和增感屏在透照过程中应始终紧密接触。
3.5 像质计采用线型金属丝像质计,其规格型号应符合JB/T7902和HB7684的规定。
3.5.1像质计选用:由Ⅰ、Ⅱ级人员按透照厚度、根据透照方法选择表2~4规定的应识别丝号。
小径管(外径≤100mm )可选用通用线型像质计或JB4730.2-2005附录F规定的专用像质计。
表2 像质计灵敏度值—单壁透照、像质计置于源侧表3 像质计灵敏度值—双壁双影透照、像质计置于源侧表4 像质计灵敏度值—双壁单影或双壁双影透照、像质计置于胶片侧3.5.2透照厚度是指材料的公称厚度(不包括余高和垫板),多层透照时,透照厚度为射线穿透的各层材料公称厚度之和。
3.5.3像质计的放置:像质计应放在射源一侧的工件表面上被检焊缝区的一端(被检区长度的1/4部位),金属丝横跨且垂直于焊缝,细丝置于外侧。
a.单壁透照像质计放置在源侧;双壁单影透照像质计放置在胶片侧;双壁双影透照像质计可放置在源侧,也可放置在胶片侧。
b.单壁透照中,如果像质计无法放置在源侧,也可放置在胶片侧。
c.单壁透照中像质计放置在胶片侧时,应进行对比试验。
对比试验方法是在射源侧和胶片侧各放一个像质计,用与工件相同的条件透照,测定出像质计放置在源侧和胶片侧的灵敏度差异,以此修正应识别像质计丝号,以保证实际透照的底片灵敏度符合要求。
d.当像质计放置在胶片侧时,应在像质计上适当位置放置铅字“F”作为标记,“F”标记的影像应与像质计的标记同时出现在底片上,且应在检测报告中注明。
e.环形对接焊接接头采用源置于中心周向曝光时,至少在圆周上等间隔地放置3个像质计。
若透照区为抽查或返修透照,则每张底片上应有象质计显示,若同时还透照纵缝,则纵缝透照区的远端也应有象质计显示。
f.小径管可选用通用线型像质计或专用像质计(等径金属丝),金属丝应横跨焊缝放置。
3.6 识别系统:透照部位的标记由识别标记和定位标记组成。
3.6.1定位标记:应有中心标记(↑)和搭接标记(↑),局部检测时,搭接标记称为有效区段标记。
3.6.2 识别标记:应有产品编号、对接焊接接头编号、部位编号和透照日期,返修和扩探部位还应有返修标记R1、R2……(其数码表示返修次数)和扩探标记K。
3.6.3 标记位置:标记应放置在焊缝边缘5mm以外的部位,不得重叠,搭接标记除中心周向曝光外,一般应放在射源侧的工件表面上,但对于源在曲面工件内,且焦距大于曲率半径时,必须放在胶片侧。
3.6.4被检部位工件表面应打起、始钢印标记,以作为对底片重新定位的依据,标记位置距焊缝边缘5mm以外适当部位。
不适合作标记时,采用详细的透照部位拍片图记录。
3.7 评片室和观片灯3.7.1评片室a.评片应在专用评片室内进行,评片室的环境应整洁安静,光线应暗且柔和。
b.评片人员在评片前应经历一定的暗适应时间。
从阳光下进入评片的暗适应时间为5min~10min;从一般的室内进入评片的暗适应时间应不少于30s。
3.7.2观片灯观片灯的亮度至少应能观察最大黑度为4.0的底片,且观察窗口的漫射光亮度可调并带有遮光板,对不需要观察或透光量过强部分屏蔽强光。
3.8黑度计与黑度片采用TD-210型数字式黑度计和仪器自带的黑度片。
黑度计误差≤±0.05。
4、受检部位的表面要求4.1同一条焊缝的余高在允许范围内应均匀,应保证底片黑度处于规定范围内。
4.2距焊缝中心各40㎜范围内的焊疤、飞溅、成型粗糙及表面缺陷等应修磨,以不掩盖或不干扰缺陷影像的显示为度。
4.3焊缝及热影响区的表面质量(包括余高高度)应经检查员检验合格。
4.4受检测表面经射线检测人员认可。
5、检测时机:射线检测应在焊后进行,对有延迟裂纹倾向的材料应在焊接完成24小时后进行射线检测;有再热裂纹倾向的材料应在热处理后再增加一次无损检测;封头拼接焊缝应在压制成型后作无损检测;筒体纵缝应在筒体校圆之后作无损检测。
6、检测工艺和检测技术射线检测人员按工艺卡和受检测件情况,使用设备器材和材料进行检测操作。
6.1透照方式只要可以实施应首选单壁透照(单壁透照首选内透法)方式,当单壁透照不能实施时采用双壁透照(双壁透照首选双壁单影法)方式。
典型透照方式参见JB4730.2-2005射线检测附录C。
6.2透照方向透照时射线束中心一般应垂直指向透照区中心,需要时也可选用有利于发现缺陷的方向透照。
6.3一次透照长度分段曝光时,一次透照长度为每次曝光所检测的长度。
应以透照厚度比K进行控制。
纵向焊接接头K≤1.03,环向焊接接头K≤1.1。
6.3.1纵缝透照纵缝单壁透照焦距选700mm,当所用胶片360mm时,一次透照长度≯320mm,当胶片长300mm时,一次透照长度≯260mm。
6.3.2环缝单壁外透照一般焦距选用700mm,透照次数由图1查得。
6.3.3环缝周向曝光源置于圆筒中心,一次检测整条环缝,采用胶片长360mm,一次透照长度≯320mm。
像质计放在筒体内侧每120°放一个,搭接标记放在筒体外侧工件表面上。
6.3.4环缝双壁单影透照焦距F=150+D,透照次数由图2查得,像质计放在胶片侧且加“F”标记。
6.3.5小径管环向对接焊接接头的透照6.3.5.1小径管采用双壁双影透照布置,当同时满足下列两条件时应采用倾斜透照方式椭圆成像:a.T(壁厚)≤8mm;/4b.g(焊缝宽度)≤D椭圆成像时,应控制影像的开口宽度(上下焊缝投影最大间距)在1倍焊缝宽度左右。
不满足上述条件或椭圆成像有困难时可采用垂直透照方式重叠成像。
6.3.5.2小径管环向对接接头的透照次数小径管环向对接焊接接头100%检测的透照次数:采用倾斜透照椭圆成像时,当T/D>0.12时,相隔120°或60°透照3次。
≤0.12时,相隔90°透照2次。
当T/D垂直透照重叠成像时,一般应相隔120°或60°透照3次。
6.3.5.3椭圆显示透照采用平移法,也可采用平移后使主射线束对准焊缝进行透照。
6.3.6封头压制成形后拼接焊缝透照工艺见附录A6.3.7几何条件射线源至工件表面的最小距离f与b、d的关系为:f≥10d b2/3式中:f---沿射线束中心测定的工件受检部位射线源与受检工件源侧表面之间的距离;b---沿射线束中心测定的工件受检部位射线源侧表面与胶片之间的距离;d---射线源有效焦点尺寸;6.4射线能量X射线照相应尽量选用较低的管电压,在采用较高管电压时,应保证适当的曝光量。
不同透照厚度允许采用的最高X射线管电压见图3。
6.5、检测部位布片规则及编号方法6.5.1布片规则6.5.1.1应100%拍片检测时,每张底片两端的搭接长度应按计算值且不少于10㎜。
6.5.1.2局部检测和用另一种方法复验的产品,所有T型焊缝处均抽查到。
抽查的位置除“T”外,其余先在其两端部布片。
6.5.1.3扩探的部位应在缺陷片的两端。
6.5.1.4以开孔中心为圆心、1.5倍开孔直径为半径的圆中所包容的焊缝及覆盖焊缝应按要求的方法100%检测。
6.5.2编号方法6.5.2.1凡是需要拍片的焊接接头,均应按100%检测的要求对焊缝进行分区,每区长度为一次透照长度L3。
环缝区起始点为A1(或第一条纵缝)纵缝及其延长线与环缝的交点,按顺时针方向,顺序由小到大编号,纵焊缝以B1方向的端点为起始点,由小到大顺序编号。
底片中心标记的箭头始终由小号指向大号,主体以外的其它部件的纵环焊缝其序号接着主体序号往下编(原则是焊缝序号不要编重),焊缝底片编号及区起点规定见下图。
B 3B 2B 1焊缝编号及分区起始点示意图6.5.2.2分段组对的筒体,各段分别按上述方法编焊缝编号起始点。
6.5.2.3封头拼接焊缝编号为P1、P2……Pn ,产品试板编号为SB 。
6.5.2.4局部检测时,检验哪个区,射线底片就编哪个区号。
6.5.2.5补照片应有搭接标记(100%拍照时)、象质计、日期等标志。
返修部位的透照可不用搭接标记,其余标记应齐全。
7.扩探要求及返修复探要求7.1当在某条焊缝上局部检测发现超标缺陷时,应扩探该条焊缝总长的10%,且≥250mm ,若仍不合格,则该条焊缝应100%检测。
7.2超标缺陷返修后应重新检测,重新检测的条件与初探条件相同。
检测前及评定前,检测人员首先核查原始记录,了解返修部位的检测编号及原来缺陷的状况。
8、曝光量曝光量在焦距为700mm 时,一般应≥15mA/min 。
当焦距改变时,可按平方反比定律对曝光量的推荐值进行换算。
9、曝光曲线9.1对每台在用射线设备均应作出经常检测材料的曝光曲线,依据曝光曲线确定曝光参数。
9.2制作曝光曲线所采用的胶片、增感屏、焦距、射线能量等条件以及底片应达到的灵敏度、黑度等参数均应符合JB/T4730.2-2005的规定。