磨床加工标准
磨床技术说明

MK8463A×30型高精度数控轧辊磨床技术说明一、机床描述和技术参数机床型号:MK8463A×30型高精度数控轧辊磨床1.1用途这里所提供的是险峰机床厂凭借三十多年制造轧辊磨床的经验,在技术上经过不断开发与研究,最新设计的数控(CNC)轧辊磨床。
它适合高精度磨削金属加工行业、塑料机械及造纸等非金属制造业的工作辊和支承辊。
在本机床上可以完成以下加工作业:-----磨削圆柱形、圆锥形辊面;-----磨削中凸或中凹曲线辊面;-----磨削CVC及任意曲线辊面。
1.2.技术参数最大磨削直径 630mm最小磨削直径 90mm最大项尖距 3000mm工件最大重量 6300Kg工件转速 7-70rpm砂轮线速度 45m/s拖板纵向移动速度 50-3000mm/min砂轮架横向快速移动速度 300mm/min手摇编码器拖板进给量 0.01mln/P手摇编码器磨架进给量 0 .001nun/P连续横进给速度 0.003-1.2 mn/min周期横进给量 0.003-0.12 mm/行程磨架横向最大程 380mm磨削最大中凸(凹)半径量≤l.3mm砂轮规格(外径×宽度×孔径)Φ750×75×305mm中心架支承范围Φ90 -Φ480mm测量装置测量范围Φ90 -0 630mm西门子主轴电机(工件电机) 22Kw西门子主轴电机(砂轮电机) 30Kw机床外形尺寸(长×宽×高)约12900×4300×2400mm机床重量(约) 42000Kg1.3精度与标准a磨削圆柱辊面达到的精度圆度 0.0015mm圆柱度 1000:0.0015m表面粗糙度 Ra0.1μmb磨削中凸或中凹辊面达到的精度(中高量为o.1mm时)辊形误差 1000:0.0015mm表面粗糙度 Ra0.2 μm标准:机床在制造中严格执行等效国际标准的中国国家标准(代号为JB5568-91),该标准是参照ISO和DIN制订的中国机械工具行业标准。
内圆磨床标准
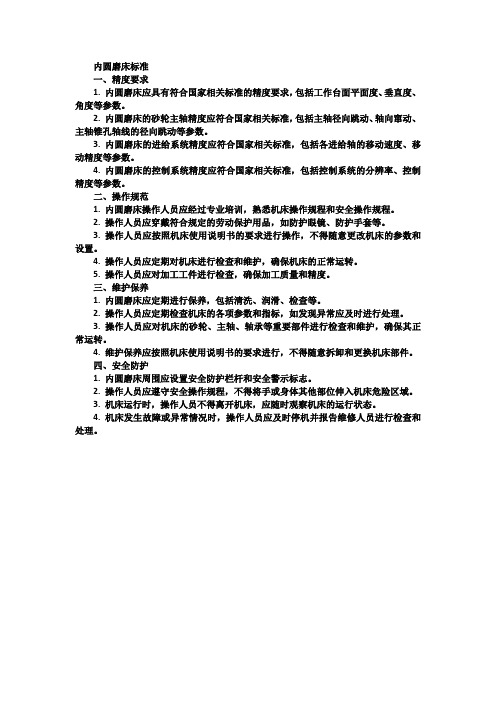
内圆磨床标准
一、精度要求
1. 内圆磨床应具有符合国家相关标准的精度要求,包括工作台面平面度、垂直度、角度等参数。
2. 内圆磨床的砂轮主轴精度应符合国家相关标准,包括主轴径向跳动、轴向窜动、主轴锥孔轴线的径向跳动等参数。
3. 内圆磨床的进给系统精度应符合国家相关标准,包括各进给轴的移动速度、移动精度等参数。
4. 内圆磨床的控制系统精度应符合国家相关标准,包括控制系统的分辨率、控制精度等参数。
二、操作规范
1. 内圆磨床操作人员应经过专业培训,熟悉机床操作规程和安全操作规程。
2. 操作人员应穿戴符合规定的劳动保护用品,如防护眼镜、防护手套等。
3. 操作人员应按照机床使用说明书的要求进行操作,不得随意更改机床的参数和设置。
4. 操作人员应定期对机床进行检查和维护,确保机床的正常运转。
5. 操作人员应对加工工件进行检查,确保加工质量和精度。
三、维护保养
1. 内圆磨床应定期进行保养,包括清洗、润滑、检查等。
2. 操作人员应定期检查机床的各项参数和指标,如发现异常应及时进行处理。
3. 操作人员应对机床的砂轮、主轴、轴承等重要部件进行检查和维护,确保其正常运转。
4. 维护保养应按照机床使用说明书的要求进行,不得随意拆卸和更换机床部件。
四、安全防护
1. 内圆磨床周围应设置安全防护栏杆和安全警示标志。
2. 操作人员应遵守安全操作规程,不得将手或身体其他部位伸入机床危险区域。
3. 机床运行时,操作人员不得离开机床,应随时观察机床的运行状态。
4. 机床发生故障或异常情况时,操作人员应及时停机并报告维修人员进行检查和处理。
磨床加工标准
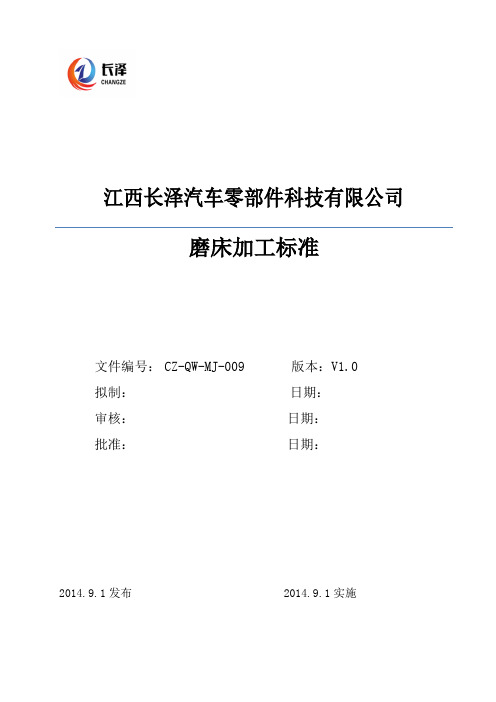
江西长泽汽车零部件科技有限公司磨床加工标准文件编号:CZ-QW-MJ-009 版本:V1.0拟制:日期:审核:日期:批准:日期:2014.9.1发布 2014.9.1实施文件修改记录表1 目的规范和指导磨床的生产作业,提升生产效率,提高生产品质。
明确机床维护保养方法及其正确操作规程延长机器使用寿命。
2 范围适用于制造部所有磨床加工。
3 职责3.1.主管宣导加工者熟练撑握。
3.2.主管负责培训,新入职员工按作业标准进行作业。
3.3.操作者按正常程序操作机台,做好保养和记录。
4 定义严格按标准作业,保证产品质量。
5 作业标准5.1 审图标准5.1.1 仔细审阅图纸的加工要求和工艺,重要的加工信息要在图纸上注明并标记。
5.1.2 检查工件和图纸是否相符,如:工件外形尺寸、厚度、材质,形状。
5.2 砂轮准备5.2.1 开料或者切料选用切割片进行加工。
5.2.2 研磨选择46L的砂轮进行加工。
5.3 加工标准5.3.1 开料的标准:根据图纸选择合适的材料进行加工,软料每次下刀0.8~1.2mm,硬料每次0.5~0.8mm;厚度超过40mm的工件要两边接,且要注意下刀的垂直度。
5.3.2 平面研磨加工标准;5.3.2.1 检查工件是否有毛刺披锋或者凹凸不平。
5.3.2.2 用旧砂轮或者砂纸砂平毛刺披锋。
5.3.2.3 对板件平面较大或较长时一定要放在磁台上进行检查,检查是否有变形。
对变形处要用塞尺或者A4纸张垫平变形处,再充磁加工。
5.3.2.4 加工的模板平面较小而长度又较长时,加工前要把工件摆斜在磁盘上充磁方可加工。
5.3.3 砂轮的进给量标准;5.3.3.1 加工非淬火件比如A3、45#未淬火 P20料时,开粗时砂轮量每次可以下刀0.1mm~0.2mm,开粗时模板留0.1余量,修整砂轮精磨。
精磨时砂轮进给量≤0.05,然后量数在进行研磨加工。
5.3.3.2 加工淬火件45#时,它的砂轮进给量和加工方法同非淬火件一样。
《磨床余量标准》
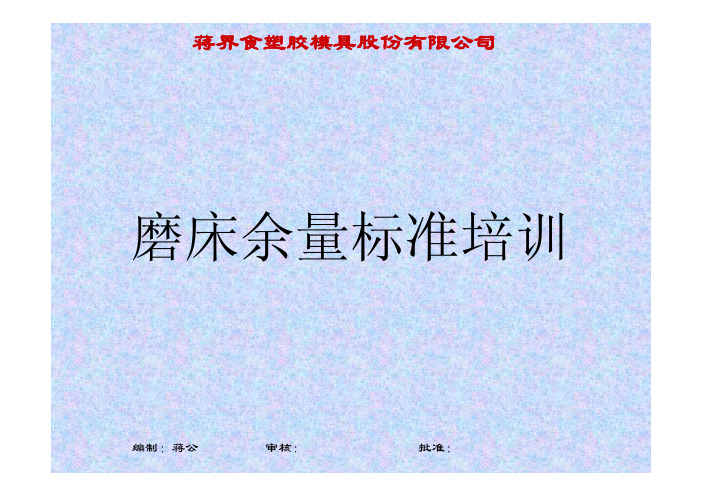
ห้องสมุดไป่ตู้
审核:
批准:
蒋界食塑胶模具股份有限公司
编制:蒋公
快走丝割外形的零件, 单面留余量0.1MM
审核:
批准:
蒋界食塑胶模具股份有限公司
小压块、 压条等小 零件,单 边留淬火
余量 0.15MM磨。 不淬火而 只需留余 量0.1MM
编制:蒋公
审核:
批准:
蒋界食塑胶模具股份有限公司
根据零件 尺寸大小, 按标准留 磨床余量, 不淬火的 减少30%
编制:蒋公
审核:
批准:
蒋界食塑胶模具股份有限公司
编制:蒋公
此类型的零件,容易 变形,余量需在标准
0.2
0.25
根据零件形 状而定
0.2
0.25
0.3
>100
0.2
21~50
0.2
>200
51~100
0.2
0.25 0.25 0.3
0.3 0.3 0.35
0.35
根据零件形 状而定
0.4
>100
0.2
0.3
0.4
0.5
注:1、本表适用于淬火零件,不淬火零件余量应减少30%. 2、本公司小磨床加工尺寸极限范围:350(长)×160(宽)×290(高) 超出小磨床加工极限的,由大水磨床加工
蒋界食塑胶模具股份有限公司
磨床余量标准培训
编制:蒋公
审核:
批准:
蒋界食塑胶模具股份有限公司
单位:毫米
磨床加工余量标准
零件厚度
零件长度 零件宽度
<100
101~250 251~400 401~600 余量(单面/MM)
磨床加工标准操作程序
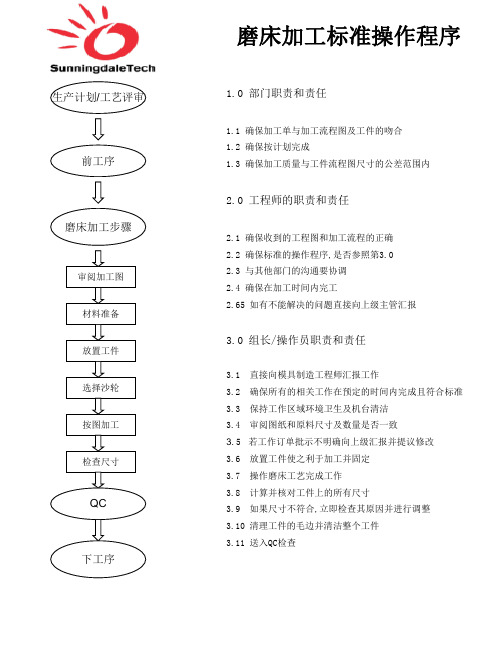
QC
3.9 如果尺寸不符合,立即检查其原因并进行调整 3.10 清理工件的毛边并清洁整个工件 3.11 送入QC检查
下工序
EDM加工标准操作程序
生产计划/工艺评审
1.0 部门职责和责任
1.1 确保加工过程中涉及到的尺寸.R角.尖角的正确 1.2 确保电极与加工设定图相一致 1.3 确保加工质量与工件流程图尺寸在公差之内 1.4 确保按计划完成
前工序
EDM加工步骤
2.0 制造工程师职责和责任
2.1 确保收到的图纸和加工流程的正确 2.2 确保电极已按照计划准备就绪 2.3 确保流程程序由组长或操作工正确执行
审阅加工图
检查工料
2.4 确保加工时间是在计划时间内完成 2.5 与其他部门的沟通要协调
ATC编程
2.6 如有不能解决的问题直接向精加工主管汇报
放置工件
3.0 组长/操作员职责和责任
3.1 确保电极设定图与电极外型.尖角和R角相一致 3.2 确保电极尺寸和3R中心与固定的尺寸一致
校表分中
3.3 控制不同高度/尺寸的电极偏差范围在0.02MM内 3.4 确保电极只带有一个基准角
X.Y.Z编程
3.5 拒绝使用带有不同基准角的电极 3.6 确保安装单和电极单之间相互一致
放置工件
3.0 组长/操作员职责和责任
3.1 直接向模具制造工程师汇报工作
选择沙轮
3.2 确保所有的相关工作在预定的时间内完成且符合标准 3.3 保持工作区域环境卫生及机台清洁
按图加工
3.4 审阅图纸和原料尺寸及数量是否一致 3.5 若工作订单批示不明确向上级汇报并提议修改
检查尺寸
3.6 放置工件使之利于加工并固定 3.7 操作磨床工艺完成工作 3.8 计算并核对工件上的所有尺寸
JBT 9919-1999 高精度无心外圆磨床 精度检验

ICS 25.080.50J 55JB/T 9919-1999高精度无心外圆磨床精度检验1999-05-20 发布2000-01-01 实施国家机械工业局发布JB/T9919-1999前言本标准是在ZB J55 030—88《高精度无心磨床精度》的基础上修订的。
本标准与ZB J55 030—88的技术内容一致,仅按有关规定重新进行了编辑。
与本标准相配套的标准有:GB/T 6470—1986无心外圆磨床参数JB/T 9905.1—1999无心外圆磨床系列型谱JB/T 9905.2—1999无心外圆磨床技术条件本标准自实施之日起代替ZB J55 030—88。
本标准由全国金属切削机床标准化技术委员会提出。
本标准由全国金属切削机床标准化技术委员会磨床分会归口。
本标准负责起草单位:无锡机床厂。
本标准于1988年11月首次发布。
11 范围本标准规定了高精度无心外圆磨床的几何精度检验和工作精度检验的要求及检验方法。
本标准适用于最大磨削直径至200 mm 的高精度无心外圆磨床。
2 引用标准下列标准所包含的条文,通过在本标准中引用而构成为本标准的条文。
本标准出版时,所示版本均为有效。
所有标准都会被修订,使用本标准的各方应探讨使用下列标准最新版本的可能性。
GB/T 17421.1—1998 机床检验通则 第1部分:在无负荷或精加工条件下机床的几何精度3 一般要求3. 1使用本标准时,应参照GB/T 17421.1的有关规定。
尤其是检验前的安装、主轴及其他部件的空运转升温、检验方法和检验工具的精度。
3. 2 参照GB/T 17421.1—1998中3.1的规定调整安装水平。
3. 3 检验前一般可按装拆工具和检验方便、热检项目的要求安排实际检验次序。
3. 4当实测长度与本标准规定的长度不同时,允差应根据GB/T 17421.1—1998中2.3.1.1的规定按能够测量的长度折算。
折算结果小于0.001 mm 时,仍按0.001 mm 计。
磨床能力等级评定标准

二、制造部经理
能力要求:
1、计划执行能力
2、下属激励能力
3、判断能力
4、责任心
5、沟通能力
6、承压能力
评估内容:
三、生产主管
能力要求:
1、培养指导能力
2、组织协调能力
3、理解能力
4、责任心
5、沟通能力
6、自控能力
评估内容:
四、磨床操作工
能力要求:
1、责任心
2、执行能力
3、理解能力
4、学习能力
5、承压能力
6、自控能力
评估内容:
五、主操手
能力要求:
2、责任心2、执行能力
3、理解能力
4、学习能力
5、承压能力
6、自控能力
备注:
评估考核定级规则:能够达到最低标准的那一项为员工的起评点,当最低标准
上有超过2个及以上并且最低能力项中只有一项则可上调一级,若最低能力项中有两项或以上则工资就执行该项标准。
模具部加工公差标准
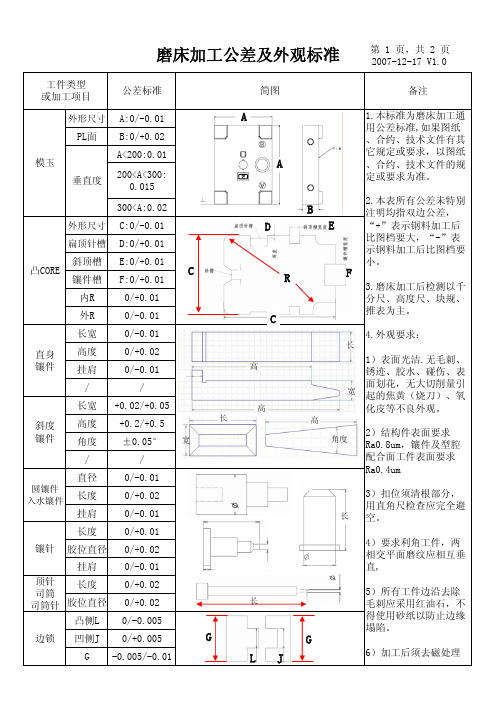
顶针板 斜顶扣 长宽:+0.03/+0.05 装配位 深度:0/+0.02
铲机槽 边锁位
行位槽 斜顶扣装配位
EDM加工公差标准
加工类型
公差标准 (任意点公差)
说
2007-12-17 V1.0
明
前模胶位 后模胶位
0/+0.05 ±0.05
纹面符合工艺要求,形状与3D图档一致;表面无 碰伤、积碳、砂孔;未注要求时表面粗糙度 Ra1.6-3.2(CH24-30),平面度≤10um
简图
PL
0/+0.02
PL
管位
凹:±0.01 凸:0/-0.02
边锁位 0/+0.005
行位槽 +0.005/+0.01
模玉
藏CORE位 +0.005/+0.01 前模:+0.03/+0.05 行位槽
胶位 后模:0/+0.05
碰穿位 0/+0.02 擦穿位 0/+0.02
藏CORE位
挂肩
0/+0.01
长度
0/-0.1
压板 宽度
0/-0.01
高度 +0.005/+0.01
P
0/-0.01
L
L 斜顶
M
0/+0.02 0/-0.01
导向块 斜顶扣
N 长宽 厚度 长宽高 挂肩
0/+0.1 宽 0/-0.02 0/-0.02 0/-0.02 0-/0.01
长 高
框底与模胚 背面高度
0/+0.02
A板厚度 0/-0.02
公差标准
简图
备注
- 1、下载文档前请自行甄别文档内容的完整性,平台不提供额外的编辑、内容补充、找答案等附加服务。
- 2、"仅部分预览"的文档,不可在线预览部分如存在完整性等问题,可反馈申请退款(可完整预览的文档不适用该条件!)。
- 3、如文档侵犯您的权益,请联系客服反馈,我们会尽快为您处理(人工客服工作时间:9:00-18:30)。
磨床加工标准
批量加工时,填写自检表需参照以下标准:±0.002mm公差,5件以下全检,5-20件全检,20件以上全检;0.002-0.01mm公差,5件以下全检,5-20件检5件以上,20件以上检8件以上;0.05mm以上公差,5件以下检2件以上,5-20件检4件以上,20件以上检6件以上。
成型位置需留神,下刀前确认清楚成型部位,用奇异笔在零件上表示出来,多次确认无误后再进行加工。
加工过程中应考虑到因材质不同零件的发热量,砂轮磨损故要预留足够的余量精磨。
以下为控制发热标准:
1.1粗磨工件预留0.2mm余量时进行第一次冷却。
此时下刀进给量0.02-0.03mm/次,加工至余量0.1mm时进行第二次冷却。
1.2此时下刀进给量0.01mm/次,加工至余量0.06mm时进行第三次冷却,最终在表面没有烧刀,平面度较好,完全冷却的情况下预留0.04mm给精磨。
1.3加工材质较软时,如铜、铝粗磨时需上油避免粘砂轮,最终留量不小于0.06mm。
再进行精磨。
1.4在精磨时,每次下刀进给量0.001-0.005mm,前后走刀要慢,保证没有火花。
用手接触工件,如有发热用酒精或挡块及时冷却,保证工件彻底冷却后,再进行加工到位。
1.5如果光洁度要求较高时,可以上油冷却及增加光洁度。
对于硬度HRC60以上的刚材,如SLD、SKH51、ASP23、留量0.04mm时要进行半精磨。
下刀量0.005-0.01mm/次,加工至余量0.016mm时,再对其精磨。
1.6对于面积较大及较长的工件,可以将工件摆30度、60度、90度加工,以减少接触面
积,避免发热及烧刀而引起变形或尺寸变小。
工件余量很多的情况下,砂轮磨削不利时要及时修锐,也可选用水磨进行逃料以减少发热。
发热量较大时要中途冷却,以免发热太大而使工件退火或影响其它尺寸。
2.工作平台的修整,尽量选择直径较小的46J砂轮,修整时平台必须处于吸磁状态下。
2.1平台平面度较差时,要先进行粗修,粗修砂轮转速为2000-2400转/分,上下进刀量为0.01-0.03mm,粗修平台转速为2000转左右,上下进刀量为0.001-0.005mm;
2.2精修砂轮转速为1800-2400转/分,上下进刀量为0.001-0.003mm,精修平台转速为1800-200转/分,上下进刀量为0.000-0.001mm;
2.3修整平台时需要注意,各方向手柄摇动须均匀一致,绝对不允许将旋转之砂轮停留在平台上,否则停留处会被吃刀而难以修平,修整过程中必须眼观,耳听,不得有大火花出现,走刀要连续勿撞击到行程限位块,可在修整时加上润滑油,可以减少磨擦,降低发热量。
修整完后可用千分表或油性笔来进行检验。
3.平面的加工。
3.1粗磨目的去除余量,粗修砂轮转速2000转/分,上下进刀量0.05-0.07mm,前后手柄一次进,快速,不可退回,粗磨工件转速3000-3600转/分,上下进刀量0.05-0.1mm,前后匀速前进;
3.2精磨目的保证尺寸及加工要求,精修砂轮转速2600-3000转/分,上下进刀量
0.001-0.005mm,前后均匀空走三次,精磨工件转速1800-2000转/分,上下进刀量
0.001-0.005mm。
冷却及留量标准参照第1条。