PFMEA、控制计划及作业指导书培训(全面)资料
PFMEA培训教材
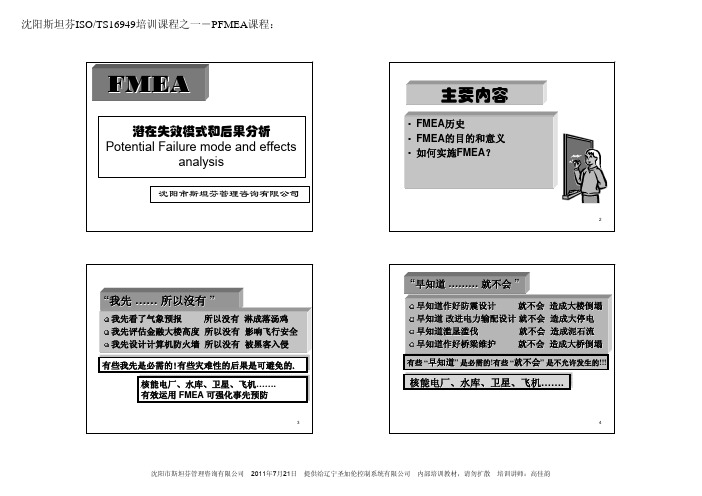
工作范围
组长
小组成员
第一 PFMEA小组 第二 PFMEA小组
第三 PFMEA小组
第四 PFMEA小组
第五 PFMEA小组
原材料进货- 张威/技术 李兰/质量
OP30
科科长 吴伟/车间
张军/设备 刘洁/模具
OP40-OP100
高汉生/质 量科
李兰/质量 黄伟亮/车间
张军/设备 刘生/刀具
OP110OP150
沈阳斯坦芬ISO/TS16949培训课程之一-PFMEA课程:
FMEA团队方法
• FMEA的编制通常指派到某个人,但FMEA的 输入应是小组人员的努力。
• 小组的人员组成:应由知识丰富的横向部 门人员组成,如:
设计、试验、制造、装配、服务、质量、 设备、工装等方面人员组成。 必要时包括供方、顾客的相关人员。 • 完善的FMEA需小组成员认真的态度和精诚
10
FMEA的益处
1. 确保所有风险被尽早识别并采取措施 2. 确定改进优先级 3. 减少废品、返工和制造成本 4. 减少出厂后的失效、降低保修成本 5. 减少“召回”的发生概率
11
12
沈阳市斯坦芬管理咨询有限公司 2011年7月21日 提供给辽宁圣加伦控制系统有限公司 内部培训教材,请勿扩散 培训讲师:高佳韵
过程流程图 PFMEA
控制计划
现场作业指导书 检验作业指导书
反应计划
35
FMEA团队方法
• FMEA不是:
个人行为 简单的会议
• FMEA必须: 由团队完成 头脑风暴(Brainstorm)
36
沈阳市斯坦芬管理咨询有限公司 2011年7月21日 提供给辽宁圣加伦控制系统有限公司 内部培训教材,请勿扩散 培训讲师:高佳韵
PFMEA_培训教材

过程流程分析
从高层次流程图到详细的流程图 [ 从宏观到微观 ]
10 20 30 40
50
60
30.1
30.2
30.3
30.4
30.5
30.6
CASE STUDY
• • • • 请结合某个具体产品识别初始流程图。 分小组分别讨论某一具体工序。 学员发表 教师点评
过程FMEA示例
潜在失效模式及后果分析(PFMEA)
– 最终顾客 – 直接顾客(下一道工序) – 中间顾客(下游工序)
• 失效模式的后果还包括对安全、环境和法规的影响 • PFMEA中描述的失效后果应与DFMEA中描述的保 持一致。
识别失效后果时的问题
1. 潜在失效模式会阻止下游工序的进行或对设备或
操作者造成潜在伤害吗?
在某工序无法装配 在顾客处不能连接 在顾客处不能附着 在某工序无法钻孔 在某工序会造成工装额外的磨损 在某工序会损伤设备 在顾客处会伤害操作者
PFMEA编制作业指导书

PFMEA编制作业指导书PFMEA(Process Failure Mode and Effects Analysis)是一种用于根据潜在的失效模式和其对过程或产品所造成的影响的方法。
它可以帮助企业发现、评估和控制过程中的潜在问题,进而采取相应的预防措施。
以下是一份PFMEA编制作业指导书的模板,旨在帮助读者了解如何编制PFMEA。
一、背景在这一部分,首先要介绍PFMEA的目的和重要性。
重要性包括:提高产品质量、降低成本、提高生产效率、确保工艺稳定性等。
此外,还要说明编制PFMEA的前提条件,例如需要有一支专业的团队、对于所研究的过程有一定的了解等。
二、编制团队指导书需要明确编制PFMEA所需的团队成员,例如生产工程师、品质工程师、设计工程师等。
每个成员的职责应该清晰明确,确保团队协作高效。
三、编制步骤3.1 收集过程信息在这一步骤中,需要收集过程信息,包括工艺流程图、控制计划、产品规范、相关图纸等。
同时,还需要了解相关的制造工艺和设备,明确每个环节的输入和输出。
3.2 识别失效模式通过仔细分析过程信息,团队可以识别潜在的失效模式。
失效模式可能包括产品性能问题、工艺偏差、设备故障等。
每个失效模式都需要详细描述,包括其可能的原因、触发条件和影响。
3.3 评估失效影响对于每个失效模式,团队需要评估其对过程或产品的影响。
评估应该包括影响的程度、频率和持续时间。
评估的结果应该是一个科学的评分系统,能够准确反映失效的严重程度。
3.4 识别已有控制措施在这一步骤中,团队需要识别已有的控制措施,即已经采取的措施来防止或减轻失效的发生。
这些措施可以包括设计变更、工艺改进、设备维护等。
控制措施的有效性需要进行评估。
3.5 确定预防措施根据评估结果和已有的控制措施,团队需要确定额外的预防措施来防止失效的发生。
预防措施可以包括员工培训、操作规程改进、设备升级等。
预防措施需要具体、可行,并能够确保失效的概率降到最低。
3.6 确定检测措施当失效无法完全预防时,需要确定相应的检测措施,旨在尽早发现失效并采取相应的纠正措施。
PFMEA作业指导书

PFMEA作业指导书12020年4月19日编写:审核:批准:受控状态:发布日期: /05/08 实施日期: /05/181目的确定与产品和过程相关的潜在失效模式和潜在制造或装配过程失效的机理/起因,评价潜在失效对顾客产生的后果和影响,采取控制来降低失效产生频度或失效条件探测度的过程变量和能够避免或减少这些潜在失效发生的措施。
2范围凡本公司所有新产品/过程、修改过的产品/过程及应用、环境发生变更的原有产品/过程的样品试制和批量生产均适用。
3引用文件产品质量先期策划控制程序4术语和定义4.1 PFMEA:指Process Failure Mode and Effects Analysis(过程失效模式及后果分析)的英文简称。
由负责制造/装配的工程师/小组主要采用的一种分析技术,用以最大限度地保证各种潜在的失效模式及其相关的起因/机理已得到充分的考虑和论述。
4.2 失效:在规定条件下(环境、操作、时间),不能完成既定功能或产品参数值和不能维持在规定的上下限之间,以及在工作范围内导致零组件的破裂卡死等损坏现象。
4.3 严重度(S):指一给定失效模式最严重的影响后果的级别,是单一的FMEA范围内的相对定级结果。
严重度数值的降低只有经过设计更改或重新设计才能够实现。
4.4 频度(O):指某一特定的起因/机理发生的可能性,描述出现的可能性的级别数具有相对意义,但不是绝正确。
4.5 探测度(D):指在零部件离开制造工序或装配之前,利用第二种现行过程控制方法找出失效起因/机理过程缺陷或后序发生的失效模式的可能性的评价指标;或者用第三种过程控制方法找出后序发生的失效模式的可能性的评价指标。
4.6 风险优先数(RPN):指严重度数(S)、频度数(0)及探测度数(D)的乘积。
4.7 顾客:一般是指“最终使用者”,但也能够是随后或下游的制造或装配工序,维修工序或政府法规。
5职责5.1 过程失效模式及后果分析(PFMEA)制定:技术部。
过程流程图,控制计划,PFMEA培训

2020/3/30
宏观的描述 装配DVD盖板
DVD总成进入流程(传送带 传送带停止(12秒) 操作人取出盖板
操作人将盖板镶边卡进DVD总成 操作人将DVD盖板放平
操作人取出两个螺钉 工作人员取出风枪
操作人用两个螺钉将盖板和DVD总成拧紧 操作人打拧紧标示 自检 ———
微 观 的 活 动
标准的过程流程图
2020/3/30
———
过程流程图含义
1
如果组织对新零 件的共通性已经 过评审,同一份 过程流程图可适 用于相似零件家 族的生产过程.
2
过程流程图分初 始过程流程图, 试生产过程流程 图和生产过程流 程图
3
过程流程图有宏 观和微观两种。
2020/3/30
———
宏观的过程流程图只是列出各个工序流程。微观的过程 流程图需详细到各个工步,进行这样的分析是为后面用 头脑风暴的方法来分析失效模式做准备。
2020/3/30
———
过程流程图的输入
2020/3/30
1. 图纸(工艺要求, KPC/PQC …) 2. 类似产品,相关人员的经验和教训 3. DFMEA 4. 开发过程中的质量问题 5. PFC 标准表格 6. …
———
过程流程图的重要性
1. 通常它是过程的第一“景象” 2. 提供代表过程方向的物流图形 3. 过程流程图是PDR的重要输入 4. 帮助项目团队对过程有一个全面的,统一的了解。 5. 用于 PMFEA,控制计划,模具布局,工作场地
平面图等的基础。 6. 为过程开发提供了交流和分析的工具。
2020/3/30
———
过程流程图的审核要点
1. 过程流程图是否进行了动态更新
2. 过程流程图与控制计划,PFMEA的一致性
PFMEA培训资料
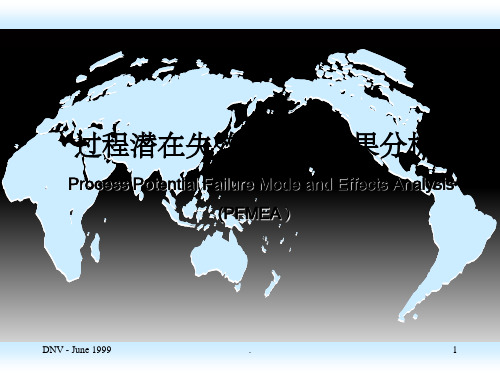
用系统的方法做改进
FAILURE PREVENTION THROUGH
TEAMWORK
通过团队合作预防失败
Once we have same vision, we have already achieved half
of success
一旦拥有共识,事情已成功一半
DNV - June 1999
.
9
9
DNV - June 1999
.
26
26
PFMEA 的开发
PFMEA运用的时机 ※ 一般的原则,FMEA使用得越早越好,这样才能最大限度地消除 或降低设计的错误
① 当设计新的制程(或设备),在进行概念设计或草图时就 可开始作PFMEA
②当制程(或设备)有新的应用或变更时
③当现有制程(或设备)被考虑要进行改善时
③ 设计工程师(Design Engineer) ④ 项目工程师(Project Engineer) ⑤ 维修工程师(Maintenance Engineer)
DNV - June 1999
.
30
30
PFMEA 的开发
小组成立
⑥ 质量工程师(Quality Engineer) ⑦ 模具工程师(Tooling Engineer) ⑧ 组装作业员(Production Operator) ⑨ 其他:供应商、销售人员等(Supplier、Sales etc.)
推倒
DNV - June 1999
.
4
4
什么是FMEA?
”早知道 ……… 就不會……… ”
早知道 作好防震設計 就不會 造成大樓倒塌 早知道 改進電力輸配設計 就不會 造成全市大停電 早知道 不濫墾濫伐 就不會 造成泥石流 早知道 作好橋樑維護 就不會 造成大橋倒塌
PFMEA培训资料

极低:失效不太可能发生
≤0.01个,每1000件 1/1500000
1
四、具体定义说明
3.检出率(Detectability)该failure mode的检出可能性
不可探测度 几乎不可能 非常微小 微小 很小 小 中等 中上 高 很高 几乎肯定
评价标准 绝对不可探测 现行控制探测度非常微小 现行控制探测度微小 现行控制探测度很小 现行控制可以探测出 现行控制探测度中等 现行控制探测度中上 现行控制探测度高 现行控制探测度很高 现行控制肯定探测得出 V V V V V V V V V 检验类型 A B C V V V V V 建议的探测方法范围 不能探测,或不检查控制 不直接的,或仅仅随机检查控制 仅仅目视检查控制 仅进行两次目视检查控制 采用图表方法控制,如SPC 在零件离开工位后,采用计量型检具进行控制,或计数型检具检验 进行100%检验进行控制 在后续操作中进行差错探测,或作业准备检查和首件检验 (仅针对作业设定起主导原因的过程) 在工位上的差错探测, 或在后续操作中通过多种认可进行差错探测: 供给、选择、配装、验证。不会接受偏差零件 在工位上的差错探测(带自动停止功能的自动监测), 偏差零件不会被通过 不会制造出偏差零件,因为已通过过程/产品设计,采用了防错
打分
10 9 8 7 6 5 4 3 2 1
四、具体定义说明
4. RPN(risk priority number)—风险优先系数
RPN=S*O*D=严重度*频率*检出率
● 我们进行PFMEA的目的是通过降低O
和D的分值来实现解决该失效模式。
● 改善对策主要围绕怎样降低发生频率
(防错)、提高检出率来进行。
● FMEA目的是发现、评价产品/过程中潜在的失效及其后 果;找到能够避免或减少潜在失效发生的措施并且不断 地完善。
PFMEA培训

品质部培训课程
B. FMEA概要介绍
FMEA的应用:
设计FMEA: 针对产品本身,产品设计、开发时期的分析技术。 主要是设计工程师和其小组应用。
系统FMEA:针对产品系统,考虑系统和系统间交互作用。 过程FMEA:
严 级 重 别 度 7 B
3 3
潜在失效模式 (10)
所谓潜在失效模式是指过程可能发生的不能满足过程或 设计要求的状况。是对某一作业可能发生的不符合性的描 述。 失效状态是以作业为单元进行。 只有以作业为审查单元时,才能把失效模式与产品和过程特 性相联系。 上游作业中的失效模式应在那层进行表述。 在确定失效模式时,试问:
风 险
建议 措施
潜在 失效 模式
现行控制 预防 现行控制 探测
影 响
原 因
现行 控制
风 险
建议 措施
现行 控制
原 因
现行 控制
风 险
建议 措施
P-FMEA输出
·过程/零件潜在失效模式的清单。 ·潜在关键特性和重要特性清单。
·消除或减少产品失效模式出现频次的过程改进措施清
单。 ·提供全面的过程控制策略。
若失效模式可能影响安全或导致违反法规,需清楚描述。
潜在影响、严重度和分级 (11-13)
表 4.2 部分通常的潜在影响清单 外观不良 ■ 顾客不满意 ■ 影响美观 ■ 不能紧固 ■ 异色 ■ 工件在后续作业中阻塞 ■ 雨水进入汽车 ■
■ ■ ■ ■ ■ ■ ■
功力损失 时强时弱 不能上锁 不可显示 配合性差 粘着于模具 等等
- 1、下载文档前请自行甄别文档内容的完整性,平台不提供额外的编辑、内容补充、找答案等附加服务。
- 2、"仅部分预览"的文档,不可在线预览部分如存在完整性等问题,可反馈申请退款(可完整预览的文档不适用该条件!)。
- 3、如文档侵犯您的权益,请联系客服反馈,我们会尽快为您处理(人工客服工作时间:9:00-18:30)。
• 必须有整体性的规划,并且循序渐进地逐步改善企业的研发环 境
8
汽车工业的质量管理系统 7/12/2019
▫ 改善现有之可靠度工程分析工具(如FMEA、FTA等)作为 前端工程作业,以提高开发产品过程中之工程决策支援,并 发展新的前端工程分析工具。
7
7/12/2019
汽车工业的质量管理系统
• 汽车工业的质量管理系统之各种作业程序与参考手册,成为美 国汽车工业共同的作业准则,其将被TS16949替代并已成为全 世界汽车行业共同规范。
有些 早知道 是必需的!有些 就不会 是不允许发生的
• 核电厂、水库、卫星、飞机、十大召回事件… …
有效运用 FMEA 可减少事后追悔
15
二、FMEA的基本概念
7/12/2019
“我先… …所以没有”
• 我先 看了气象预报 所以没有 淋成落汤鸡 • 我先 评估金融大楼高度 所以没有 影响飞机安全 • 我先 设计电脑放火墙 所以没有 被骇客入侵 • 我先 作好桥梁设计 所以没有 造成重庆彩虹大桥倒塌
控制计划必须…………. 当发生影响产品、制造过程、测量、物流、供应资源或
FMEA的变化时,必须对控制计划进行评审和更新(见 7.1.4)。
14
二、FMEA的基本概念
7/12/2019
“早知道… …就不会”
• 早知道 作好防震设计 就不会 造成大楼倒塌 • 早知道 改进电力输配设计 就不会 造成美国等国的大停电 • 早知道 不滥砍滥伐 就不会 造成泥石流 • 早知道 作好桥梁设计 就不会 造成重庆彩虹大桥倒塌
TS16949汽车工业质量体系要求
ISO9001质量管理体系要求
客户要求 TS16949+IATF PPAP/客户特殊要求
质量手册 程序文件 作业文件/记录
客户参考手册 APQP&CP FMEA MSA SPC
9
7/12/2019
ISO/TS16949中的 失效模式和后果分析
• 7.3.1.1 多方论证方法 组织必须使用多方论证方法进行产品实现的准备工作,包 括: - 特殊特性的开发/最终确定和监测 - FMEA的开发和评审,包括采取减少潜在风险的 措施 - 开发和评审控制计划。
11
7/12/2019
ISO/TS16949中的 失效模式和后果分析
• 7.3.3.1 产品设计输出-补充 产品设计输出必须用能够与产品设计输入要求进行验证和 确认的方式表示。产品设计输出必须包括:
- 设计FMEA、可靠性结果, - 产品特殊特性、规范, - 产品防错、适用时, - 产品定义、包括图纸和数学数据 - 产品设计评审结果, - 特征指南,适用时。
有些 我先 是必需的!有些 所以没有 是可预期避免的
• 核电厂、水库、卫星、飞机、十大召回事件… …
有效运用 FMEA 可减少事后追悔
16
二、FMEA的基本概念
7/12/2019
• 及时性是成功实施FMEA的最重要因素之一。
• 它是“事前的预防”而不是“事后的追悔”。
• 事先花时间进行FMEA分析,能够容易且低成本地对 产品设计或制程进行修改,从而减轻事后修改的危机。
1
PFMEA , CP , WI 过程潜在失效模式和后果分析、 控制计划及作业指导书
7/12/2019
课程目标
• PFMEA 开发 • 控制计划方法论 • 作业指导书
2
7/12/2019
•
ISO 9001主任审核员 QS-9000 主任审核员 ISO/TS 主任审核员 IRCA 注册主任培训师
4
12
7/12/2019
ISO/TS16949中的 失效模式和后果分析
• 7.3.3.2 制造过程设计输出 制造过程设计输出必须用能够与制造过程设计输入要求进行
验证和确认的方式体现。制造过程设计输出必须包括: - 规范和图样, - 制造过程流程图/布局 - 制造过程FMEA, - 控制计划, - 作业指导书,
• FMEA能够减少或消除因修改而带来更大损失的机会, 它是一个相互作用的过程,永无止境的改善活动。
17
二、FMEA的基本概念
7/12/2019
FEMA内容:
• 利用表格方式协助工程师进行工程分析,使其在工程设计早期发现潜在 缺陷及其影响程度,及早谋求解决之道,以避免失效之发生或降低其发 生时/TS16949中的 失效模式和后果分析
• 7.3.2.3 特殊特性 组织必须明确特殊特性,并且: - 在控制计划中包括所有特殊特性 - 与顾客特定的定义和符号相一致 - 过程控制文件,包括图纸、FMEA、控制计划、和
操作指导书,必须标明顾客的特殊特性符号,或组织的等 效符号或记号,以包括的特殊特性有影响的过程步骤。
6
汽车工业的质量管理系统 7/12/2019
•: ▫ TS16949,QS9000为汽车工业的品质管理系统,其以持续 改进为目标,强调缺点预防,降低品质差异,减少生产过程 的浪费与废弃物。
▫ 面对市场开放与日本的竞争压力,美国福特、克莱斯勒、通 用汽车等三大汽车厂共同主导制定QS9000品质系统,并结 合美国品管学会(ASCQ)与车辆工程学会(SAE),开始研 究如何将可靠度之失效预防观念工程技术导入汽车业。
…….
13
7/12/2019
ISO/TS16949中的 失效模式和后果分析
• 7.5.1.2 控制计划 组织必须:
- 针对所提供的产品在系统、子系统、部件和/或材料层 次开发控制计划(见附录A),包括由组织生产的散装材料,
- 在试生产和生产阶段有控制计划,利用设计FMEA 和制 造过程 FMEA 的输出。
7/12/2019
何谓FMEA
• FMEA是一组系统化的活动,其目的是
▫ 发现、评价产品/过程中潜在的失效和后果。 ▫ 找到能够避免或减少这些潜在失效发生的措施。 ▫ 书面总结上面的过程。 ▫ 确保顾客满意,这是对设计过程的完善。
5
7/12/2019
FMEA发展史
• 虽然许多技术人员在他们设计或制造过程中应用 了FMEA这分析方法。但首次正式应用技术是在六 十年代中期的航天工业中的一项革新。