模具制作标准.
模具制作标准

模具制作标准模具制作标准是指在制造模具的过程中,必须遵循的一系列规范和标准化的操作流程,确保生产出的模具符合质量要求、安全有保障、使用寿命长久。
在当今不断发展的制造业中,模具作为生产工具,其重要性日益凸显,因此,制定模具制作标准显得尤为重要。
模具制作标准的目的:1.确保模具的准确性和完整性在模具制造过程中,不同环节需要采取不同的标准和规范来控制和管控,以确保模具制造的准确性和完整性。
比如,切削加工与磨削加工的工艺标准,表面质量的标准,钢材、电极等制造标准和选用标准。
2.确保制造过程的安全性模具制造中,涉及到的设备、工具等都有一定的危险性。
因此,制订一套完善的操作标准可以有效保障制造过程的安全性。
在操作规范中应该包含安全标准,操作员应该遵守的安全要求,以确保工人的人身安全。
3.确保模具的质量制定模具制作标准,是为了提高模具的质量水平,从而提升模具的性能和使用寿命。
这些规范包括材质含量标准,尺寸精度规范等,以确保模具达到或超过客户的要求及国际标准要求。
模具制作标准的详细规范:1.模具制造的成本、质量和交货期模具的制造成本、质量和交货期应始终围绕在客户要求之内。
•成本:模具制造的各阶段的成本,比如、原材料和某些模具零部件,应该与客户及制造方一致。
•质量:模具必须符合客户的质量标准。
模具必须满足设计、材料和制造方面的所有特定要求。
•交货期:模具的交货期应该符合客户的进度,确保模具在需求日前交付。
2.模具设计标准模具的设计标准决定了模具的准确性和使用寿命。
设计标准应安全、可靠。
设计标准还应包括使用材料,工艺和表面加工要求等等。
3.制造标准制造标准是模具制造的过程中必须遵循的标准。
制造标准主要包括硬度标准,Moldcore 设计和加工标准,线切割要求等。
4.工装和夹具为了保障模具生产效率、质量,设计和制造定点夹具以固定模具和工装辅助模具制造过程、修补。
5.模具的维修和保养故障发生时,很多时候可以通过保养和维修来解决,以延长模具寿命。
压铸模具制造标准

压铸模具制造标准为规范模具制造,保证模具质量,特制定此标准一、总体要求:1、所有零件按二维图纸尺寸、技术要求制作,检验依据二维图纸2、 CNC加工采用按3D编程,相关公差按二维图要求制作3、组立组要按总装图要求组合模具及配模4、发现二维图纸少尺寸、3D与2D不符、制作中出错、安装干涉等情况,及时上报质量组和设计组,由设计组及时做出解决方案,并下发新资料。
质量组确认后,有新资料时电脑上错误资料第一时删除。
5、所有零件热处理按图纸要求操作、6、所有零件表面处理按图纸要求操作7、所有零件上机加工分中、打表规定,打表要求打长面复查短面,分中要求在毎面中心分中(中心误差超10mm),同时用量具复查尺寸。
二、模芯、滑块1、材材为H13或DIEVR2、模芯应图纸硬度要求,要淬火处理。
淬火会造成变形及材料内部硬度达到要求,制作工艺路线为粗加工、淬火、精加工、去应力回火(高温腐蚀会造成应力),才能达图纸3、开粗前外形保证六面垂直度0.1mm、平行度0.02mm以内,4、外形淬火前放精加工余量,外形按最长面来计算,规定如下:长度宽度300mm以内长宽均放1mm,厚放1.2MM。
300~500mm长宽均放1~1.5mm,厚放1.5MM。
500~800mm长宽均放1.5~2mm,厚放2MM。
800mm以上长宽均放2~2.5mm,厚放2.5MM。
5、CNC编程按图编制合理精粗程序,保证质量同时缩短加工时间,减少不必要空刀(采用分段加工)。
CNC操机员按程序参数全部开到100%,不得改度参数,有问题向编程员反映。
6、CNC开粗留单边留1~1.5mm,厚1.5~2MM的淬火后精加工余量,注意不能产生内清角(最小不得小于R2),与外形贯通的槽深不足30mm,宽不足60的不做保护措施,超过时要求两侧底角最小为R15或口部连筋,具体分析后确认。
反面倒角C7,4个R角、分流锥(留有效高度30mm)、料筒等反面台阶处辟空淬火前加工到位。
模具技术标准
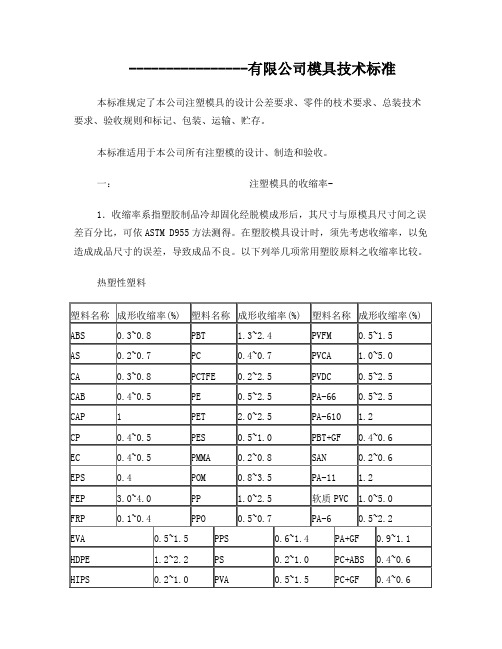
----------------有限公司模具技术标准本标准规定了本公司注塑模具的设计公差要求、零件的枝术要求、总装技术要求、验收规则和标记、包装、运输、贮存。
本标准适用于本公司所有注塑模的设计、制造和验收。
一:注塑模具的收缩率-1.收缩率系指塑胶制品冷却固化经脱模成形后,其尺寸与原模具尺寸间之误差百分比,可依ASTM D955方法测得。
在塑胶模具设计时,须先考虑收缩率,以免造成成品尺寸的误差,导致成品不良。
以下列举几项常用塑胶原料之收缩率比较。
热塑性塑料2.收缩率与塑料的材质,填充剂,产品壁厚,塑机料温、模温、保压压力、保压时间,模具进胶位置、进胶数量、进胶形式,冷却效果等有关。
常用塑料在壁厚为2.5mm时, 参考值二: 产品的公差要求模具制造时会根据客户的不同要求对产品的关键尺寸给予公差要求以满足塑胶制品的公差要求。
本公司设计时是以下表所示的公差标准执行。
根据本公司对空调壳体配合间隙及公差标准的执行。
三: 模具的总体要求参考模具协会的标准,本公司依照以下要求。
大量生产模(250,000— 1,000,000模或以上),具体要求如下:1.要有详细模具结构图。
2.精确的散件图。
3. 用Mold-flow软件模拟模具注塑过程、注射分析、压力分布及温度分布,以确定最好的入水位置、流道尺寸、疏气位置等。
4.模胚的A、B板及通腔背板均用28Hrc硬度的钢材;(内采用镶嵌模腔)。
5.上、下模及镶件使用硬度为48Hrc或以上的钢料,所有移动的零件应使用硬钢,而且必须有限位及定位锁。
6.模具尽可能自动断水口。
如可能,尽量使用潜水、细水口、香蕉型水口、并要考虑热流道的可行性。
7.模具设计应具备最大限度的冷却,上、下模肉高温度点应该个别地冷却。
8.顶出方法应尽可能使流道与产品自动掉下,避免运用多次顶出方法。
9.模具应能够全自动生产,大的零件应能够轻松取出。
10.顶针板必须有导向柱,顶出限位,以及模具支撑柱。
11.安装浇口定位环应与塑机尺寸匹配12.非天侧处有油缸装置,必须有油缸立柱。
模具制作标准(精)

模具制作标准目的:为使模具制作及维修作业能降低成本, 缩短模具制作周期, 确保模具寿命,保证产品品质。
一、制作模具编号:1、必须在模具外恻上方雕刻或锻打模具编号,字体要求整套模具字高统一。
2、每块模板均须用字码打上模具编号,且方向统一。
3、模具所有螺丝、吊圈孔及模具部件都必须是公制规格,而附加模具配件必须是标准规格,禁止自行土制。
二、基准位:1、每套模具必须在 B 板和动模板(以动模板为参照俯视图视角的右下方做上记号以示基准,以便模具后续维修。
三、码模槽:1、非工字模胚均需在前后模铣出码模槽,具体尺寸根据模具大小设计而定。
四、顶柱孔:1、动模必须开有足够大的顶柱孔,根据模具配比的机台,比实际顶柱的尺寸大直径 10-20MM (除真空模具。
2、小型且中心进浇模具只需中间开一个顶柱孔,中型模具必须开三个以上顶柱孔以保持顶出平衡。
五、复位机构装置:当顶针(丝筒与行位顶出装置干涉时,必须在模具上设有先复位装置, 不谨靠弹簧使顶针板复位, 以免弹簧日后失效,行位(抽芯与顶针(丝筒相碰撞。
六、顶针动作:1、应考虑模具在任何场合顶针都能可靠的顶出产品, 并在合模前顶针不与模具的任何配件相干涉地复位。
2、顶出时产品不能有任何超出产品要求的变形, 迅速顶出痕迹不影响产品表面质量。
3、顶出应平衡很顺, 不可出现顶出倾斜现象及顶出有杂音的产生。
七、行位动作:1、滑块行位动作应顺滑, 保证产品不得有拉变形现象, 不可出现卡死动作,不均匀松动等现象。
2、大滑块滑动部位应开油槽3、在表面要求较高和壁厚较厚的铸件且有强度要求的产品, 滑块上应设有冷却水路。
4、当滑块滑动行程过长时, 必须在模座上增长导向, 通常滑动部位做到宽度的1.5倍左右为宜,抽芯时滑块在导向槽的部分,要有滑块滑动部位的 2/3在导向滑槽内。
5、斜导柱与导柱孔的配合间隙必须留有 0.2MM 以上,禁止非间隙配合。
6、斜导柱的角度小于滑块锲紧面 2度, 大滑块的锲尽紧块须伸入下模 15-20MM 以斜度面互锁反压。
注塑模具制作标准

xx注塑模具制作标准1目的1.1规范xxx模具部模具制作规范和验收标准。
1.2不断提高模具质量,确保模具正常投入生产。
1.3确保生产出合格的注塑件及产品。
1.4本部必须按照此标准进行模具设计及制造,若模具设计及制造因不符合此标准而引起的模具质量问题,由模具厂家承担一切后果。
2范围2.1本标准规定xx模具部注塑模具制作及验收标准。
2.2本标准只适用于xxx模具部各产品模具制作。
2.3本标准包括以下三个方面的内容。
2.3.1模具结构2.3.2塑料件外观要求。
2.3.3模具验收。
3引用标准无4定义无5管理要求5.1模具制作5.1.1模具材料5.1.1.1模坯各板材料所用钢板不低于1050钢。
5.1.1.2胚司、边钉、回钉、中托边所用材料表面硬度不低于HRC60±2。
5.1.1.3啤ABS、PP、PPC料的模具,前模及前模镶件材料不低于超级P20钢,后模材料不低于P20钢。
5.1.1.4啤PC、POM、PE等腐蚀性材料的模具,前模及前模镶件、后模材料不低于LKM2316ESR钢。
5.1.1.5啤透明AS、ABS、PC、PVC等透明材料的模具材料不低于瑞典一胜百S136透明耐腐镜面模钢。
5.1.1.6斜顶、摆杆表面硬度不少于HRC35,推板表面硬度不少于HRC28。
5.1.1.7如果因产品需要由客户指定某模具的材料时,应满足客户要求。
5.1.1.8注明:以上材料由材料厂提供材料证明。
5.1.2模具结构5.1.2.1零部件按图纸加工,外观整洁美观。
5.1.2.2零部件的装配间隙须符合图纸要求。
5.1.2.3浇注系统的加工要求a) 浇注系统设计要求:设计时要充分考虑浇注系统对产品外观和产品装配的影响.浇注系统对产品外观影响大的产品在设计中要留出可能更改的空间,包括顶出位置,冷却系统位置等。
b) 进料口结构形式:进料口由压环和唧咀组成,根椐产品的不同形式进料口结构分为以下三种方式(图1).要求优先采用A、C形式。
模具的设计与制作要求

模具的设计与制作要求1.准确的产品尺寸和形状:模具的设计要根据产品的准确尺寸和形状进行,这是保证产品质量和一致性的基础。
同时,也要考虑到产品的形状复杂性,进行合理布局和结构设计。
2.合理的材料选择:模具的工作环境要考虑到温度、压力、磨损等因素,所以在材料的选择上需要具有良好的耐磨性、耐腐蚀性和热稳定性。
一般常用的模具材料有铸钢、工具钢、硬质合金等。
3.可靠的结构设计:模具的结构设计要考虑到产品的工艺要求和承受的力,以确保模具在工作过程中不变形、不破裂,并有足够的刚度和强度。
另外,还要考虑到模具的分解性、装配性和可维修性,方便模具的更换和维护。
4.高效的冷却系统设计:模具的制作过程中会产生大量的热量,如果不能有效地散热,会导致模具温度过高,进而影响产品质量和模具寿命。
因此,模具的设计中要充分考虑冷却系统的设置,合理布置冷却通道和出水口,以提高散热效果。
5.精密的加工工艺:模具的制作一般采用数控机床进行精密加工,要求加工精度高,尺寸精确,表面光洁度好。
加工工艺包括铣削、钻孔、褶皱、车削、车削、划线等,要保证模具的加工质量和尺寸精度。
6.严格的质量控制:模具的设计与制作过程中,要进行严格的质量控制,包括原材料的采购、模具制作过程中的检测和验收,以及最终的模具出厂检验。
尤其对于关键部件和加工工艺要进行特别的把关。
7.合理的模具使用和维护:模具的使用和维护也非常重要,要按照操作规范进行使用,定期保养和维修,并且要妥善保管模具,以延长模具的使用寿命。
总之,模具的设计与制作是一个相对复杂和繁琐的工作,需要综合考虑产品的需求、材料的特性、工艺的要求以及工装设备的配合等多个因素,以实现高效、精确、持久的生产制造目的。
模具设计标准PPT课件

1.模胚的类型:
二.模胚
1.1. 卧式成型机〕:根据模具的大小和选用成型机不同,选用直身模胚或工字型模胚。
1.2. C型成型机〕:选用左右工字型模胚
2.模具编号位置:
3. 模胚的加工要求:
3.1. 导柱外面要加导套〔防止敲导柱拉伤模胚的孔〕;导柱要做油槽,导套后面做 开排气槽
3.2. 导柱和导套外表光洁度到达以上〔外表用肉眼看不到刀纹〕
3.3. 导柱和导套的配合问隙为〔双边〕
深,并且开通导套
3.4. 导柱和衬套之间的间隙为〔双边〕
导套
Ød
导柱 衬套
外表(内 外)光洁 度到达以 上
Ød+00.020
ØD1 0
导套挂台处 排气槽
5
3.5. A板和B板基准边错位最大 3.6. A板和B板直角度在以内 3.7. A板和B板框基准边的尺寸相差在以内
高的内模四边加直身导柱/导柱. 4.前后模型芯:采用斜度四个方向定位〔前后左右〕 5.前后模型芯镶件:采用直斜度四个方向定位〔前后左右〕 6.精定位尽量在模仁上原身留,拆镶件增加误差,结构性不强 7.精定位必须设计斜面,防止烧伤 8.模胚挖框和边锁由模胚厂加工〔预防挖框后模胚变形〕 9.零位和基准面要一致〔一套模具标数基准要一致〕,图面标数注意配合公差 10.层层定位要注意加工顺序,一层定位加工完后再加工另一层
IN“, 〞OUT“字样左来自图左边接运水17
模具做转水口
转水口镶件
18
4.16.模具加一百万次计数器,指定计数器(我司实际安装右图所示计数器〕,并 安装在操作面这边 我司所使用计数器规格 25
48 53
19
4.17.模胚出线槽局部倒圆角
20
4.18.前模胚边要做避空(红色区域避空0.5MM) 防止插伤后模模仁边
模具制作标准化

图(2)
图(3)
母模板
公模板
楔块
斜导柱
垫块
耐磨块
5
采用整体式 加工困难, 一般用在 模具较小 的场合。
用矩形的 压板形式, 加工简单, 强度较好, 应用广泛, 压板规格 可查标准零 件表.
采用”7”字形 压板,加工简单, 强度较好, 一般要加销孔定位.
采用镶嵌式的T形槽 ,稳定性较好,加工困难.
图(2)
图(3)
14
6-2 模具顶出系统设计要求
15
7-1 模具冷却系统设计要求
⑴模具冷却统设计时应遵循以下要求:
冷却系统应保证制品冷却的充分性和均匀性; 模具水路边距制品胶位的距离S以模具基准取整(图2),最少要求距离为10-15mm; 模具水路的直径ΦD≥8mm;隔水片要求见(图1); 模具入水口(IN)和出水口(OUT)的温度差小于5度.
模具顶出系统设计时应遵循以下要求:
顶针直径小于2mm时,使用带托顶针; 顶针防反转设计的定位方式(图1)使用定位方式2,其它方式禁止使用; 顶针头上须加工字码(图2); 顶针设计在斜面位置时必须追加防滑设计(图3)。
定位方式1
定位方式3
如图示顶针头应打上对应字码,必须工整,端正,不得歪扭
定位方式2
图(1)
图(1)
图(2)
图(3)
⑷滑块压板(导轨)要求:
滑块导轨设计时使用下列两种形式,要求如下:
W
配合间隙
8
4-1 模具斜顶设计标准
由产品的形状确定出抽芯距:S=S + (2~5)mm(图1,2) 根据顶出行程,计算斜顶的角度α (tgα = S/S) , α值取值范围,3≤α≤8° 斜顶与模芯之间的靠破距离H(图1,2)取值范围为5~10mm(依模芯厚度而定) 斜顶的厚度取0.5的倍数(图3). 斜顶须加工圆环油槽,详细见(图4)
- 1、下载文档前请自行甄别文档内容的完整性,平台不提供额外的编辑、内容补充、找答案等附加服务。
- 2、"仅部分预览"的文档,不可在线预览部分如存在完整性等问题,可反馈申请退款(可完整预览的文档不适用该条件!)。
- 3、如文档侵犯您的权益,请联系客服反馈,我们会尽快为您处理(人工客服工作时间:9:00-18:30)。
模具系统 一, 模胚构件模架:按拆装顺序,用阿拉伯数字在模架基准角标识面打上字码,同时打上模号;模架配件:导柱;回针;模架螺丝;法兰;射嘴;用风动打磨机打磨机打上清晰模具编号便于查找;方铁上CNC 锣上模具编号。
参考以下图片撬模坑,设计画出模架厂做出模具号,用12号字码打上吊环孔大小,用12号字打上方铁字码制作CNC完成,深0.5MM ,两条同做模具向上标识CNC 完成,大小深度跟随字码模具装配顺序编号1, 方脚:2.1按比例大小锣上模号;字深度为0.5MM !(由CNC 锣出);如上图 2.2方铁高度=产品脱模距离+10MM内模:3.1内模基准角编号(前内模M1;M2;---Mn ;后内模C1;C2;----Cn 前后M1与C1前后相对应), 分模时做好,CNC 直接锣出,具做数据按下图要求字码长度如图位置锣上深0.5MM 槽位,再锣上8号字码,深0.2MM ,3.2前,后模料的硬度不能相同(错开2度;例如前模HRC42;那后模则用HRC40),内 内模里的有擦穿配合的镶件也需同样做法!3.3内模必须做锁位,r 所有的锁位必须是CNC 直接锣准,不能打磨飞配;如图:4,镶件:1. 所有插位角度不得小于2°度(图1)2. 有插位的镶件不能采用相同硬度,相同材料的钢材,防止生产中容易”烧伤”不良(图1);三D 分模时做出,CNC 加工完成;槽宽10MM ,深0.5MM ,字高6MM三D 分模时做出,CNC 加工完成;直径12MM ,深0.5MM ,字高8MM ,锁位三D 分模时做出,CNC 加工完成;前模做凹,后模做凸型腔周围避空处理,改良夹口,披峰,3.前后模镶件的靠破面处a≥2mm(图2),避免应强度不足造成披锋不良;4.避免镶件尖角靠破(图3),镶件尖角处靠破易塌角,造成披锋不良;5.形状复杂,加工困难,不易成型,排气困难的位置需要考虑设计镶件结构(注需要事先检讨,要不影响外观6.筋位深度≥10mm时,需要考虑设计镶件结构注:`对于比较多的模具镶件,其形状尽可能规则,而且长,宽尺寸尽可能取整数,减少加工误差镶⑵镶件定位要求:1.定位方式很多,下图示1,2 为两种优先使用的镶件定位方法;2.当镶件无法做定位时,镶件四周做1~2°斜度定位(图3),有特殊情况提出商讨后确认.图5.2.12c图5.2.12a图5.2.12b7.齿轮:品前后模均需做镶件,入水点顾及产品变形情度分配:镶件孔一般前后模一起割出,镶件数控车加工,型腔用中走丝加工。
如图:三点入浇,减小流动垂直向收缩大,产生的收缩不一致(各向异性),提高胶件精度5,;山打螺丝牙孔必须垂直模板平面,牙头部平面级位必须帖紧帖平被锁平面;螺丝沉头孔底部必须是平面;螺丝过孔比螺丝直径避大0.5MM!常用的有M16,M20,后续其螺丝头部要装胶圈(可用运水圈),有以利缓冲,螺丝头低于沉孔口1.0MM;螺丝沉孔口倒45度角1.0MM,孔底部必须是平面;螺丝过孔比螺丝直径避大0.5MM!山打螺丝长度確定。
长度L=前模+水口长度+30﹐见图﹐也即L=A+C+D+H+30。
6,顶棍孔:如下图:模架的(高度*宽度)35*35以下模架做一个顶棍孔;40*40以上到55*55以下做如图(1环以内)顶棍孔;60*60以上到85*85以下做如图(2环以内)顶棍孔;100*100以上做如图(3以内环)顶棍孔!(模架高度,宽度参数分开对;例:高45*宽25的模架就做中间一个和高度的1环上下两个就好)6,尼龙塞一般细水口模较常采用尼龙胶钉代替拉勾﹐控制开模的先后次序。
尼龙胶钉结构简单,易装配﹐并且可通过调整螺丝的松紧来控制尼龙棒的膨胀﹐开模时﹐利用尼龙棒与孔的真空摩擦力使A ﹑B板一起运动。
但对于大型模具﹐这种结构不常用。
尼龙塞孔;跟所配胶塞直径相等,锁胶塞板胶塞头沉入3.0MM,避免合模挤压膨胀失效;胶塞孔深度可以完含盖胶塞高度,孔必须是盲孔,孔壁要光滑7,水口勾针水口勾针藏进水口推板內﹐以防阻碍熔融塑料的流动。
其大小一般为ø6.0MM”,其中心与竖直分流道中心重合,如图所示﹕8,唧咀所有模具一般采用标准唧咀,超过55*55以上的模胚,采用大唧嘴,当面板较厚时﹐在保证唧咀托底与面板底之间10MM至少5MM距离的情況下,將唧咀沉入面板﹐见图;9,拉板:1,反向顶出结构的模具用到拉板,一定注重其动作平衡,2,小水口入水扣针较多的,考虑用拉板;3,技术要求:D1一般取10~12mm;D2的尺寸应稍大于流道在开模方向上的投影总长度,但不能小于110mm;D3要求大于1.0mm;D4一般取25mm左右,其他尺寸参靠图示1—面板 2—水口板 3—A板 4—定距拉板图5.5.1610,锁紧块:内模大于300*300时设计锁紧块配框。
T大于2/3H,A大于2/3L,(A可以是多块集合)斜度做5度。
(另常规模用标准件100*30*40)11,螺丝:参考列制作固定内模的螺丝位于内模边时,其与内模边的尺寸对应关系见表螺絲規格B最小值B常用值M6"8 12M8"10 12M10"15 15M12"15 1512,水口牌,弹块、镶件等用3号数字字码打上编号;无法用字码打的可用风动打磨机刻上!用于装配防呆!13,撑头:2525以上模胚﹐原則上要求加撑头,保证模具强度足夠。
小模(45*45以下撑头比方铁高0.1mm, 大模(4545以上)撑头比方铁高0.15mm,撑头一般规格为ø25﹑ø30﹑ø35﹑ø45﹑ø50、也可以为方块撑头,撑头孔单边避空0.5---1.0mm在距两方铁内则50MM的中间:视位置、视库存材料大小尽可能做大;直径小于30MM的撑头位必要时可考虑方块式撑头;模架小于250*250的不用做撑头14,垃圾钉:垃圾钉种在顶针底板上,回针底各有一粒,每隔100~150以上加一粒,大型模的顶针底也种垃圾钉。
不论模具大小,垃圾钉规格均一致。
所有垃圾钉必须紧配在顶针底板上!为回针底部垃圾钉;其它的做法边入15;以大于80小于100的间隔平均分配15,安全锁:凡是中心吊环孔偏中,或模具吊起重心偏向一边的模具必须做安全锁块,安全锁块漆上黄色油漆!顶出限位16,模脚:凡是模具的底部有功能部件外置的都要加模脚,做到模具本身能平稳摆放而不会压坏外置的功能部件!二,浇注系统1,入胶方式:按研发工程排模表定好的入胶方式制作。
产品小于100*100的用12MM的唧嘴,反之用16MM的,产品重量超过200克的优级先使用大唧嘴或热流道填允方式。
本厂常用的入胶方式,相应使用的结构:A:大水口;B:细水口;C:简化细水口;D:热流道E:吹气模浇口类型优点缺点适用产品直接浇口熔融树脂直接入腔、压力损失小、保压补缩作用强.去除困难、浇口痕迹明显、浇口周围应力大.CD门、底壳.侧浇口加工容易、易保证浇口加工精度.有浇口痕迹、浇口修改困难.CD门、中层、镜件、按钮、布网架、手挽、电池门、CD座、装饰件、面板、盖板.潜伏式浇口浇口痕迹不明显、可自动切断浇口.加工困难、浇口尺寸精度不易保证.齿轮、手挽、按钮(仅指钮身高度大于15MM的情况).点浇口开模时自动切断浇口、浇口周围残留应力小、痕迹小、可设置多点浇口.压力损失大、要求较高的注射力.底壳、面壳、按钮(仅指钮周边均有骨位的情况)例CD109钮组.2,浇口:喷流(差)喷流(差)顺流(良)顺流(良)边缘浇口与搭接浇口的选择潜伏式浇口有潜顶针﹑潜薄片﹑潜產品等几种.潜水也可以开在前模一侧 α=30~45o β=15~20o頂針排氣大型深腔制品﹐非常適合采用頂針排氣﹐將頂針双边車小0.02~~0.03即可。
同時﹐当产品中間有燒焦等缺陷時也可采用頂針排氣來解決。
镶件排氣制品上深的骨位常采用镶拼结构﹐既方便加工﹐又可起到排气参数:导套孔排气导套上排气槽一般宽5—8mm, 深0.5—1.0mm。
当产品中柱位孔为前模碰穿方式,其下放置顶针时,处理方式如图(假司筒)5,司筒针、水口钩针:制作按以下3种方式:司筒针一般采用无头螺线固定,但当多支司筒针相距很近时,采用压块与杯头螺丝固定。
顶针的管位.妆顶针位于圆弧面或者当顶针和司筒受胶位方向限制时,往往要設设置管位装置,管位方式有下列三種: 见图,其中图a为设置管位针,较常用;图b为加一管位块;图c为将顶针头部加工为直身边,此方式为。
顶针:A.顶针布置原则(1)顶针布置应使顶出力尽量平衡。
结构复杂部位所需脱模力较大,顶针数量应相应增加。
(2)顶针应设置于有效部位,如骨位、柱位、台阶、金属嵌件、局部厚胶等结构复杂部位。
骨位、柱位两侧的顶针应尽量对称布置,顶针与骨位、柱位的边间距一般取D=1.5mm,如图5.5.8所示,另外,应尽量保证柱位两侧顶针的中心连线通过柱位中心。
顶针顶面为斜面、台阶不好顶针顶面为平面较好图5.5.9顶针受力结构较好部位合理布置图5.5.8a 不合理布置图5.5.8b顶针中心连线未通过柱位中心顶针中心连线通过柱位中心对称布置对称布置1.顶针直径小于2mm时,使用带托顶针;2.顶针防反转设计的定位方式(图1)使用定位方式2,其它方式禁止使用;3.顶针头上须加工字码(图2);顶针设计在斜面位置时必须追加防滑设计(图3)。
顶针,司筒;直顶,斜顶;用字码或打磨机打上(1;2;----n)编号,装配位边上打上同样编号;(斜顶,直顶在分型面同时标上下相同编号,尽可能用字码打出,方便装好模后查验)6,扁顶,当制品上有较深的骨位时,采用扁顶针頂出是切实有效的方法.但其加工困难,因此,模具型芯常采用镶拼结构﹐6,直顶、直顶有两种结构形式:原身直顶和推块+顶杆。
2) 直顶与产品完全贴合的一面做1°斜度,其余三面做3°斜度。
3) 当后模原身出时,直顶与产品胶位內侧距离为0.3~0.5,当后模是镶件时,直顶边紧帖镶呵边:如图方法.其工作原理为:在頂出制品的同时受斜面限制,同时作橫向移动,从而使制品脱离。
有挤压复位条件的斜顶按本厂常规做法;其他参考以下图示做。
1.由产品的形状确定出抽芯距:S抽=S倒勾+ (2~5)mm(图1,2)2.根据顶出行程,计算斜顶的角度α(tgα= S抽/S顶) , α值取值范围,3≤α≤8°3.斜顶与模芯之间的靠破距离H(图1,2)取值范围为5~10mm(依模芯厚度而定)4.斜顶的厚度取0.5的倍数(图3).5.斜顶须加工圆环油槽,详细见(图4)槽范围1 图2 图3 图4当斜顶大小与頂顶出高度受周围骨位﹑枕位等限制或者两斜顶出干涉,解決方法有:设置由于制品的特殊要求﹐其某部位的脱模方向与注射机开模方向不一致﹐需进行侧面分型与抽芯方可而利顶出制品。