冲压模具
冲压模具的基础知识
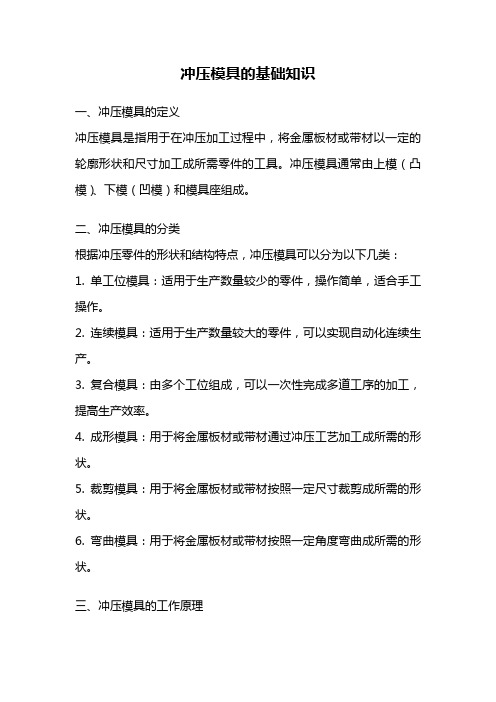
冲压模具的基础知识一、冲压模具的定义冲压模具是指用于在冲压加工过程中,将金属板材或带材以一定的轮廓形状和尺寸加工成所需零件的工具。
冲压模具通常由上模(凸模)、下模(凹模)和模具座组成。
二、冲压模具的分类根据冲压零件的形状和结构特点,冲压模具可以分为以下几类:1. 单工位模具:适用于生产数量较少的零件,操作简单,适合手工操作。
2. 连续模具:适用于生产数量较大的零件,可以实现自动化连续生产。
3. 复合模具:由多个工位组成,可以一次性完成多道工序的加工,提高生产效率。
4. 成形模具:用于将金属板材或带材通过冲压工艺加工成所需的形状。
5. 裁剪模具:用于将金属板材或带材按照一定尺寸裁剪成所需的形状。
6. 弯曲模具:用于将金属板材或带材按照一定角度弯曲成所需的形状。
三、冲压模具的工作原理冲压模具通过上模和下模之间的相对运动,将金属板材或带材置于模具座上,然后施加压力使其发生塑性变形,最终得到所需的零件。
四、冲压模具的主要构成部分1. 上模(凸模):也称为冲头,是冲压模具中与下模相对应的零件,用于施加压力。
2. 下模(凹模):也称为模座,是冲压模具中与上模相对应的零件,用于支撑工件和定位。
3. 模具座:用于固定上模和下模的基座,通常由钢板焊接而成。
4. 引导柱和导套:用于引导和定位上模和下模的相对位置,确保模具的精度和稳定性。
5. 推杆和导向机构:用于传递压力和控制上模和下模的运动轨迹。
6. 压力调节机构:用于调节上模和下模施加的压力大小。
7. 模具材料:通常采用高硬度、高强度的合金工具钢或硬质合金制作,以保证模具的耐用性和使用寿命。
五、冲压模具的制造工艺冲压模具的制造工艺通常包括以下几个步骤:1. 设计:根据零件的形状和尺寸要求进行模具设计,确定模具的结构和工艺参数。
2. 材料准备:选择合适的模具材料,并进行切割、锻造或热处理等预处理工艺。
3. 加工制造:采用数控机床、电火花机等设备进行精密加工,包括车削、铣削、钻孔等工序。
冲压模具及工艺简介

结构
通常由多个单工序模具组合而成 ,材料通过送料器连续送入模具
中。
特点
生产效率高,适合大批量生产。 但模具结构复杂,制造成本高。
复合模具结构及特点
定义ቤተ መጻሕፍቲ ባይዱ
复合模具是指在一个压力机上,可以同时完成多 个冲压工序的模具。
结构
通常由多个模具组合而成,每个模具完成不同的 工序,材料通过送料器连续送入模具中。
特点
生产效率非常高,适合大批量生产。但模具结构 非常复杂,技术要求高,制造成本非常高。
03
冲压工艺流程及要点
Chapter
冲压件的工艺性分析
01
分析冲压件的形状和尺寸是否适合冲压加工,考虑是否容易制造、成本低廉、使 用性能高等因素。
02
考虑冲压件的材料性质、力学性能、表面质量等,以及尺寸精度、形状复杂程度 等要求。
模具分类
根据成型材料和工艺的不同,模 具可分为塑料模具、金属模具、 玻璃模具等。
模具在生产中的重要性
01
02
03
提高生产效率
使用模具可以大幅提高生 产效率,降低生产成本。
保证产品质量
模具的设计和制造精度直 接影响产品的质量和稳定 性。
促进产品创新
模具技术的发展为产品创 新提供了可能,使得企业 能够快速响应市场需求。
冲压模具及工艺简介
汇报人: 2023-11-29
目录
• 冲压模具概述 • 冲压模具结构及特点 • 冲压工艺流程及要点 • 冲压模具材料及热处理 • 冲压模具的制造及维护 • 冲压模具在现代工业中的应用及前景
01
冲压模具概述
Chapter
模具的定义及分类
模具定义
模具是一种用于成型、整形、冲 压、挤出、注塑等工艺的工艺装 备。
冲压模具的组成及各零件作用

冲压模具的组成及各零件作用冲压模具的组成可谓是个复杂却又充满乐趣的世界,像一场机械的“家庭聚会”,每个零件都有自己独特的角色。
首先说说模具的上半部分,叫做“上模”,这个家伙就像个天花板,负责将材料压制成型。
哎呀,它可真是个强壮的角色,毕竟它得忍受巨大的压力,简直就是力气活儿。
然后是“下模”,这个就像个忠实的地基,稳稳地接住上模带来的所有重量,没它可不行啊,毕竟上面再强壮,没有个好的支撑,最终还是得塌。
接下来得提提“导柱”和“导套”了,这对小搭档真是默契得不得了,像双胞胎兄弟,负责确保上下模具的对齐。
没有他们,模具可就乱套了,部件可能会错位,结果就是“赔了夫人又折兵”,一切都得重来,真是得不偿失。
还有“压料板”,这个家伙有点像“门卫”,守住材料的去向,确保它不会在模具中四处乱窜,挺辛苦的。
再来聊聊“弹簧”,哎,这个小东西可真灵活,它负责模具开合时的反弹,确保模具能够顺畅地工作。
想想看,要是没有它,那模具就得一直维持在一个状态,活得简直太累了。
还有“定位块”,它像是模具中的“GPS”,确保各个零件在合适的位置,不然一不小心就会走偏,造成大麻烦。
然后,咱们不能忘了“卸料板”,这个小家伙就像是个贴心的服务员,负责把成品轻轻送出来,确保每一个部件都能顺利地离开模具。
想象一下,如果没有它,成品就得在模具里“闷”着,真是太不划算了。
还得提提“润滑系统”,这可真是模具的“油条”,让所有的零件都能顺畅运作,不至于卡在一起,毕竟没有人喜欢“卡壳”的感觉。
冲压模具的每个零件都像是一个小角色,大家齐心协力,共同完成一项“大事业”。
每个零件都有自己的使命,没谁能少了谁。
模具的工作就是把一块平平无奇的金属,变成我们生活中各种各样的物品,从汽车零件到家电外壳,无不离不开它们的辛勤付出。
就像我们在生活中,每个人都有自己的角色,团队合作才能让事情变得顺利。
所以,冲压模具的组成及各零件的作用,真是让人感慨万千。
看似简单的模具背后,却隐藏着无数的智慧与设计。
冲压模具的基本结构及工作原理
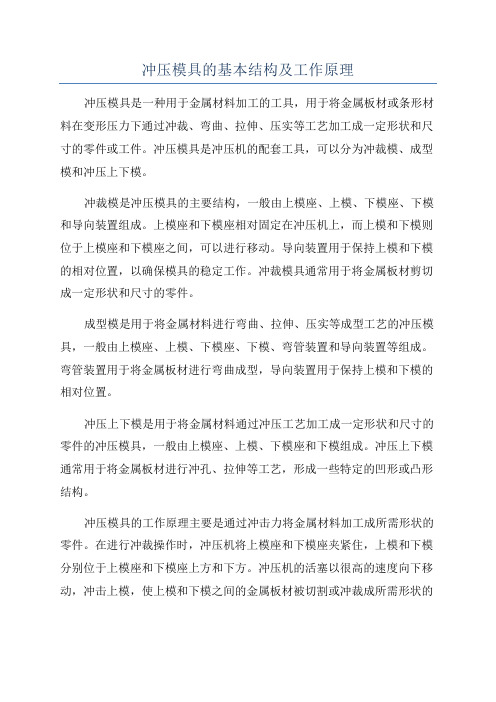
冲压模具的基本结构及工作原理冲压模具是一种用于金属材料加工的工具,用于将金属板材或条形材料在变形压力下通过冲裁、弯曲、拉伸、压实等工艺加工成一定形状和尺寸的零件或工件。
冲压模具是冲压机的配套工具,可以分为冲裁模、成型模和冲压上下模。
冲裁模是冲压模具的主要结构,一般由上模座、上模、下模座、下模和导向装置组成。
上模座和下模座相对固定在冲压机上,而上模和下模则位于上模座和下模座之间,可以进行移动。
导向装置用于保持上模和下模的相对位置,以确保模具的稳定工作。
冲裁模具通常用于将金属板材剪切成一定形状和尺寸的零件。
成型模是用于将金属材料进行弯曲、拉伸、压实等成型工艺的冲压模具,一般由上模座、上模、下模座、下模、弯管装置和导向装置等组成。
弯管装置用于将金属板材进行弯曲成型,导向装置用于保持上模和下模的相对位置。
冲压上下模是用于将金属材料通过冲压工艺加工成一定形状和尺寸的零件的冲压模具,一般由上模座、上模、下模座和下模组成。
冲压上下模通常用于将金属板材进行冲孔、拉伸等工艺,形成一些特定的凹形或凸形结构。
冲压模具的工作原理主要是通过冲击力将金属材料加工成所需形状的零件。
在进行冲裁操作时,冲压机将上模座和下模座夹紧住,上模和下模分别位于上模座和下模座上方和下方。
冲压机的活塞以很高的速度向下移动,冲击上模,使上模和下模之间的金属板材被切割或冲裁成所需形状的零件。
通过适当的模具结构设计和材料选用,冲压模具能够实现高速、高效、高精度的加工。
总之,冲压模具是一种重要的金属加工工具,其基本结构包括冲裁模、成型模和冲压上下模。
冲压模具通过冲击力将金属材料加工成所需形状的零件,具有高速、高效、高精度等优点。
冲压模具的设计和制造需要综合考虑多个因素,以满足零件的加工要求。
冲压模具组装基本知识

冲压模具组装基本知识一、模具结构认知冲压模具是一种用于冲压工艺的模具,其结构主要由以下几个部分组成:1.工作零件:包括凸模、凹模、凸凹模等,是模具的核心部分,用于形成冲压件的外形。
2.定位零件:包括定位销、挡料销、导正销等,用于确定被冲压材料的位置和方向。
3.压料装置:包括压料板、弹簧、压力板等,用于将被冲压材料压紧在工作零件上。
4.导向零件:包括导柱、导套等,用于保证模具在冲压过程中上下模的相对位置。
5.卸料零件:包括卸料板、弹簧、限位块等,用于将冲压件从工作零件上卸下。
6.支撑零件:包括上模座、下模座、垫板等,用于支撑和固定模具的各部分。
二、模具材质选择冲压模具的材质选择对模具的使用寿命和冲压件的品质有着重要的影响。
一般而言,冲压模具的材质应根据被冲压材料的性质、冲压工艺的要求和模具的使用条件等因素进行选择。
常用的模具材质包括优质碳素钢、合金钢、不锈钢、硬质合金等。
三、模具装配流程冲压模具的装配流程主要包括以下步骤:1.准备模具:检查模具各部分是否齐全、完好,如有需要,进行必要的修整和更换。
2.安装定位零件:将定位零件按照设计要求安装到模具上,确保被冲压材料能够准确定位。
3.安装工作零件:将工作零件按照设计要求安装到模具上,确保能够形成正确的冲压件外形。
4.安装压料装置:将压料装置按照设计要求安装到模具上,确保被冲压材料能够被压紧。
5.安装导向零件:将导向零件按照设计要求安装到模具上,确保模具在冲压过程中上下模的相对位置准确。
6.安装卸料零件:将卸料零件按照设计要求安装到模具上,确保冲压件能够被顺利卸下。
7.安装支撑零件:将支撑零件按照设计要求安装到模具上,确保模具能够被稳定支撑。
8.调试模具:对装配完成的模具进行调试,检查各部分是否工作正常,如有需要,进行调整和修复。
四、模具调试模具调试是确保模具正常工作的关键步骤,主要包括以下内容:1.检查各部分是否工作正常,如发现异常,进行修复或更换。
冲压模具概念

冲压模具概念一、概述冲压模具是用于加工金属材料的专用工具,它能够将金属材料在一定条件下进行变形、分离、翻折等加工操作。
冲压模具广泛应用于汽车、电子、家电等行业,是现代制造业中不可或缺的重要组成部分。
二、分类1.按照加工方式分类:(1)单向拉伸模:主要用于拉伸薄壁管材;(2)多向拉伸模:主要用于制造各种形状的壳体;(3)冲裁模:主要用于将板材切割成所需要的形状;(4)弯曲模:主要用于将板材弯曲成所需形状;(5)复合模:主要用于同时完成多种加工操作。
2.按照结构分类:(1)单步进模:只能完成一次加工操作;(2)连续进给模:可以完成多次连续加工操作;(3)复合式模:可以同时完成多种不同的加工操作。
三、结构组成1.上下模板:由大型钢板焊接而成,承载着整个冲压过程中产生的巨大力量。
2.导向柱与导套:导向柱固定在下模板上,导套则固定在上模板上,能够确保上下模板的相对位置不发生偏差。
3.顶针:通过顶针将金属材料固定在下模板上,以便进行加工。
4.切割刃:用于冲裁模具中将金属材料切割成所需形状。
5.弯曲块:用于弯曲模具中将金属材料弯曲成所需形状。
6.压花块:用于压花模具中将金属材料制造出各种花纹。
四、制造工艺1.设计:根据产品的要求设计出冲压模具的结构、尺寸、加工精度等参数。
2.制造:采用数控加工设备对冲压模具进行精密加工,确保其尺寸和精度符合要求。
3.组装:将各个零部件组装起来,并进行调试和测试,确保冲压效果达到要求。
4.维护:对已经使用的冲压模具进行定期检查和维护,延长其使用寿命。
五、应用领域1.汽车制造业:冲压模具广泛应用于汽车车身、底盘、发动机等部件的制造中。
2.电子制造业:冲压模具用于电子产品的外壳、散热器等部件的制造中。
3.家电制造业:冲压模具用于家电产品的外壳、零部件等的制造中。
4.建筑行业:冲压模具可以用于制造各种门窗、楼梯、栏杆等金属构件。
六、发展趋势1.高精度化:随着科技的不断进步,对冲压模具加工精度要求越来越高,未来将会出现更加精密化的冲压模具。
冲压模具及冲模设计

冲压模具及冲模设计引言冲压模具是冲压工艺中不可缺少的工具,通过将金属板材置于模具之间施加压力从而将其裁剪成所需形状。
冲模设计则是为了确保冲压过程能够顺利进行而进行的重要步骤。
本文将深入介绍冲压模具及冲模设计的相关内容。
一、冲压模具的分类根据冲压工艺的不同需求,冲压模具可分为以下几类:1.单工位模具:每工位完成一道工序,适用于简单形状的冲压件。
2.进料式模具:通过进料装置将金属板材连续送入模具进行冲压,适用于大批量生产。
3.连续式模具:在连续进行冲压的同时,实现多道工序的一体化,提高生产效率。
4.多工位模具:在一个模具上设置多个工位,适用于复杂形状的冲压件。
二、冲压模具的设计原则在进行冲模设计时,需要遵循以下几个原则:1.合理布局:模具的各个部分要合理分布,便于材料的进料、定位和排渣。
2.简化结构:尽量减少模具的零件数量和工艺复杂度,提高制作和维修的便利性。
3.提高刚度:通过加强模具的结构,提高其刚度和稳定性,以提高冲压精度和延长使用寿命。
4.正确选择材料:根据冲压件的材质和数量,选择合适的模具材料,以确保其耐磨性和抗拉强度。
三、冲模设计的步骤进行冲模设计时,需要按照以下步骤进行:1.冲压件分析:对冲压件进行分析,包括形状、尺寸、材质等方面的特点。
2.模具结构设计:根据冲压件的特点,设计模具的整体结构,包括上模、下模、导向机构等部分。
3.模具零部件设计:对模具的各个零部件进行设计,包括定位销、排渣孔、导向柱等。
4.模具加工制造:根据设计图纸,进行模具的加工制造,包括车削、铣削、磨削等工序。
5.模具调试和试模:对制造好的模具进行调试和试模,确保其能够正常运行。
6.模具维护和维修:及时进行模具的维护和维修,以延长其使用寿命和保证冲压质量。
四、冲压模具的常见问题及解决方法在冲压模具的使用过程中,可能会遇到以下常见问题:1.模具磨损:由于长时间使用和摩擦,模具表面可能会磨损,影响冲压质量。
解决方法包括定期维护和更换磨损部件。
冲压模的工作原理

冲压模的工作原理
冲压模的工作原理是通过冲击、挤压或者剪切的力量将金属或非金属材料加工成具有所需形状和尺寸的零件或产品。
冲压模具通常由上模和下模两部分组成,上模固定在冲压机上,下模固定在工作台上。
在工作时,冲压机的压力使得上模和下模闭合,材料置于两模之间。
当上下模闭合后,冲压机施加的压力使得上模和下模之间的空间逐渐减小,材料开始受到挤压、拉伸、剪切等力量的作用。
这些力量迫使材料发生塑性变形,并依照模具的凹凸形状逐渐成型。
在成型的过程中,冲压模具上通常还配备有进料装置、导向装置、保持装置等辅助设备,以确保材料的正确进入和成型。
冲压模具的工作原理基于冲压加工的基本原理,即通过外力作用使材料发生塑性变形,从而实现所需形状和尺寸的加工。
冲压模具经常应用于大批量生产,其工艺稳定性高,精度高,效率高。
冲压模具具有较高的刚性和强度,能够承受较大的外力和摩擦力,同时要求模具的设计和制造具有较高的精度和耐用性。
冲压模具的工作原理是通过合理的模具设计和制造,利用材料的塑性变形特性,通过冲压机施加的力量,使得材料按照模具的形状逐渐成型。
这种工作原理被广泛应用于汽车、电子、家电、航空航天等制造行业,以生产各种形状和尺寸的零件和产品。
- 1、下载文档前请自行甄别文档内容的完整性,平台不提供额外的编辑、内容补充、找答案等附加服务。
- 2、"仅部分预览"的文档,不可在线预览部分如存在完整性等问题,可反馈申请退款(可完整预览的文档不适用该条件!)。
- 3、如文档侵犯您的权益,请联系客服反馈,我们会尽快为您处理(人工客服工作时间:9:00-18:30)。
要:以簧片级进模的设计为例,介绍了高速冲压硬质合金模的结构,特别是在模具精度的保证,凸模与凹模的可调整性和关键零件的设计,材料的取用和加工等方面;进行了重点阐述。
;关键词:高速冲压;硬质合金;级进模
1 引言
随着高速冲压在国内的逐步推广,相应对模具的要求也越来越高,传统的依靠经验设计制造的模具其性能是不易保证的,特别是在模具的装配调试阶段,对模具钳工经验与技能的依赖性往往是和模具的质量与精度的可靠性成反比的。
2 零件工艺分析
外线簧片是保安单元上的一个零件,材料为QSn6.5-0.1,料厚0.3mm,外观要求无裂纹;毛刺,成形后表面电镀处理。
由于该零件批量需求很大,原采用普通级进模生产,但模具使用寿命不高,经常须刃磨,特别是易损部分更换频繁,而更换部分的互换性要求和重新装配后的精度要求不易保证(钳工碾配),故易产生不同批次冲压零件的一致性不高,因此决定利用引进高速冲压生产线开发高精密硬质合金级进模。
(我厂九十年代从法国引进了两条高速冲压生产线,理论冲压:0~1200次/min)。
本簧片的主要特点是弯曲部分多,且尺寸要求较高,在连续的高速冲压环境下模具工作部分易磨损,所以除在选取模具材料需要慎重考虑外对模具结构就提出了较高要求,主要是尽可能提高模具在冲床上的冲压时间,降低模具的等待时间,否则过多地拆卸整付模具进行修理,那么就失去了高速冲压的意义。
3 排样设计
总体布局上是利用零件中部的水平面段为连料载体,先逐步切外形分离废料,后压弯成形,最终切除载体分离零件。
3.1 步距的控制
由于冲压线上带有非常精确的数控自动送料装置,(误差0.01mm)所以此模具未采取侧刃定距,由活动初始挡钉确定条料的最初送料位置〔其位置的安排应避免后面薄片型凸模第一次的半料冲裁〕,送料装置定距,双排导正钉导正,为提高材料利用率,经产品设计部门同意增加了一个导正工艺孔,否则17~26步无法安排。
3.2 工步的安排
从条料的稳定性出发,开始尽可能保持条料的宽度,逐步切除变窄,压弯方面尺寸要求较高的应单独压,便于调整,压弯角度较大的分步压,避免材料的拉伸甚至断裂,弯曲的次序应从远端逐步向载体对称收缩,另外针对工艺分析中所说的为减缓压弯镶件的过快磨损,采取了两样措施:
〔1〕一组凸模与镶件连续两步同时压弯,使后一步的磨损大部分由前一步承担,如排样图11,12,13,14,21,22,23,24工位,通过镶件上两条压痕深浅的对比,证明是有效的。
〔2〕设计时适当加大角度和曲率回弹的补偿值,同时使镶件与凸模之间的纵向压弯间隙略大于一个料厚,视磨损情况调节压弯深度〔冲压过程中进行调整〕给予补偿,其具体结构见我《解决弯曲成形件回弹的一种快速可调机构》一文〔《模具制造》2002第九期〕。
<;BR>4 模具结构和关键零件设计
(为清楚起见,省略一部分未画)总体上是采取了以卸料板为导向的三板式模具形式。
4.1导向结构
对高速冲压而言,模架的导向精度非常重要,可以说是整副模具的心脏,如图3所示,此模具采用乐三板式四导柱精密模架,而且必须是可拆卸式,除方便模板的加工外,更主要的是高速冲压环境下导柱和滚珠较一般模具易磨损,应及时更换,这就对其互换性要求非常高,一般说来由模架专业厂定做。
另外,还加装了四个小导柱。
4.2 限位装置
; 41,43上下限位柱闭合,42限位块与凹模套闭合,44限位条与大卸料板闭合的同时,冲裁与压弯到位,限位装置易加工〔尺寸可磨削至微米级〕,其主要作用有:
(一)确定模架的冲裁深度始终保持不变,刃模后通过增加镶片厚度维持原高度〔如图3中14,15,24〕,凸模采取压板固定嵌入式结构,直接装入固定板,可拆卸。
(二); 维持模板的平衡性〔关键是大斜料板相对于上下模板的平行度〕,通过双排对称6个限位块的平衡支撑,防止因条料偏离中心〔特别是初次送料〕而产生的卸料板倾斜趋势,保护导向精度,缓解导向磨损。
(三)通过左右两限位条和限位块的共同作用,使机床到达预设的下死点时模具刚性闭合,可将极细的碎屑强行压入条料,防止不必要的停车,保护设备和模具。
4.3 模板的设计加工与装配
为保证精度要求和便于维修更换,凹模与卸料板都采取了完全镶拼式,总体设计原则为:(一)的强度和刚度。
(二)变封闭式为敞开式,外形简单化,便于精加工与测量。
(三)尽量减少拼块数量,方便装配、拆卸与更换。
如图3所示,先线切割粗加工,再磨削精加工到尺寸要求,(0.001mm)具体为:
〔一〕镶件与拼合后型腔0~0.02mm过盈轻压入配合。
〔二〕凸模与卸料板型腔双面0.002~0.006mm间隙配合。
〔三〕凸模与固定板型腔双面0.01~0.02mm间隙配合。
〔四〕凸模与凹模型腔双面0.04mm间隙配合。
另外,最后装配销钉时为减少装配误差,采取镶套后粘合装配。
4.4 主要零件的材料及热处理
冲裁凹模镶件与凸模:硬质合金YG20,压弯凸、凹模ASP23〔引进〕凹模拼块、卸料板拼块、固定板:CrWMnHRC58~62,凹模套、固定板套、大卸料板、卸料钩:45#钢HRC43~48,其中大卸料板调质处理。
;4.5 卸料装置
〔一〕由于冲裁速度快,所以采用了卸料钩的形式〔传统的卸料螺钉高速下易松动〕。
〔二〕为使卸料力量均衡,防止卸料板倾斜受力,保护导向精度。
采用了可调节式弹簧预紧装置,可直接放入固定板套装配孔。
通过螺钉调节弹簧预压力。
使6个弹簧力量一致。
4.6 导料装置
主要采用侧导板、导料钉导料,抬料钉、托芯抬料,上弹顶钉弹料〔防止导正销向上带料〕。
另外,如果空位不够或为保证凹模拼块强度,可借用导正销让孔安置抬料钉,在抬料的同时让开导正销。
4.7 辅助装置
〔一〕告警销失步告警,当条料位置偏差,告警销不能进入导正孔而上浮,转化成横向运动传递至微动开关而停车。
〔二〕与冲裁同步间隙吹料和吸料,在切断工步安置浮动吹料钉,凹模座侧面安装了进气嘴,工件分离后随卸料板上浮吹出工件防止堆积;在下模座安装高压气泵同步吸料,防止废料上浮。
5 结束语
本文不止一次提到如何保证模架精度,对提高冲压而言,在加工手段上怎样达到模具精度要求固然重要,但在结构设计上如何对模具固有精度进行保护更为重要,但在结构设计上如何对模具固有精度进行保护更为关键,本模具目前已冲压零件600多万,现实际冲速500次/min。
在提高工作效率和产品质量、增强市场反应速度方面收到了良好效果。