供方审核检查表-125
供方质量体系和过程审核检查表(空表)
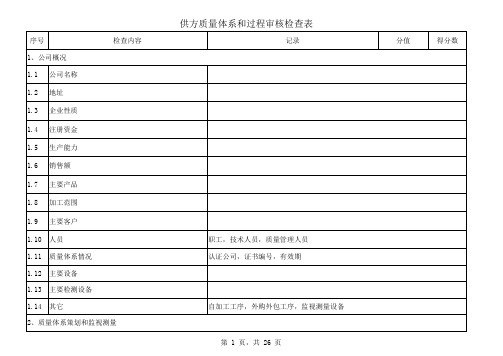
4.2
8
4.3
2
4.4
6
4.5
2
4.6
2
供方质量体系和过程审核检查表
序号 检查内容 记录 分值 得分数
5、采购/采购产品质量控制/供方控制 供方管理 —是否制定供方管理办法? —是否有经过批准的合格供方名录? —是否对供应商现场评审?现场发现的问题是否 关闭? —是否定期对供方进行业绩评价? —对业绩评价不合格的供方是否要求其整改或淘 汰? 采购管理 —是否签订采购订单,明确产品规格、数量、交 期、交货地点? —是否明确采购产品的技术质量要求? 采购产品质量控制 —是否有进货检验程序? —进货检验程序是否规定了检测项目、检测方法 、抽样方法、判定准则? —是否有保存检验记录? —检验记录是否完成、规范?
6.1
4
6.2
4
6.3
2
6.4
3
6.5
是否有检验记录? 检验记录是否正确、完成、清晰?
2
6.6
是否对设备进行日常点检?
2
第 7 页,共 26 页
供方质量体系和过程审核检查表
序号 检查内容 记录 分值 得分数
6.7
是否进行首件验证?
2
6.8
是否所有生产过程均受控有序?
3
6.9 6.9 6.10 6.11
1
8、生产设备/工装模具管理 8.1 对生产设备的整体印象,设备的精度/能力/状态 能否满足审核产品制造要求? 3
8.2
是否有设备管理部门和人员负责设备的管理?
1
8.3
是否制定生产设备/管理程序? 是否制定工装模具管理程序? 是否编制生产设备台账? 是否编制工装模具台账? 是否编制生产设备维护保养计划? 是否编制工装模具维护保养计划? 是否制定设备维护保养作业指导书? 是否制定工装模具维护保养作业指导书? 第 10 页,共 26 页
供方现场审核检查表(制造商)

1
重要的工艺参数有规定(如压力、温度、速度)。
○
○
1.5
2
各工艺参数的执行有据可查(检查、调节按钮、显示仪)。
○
○
1.5
3
对检验结果作质量变化趋势分析、评价。
○
○
1.2
4
缺陷排除措施,做好记录,并对措施有效性进行验证。
○
○
1.2
5
重要产品/过程特性在文件中标识规定。
○
1.2
6
对关键特性采用SPC方法进行过程监测。
○
○
1.2
7
模具和设备受到有效监控。
○
○
1.2
8
试生产和批产时进行过程能力分析,能力不足时采取适当的措施。
○
○
1.2
八、产品监测
1
按控制计划和工艺卡片等对生产制造过程实施监控(定期实施过程自查)
○
○
○
1.2
2
有首件检验规定,并严格执行。
○
○
1.5
3
最终检验有详细的检验规程。
○
○
1.2
4
监测装置和方法对发现缺陷的合理性。
供方名称:
序号
内容
评价对象/结果
评分
程序文件
计划
实施
记录
一、质量管理体系
1
建立ISO9001或TS16949质量管理体系,并通过认证。
○
1.5
2
对ISO/TS16949技术规范有所了解,并按要求正在逐步实施。
○
○
1.2
3
质量方针符合汽车行业市场和顾客期望。
○
○
1.5
供应商审核检查表

的控制
25.检查时的使用工具是否放在指
定的地方。
A B C D E
26.检查前,合格和不合格的产品
是否容易识别?
A B C D E
27.检查用的规格书是否最新版
本?
A B C D E
28.检查时出现不合格品的处理。
A B C D E
29、检验员是否随意更改作业指导
书?
A B C D E
30.是否有明确的抽样标准(AQL)?
考察结果
得分
重点说明
a.管理质量体系有无建立
b.责任与权限是否明确
c.有无组织表
口是2口否0
口是1口否0
口是1口否0
2,品管单位是否属于经营者的
独立组织形式?
A B C D E
管理者
3上.有无确立质量方针和目标?
匕是否公布全员了解?
□是2口否0
□是2口否0
的责任
4.确认质量目标后,有无具体推
进的活动容?
生产
过程
管理
37.生产作业场所光线是否充足?
A B C D E
38.作业场所是否整洁、整理、整
顿有无做好?
A B C D E
39.作业现场是否都有作业指导
书?
A B C D E
40.作业指导书是否记载作业顺
序,并浅显易懂?
A B C D E
41.作业指导书是否一致?
A B C D E
42.作业指导书是否说明产品缺陷
仪器
管理
64.仪器维护保养流程的制定与执行。
A B C D E
65.测试仪器是否定期检定?
A B C D E
66.检定用的器具是否经过专业计量
供应部审核检查表(最终稿)

检查内容
涉及
条款
参考
文件
检查方法
检查结果记录
备注
10
为管理评审提供什么资料。
11
资源管理
6
(1)询问供应部部长,资源短缺时如何配置。
(2)查看人力资源是否充足。与2-3名采购员进行面谈,了解他们的质量意识。
(3)询问采购员培训情况。
12
产品实现的策划
7.1
(1)询问供应部部长如何参与特定产品、项目或合同的质量计划的制定与实施工作。
8
职责和权限
5.5.1
(1)询问供应部部长采购部在公司中的作用是什么。
(2)询问2-3名采购员,看其对自己的职责和权限是否了解,是否知道与其他部门(岗位)的关系。
9
内部沟通
5.5.3
(1)询问2-3名采购员,了解如何与其他部门(岗位)进行沟通。
10
管理评审
5.6
(1)询问供应部部长参加管理评审的情况,采购部应
检查方法
检查结果记录
备注
e.对供应商的过程、设备、人员、质量体系有无必需要的要求。
f.采购文件发放前是否授权人员进行审批。是否在采购单或其他文件中对验证的安排和产品放行的方法作了具体规定。抽查1-2份相应文件及验证记录(若存在)
(4)查阅有关采购产品验证规定及验证记录,以核实是否满足规定要求。
2
文件控制
20
产品的监视和测量
8.2.4
(1)如何配合品管部做好进货验证工作。
21
不合格品控制
8.3
(1)询问供应部部长参加不合格来料处理的情况。
22
数据分析
8.4
(1)查看采购部是否对采购信息及进行分析,并针对其中的问题,采取相应的纠正措施。
供应商审核检查表

抽查现场
12.质量记录是否按规定的保存 抽查“质量记录归档、销毁记录 期限,并在过期后按规定销毁。 ”
1.是否按要求组织了合同评
审,并形成了“合同评审记录” 抽查“合同评审记录”
9
顾客要求评 审过程
产品交付管 理过程
供应商 管理专
员
。 2.合同修订是否按规定程序并 得到评审和审批。 3.是否对合同订单实时进行监 控。
抽查“设备设施日常维修保养记 录”
5.生产科是否不定期检查设备 抽查“设备设施日常维修保养记
日常维护保养的执行情况
录”
6.是否按照要求编制了设备的
预防性和预测性维护保养计划, 抽查“设备维修保养计划”
并按计划组织实施
7.是否按照规定对超过6个月不 使用的设备进行封存,重新启用 时是否履行了相关手续
检查“设备封存(启用)申请表 ”
质量管理 体系的领导作用和承诺
的理解,了解其相关 职责的履行
明确与质量管理体系有效性及策 情况; 2、在其他部一步证实最高管 理者对质量管
者的职责
理体系的领导作用和承诺; 3、
依据上述结果,综合判定组织最
高管理 者的作用与承诺是否发挥
到位。
供应商 2 领导作用 管理专
8.设备报废是否履行了相应的手 续
查“设备报废单”
3.是否按照规定建立了“工装模
具管理台帐”,并及时进行更新 抽查“工装模具管理台帐”
、维护
6
工装模具管 理过程
体系专 员
4.工装模具是否合格并且能够满 足/保证产品的要求。
抽查“工装模具检验记录”
5.是否按照规定定期对工装模具 进行维护保养。
抽查“工装模具使用记录”
供应商 求
供应商审核检查表

R.S N/A审核发现不符合内容OK NG1.4####√2.4####√3.4####现场询问带班人员,通过以过程为模式的管理,持续改进稳步提高产品质量,以诚信服务为导向,不断增强客户满意度√4.4####制定公司的KPI,并每月对不达标的KPI进行分析,并改善√5.4####通过系统抽查,抽查2021年绞线车间4月份培训,并对培训后的结果进行评价√R.S N/A审核发现不符合内容OKNG1.4####√2.4####√3.4####√R.S N/A审核发现不符合内容OKNG1.4####√2.4####√3.3####915机台 TX54/0.18,绞线员工米交接班记录本机速1000+/-100m/min,实际为1500√√4.3####车间看板职业卫生报告已经过期,未及时更新√R.S N/A审核发现不符合内容OK NG1.3####部分设备5S 部不到位√2.4####3.3####仓库不良品区未按照文件中的要求进行放置√R.S N/A审核发现不符合内容OKNG1.4####绞线机台工艺卡AX201903150017 19/9/0.32,要求记录13条的张力,实际只有12条√2.4####√3.4####√4.4####√5.4####√R.S N/A审核发现不符合内容OKNG1.4####√2.3####实验室镀层厚度记录表0120T有检验人员签字,无检测数据√3.4####√R.S N/A审核发现不符合内容OKNG1.4####√2.4####根据出货计划实施出货√3.4####WIPC001包装作业指导有规定√4.4####PD610-01风险和机遇应对控制程序,√5.4####每月5号进行统计汇总,并实施相应的改善措施√6.4####PFRE003工程变更管理程序,抽查Z1-03-02 按照要求进行工程变更√R.S N/A审核发现不符合内容OKNGH A B C D E F G 有无紧急对应体系和方法?对应能力如何?每月是否对各客户进行纳期达成率统计?如有纳期不理想时有无采取相应措施?有无变更部品管理规定?有无管理台帐及记录?供应商管理评分成品管理评分有无按客户的排期进行生产前能力评估?异常时有无书面联络给客户?是否按客户的排期进行出货?有无出货计划表?有无包装作业管理规定?包装要求是否明确?检查管理评分检查规格,判定基准是否明确?检查员是否理解检查规格?实施状况如何?检查结果有否记录(DATE)?是否按抽样标准进行抽样?依据检查结果对LOT的判定,处理及向相关部门的反馈是否适切?是否有QC工程表与作业标准书,内容是否适切?文件规定的内容是否得到了实施?工程能力能否达到客户的纳期、品质要求?工程内不良有无使用统计手法进行原因分析及对策?工程内不良有无使用统计手法进行原因分析及对策?有无按客户的排期制定月、日生产计划表?实施状况如何?整理、整顿、清扫(5S)是否充分实施?作业环境是否适当?材料、半成品、完成品的保管状态是适当?良品、不良品及半成品、成品的标识,区分是否明确?工程管理(制造的日常管理)评分是否采用品质统计手段进行质量管理?有无采取相应的措施?客户情报有否发行,配布及回览,是否进行配布以确得可见性?检查基准书、其他相关资料是否规定的管理方法?实施状况如何?对旧文件的管理(改版)是否确切地在执行?新旧版本有无明确标识?环境、现品管理评分品质保证体制的基本要点是否在组织上予以保证实态是否相仿?品质保证责任者是否对品质保证业务的正常运作实施监控,是否采取了适当的改善行动。
供方过程审核检查表

1、审核目的:验证产品所属的过程是否符合规定要求和可靠,验证过程是否具有能力并受控; 评定过程相关结果的有效性,确保满足质量目标2、审核依据:过程审核提问表3、审核组长/成员:苏理彬/徐瑛、辛燕萍4、日期:2004.06.16~2004.06.17审核时间对应要素(过程审核表)2004.06.16 9:00~9:302004.06.16 9:30~10:30 3.过程开发的策划2004.06.16 10:30~11:304.过程开发的落实2004.06.16 12:30~14:00 5.供方/原材料2004.06.16 14:00~15:306.1人员/素质;2004.06.16 15:30~17:00 6.2生产设备/工装2004.06.17 10:00~11:306.3运输/搬运/贮存/包装2004.06.17 12:30~14:00 6.4缺陷分析/纠正措施/持续改进2004.06.17 14:00~15:307.服务/顾客满意度2004.06.17 15:30~16:002004.06.17 16:00~16:30制定:管理者代表:起始会议中饭时间Solid Pacakging Technology (Shanghai) Co., Ltd.内部过程审核日程计划日程安排受审部门/现场审核员对应人员第二日采购部、质保部、实验室苏理彬;辛燕萍宋定霞、徐瑛生产现场;检验现场;翻检区、行政部苏理彬;辛燕萍生产设备现场、检验现场苏理彬;辛燕萍刘亮、徐瑛质保部、客户服务苏理彬;辛燕萍徐瑛、秦天玺物料仓库、工装仓库辛燕萍;徐瑛SPT-D/Q/QC-07-02-R0工程部苏理彬;辛燕萍陈玉玲工程部苏理彬;徐瑛陈玉玲刘亮、张秋风、陆燕刘亮、李勇强、张秋凤任明超、李勇强中饭时间末次会议分发部门(人员)QC——徐瑛;PR——Lisa ;PD——沈晓通、李勇强、刘亮;WH——任明超AD——陆燕;SA——秦天玺审核组长:苏理彬分发日期:2004.06.09审核小组会议生产现场,检验现场苏理彬;辛燕萍。
供方审核检查表
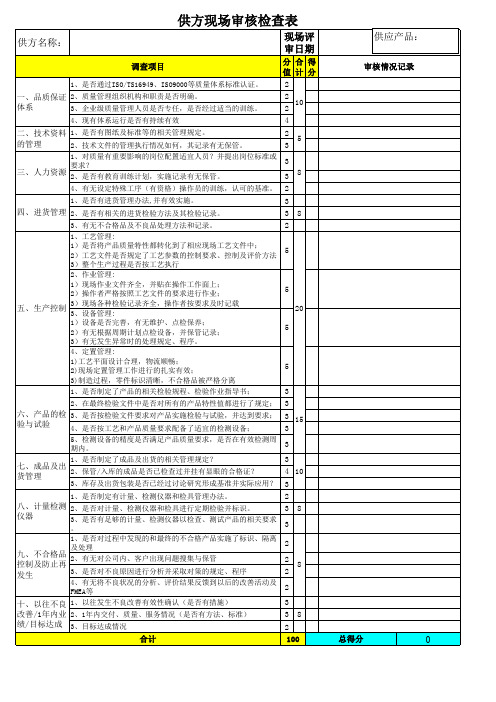
1、是否制定了产品的相关检验规程、检验作业指导书;产品特性值都进行了规定; 3
六、产品的检 3、是否按检验文件要求对产品实施检验与试验,并达到要求;
验与试验
4、是否按工艺和产品质量要求配备了适宜的检测设备;
3 3
15
5、检测设备的精度是否满足产品质量要求,是否在有效检测周 期内。
2
十、以往不良 1、以往发生不良改善有效性确认(是否有措施) 改善/1年内业 2、1年内交付、质量、服务情况(是否有方法、标准) 绩/目标达成 3、目标达成情况
3 38 2
合计
100
供应产品:
审核情况记录
总得分
0
供方现场审核检查表
供方名称:
现场评 审日期
调查项目
分合得 值计分
1、是否通过ISO/TS16949、ISO9000等质量体系标准认证。
2
一、品质保证 2、质量管理组织机构和职责是否明确。
体系
3、企业级质量管理人员是否专任,是否经过适当的训练。
2 10 2
4、现有体系运行是否有持续有效
4
二、技术资料 1、是否有图纸及标准等的相关管理规定。
的管理
2、技术文件的管理执行情况如何,其记录有无保管。
25 3
1、对质量有重要影响的岗位配置适宜人员?并提出岗位标准或 要求?
3
三、人力资源 2、是否有教育训练计划,实施记录有无保管。
38
4、有无设定特殊工序(有资格)操作员的训练,认可的基准。 2
1、是否有进货管理办法,并有效实施。
3
四、进货管理 2、是否有相关的进货检验方法及其检验记录。
3
1、是否制定了成品及出货的相关管理规定?
3
- 1、下载文档前请自行甄别文档内容的完整性,平台不提供额外的编辑、内容补充、找答案等附加服务。
- 2、"仅部分预览"的文档,不可在线预览部分如存在完整性等问题,可反馈申请退款(可完整预览的文档不适用该条件!)。
- 3、如文档侵犯您的权益,请联系客服反馈,我们会尽快为您处理(人工客服工作时间:9:00-18:30)。
○
○
○
6
理解过程方法,明确顾客导向过程、支持过程及管理过程。
○
○
○
7
对新产品制造过程设计和开发(APQP)的认识程度。
○
8
对生产件批准程序(PPAP)理解,可能实施的程度。
○
9
制造过程变差采用统计技术方法控制。
○
○
10
进行产品审核,进行缺陷分析。
○
○
11
建立实验室管理程序,并实施。
○
○
○
二、设计和开发控制
○
10
原、辅材料等均有明显标识,确保存放、搬运不混料、混批。
○
11
明确生产制造过程中检验场所,标识检验产品(零部件)的状态。
○
六、技术文件管理
1
现有的加工流程编制工艺规程。
○
2
工艺规程和操作规程等作业指导书在生产现场易于得到。
○
3
所有技术文件,作业指导书受控并有效。
○
七、过程控制
1
重要的工艺参数有规定(如压力、温度、速度)。
○
8
有缺陷的产品采用统计方法(如排列图、因果图)分析,并制定改进措施。
○
○
9
返工作业制订作业指导书。
○
10
返工必须在规定的场所、人员按文件规定进行,返工的产品重新检验。
○
○
11
产品包装按照顾客的要求实施。
○
12
新的和更改过的产品/过程应规定批量生产认可的条件。
○
○
○
13
对库存件确保留有必要的间隔,检查其损坏程度和质量。
评审人员:
评审结论:
评审日期:
○
○
○
2
生产设备有计划/规定进行维护、保养。
○
○
○
3
关键设备的标识,要求进行点检,重要参数有控制和调节规定。
○
○
4
设备和工装模具按要求存放和维护。
○
○
5
关键设备、工装有备件计划,能适应“应急计划”要求。
○
五、现场管理
1
操作岗位员工素质符合相应岗位的能力要求,并得到培训。
○
○
2
生产和检验场地符合要求(整洁、干净、照明和安全等)。
1
在开发各阶段和批量生产前进行产品评审、确认、试验、验证等,并有产品开发计划和实施记录。
○
○
2
产品开发工作的结果在规范中形成文件。
○
○
3
设计变更时要有书面文件记录,经重新批准后才能实施。
○
○
三、采购管理控制
1
采购原材料等产品按照质量要求供货。
○
○
2
做到只有合格的材料才能入库或进入生产车间。
○
3
材料存放和搬运做到了“先进先出”。
供方名称:
序号
内容
评价对象/结果
评分
程序文件
计划
实施
记录
一、质量管理体系
1
建立ISO9001或TS16949质量管理体系,并通过认证。
○
2
对ISO/TS16949技术规范有所了解,并按要求正在逐步实施。
○
○
3
质量方针符合汽车行业市场和顾客期望。
○
○
4
质量目标可测量并层层分解至各职能部门。
○
○
○
5
最高管理者定期实施评审质量体系的有效性。
○
○
14
外购产品规定验收要求和有关质量认明。
○
○
九、纠正和预防措施
1
对顾客提出的纠正指导书,确实进行回复。
扣分说明:
○
○
2
对实施的纠正措施进行有效性评价。
○
○
3
对退货批的不合格品,分析发生的原因,防止再次发生。
○
○
4
使用各种活动计划等,对提高质量、服务(交货期、交付)、价格等,实施持续改进。
○
○
○
总分合计:
○
3
设备、产品、操作和检验场地有定置管理规定,并执行。
○
○
4
对调整加工和自检有调整样件或极限标样。
○
○
5
检测器具在加工场地和检验点按照要求存放,并维护。
○
○
6
存放和运输工位器具和产品特点相适合。
○
○
7
材料/零件的物流合理。
○
8
材料/零件在加工工位前后有明显标记(加工和检验状态)。
○
9
不合格品,可疑品及废品须作明确标记,并隔离存放。
评分规则:
1、本表共九大项,67条,合计100分,其中每条1.5分。
2、若某项(或条款)不适宜(如没有产品设计职责),则将不适宜项(或条款)去掉,按∑实得分/∑标准分×100分计算。
3、计分:①未开展0分,②刚开始(起步)0.5分,③基本做到0.8分,④做得比较好1.2分,⑤很好满分。
4、审核得分评定:≥90分,优良;75-89分,合格;60-74分,不合格但可用;<60分,不合格且不可用。
○
○
2
各工艺参数的执行有据可查(检查、调节按钮、显示仪)。
○
○
3
对检验结果作质量变化趋势分析、评价。
○
○
4
缺陷排除措施,做好记录,并对措施有效性进行验证。
○
○
5
重要产品/过程特性在文件中标识规定。
○
6
对关键特性采用SPC方法进行过程监测。
○
○
7
模具和设备受到有效监控。
○
○
8
试生产和批产时进行过程能力分析,能力不足时采取适当的措施。
○
○
4
入库检验接收准则(如检验计划、职责)确定,并且得到很好应用。
○
○
○
5
质量能力强的合格供方供货倾斜性。
○
○
6
外购产品执行“首批样件”认可制度。
○
○
○
7
对供货商作质量能力调查。
○
○
8
对供方供货质量业绩进行评价,并对存在缺陷要求采取措施纠正。○○四、生产设备管理
1
合理配备生产设备(机器、工装模具),并有登记台帐。
○
○
八、产品监测
1
按控制计划和工艺卡片等对生产制造过程实施监控(定期实施过程自查)
○
○
○
2
有首件检验规定,并严格执行。
○
○
3
最终检验有详细的检验规程。
○
○
4
监测装置和方法对发现缺陷的合理性。
○
5
定期对检验、测量和试验设备实施检查,必要时进行校准。
○
○
○
6
重要产品特性项目的监测得到充分考虑。
○
○
7
制订全尺寸检验和试验规定。