应用机器视觉技术检测电路板焊点
基于机器视觉的电气自动化智能检测技术的研究

基于机器视觉的电气自动化智能检测技术的研究摘要:随着科技的不断发展,电气自动化在工业生产中的应用日益广泛,对电气设备的检测要求也越来越高。
机器视觉作为一种新兴的检测技术,具有非接触、高精度、高速度等优点,为电气自动化智能检测提供了新的解决方案。
本文深入研究了基于机器视觉的电气自动化智能检测技术,包括其原理、系统组成、关键技术以及应用实例,并对该技术的发展前景进行了展望。
关键词:机器视觉;电气自动化;智能检测一、引言电气设备在工业生产、电力系统、交通运输等领域中起着至关重要的作用。
为了确保电气设备的安全、可靠运行,需要对其进行定期检测和维护。
传统的电气检测方法主要依靠人工检测,存在检测效率低、误差大、危险性高等问题。
随着机器视觉技术的不断发展,其在电气自动化检测中的应用越来越受到关注。
机器视觉技术可以快速、准确地获取电气设备的图像信息,并通过图像处理和分析算法实现对设备的智能检测,大大提高了检测效率和精度。
二、机器视觉技术概述(一)机器视觉的定义机器视觉是用机器代替人眼来做测量和判断的技术,它通过图像摄取装置将被摄取目标转换成图像信号,传送给专用的图像处理系统,根据像素分布和亮度、颜色等信息,转变成数字化信号;图像系统对这些信号进行各种运算来抽取目标的特征,进而根据判别的结果来控制现场的设备动作。
(二)机器视觉的原理机器视觉的原理主要包括图像采集、图像处理和图像分析三个部分。
图像采集是通过相机、镜头等设备获取被检测物体的图像;图像处理是对采集到的图像进行去噪、增强、分割等操作,以提高图像的质量和可识别性;图像分析是对处理后的图像进行特征提取、模式识别等操作,以获取被检测物体的相关信息。
(三)机器视觉的优势与传统的检测方法相比,机器视觉技术具有以下优势:1.非接触式检测,不会对被检测物体造成损伤;2.检测速度快,可以实现实时检测;3.检测精度高,可以检测到微小的缺陷和变化;4.可以实现自动化检测,减少人工干预,提高检测效率和可靠性。
基于AOI技术的PCB常见质量缺陷检测

基于AOI技术的PCB常见质量缺陷检测一、AOI技术原理AOI技术利用光学原理和图像处理技术,通过自动化设备对PCB进行全面、高效的检测。
其工作原理如下:1. 图像采集:AOI设备利用高分辨率的摄像头对PCB表面进行快速高清的扫描,获取表面的图像信息。
2. 图像处理:通过图像处理算法,将采集的图像进行处理,提取出PCB的各种特征信息,比如焊点、元器件、线路等。
3. 缺陷检测:通过预设的检测算法,对提取出的特征信息进行比对,发现PCB表面的质量缺陷,比如焊点漏锡、虚焊、短路、错位等。
4. 报警和记录:一旦检测到质量缺陷,AOI设备会即时报警,并将缺陷信息记录下来,为后续的修复和改进提供参考。
二、AOI技术在PCB质量检测中的应用AOI技术在PCB质量检测中的应用已经非常广泛,主要体现在以下几个方面:1. 焊点检测:AOI设备能够对PCB表面的焊点进行全面检测,包括焊接不良、短路、漏锡、虚焊等质量缺陷,并能够快速准确地将缺陷点标记出来,为后续的修复工作提供参考。
2. 元器件检测:AOI设备可以对PCB表面的元器件进行识别和检测,包括元器件的位置、方向、标识等,发现元器件的错位、反向安装等问题。
3. 线路检测:AOI设备能够检测PCB表面的线路连接情况,发现线路断路、短路等问题,提高了PCB的整体稳定性和可靠性。
4. 其他检测:AOI技术还可以应用于PCB表面的防护层、印刷标识等方面的检测,确保整个PCB的质量达到标准要求。
基于AOI技术的PCB常见质量缺陷检测主要包括焊点缺陷、元器件缺陷和线路缺陷等几个方面。
1. 焊点缺陷检测焊点是PCB上最为关键的部分之一,良好的焊点对整个电子产品的性能和稳定性至关重要。
基于AOI技术的焊点缺陷检测主要包括以下几种情况:(1)虚焊:AOI设备能够检测出焊点与焊盘之间的连接是否良好,发现虚焊情况,并及时报警。
(2)漏锡:在焊点未完全覆盖焊盘的情况下,AOI设备能够快速准确地检测出漏锡情况,并指示操作员进行修复。
基于机器视觉的弧焊缺陷检测技术研究

基于机器视觉的弧焊缺陷检测技术研究随着现代工业技术的发展,焊接技术已经成为工业中不可缺少的一环。
其中,弧焊技术因其高效、便捷、工业化生产能力强的特点,被广泛应用于轨道、采矿、机械加工等领域。
但是焊接过程中出现的缺陷问题,也一直困扰着行业的发展。
传统的焊缝检测方法通过肉眼或显微镜进行检查,存在不稳定、繁琐、误判率高等问题。
而基于机器视觉的焊缝缺陷检测技术,正逐渐成为研究热点。
一、机器视觉技术在焊缝缺陷检测中的应用机器视觉技术主要包括图像处理、模式识别和计算机视觉等方面。
在焊缝缺陷检测中,图像处理技术可以对焊缝进行预处理,提高图像质量;模式识别技术可以自动确定参数进行分类,以识别焊接质量;而计算机视觉则是对图像进行更多的分析和处理,可以达到更高的准确度和稳定性。
图像处理和计算机视觉通常采用的都是数字化图像。
数字化图像是将图像转化为数值信息,以便计算机进行处理和分析。
图像处理主要包括灰度处理、滤波、边缘检测、形态学变换等方法,可以使得图像在被用于分析之前有更好的清晰和可分辨性。
计算机视觉主要包括区域分割、特征提取、目标匹配、分类识别等过程。
这些方法可以使得计算机通过图像处理技术自动分析出焊接缺陷,从而达到自动化检测的效果。
二、机器视觉技术的优势和挑战利用机器视觉技术进行焊缝缺陷检测有许多优势。
首先,机器视觉技术能够确保检测质量的一致性和唯一性。
其次,机器视觉技术能够自动化对焊缝进行检测,减少了人工检测的不确定性和成本,提高了效率和准确性。
此外,机器视觉技术也可以对焊接工艺进行调整,提高焊接质量和生产效率,同时减少了资源的浪费。
然而,机器视觉技术的应用也有许多挑战。
首先,焊接缺陷识别需要考虑到大量的因素,如焊接参数、焊接方向等,这些因素都会影响到检测质量。
其次,在一些特殊情况下,存在类似于仿射变换等数学模型无法适用的情况,这就需要研究人员采用更多的手段来进行处理。
最后,在对焊接质量进行检测时,机器视觉技术往往需要特殊的硬件设备来保证数据的准确度和稳定性。
基于机器视觉的自适应焊接技术研究

基于机器视觉的自适应焊接技术研究近年来,随着制造业的不断发展和智能制造技术的迅猛发展,各种自动化生产设备被广泛应用于生产领域。
其中,焊接技术是制造业中非常重要的一环。
传统的焊接技术主要依靠人工操作,无法满足高效、智能的生产需求。
因此,基于机器视觉的自适应焊接技术应运而生。
机器视觉是人工智能技术的一种重要应用,可以使机器模拟人类视觉,从而实现物体的识别和检测。
基于机器视觉的自适应焊接技术可以通过自动识别、定位和追踪焊缝,实现更加准确和稳定的焊接效果,有效提高生产效率和焊接质量。
一、自适应焊接技术的基本原理自适应焊接技术利用机器视觉系统实时获取焊缝图像信息,通过算法分析、处理和比较,对焊接过程进行数字化控制。
该技术主要包含焊缝检测、焊缝分类、焊接路径规划、优化焊接参数等几个方面。
首先是焊缝检测,采用机器视觉技术对焊缝进行实时检测和识别,确定焊接位置和焊接线路,为下一步的焊接路径规划提供数据基础。
其次,是焊缝分类,根据不同的焊缝类型选取不同的焊接参数和焊接策略,实现不同类型焊缝的有效焊接。
接着是焊接路径规划,根据焊接目标信息和焊接参数,自动生成最佳的焊接路径和焊接速度参数,实现最优化的焊接控制。
最后是优化焊接参数,根据不同的焊接类型和焊接材料,自动调整焊接电流、电压、焊丝进给速度等参数,以保证焊接质量和稳定性。
二、自适应焊接技术的优势相比较传统的焊接技术,基于机器视觉的自适应焊接技术具有以下优势:(一)高效节能。
节约人力,减少生产成本,提高生产效率;(二)应用广泛,可适用于多种焊接场景;(三)灵活性和自适应性强,可以自主识别、分类和调整焊接参数;(四)焊接质量稳定,精度高,可以保证焊接质量和产品质量;(五)真正意义上实现了智能化制造,推动了制造业的高质量、高效率和高精确度发展。
三、自适应焊接技术的应用领域自适应焊接技术目前被广泛应用于汽车制造、电子制造、航空航天和机械制造等多个领域。
例如,在汽车制造行业,自适应焊接技术可应用于车身焊接和底盘焊接等多个环节,可以大幅提高效率和质量。
机器视觉技术在质量控制中的应用
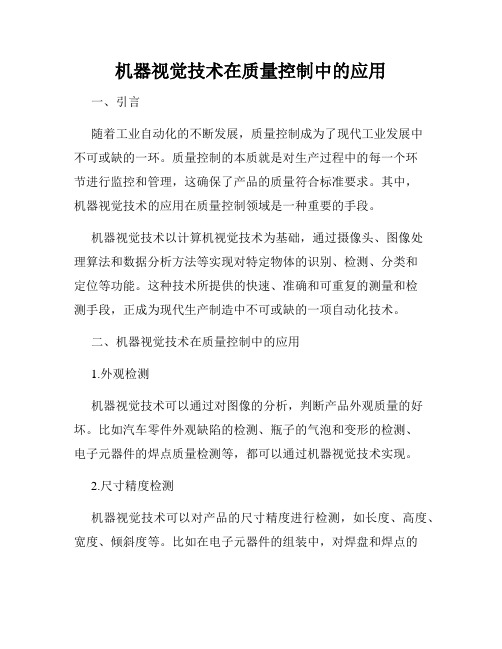
机器视觉技术在质量控制中的应用一、引言随着工业自动化的不断发展,质量控制成为了现代工业发展中不可或缺的一环。
质量控制的本质就是对生产过程中的每一个环节进行监控和管理,这确保了产品的质量符合标准要求。
其中,机器视觉技术的应用在质量控制领域是一种重要的手段。
机器视觉技术以计算机视觉技术为基础,通过摄像头、图像处理算法和数据分析方法等实现对特定物体的识别、检测、分类和定位等功能。
这种技术所提供的快速、准确和可重复的测量和检测手段,正成为现代生产制造中不可或缺的一项自动化技术。
二、机器视觉技术在质量控制中的应用1.外观检测机器视觉技术可以通过对图像的分析,判断产品外观质量的好坏。
比如汽车零件外观缺陷的检测、瓶子的气泡和变形的检测、电子元器件的焊点质量检测等,都可以通过机器视觉技术实现。
2.尺寸精度检测机器视觉技术可以对产品的尺寸精度进行检测,如长度、高度、宽度、倾斜度等。
比如在电子元器件的组装中,对焊盘和焊点的规格要求非常严格,通过机器视觉技术的测量和分析,可以快速、准确地判断焊盘和焊点的规格是否合格。
3.自动排序机器视觉技术可以通过对图像的识别和分类,自动将产品进行排序,将不合格品和合格品自动分开。
比如,在食品加工中,机器视觉技术可以对颜色、大小、形状等特征进行识别和分类,将不同种类的食品自动进行分拣。
4.质量追溯机器视觉技术可以对生产过程中产品的每一个环节进行监控和记录,从而实现质量追溯的功能。
比如,对食品包装过程中每个产品的生产日期、批次号等信息进行记录和存储,在产品出现质量问题时,能够快速找到引起问题的原因和责任,并采取相应的措施进行处理。
三、机器视觉技术在质量控制中的优势1.快速、准确机器视觉技术能够在很短的时间内对多个图像进行处理,并准确地判断产品的质量。
在生产线上,能够实现对产品的及时检测,提高生产效率和生产质量。
2.自动化机器视觉技术实现了对质量控制的自动化,减少了人工干预的机会,降低了人为误差的发生,提高了生产效率。
机器视觉在焊点检测中的应用

1.引言
如今伴随数字产品已在人们生活中的大量使用,半导体设备制造业得到迅猛的发展,键合机就是半导体封装其中很重要的一个工序,而焊线后检测(PBI:Post Bond Inspect)又是键合机提高机器性能,拓展机器功能的一个重要课题。
结果证明,PBI算法可以快速判定在指定位置是否存在球,也可以精准的计算球的位置和半径。
4.2PBI算法的应用展望
根据检测出来球的状态,位置和半径这些详细的信息,我们可以打开思路,在工业上会有非常多的具体的应用。本文只是浅谈几项该技术的具体应用。
1).PBI算法一开始被提出来就是为了实现断线检测而开始被大家去研究的,断线检测就是机器取代替人工去找出没焊上线的次品芯片,相当于一个自动质检的过程(很重要,能省很多人力)。有了完善的算法之后,我们可以通过图像处理在理想位置附近寻找球的存在与否来判定焊线状况,很大程度上完善了机器的功能和提高了设备的效益。
4.PBI(焊线检测)的测验结果和应用展望
4.1PBI算法的测验结果
将PBI算法应用在设备上,通过大量的测试,得到了很好的实验结果。
以下是部分实验结果:
图4-1各种焊点正常下的PBI处理结果
图4-2各种焊点不正常的PBI处理结果
从图中我们可以知道,针对焊点正常的情况,不计环境的差异性,光路的差异性,球形的差异性,都可以用该算法,正确的找到球的位置和半径;而针对各种焊点不正常的情况,均没有误找的发生。
腐蚀的作用是消除物体消除物体边界点,使目标缩小,可以消除小于结构元素的噪声点;膨胀的作用是将与物体接触的所有背景点合并到物体中,使目标增大,,可添补目标中的空洞。
焊点测试的原理和应用

焊点测试的原理和应用焊点测试的原理焊点测试是通过对焊点进行检测,以确定焊点的质量和可靠性。
焊点测试主要目的是检测焊点的连接强度、电气性能和耐久性。
焊点测试可以帮助制造商评估焊点的可靠性,并及时发现焊点故障,从而提高产品质量和可靠性。
以下是常用的焊点测试原理:1.视觉检测:通过人眼观察焊点的外观,检查是否有未焊接、焊接质量差或焊点损坏等问题。
2.电阻检测:通过测量焊点的电阻来评估焊点的连接质量。
正常情况下,焊点的电阻应该很低,如果电阻过高,则可能是焊点存在问题。
3.拉力测试:通过施加拉力作用于焊点,并测量焊点的抗拉强度,来评估焊点的可靠性。
4.耐久性测试:通过连续施加电流、温度、振动或其他外部刺激,来模拟实际使用条件下焊点的工作状态,评估焊点的耐久性和可靠性。
焊点测试的应用焊点测试广泛应用于电子制造业中,特别是在电子产品的生产过程中。
以下是焊点测试的一些常见应用场景:1.PCB制造:焊点测试可以检测PCB上的焊点连接质量,确保焊点与PCB之间的连接良好。
在大规模生产中,焊点测试可以提高生产效率,并降低因焊点质量不良引起的产品故障率。
2.电子组件制造:焊点测试可以用于检测电子组件之间的焊接连接,以确保组件之间的电气连接可靠。
焊点测试可以帮助制造商及时发现焊点问题,并及时采取措施修复或更换焊点,以提高产品质量和可靠性。
3.汽车制造:焊点测试在汽车制造中扮演重要角色。
焊点测试可以帮助汽车制造商检测车身焊接点的质量,确保车身结构的稳定性和安全性。
焊点测试可以帮助汽车制造商发现焊点质量不良的问题,并及时采取措施,防止车辆在使用中出现安全隐患。
4.航空航天制造:在航空航天制造领域,焊点测试尤为重要。
焊点测试可以用于检测飞机和航天器上的焊点连接质量,确保航空航天器的结构稳定性和安全性。
焊点测试可以帮助制造商检测焊点的可靠性,并及时发现焊点故障,以确保航空器和航天器的安全飞行。
总结起来,焊点测试是提高产品质量和可靠性的关键步骤之一。
基于机器视觉的焊接质量检测技术研究
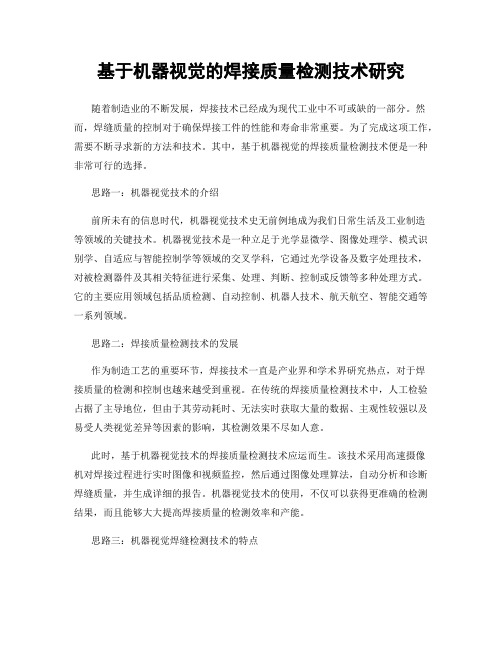
基于机器视觉的焊接质量检测技术研究随着制造业的不断发展,焊接技术已经成为现代工业中不可或缺的一部分。
然而,焊缝质量的控制对于确保焊接工件的性能和寿命非常重要。
为了完成这项工作,需要不断寻求新的方法和技术。
其中,基于机器视觉的焊接质量检测技术便是一种非常可行的选择。
思路一:机器视觉技术的介绍前所未有的信息时代,机器视觉技术史无前例地成为我们日常生活及工业制造等领域的关键技术。
机器视觉技术是一种立足于光学显微学、图像处理学、模式识别学、自适应与智能控制学等领域的交叉学科,它通过光学设备及数字处理技术,对被检测器件及其相关特征进行采集、处理、判断、控制或反馈等多种处理方式。
它的主要应用领域包括品质检测、自动控制、机器人技术、航天航空、智能交通等一系列领域。
思路二:焊接质量检测技术的发展作为制造工艺的重要环节,焊接技术一直是产业界和学术界研究热点,对于焊接质量的检测和控制也越来越受到重视。
在传统的焊接质量检测技术中,人工检验占据了主导地位,但由于其劳动耗时、无法实时获取大量的数据、主观性较强以及易受人类视觉差异等因素的影响,其检测效果不尽如人意。
此时,基于机器视觉技术的焊接质量检测技术应运而生。
该技术采用高速摄像机对焊接过程进行实时图像和视频监控,然后通过图像处理算法,自动分析和诊断焊缝质量,并生成详细的报告。
机器视觉技术的使用,不仅可以获得更准确的检测结果,而且能够大大提高焊接质量的检测效率和产能。
思路三:机器视觉焊缝检测技术的特点与传统的人工检测方法相比,机器视觉技术在焊接质量检测中具有多个独特的特点:(1) 非接触式检测,不会对产品形态和尺寸造成影响;(2) 可重复性好,可以减少人员不确定因素和测试误差;(3) 自动化程度高,效率提高,削减人工成本;(4) 可以实现在线检测,缩短反馈闭环时间,提高产品的一致性和稳定性。
思路四:机器视觉检测技术的应用现代工业中的焊接生产存在很多因素影响焊接质量,如板材的出现了偏差、板材因翻转后位置不稳定、焊枪的工作状态不稳定、电源输出不稳定、杂散电磁场的干扰等等。
- 1、下载文档前请自行甄别文档内容的完整性,平台不提供额外的编辑、内容补充、找答案等附加服务。
- 2、"仅部分预览"的文档,不可在线预览部分如存在完整性等问题,可反馈申请退款(可完整预览的文档不适用该条件!)。
- 3、如文档侵犯您的权益,请联系客服反馈,我们会尽快为您处理(人工客服工作时间:9:00-18:30)。
维普资讯
要有 值 为 1的 区域 面积 大 于 阈值 , 认 为 电路 板 焊 就
图像实际上是光 电信息 , 因此 噪声的影响会导 致图像质量下 降, 图 3 使图像模糊 , 至改变了 如 , 甚
图像 的特 征 , 图像 分 析 和识 别 带来 了 困难 。 图 3 给
照片。图像通过采集卡送人计算机进行处理 , 同时
在 监视 器上 可显 示 当前 的 电路 板 , 供人 工 检i 。 贝 0
化生产 中占有着 非 常重 要的地位。如何 提高检测 效率和检测准确性是 目前需要解决的问题 , 采用机 器视觉技术与其它检测方式相 比, 它能够节约时 间
和节 省劳 动力 。 目前 , 用机 器 视 觉 技 术 的检 测 系 采 统具 有速 度快 、 度高 、 接触 式 等优 点 。本 系统 是 精 非 对 电路板 焊 点 进 行 检 测 , 主要 检 测 目标 是 : 检测 焊 点 的有无及 指 出漏 焊 的位置 。
l o o 1 J
图 5 灰度分布直方 图
50 0
0
0
图 6 灰 度分 布直方图
维普资讯
6期
朱
岩, : 等 应用机器视觉技 术检测 电路板焊点
图 9 标准
图 1 相减 的结 果 图 0
2 2 判别 过程 .
在本系统 中 , 由于摄 像机 的位置 固定 , 电路板
维普资讯
第 7卷
第 6期
20 0 7年 3月
科
学
技
术
与
工
程
@
Vo . No 6 17 .
Ma .2 0 r 07
17 —89 2 0 ) —0 50 6 11 1 (0 7 6 14 — 4
S in e T c n l g n n i e r g ce c e h o o y a d E gn e i n
20 Si Tc.nn. 07 c ehE gg .
应 用机器视觉技术检 测 电路板焊 点
朱 岩 段哲 民
( 西北工业大学 电子信 息学 院 , 西安 7 07 ) 10 2
摘
要
在 线检测技术在 自动化 生产 中占有 重要 的地位 , 计 了一个 图像 处理 系 统, 用工 业摄 像镜 头替 代 目视作 为传感 设 利 检 测 图像处理 图像 分割 焊点
为采集 的原始图像 , 了消除噪声 , 为 常采用滤 波的 方法 , 见图 2 。在此选用了二维 中值滤波 , 即用该像
2 系统的软件设计
系统选用 M tb语言来进 行 图像处 理算法 的 aa l
20 0 6年 1 月 1日收 到 1
素的相邻像素 的灰度 中值来替代该像 素 的值¨ 。
光
c
图 1 系统基本构成
编写 , 图像信号在 图像采集 卡中经过 A D转换为 8 /
位 的数字信号 , 0为暗 ,5 25为亮 ,—25对应不 同 0 5
1 系统的硬 件设计
系统 的硬 件 构 成 如 图 1所示 , 能灯 管 具 有 功 节
的明暗情况 。该算法 的基本原理 是采用待 检测 板 与标准板的比对来进行检测 , 故第一 步要 已知标准
板 的信息 。
2 1 标 准板信 息 的提 取 .
2 1 1 图像 的预 处理 . .
率低 、 亮度高 、 寿命 长等优点 , 故光源选 择节能灯 。
由于要 达 到在线 检测 的 要 求 , 该 系 统 选 用 了 具有 故 异 步复 位功 能 的 黑 白 C D摄 像 机 进 行 拍 照来 获取 C
:
丢
【 ∑h
h
合本 图像 的灰度分 布, 采用 线性灰度变换 ( ( ) 见 2 式) 原图像的灰度范围见图 5 为[020 , , , 5 , ] 线性变 5 换后图像灰度范 围见 图 6 为 [ ,5 ] 图 7为灰度 , 0 25 ,
变换 增强 后 的效果 。
『 o o ]
14 O6
科
学
技
术
与
工
程
7卷
0一 圜 噪_ — 声 —
图 2 图像 复原模型
:
g m, )=d-c/ ( n (
一
口 )+c
() 2
∑Md nX} ea{ i
A
() 1
图 7 灰度变换增 强 图 8 阈值 分割图像 A
图 3 C D采集 的图像 C
一
图4 二维中值 滤波
在 传送 带上 拍 照 的位 置 是 不 变 的 , 以认 为每 次 拍 可
照得到图像 的大小 、 尺寸 、 角度是一致的。 判别的具体过程为 : () 1 将待检测 板 图像进行 预处理和 阈值 分割 , 得到全部的焊点信息 ; 与如上处理标准板 的过程是 的图像 相减 , 到一 得 幅二值图像 , 其中含有一些不相关的干扰点。 () 3 预先给定一个 阈值 , 为判别 的依据。只 作
般的成像系统只具有一定 的亮度范围, 亮度
的最大值和最小值 之 比称为对 比度 。提高 图像 的 对 比度 能够方便 我们 进行 以后 的图像 处理 工作。 通过灰度变换可以提高对 比度 , 灰度变换又可以分
为 3种 : 性 变 换 、 段 线性 变 换 、 线性 变 换 。结 线 分 非
器, 通过 图像采集 、 图像处理 、 图像识别等 一系列操作 , 达到在 线对 电路板焊点检测 的 目的。 关键词
中图法分类号
T 314 ; P9.1
文献标识 码
B
考虑到传统 的检测手段 已经 不能满 足现代工
业 生产水 平对 产 品质 量 检 测 的要 求 , 线检 测 已经 在 成 为一个 必然 趋 势 。 目前 , 线 检测 技 术 已在 自动 在